Diferencia entre revisiones de «2021/Grupo13/DimensionamientoFisico»
(No se muestran 12 ediciones intermedias de 3 usuarios) | |||
Línea 331: | Línea 331: | ||
'''Recepción y almacén de materias primas.''' | '''Recepción y almacén de materias primas.''' | ||
Las placas de melamina se reciben del proveedor en conjuntos de 10 placas | Las placas de melamina se reciben del proveedor en conjuntos de 10 placas que son enviadas en un camión el cual es descargado por los operarios de la siguiente manera: | ||
En esta fase, la materia prima queda | Primero se coloca una escalera para facilitar el acceso de los 2 operarios que ingresan al camión. Luego, con la ayuda de una carretilla elevadora dotada de un brazo tensor en su extremo, se toman las placas (de a una por vez) y se llevan al almacén. | ||
En esta fase, la materia prima queda guardada en el almacén de madera de forma que se coloque equitativamente los tipos de materia prima (el color de la melamina). La cantidad de placas de cada color que se asignan a cada componente corresponde con la cantidad de placas necesarias para cumplir con el plan de producción. | |||
'''Transporte a la sección de corte.''' | '''Transporte a la sección de corte.''' | ||
Los operarios transportan las placas en zorras a la sección de corte y quedan | Los operarios transportan las placas en zorras a la sección de corte y estas quedan dispuestas de forma tal que el operario tome siempre la placa que se encuentra por encima del resto. | ||
'''Corte de melamina y fibroplus.''' | '''Corte de melamina y fibroplus.''' | ||
Línea 347: | Línea 349: | ||
'''Transporte de piezas cortadas.''' | '''Transporte de piezas cortadas.''' | ||
Se transportan las piezas al área de pegado de cantos. | Se transportan las piezas al área de pegado de cantos de manera manual a medida que la sección de pegado de cantos lo requiera. | ||
'''Pegado de cantos y lijado.''' | '''Pegado de cantos y lijado.''' | ||
Línea 355: | Línea 357: | ||
'''Control de calidad.''' | '''Control de calidad.''' | ||
Se hace el CC a la salida de la máquina pega cantos para evitar defectos de fabricación. El CC consiste en un control visual del pegado y un lijado fino de las piezas. | Se hace el CC a la salida de la máquina pega cantos para evitar defectos de fabricación. El CC consiste en un control visual del pegado y un lijado fino de las piezas si el borde las mismas es filoso (un operario realiza ambas tareas). | ||
'''Transporte de piezas con canto.''' | '''Transporte de piezas con canto.''' | ||
Se transportan las piezas al área de agujereado. | Se transportan las piezas al área de agujereado de forma manual a medida que la sección de agujereado lo requiera. | ||
'''Agujereado.''' | '''Agujereado.''' | ||
En esta etapa se hace el agujereado manual en las piezas | En esta etapa se hace el agujereado manual en las piezas. Aquí el operario coloca el semielaborado en una esquina y utiliza matrices de agujereado que ya tiene a su disposición en el área de trabajo las cuales al colocarlas sobre la madera le indica al trabajador donde se debe agujerear la pieza y este marca con un lápiz los agujeros. Luego retira la matriz y realiza los agujeros con un taladro manual. | ||
Las piezas que no requieren esta operación esperan a pie de máquina a que el lote completo esté disponible para llevar al área de embalado. | Las piezas que no requieren esta operación esperan a pie de máquina a que el lote completo esté disponible para llevar al área de embalado. | ||
Línea 369: | Línea 371: | ||
'''Transporte de piezas terminadas a embalado.''' | '''Transporte de piezas terminadas a embalado.''' | ||
Se transportan las piezas al área de embalado. | Se transportan las piezas al área de embalado de forma manual según el sector lo requiera. | ||
'''Control de calidad.''' | '''Control de calidad.''' | ||
Se hace el CC previo al embalado | Se hace el CC visual previo al embalado con la finalidad de garantizar que las piezas cumplan con las tolerancias requeridas por el cliente. | ||
'''Embalado.''' | '''Embalado.''' | ||
Se realiza el embolsado de los herrajes, tornillos y clavos necesarios para la orden de producción. Luego se colocan en la mesa de trabajo y | Se realiza el embolsado de los herrajes, tornillos y clavos necesarios para la orden de producción. Luego se colocan en la mesa de trabajo y espera a que lleguen las piezas de madera. Cuando llegan, se hace el embalado del producto terminado utilizando cajas, material de embalaje y cinta. | ||
== Determinación de las maquinas e instalaciones == | == Determinación de las maquinas e instalaciones == | ||
=== Ficha Técnica de las Maquinas === | === Ficha Técnica de las Maquinas === | ||
