Diferencia entre revisiones de «2025/Grupo6/DimensionamientoFisico»
(Evolucion de produccion) |
Sin resumen de edición |
||
(No se muestran 7 ediciones intermedias de 3 usuarios) | |||
Línea 361: | Línea 361: | ||
* Reposición de agua por prueba: 0,25 lt/h (circuito cerrado) | * Reposición de agua por prueba: 0,25 lt/h (circuito cerrado) | ||
=== <u> | ==== <u>Cuadro Resumen:</u> ==== | ||
{| class="wikitable" | {| class="wikitable" | ||
!Máquina | |||
!Modelo | |||
!Consumo Energético | |||
!Consumo de Agua | |||
!Dimenisones | |||
|- | |- | ||
|Torno CNC | |Torno CNC | ||
Línea 405: | Línea 405: | ||
|3100 × 1150 ×1800 mm | |3100 × 1150 ×1800 mm | ||
|} | |} | ||
=== Consumos de Energía, Agua y Otros Servicios: === | |||
=== Mantenimiento y medios de control (máquinas, tareas, etc.) === | === Mantenimiento y medios de control (máquinas, tareas, etc.) === | ||
Se desarrolla un plan de mantenimiento preventivo, el cual consiste en la revisión mensual de | Se desarrolla un plan de mantenimiento preventivo, el cual consiste en la revisión mensual, semanal o quincenal dependiendo de la máquinas. Se utilizarán planillas en donde se registrarán los mantenimientos realizados con fecha, observaciones y firma del responsable. Estos consisten en chequeo de temperaturas, velocidades de funcionamiento, verificación del cableado, enchufes, entre otros. | ||
A continuación se detallan las tareas de mantenimiento sobre las maquinas: | |||
{| class="wikitable" | |||
!Equipamiento | |||
!Tareas principales | |||
!Frecuencia | |||
!Medios de Control | |||
|- | |||
|Torno CNC | |||
|Lubricación, verificación de precisión, limpieza de guías, cambio de fluidos de corte, revisión de husillo, calibración de sensores. | |||
|Mensual | |||
|• Sensores de temperatura y vibración en el husillo y el motor principal. | |||
• Sistemas de monitoreo por software. | |||
• Alarmas que indican sobrecarga, pérdida de origen o interferencias. | |||
|- | |||
|Brazo Robótico de Pulido | |||
|Lubricación de ejes, chequeo de presión neumática | |||
|Quincenal | |||
| rowspan="2" |• Ciclos de calibración automática en el cabezal. | |||
• Sensores de fin de carrera y sensores de emergencia. | |||
|- | |||
|Brazo Robótico de soldadura MIG / TIG | |||
|Limpieza de boquillas, revisión de cables y gas, lubricación de ejes, chequeo de presión neumática | |||
|Quincenal | |||
|- | |||
|Banco de pruebas hidráulicas | |||
|Verificación de estanquedad, control de bomba, revisión de filtros de agua, rellenado de tanques | |||
|Mensual (el rellenado del tanque es diario) | |||
|• Manómetros calibrados y sensores de presión | |||
• Control automático de ciclos | |||
• Sistemas de corte automático | |||
|} | |||
Además, los equipos programables con softwares integrads, como los brazos robóticos o el torno CNC, recibirán las actualizaciones correspondientes cada vez que sea necesario. El encargado de realizar esto es el responsable de programación de máquinas. | |||
Además de estos mantenimientos, se capacitará al personal que controle y opere dichas máquinas para evitar fallas no deseadas en el funcionamiento | Además de estos mantenimientos, se capacitará al personal que controle y opere dichas máquinas para evitar fallas no deseadas en el funcionamiento y para realizar una limpieza adecuada y una correcta puesta en marcha de las máquinas, con el fin de asegurar los parámetros y la correcta operación de las mismas. | ||
