Diferencia entre revisiones de «2020/Grupo5/DimensionamientoFisico»
(No se muestran 58 ediciones intermedias de 5 usuarios) | |||
Línea 1: | Línea 1: | ||
== Determinación de la Localización == | == Determinación de la Localización == | ||
Para determinar la localización de nuestra organización realizamos una matriz de localización. En la misma se enumeraron una serie de factores, a la cual se les asigno un nivel de importancia (siendo 1 poca importancia y 5 mucha importancia). Luego se le asigno un valor de disponibilidad, siendo nuevamente 1 para poca disponibilidad o desfavorable y 5 para mucha disponibilidad y favorable. | |||
A continuación se adjunta la matriz con sus resultados: | |||
[[Archivo:Matrizzzzzzzzzz.jpg|centro|miniaturadeimagen|955x955px]] | |||
Dentro de los factores que creemos claves en el proyecto se encuentra la cercanía a proveedores y al mercado. Los mismos nos abarataran los costos de logística en el traslado (en especial el traslado de caños y columnas). Dentro de los proveedores, la alternativa Pompeya presenta una ventaja debido a que uno de los proveedores se encuentra en las cercanías, pero la zona de Quilmes presenta ventajas en cuanto al acceso al mercado y al traslado de los productos. Por ultimo, no queremos dejar de mencionar la carga impositiva. Este es un factor que suele ser de gran peso para las empresas en Argentina. Para el caso particular, creemos que las alternativas de Quilmes y Gral. Las Heras tendrán ventajas debido a que cuentan con parques industriales en dichas jurisdicciones. | |||
En especial, el factor mano de obra especializada no posee un valor de importancia muy elevado debido a que nuestro proceso solo tiene como requerimiento especial la contratación de soldadores certificados nivel II. El resto de los operarios deberían presentar conocimientos mas del tipo técnico que no creemos sea algo difícil de encontrar. | |||
Factores tales como los climáticos, topografía o el tratamiento de desechos no hacen demasiada importancia a nuestro proyecto por lo que presentan valores relativamente mas bajos que el resto. Las razones particulares son que el clima no afecta nuestras actividades de gran manera al igual que no creemos que la topografía sea un gran problema en las áreas mencionadas como alternativas. El tratamiento de desechos tampoco debería ser de gran problema debido a que nuestro proceso no presenta cantidades importantes de residuos, efluentes y/o emanaciones. | |||
Como resultado de la matriz de localización, llegamos a la conclusión de que nuestra empresa se ubicará en la zona de Quilmes. Dicha alternativa cuenta ventajas en cuanto a la cercanía de mercados y proveedores. También cuenta con un complejo industrial donde podríamos analizar instalarnos. Es una zona accesible con los medios de transportes y creemos no tiene grandes dificultades en el acceso a operarios calificados. | |||
== Definición Técnica del Producto == | == Definición Técnica del Producto == | ||
=== '''Planos''' === | |||
A continuación adjuntamos un plano hecho con la herramienta AutoCAD. El mismo muestra las 4 secciones de caños con sus largos y espesores correspondientes. | |||
[[Archivo:PLANO-GENERAL-.jpg|centro|miniaturadeimagen|926x926px|Plano Columna Luminaria Unidireccional.]][[Archivo:ZOOM-SECCION-SUPERIOR.jpg|centro|marco|Zoom tramo superior.]] | |||
=== '''Listado de Materiales''' === | |||
=== '''Especificaciones Técnicas''' === | |||
[[Archivo:Bomfot.jpg|centro|miniaturadeimagen|1075x1075px]] | |||
[[Archivo:Arboleo modificado.jpg|centro|marco]] | |||
=== '''Normas Aplicables''' === | |||
Las normas que aplicarán en nuestro producto son las que contempla el Pliego de Especificaciones Técnicas Particulares para Iluminación de Viabilidad Nacional. | |||
Partiendo del poste de acero en sí, que será el producto que fabricaremos, aplican las normas: | |||
* IRAM 2591/2592 e IRAM-IAS U 500 2592 en cuanto a lo referido al material de las columnas de acero. El límite de fluencia mínimo debe ser de 30 kg/mm2 y la carga de rotura mínima de 45 kg/mm2. Se establece el uso en el extremo de los caños un sistema de abocardado en frío para mantener las propiedades originales del acero, mediante una curva de transición suave. También se deben realizar soldados con máquinas semiautomáticas con aporte continuo de alambre y protección gaseosa tipo MIG (Metal Inert Gas), con gas CO2 o argón. El solape de un caño dentro del otro no deberá ser menor a 1,5 veces el diámetro del menor caño. Además se establece que la flecha admisible en la dirección más desfavorable con una carga en el extremo del pescante de 30 kg no excederá del 1,5% de la longitud desarrollada en la parte exterior del empotramiento. | |||
* Reglamento CIRSOC 301 el cual establece que Las columnas deberán ser dimensionadas para soportar un peso mínimo del artefacto de 25 kg, más los efectos producidos por el viento máximo de la zona, considerando una superficie efectiva del artefacto de 0,28 m2 en el plano de la columna y 0,14 m2 en el plano normal a la misma. | |||
* IRAM 2619/2620 que establece lo referido a los ensayos solicitados y el dimensionamiento de los caños. Para el control de deformación se debe ensayar hasta el 5% de la cantidad de las columnas por partida. En las columnas rectas y/o con brazo se aplicará una carga vertical equivalente a una vez y media (1,5) la utilizada para las hipótesis de cálculo. Para su aceptación, con estas cargas, no deberán sufrir deformaciones permanentes de ningún tipo. Por el lado del dimensionamiento, el escalonado entre los distintos diámetros tiene que hacerse con una curva de transición, lograda por el procedimiento que se considere más adecuado, observando siempre que la resistencia de conjunto sea la exigida. El coeficiente de seguridad no deberá ser inferior a 2,0. En lo que respecta a las ventanas de inspección, la norma establece que todas las columnas deben poseer una abertura ubicada a una altura de 2,40 m., por encima del nivel de empotramiento de la misma, con una chapa de hierro de 3mm de espesor soldada en el interior de la misma, para soporte del tablero eléctrico de derivación. Tendrá una tapa de cierre metálica a bisagra (anti vandálica) con un tornillo Allen oculto, imperdible; el espesor de la tapa deberá ser no menor a 3 mm. La dimensión de la ventana de inspección, deberá se de 100 mm. x 170 mm. | |||
* IRAM 1042 referida a la protección de la estructura. Establece que se debe aplicar sobre la columna un espesor mínimo de cuarenta micrones (40 μm) de antióxido al cromato de zinc en toda su extensión e interiormente desde su extremo inferior hasta una altura de 0,30 m por encima de la longitud de empotramiento. El color final de la columna se establecerá con dos manos de esmalte sintético color blanco. | |||
Por el lado de la luminaria, más allá que no seamos nosotros quienes la fabriquemos (la adquirimos de terceros), tendremos que cumplir ciertas normas a la hora de tratar con nuestros clientes, las cuales exigiremos a nuestros proveedores. Estas son: | |||
* IRAM-AADL J 2022-1 es la norma referida a las condiciones fotométricas de los artefactos de iluminación. Se debe presentar documentación de las condiciones fotométricas de la luminaria. La documentación deberá acompañarse con una copia legalizada de las curvas y los protocolos de ensayo del artefacto ofrecido, para la lámpara /unidad de módulos led con la cual funcionará. Los protocolos de ensayo fotométricos y documentación adicional que serán exigidos son: | |||
# Curvas Isolux. | |||
# Curvas Isocandelas. | |||
# Curvas Polares Radiales o de Distribución. | |||
# Curvas de Utilización. | |||
# Marca y modelo: memoria descriptiva del elemento, detalles constructivos, materiales empleados, forma de instalación, conservación; planos a escala conveniente, de planta, alzado y perspectiva del elemento; distribución fotométrica, flujo luminoso total emitido por la luminaria y flujo luminoso emitido al hemisferio superior en posición de trabajo. | |||
# Potencia nominal asignada y consumo total del sistema. | |||
# Eficiencia de la luminaria (lm/W) y vida útil estimada para la luminaria en horas de funcionamiento (el parámetro de vida útil se calculará de modo que transcurridas las horas señaladas, el flujo luminoso sea del 80% respecto del flujo total emitido inicialmente). | |||
# Gráfico sobre el mantenimiento lumínico a lo largo de la vida de la luminaria, indicando la pérdida de flujo cada 4000 horas de funcionamiento. | |||
# Rango de temperaturas ambiente de funcionamiento sin alteración en sus parámetros fundamentales. Se deberán aportar, mediciones sobre las características de emisión luminosa de la luminaria en función de la temperatura ambiente exterior, indicando al menos de -10°C a 50°C. | |||
# Grado de hermeticidad de la luminaria completa. | |||
# Declaración de Conformidad y Expediente Técnico o documentación técnica asociada expedida por Laboratorio acreditado. | |||
Adicionalmente, por lo respectivo a luminaria LED se deberá presentar: | |||
# Marca, modelo y datos del fabricante del LED / Módulo LED; potencia nominal y flujo luminoso emitido por cada LED individualmente y por el módulo completo. | |||
# Curvas de duración de vida, en horas de funcionamiento, en función de la temperatura de unión. Índice de reproducción cromática; temperatura de color (cuando el LED o el módulo LED pueda alimentarse a diferentes corrientes o tensiones de alimentación, los datos anteriores se referirán a cada una de dichas corrientes o tensiones). | |||
# Temperatura máxima asignada. | |||
# Vida útil estimada de cada LED y del módulo LED en horas de funcionamiento. | |||
Por último, en lo que respecta a el cableado (conductores eléctricos) encontramos las siguientes normas: | |||
* IRAM 2281-8 y IRAM 2022 que indican que las columnas deberán contar con una puesta a tierra de seguridad. El cable de protección de puesta a tierra de las columnas, será, en todos los casos, de cobre, de 35 mm2 de sección mínima con un diámetro mínimo del alambre de 1,8 mm. | |||
* IRAM 2178 establece que los conductores podrán ser unipolares o multipolares, con aislación de PVC, de cobre flexible o rígido, aptos para trabajar a una tensión de 1,1 kV. Su sección no será inferior a 4mm2. | |||
=== '''Características Condición del Producto''' === | |||
Las condiciones del producto son aquellas presentes en las especificaciones del cliente. Al ser un producto de uso en el servicio público de iluminación, las condiciones son las que se encuentran presentes en las normas expuestas del punto anterior. | |||
=== '''Plan de Ensayos''' === | |||
El ensayo que nos corresponde es el de torsión, según la Norma IRAM AADL J2021. Los componentes eléctricos vienen de fábrica ya testeados. | |||
Se debe ensayar, para una partida, una muestra del 5%. Se trata de aplicar una carga vertical equivalente a una vez y media la utilizada para la hipótesis de cálculo sobre el extremo máximo horizontal del brazo de la columna. | |||
Para la aceptación, con estas cargas la columna no debe sufrir deformaciones permanentes de ningún tipo. | |||
Se ensayarán las columnas según lo exijan los clientes: no todos requieren tener el estudio realizado para sus aplicaciones, pero estimaremos que alrededor del 10% de los clientes pedirán que se realice. Además, el estudio será tercerizado, y lo realizará la empresa | |||
=== '''Acondicionamiento del Producto''' === | |||
Por las magnitudes del producto, y dado que su principal función es iluminar en espacios al aire libre, hace que no requiera de packaging o envoltorios protectores para su disposición y despacho. | |||
Solamente se colocarán sobre tacos al transportarse, y entre los tacos y columnas se colocará alfombra para evitar que se puedan dañar entre ellas al moverse. | |||
== Definición del Proceso de Producción == | == Definición del Proceso de Producción == | ||
=== '''Diagrama de Flujo''' === | |||
[[Archivo:Diagrama flujo nuevo.jpg|centro|alt=|marco]] | |||
=== '''Cursograma Sinoptico''' === | |||
[[Archivo:Cursograma modificado.jpg|centro|miniaturadeimagen|1220x1220px]] | |||
=== '''Descripción de Cada Etapa''' === | |||
* Cortado: | |||
Una vez que contamos con los materiales en el depósito de MP, podremos comenzar con el proceso productivo. En la primer etapa del mismo se procede a realizar el cortado de los caños de los distintos diámetros de forma transversal delimitando cada uno de ellos a su medida establecida. Para trasladar estos caños los cuales cuentan con un gran peso, se opta por la utilización de un puente de grúa para facilitar esta tarea. | |||
En la sierra se cuenta con unos topes los cuales nos permiten marcar correctamente el punto donde se realiza el corte. Esta actividad es relativamente fácil y suele llevar poco tiempo. Simplemente Se reduce de tamaño los largos caños de cada uno de los diámetros uno a la vez. Es decir, que una vez dispuesto en la máquina el caño de diámetro mayor (168mm) realizarse sobre el mismo todos los cortes que me permita en caño respetando siempre la longitud establecida para dicho diámetro, una vez que concluyó con los cortes de dicho diámetro puedo pasar a realizar la actividad en el siguiente tamaño de caño. | |||
* Aboquillado: | |||
Esta etapa del proceso será nuestra diferenciadora de nuestro ciclo productivo respecto a la competencia. La actividad de aboquillado hace referencia trabajar un extremo del caño de forma tal que este obtenga una forma más cónica. Esto se realiza para facilitar la unión entre los caños de distintos diámetros. En el caso de nuestro proceso este paso se realizará en frío, sin necesidad de calentar la pieza antes del conformado. Al calentar el material se pierden varias propiedades mecánicas, en cambio al conformar un material en frío aumenta la resistencia a la deformación. | |||
