2025/Grupo11/DimensionamientoFisico
Determinación de Localización
El método elegido para determinar la localización consiste en una Matriz de Localización para comparar las distintas alternativas de localizar físicamente el centro de producción. Se eligieron 3 alternativas. Las cuales son:
- Escobar
- Avellaneda
- Parque industrial de Pilar
En esta matriz, se analizaron distintos factores. Un factor crítico es la disponibilidad de energía eléctrica estable y confiable. Otros factores también se tuvieron en cuenta como deseables y se ponderaron de acuerdo con su relevancia.
- medios de transporte: Avellaneda cuenta con la disposición del tren Roca y con varias líneas de colectivos que la conectan con CABA. Tiene acceso a autopistas viales y una conexión directa por la ruta provincial 36. Escobar tiene acceso al tren Mitre, el cual tiene una frecuencia menor al tren Roca. También tiene acceso a diversas líneas de colectivos, aunque menos aunque menos que las de Avellaneda. Por último, tiene acceso a la ruta 9, la cual suele tener tránsito alto.
- Disponibilidad de MO: La mano de obra debe estar calificada para realizar sus distintos roles y funciones. Desde el punto de vista de la localización, se está buscando zonas en donde haya una población de entre 25 a 49 años, teniendo en cuenta el perfil de profesionales de la empresa. Las 3 alternativas cuentan con una valoración similar.
- Cercanía de las fuentes de abastecimiento/proveedores: las fuentes de abastecimiento y proveedores fueron mencionados en el apartado comercial, las cuales consisten en los proveedores de aceites de mecanizado y anticorrosivos. En el caso del Parque industrial de Pilar, tiene una ventaja clara debido a que las empresas de este estilo buscan colocarse cerca de esta zona para facilitar el acceso a las empresas ubicadas ahí. En el caso de Avellaneda, hay un puerto en la zona en donde se puede encargar que lleguen los insumos y materia prima, al igual que la ruta 36 mencionada en el apartado de medios de transporte. En el caso del Parque industrial de Pilar, tiene una ventaja clara debido a que las empresas de este estilo buscan colocarse cerca de esta zona para facilitar el acceso a las empresas ubicadas ahí. En el caso de Avellaneda, hay un puerto en la zona en donde se puede encargar que lleguen los insumos y materia prima, al igual que la ruta 36 mencionada en el apartado de medios de transporte.
- Cercanía de Mercado consumidor: el análisis es parecido a las fuentes de abastecimiento/proveedores. En Avellaneda estás en una zona muy cercana a capital federal respecto a las otras alternativas, además de contar con acceso a rutas provinciales. En el parque industrial Pilar también se tiene accesos a las rutas, pero está más alejado del centro de la ciudad. Escobar está mucho más alejado que las otras 2 alternativas a CABA y, a pesar de tener acceso a rutas y puertos, el transporte se puede hacer más caro.
- Valor y disponibilidad de terrenos: para el proyecto es necesario un espacio de 450 m2 teniendo en cuenta la planta, las oficinas y las instalaciones de servicios (baños, por ejemplo). En el parque industrial de Pilar hay espacios para naves industriales de gran escala como de pequeña escala, siendo un lugar muy valorado y por lo tanto muy caro, este también siendo el caso de Escobar. En el caso de Avellaneda, hay terrenos más baratos que se adecuan a las necesidades del proyecto.
- Disponibilidad de energía eléctrica: En este punto las tres ubicaciones estudiadas poseen un buen servicio en cuanto a disponibilidad de Energía Eléctrica. En el caso de Pilar los cortes de servicios no suelen ser frecuentes, adicionalmente de que en el caso de Pilar, las industrias ubicadas ahí tienen servicios de energía de respaldo. Para Escobar el servicio de luz está dado por Edenor y para Avellaneda el servicio de luz está dado por Edesur. Históricamente, es más usual que Edesur tenga 8,1 cortes de luz anuales con 16,4 horas de interrupción al año y Edenor 3,5 cortes de luz al año con 8,7 horas de interrupción anual.
Requerimietos | ponderación | Parque industrial de Pilar | puntaje | Avellaneda | puntaje | Escobar | puntaje | ||||
medios de transporte | 6 | 4 | 24 | 6 | 36 | 5 | 30 | ||||
disponibilidad de MO | 8 | 5 | 40 | 5 | 40 | 5 | 40 | ||||
cercania de las fuentes de abastecimiento/proveedores | 7 | 9 | 63 | 8 | 56 | 9 | 63 | ||||
Cercania de Mercado consumidor | 7 | 7 | 49 | 8 | 56 | 6 | 42 | ||||
Valor y disponibilidad de terrenos | 8 | 5 | 40 | 7 | 56 | 5 | 40 | ||||
Disponibilidad de energía electrica | 10 | 7 | 70 | 5 | 50 | 6 | 60 | ||||
Valuación | 286 | 294 | 275 |
El lugar físico en el que se realizara el proyecto es en un depósito en alquiler en DEAN FUNES 254, Avellaneda, Avellaneda [1]
Tiene 920 m2, varios ambientes para poder hacer las oficinas con los distintos departamentos y baños para el personal. Tiene disponibilidad de servicios de luz, agua y gas.
Definición Técnica del Producto
Planos e Ilustración del conjunto.