[[Archivo:Fichatecnica pegacantos.png|no|miniaturadeimagen]] | Maquina Pega cantos[[Archivo:Fichatecnica pegacantos.png|no|miniaturadeimagen]] | ||
Máquina Escuadradora[[Archivo:Escuadrado.png|no|miniaturadeimagen]] | |||
=== Especificaciones técnicas de las maquinas === | === Especificaciones técnicas de las maquinas === | ||
Línea 500: | Línea 504: | ||
| colspan="1" rowspan="2" |Unidades | | colspan="1" rowspan="2" |Unidades | ||
|- | |- | ||
|- | |||
| | |||
| | |||
| | |||
| | |||
| | |||
| | |||
|- | |- | ||
|A | |A | ||
Línea 617: | Línea 628: | ||
| colspan="1" rowspan="2" |PT/hs | | colspan="1" rowspan="2" |PT/hs | ||
|- | |- | ||
|- | |||
| | |||
| | |||
| | |||
| | |||
| | |||
| | |||
| | |||
|- | |- | ||
| colspan="2" rowspan="2" |Embalado | | colspan="2" rowspan="2" |Embalado | ||
Línea 1418: | Línea 1437: | ||
Gerente Producción: su función es la planificación programación y control de la producción, es el nexo entre el área productiva y el área administrativa de la empresa. | Gerente Producción: su función es la planificación programación y control de la producción, es el nexo entre el área productiva y el área administrativa de la empresa. | ||
{| class="wikitable" | |||
|Sector | |||
|Cantidad de operarios | |||
|Nivel de educación | |||
|Capacitación | |||
|- | |||
|Corte | |||
|7 | |||
|Secundario completo | |||
|Si | |||
|- | |||
|Pega Cantos | |||
|4 | |||
|Secundario completo | |||
|Si | |||
|- | |||
|Lijado y CC | |||
|2 | |||
|Secundario completo | |||
|Si | |||
|- | |||
|Embalado | |||
|4 | |||
|Secundario completo | |||
|Si | |||
|- | |||
|Contador | |||
|1 | |||
|Estudiante avanzado de lincenciatura en contabilidad | |||
|No | |||
|- | |||
|Gerente de admin | |||
|1 | |||
|Gradudado de carreras afines a administración | |||
|No | |||
|- | |||
|Gerente de prod | |||
|1 | |||
|Ingeniero industrial Industrial | |||
|No | |||
|} | |||
== Listado de Equipos Auxiliares, Muebles y Útiles. == | == Listado de Equipos Auxiliares, Muebles y Útiles. == | ||
Línea 1466: | Línea 1526: | ||
|- | |- | ||
|Microondas | |Microondas | ||
|1 | |1 | ||
|- | |- | ||
Línea 1503: | Línea 1560: | ||
== Cronograma de Ejecución == | == Cronograma de Ejecución == | ||
[[Archivo: | [[Archivo:Explotacion11.png|sinmarco|900x900px]] |
Revisión actual - 00:27 20 jul 2021
Determinación de la Localización
Matriz de localización
Para determinar la localización de nuestra operación realizaremos una matriz de localización. En la misma enumeramos una lista de factores fundamentales, a los cuales se les asigno un factor de importancia (con 1 siendo poca importancia y 5 mucha importancia). Luego, a cada alternativa se le asignó un factor de disponibilidad para cada factor en los cuales 1 significa poca disponibilidad y 5 mucha disponibilidad de dicho factor.
A partir del análisis de la matriz, se decide por la alternativa 1, ubicada en la zona de Floresta, Capital Federal.
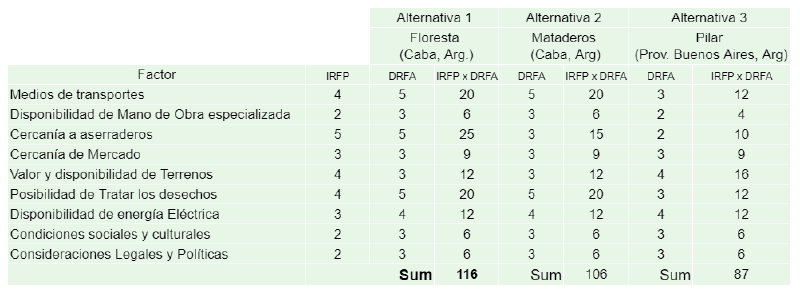
Definición Técnica del Producto
Planos y/o Dibujos
Listado de Materiales (BOM)
ITEM | DENOMINACIÓN | NIVEL | CANTIDAD | UNIDAD | OBSERVACIÓN | |||||
1 | 2 | 3 | ||||||||
1 | Escritorio | X | 1 | Unidad | ||||||
2 | Lateral A | X | 1 | Unidad | 76 x 44,5 cm | |||||
3 | Lateral B | X | 1 | Unidad | 76 x 44,5 cm | |||||
4 | Tapa C | X | 1 | Unidad | 100 x 45 cm | |||||
5 | Columna D | X | 1 | Unidad | 38,5 x 28 cm | |||||
6 | Escuadra F | X | 1 | Unidad | 32,5 x 12 cm | |||||
7 | Escuadra E | X | 1 | Unidad | 97 x 28 cm | |||||
8 | Frente cajon G | X | 2 | Unidad | 33,5 x 13,5 cm | |||||
9 | Lateral cajon H | X | 4 | Unidad | 30 x 11 cm | |||||
10 | Trasero cajon I | X | 2 | Unidad | 27 x 11 cm | |||||
11 | Fondo cajon J | X | 2 | Unidad | 29,5 x 29,5 cm | |||||
12 | Bolsa | X | 1 | Unidad | ||||||
13 | Tirador | X | 2 | Unidad | ||||||
14 | Perno minifix Q | X | 4 | Unidad | ||||||
15 | Tornillos P | X | 8 | Unidad | ||||||
16 | Clavos | X | 7 | Unidad | ||||||
17 | Tornillos Y | X | 8 | Unidad | ||||||
18 | Tornillos J | X | 4 | Unidad | ||||||
19 | Tornillos W | X | 8 | Unidad | ||||||
20 | Tornillos Z | X | 6 | Unidad | ||||||
21 | Perno minifix Q | X | 6 | Unidad | ||||||
22 | Patin plastico | X | 4 | Unidad | ||||||
24 | Cajas | X | 1 | Unidad | ||||||
25 | Cinta de embalar | X | - | - | ||||||
26 | Material para embalaje | X | - | - | ||||||
27 | Caja | X | ||||||||
28 | Correderas | X | 2 | Unidad | Una izquierda y una derecha |
Diagrama Arbóreo
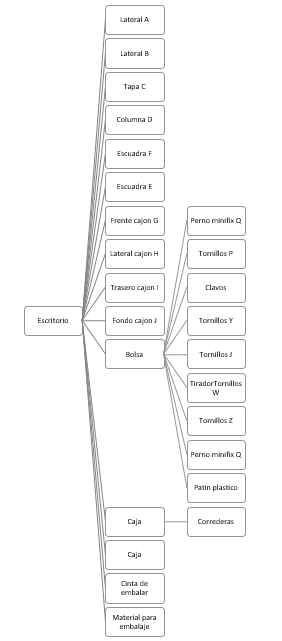
Especificaciones físicas
Especificaciones técnicas del producto:
Escritorio Muena | ||
Codigo | Dimensiones (cm) | Peso (kg) |
.E001 | 100 x 77 x 45 | 21.5 |
Especificaciones embalaje:
Dimensiones (cm) |