En la máquina se cuenta con una prensa que presiona el caño dentro una matriz que permite realizar este proceso con buena terminación y de en poco tiempo en comparación con la diferencia, ya que no hace falta un calentamiento previo. | |||
* Corte de ventana de inspección: | |||
El corte de la ventana de inspección solo se realizará en el caño de mayor diámetro,suele colocarse a una altura de 2,4 m del suelo ( además debo sumarle el 1,5 m que se encuentra). Esta ventana cumple la función de permitir acceso al interior de la columna una vez instalada, para chequear las conexiones y permite la acceso a la chapa soporte donde se hace la fijación de los cables. Este pequeño corte se realizará con plasma, el corte por plasma es un proceso que utiliza una boquilla, con un orificio para la circulación del gas ionizado a altas temperatura, de tal forma que se obtiene un rayo que se puede utilizar para cortar secciones de metales tales como el acero al carbono, acero inoxidable, aluminio y otros metales conductores de la electricidad. Por medio del uso de esta técnica, el arco de plasma funde el metal, y el gas elimina el material fundido. Las dimensiones de la ventana son de aproximadamente 20 cm de y el ancho está dado por el ancho de curvatura de la columna ( el cual suele ser de 12cm) | |||
* Instalación de puesta a tierra: | |||
La puesta a tierra es un sistema que asegura que, ante cualquier falla de aislamiento, las partes metálicas de todo el equipo eléctrico descarguen la corriente eléctrica a tierra, sin afectar al usuario que entre en contacto con el aparato eléctrico, evitando así que sufra una descarga eléctrica. | |||
En nuestro caso la misma se colocará a 30 cm del piso, es decir 1,8 m debido a la parte de la columna que está debajo del suelo. Su colación es realmente sencilla. Solo se debe realizar un pequeño punto de bronce en el exterior de la columna. El mismo será traspasado por un macho el cual formará la rosca necesaria para el paso de un tornillo al interior de la columna el cual será ajustado con una tuerca. Así una vez que se realice el cableado final de la columna en dicho tornillo se pondrá el cable de puesta a tierra. | |||
* Doblado: | |||
Este proceso solo se realizará en el caño de menor diámetro ya que es el que se encontrara más lejos del suelo. En nuestro caso utilizaremos el método de doblado horizontal. La máquina cuenta con soportes que afirman la columna, mientras que un pistón hidráulico presiona con una matriz al caño en una altura determinado. Esta máquina cuenta con unos swich electrónicos que permiten avanzar al pistón hasta una profundidad determinada que nos permitirá obtener el ángulo deseado. El pistón queda algunos segundos presionando al tubo en dicha posición y luego es retirado lentamente. Cabe destacar que los soportes que sostienen la columna no son fijos, y a medida que el caño se dobla estos van rotando acompañó dicho movimiento. | |||
* Soldado: | |||
A continuación se procede a llevar los caños de distintos diámetros a la mesa de soldado. | |||
Aquí se disponen los mismo en la posición que cada uno va a ocupar en la estructura final. Ya que previamente se procedió a realizar el aboquillado a cada extremo de caño en el extremo que conecta con el siguiente caño del diámetro más próximo, se podrá encajar de forma más sencilla cada uno de ellos previo al soldado. | |||
UNn veces dispuestos los 4 caños, se procede a soldar la primera unión de la estructura. la facilidad que brinda la mesa de soldado en esta parte de la operación es que mediante una serie de rodillos permite ir rotando lentamente el conjunto de caños logrando así un movimiento más uniforme al ir soldado. | |||
Una vez concluida la primer unión, se procede a realizar la misma actividad con las otras dos uniones de la estructura. | |||
* Pintado: | |||
El proceso de pintado cuenta con 3 etapas bien definidas: la capa de antióxido, la capa de pintura y la capa de brea paltica solo en el área determinada. | |||
La primer mano que se le aplica a la columna es de antióxido al cromato de zinc, la cual se aplica de forma manual a la totalidad de la estructura. Esta permitirá proteger la columna ante el ataque de agentes externos, permitiendo aumentar la vida útil de la columna. | |||
Próximo a la primera mano de antióxido, se procede a levantar la columna mediante el puente de grúa y dirigirla hacia una pileta de pintura. La columna es sumergida en su totalidad dentro del piletón de pintura, logrando así un mejor acabado y llegar a todas las partes de la estructura ( inclusive el interior cosa que no se logra en la mano de antióxido). De esta forma se reduce considerablemente el tiempo que requiere cada columna para ser pintada. Este tipo de proceso de pintura se lo conoce como “inmersión” | |||
Por último, una vez que seque la pintura se debe aplicar la mano de brea paltica solo a los 40 cm de columna que estarán sobre la parte empotrada. Esto se debe realizar por normativa vial nacional, los primeros 40 cm de la estructura que se ven en el exterior deben estar recubiertos por este material. Este proceso se realiza de forma manual | |||
* Cableado: | |||
La última etapa de nuestro proceso será el cableado. Es un proceso manual muy simple donde se colocan los correspondientes cables que llevaran la corriente eléctrica a la lámpara en el extremo superior de la lámpara. | |||
Costa de tres cables, uno de ellos será para la puesta a tierra el cual llegará sólo hasta la altura donde está instalada la puesta a tierra ( Se encuentra a 30 cm sobre base del piso, lo que sería 180cm desde el inicio de la columna).Mientras que los otros dos cables llegan hasta el portalámpara en la parte superior. | |||
Además del pase de cables, se debe instalará la correspondiente portalampara donde estara dispuesto lampara en si. | |||
== Determinación de las Máquinas e Instalaciones. Cálculos == | == Determinación de las Máquinas e Instalaciones. Cálculos == | ||
=== '''Especificaciones Técnicas de las Maquinas''' === | |||
[[Archivo:Maquinasfotos.jpg|centro|marco]]A continuación adjuntaremos imágenes de las maquinas utilizadas en nuestro proceso. | |||
[[Archivo:Cortadora plasma.jpg|centro|marco]] | |||
[[Archivo:Dobladora..jpg|centro|miniaturadeimagen|647x647px|Aqui se puede apreciar la dobladora de caños ]] | |||
[[Archivo:Soldadora mig.png|centro|miniaturadeimagen|327x327px|La soldadora mig con todos sus componentes]] | |||
[[Archivo:Aboquilladora foto.jpg|centro|marco|Aboquilladora]] | |||
[[Archivo:Sierra sin fin.png|centro|miniaturadeimagen|356x356px|Sierra sin fin]] | |||
=== '''Servicios y Consumo''' === | |||
'''Consumo de energía eléctrica:''' | |||
Se estimarán los consumos eléctricos en principio de todas las máquinas que participan en el proceso productivo y del compresor utilizado en las tareas de limpieza de viruta. Por otro lado, se calcularon las cantidades y potencia de las luminarias del establecimiento a partir de un estudio de medición de intensidad de luz de acuerdo al plano de trabajo establecido en la planta, y en las oficinas. El mismo se dispondrá como anexo, y los resultados se ven en las siguientes imágenes: | |||
[[Archivo:Superficie de evaluación planta.png|centro|miniaturadeimagen|500x500px|Evaluación superficie planta]] | |||
[[Archivo:Evaluación superficie oficina.png|centro|miniaturadeimagen|500x500px|Evaluación superficie oficina]] | |||
A continuación procedemos a los cálculos de consumo eléctrico: | |||
{| class="wikitable" | |||
|'''Equipo''' | |||
|'''Potencia unitaria [Kw]''' | |||
|'''Cantidad''' | |||
|'''Horas de uso anuales [h]''' | |||
|'''Consumo eléctrico anual [Kw.h]''' | |||
|- | |||
|Luces planta | |||
|0,123 | |||
|43 | |||
|1928 | |||
|10214,5 | |||
|- | |||
|Luces oficina | |||
|0,01 | |||
|63 | |||
|1928 | |||
|1214,64 | |||
|- | |||
|Computadora | |||
|0,022 | |||
|3 | |||
|1928 | |||
|127,25 | |||
|- | |||
|Sierra | |||
|0,84 | |||
|1 | |||
|1192,32 | |||
|1001,55 | |||
|- | |||
|Aboquilladora | |||
|14,91 | |||
|1 | |||
|447,12 | |||
|6666,56 | |||
|- | |||
|Cortadora de plasma | |||
|6,52 | |||
|1 | |||
|447,12 | |||
|2915,22 | |||
|- | |||
|Dobladora | |||
|5,6 | |||
|1 | |||
|447,12 | |||
|2503,87 | |||
|- | |||
|Mesa de soldado | |||
|0,746 | |||
|1 | |||
|1676,7 | |||
|1250,82 | |||
|- | |||
|Soldadora | |||
|17 | |||
|1 | |||
|1676,7 | |||
|28503,9 | |||
|- | |||
|Puente de grúa | |||
|6 | |||
|1 | |||
|465,75 | |||
|2794,5 | |||
|- | |||
|Compresor | |||
|9,32 | |||
|1 | |||
|241 | |||
|2246,12 | |||
|- | |||
| | |||
| | |||
| | |||
|'''TOTAL=''' | |||
|59438,93 | |||
|} | |||
Se estima para el año 1 un consumo eléctrico de 90% comparado con el de año régimen, por ende va a ser un total de 53495 Kw.h. | |||
'''Consumo de agua:''' | |||
El consumo de agua en Argentina se mide a partir de la cantidad de metros cuadrados de la planta. La misma tiene la dimensión de 36m x 48m, por lo tanto 1728 m2. Vale aclarar ninguna etapa de nuestro proceso productivo necesita del suministro externo de agua. Por lo que el consumo estará acotado a más que nada a la requerida para necesidades humanas. | |||
'''Consumo de combustible:''' | |||
El consumo de combustible estará dado por el que consumirá el clark y el grupo electrógeno. | |||
Por el lado del clarck, al tener uno solo en la fábrica y con un motor diesel de 49 HP, va a consumir un promedio de 10 litros por semana según la estimación brindada por el tecnólogo. Esto nos daría un total de 0,25 litros/hora. Entonces el consumo en año régimen será de 421,75 litros. | |||
En el caso del grupo electrógeno, será utilizado solo en caso de emergencia, por ende no consideramos su consumo. | |||
=== '''Mantenimiento y Medios de Control''' === | |||
Se llevará a cabo un mantenimiento preventivo en lo que refiere a cambio de aceite, engrasado, limpieza y repuesto de algunos componentes de las máquinas en general. La última hora de cada turno se la dedicará únicamente a limpieza general de las máquinas y lubricado. | |||
Desarrollamos a continuación particularidades de algunos equipos: | |||
* Sierra: como toda herramienta de corte se debe mantener afilada y limpia. El mantenimiento adecuado, con los bordes bien afilados reduce el riesgo de que la herramienta ceda y la hace más fácil de controlar. La sierra debe estar limpia de restos de materiales (limpieza manual cada todos los días). Se debe aplicar lubricante para mantener las cuchillas en las condiciones óptimas. Tanto las operaciones de mantenimiento, como las de cambio del hoja de corte (se realizará cada un mes y medio), se deben efectuar con la máquina desconectada de la red eléctrica. | |||
* Aboquilladora, dobladora, puente de grúa y mesa de soldado: el mantenimiento que se realizará está basado únicamente en el lubricado y limpieza superficial. | |||
* Cortadora de plasma: el mantenimiento requiere del cambio de los consumibles (toberas y electrodos) cada un mes y medio y limpieza superficial de la máquina. | |||
* Clark: se le hará un service cada 300 horas de uso aproximadamente. | |||
En cuanto a los demás requerimientos se aplicará a todos los equipos mantenimiento correctivo. | |||
=== '''Sistemas de Seguridad''' === | |||
'''Seguridad contra incendios:''' | |||
De acuerdo a las instalación donde se trabajará y los equipos que usaremos estaremos en riesgo de producciones de fuego tipo C (equipamientos eléctricos, maquinarias, motores, etc.), por lo que instalaremos un sistema de protección activa a través del uso de matafuegos de CO2. Estos actuarán por sofocación y enfriamiento, y son los indicados para tratar con equipos eléctricos. | |||
Se requerirá tener al personal capacitado sobre el método de uso de matafuegos. Se le indicará la forma de quite del seguro, el distanciamiento adecuado (en general se recomiendan 3 metros) y la forma de accionar la palanca y dirigir el extintor a presión. También se hará un plan de evacuación de emergencia para que se libere la zona lo más rápido posible, ya que el uso de estos matafuegos requiere que no haya personas en el ambiente a la hora de activarlos. | |||
'''Seguridad contra accidentes eléctricos:''' | |||
Se contará con los elementos de protección requeridos y obligatorios para la instalación eléctrica con la que se va a trabajar. Estos son: | |||
* Llave termomagnética para el actuar ante cortocircuitos o sobrecargas que pueda sufrir la instalación por el uso de maquinarias. | |||
* Disyuntor diferencial para que actúe ante alguna derivación en la instalación o en algún equipo. | |||
* Sistema de Puesta a Tierra con unión eléctrica entre todos los equipos metálicos del proceso productivo para que desvíe la corriente en el caso de fugas a un electrodo que se va a enterrar en el suelo. | |||
'''Elementos de protección requeridos por el proceso:''' | |||
Se dotará al personal de planta con los elementos de protección necesarios para evitar riesgos que conlleva el proceso productivo. Los mismos serán: | |||
* Casco de seguridad | |||
* Calzado de seguridad tipo puntera de acero | |||
* Fajas | |||
* Guantes de trabajo y para soldadura | |||
* Protectores visuales (tipo lentes) | |||
* Caretas para soldadura | |||
* Ropa de trabajo | |||
'''Seguridad en uso de clark y puente de grúa:''' | |||