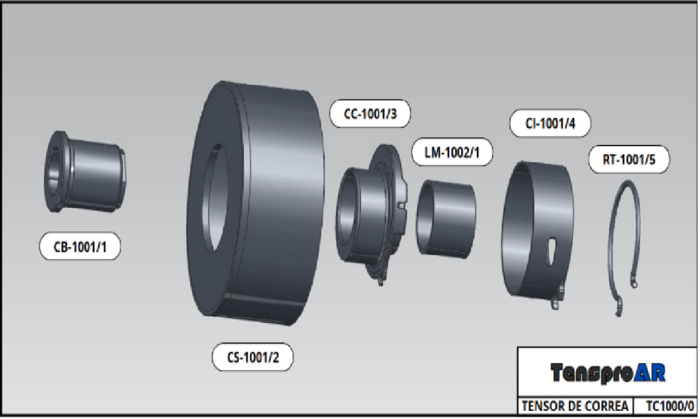
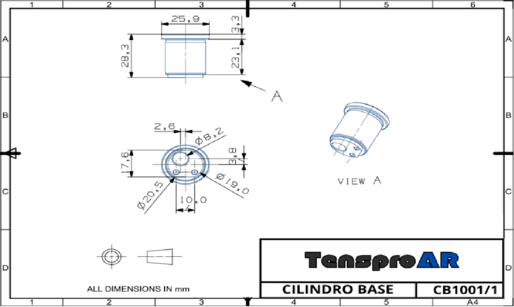
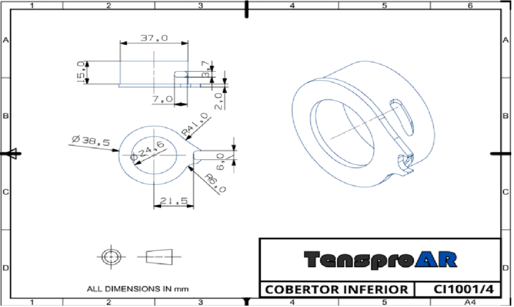

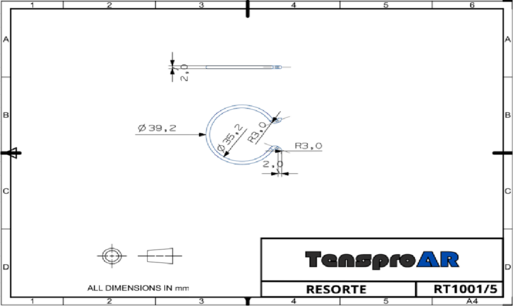
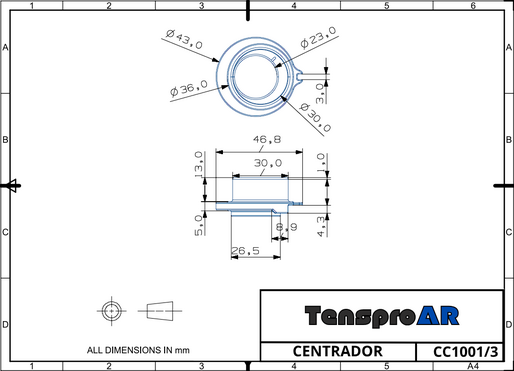
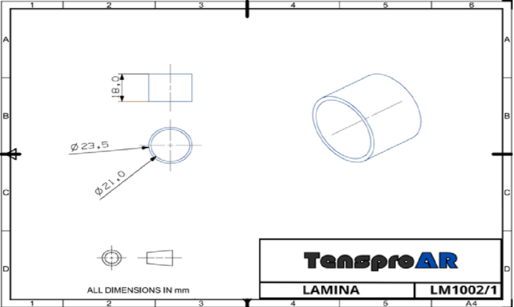
Listado de Materiales
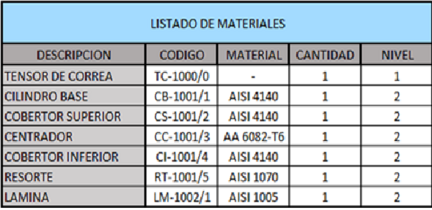
Especificaciones Tecnicas
- Cilindro Base: Acero AISI 4140
- Cobertor superior y cobertor inferior: Acero AISI 4140
- Lámina Moldeable: AISI 1005
- Centrador: Aluminio AA 6082-T6
- Resorte: AISI 1070
La carga maxima del resorte es de 250 N. Es un tipo de resorte a Torsion de instalación manual.
Acabado superficial fino - Ra 2
Recorrido de giro: +/- 30°
Normas aplicables
ISO 9001 – Gestión de Calidad: Establece un sistema para garantizar la calidad del producto y la mejora continua de los procesos. Asegurando la trazabilidad, control en cada etapa productiva y satisfacción del cliente. Es la base para certificar el profesionalismo en la fabricación.
IATF 16949 – Calidad Automotriz: Es una norma específica para proveedores del sector automotriz. Exige trazabilidad total, control de riesgos y documentación técnica (como FMEA y PPAP). Permite acceder a clientes del rubro automotor bajo altos estándares.