44 x 8 x 90 |
Con el producto se incluyen:
Normas aplicables
La fabricación de muebles de melamina no tiene ninguna norma específica de la industria. Sin embargo, se va a tener que cumplir con la ley 19587 que establece las reglamentaciones de higiene y seguridad del trabajo. Entre las partes más destacables de la ley se encuentra el artículo 4, en el cual se especifica que se deben tomar medidas para proteger, preservar y mantener la integridad psicofísica de los trabajadores; se debe prevenir, reducir, eliminar o aislar los riesgos de los distintos centros o puestos de trabajo.
Características y condición del producto
El producto será entregado desarmado, dentro de una caja con secciones para las diferentes partes del mueble (cajón y estructura). Dentro de la caja también habrá un set de pasos para poder realizar el armado del mismo.
Plan de ensayos
El plan de ensayos en el proceso productivo tendrá dos etapas:
- La primera será a la mitad del proceso de forma visual para controlar que el lijado de la madera esté bien hecho.
- La segunda será de forma visual antes del embalaje y controlará que los productos cumplan con las tolerancias requeridas para el posterior armado por parte del cliente.
Acondicionamiento del Producto
El producto se presentará en una caja de cartón con la identificación de la marca y el detalle del mueble que contiene.
Dentro de cada caja se colocará:
- Un folleto con el manual de usuario y una guía para el ensamblado del mueble
- Certificado de garantía, con el detalle del tiempo de garantía y las condiciones generales.
- Todas las piezas necesarias para poder ensamblar el producto de manera correcta.
Las piezas se colocarán dentro de una caja para preservar la integridad del producto en el traslado del mismo para evitar que las maderas tengan contacto con el exterior. Las piezas metálicas (herrajes) estarán dentro de una bolsa para evitar que con el movimiento de la caja estas piezas dañen la madera.
La caja del producto tendrá cinta de embalar para evitar que la caja se abra durante el traslado.
Definición del Proceso de Producción
Diagrama de Flujo de Fabricación y Control
Cursograma Sinóptico de Proceso (CSP)
Descripción de cada etapa del proceso productivo.
Recepción y almacén de materias primas.
Las placas de melamina se reciben del proveedor en conjuntos de 10 placas que son enviadas en un camión el cual es descargado por los operarios de la siguiente manera:
Primero se coloca una escalera para facilitar el acceso de los 2 operarios que ingresan al camión. Luego, con la ayuda de una carretilla elevadora dotada de un brazo tensor en su extremo, se toman las placas (de a una por vez) y se llevan al almacén.
En esta fase, la materia prima queda guardada en el almacén de madera de forma que se coloque equitativamente los tipos de materia prima (el color de la melamina). La cantidad de placas de cada color que se asignan a cada componente corresponde con la cantidad de placas necesarias para cumplir con el plan de producción.
Transporte a la sección de corte.
Los operarios transportan las placas en zorras a la sección de corte y estas quedan dispuestas de forma tal que el operario tome siempre la placa que se encuentra por encima del resto.
Corte de melamina y fibroplus.
Las placas y fibroplus se cortan según las medidas que correspondan a cada pieza en las escuadradoras. Las piezas estarán identificadas por sus dimensiones. Se obtienen los siguientes cortes:
Transporte de piezas cortadas.
Se transportan las piezas al área de pegado de cantos de manera manual a medida que la sección de pegado de cantos lo requiera.
Pegado de cantos y lijado.
Esta operación se realizará con la máquina pega cantos, la cual realiza el pegado y un lijado primario a los cantos de la melamina, dejando los cantos con defectos en algunos casos, es por eso que luego se hace un control de calidad.
Control de calidad.
Se hace el CC a la salida de la máquina pega cantos para evitar defectos de fabricación. El CC consiste en un control visual del pegado y un lijado fino de las piezas si el borde las mismas es filoso (un operario realiza ambas tareas).
Transporte de piezas con canto.
Se transportan las piezas al área de agujereado de forma manual a medida que la sección de agujereado lo requiera.
Agujereado.
En esta etapa se hace el agujereado manual en las piezas. Aquí el operario coloca el semielaborado en una esquina y utiliza matrices de agujereado que ya tiene a su disposición en el área de trabajo las cuales al colocarlas sobre la madera le indica al trabajador donde se debe agujerear la pieza y este marca con un lápiz los agujeros. Luego retira la matriz y realiza los agujeros con un taladro manual.