Como ya dijimos se le realizará al clarck el service correspondiente para evitar y prevenir fallas. Tanto el uso de éste como el de puente de grúa debe llevarse bajo un protocolo que establezca un procedimiento a realizar que brinde seguridad y logre prevenir posibles accidentes que conlleven lesiones o pérdidas materiales. Algunas medidas básicas son: | |||
* No deben encontrarse operarios bajo las cargas en los izajes. | |||
* Se comunicará a los operarios cuando se realicen movimientos de cargas susceptibles de caerse. | |||
* El encargado de conducir el clarck debe ser un operario capacitado para su manejo. Lo mismo la persona encargada de controlar los izajes del puente grúa. | |||
* La carga que transporte el clark debe ser tal que le permita al conductor tener un amplio panorama visual para evitar posibles incidentes y/o accidentes. | |||
'''<big>Balance anual de material:</big>''' | |||
Procedemos en principio a calcular el '''volumen total ingresado''' en la primer sección operativa: | |||
Como ya se ha nombrado anteriormente, la columna se compone de 4 tubos de diferentes longitudes y espesores. | |||
* 1 caño de 4,20m., diámetro de 168mm. y espesor de 6,35mm. (volumen de 13537,75 cm3). | |||
* 1 caño de 3m., diámetro de 140mm. y espesor de 4,80mm. (volumen de 6116,68 cm3). | |||
* 1 caño de 3m., diámetro de 114mm. y espesor de 4mm. (volumen de 4146,9 cm3). | |||
* 1 caño de 5m., diámetro de 89mm. y espesor de 3,6mm. (volumen de 4829,256 cm3). | |||
Si sumamos los volúmenes obtenemos que el volumen total de materia prima para una columna es de 28630,586 cm3. El acero 1020 posee un peso específico de 7,87 g/cm3. Por ende el peso de 1 columna es de 225,323 kg. | |||
En año régimen se producen un total de 5589 columnas, entonces el volumen total ingresado en la primer sección operativa será de 1259,33 tn. | |||
Para el cálculo del '''porcentaje de desperdicio operativo y porcentaje de desperdicio real''' hay que tener en cuenta que el único proceso que conlleva a desperdicio de toda la línea de fabricación es el de el cortado de la ventana de inspección. Por lo tanto ambos porcentajes serán de igual valor, pues sólo existen desperdicios no recuperables. | |||
La ventana de inspección debe tener las medidas establecidas en la Norma IRAM 2620 (100mm x 170mm) y su corte se realizará en el caño inferior (diámetro de 168mm.). Este caño, posee un espesor de 6,35mm. Por lo tanto el volumen de la ventana es de 107,95 cm3. y el peso de una ventanilla de 0,85kg. A partir de esto obtenemos que en año régimen habrá un total de 4750,65kg. de desperdicio (no recuperable). | |||
<big>% desperdicio real = % desperdicio operativo = 4750,65kg/1259330kg = 0,0377%</big> | |||
<big>'''Ritmo de trabajo:'''</big> | |||
Se trabajará de lunes a viernes en un turno de 8hs. Se usarán 7 hs. productivas mientras que la última se la dedicará a limpieza de las máquinas (limpieza de viruta con compresor) y lubricación. | |||
Por lo tanto, en lo que sería cantidad de horas productivas al año partimos de: | |||
365 días/año - 104 días/años (fines de semana) - 10 días/año (feriados) -10 días/año (vacaciones) = 241 días. | |||
'''Horas activas/año de las máquinas productivas''': | |||
HA = 241 días activos/año x 7 horas/día = 1687 horas/año. | |||
En cuanto a los empleados, todos trabajarán de lunes a viernes 8hs. | |||
'''Horas trabajadas por cada operario:''' | |||
HT = 241 días activos/año x 8 horas/día = 1928 horas/año | |||
<big>'''Capacidad real anual de cada sección operativa:'''</big> | |||
A partir de la información brindada por el tecnólogo se estimaron los distintos coeficientes operativos de cada máquina. | |||
{| class="wikitable" | |||
|'''Operación''' | |||
|'''Cap. teórica por hora''' | |||
|'''Horas activas al año''' | |||
|'''Cap. teórica anual''' | |||
|'''Rendimiento operativo''' | |||
|'''Capacidad real anual''' | |||
|- | |||
|Sierra | |||
|16,18 | |||
cortes/hora | |||
|1687 hs. | |||
|27289,71 cortes/año | |||
|85% | |||
|23196,25 | |||
cortes/año | |||
|- | |||
|Aboquilladora | |||
|41,67 aboquillados/hora | |||
|1687 hs. | |||
|70291,67 aboquillados/año | |||
|90% | |||
|63262,5 aboquillados/año | |||
|- | |||
|Dobladora | |||
|13,9 doblados/hora | |||
|1687 hs. | |||
|23430,56 doblados/año | |||
|90% | |||
|21087,5 doblados/año | |||
|- | |||
|Cortadora por plasma | |||
|13,16 aberturas/hora | |||
|1687 hs. | |||
|22197,37 aberturas/año | |||
|95% | |||
|21087,5 aberturas/año | |||
|- | |||
|Soldadora MIG | |||
|11,76 soldados/hora | |||
|1687 hs. | |||
|19847,06 soldados/año | |||
|85% | |||
|16870 soldados/año | |||
|- | |||
|Pintado | |||
|3,95 pintados/hora | |||
|1687 hs. | |||
|6659,21 | |||
|95% | |||
|6326,25 pintados/año | |||
|} | |||
Se debe tener en cuenta que una columna involucra: | |||
* 4 cortes en sierra | |||
* 3 aboquillados | |||
* 1 doblado | |||
* 1 abertura | |||
* 3 soldados | |||
* 1 operación de pintado. | |||
Por lo tanto, se hará una capacidad real equivalente en unidades/año: | |||
{| class="wikitable" | |||
|'''Operación''' | |||
|'''Capacidad real anual equivalente''' | |||
|- | |||
|Sierra | |||
|5799,0625 unidades/año | |||
|- | |||
|Aboquilladora | |||
|21087,5 unidades/año | |||
|- | |||
|Dobladora | |||
|21087,5 unidades/año | |||
|- | |||
|Cortadora por plasma | |||
|21087,5 unidades/año | |||
|- | |||
|Soldado MIG | |||
|5623,333333 unidades/año | |||
|- | |||
|Pintado | |||
|6326,25 unidades/año | |||
|} | |||
<big>'''Determinación de la cantidad de máquinas operativas por sección, capacidad real anual de cada sección y aprovechamiento el relación al programa de producción:'''</big> | |||
{| class="wikitable" | |||
|'''Operación''' | |||
|'''Programa anual de producción (unid/año)''' | |||
|'''Capacidad real anual equivalente (unid/año)''' | |||
|'''Cantidad necesaria''' | |||
|'''Capacidad anual de la sección (unid/año)''' | |||
|'''Aprovechamiento seccional''' | |||
|- | |||
|Sierra | |||
|5589 | |||
|5799,0625 | |||
|1 | |||
|5799,0625 | |||
|96,38% | |||
|- | |||
|Aboquilladora | |||
|5589 | |||
|21087,5 | |||
|1 | |||
|21087,5 | |||
|26,50% | |||
|- | |||
|Dobladora | |||
|5589 | |||
|21087,5 | |||
|1 | |||
|21087,5 | |||
|26,50% | |||
|- | |||
|Cortadora por plasma | |||
|5589 | |||
|21087,5 | |||
|1 | |||
|21087,5 | |||
|26,50% | |||
|- | |||
|Soldado MIG | |||
|5589 | |||
|5623,333333 | |||
|1 | |||
|5623,333333 | |||
|99,39% | |||
|- | |||
|Pintado | |||
|5589 | |||
|6326,25 | |||
|1 | |||
|6326,25 | |||
|88,35% | |||
|} | |||
A partir de la información del cuadro, vemos que la sección de mayor aprovechamiento es la de soldado. Es decir, esta operación es nuestro Cuello de Botella. Su capacidad real es de 5623,33 unidades/año (es decir, lo que produce trabajando al 100% de aprovechamiento). Como no hay recortes intermedios entre esta operación y la última de la línea, la cantidad anual que sale de la última operación también será 5623 unidades. Esa será nuestra capacidad máxima. | |||
== Determinación de la Evolución de Mercaderías == | == Determinación de la Evolución de Mercaderías == | ||
=== '''Tiempos de Entrega , envío de Mercaderías, tamaños y Frecuencias de Compras''' === | |||
{| class="wikitable" | |||
|Elemento | |||
|Cantidad x compra | |||
|Frecuencia compra | |||
|Lead-Time | |||
|- | |||
|Columna de acero | |||
|30 ton | |||
|Semanal | |||
|3 dias habiles | |||
|- | |||
|Pintura | |||
| | |||
| | |||
| | |||
|- | |||
| Cromato de zinc | |||
|45 litros | |||
|Cada 3 semanas | |||
|1 semana | |||
|- | |||
| Sintetico Duo | |||
|65 litros | |||
|Cada 3 semanas | |||
|1 semana | |||
|- | |||
| Brea Asfaltica | |||
|20 litros | |||
|Semanal | |||
|1 dia habil | |||
|- | |||
|Soldadura | |||
| | |||
| | |||
| | |||
|- | |||
| Rollo alambre | |||
|40 rollos | |||
|Cada 2 meses | |||
|4 dias habiles | |||
|- | |||
| Gas | |||
|50 m3 | |||
|Cada 2 semanas | |||
|4 dias habiles | |||
|- | |||
| Mecha | |||
|2 unidades | |||
|Mensual | |||
|4 dias habiles | |||
|- | |||
| Macho | |||
|2 | |||
|Mensuak | |||
|4 dias habiles | |||
|- | |||
|Boca inspeccion | |||
| | |||
| | |||
| | |||
|- | |||
| Chapa | |||
|485 unidades | |||
|Mensual | |||
|10 dias | |||
|- | |||
| Tornillos | |||
|10000 unidades | |||
|Semestral | |||
|10 dias | |||
|- | |||
| Bronce | |||
|1kg | |||
|Semanal | |||
|4 dias habiles | |||
|- | |||
|Luminaria | |||
|485 unidades | |||
|Mensual | |||
|10 dias | |||
|- | |||
|Cableado | |||
|12000 metros | |||
|Mensuales | |||
|1 semana | |||
|} | |||
=== Volúmenes de producción === | |||
Basado en el plan de ventas y teniendo en cuenta el diseño de nuestro lay-out, tenemos que mensualmente la empresa realizaria 486 unidades contando con 15 días de vaciones en la cual la planta permanecerá cerrada. Con un periodo de puesta en marcha de 4 meses, debido a la complejidad de realizar la puesta en marcha de nuestra aboquilladora de deformado en frio, equipos de transporte sumado a los ensayos que deben realizarse. Esto nos da: | |||
Puesta en marcha: | |||
{| class="wikitable" | |||
|Mes | |||
|Ritmo Produccion incial | |||
|Ritmo Produccion Final | |||
|Ritmo Produccion prom. | |||
|Produccion Mensual | |||
|Prod. Propuesta(uds) | |||
|- | |||
|1 | |||
|0% | |||
|20% | |||
|10,0% | |||
|486 | |||
|49 | |||
|- | |||
|2 | |||
|20% | |||
|45% | |||
|32,5% | |||
|486 | |||
|158 | |||
|- | |||
|3 | |||
|45% | |||
|70% | |||
|57,5% | |||
|486 | |||
|279 | |||
|- | |||
|4 | |||
|70% | |||
|100% | |||
|85,0% | |||
|486 | |||
|413 | |||
|} | |||
Volúmenes de venta: | |||
{| class="wikitable" | |||
|Vol.Año 1 | |||
|4544 | |||
|unidades | |||
|- | |||
|Vol.Año 2 | |||
|5589 | |||
|unidades | |||
|- | |||
|Vol.Año 3 | |||
|5589 | |||
|unidades | |||
|- | |||
|Vol.Año 4 | |||
|5589 | |||
|unidades | |||
|- | |||
|Vol.Año 5 | |||
|5589 | |||
|unidades | |||
|} | |||
'''Stock promedio''' | |||
Nuestra planta realizara entregas cada 10 días contando con un stock de segurar de 3 días en promedio. Esto representan 15 toneladas de MP. Teniendo en cuenta que la producción diaria es de 22 unidades, nuestro stock variara entre 15 y 50 toneladas. Esto nos dará un stock promedio de 32.5 toneladas. | |||
'''Evolución de las ventas''' | |||
En el año 1 tendremos la puesta en marcha y la fabricación del stock promedio, por lo que nuestra evolución de las ventas sera: | |||
{| class="wikitable" | |||
|Ventas año 1 | |||
|4400 | |||
|unidades | |||
|- | |||
|Ventas año 2 | |||
|5589 | |||
|unidades | |||
|- | |||
|Ventas año 3 | |||
|5589 | |||
|unidades | |||
|- | |||
|Ventas año 4 | |||
|5589 | |||
|unidades | |||
|- | |||
|Ventas año 5 | |||
|5589 | |||
|unidades | |||
|} | |||
'''Materias primas''' | |||
En nuestra puesta en marcha por lo comentado anteriormente tendremos un 70% extra de desperdicios. por lo que nuestro consumo de materia prima sera: | |||
{| class="wikitable" | |||
| colspan="2" |Consumo MP año 1 | |||
|343,9 | |||
|toneladas | |||
|- | |||
| | |||
| | |||
|820,4 | |||
|toneladas | |||
|- | |||
| colspan="2" |Total año 1 | |||
|1164,3 | |||
|toneladas | |||
|- | |||
| colspan="2" |Consumo 2 al N | |||
|1258,0 | |||
|toneladas | |||
|} | |||
Siendo 343,9 toneladas la consumida durante la puesta en marcha. | |||
En proceso tendremos (teniendo en cuenta que tomamos un ciclo igual a la entregas de 10 días): | |||
{| class="wikitable" | |||
|Prod. Termin | |||
|49,95 | |||
|toneladas | |||
|- | |||
|Desp no rec | |||
|0,01883115 | |||
|toneladas | |||
|} | |||
Por lo que el consumo total de materia prima por año sera: | |||
{| class="wikitable" | |||
|Total año 1 | |||
|1214,25 | |||
|toneladas | |||
|- | |||
|Total año 2 | |||
|1258,0 | |||
|toneladas | |||
|- | |||
|Total año 3 | |||
|1258,0 | |||
|toneladas | |||
|- | |||
|Total año 4 | |||
|1258,0 | |||
|toneladas | |||
|- | |||
|Total año 5 | |||
|1258,0 | |||
|toneladas | |||
|} | |||
'''Stock de seguridad y mensual promedio''' | |||
Contaremos con un stock de seguridad de 15 toneladas como dijimos antes. Las compras de los caños, nuestro insumo principal, se realizara de manera semanal. Tendremos un stock promedio de 22,5 toneladas semanalmente. (variacion entre 15 y 45 toneladas). | |||
'''Resumen de materiales''' | |||
{| class="wikitable" | |||
| | |||
|Periodo instalacion | |||
|Año 1 | |||
|Año 2 al 5 | |||
|- | |||
|Ventas | |||
| | |||
|990 | |||
|1257,5 | |||
|- | |||
|Stock prom elaborado | |||
| | |||
|32,5 | |||
|32,5 | |||
|- | |||
|Produccion | |||
| | |||
|1022,4 | |||
|1257,5 | |||
|- | |||
|Desperdicios | |||
| | |||
|0,458 | |||
|0,474 | |||
|- | |||
|En curso y SE | |||
| | |||
|49,95 | |||
|49,95 | |||
|- | |||
|Consumo | |||
| | |||
|1072,81 | |||
|1258,00 | |||
|- | |||
|Stock Mp | |||
|200 | |||
|109,6 | |||
|109,6 | |||
|- | |||
|Compra MP | |||
|200 | |||
|982,41 | |||
|1258,00 | |||
|} | |||
Las 200 toneladas del periodo de instalación se utilizaran para comenzar la puesta en marcha en el año 1. | |||
Todos los valores están expresados en toneladas. Correspondiendo 0,225 toneladas por Producto termiando. | |||
== Determinación del Personal == | == Determinación del Personal == | ||
=== '''Organigrama''' === | |||
[[Archivo:Organigrama correcion.png|alt=|centro|marco|Organigrama de la empresa.]] | |||
=== '''Descripción de los Puestos de Trabajo''' === | |||
<u>Recepción de Materia Prima:</u> | |||
Descarga con autoelevadores de los caños al depósito con autoelevador. | |||
Por la cercanía al lugar, se encargarán los dos operarios del sector de Corte. | |||
<u>Abastecimiento de insumos a puestos, retiro de residuos de puestos, movimiento de producto semielaborado (caños, no columna sin pintar):</u> | |||