Norma de Materiales: AISI 4140 - AISI 1005 - AISI 1070 - AA 6082/T6
ISO 2859-1 – Muestreo para inspección por atributos: Establece planes de muestreo para inspeccionar lotes mediante atributos (apto/no apto). Permite decidir cuántas piezas inspeccionar y cuántas fallas se aceptan según el nivel de calidad deseado (AQL).
ISO 14001 – Gestión Ambiental: Define cómo minimizar el impacto ambiental en la producción. Exige control de residuos, eficiencia energética y cumplimiento legal.
Plan de ensayos
- Ensayo dimensional: Se realizan controles sobre todas las dimensiones críticas del tensor, tales como diámetros, longitudes, posiciones relativas de los componentes. Las mediciones se efectúan mediante instrumentos de precisión como calibres, micrómetros, relojes comparadores y calibres pasa no pasa o de posición por herraduras.
- Ensayo visual: Se verifica visualmente que el tensor esté completamente en condiciones.
- Ensayo funcional: Permiten verificar que el tensor cumpla su función correctamente una vez ensamblado. Se incluye la prueba de funcionamiento en banco, donde se analiza el comportamiento del conjunto bajo condiciones simuladas de trabajo. También se realizan ensayos de precarga del resorte y pruebas de ruido. También existen ensayos de ciclo de vida, simulando el comportamiento del tensor ante miles de ciclos de trabajo. El mismo se realiza en la planta del cliente, para corroborar en conjunto su funcionamiento.
- Ensayo de materiales: Se verifican las propiedades del material base y de los tratamientos aplicados. Se realiza un control de dureza (Rockwell) para confirmar que se alcanzaron los valores esperados tras los tratamientos térmicos. De todas formas, el material viene con un certificado de calidad, es por ese motivo que no se les realiza este ensayo a todos los lotes.
- Acondicionamiento del Producto: Se arregla con el cliente para el acondicionamiento del producto terminado, ya que se puede colocar en una caja de madera lo que sería “a granel” o se puede entregar el producto dentro de una caja de cartón con su etiquetado correspondiente para la venta directa del producto.
Definición del Proceso de Producción
Diagrama de Flujo de Fabricación y Control. Cursogramas gráficos o analíticos.
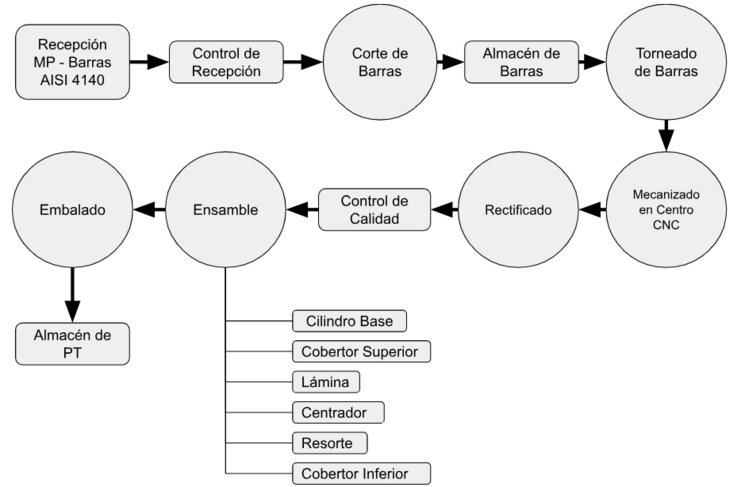
Cursograma analítico del tensor de correas
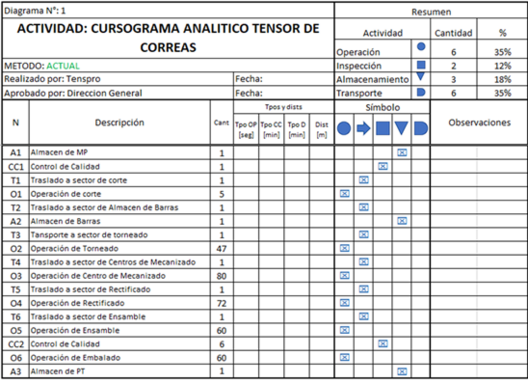
- Corte de Barra: El proceso comienza con la operación de corte, el mismo se realiza con una sierra sin fin semiautomática para metales. La capacidad de la sierra son 5 barras/hora de un acero AISI 4140, de 6000 mm de largo y 31 mm de diámetro. Donde cada barra es fraccionada en 6 pedazos iguales.
- Torneado: Como segunda operación se dispone del torneado, donde la barra de 1000mm entra y salen las piezas con su longitud definida. El proceso es automático, se coloca la barra en el torno CNC y salen las piezas con sus respectivas dimensiones basadas en el plano por la cinta transportadora, la máquina posee una capacidad es de 48 piezas/hora.
- Centro de Mecanizado (CNC): La tercera operación es el mecanizado en centros CNC, las piezas se colocan en un dispositivo y las herramientas atacan las piezas de forma horizontal, dándole la forma y dimensiones deseadas, de manera repetitiva y precisa. El centro tiene una capacidad de 80 piezas/hora.
- Rectificado en Torno: Posteriormente las piezas irán a otro torno CNC, el cual se encargará del rectificado de las piezas, donde se mejora la precisión dimensional y el acabado superficial, dando la rugosidad deseada en la pieza. La capacidad del rectificado es de 72 piezas/hora.