Las piezas que no requieren esta operación esperan a pie de máquina a que el lote completo esté disponible para llevar al área de embalado.
Transporte de piezas terminadas a embalado.
Se transportan las piezas al área de embalado de forma manual según el sector lo requiera.
Control de calidad.
Se hace el CC visual previo al embalado con la finalidad de garantizar que las piezas cumplan con las tolerancias requeridas por el cliente.
Embalado.
Se realiza el embolsado de los herrajes, tornillos y clavos necesarios para la orden de producción. Luego se colocan en la mesa de trabajo y espera a que lleguen las piezas de madera. Cuando llegan, se hace el embalado del producto terminado utilizando cajas, material de embalaje y cinta.
Determinación de las maquinas e instalaciones
Ficha Técnica de las Maquinas
Maquina Pega cantos
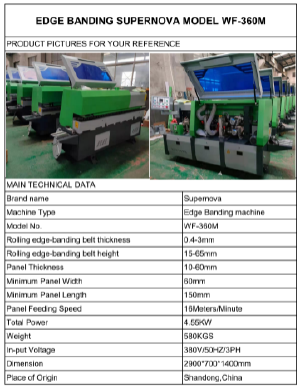
Máquina Escuadradora
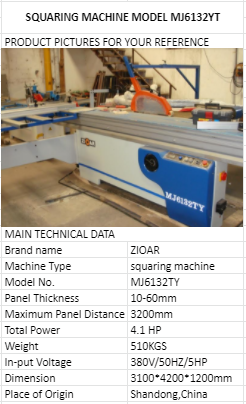
Especificaciones técnicas de las maquinas
Capacidad de la escuadradora
A continuación se puede observar un cuadro en el cual se ven los cálculos realizados para calcular la capacidad de cada máquina según la producción de producto terminado. Los desperdicios están calculados con un método de trabajo que consiste en utilizar placas enteras de melamina para la fabricación de cada pieza del producto terminado. Los tiempos de corte por pieza están calculados como 2 cortes por cada pieza, ya que las otras dos esquinas son los bordes de la placa.
Dado que la velocidad de corte es de 50cm/min lo único que hay que calcular para saber cuanto tiempo de corte hay por pieza es multiplicar este número por el largo de los laterales específicos de la pieza.
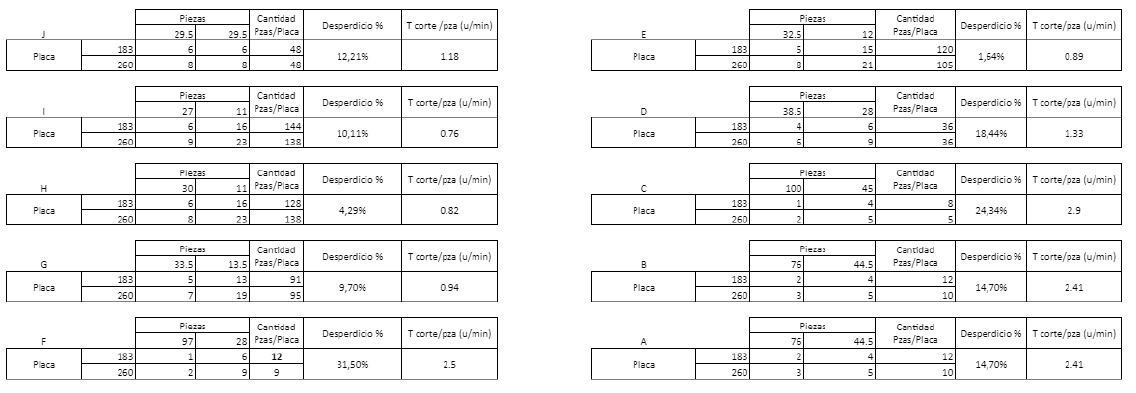
Con los datos calculados en el cuadro anterior y el plan de ventas del dimensionamiento comercial calculamos la cantidad diaria de placas que va a necesitar el proceso productivo para poder cumplir con la planificación de producción anual.
Q diaria
(unidad) |
Q por placa (unidad) | Cantidad de placas por día | |
Tapa C | 186 | 8 | 24.0 |
Columna D | 186 | 36 | 6.0 |
Escuadra F | 186 | 120 | 2.0 |
Escuadra E | 186 | 12 | 16.0 |
Frente cajon G | 372 | 95 | 4.0 |
Lateral cajon H | 744 | 138 | 6.0 |
Trasero cajon I | 372 | 144 | 3.0 |
Fondo cajon J | 372 | 48 | 8.0 |
Lateral A | 186 | 12 | 16.0 |
Lateral B | 186 | 12 | 16.0 |
Total | 101.0 |
Una vez obtenidos el tiempo de corte por unidad de producto terminado, la cantidad de unidades a fabricar por día y la cantidad de placas utilizadas por día, realizamos estimaciones para el tiempo de carga (10 segundos por placa), el tiempo de descarga (30 segundos por placa) y al tiempo de preparación (estimado en 51 segundos).
Estas estimaciones las multiplicamos por la cantidad de placas que se deben cortar y luego lo dividimos por la cantidad de unidades de producto terminado que se fabrican por día y, sumado al tiempo de corte y el tiempo de manipuleo (que estimamos es la mitad del tiempo de corte), obtenemos la cantidad de tiempo utilizado para producir una unidad de producto terminado. La inversa de dicho número es la capacidad.