En caso de ocurrencia de fallas imprevistas, se contactará al proveedor de las máquinas para llevar a cabo un mantenimiento correctivo lo antes posible y continuar con la producción. | En caso de ocurrencia de fallas imprevistas, se contactará al proveedor de las máquinas para llevar a cabo un mantenimiento correctivo lo antes posible y continuar con la producción. | ||
Línea 418: | Línea 451: | ||
Para tener un funcionamiento óptimo y seguro de la planta, es esencial contar con medidas que protejan a los trabajadores, las maquinarias y la materia prima. La seguridad no solo previene accidentes, sino que garantiza el correcto funcionamiento de los procesos. Por ello se implementarán los siguientes sistemas de seguridad: | Para tener un funcionamiento óptimo y seguro de la planta, es esencial contar con medidas que protejan a los trabajadores, las maquinarias y la materia prima. La seguridad no solo previene accidentes, sino que garantiza el correcto funcionamiento de los procesos. Por ello se implementarán los siguientes sistemas de seguridad: | ||
* Detectores de humo, alarma contra incendios | <u>Infraestructura:</u> | ||
* Salidas de emergencia señalizadas y libres. | |||
* Matafuegos tipo ABC distribuidos según carga de fuego. | |||
* Sistemas de señalización y evacuación . | * Iluminación de emergencia. | ||
* Detectores de humo, alarma contra incendios y aspersores contra incendios, los cuales se activarán automaticamente frente a la detección de un incendio. | |||
* Sistemas de señalización y evacuación. | |||
* Sistemas de seguridad eléctrica como disyuntores o puesta a tierra de maquinas - en caso de detectar una pérdida, cortarán automaticamente el funcionamiento de las máquinas. | * Sistemas de seguridad eléctrica como disyuntores o puesta a tierra de maquinas - en caso de detectar una pérdida, cortarán automaticamente el funcionamiento de las máquinas. | ||
* Sistema de vigilancia. | * Sistemas de seguridad eléctrica como disyuntores y puesta a tierra de maquinas que, en caso de detectar una desperfecto, cortarán automaticamente el suministro eléctrico. | ||
<u>Sistemas de Seguridad Activa en Máquinas:</u> | |||
* Botones mushroom para paradas de emergencia. | |||
* Sensores de proximidad en prensas, herramientas de corte y robots. | |||
* Encapsulado de partes moviles en los equipos CNC. | |||
* Lock Out para tareas de mantenimiento. | |||
* Tarjetas con instrucciones operativas en cada estación | |||
<u>Equipos de Protección Personal (EPP):</u> | |||
* Obligatorios: botines con puntera, anteojos, guantes, protección auditiva y ropa ignífuga (en los puestos de soldadura). | |||
* Capacitación y cartelera con pictogramas de uso obligatorio. | |||
<u>Seguridad del Personal y Activos de la Empresa:</u> | |||
* Sistema de vigilancia CCTV. | |||
* Alarma de seguridad antirobos. | |||
* Sistema de control de ingresos y egresos a planta. | * Sistema de control de ingresos y egresos a planta. | ||
=== Balance de | === Balance Anual de Materiales === | ||
A continuación, presentamos el cuadro de necesidades de alimentación de MP en estado de régimen que se precisan según cada pieza, de acuerdo al volumen establecido en el plan de ventas. | |||