Actividades de acarreo de materiales y retiro de descartes de los puestos de trabajo. Movimiento de un puesto a otro de productos semielaborados: específicamente previo al conformado de la estructura, cuando los semielaborados aun son caños. | |||
Por la cantidad de tiempo ocioso del puesto de Aboquillado, las dos personas de dicho sector se encargarán, además, de las tareas de este puesto. Para ello, utilizarán autoelevadores. | |||
<u>Sector de Corte:</u> | |||
Cortado de los caños a las medidas requeridas con sierras sin fin., ademas de la recepción de materias primas. | |||
En este puesto por turno se asignarán dos personas. | |||
<u>Aboquillado:</u> | |||
Operación de aboquilladora. En este puesto se asignan dos operarios por turno. | |||
<u>Doblado:</u> | |||
Operación con maquina dobladora. En este puesto se asigna un operario por turno. | |||
<u>Mesa de Trabajo:</u> | |||
Corte de plasma para corrección de imperfecciones derivadas del sector Corte, agujereado y conformado de la ventana de inspección. Soldado de la puesta a tierra. | |||
Al puesto se asignan dos operarios, uno como soldador y otro como auxiliar de este último. | |||
<u>Mesa de Soldado:</u> | |||
Soldado de la estructura con soldadura MIG, utilizando mesa giratoria. Carga de estructura a carro especial con aparejo. Transporte a sector de pintado con carro especial. | |||
Al puesto se asignan tres operarios, uno como soldador y dos como auxiliares de este último. | |||
<u>Pintado:</u> | |||
Pintado con pistola de pintura de antioxido. Pintado con inmersión de la estructura. Pintura manual de brea en la base con rodillo manualmente. Utilización de puente grua. Traslado a zona de producto terminado. | |||
Al puesto se asignan 2 operarios. | |||
<u>Compras de abastecimiento de materia prima, materiales, insumos productivos, e insumos de mantenimiento. Programación de la producción. Jefatura de planta:</u> | |||
Se asignan dos personas para las tareas mencionadas, y una persona auxiliar. | |||
<u>Mantenimiento mecánico:</u> | |||
Se asigna un operario al puesto. | |||
=== '''Calificación y Formación''' === | |||
{| class="wikitable" | |||
! colspan="7" |Requerimientos por Puesto | |||
|- | |||
|'''Sector''' | |||
|'''Nombre del puesto''' | |||
|'''Formación obligatoria''' | |||
|'''Experiencia deseada''' | |||
|'''Experiencia obligatoria''' | |||
|'''Capacitaciones''' | |||
|- | |||
| rowspan="2" |Recepción de MP y Corte | |||
|Operario 1 | |||
|Técnico | |||
|Manejo de maquinaria | |||
|Operario industrial metalúrgico | |||
|Clarkista; Operación de sierra | |||
|- | |||
|Operario 2 | |||
|Técnico | |||
|Manejo de maquinaria | |||
|Operario industrial metalúrgico | |||
|Clarkista; Operación de sierra | |||
|- | |||
| rowspan="2" |Aboquillado | |||
|Operario 3 | |||
|Técnico | |||
|Clarkista; Manejo de maquinaria | |||
|Operario industrial metalúrgico | |||
|Clarkista; Manejo de aboquilladora | |||
|- | |||
|Operario 4 | |||
|Técnico | |||
|Clarkista; Manejo de Maquinaria | |||
|Operario industrial metalúrgico | |||
|Clarkista; Manejo de aboquilladora | |||
|- | |||
|Doblado | |||
|Operario 5 | |||
|Técnico | |||
|Manejo de maquinaria | |||
|Operario industrial metalúrgico | |||
|Manejo de maquina de doblado | |||
|- | |||
| rowspan="2" |Mesa de trabajo | |||
|Operario 6 | |||
|Técnico | |||
|Manejo de maquinaria | |||
|Operario industrial metalúrgico | |||
|Manejo de maquinaria y asistencia al soldador | |||
|- | |||
|Operario 7 | |||
|Técnico; Soldador con Certificación | |||
|Soldado de cañerías y tubos | |||
|Operario industrial metalúrgico; soldador | |||
| | |||
|- | |||
| rowspan="3" |Mesa de soldado | |||
|Operario 8 | |||
| rowspan="2" |Técnico | |||
| rowspan="2" |Manejo de maquinaria | |||
| rowspan="2" |Operario industrial metalúrgico | |||
| rowspan="2" |Manejo de maquinaria; asistencia al soldador; carga y manipulación con aparejo | |||
|- | |||
|Operario 9 | |||
|- | |||
|Operario 10 | |||
|Técnico; Soldador con Certificación | |||
|Soldado de cañerías y tubos | |||
|Operario industrial metalúrgico; soldador | |||
|Carga y manipulación con aparejo | |||
|- | |||
| rowspan="2" |Pintado | |||
|Operario 11 | |||
|Técnico | |||
|Manejo de herramientas de pintado; Manejo de puente grúa | |||
|Operario industrial metalúrgico | |||
|Manejo de herramental de pintado; mantenimiento de herramental de pintado; manejo de puente grúa | |||
|- | |||
|Operario 12 | |||
|Técnico | |||
|Manejo de herramientas de pintado; Manejo de puente grúa | |||
|Operario industrial metalúrgico | |||
|Manejo de herramental de pintado; mantenimiento de herramental de pintado; manejo de puente grúa | |||
|- | |||
|Mantenimiento | |||
|Mecánico | |||
|Técnico electromecanico | |||
| colspan="2" |Mantenimiento mecánico | |||
| | |||
|- | |||
| rowspan="3" |Oficinas y recepción | |||
|Jefe de planta y programación | |||
|Técnico | |||
|Operario industrial metalúrgico; Programación de producción | |||
|Programación de producción | |||
| | |||
|- | |||
|Compras de abastecimiento productivo y de mantenimiento | |||
|Técnico | |||
|Mantenimiento; personal administrativo en empresa industrial | |||
|Personal administrativo en empresa industrial | |||
|Procedimientos de compra | |||
|- | |||
|Recepcionista y cadetería | |||
|Secundario completo | |||
|Cadete; recepcionista | |||
| | |||
| | |||
|} | |||
== Listado de Equipos Auxiliares, Muebles y Útiles == | == Listado de Equipos Auxiliares, Muebles y Útiles == | ||
Línea 18: | Línea 913: | ||
* Aparejo sobre cama de soldado | * Aparejo sobre cama de soldado | ||
* Carro diseñado a medida para recibir material en proceso del aparejo de la cama de soldado, y transportar los semielaborados al sector de pintado. | * Carro diseñado a medida para recibir material en proceso del aparejo de la cama de soldado, y transportar los semielaborados al sector de pintado. | ||
=== '''Administración''' === | === '''Administración''' === | ||
Línea 25: | Línea 919: | ||
== Anteproyecto de Planta == | == Anteproyecto de Planta == | ||
=== '''Plano de Planta''' === | |||
Se realizo en Autocad un posible plano de planta de la instalación. Es un espacio techado de 36x48metros con una altura de 8,5metros en el sector de planta y de 3 metros en oficinas siendo esta una construcción aparte. El sector de planta cuenta con las siguientes instalaciones: | |||
{| class="wikitable" | |||
!Identificacion | |||
!Descripción | |||
|- | |||
|1 | |||
|Mesa soldado | |||
|- | |||
|2 | |||
|Deposito Insumos | |||
|- | |||
|3 | |||
|Aboquilladora | |||
|- | |||
|4 | |||
|Dobladora | |||
|- | |||
|5 | |||
|Torno | |||
|- | |||
|6 | |||
|Mesa de trabajo#1 | |||
|- | |||
|7 | |||
|Mesa de trabajo#2 | |||
|- | |||
|8 | |||
|Pintado | |||
|- | |||
|9 | |||
|Sierra sensitiva | |||
|- | |||
|10 | |||
|Puente grua | |||
|- | |||
|A1 | |||
|Almacen MP | |||
|- | |||
|A2 | |||
|Almacen PT | |||
|} | |||
[[Archivo:Plano-Planta.png|centro|miniaturadeimagen|775x775px]] | |||
=== '''Recorrido de Materiales''' === | |||
Para los diagramas de flujos se decidió por adjuntarlos separados por las distintas denominaciones de caños ya que, de acuerdo a sus especificaciones, es colocado en lugares específicos del producto final y conllevan distintos procesos. | |||
Primero comenzamos con los caños de 168mm de diámetro. El recorrido que realiza a lo largo de todo el proceso es el siguiente: | |||
Deposito Materias Primas --> Cortado --> Aboquillado --> Corte Ventana Inspección y Colocación PAT --> Soldado --> Pintado --> Cableado --> Deposito Producto Terminado. | |||
[[Archivo:Planos 168mm.jpg|alt=|centro|marco|Diagrama Flujo Caños 168mm]] | |||
En el siguiente gráficos se pueden ver los recorridos dentro de la planta de los caños de 140mm y 114mm. Los mismos se grafican dentro del mismo plano debido a que sufren el mismo proceso. El recorrido que realiza a lo largo de todo el proceso es el siguiente: | |||
Deposito Materias Primas --> Cortado --> Aboquillado --> Soldado --> Pintado --> Cableado --> Deposito Producto Terminado. | |||
[[Archivo:Planos 140-114mm.jpg|alt=|centro|marco|Diagrama Flujo Caños 140mm y 114mm]] | |||
En tercer lugar, colocamos el diagrama de flujo de los caños de 89mm. Estos tienen un proceso distinto al resto ya que se les realiza un doblado para obtener la curva caracteristica de las luminarias en su extremo superior. El recorrido que realiza a lo largo de todo el proceso es el siguiente: | |||
Deposito Materias Primas --> Cortado --> Aboquillado --> Doblado --> Soldado --> Pintado --> Cableado --> Deposito Producto Terminado. | |||
[[Archivo:Planos 89mm.jpg|alt=|centro|marco|Diagrama Flujo Caños 89mm]] | |||
En cuarto lugar mencionaremos los flujos del material de cableado. Por mas simple que sea es una parte importante de nuestras columnas para luminaria. El recorrido que realiza a lo largo de todo el proceso es el siguiente: | |||
Deposito Materias Primas --> Soldado --> Deposito Producto Terminado. | |||
[[Archivo:Planos Insumos Electricos.jpg|alt=|centro|marco|Diagrama Flujos Material Eléctrico.]] | |||
Por ultimo, adjuntamos un diagrama que muestra las zonas de trabajo del montacargas y el puente de grúa. | |||
[[Archivo:Planos Movimientos.jpg|centro|marco|Zonas de trabajo del montacargas y puente de grúa.]] | |||
== Cronograma de Ejecución == | == Cronograma de Ejecución == | ||
[[Archivo:Ejecucion.png|centro|marco]] |
Revisión actual - 22:15 29 ago 2020
Determinación de la Localización
Para determinar la localización de nuestra organización realizamos una matriz de localización. En la misma se enumeraron una serie de factores, a la cual se les asigno un nivel de importancia (siendo 1 poca importancia y 5 mucha importancia). Luego se le asigno un valor de disponibilidad, siendo nuevamente 1 para poca disponibilidad o desfavorable y 5 para mucha disponibilidad y favorable.
A continuación se adjunta la matriz con sus resultados:
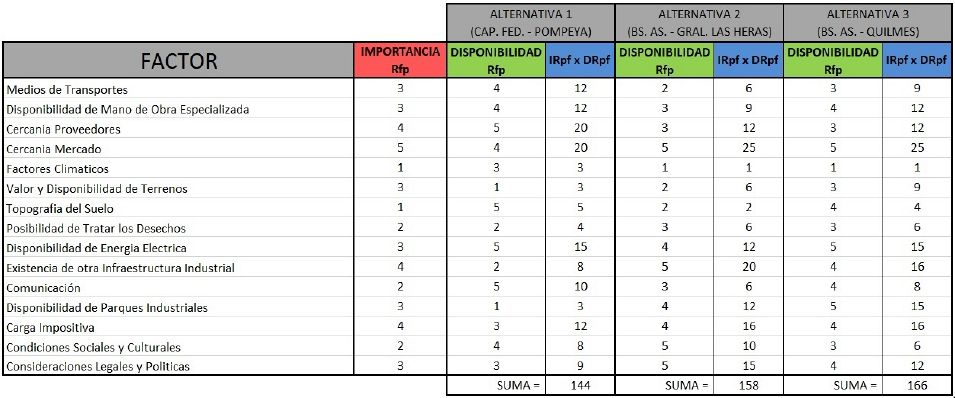
Dentro de los factores que creemos claves en el proyecto se encuentra la cercanía a proveedores y al mercado. Los mismos nos abarataran los costos de logística en el traslado (en especial el traslado de caños y columnas). Dentro de los proveedores, la alternativa Pompeya presenta una ventaja debido a que uno de los proveedores se encuentra en las cercanías, pero la zona de Quilmes presenta ventajas en cuanto al acceso al mercado y al traslado de los productos. Por ultimo, no queremos dejar de mencionar la carga impositiva. Este es un factor que suele ser de gran peso para las empresas en Argentina. Para el caso particular, creemos que las alternativas de Quilmes y Gral. Las Heras tendrán ventajas debido a que cuentan con parques industriales en dichas jurisdicciones.
En especial, el factor mano de obra especializada no posee un valor de importancia muy elevado debido a que nuestro proceso solo tiene como requerimiento especial la contratación de soldadores certificados nivel II. El resto de los operarios deberían presentar conocimientos mas del tipo técnico que no creemos sea algo difícil de encontrar.
Factores tales como los climáticos, topografía o el tratamiento de desechos no hacen demasiada importancia a nuestro proyecto por lo que presentan valores relativamente mas bajos que el resto. Las razones particulares son que el clima no afecta nuestras actividades de gran manera al igual que no creemos que la topografía sea un gran problema en las áreas mencionadas como alternativas. El tratamiento de desechos tampoco debería ser de gran problema debido a que nuestro proceso no presenta cantidades importantes de residuos, efluentes y/o emanaciones.
Como resultado de la matriz de localización, llegamos a la conclusión de que nuestra empresa se ubicará en la zona de Quilmes. Dicha alternativa cuenta ventajas en cuanto a la cercanía de mercados y proveedores. También cuenta con un complejo industrial donde podríamos analizar instalarnos. Es una zona accesible con los medios de transportes y creemos no tiene grandes dificultades en el acceso a operarios calificados.
Definición Técnica del Producto
Planos
A continuación adjuntamos un plano hecho con la herramienta AutoCAD. El mismo muestra las 4 secciones de caños con sus largos y espesores correspondientes.
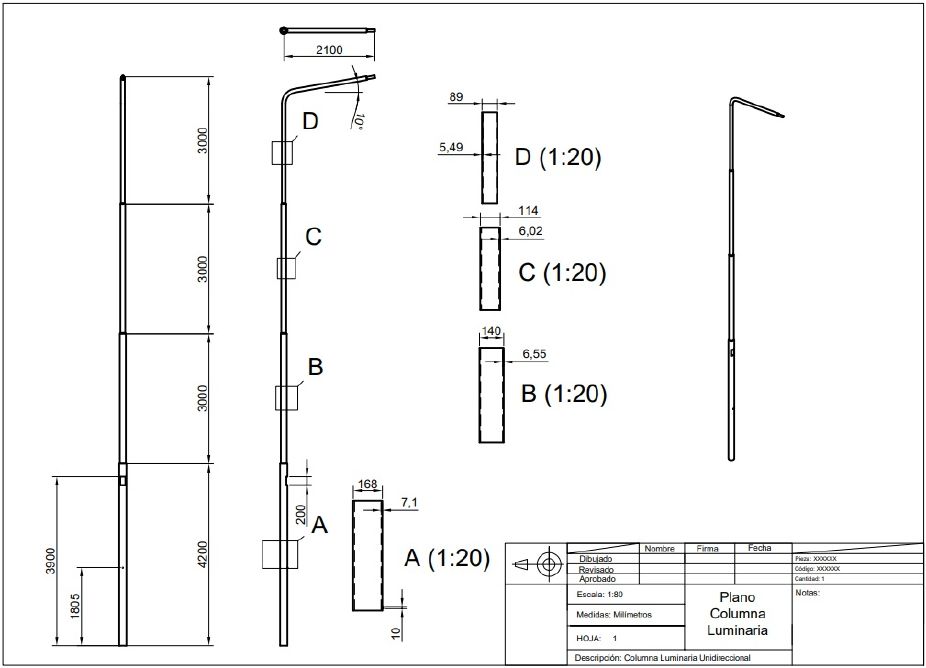
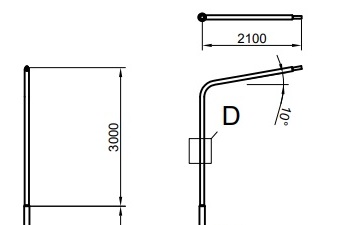
Listado de Materiales
Especificaciones Técnicas
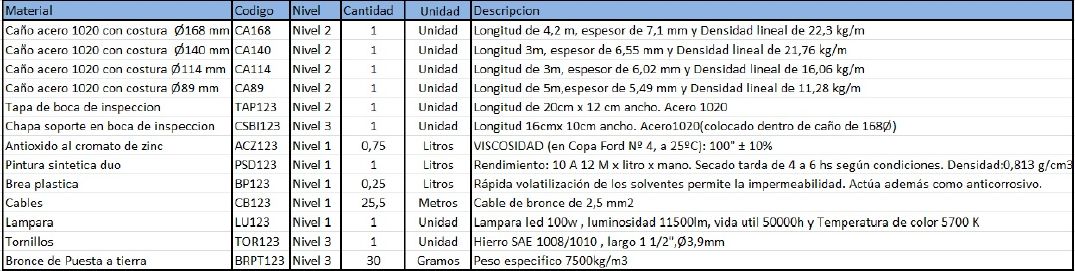
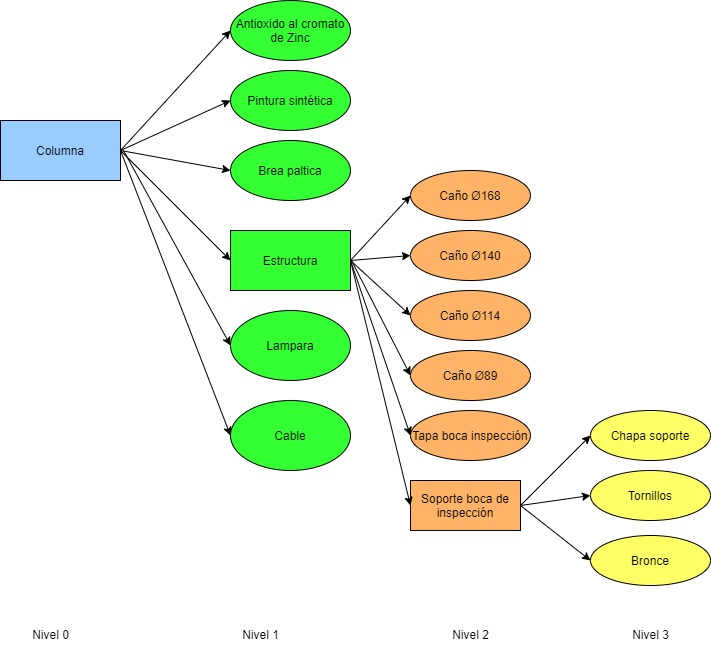
Normas Aplicables
Las normas que aplicarán en nuestro producto son las que contempla el Pliego de Especificaciones Técnicas Particulares para Iluminación de Viabilidad Nacional.
Partiendo del poste de acero en sí, que será el producto que fabricaremos, aplican las normas:
- IRAM 2591/2592 e IRAM-IAS U 500 2592 en cuanto a lo referido al material de las columnas de acero. El límite de fluencia mínimo debe ser de 30 kg/mm2 y la carga de rotura mínima de 45 kg/mm2. Se establece el uso en el extremo de los caños un sistema de abocardado en frío para mantener las propiedades originales del acero, mediante una curva de transición suave. También se deben realizar soldados con máquinas semiautomáticas con aporte continuo de alambre y protección gaseosa tipo MIG (Metal Inert Gas), con gas CO2 o argón. El solape de un caño dentro del otro no deberá ser menor a 1,5 veces el diámetro del menor caño. Además se establece que la flecha admisible en la dirección más desfavorable con una carga en el extremo del pescante de 30 kg no excederá del 1,5% de la longitud desarrollada en la parte exterior del empotramiento.