T corte PT | T prep | Carga | Descarga | Manipuleo |
16.14 | 51.76 | 16.83333333 | 50.5 | 8.07 |
T por PT | 24.85028674 | min/u | ||
Capacidad | 2,24 | u/hs |
Capacidad de la Maquina Pega cantos
Los cantos en las piezas se pegan únicamente para aquellos bordes visibles, es decir, si el borde de una madera está en contacto con otra madera, este lado no llevará canto. Por esta razón no se colocan los 4 cantos en todas las piezas
Pieza | Cantos a pegar por pieza | cm de canto por unidad | Piezas por escritorio | cm de canto por escritorio | Unidades |
A | 3 | 196.5 | 1 | 196.5 | cm |
B | 3 | 196.5 | 1 | 196.5 | cm |
C | 4 | 290 | 1 | 290 | cm |
D | 2 | 66.5 | 1 | 66.5 | cm |
E | 1 | 32.5 | 1 | 32.5 | cm |
F | 1 | 97 | 1 | 97 | cm |
G | 4 | 94 | 2 | 188 | cm |
H | 2 | 41 | 4 | 164 | cm |
I | 4 | 76 | 2 | 152 | cm |
Total | 24 | - | - | 13.83 | m |
Una vez que obtenemos los metros de canto a pegar por escritorio, dividimos la cantidad de metros sobre la velocidad obteniendo así el tiempo que tarda la máquina en pegar todos los cantos, a este número le agregamos un adicional por preparación (tiempo que tarda el operario en colocar en posición la madera a la cual se le pegará el canro) para obtener el tiempo total.
Velocidad del pegacantos | 16 | m/min | |
Pegado | 0.86 | min | |
Adicional por preparacion | 3.14 | min | |
Tiempo | 4 | min | |
Capacidad pegacantos | 15 | PT/h |
Capacidad de CC, Lijado, agujereado y embalado
En el proceso de control de calidad (el cual incluye un lijado final) se calculo de forma estimativa cuanto se tarda por por canto y a ese numero se lo multiplica por la cantidad de cantos lo cual da como resultado el tiempo de operación para un escritorio.
El calculo del proceso de agujereado se hace de la misma manera nada más que en lugar de cantos se hacen las mismas cuantas con agujeros.
En el caso del embalado estimamos directamente el tiempo de operación ya que en este proceso simplemente se colocan las maderas, los herrajes y el manual de instrucciones en una caja.
Proceso | Top (min/PT) | Capacidad | ||||
Control de calidad (Lijado) | 24 cantos a lijar x 0,16 min /canto | 3.84 | 15.625 | PT/hs | ||
Agujereado | 44 agujeros por PT x 10 seg / agujero | 7.3 | 8.22 | PT/hs | ||
Embalado | 2.0 | - | 30.0 | PT/hs |
Consumo de Energía, Agua y otros Servicios
Calculamos el consumo de electricidad para saber (de manera aproximada) el valor a pagar cada mes.
Maquina | Cantidad | Potencia [kW] | Hs diarias | Consumo diario | Hs mensuales | Consumo mensual [kWh] |
Escuadradora | 7 | 4.1 | 16 | 459.2 | 412.8 | 11847.36 |
Pegacantos | 2 | 4.55 | 8 | 72.8 | 206.4 | 1878.24 |
Agujereadora | 4 | 0.7 | 8 | 22.4 | 206.4 | 577.92 |
Total | 14303.52 |
El consumo de agua es despreciable ya que el agua no forma parte de nuestro proceso productivo. Se usa únicamente para la higiene personal de los operarios.
Debido a la alta cantidad de material combustible que hay en la fábrica habrá un plan de evacuación contra incendios y se tomarán distintas mediadas para evitar la propagación de un incendio (por ejemplo pintura inífuga, detectores de humo y sensores de temperatura). También, para evitar los accidentes laborales se establecerá una metodología de trabajo segura y con los equipos de seguridad requeridos por cada tarea.
Balance Anual de Material
Según el Plan de ventas vamos a producir 58000 u/año en estado de regimen.
En base al estudio de desperdicios en la etapa de corte para cada pieza, llegamos plantear un promedio ponderado teniendo en cuenta las cantidades de placas que utilizaremos para la producción. De esta forma llegamos a los desperdicios totales del proceso.
Corte | |||
Pieza | Desperdicio | Nro de placas | Promedio ponderado |
Lateral A | 14.70% | 16 | 2.33% |
Lateral B | 14.70% | 16 | 2.33% |
Tapa C | 24.34% | 24 | 5.78% |
Columna D | 18.44% | 6 | 1.10% |
Escuadra F | 1.64% | 2 | 0.03% |
Escuadra E | 31.50% | 16 | 4.99% |
Frente cajon G | 9.70% | 4 | 0.38% |
Lateral cajon H | 4.29% | 6 | 0.25% |
Trasero cajon I | 10.11% | 3 | 0.30% |
Fondo cajon J | 12.21% | 8 | 0.97% |
Total | 101 | 18.47% |
El desperdicio promedio del sector de corte es 18,47% en estado de regimen.
En el siguiente cuadro calculamos la superficie de madera utilizada para fabricar cada parte del producto terminado y luego lo sumamos para obtener la superficie de madera total requerida para fabricar el escritorio.