Comenzamos por la salida final de la línea, donde contamos con un descarte estimado de control de calidad de 2 válvulas cada 100 fabricadas. Este descarte nos va a obligar a producir un 2% por encima de las necesidades de PT planteadas en el plan de ventas. | |||
{| class="wikitable" | |||
! colspan="6" |CONJUNTO FINAL | |||
|- | |||
! rowspan="2" |Sección operativa | |||
! rowspan="2" |Alimentacion KG | |||
! rowspan="2" |Agregado | |||
! colspan="2" |Desperdicios | |||
! rowspan="2" |Producción (KG) | |||
|- | |||
!Recuperable | |||
!No recuperable | |||
|- | |||
|Lavado de partes | |||
|82285,71 | |||
| - | |||
| - | |||
| - | |||
|82285,71 | |||
|- | |||
|Ensamble de partes | |||
|82285,71 | |||
| - | |||
| - | |||
| - | |||
|82285,71 | |||
|- | |||
|Ensayo / control de calidad | |||
|82285,71 | |||
| - | |||
| - | |||
|Descarte de CC (2 cada 100) | |||
|80640 | |||
|- | |||
|Empaquetado | |||
|80640 | |||
| - | |||
| - | |||
| - | |||
|44800*1,8 = 80640 | |||
|} | |||
Trabajamos con kilogramos para poder adaptarlo a los desperdicios en función del peso. Como esta línea trabaja con válvulas completas, simplemente multiplicamos la necesidad en válvulas por el peso de una válvula de 2", nuestro producto más representativo (1,8kg). | |||
'''Estimaciones de desperdicios:''' | |||
Basándonos en características técnicas del mecanizado en torno CNC, estimamos un desperdicio del 15% para torneados que parten de forjas semielaboradas y un 20% para los que parten de cortes brutos de MP. | |||
Colocamos desperdicios de entre el 0,05% y 0,5% para procesos de tratamiento de superficies como el pulido y el rebabado, donde la pérdida es mínima. | |||
Al utilizar procesos de corte manuales con sierra, estimamos un desperdicio por corte de un 2% | |||
Como los porcentajes de desperdicio se encuentran en función del peso, usaremos como referencia para pasar de necesidades de PT a necesidades en KG, el peso de nuestro producto más representativo, la válvula de 2", la cuál pesa 1,8kg. | |||
Todos nuestros desperdicios son no recuperables vendibles, por lo que no afectarán a la cantidad de materia prima a adquirir. | |||
'''Ahora pasamos a los procesos de fabricación del cuerpo, clapeta, eje y maneta; distinguiendo la materia prima necesaria para cada una.''' | |||
{| class="wikitable" | |||
! colspan="6" |FORJA PARA CUERPO | |||
|- | |||
! rowspan="2" |Sección operativa | |||
! rowspan="2" |Alimentacion (KG) | |||
! rowspan="2" |Agregado | |||
! colspan="2" |Desperdicios | |||
! rowspan="2" |Producción (KG) | |||
|- | |||
!Recuperable | |||
!No recuperable | |||
|- | |||
|Mecanizado de cuerpo | |||
|'''67968,61''' | |||
| - | |||
| - | |||
|15% | |||
|57773,32 | |||
|- | |||
|Rebabado de cuerpo | |||
|57773,32 | |||
| - | |||
| - | |||
|0,30% | |||
|44800/0,98*1.8*0.7=57600 | |||
|} | |||
''<u>Nota:</u> el cuerpo representa un 70% del peso total de una válvula, por lo que para obtener la salida final del proceso, multiplicamos la necesidad de válvulas (tomando en cuenta el descarte de control de calidad) x 1,8kg x 0,7.'' | |||
{| class="wikitable" | |||
! colspan="6" |FORJA PARA CLAPETA | |||
|- | |||
! rowspan="2" |Sección operativa | |||
! rowspan="2" |Alimentacion (KG) | |||
! rowspan="2" |Agregado | |||
! colspan="2" |Desperdicios | |||
! rowspan="2" |Producción (KG) | |||
|- | |||
!Recuperable | |||
!No recuperable | |||
|- | |||