- Reglamento CIRSOC 301 el cual establece que Las columnas deberán ser dimensionadas para soportar un peso mínimo del artefacto de 25 kg, más los efectos producidos por el viento máximo de la zona, considerando una superficie efectiva del artefacto de 0,28 m2 en el plano de la columna y 0,14 m2 en el plano normal a la misma.
- IRAM 2619/2620 que establece lo referido a los ensayos solicitados y el dimensionamiento de los caños. Para el control de deformación se debe ensayar hasta el 5% de la cantidad de las columnas por partida. En las columnas rectas y/o con brazo se aplicará una carga vertical equivalente a una vez y media (1,5) la utilizada para las hipótesis de cálculo. Para su aceptación, con estas cargas, no deberán sufrir deformaciones permanentes de ningún tipo. Por el lado del dimensionamiento, el escalonado entre los distintos diámetros tiene que hacerse con una curva de transición, lograda por el procedimiento que se considere más adecuado, observando siempre que la resistencia de conjunto sea la exigida. El coeficiente de seguridad no deberá ser inferior a 2,0. En lo que respecta a las ventanas de inspección, la norma establece que todas las columnas deben poseer una abertura ubicada a una altura de 2,40 m., por encima del nivel de empotramiento de la misma, con una chapa de hierro de 3mm de espesor soldada en el interior de la misma, para soporte del tablero eléctrico de derivación. Tendrá una tapa de cierre metálica a bisagra (anti vandálica) con un tornillo Allen oculto, imperdible; el espesor de la tapa deberá ser no menor a 3 mm. La dimensión de la ventana de inspección, deberá se de 100 mm. x 170 mm.
- IRAM 1042 referida a la protección de la estructura. Establece que se debe aplicar sobre la columna un espesor mínimo de cuarenta micrones (40 μm) de antióxido al cromato de zinc en toda su extensión e interiormente desde su extremo inferior hasta una altura de 0,30 m por encima de la longitud de empotramiento. El color final de la columna se establecerá con dos manos de esmalte sintético color blanco.
Por el lado de la luminaria, más allá que no seamos nosotros quienes la fabriquemos (la adquirimos de terceros), tendremos que cumplir ciertas normas a la hora de tratar con nuestros clientes, las cuales exigiremos a nuestros proveedores. Estas son:
- IRAM-AADL J 2022-1 es la norma referida a las condiciones fotométricas de los artefactos de iluminación. Se debe presentar documentación de las condiciones fotométricas de la luminaria. La documentación deberá acompañarse con una copia legalizada de las curvas y los protocolos de ensayo del artefacto ofrecido, para la lámpara /unidad de módulos led con la cual funcionará. Los protocolos de ensayo fotométricos y documentación adicional que serán exigidos son:
- Curvas Isolux.
- Curvas Isocandelas.
- Curvas Polares Radiales o de Distribución.
- Curvas de Utilización.
- Marca y modelo: memoria descriptiva del elemento, detalles constructivos, materiales empleados, forma de instalación, conservación; planos a escala conveniente, de planta, alzado y perspectiva del elemento; distribución fotométrica, flujo luminoso total emitido por la luminaria y flujo luminoso emitido al hemisferio superior en posición de trabajo.
- Potencia nominal asignada y consumo total del sistema.
- Eficiencia de la luminaria (lm/W) y vida útil estimada para la luminaria en horas de funcionamiento (el parámetro de vida útil se calculará de modo que transcurridas las horas señaladas, el flujo luminoso sea del 80% respecto del flujo total emitido inicialmente).
- Gráfico sobre el mantenimiento lumínico a lo largo de la vida de la luminaria, indicando la pérdida de flujo cada 4000 horas de funcionamiento.
- Rango de temperaturas ambiente de funcionamiento sin alteración en sus parámetros fundamentales. Se deberán aportar, mediciones sobre las características de emisión luminosa de la luminaria en función de la temperatura ambiente exterior, indicando al menos de -10°C a 50°C.
- Grado de hermeticidad de la luminaria completa.
- Declaración de Conformidad y Expediente Técnico o documentación técnica asociada expedida por Laboratorio acreditado.
Adicionalmente, por lo respectivo a luminaria LED se deberá presentar:
- Marca, modelo y datos del fabricante del LED / Módulo LED; potencia nominal y flujo luminoso emitido por cada LED individualmente y por el módulo completo.
- Curvas de duración de vida, en horas de funcionamiento, en función de la temperatura de unión. Índice de reproducción cromática; temperatura de color (cuando el LED o el módulo LED pueda alimentarse a diferentes corrientes o tensiones de alimentación, los datos anteriores se referirán a cada una de dichas corrientes o tensiones).
- Temperatura máxima asignada.
- Vida útil estimada de cada LED y del módulo LED en horas de funcionamiento.
Por último, en lo que respecta a el cableado (conductores eléctricos) encontramos las siguientes normas:
- IRAM 2281-8 y IRAM 2022 que indican que las columnas deberán contar con una puesta a tierra de seguridad. El cable de protección de puesta a tierra de las columnas, será, en todos los casos, de cobre, de 35 mm2 de sección mínima con un diámetro mínimo del alambre de 1,8 mm.
- IRAM 2178 establece que los conductores podrán ser unipolares o multipolares, con aislación de PVC, de cobre flexible o rígido, aptos para trabajar a una tensión de 1,1 kV. Su sección no será inferior a 4mm2.
Características Condición del Producto
Las condiciones del producto son aquellas presentes en las especificaciones del cliente. Al ser un producto de uso en el servicio público de iluminación, las condiciones son las que se encuentran presentes en las normas expuestas del punto anterior.
Plan de Ensayos
El ensayo que nos corresponde es el de torsión, según la Norma IRAM AADL J2021. Los componentes eléctricos vienen de fábrica ya testeados.
Se debe ensayar, para una partida, una muestra del 5%. Se trata de aplicar una carga vertical equivalente a una vez y media la utilizada para la hipótesis de cálculo sobre el extremo máximo horizontal del brazo de la columna.
Para la aceptación, con estas cargas la columna no debe sufrir deformaciones permanentes de ningún tipo.
Se ensayarán las columnas según lo exijan los clientes: no todos requieren tener el estudio realizado para sus aplicaciones, pero estimaremos que alrededor del 10% de los clientes pedirán que se realice. Además, el estudio será tercerizado, y lo realizará la empresa
Acondicionamiento del Producto
Por las magnitudes del producto, y dado que su principal función es iluminar en espacios al aire libre, hace que no requiera de packaging o envoltorios protectores para su disposición y despacho.
Solamente se colocarán sobre tacos al transportarse, y entre los tacos y columnas se colocará alfombra para evitar que se puedan dañar entre ellas al moverse.
Definición del Proceso de Producción
Diagrama de Flujo
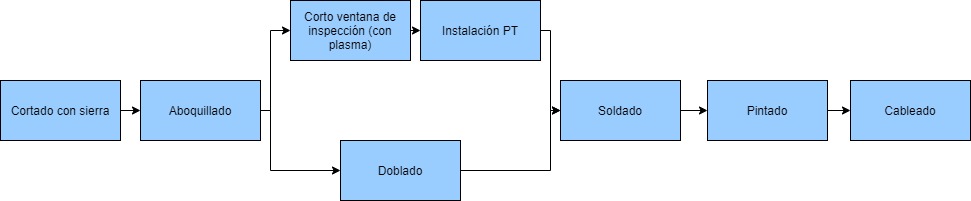
Cursograma Sinoptico
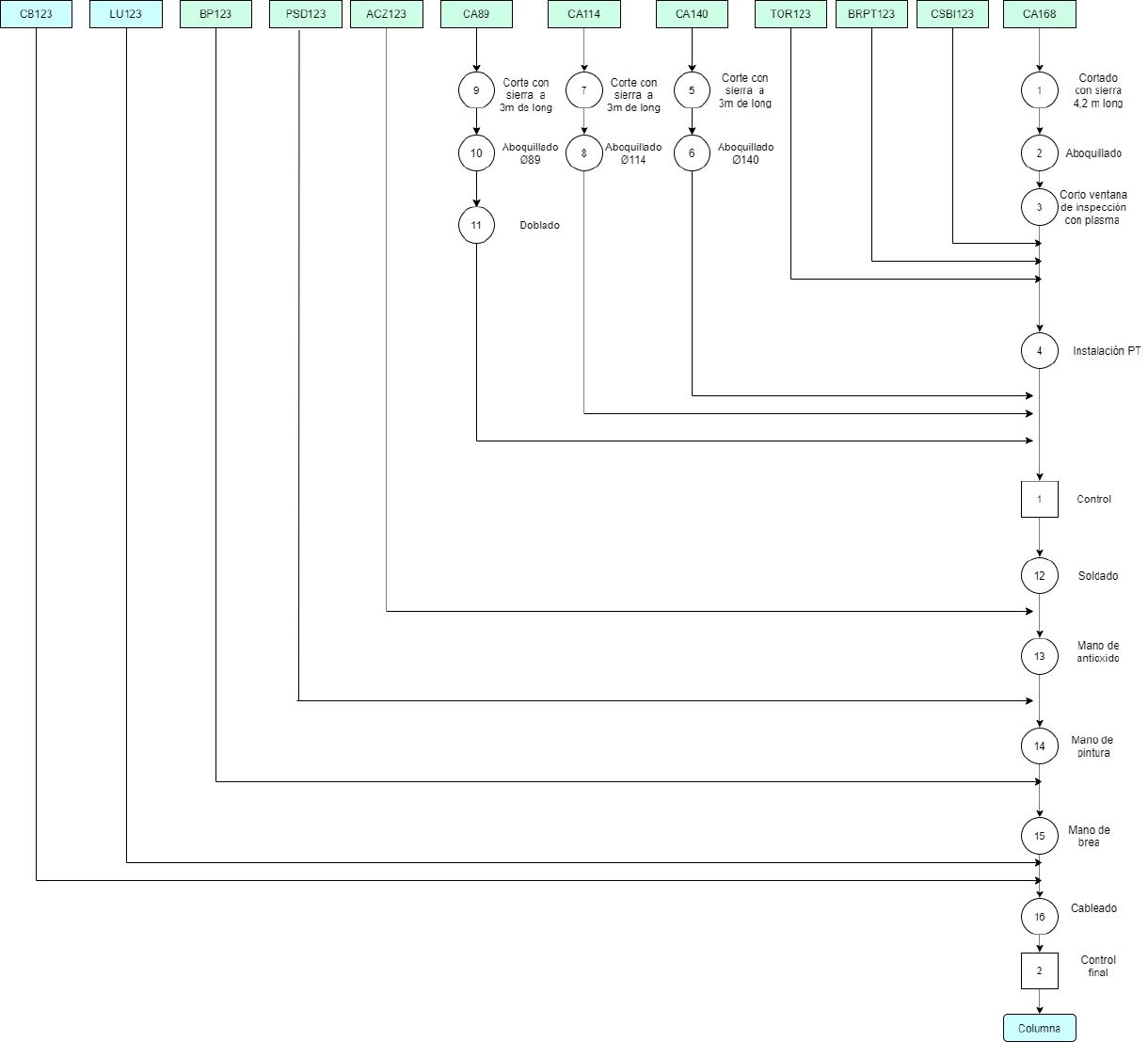
Descripción de Cada Etapa
- Cortado:
Una vez que contamos con los materiales en el depósito de MP, podremos comenzar con el proceso productivo. En la primer etapa del mismo se procede a realizar el cortado de los caños de los distintos diámetros de forma transversal delimitando cada uno de ellos a su medida establecida. Para trasladar estos caños los cuales cuentan con un gran peso, se opta por la utilización de un puente de grúa para facilitar esta tarea.
En la sierra se cuenta con unos topes los cuales nos permiten marcar correctamente el punto donde se realiza el corte. Esta actividad es relativamente fácil y suele llevar poco tiempo. Simplemente Se reduce de tamaño los largos caños de cada uno de los diámetros uno a la vez. Es decir, que una vez dispuesto en la máquina el caño de diámetro mayor (168mm) realizarse sobre el mismo todos los cortes que me permita en caño respetando siempre la longitud establecida para dicho diámetro, una vez que concluyó con los cortes de dicho diámetro puedo pasar a realizar la actividad en el siguiente tamaño de caño.
- Aboquillado:
Esta etapa del proceso será nuestra diferenciadora de nuestro ciclo productivo respecto a la competencia. La actividad de aboquillado hace referencia trabajar un extremo del caño de forma tal que este obtenga una forma más cónica. Esto se realiza para facilitar la unión entre los caños de distintos diámetros. En el caso de nuestro proceso este paso se realizará en frío, sin necesidad de calentar la pieza antes del conformado. Al calentar el material se pierden varias propiedades mecánicas, en cambio al conformar un material en frío aumenta la resistencia a la deformación.
En la máquina se cuenta con una prensa que presiona el caño dentro una matriz que permite realizar este proceso con buena terminación y de en poco tiempo en comparación con la diferencia, ya que no hace falta un calentamiento previo.
- Corte de ventana de inspección:
El corte de la ventana de inspección solo se realizará en el caño de mayor diámetro,suele colocarse a una altura de 2,4 m del suelo ( además debo sumarle el 1,5 m que se encuentra). Esta ventana cumple la función de permitir acceso al interior de la columna una vez instalada, para chequear las conexiones y permite la acceso a la chapa soporte donde se hace la fijación de los cables. Este pequeño corte se realizará con plasma, el corte por plasma es un proceso que utiliza una boquilla, con un orificio para la circulación del gas ionizado a altas temperatura, de tal forma que se obtiene un rayo que se puede utilizar para cortar secciones de metales tales como el acero al carbono, acero inoxidable, aluminio y otros metales conductores de la electricidad. Por medio del uso de esta técnica, el arco de plasma funde el metal, y el gas elimina el material fundido. Las dimensiones de la ventana son de aproximadamente 20 cm de y el ancho está dado por el ancho de curvatura de la columna ( el cual suele ser de 12cm)
- Instalación de puesta a tierra:
La puesta a tierra es un sistema que asegura que, ante cualquier falla de aislamiento, las partes metálicas de todo el equipo eléctrico descarguen la corriente eléctrica a tierra, sin afectar al usuario que entre en contacto con el aparato eléctrico, evitando así que sufra una descarga eléctrica.
En nuestro caso la misma se colocará a 30 cm del piso, es decir 1,8 m debido a la parte de la columna que está debajo del suelo. Su colación es realmente sencilla. Solo se debe realizar un pequeño punto de bronce en el exterior de la columna. El mismo será traspasado por un macho el cual formará la rosca necesaria para el paso de un tornillo al interior de la columna el cual será ajustado con una tuerca. Así una vez que se realice el cableado final de la columna en dicho tornillo se pondrá el cable de puesta a tierra.
- Doblado:
Este proceso solo se realizará en el caño de menor diámetro ya que es el que se encontrara más lejos del suelo. En nuestro caso utilizaremos el método de doblado horizontal. La máquina cuenta con soportes que afirman la columna, mientras que un pistón hidráulico presiona con una matriz al caño en una altura determinado. Esta máquina cuenta con unos swich electrónicos que permiten avanzar al pistón hasta una profundidad determinada que nos permitirá obtener el ángulo deseado. El pistón queda algunos segundos presionando al tubo en dicha posición y luego es retirado lentamente. Cabe destacar que los soportes que sostienen la columna no son fijos, y a medida que el caño se dobla estos van rotando acompañó dicho movimiento.
- Soldado:
A continuación se procede a llevar los caños de distintos diámetros a la mesa de soldado.
Aquí se disponen los mismo en la posición que cada uno va a ocupar en la estructura final. Ya que previamente se procedió a realizar el aboquillado a cada extremo de caño en el extremo que conecta con el siguiente caño del diámetro más próximo, se podrá encajar de forma más sencilla cada uno de ellos previo al soldado.
UNn veces dispuestos los 4 caños, se procede a soldar la primera unión de la estructura. la facilidad que brinda la mesa de soldado en esta parte de la operación es que mediante una serie de rodillos permite ir rotando lentamente el conjunto de caños logrando así un movimiento más uniforme al ir soldado.