- Ensamble en Prensa: La próxima operación es el ensamble, donde unen las distintas partes del tensor de forma precisa y segura, utilizando una prensa hidráulica que asegura el ajuste de los componentes. Donde la prensa tiene una capacidad de 60 p/h.
- Embalado: Por último, se procede al embalaje de las piezas, salen de la prensa y se depositan en una caja de madera la cual es dada por el cliente.
Determinación de las máquinas e instalaciones
Especificaciones técnicas de las máquinas (capacidades, tamaño de lotes, tiempos).
Tornos Haas - ST 10 (2 unidades)
Peso: 3585 kg
Dimensiones: 320 cm x 178 cm x 206 cm
Diámetro Máximo de trabajo: 419 mm
N° de potes en magazine: 12
Velocidad del Husillo: 6000 rpm
Consumo de energía: 11,2 kWh
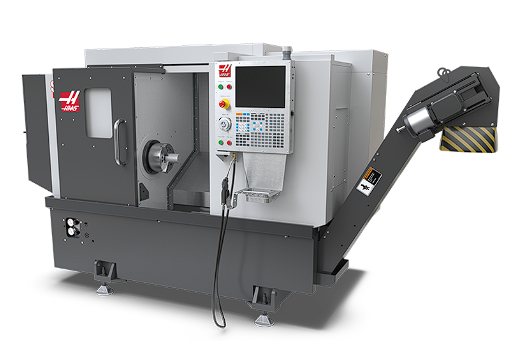
Centro CNC - Okuma MB4000
Peso: 9500 kg
Dimensiones: 242 cm x 470 cm x 265 cm
Tamaño de mesa: 400 x 400 mm
Velocidad de Husillo: 15000 rpm
N° de potes en magazine: 48
Consumo de energía: 26 KwH
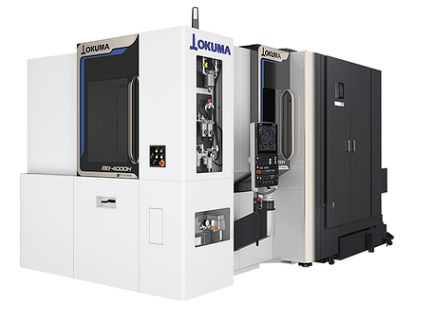
Sierra Sin Fin Cutmac S125:
Peso: 75 kg
Dimensiones: 104 cm x 94 cm x 51 cm
Diámetro Máximo de trabajo: 125 mm
Sistema de bajada: Hidráulico
Consumo de energía: 750 Wh
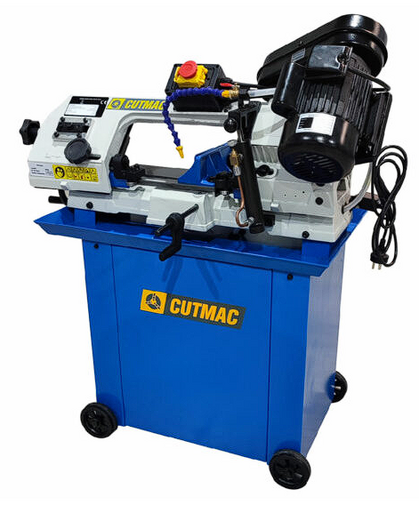
Prensa Hidráulica de Mesa - Torin
Peso: 50 kg
Dimensiones: 68 cm x 45 cm x 107 cm
Área de trabajo: 420 mm x 333 mm x 175 mm
Capacidad de presión: 10 tn
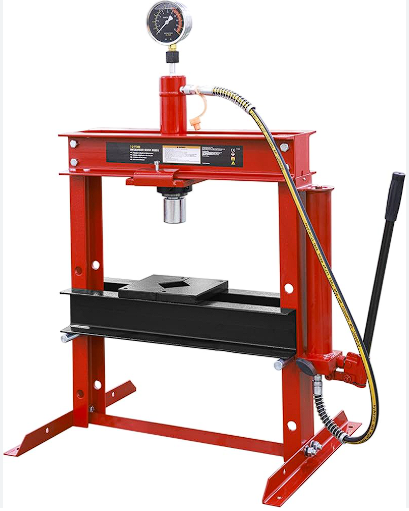
Mantenimiento y medios de control (máquinas, tareas, etc.). Descripción de los sistemas de seguridad (incendios, accidentes, etc.)
En el sistema de seguridad contra incendios la planta cuenta con matafuegos ABC distribuidos estratégicamente, en general cercanos a tableros eléctricos, estaciones de trabajo con riesgo de chispas y accesos principales. Todos los matafuegos están señalizados, así como también los sistemas de evacuación. Existen alarmas contra incendios las cuales deberán ser activadas manualmente en botones repartidos en la planta, debidamente señalizados.
Con respecto a la electricidad, se dispone de disyuntores y cableado puesta a tierra de máquinas y tomacorrientes.
Dentro de la planta el personal deberá tener los equipos de protección personal, obligatoriamente, zapatos de trabajo con puntera de acero, anteojos de protección y protección auditiva (los guantes no son obligatorios al menos que se encuentre trabajando). Además se cuenta con un sistema de entrada y salidas a la planta para mantener la seguridad de la misma, que trabaja en conjunto con un sistema de vigilancia a través de cámaras de seguridad.