|Mecanizado de forja y clapeta | |||
|'''4889,23''' | |||
| - | |||
| - | |||
|15% | |||
|4155,84 | |||
|- | |||
|Pulido de clapeta | |||
|4122,53 | |||
| - | |||
| - | |||
|0,20% | |||
|4114,29 | |||
|} | |||
''<u>Nota:</u> la clapeta representa aproximadamente un 5% de la totalidad de la válvula. Cálculos análogos a la forja de cuerpo.'' | |||
{| class="wikitable" | |||
! colspan="6" |BARRA PARA MANETA | |||
|- | |||
! rowspan="2" |Sección operativa | |||
! rowspan="2" |Alimentacion (KG) | |||
! rowspan="2" |Agregado | |||
! colspan="2" |Desperdicios | |||
! rowspan="2" |Producción (KG) | |||
|- | |||
!Recuperable | |||
!No recuperable | |||
|- | |||
|Corte de barra | |||
|'''10569,5077''' | |||
| | |||
| | |||
|2% | |||
|10358,12 | |||
|- | |||
|Mecanizado de maneta | |||
|10358,12 | |||
| - | |||
| - | |||
|20% | |||
|8286,49 | |||
|- | |||
|Armado de maneta | |||
|8286,49 | |||
| - | |||
| - | |||
| - | |||
|8286,49 | |||
|- | |||
|Soldadura de maneta | |||
|8286,49 | |||
| - | |||
| - | |||
| - | |||
|8286,49 | |||
|- | |||
|Desbaste de maneta | |||
|8286,49 | |||
| - | |||
| - | |||
|0,50% | |||
|8245,06 | |||
|- | |||
|Pulido de maneta | |||
|8245,06 | |||
| - | |||
| - | |||
|0,20% | |||
|8228,57 | |||
|} | |||
''<u>Nota:</u> la maneta representa un 10% del peso de la válvula'' | |||
{| class="wikitable" | |||
! colspan="6" |BARRA PARA EJE | |||
|- | |||
! rowspan="2" |Sección operativa | |||
! rowspan="2" |Alimentacion (KG) | |||
! rowspan="2" |Agregado | |||
! colspan="2" |Desperdicios | |||
! rowspan="2" |Producción (KG) | |||
|- | |||
!Recuperable | |||
!No recuperable | |||
|- | |||
|Corte de barra | |||
|'''9898,03308''' | |||
| | |||
| | |||
|2% | |||
|9700,07 | |||
|- | |||
|Mecanizado de eje | |||
|9700,07 | |||
| - | |||
| - | |||
|15% | |||
|8245,06 | |||
|- | |||
|Pulido de eje | |||
|8245,06 | |||
| - | |||
| - | |||
|0,20% | |||
|8228,57 | |||
|} | |||
''<u>Nota:</u> El eje representa un 10% del peso de la válvula'' | |||
El resto de materias primas son componentes terminados que se ensamblan junto a las otras partes para armar las válvulas y no pasan por ningún proceso de transformación que haga que sufran desperdicios. Tomamos en cuenta que partimos de una necesidad superior a la del plan de ventas por el descarte de control de calidad: | |||
{| class="wikitable" | |||
!Nivel | |||
!Componente | |||
!Material | |||
!Cantidad | |||
!Necesidad anual según plan de ventas | |||
!Necesidad anual tomando en cuenta descarte de CC | |||
!Necesidad anual redondeada | |||
|- | |||
|3 | |||
|Perno con Cabezal para Palanca | |||
|Acero Inoxidable 304 | |||
|1 | |||
|44800 | |||
|45714,28571 | |||
|45714 | |||
|- | |||
|2 | |||
|Resorte Maneta | |||
|Acero Inoxidable 302 | |||
|1 | |||
|44800 | |||
|45714,28571 | |||
|45714 | |||
|- | |||
|2 | |||
|Casquilo de Maneta | |||
|Acero Inoxidable 304 | |||
|1 | |||
|44800 | |||
|45714,28571 | |||
|45714 | |||
|- | |||
|2 | |||
|Tapón Plástico Maneta | |||
|PTFE con base EPDM | |||
|1 | |||
|44800 | |||
|45714,28571 | |||
|45714 | |||
|- | |||
|2 | |||
|Etiqueta Maneta | |||
| | |||
|1 | |||
|44800 | |||
|45714,28571 | |||
|45714 | |||
|- | |||
|2 | |||
|Tapón de Buje | |||
|PTFE con base EPDM | |||
|2 | |||
|89600 | |||
|91428,57143 | |||
|91428 | |||
|- | |||
|2 | |||
|Buje Plástico para Clapeta | |||
|PEEK (Polieter Éter Cetona) | |||