Una vez concluida la primer unión, se procede a realizar la misma actividad con las otras dos uniones de la estructura.
- Pintado:
El proceso de pintado cuenta con 3 etapas bien definidas: la capa de antióxido, la capa de pintura y la capa de brea paltica solo en el área determinada.
La primer mano que se le aplica a la columna es de antióxido al cromato de zinc, la cual se aplica de forma manual a la totalidad de la estructura. Esta permitirá proteger la columna ante el ataque de agentes externos, permitiendo aumentar la vida útil de la columna.
Próximo a la primera mano de antióxido, se procede a levantar la columna mediante el puente de grúa y dirigirla hacia una pileta de pintura. La columna es sumergida en su totalidad dentro del piletón de pintura, logrando así un mejor acabado y llegar a todas las partes de la estructura ( inclusive el interior cosa que no se logra en la mano de antióxido). De esta forma se reduce considerablemente el tiempo que requiere cada columna para ser pintada. Este tipo de proceso de pintura se lo conoce como “inmersión”
Por último, una vez que seque la pintura se debe aplicar la mano de brea paltica solo a los 40 cm de columna que estarán sobre la parte empotrada. Esto se debe realizar por normativa vial nacional, los primeros 40 cm de la estructura que se ven en el exterior deben estar recubiertos por este material. Este proceso se realiza de forma manual
- Cableado:
La última etapa de nuestro proceso será el cableado. Es un proceso manual muy simple donde se colocan los correspondientes cables que llevaran la corriente eléctrica a la lámpara en el extremo superior de la lámpara.
Costa de tres cables, uno de ellos será para la puesta a tierra el cual llegará sólo hasta la altura donde está instalada la puesta a tierra ( Se encuentra a 30 cm sobre base del piso, lo que sería 180cm desde el inicio de la columna).Mientras que los otros dos cables llegan hasta el portalámpara en la parte superior.
Además del pase de cables, se debe instalará la correspondiente portalampara donde estara dispuesto lampara en si.
Determinación de las Máquinas e Instalaciones. Cálculos
Especificaciones Técnicas de las Maquinas
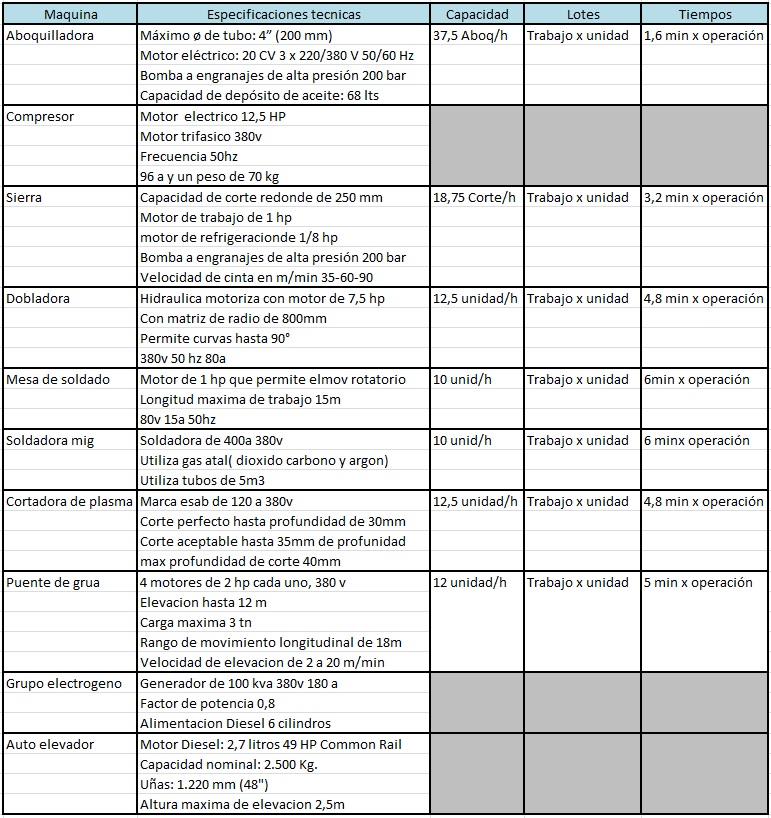
A continuación adjuntaremos imágenes de las maquinas utilizadas en nuestro proceso.
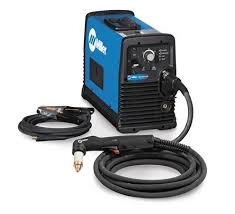
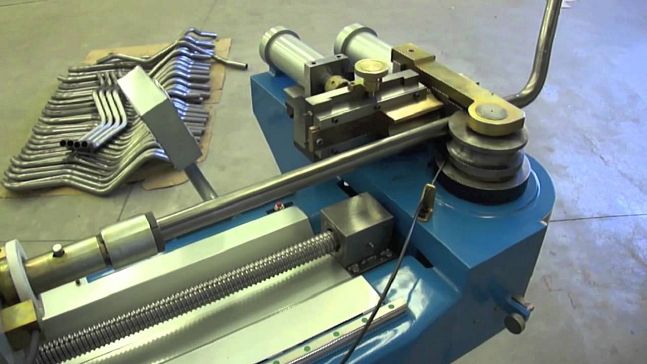
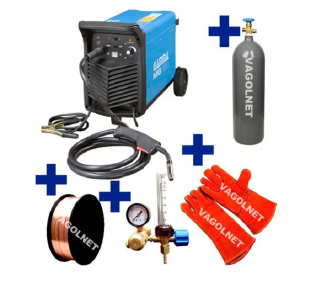
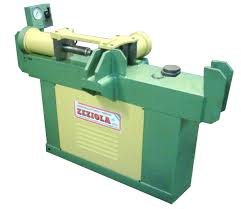
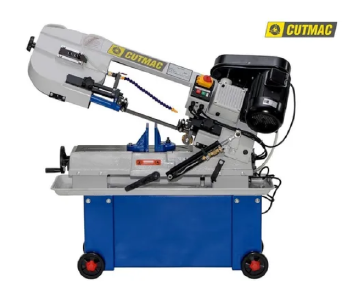
Servicios y Consumo
Consumo de energía eléctrica:
Se estimarán los consumos eléctricos en principio de todas las máquinas que participan en el proceso productivo y del compresor utilizado en las tareas de limpieza de viruta. Por otro lado, se calcularon las cantidades y potencia de las luminarias del establecimiento a partir de un estudio de medición de intensidad de luz de acuerdo al plano de trabajo establecido en la planta, y en las oficinas. El mismo se dispondrá como anexo, y los resultados se ven en las siguientes imágenes:
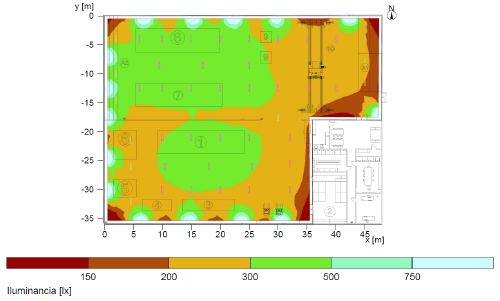
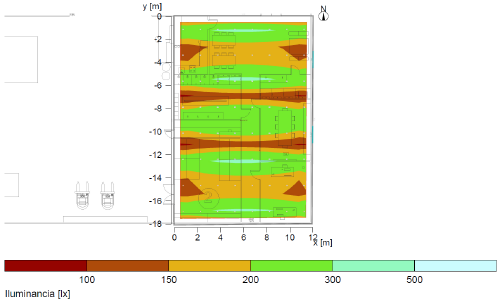
A continuación procedemos a los cálculos de consumo eléctrico:
Equipo | Potencia unitaria [Kw] | Cantidad | Horas de uso anuales [h] | Consumo eléctrico anual [Kw.h] |
Luces planta | 0,123 | 43 | 1928 | 10214,5 |
Luces oficina | 0,01 | 63 | 1928 | 1214,64 |
Computadora | 0,022 | 3 | 1928 | 127,25 |
Sierra | 0,84 | 1 | 1192,32 | 1001,55 |
Aboquilladora | 14,91 | 1 | 447,12 | 6666,56 |
Cortadora de plasma | 6,52 | 1 | 447,12 | 2915,22 |
Dobladora | 5,6 | 1 | 447,12 | 2503,87 |
Mesa de soldado | 0,746 | 1 | 1676,7 | 1250,82 |
Soldadora | 17 | 1 | 1676,7 | 28503,9 |
Puente de grúa | 6 | 1 | 465,75 | 2794,5 |
Compresor | 9,32 | 1 | 241 | 2246,12 |
TOTAL= | 59438,93 |
Se estima para el año 1 un consumo eléctrico de 90% comparado con el de año régimen, por ende va a ser un total de 53495 Kw.h.
Consumo de agua:
El consumo de agua en Argentina se mide a partir de la cantidad de metros cuadrados de la planta. La misma tiene la dimensión de 36m x 48m, por lo tanto 1728 m2. Vale aclarar ninguna etapa de nuestro proceso productivo necesita del suministro externo de agua. Por lo que el consumo estará acotado a más que nada a la requerida para necesidades humanas.
Consumo de combustible:
El consumo de combustible estará dado por el que consumirá el clark y el grupo electrógeno.
Por el lado del clarck, al tener uno solo en la fábrica y con un motor diesel de 49 HP, va a consumir un promedio de 10 litros por semana según la estimación brindada por el tecnólogo. Esto nos daría un total de 0,25 litros/hora. Entonces el consumo en año régimen será de 421,75 litros.
En el caso del grupo electrógeno, será utilizado solo en caso de emergencia, por ende no consideramos su consumo.
Mantenimiento y Medios de Control
Se llevará a cabo un mantenimiento preventivo en lo que refiere a cambio de aceite, engrasado, limpieza y repuesto de algunos componentes de las máquinas en general. La última hora de cada turno se la dedicará únicamente a limpieza general de las máquinas y lubricado.
Desarrollamos a continuación particularidades de algunos equipos:
- Sierra: como toda herramienta de corte se debe mantener afilada y limpia. El mantenimiento adecuado, con los bordes bien afilados reduce el riesgo de que la herramienta ceda y la hace más fácil de controlar. La sierra debe estar limpia de restos de materiales (limpieza manual cada todos los días). Se debe aplicar lubricante para mantener las cuchillas en las condiciones óptimas. Tanto las operaciones de mantenimiento, como las de cambio del hoja de corte (se realizará cada un mes y medio), se deben efectuar con la máquina desconectada de la red eléctrica.
- Aboquilladora, dobladora, puente de grúa y mesa de soldado: el mantenimiento que se realizará está basado únicamente en el lubricado y limpieza superficial.
- Cortadora de plasma: el mantenimiento requiere del cambio de los consumibles (toberas y electrodos) cada un mes y medio y limpieza superficial de la máquina.
- Clark: se le hará un service cada 300 horas de uso aproximadamente.
En cuanto a los demás requerimientos se aplicará a todos los equipos mantenimiento correctivo.
Sistemas de Seguridad
Seguridad contra incendios:
De acuerdo a las instalación donde se trabajará y los equipos que usaremos estaremos en riesgo de producciones de fuego tipo C (equipamientos eléctricos, maquinarias, motores, etc.), por lo que instalaremos un sistema de protección activa a través del uso de matafuegos de CO2. Estos actuarán por sofocación y enfriamiento, y son los indicados para tratar con equipos eléctricos.
Se requerirá tener al personal capacitado sobre el método de uso de matafuegos. Se le indicará la forma de quite del seguro, el distanciamiento adecuado (en general se recomiendan 3 metros) y la forma de accionar la palanca y dirigir el extintor a presión. También se hará un plan de evacuación de emergencia para que se libere la zona lo más rápido posible, ya que el uso de estos matafuegos requiere que no haya personas en el ambiente a la hora de activarlos.
Seguridad contra accidentes eléctricos:
Se contará con los elementos de protección requeridos y obligatorios para la instalación eléctrica con la que se va a trabajar. Estos son:
- Llave termomagnética para el actuar ante cortocircuitos o sobrecargas que pueda sufrir la instalación por el uso de maquinarias.
- Disyuntor diferencial para que actúe ante alguna derivación en la instalación o en algún equipo.
- Sistema de Puesta a Tierra con unión eléctrica entre todos los equipos metálicos del proceso productivo para que desvíe la corriente en el caso de fugas a un electrodo que se va a enterrar en el suelo.
Elementos de protección requeridos por el proceso:
Se dotará al personal de planta con los elementos de protección necesarios para evitar riesgos que conlleva el proceso productivo. Los mismos serán:
- Casco de seguridad
- Calzado de seguridad tipo puntera de acero
- Fajas
- Guantes de trabajo y para soldadura
- Protectores visuales (tipo lentes)
- Caretas para soldadura
- Ropa de trabajo
Seguridad en uso de clark y puente de grúa:
Como ya dijimos se le realizará al clarck el service correspondiente para evitar y prevenir fallas. Tanto el uso de éste como el de puente de grúa debe llevarse bajo un protocolo que establezca un procedimiento a realizar que brinde seguridad y logre prevenir posibles accidentes que conlleven lesiones o pérdidas materiales. Algunas medidas básicas son:
- No deben encontrarse operarios bajo las cargas en los izajes.
- Se comunicará a los operarios cuando se realicen movimientos de cargas susceptibles de caerse.
- El encargado de conducir el clarck debe ser un operario capacitado para su manejo. Lo mismo la persona encargada de controlar los izajes del puente grúa.
- La carga que transporte el clark debe ser tal que le permita al conductor tener un amplio panorama visual para evitar posibles incidentes y/o accidentes.
Balance anual de material:
Procedemos en principio a calcular el volumen total ingresado en la primer sección operativa:
Como ya se ha nombrado anteriormente, la columna se compone de 4 tubos de diferentes longitudes y espesores.
- 1 caño de 4,20m., diámetro de 168mm. y espesor de 6,35mm. (volumen de 13537,75 cm3).
- 1 caño de 3m., diámetro de 140mm. y espesor de 4,80mm. (volumen de 6116,68 cm3).
- 1 caño de 3m., diámetro de 114mm. y espesor de 4mm. (volumen de 4146,9 cm3).
- 1 caño de 5m., diámetro de 89mm. y espesor de 3,6mm. (volumen de 4829,256 cm3).
Si sumamos los volúmenes obtenemos que el volumen total de materia prima para una columna es de 28630,586 cm3. El acero 1020 posee un peso específico de 7,87 g/cm3. Por ende el peso de 1 columna es de 225,323 kg.
En año régimen se producen un total de 5589 columnas, entonces el volumen total ingresado en la primer sección operativa será de 1259,33 tn.
Para el cálculo del porcentaje de desperdicio operativo y porcentaje de desperdicio real hay que tener en cuenta que el único proceso que conlleva a desperdicio de toda la línea de fabricación es el de el cortado de la ventana de inspección. Por lo tanto ambos porcentajes serán de igual valor, pues sólo existen desperdicios no recuperables.
La ventana de inspección debe tener las medidas establecidas en la Norma IRAM 2620 (100mm x 170mm) y su corte se realizará en el caño inferior (diámetro de 168mm.). Este caño, posee un espesor de 6,35mm. Por lo tanto el volumen de la ventana es de 107,95 cm3. y el peso de una ventanilla de 0,85kg. A partir de esto obtenemos que en año régimen habrá un total de 4750,65kg. de desperdicio (no recuperable).
% desperdicio real = % desperdicio operativo = 4750,65kg/1259330kg = 0,0377%
Ritmo de trabajo:
Se trabajará de lunes a viernes en un turno de 8hs. Se usarán 7 hs. productivas mientras que la última se la dedicará a limpieza de las máquinas (limpieza de viruta con compresor) y lubricación.
Por lo tanto, en lo que sería cantidad de horas productivas al año partimos de:
365 días/año - 104 días/años (fines de semana) - 10 días/año (feriados) -10 días/año (vacaciones) = 241 días.
Horas activas/año de las máquinas productivas:
HA = 241 días activos/año x 7 horas/día = 1687 horas/año.
En cuanto a los empleados, todos trabajarán de lunes a viernes 8hs.