Superficie de madera por producto terminado | |||||
Pieza | Cantidad | Ancho | Largo | Superficie | Unidad |
Lateral A | 1 | 76 | 44.5 | 0.3382 | m2 |
Lateral B | 1 | 76 | 44.5 | 0.3382 | m2 |
Tapa C | 1 | 100 | 45 | 0.45 | m2 |
Columna D | 1 | 38.5 | 28 | 0.1078 | m2 |
Escuadra F | 1 | 32.5 | 12 | 0.039 | m2 |
Escuadra E | 1 | 97 | 28 | 0.2716 | m2 |
Frente cajon G | 2 | 33.5 | 13.5 | 0.09045 | m2 |
Lateral cajon H | 4 | 30 | 11 | 0.132 | m2 |
Trasero cajon I | 2 | 27 | 11 | 0.0594 | m2 |
Fondo cajon J | 2 | 29.5 | 29.5 | 0.17405 | m2 |
PT | 1 | 2.0007 | m2 |
Una vez obtenidos los valores en metros cuadrados por unidad de producto terminado, lo multiplicamos por la cantidad que se planea vender en un año en régimen (58.000 unidades) y obtenemos la cantidad de superficie de madera que compondrá la venta anual de producto terminado. A continuación calculamos la cantidad de materia prima requerida en superficie de madera para obtener la superficie que compondrá a los productos terminados durante el año, teniendo en cuenta el desperdicio porcentual de metros cuadrados de cada operación.
Secciones Operativas | Alimentacion | Desperdicios | Producciones seccionales | Unidad |
Corte | 142328.7 | 18.47% | 116040.6 | m2 |
Pegado de cantos | 116040.6 | 0.00% | 116040.6 | m2 |
Agujereado | 116040.6 | 0.00% | 116040.6 | m2 |
Emabalado | 116040.6 | 0.00% | 116040.6 | m2 |
Total | 142328.7 | 26288.1 | 116040.6 | m2 |
Con el cuadro se puede concluir que la cantidad de metros cuadrados de melamina que deben ingresar al proceso son 142.328,7.
También se puede ver que habrán desperdicios no recuperables de 26288,1 metros cuadrados, los cuales representan un 22,65% de desperdicio en función de la cantidad producida.
Ritmo de trabajo
Debido a la naturaleza de la tecnología utilizada y al de la forma de trabajo de la industria se decidió trabajar con un equipo seis días a la semana con un turno de 8 horas. Considerando un promedio de 8 días de feriados obligatorios al año y 2 días de mantenimiento de maquinaria obtenemos 302 días laborales.
En el caso de las escuadradoras, se mantendrá la misma metodología que en el resto de los puestos pero con dos turnos de 8 horas por día con la finalidad de mantener una producción pareja.
Días activos | 312-10 | 302 | dias |
Horas Activas | 302*8 | 2416 | horas |
Horas Activas esc | 302*16 | 4832 | horas |
Las horas de trabajo de los operarios de los sectores pegado de canto, agujereado y embalado son:
2416hs/1eq | 2416 | horas |
Las horas de trabajo de los operarios del sector de corte son:
4832hs/2eq | 2416 | horas |
Capacidad real anual de la maquinaria tipo de cada sección operativa
A continuación haremos un análisis de la capacidad real de las máquinas, empezando a partir del valor de la capacidad teórica de las mismas y modificando el valor según la cantidad de horas activas por año y el rendimiento operativo promedio esperado de la sección.
Secciones | Capacidad teórica / máquina x hora | Horas activas/año | Capacidad teorica/ máquina x año | Rendimiento operativo | Capacidad real /maquina x año |
Corte | 2.24 | 4832 | 10823.68 | 0.85 | 9200.1 |
Pegado de cantos | 15.00 | 2416 | 36240 | 0.85 | 30804.0 |
Lijado | 15.65 | 2416 | 37810.4 | 0.85 | 32138.8 |
Agujereado | 8.18 | 2416 | 19762.88 | 0.85 | 16798.4 |
Emabalado | 30 | 2416 | 72480 | 0.9 | 65232.0 |
Determinación de la cantidad de maquinas operativas por sección, capacidad real anual de cada sección y su aprovechamiento en relación al programa de producción
Utilizaremos la capacidad real anual de cada máquina, la cantidad de máquinas utilizadas por sección y la utilización que se le dará con el programa de producción anual para obtener el aprovechamiento que se le dará a cada una de las secciones.
Secciones | Programa anual de producción [pt] | Capacidad real /maquina x año [pt/año] | Cantidad de maquinas necesarias | Capacidad real/sección por año | Aprovechamiento seccional (%) |
Corte | 58000 | 9200.128 | 7.0 | 64400.9 | 0.90 |
Pegado de cantos | 58000 | 30804 | 2.0 | 61608.0 | 0.94 |
Lijado | 58000 | 32138.84 | 2.0 | 64277.7 | 0.90 |
Agujereado | 58000 | 16798.448 | 4.0 | 67193.8 | 0.86 |
Embalado | 58000 | 65232 | 1.0 | 65232.0 | 0.89 |
La cantidad de maquinas necesarias se calcula a través del cociente entre la cantidad a producir y la capacidad real por máquina, redondeando al numero entero superior.
El grado de aprovechamiento seccional se calcula como la división entre el programa anual de producción y la capacidad real por sección por año.
Detección del cuello de botella y la capacidad anual del equipo.
El cuello de botella corresponde a la sección de mayor aprovechamiento, en este caso el pegado de cantos
la capacidad de la sección de pega cantos es de 61.608 unidades de producto terminado por año, debido a que las secciones siguientes no tienen desperdicio desperdicio entonces sabemos que dicha producción irá directamente al producto terminado.