|2 | |||
|89600 | |||
|91428,57143 | |||
|91428 | |||
|- | |||
|2 | |||
|Junta O-Ring | |||
|Vitón(FMK) | |||
|2 | |||
|89600 | |||
|91428,57143 | |||
|91428 | |||
|- | |||
|2 | |||
|Bulones 304 | |||
|Acero Inoxidable 304 | |||
|4 | |||
|179200 | |||
|182857,1429 | |||
|182857 | |||
|- | |||
|2 | |||
|Arandelas 304 | |||
|Acero Inoxidable 304 | |||
|4 | |||
|179200 | |||
|182857,1429 | |||
|182857 | |||
|- | |||
|2 | |||
|Etiqueta Tapa | |||
| | |||
|1 | |||
|44800 | |||
|45714,28571 | |||
|45714 | |||
|} | |||
=== Ritmo de Trabajo === | |||
Se decide que, en general, la planta trabajará con un turno de 8 horas, de manera tal que se obtiene el siguiente cuadro detallando el rítmo de trabajo: | |||
{| class="wikitable" | |||
|Días del Año | |||
|365 | |||
|- | |||
|Feriados | |||
|15 | |||
|- | |||
|Vacaciones | |||
|15 | |||
|- | |||
|Sabados y Domingos | |||
|100 | |||
|- | |||
|Días Activos | |||
|235 | |||
|- | |||
|Turnos | |||
|1 | |||
|- | |||
|Horas por Turno | |||
|8 | |||
|- | |||
|'''Horas Activas''' | |||
|'''1880''' | |||
|} | |||
Sin embargo, en las secciones de mecanizado se trabajará en dos turnos de 6 horas para reducir el número de tornos necesarios en la planta. | |||
=== Capacidad Real por Sección Operativa === | |||
Se analizan las capacidades reales de cada sección, teniendo en cuenta las horas activas al año, la información brindada por el tecnólogo y la capacidad teórica: | |||
{| class="wikitable" | |||
|'''Sección Operativa''' | |||
|'''Cap. Teórica (pz/hora)''' | |||
|'''Horas Activas al Año''' | |||
|'''Cap. Teórica Anual (pz/año)''' | |||
|'''Rendimiento''' | |||
|'''Cap. Real Anual''' | |||
|- | |||
|Mecanizado de cuerpo | |||
|12 | |||
| 2.820 | |||
| 33.840 | |||
|100% | |||
| 33.840 | |||
|- | |||
|Rebabado de cuerpo | |||
|60 | |||
| 1.880 | |||
| 112.800 | |||
|95% | |||
| 107.160 | |||
|- | |||
|Mecanizado de clapeta | |||
|7,60 | |||
| 2.820 | |||
| 21.445 | |||
|100% | |||
| 21.445 | |||
|- | |||
|Pulido de clapeta | |||
|10 | |||
| 1.880 | |||
| 18.800 | |||
|100% | |||
| 18.800 | |||
|- | |||
|Corte de barra | |||
|60 | |||
| 1.880 | |||
| 112.800 | |||
|95% | |||
| 107.160 | |||
|- | |||
|Mecanizado de maneta | |||
|20 | |||
| 2.820 | |||
| 56.400 | |||
|100% | |||
| 56.400 | |||
|- | |||
|Armado de maneta | |||
|12 | |||
| 1.880 | |||
| 22.560 | |||
|95% | |||
| 21.432 | |||
|- | |||
|Soldadura de maneta | |||
|30 | |||
| 1.880 | |||
| 56.400 | |||
|100% | |||
| 56.400 | |||
|- | |||
|Desbaste de maneta | |||
|30 | |||
| 1.880 | |||
| 56.400 | |||
|100% | |||
| 56.400 | |||
|- | |||
|Pulido de maneta | |||
|5 | |||
| 1.880 | |||
| 9.400 | |||
|100% | |||
| 9.400 | |||
|- | |||
|Corte de barra | |||
|60 | |||
| 1.880 | |||
| 112.800 | |||
|95% | |||
| 107.160 | |||
|- | |||
|Mecanizado de eje | |||
|26,32 | |||
| 2.820 | |||
| 74.211 | |||
|100% | |||
| 74.211 | |||
|- | |||
|Pulido de eje | |||
|10 | |||
| 1.880 | |||
| 18.800 | |||
|100% | |||
| 18.800 | |||
|- | |||
|Lavado de partes | |||
|20 | |||
| 1.880 | |||
| 37.600 | |||
|95% | |||
| 35.720 | |||
|- | |||
|Ensamble de partes | |||
|12 | |||
| 1.880 | |||
| 22.560 | |||
|95% | |||
| 21.432 | |||
|- | |||
|Ensayo / control de calidad | |||
|12 | |||
| 1.880 | |||
| 22.560 | |||
|100% | |||
| 22.560 | |||
|- | |||
|Empaquetado | |||
|60 | |||
| 1.880 | |||
| 112.800 | |||