Para la seguridad en maquinaria, se disponen de botones hongos para las paradas de emergencia, a su vez tienen lock out en sus puertas y cobertores en su zonas de trabajo.
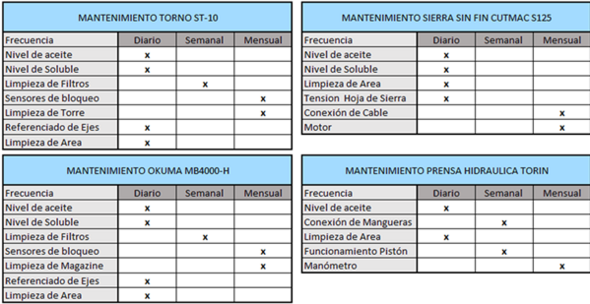
BALANCE ANUAL DE MATERIAL. PRODUCCIÓN SECCIONA
De acuerdo con la tecnología adoptada, la actividad industrial se desarrollará a través de 5 secciones: Sierra eléctrica, torneado, centro CNC, Torno Rectificado y Prensa hidráulica.
Los desperdicios seccionales:
SECCIONES OPERATIVAS | DESPERDICIOS | ||
RECUPERABLE | NO RECUPERABLE | TOTAL (dato en %) | |
sierra electrica | 0,00% | 100,00% | 0,25% |
torneado | 0,00% | 100,00% | 45,48% |
centro CNC | 0,00% | 100,00% | 16% |
Torno Rectificado | 0,00% | 100,00% | 0 |
Prensa hidraulica | 0,00% | 100,00% | 0 |
Los desperdicios se venden como viruta, por eso son desperdicios no recuperables, porque no se reingresan al proceso productivo.
SECCIONES OPERATIVAS | ALIMENTACIÓN | DESPERDICIOS | PRODUCCIONES SECCIONALES | |
RECUPERABLE | NO RECUPERABLE | |||
sierra electrica | 1482 | 0 | 4 | 8871 |
torneado | 8871 | 0 | 4034 | 154762 |
centro CNC | 154762 | 0 | 24762 | 130000 |
Torno Rectificado | 130000 | 0 | 0 | 130000 |
Prensa hidraulica | 130000 | 0 | 0 | 130000 |
TOTALES | 284575 | 0 | 154574 | 130000 |
Estos datos corresponden a la producción del último año, dado a que es la más grande de todos los demás años.
En la sierra eléctrica se introduce una barra de acero de la cual salen 6 barras por cada una, que después serán ingresadas en el torneado. El 8871 responde a la cantidad de barras que salieron de la sierra y el 4 corresponde a la cantidad de materia prima perdida.
Del torneado, por cada barra que se ingresa (barra que salió de la sierra) salen 32 piezas que avanzan en el proceso productivo. El 4034 representa la cantidad de barras perdidas en el proceso, y 154762 representan la cantidad de piezas que se puede hacer con el material que salió del torneado. Los demás números del cuadro expresan la cantidad de piezas que se pueden hacer con ese material.
El desperdicio total que se expresa como no recuperable responde a la cantidad de piezas que se podrían realizar con ese material en caso de estar en condiciones de incorporarse al proceso productivo (más tarde ese desperdicio se vende).
Lo que se ingresa es lo que se produce porque ningún desperdicio es recuperable y el porcentaje de desperdicio operativo en función de la producción es de un 118,9%.
RITMO DE TRABAJO
Se trabaja 5 días a la semana, con 2 turnos de 8 horas. Se tiene en cuenta 15 días de vacaciones y 10 días feriados.
Datos: 260 días al año- 10 días de feriados- 15 días de vacaciones= 235 días al año.
a) horas anuales trabajadas por las máquinas:
235 días * 16 horas diarias= 3760 horas anuales.
b) horas trabajadas por cada operario: 3760.
CAPACIDAD REAL ANUAL DE LA MAQUINARIA TIPO DE CADA SECCIÓN OPERATIVA
Se supone en cada sección operativa un solo tipo de máquina.
SECCIONES OPERATIVAS | Capacidad (p/h) | maquina por hora | horas activas en el año | capacidad teorica anual | rendimiento operativo | capacidad real | |
sierra electrica | 5,0 | 960,0 | 3760,0 | 3609600,0 | 75,00% | 2707200 | |
torneado | 1,5 | 48,0 | 3760,0 | 180480,0 | 90,00% | 162432 | |
centro CNC | 80,0 | 80,0 | 3760,0 | 300800,0 | 85,00% | 255680 | |
Torno Rectificado | 72,0 | 72,0 | 3760,0 | 270720,0 | 95,00% | 257184 | |
Prensa hidraulica | 47,0 | 47,0 | 3760,0 | 176720,0 | 90,00% | 159048 |
La capacidad de cada máquina está expresada en la cantidad de piezas producidas por hora.