Evolución de la producción
Teniendo en cuenta la complejidad de las máquinas y del trabajo a realizar calculamos que en 2 meses los trabajadores de la planta se encontrarán trabajando en estado de régimen, entonces:
El volumen de producción mensual en estado de régimen: | 58000/12 | 4833 | PT/mes |
Periodo de puesta en marcha es de 2 meses.
La cantidad producida en los meses de puesta en régimen:
Mes | Ritmo de producción al inicio [%] | Ritmo de producción al final [%] | Producción promedio [%] | Producción mensual promedio [PT] | Producción propuesta [PT] |
1 | 0% | 30% | 15% | 4833 | 725 |
2 | 30% | 100% | 65% | 4833 | 3142 |
Total | 3867 |
Luego calculamos la producción en el resto del año (en los 10 meses siguientes la producción ya está en régimen debido a que el período de aprendizaje finalizó).
Volumen de producción durante el resto del año 1 (obtenido del plan de ventas):
12-2 meses | 10 meses | 4833 u/mes * 10 meses= | 48333.33 | PT |
La cantidad de unidades producidas en el primer año teniendo en cuenta la puesta en régimen es igual a la cantidad producida en los primeros dos meses sumada a la cantidad producida en los otros 10 meses en régimen, los cuales siguen lo determinado por el plan de ventas.
Volumen de producción en el año 1 | ||
3867 + 48333 | 52200 | unidades |
Determinar el stock promedio de producto elaborado
Con la finalidad de poder mantener a la fábrica produciendo hasta que llegue la próxima entrega se mantiene un stock de seguridad de media semana.
El ritmo de entregas es de una semana.
La cantidad de producto terminado que se fabrica semanalmente según el plan de ventas es la siguiente:
Volumen de producción diaria promedio en estado de régimen: | ||
Semanas por año | 52 | semanas/año |
Producción por semana | 1115.4 | u/semana |
La cantidad de producto terminado promedio que habrá en el almacén es igual a el stock mínimo (stock de seguridad) + el stock máximo dividido 2:
Stock promedio de elaborado: | ||
(1115.4+557.7)/2 | 836.5 | unidades |
Para calcular las ventas en el año 1 le restamos a la producción total de este año el stock promedio de producto terminado.
Ventas año 1: | 48333.3 - 836.5 | 47496.79 | unidades |
En este caso no restamos el stock promedio de producto terminado ya que este se mantiene constante y que quedan en el almacén se renuevan constantemente.
Ventas año 2 a 5: | 58000 | unidades |
Consumo de MP para el programa de producción y formación de la mercadería en curso y semielaborado
Aumentamos el porcentaje de desperdicios no recuperables porque al estar empezando no sería raro que los operarios se equivoquen a la hora de realizar las operaciones y haya que desechar piezas.
Porcentaje de desperdicios no recuperable adicional: | 100% |
Sumamos todos los tiempos en minutos de los procesos y luego este tiempo lo pasamos a días de elaboración.
Y luego dividiendo la cantidad de días que se trabajan en un año por el número obtenido anteriormente obteniendo así la cantidad de ciclos que se realizarán dentro de la fabrica a lo largo del año.
Pegacanto | 4.86 | min |
Corte | 26.7 | min |
CC | 3.84 | min |
Agujereado | 7.3 | min |
Embalado | 2 | min |
Total | 44.7 | min |
Dias de elaboración | 0.09313 | dias |
312 / 0.09313 | 3350.3 | Ciclos de elaboración anuales |
Producción en período de aprendizaje | 3867 | unidades | |
Producción en período régimen | 48333 | unidades | |
Superficie de madera por unidad | 2 | m2 | |
Superficie Total en régimen | 96666 | m2 | |
Superficie Total Aprendizaje | 7734 | m2 | |
Desperdicio en régimen | 22.65% | ||
Desperdicio en Aprendizaje | 45.30% |
Desperdicio | ||
meses 1 y 2 | 11237.50 | m2 |
meses 3 a 12 | 118560.85 | m2 |
MP para prod | 129798.35 | m2 |
Prod en el año 1 | 104400 | m2 |
desp no rec año 1 | 25398.35 | m2 |
La MP para prod. es la cantidad de materia prima requerida para la producción del año 1.
El desp no rec año 1 es la cantidad de desperdicio no recuperable del año 1.
Volumen de materia prima requerido para alimentar el proceso | ||
MP que ingresa | 142328.7 | m2 |
Vol de MP requerido | 42.5 | m2 |
Producto elaborado | 34.6 | m2 |
Desperdicio no rec | 7.8 | m2 |
Tot MP en proceso | 42.5 | m2 |
El total de MP en proceso determina la cantidad de materia prima que se encuentra en proceso para cada ciclo.
Consumo total de materia prima en el año 1 | |||
Para los prod elaborados | 129798.35 | m2 | |
Para la mercadería en curso y semielaborados | 42.5 | m2 | |
Total consumo de materia prima en el año 1 | 129840.83 | m2 |
El consumo total de materia prima en el año 1 será igual a la suma entre los productos terminados y la mercadería en curso y semielaborados.
Año 2 al 5: El consumo de materia prima es exclusivamente destinado a la prod: | ||
Cada año | 58000 | unidades |
Desperdicios | 1.2265 | % |
71137 | unidades |
Stock promedio de MP y programa de compras
El stock de seguridad es 3.5 días para tener stock en caso de que falle una de las entregas.