Horas trabajadas por cada operario:
HT = 241 días activos/año x 8 horas/día = 1928 horas/año
Capacidad real anual de cada sección operativa:
A partir de la información brindada por el tecnólogo se estimaron los distintos coeficientes operativos de cada máquina.
Operación | Cap. teórica por hora | Horas activas al año | Cap. teórica anual | Rendimiento operativo | Capacidad real anual |
Sierra | 16,18
cortes/hora |
1687 hs. | 27289,71 cortes/año | 85% | 23196,25
cortes/año |
Aboquilladora | 41,67 aboquillados/hora | 1687 hs. | 70291,67 aboquillados/año | 90% | 63262,5 aboquillados/año |
Dobladora | 13,9 doblados/hora | 1687 hs. | 23430,56 doblados/año | 90% | 21087,5 doblados/año |
Cortadora por plasma | 13,16 aberturas/hora | 1687 hs. | 22197,37 aberturas/año | 95% | 21087,5 aberturas/año |
Soldadora MIG | 11,76 soldados/hora | 1687 hs. | 19847,06 soldados/año | 85% | 16870 soldados/año |
Pintado | 3,95 pintados/hora | 1687 hs. | 6659,21 | 95% | 6326,25 pintados/año |
Se debe tener en cuenta que una columna involucra:
- 4 cortes en sierra
- 3 aboquillados
- 1 doblado
- 1 abertura
- 3 soldados
- 1 operación de pintado.
Por lo tanto, se hará una capacidad real equivalente en unidades/año:
Operación | Capacidad real anual equivalente |
Sierra | 5799,0625 unidades/año |
Aboquilladora | 21087,5 unidades/año |
Dobladora | 21087,5 unidades/año |
Cortadora por plasma | 21087,5 unidades/año |
Soldado MIG | 5623,333333 unidades/año |
Pintado | 6326,25 unidades/año |
Determinación de la cantidad de máquinas operativas por sección, capacidad real anual de cada sección y aprovechamiento el relación al programa de producción:
Operación | Programa anual de producción (unid/año) | Capacidad real anual equivalente (unid/año) | Cantidad necesaria | Capacidad anual de la sección (unid/año) | Aprovechamiento seccional |
Sierra | 5589 | 5799,0625 | 1 | 5799,0625 | 96,38% |
Aboquilladora | 5589 | 21087,5 | 1 | 21087,5 | 26,50% |
Dobladora | 5589 | 21087,5 | 1 | 21087,5 | 26,50% |
Cortadora por plasma | 5589 | 21087,5 | 1 | 21087,5 | 26,50% |
Soldado MIG | 5589 | 5623,333333 | 1 | 5623,333333 | 99,39% |
Pintado | 5589 | 6326,25 | 1 | 6326,25 | 88,35% |
A partir de la información del cuadro, vemos que la sección de mayor aprovechamiento es la de soldado. Es decir, esta operación es nuestro Cuello de Botella. Su capacidad real es de 5623,33 unidades/año (es decir, lo que produce trabajando al 100% de aprovechamiento). Como no hay recortes intermedios entre esta operación y la última de la línea, la cantidad anual que sale de la última operación también será 5623 unidades. Esa será nuestra capacidad máxima.
Determinación de la Evolución de Mercaderías
Tiempos de Entrega , envío de Mercaderías, tamaños y Frecuencias de Compras
Elemento | Cantidad x compra | Frecuencia compra | Lead-Time |
Columna de acero | 30 ton | Semanal | 3 dias habiles |
Pintura | |||
Cromato de zinc | 45 litros | Cada 3 semanas | 1 semana |
Sintetico Duo | 65 litros | Cada 3 semanas | 1 semana |
Brea Asfaltica | 20 litros | Semanal | 1 dia habil |
Soldadura | |||
Rollo alambre | 40 rollos | Cada 2 meses | 4 dias habiles |
Gas | 50 m3 | Cada 2 semanas | 4 dias habiles |
Mecha | 2 unidades | Mensual | 4 dias habiles |
Macho | 2 | Mensuak | 4 dias habiles |
Boca inspeccion | |||
Chapa | 485 unidades | Mensual | 10 dias |
Tornillos | 10000 unidades | Semestral | 10 dias |
Bronce | 1kg | Semanal | 4 dias habiles |
Luminaria | 485 unidades | Mensual | 10 dias |
Cableado | 12000 metros | Mensuales | 1 semana |
Volúmenes de producción
Basado en el plan de ventas y teniendo en cuenta el diseño de nuestro lay-out, tenemos que mensualmente la empresa realizaria 486 unidades contando con 15 días de vaciones en la cual la planta permanecerá cerrada. Con un periodo de puesta en marcha de 4 meses, debido a la complejidad de realizar la puesta en marcha de nuestra aboquilladora de deformado en frio, equipos de transporte sumado a los ensayos que deben realizarse. Esto nos da:
Puesta en marcha:
Mes | Ritmo Produccion incial | Ritmo Produccion Final | Ritmo Produccion prom. | Produccion Mensual | Prod. Propuesta(uds) |
1 | 0% | 20% | 10,0% | 486 | 49 |
2 | 20% | 45% | 32,5% | 486 | 158 |
3 | 45% | 70% | 57,5% | 486 | 279 |
4 | 70% | 100% | 85,0% | 486 | 413 |
Volúmenes de venta:
Vol.Año 1 | 4544 | unidades |
Vol.Año 2 | 5589 | unidades |
Vol.Año 3 | 5589 | unidades |
Vol.Año 4 | 5589 | unidades |
Vol.Año 5 | 5589 | unidades |
Stock promedio
Nuestra planta realizara entregas cada 10 días contando con un stock de segurar de 3 días en promedio. Esto representan 15 toneladas de MP. Teniendo en cuenta que la producción diaria es de 22 unidades, nuestro stock variara entre 15 y 50 toneladas. Esto nos dará un stock promedio de 32.5 toneladas.
Evolución de las ventas
En el año 1 tendremos la puesta en marcha y la fabricación del stock promedio, por lo que nuestra evolución de las ventas sera:
Ventas año 1 | 4400 | unidades |
Ventas año 2 | 5589 | unidades |
Ventas año 3 | 5589 | unidades |
Ventas año 4 | 5589 | unidades |
Ventas año 5 | 5589 | unidades |
Materias primas
En nuestra puesta en marcha por lo comentado anteriormente tendremos un 70% extra de desperdicios. por lo que nuestro consumo de materia prima sera:
Consumo MP año 1 | 343,9 | toneladas | |
820,4 | toneladas | ||
Total año 1 | 1164,3 | toneladas | |
Consumo 2 al N | 1258,0 | toneladas |
Siendo 343,9 toneladas la consumida durante la puesta en marcha.
En proceso tendremos (teniendo en cuenta que tomamos un ciclo igual a la entregas de 10 días):
Prod. Termin | 49,95 | toneladas |
Desp no rec | 0,01883115 | toneladas |
Por lo que el consumo total de materia prima por año sera:
Total año 1 | 1214,25 | toneladas |
Total año 2 | 1258,0 | toneladas |
Total año 3 | 1258,0 | toneladas |
Total año 4 | 1258,0 | toneladas |
Total año 5 | 1258,0 | toneladas |
Stock de seguridad y mensual promedio
Contaremos con un stock de seguridad de 15 toneladas como dijimos antes. Las compras de los caños, nuestro insumo principal, se realizara de manera semanal. Tendremos un stock promedio de 22,5 toneladas semanalmente. (variacion entre 15 y 45 toneladas).
Resumen de materiales
Periodo instalacion | Año 1 | Año 2 al 5 | |
Ventas | 990 | 1257,5 | |
Stock prom elaborado | 32,5 | 32,5 | |
Produccion | 1022,4 | 1257,5 | |
Desperdicios | 0,458 | 0,474 | |
En curso y SE | 49,95 | 49,95 | |
Consumo | 1072,81 | 1258,00 | |
Stock Mp | 200 | 109,6 | 109,6 |
Compra MP | 200 | 982,41 | 1258,00 |
Las 200 toneladas del periodo de instalación se utilizaran para comenzar la puesta en marcha en el año 1.
Todos los valores están expresados en toneladas. Correspondiendo 0,225 toneladas por Producto termiando.
Determinación del Personal
Organigrama
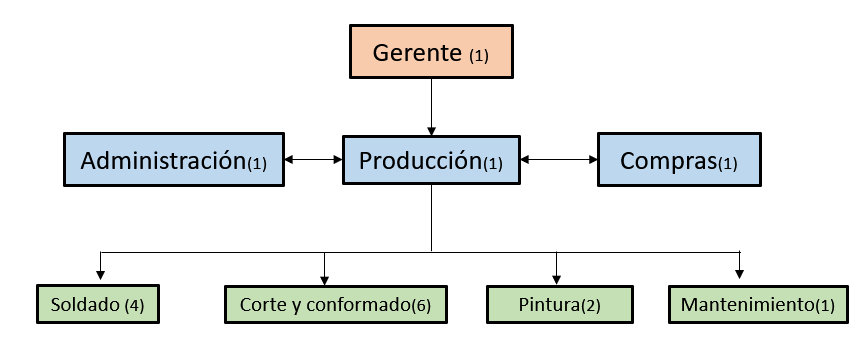
Descripción de los Puestos de Trabajo
Recepción de Materia Prima:
Descarga con autoelevadores de los caños al depósito con autoelevador.
Por la cercanía al lugar, se encargarán los dos operarios del sector de Corte.
Abastecimiento de insumos a puestos, retiro de residuos de puestos, movimiento de producto semielaborado (caños, no columna sin pintar):
Actividades de acarreo de materiales y retiro de descartes de los puestos de trabajo. Movimiento de un puesto a otro de productos semielaborados: específicamente previo al conformado de la estructura, cuando los semielaborados aun son caños.
Por la cantidad de tiempo ocioso del puesto de Aboquillado, las dos personas de dicho sector se encargarán, además, de las tareas de este puesto. Para ello, utilizarán autoelevadores.
Sector de Corte:
Cortado de los caños a las medidas requeridas con sierras sin fin., ademas de la recepción de materias primas.
En este puesto por turno se asignarán dos personas.
Aboquillado:
Operación de aboquilladora. En este puesto se asignan dos operarios por turno.
Doblado:
Operación con maquina dobladora. En este puesto se asigna un operario por turno.
Mesa de Trabajo:
Corte de plasma para corrección de imperfecciones derivadas del sector Corte, agujereado y conformado de la ventana de inspección. Soldado de la puesta a tierra.
Al puesto se asignan dos operarios, uno como soldador y otro como auxiliar de este último.
Mesa de Soldado:
Soldado de la estructura con soldadura MIG, utilizando mesa giratoria. Carga de estructura a carro especial con aparejo. Transporte a sector de pintado con carro especial.
Al puesto se asignan tres operarios, uno como soldador y dos como auxiliares de este último.
Pintado:
Pintado con pistola de pintura de antioxido. Pintado con inmersión de la estructura. Pintura manual de brea en la base con rodillo manualmente. Utilización de puente grua. Traslado a zona de producto terminado.
Al puesto se asignan 2 operarios.
Compras de abastecimiento de materia prima, materiales, insumos productivos, e insumos de mantenimiento. Programación de la producción. Jefatura de planta:
Se asignan dos personas para las tareas mencionadas, y una persona auxiliar.
Mantenimiento mecánico:
Se asigna un operario al puesto.
Calificación y Formación
Requerimientos por Puesto | ||||||
---|---|---|---|---|---|---|
Sector | Nombre del puesto | Formación obligatoria | Experiencia deseada | Experiencia obligatoria | Capacitaciones | |
Recepción de MP y Corte | Operario 1 | Técnico | Manejo de maquinaria | Operario industrial metalúrgico | Clarkista; Operación de sierra | |
Operario 2 | Técnico | Manejo de maquinaria | Operario industrial metalúrgico | Clarkista; Operación de sierra | ||
Aboquillado | Operario 3 | Técnico | Clarkista; Manejo de maquinaria | Operario industrial metalúrgico | Clarkista; Manejo de aboquilladora | |
Operario 4 | Técnico | Clarkista; Manejo de Maquinaria | Operario industrial metalúrgico | Clarkista; Manejo de aboquilladora | ||
Doblado | Operario 5 | Técnico | Manejo de maquinaria | Operario industrial metalúrgico | Manejo de maquina de doblado | |
Mesa de trabajo | Operario 6 | Técnico | Manejo de maquinaria | Operario industrial metalúrgico | Manejo de maquinaria y asistencia al soldador | |
Operario 7 | Técnico; Soldador con Certificación | Soldado de cañerías y tubos | Operario industrial metalúrgico; soldador | |||
Mesa de soldado | Operario 8 | Técnico | Manejo de maquinaria | Operario industrial metalúrgico | Manejo de maquinaria; asistencia al soldador; carga y manipulación con aparejo | |
Operario 9 | ||||||
Operario 10 | Técnico; Soldador con Certificación | Soldado de cañerías y tubos | Operario industrial metalúrgico; soldador | Carga y manipulación con aparejo | ||
Pintado | Operario 11 | Técnico | Manejo de herramientas de pintado; Manejo de puente grúa | Operario industrial metalúrgico | Manejo de herramental de pintado; mantenimiento de herramental de pintado; manejo de puente grúa | |
Operario 12 | Técnico | Manejo de herramientas de pintado; Manejo de puente grúa | Operario industrial metalúrgico | Manejo de herramental de pintado; mantenimiento de herramental de pintado; manejo de puente grúa | ||
Mantenimiento | Mecánico | Técnico electromecanico | Mantenimiento mecánico | |||
Oficinas y recepción | Jefe de planta y programación | Técnico | Operario industrial metalúrgico; Programación de producción | Programación de producción | ||
Compras de abastecimiento productivo y de mantenimiento | Técnico | Mantenimiento; personal administrativo en empresa industrial | Personal administrativo en empresa industrial | Procedimientos de compra | ||
Recepcionista y cadetería | Secundario completo | Cadete; recepcionista |
Listado de Equipos Auxiliares, Muebles y Útiles
Producción
- Autoelevadores Toyota 25: en el área de producción se cuenta con dos de estos equipos, para el movimiento de producto semielaborado entre los puestos de Corte de Caños a Aboquillado, de este último a Doblado y Mesa de Trabajo, y de este último a Mesa de Soldado. También se utilizan para el abastecimiento de materiales e insumos a los puestos.
- Puente Grúa: en el sector de pintado para el movimiento de las columnas sin pintar y en proceso intermedio de pintado hasta el lugar de productos terminados.
- Aparejo sobre cama de soldado
- Carro diseñado a medida para recibir material en proceso del aparejo de la cama de soldado, y transportar los semielaborados al sector de pintado.
Administración
- Juegos de escritorio, estantes, archivadores, sillas: dos de estos juegos para el equipamiento de la sala oficina junto a la planta.
- Útiles de oficina: resmas de hojas A4, lapiceras, fibrones, cinta scotch, clips, chinches, plancha de corcho, bandejas archivadoras.