DETERMINACIÓN DE LA CANTIDAD DE MÁQUINAS OPERATIVAS POR SECCIÓN, CAPACIDAD REAL ANUAL DE CADA SECCIÓN Y SU APROVECHAMIENTO EN RELACIÓN AL PROGRAMA DE PRODUCCIÓN
SECCIONES OPERATIVAS | PROGRAMA ANUAL DE PRODUCCIÓN | CAPACIDAD REAL | CANTIDAD DE MAQUINAS NECESARIAS | CANTIDAD DE MAQUINAS NECESARIAS (REDONDEADO) | CAPACIDAD REAL | APROVECHAMIENTO |
sierra electrica | 8871 | 2707200 | 0,003276716755 | 1 | 2707200 | 0,33% |
torneado | 154762 | 162432 | 0,9527818533 | 1 | 162432 | 95,28% |
centro CNC | 130000 | 255680 | 0,5084492337 | 1 | 255680 | 50,84% |
Torno Rectificado | 130000 | 257184 | 0,5054758464 | 1 | 257184 | 50,55% |
Prensa hidraulica | 130000 | 159048 | 0,8173651984 | 1 | 159048 | 81,74% |
El cuello de botella es el torneado con un grado de aprovechamiento del 95% y con una capacidad real de 162432 piezas por año.
Evolución de la mercadería
EVOLUCIÓN DE LA PRODUCCIÓN
año | produccion anual | producción mensual |
1 | 26000 | 2261 |
2 | 52000 | 4522 |
3 | 78000 | 6783 |
4 | 104000 | 9043 |
5 | 130000 | 11304 |
Este cuadro representa la cantidad a producir año a año y la cantidad mensual que se debe producir año a año.
El periodo de puesta en marcha llevará 3 meses y después se estará en régimen.
mes | ritmo prod inicio | ritmo prod final | produccion promedio | produccio mensual promedio | produccion propuesta |
1 | 0,00% | 25,00% | 12,50% | 2261 | 283 |
2 | 25,00% | 50,00% | 37,50% | 2261 | 848 |
3 | 50,00% | 100,00% | 75,00% | 2261 | 1696 |
total | 2826 |
Durante el periodo de puesta en marcha se producirán 2826 piezas. Para poder cumplir con la orden de producción en los siguientes meses se deben producir 23174 piezas más. Mensualmente esto se traduce a 2575 piezas por mes.
DETERMINAR EL STOCK PROMEDIO DE PRODUCTO ELABORADO
La política de stock de producto terminado es tener almacenado lo que se produce en 1 semana del año 1 y se mantendrá constante pero renovado a medida que se desarrolle el ejercicio. Se generará en el 4to mes, con la empresa ya en marcha.
Produccion mensual en el año 1 en regimen. | 2575 | ||
produccion semanal en el año 1 en regimen | 644 | ||
El promedio de producto terminado va de 0 a 644: | 322 |
DETERMINAR LA EVOLUCIÓN DE LAS VENTAS DURANTE LA VIDA ÚTIL DEL PROYECTO
a) ventas del año 1: | 26000 | - | 322 | 25678 |
Del año 2 al 5:
año | ventas |
2 | 52000 |
3 | 78000 |
4 | 104000 |
5 | 130000 |
En estos años no se le resta stock de producto terminado dado a que ya se restó en el año 1.
DETERMINAR EL CONSUMO DE MATERIA PRIMA PARA EL PROGRAMA DE PRODUCCIÓN Y FORMACIÓN DE LA MERCADERÍA EN CURSO Y SEMIELABORADA
Durante el periodo de puesta en marcha hay un 25% de desperdicio adicional. Dado a que el presupuesto de la materia prima está dado por el cliente, estos desperdicios extras se consideran como ya pactados y aprobados por el cliente.
El ciclo de elaboración del producto es de 5 días de trabajo, por lo tanto se cuentan con:
Año 1: El consumo de materia prima en este año está destinado a la producción realizada y a la formación de stock de producto terminado.
Desperdicio de la puesta en marcha= 2826 * 1,18*1,25 = 4168 piezas.
meses restantes= 23174 * 1,18 = 27345 piezas
4168 + 27345 = 31514 piezas
volumen de producción realizada: 26000
real utilizado= 31514
desperdicio real= 5514 piezas
Año 2 al 10: El consumo de materia prima es exclusivamente destinado a la producción.
DETERMINAR ELCONSUMO DE MATERIA PRIMA PARA EL PROGRAMA DE PRODUCCION
Durante el periodo de puesta en marcha hay un 25% de desperdicio adicional. Dado a que el presupuesto de la materia prima esta dado por el cliente, estos desperdicios extras se consideran como ya pactados y aprobados por el cliente. El desperdicio del proceso es después revendido como viruta, con lo cual no se vuelve a introducir en el proceso. Por lo tanto, no es recuperable.
Año 1: El consumo de materia prima en este año está destinado a la producción realizada y a la formación de stock de producto terminado.
Producción de la puesta en marcha= | 2826 | x | 147,50% | = | 4168 | piezas |
Como para fabricar cada pieza se cuenta con un 118% de desperdicio, si le sumas un 25% da como resultado 147,5% de desperdicio.
meses restantes | 23174 | piezas | las cuales necesitan: | 27345 | piezas |
Los meses restantes se necesita fabricar 23174 piezas. Teniendo en cuenta el desperdicio, se necesita material para fabricar 27345 piezas para cumplir con la orden de producción.
Esto da un total de 31514 piezas en material el primer año. Esto implica que hay un desperdicio de 5514 piezas en el primer año.