Producción diaria | 371.8 | m2 | ||
Consumo diario de MP | 456.0 | m2 | ||
Stock minimo de materia prima: | 3.5 días | 1596.0 | m2 |
Este cuadro simula las entregas de materia prima que se realizan en una semana de trabajo.
A finalizar el dia | Stock al inicio del dia | Compras | Unidades |
Lun | 1596.0 | 912.0254 | m2 |
Mar | 2052.1 | 0 | m2 |
Mier | 1596.0 | 912.0254 | m2 |
Jue | 2052.1 | 0 | m2 |
Vie | 1596.0 | 912.0254 | m2 |
Sab | 2052.1 | 0 | m2 |
Dom | 2052.1 | 0 | m2 |
Las compras son cada 2 días (exceptuando los domingos que es día no laboral).
Stock promedio | (2052.1+1596)/2 | 1824.1 |
Equivale a | 4.00 | días de consumo |
El stock promedio se calcula sumando el stock máximo y el stock de seguridad, luego se divide este número por 2.
Cuadro resumen del programa general de evolución
En este ejercicio realizamos el cuadro de evolución de mercaderías el cual es un cuadro resumen de todos los datos obtenidos en ejercicios anteriores.
U de Medida | Período de Instalación | Año 1 | Año 2 al 5 | |
Ventas | PT | 0 | 47496.76 | 58000 |
Stock promedio de Elaborado | PT | 0 | 836.5384615 | 836.5384615 |
DNR | m2 | 0 | 25398.35 | 142274 |
En curso y semielborado | m2 | 0 | 42.5 | 42.5 |
Consumo de MP | m2 | 0 | 129840.83 | 129840.83 |
Stock de MP | m2 | 0 | 1486.9 | 1486.9 |
Compra de MP | m2 | 0 | 131327.73 | 129840.83 |
La materia prima se compra en el período de explotación ya que no es necesario disponer de esta en el período de preinversión.
Determinación del Personal
Organigrama de toda la empresa
Descripción de puesto de trabajo. Calificación y Formación de los operadores.
Sector Corte: Los operarios encargados de este sector deben estar capacitados por la empresa. La tarea es realizar el corte de toda la madera que ingrese a la fábrica, tanto placas de melamina como fibroplus para el fondo de los cajones. Se necesitará 1 operario por escuadradora, en total serán 7 operarios por turno.
Sector Pega Cantos: Aquí se necesitaran 2 operarios por máquina pega cantos, el de inicio de línea para colocar las piezas sin canto al comienzo de la máquina y el del final de línea para retirar las piezas con canto y abastecer de nuevo la línea cuando la pieza lo requiera. Vamos a necesitar 4 operarios para las 2 máquinas que tendremos en la planta.
Sector CC y Lijado: En esta etapa se van a necesitar 2 puestos de CC con un operario cada uno, donde cada operario realizará un control visual de la pieza que sale del pega cantos y si es necesario realizará un lijado fino para dar una mejor terminación.
Sector agujereado: En este sector tendremos 4 puestos de agujereado, cada uno con un operario, resultando un total de 4 operarios, los cuales serán los encargados de realizar el agujereado de todas las piezas que salen del control de calidad, la operación se realiza con taladro manual y matrices de agujereado para acelerar el proceso.
Sector embalado: el operario encargado de esta tarea cuenta con todas las piezas necesarias para un PT, así como con los herrajes, tornillos, minifix, y clavos. Su tarea es preparar el paquete que ira luego al almacén de PT.
Gerente de administración: Será una persona con conocimientos en contabilidad y finanzas, capaz de leer balances y comunicarse con los contadores de la empresa de forma fluida, así como el encargado de garantizar el abastecimiento de materiales en la empresa.
Empleado administrativo contable: Su tarea va a ser ayudar con el trabajo operativo al gerente de administración, así como lidiar con presupuestos, liquidación de sueldos y pagos a proveedores. Tendremos dos personas en este puesto, un empleado administrativo y otro más orientado a las tareas de contabilidad.
Gerente Producción: su función es la planificación programación y control de la producción, es el nexo entre el área productiva y el área administrativa de la empresa.
Sector | Cantidad de operarios | Nivel de educación | Capacitación |
Corte | 7 | Secundario completo | Si |
Pega Cantos | 4 | Secundario completo | Si |
Lijado y CC | 2 | Secundario completo | Si |
Embalado | 4 | Secundario completo | Si |
Contador | 1 | Estudiante avanzado de lincenciatura en contabilidad | No |
Gerente de admin | 1 | Gradudado de carreras afines a administración | No |
Gerente de prod | 1 | Ingeniero industrial Industrial | No |
Listado de Equipos Auxiliares, Muebles y Útiles.
Equipos Auxiliares, Muebles y Útiles.
Item | Cantidad |
Aire acondicionado | 1 |
Amoblamiento para pañol de herramientas | 2 |
Botiquín | 1 |
Cafetera | 1 |
Amoblamiento para ferreteria | 2 |
Escritorio recepcion | 1 |
Silla recepcion | 1 |
Computadoras | 4 |
Dispensers de agua frío-calor | 2 |
Escritorio | 4 |
Heladera | 1 |
Impresora | 1 |
Mesa para cocina | 1 |
Microondas | 1 |
Mueble de archivo | 1 |
Silla para escritorio | 4 |
Teléfono fijo | 1 |
Teléfono móvil | 1 |
Anteproyecto de Planta.
Plano de planta y Distribución de áreas.
Planta baja
Oficinas
Segundo Piso