Anteproyecto de Planta
Plano de Planta
Se realizo en Autocad un posible plano de planta de la instalación. Es un espacio techado de 36x48metros con una altura de 8,5metros en el sector de planta y de 3 metros en oficinas siendo esta una construcción aparte. El sector de planta cuenta con las siguientes instalaciones:
Identificacion | Descripción |
---|---|
1 | Mesa soldado |
2 | Deposito Insumos |
3 | Aboquilladora |
4 | Dobladora |
5 | Torno |
6 | Mesa de trabajo#1 |
7 | Mesa de trabajo#2 |
8 | Pintado |
9 | Sierra sensitiva |
10 | Puente grua |
A1 | Almacen MP |
A2 | Almacen PT |
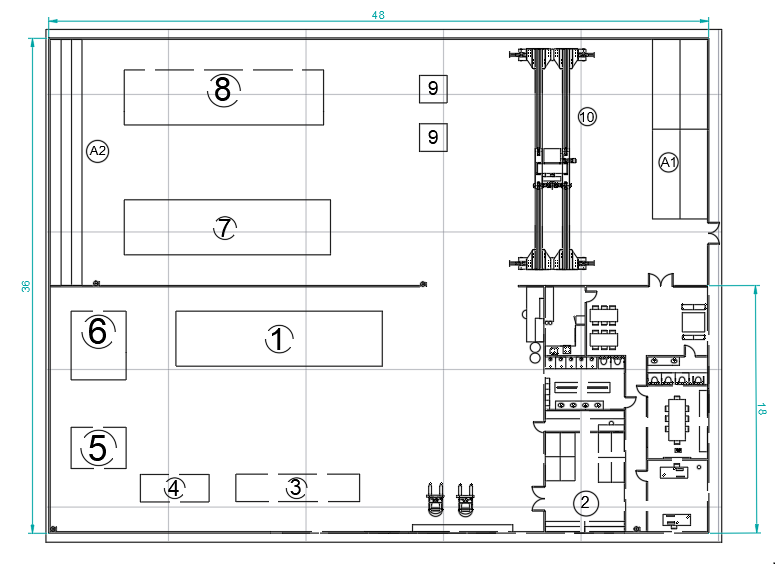
Recorrido de Materiales
Para los diagramas de flujos se decidió por adjuntarlos separados por las distintas denominaciones de caños ya que, de acuerdo a sus especificaciones, es colocado en lugares específicos del producto final y conllevan distintos procesos.
Primero comenzamos con los caños de 168mm de diámetro. El recorrido que realiza a lo largo de todo el proceso es el siguiente:
Deposito Materias Primas --> Cortado --> Aboquillado --> Corte Ventana Inspección y Colocación PAT --> Soldado --> Pintado --> Cableado --> Deposito Producto Terminado.
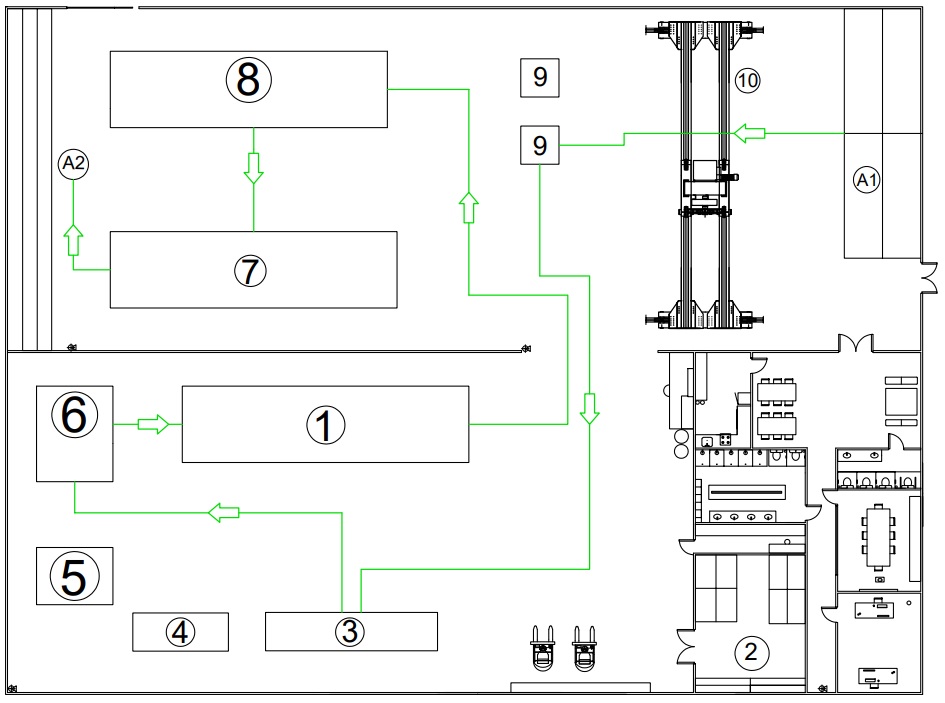
En el siguiente gráficos se pueden ver los recorridos dentro de la planta de los caños de 140mm y 114mm. Los mismos se grafican dentro del mismo plano debido a que sufren el mismo proceso. El recorrido que realiza a lo largo de todo el proceso es el siguiente:
Deposito Materias Primas --> Cortado --> Aboquillado --> Soldado --> Pintado --> Cableado --> Deposito Producto Terminado.
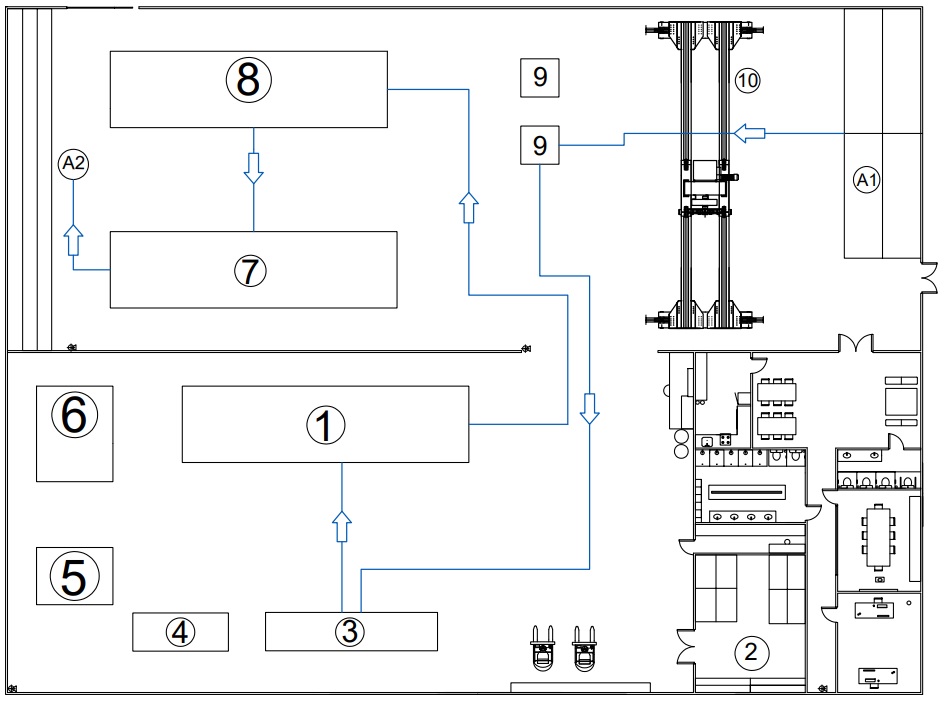
En tercer lugar, colocamos el diagrama de flujo de los caños de 89mm. Estos tienen un proceso distinto al resto ya que se les realiza un doblado para obtener la curva caracteristica de las luminarias en su extremo superior. El recorrido que realiza a lo largo de todo el proceso es el siguiente:
Deposito Materias Primas --> Cortado --> Aboquillado --> Doblado --> Soldado --> Pintado --> Cableado --> Deposito Producto Terminado.
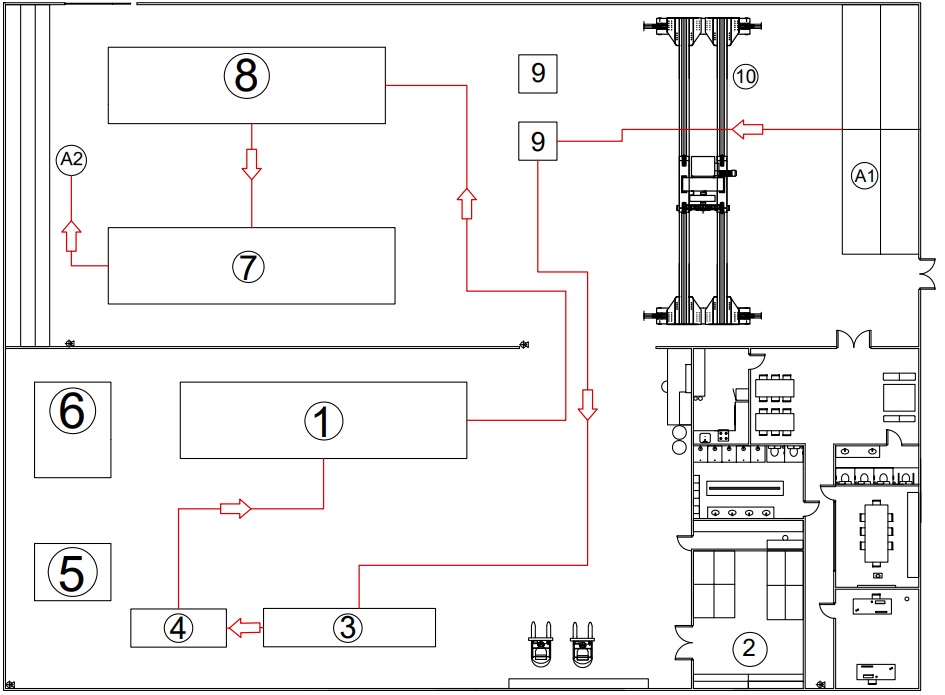
En cuarto lugar mencionaremos los flujos del material de cableado. Por mas simple que sea es una parte importante de nuestras columnas para luminaria. El recorrido que realiza a lo largo de todo el proceso es el siguiente:
Deposito Materias Primas --> Soldado --> Deposito Producto Terminado.
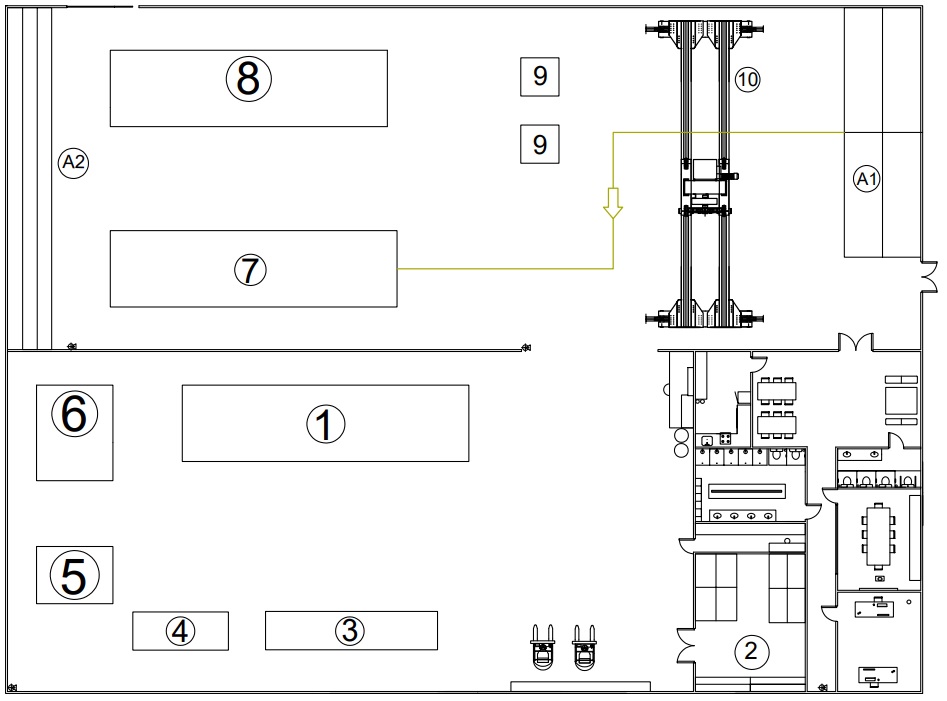
Por ultimo, adjuntamos un diagrama que muestra las zonas de trabajo del montacargas y el puente de grúa.
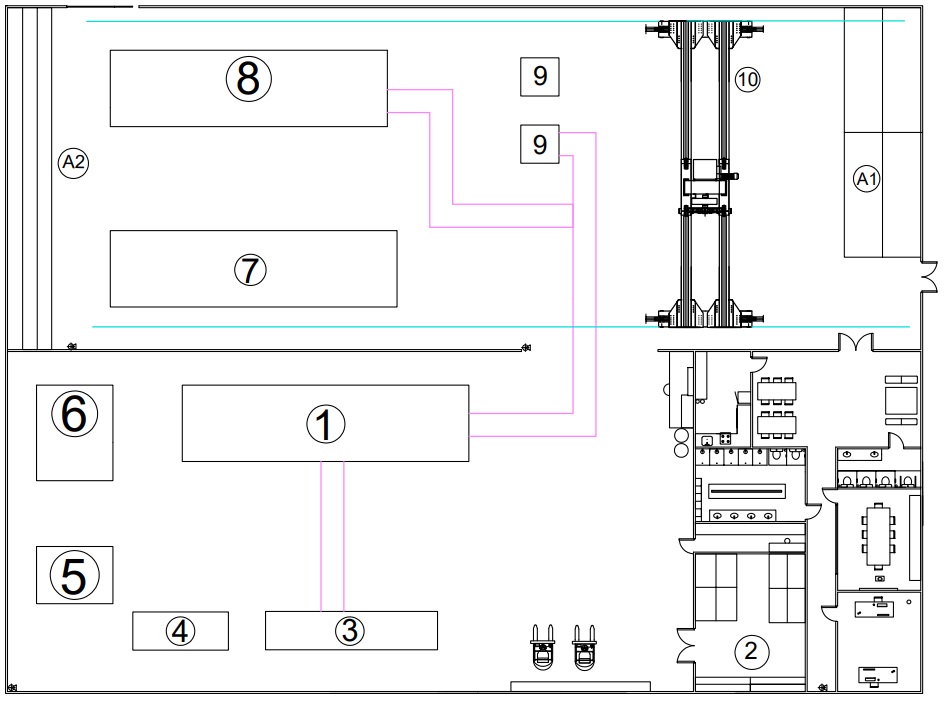
Cronograma de Ejecución
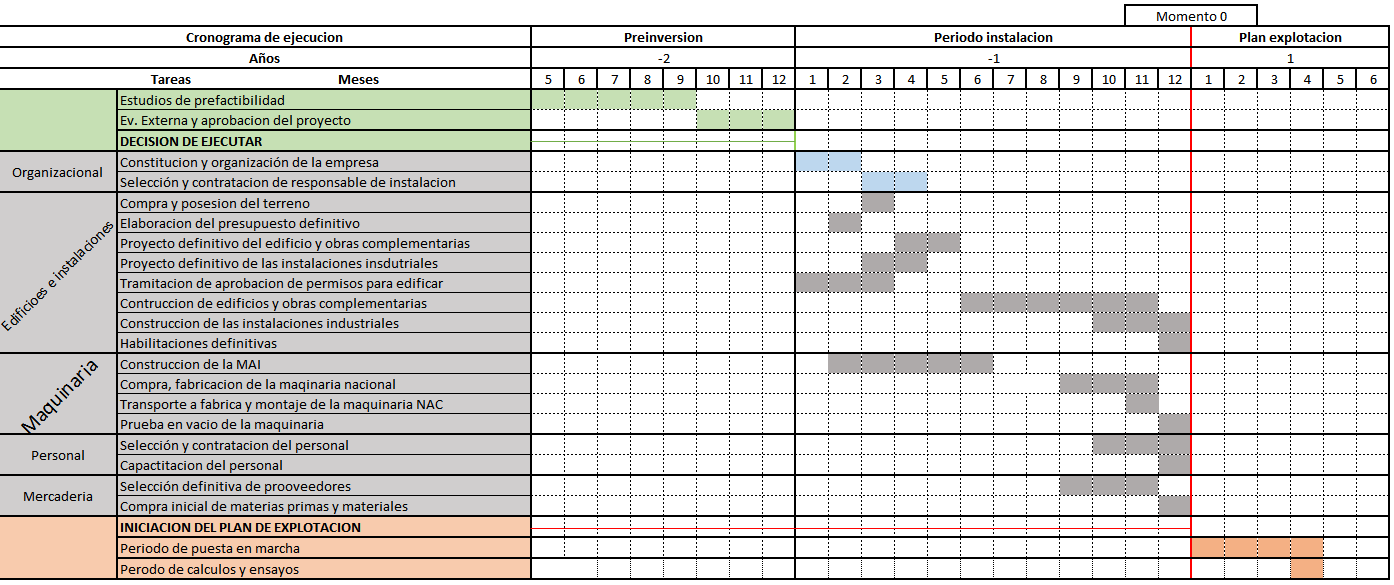