Año 2 al 10: El consumo de materia prima es exclusivamente destinado a la producción.
Año | producción anual | desperdicio |
2 | 52000 | 61360 |
3 | 78000 | 92040 |
4 | 104000 | 122720 |
5 | 130000 | 153400 |
total | 429520 |
Estos números están expresados en piezas fabricadas.
DETERMINAR EL STOCK PROMEDIO DE MATERIA PRIMA Y EL PROGRAMA DE COMPRAS
*Aclaración: la materia prima es suministrada por los clientes para asegurarse de la calidad del producto. Esta es una práctica común en el rubro.
*Aclaración 2: la materia prima no tiene problemas de estacionalidad.
Variación del stock de materia prima durante el año y programa de compras
AÑO 1
al fin del mes | stock | compra | al fin del mes | stock | compra |
enero | 283 | 283 | julio | 2575 | 2575 |
febrero | 848 | 848 | agosto | 2575 | 2575 |
marzo | 1696 | 1696 | septiembre | 2575 | 2575 |
abril | 2575 | 2575 | octubre | 2575 | 2575 |
mayo | 2575 | 2575 | noviembre | 2575 | 2575 |
junio | 2575 | 2575 | diciembre | 2575 | 2575 |
Estos números representan la cantidad de piezas que se realizan con la materia prima a comprar.
Para los años 2-5 se sigue el mismo concepto de "comprar" lo que se planea vender ese mes
Stock promedio del año 1= (283+2575) /2 = 1429.
EL CUADRO RESUMEN DEL PROGRAMA GENERAL DE EVOLUCIÓN
año | 1 | 2 | 3 | 4 | 5 |
ventas | 25678 | 52000 | 78000 | 104000 | 130000 |
producción | 26000 | 52000 | 78000 | 104000 | 130000 |
Desperdicio no recuperables | 5514 | 61360 | 92040 | 122720 | 153400 |
consumo de materia prima | 165 | 594 | 891 | 1188 | 1482 |
compra de materia prima | 165 | 594 | 891 | 1188 | 1482 |
*aclaración3: por cada pieza fabricada necesito 0,00524 barras que ingresan a la alimentación. De esa conversión surgieron los números de consumo de materia prima y compra de materia prima.
*aclaración 4: el consumo de materia prima y compra de materia prima está expresado en cantidad de barras de metal que ingresan a la alimentación.
Determinación del Personal.
Organigrama de toda la empresa
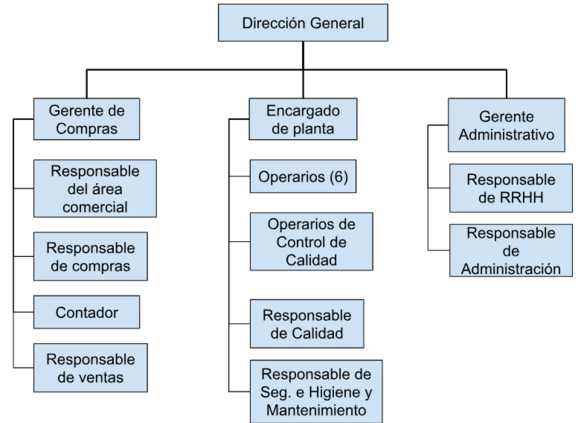
Descripción de los Puestos de Trabajo
- Dirección General: responsable máximo de la empresa, encargado de establecer los objetivos estratégicos, tomar decisiones operativas y/o de inversiones y coordinar los sectores para asegurar el cumplimiento de la misión y visión organizacional. Supervisa directamente a las tres áreas claves: Compras y Comercial, Producción y Administración.
- Gerencia de Compras / Comercial: El puesto es ocupado por una sola persona, la cual es responsable del abastecimiento, compras de insumos y materias primas, así como también del vínculo con proveedores estratégicos. Además, cumple funciones en el área comercial, siendo responsable tanto de la gestión de ventas como del seguimiento de clientes, presupuestos y contratos. Colabora con tareas contables asociadas al ciclo de compras-ventas, apoyando al área administrativa en lo que respecta a documentación fiscal, pagos y cobranzas, donde se reporta directamente a Dirección General.
- Gerencia Administrativa: Puesto ocupado por una sola persona, responsable de la gestión administrativa, financiera y de recursos humanos de la empresa. Administra procesos contables básicos, pagos, cobranzas, archivo de documentación, y gestiona el vínculo con entidades bancarias, proveedores de servicios y organismos oficiales. Además, lidera las actividades del área de Recursos Humanos, incluyendo altas de personal, liquidación de sueldos, licencias, y cumplimiento de normativa laboral. Reporta directamente a Dirección General y colabora con la Gerencia de Compras en temas contables.
- Encargado de Planta: Puesto ocupado por una sola persona, donde es responsable operativo del funcionamiento de la planta productiva. Supervisa directamente al equipo de operarios y al operario de calidad, organizando la producción diaria, asignando tareas, controlando tiempos y asegurando el cumplimiento de los estándares de calidad. Además, tiene bajo su responsabilidad las funciones de mantenimiento general, seguridad e higiene y el área de calidad del producto. Actúa como nexo entre el sector productivo y la Dirección General, informando avances, desvíos y necesidades del área.
- Operarios (6): Ejecutan tareas operativas en las distintas etapas del proceso productivo: corte, mecanizado, rectificado, ensamblado y embalado. Trabajan bajo las instrucciones del Encargado de Planta, respetando normas de seguridad, procedimientos estandarizados y tiempos asignados. Cada operario puede desempeñarse en más de un puesto dependiendo de la carga de trabajo y su capacitación. Se genera una matriz de polivalencia entre empleados, para que cada uno pueda ocupar el lugar del otro.
- Operario de Calidad (1): Tiene a su cargo la inspección de piezas durante y al final del proceso productivo. Se asegura de que los productos cumplan con las tolerancias, dimensiones y características establecidas en los planos o especificaciones técnicas. Además, colabora con el Encargado de Planta en temas de control de procesos, trazabilidad y documentación de calidad. También participa en tareas relacionadas con seguridad e higiene industrial.
Calificación y Formación necesaria de los Operadores.
Formación de operarios, los mismos poseen una formación técnica y una capacitación práctica continua, para garantizar el cumplimiento y la eficiencia operativa, los mismos disponen de cursos CNC básicos para comenzar a trabajar en máquina y luego ir ganando experiencia en la misma, así como también en el área de corte y ensamble. Tener una familiaridad con las máquinas herramientas y buen manejo de instrumentos de medición es altamente necesario. Adicionalmente los operadores tienen conocimientos básicos en seguridad industrial, donde se incluye una capacitación externa de técnico en seguridad e higiene y una persona capacitada anti-incendios. Sumado a eso cada operario está capacitado para el uso adecuado de elementos de protección personal (EPP).
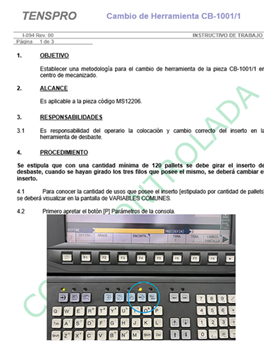
Listado de Equipos Auxiliares, Muebles y Útiles
Producción
Para el área de producción se utilizan ganchos con poleas y motor para levantar los dispositivos sin fuerza hombre:
- Aparejo Eléctrico Gadnic AP250 Hasta 250kg 550w Gancho Doble y Simple Reforzado
- Taladro Electrico
- Banco de trabajo
- Contenedores de Plastico
- Carretilla de 2 ruedas
- Un clark para descargar material
- Guantes de protección
- Lockers: Para que los empleados guarden sus pertenencias.
- Estanterías metálicas
Calidad
- Máquina de medir 3D ZEISS modelo Accura II: Se usa para medir con extrema precisión las dimensiones de piezas mecánicas o industriales
- Zoller Venturion: es una máquina de medición universal
- Calibres de 150 mm
- Micrómetro
- Equipos UD
Oficinas
- Escritorios amplios con espacio para colocar la computadora, periféricos y papeles
- Sillas ergonómicas regulables y cómodas para los trabajadores que pasan mucho tiempo sentados.
- Estantería y armarios para almacenar documentación en papel y carpetas
- Computadoras, impresoras, proyector y pizarra para presentaciones y reuniones y periféricos.
- Equipos de cocina: Microondas, heladera, cafetera y dispenser de agua.
Anteproyecto de Planta
Plano de la Planta mostrando la distribución de las distintas áreas (Producción, Administración y Comercialización).
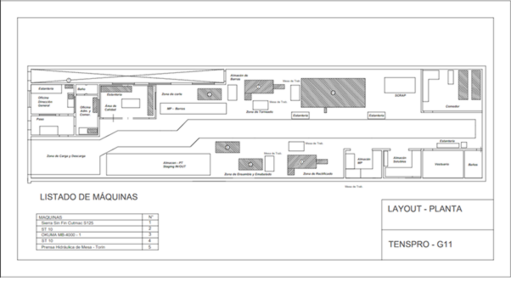
Plano mostrando el recorrido de los materiales.
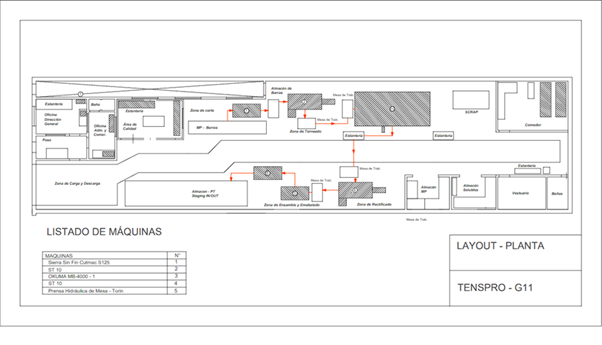
Cronograma de ejecución
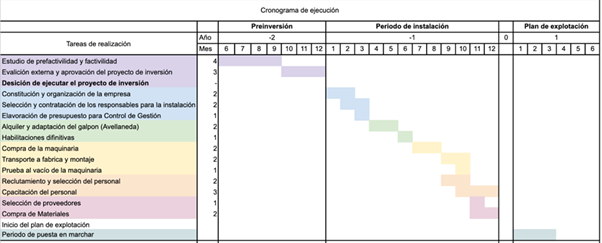