|90% | |||
| 101.520 | |||
|} | |||
=== | === Cantidad de Máquinas y Puestos de Trabajo === | ||
En función de las capacidades reales y el programa anual de producción, se definen la cantidad de máquinas y puestos de trabajo necesarias para cumplir con el programa anual de producción: | |||
{| class="wikitable" | |||
|'''Sección Operativa''' | |||
|'''Cap. Real Anual''' | |||
|'''Necesidad Anual''' | |||
|'''Máq. Necesarias''' | |||
|'''Máq. Necesarias Redond.''' | |||
|'''Cap. Real Anual (pz/año)''' | |||
|'''Aprovechamiento Seccional''' | |||
|- | |||
|Mecanizado de cuerpo | |||
| 33.840 | |||
| 45.714 | |||
|1,35 | |||
|2 | |||
| 67.680 | |||
|68% | |||
|- | |||
|Rebabado de cuerpo | |||
| 107.160 | |||
| 45.714 | |||
|0,43 | |||
|1 | |||
| 107.160 | |||
|43% | |||
|- | |||
|Mecanizado de clapeta | |||
| 21.445 | |||
| 45.714 | |||
|2,13 | |||
|3 | |||
| 64.335 | |||
|71% | |||
|- | |||
|Pulido de clapeta | |||
| 18.800 | |||
| 45.714 | |||
|2,43 | |||
|3 | |||
| 56.400 | |||
|81% | |||
|- | |||
|Corte de barra | |||
| 107.160 | |||
| 45.714 | |||
|0,43 | |||
|1 | |||
| 107.160 | |||
|43% | |||
|- | |||
|Mecanizado de maneta | |||
| 56.400 | |||
| 45.714 | |||
|0,81 | |||
|1 | |||
| 56.400 | |||
|81% | |||
|- | |||
|Armado de maneta | |||
| 21.432 | |||
| 45.714 | |||
|2,13 | |||
|3 | |||
| 64.296 | |||
|71% | |||
|- | |||
|Soldadura de maneta | |||
| 56.400 | |||
| 45.714 | |||
|0,81 | |||
|1 | |||
| 56.400 | |||
|81% | |||
|- | |||
|Desbaste de maneta | |||
| 56.400 | |||
| 45.714 | |||
|0,81 | |||
|1 | |||
| 56.400 | |||
|81% | |||
|- | |||
|Pulido de maneta | |||
| 9.400 | |||
| 45.714 | |||
|4,86 | |||
|5 | |||
| 47.000 | |||
|97% | |||
|- | |||
|Corte de barra | |||
| 107.160 | |||
| 45.714 | |||
|0,43 | |||
|1 | |||
| 107.160 | |||
|43% | |||
|- | |||
|Mecanizado de eje | |||
| 74.211 | |||
| 45.714 | |||
|0,62 | |||
|1 | |||
| 74.211 | |||
|62% | |||
|- | |||
|Pulido de eje | |||
| 18.800 | |||
| 45.714 | |||
|2,43 | |||
|3 | |||
| 56.400 | |||
|81% | |||
|- | |||
|Lavado de partes | |||
| 35.720 | |||
| 45.714 | |||
|1,28 | |||
|2 | |||
| 71.440 | |||
|64% | |||
|- | |||
|Ensamble de partes | |||
| 21.432 | |||
| 45.714 | |||
|2,13 | |||
|3 | |||
| 64.296 | |||
|71% | |||
|- | |||
|Ensayo / control de calidad | |||
| 22.560 | |||
| 45.714 | |||
|2,03 | |||
|3 | |||
| 67.680 | |||
|68% | |||
|- | |||
|Empaquetado | |||
| 101.520 | |||
| 45.714 | |||
|0,45 | |||
|1 | |||
| 101.520 | |||
|45% | |||
|} | |||
=== Cuello de botella y capacidad real === | === Cuello de botella y capacidad real === | ||
Línea 468: | Línea 1118: | ||
=== Stock promedio de producto terminado === | === Stock promedio de producto terminado === | ||
Para el stock promedio de producto terminado, hay que trabajar en el período en régimen y además, tener en cuenta el stock de seguridad y el ritmo de entregas. | |||
* Ritmo de entregas se define en entregas cada 1 semana. | |||
* Stock de seguridad, al ser un producto de nicho y no de consumo masivo, se estabelece en 0 semanas. | |||
En función de dichas condiciones y las semanas activas al año (47 semanas) se establece el stock promedio de producto terminado: | |||
{| class="wikitable" | |||
|+ | |||
! colspan="2" |Stock promedio de producto terminado | |||
|- | |||
|Semanas activas al año | |||
|47 semanas | |||
|- | |||
|Stock de seguridad | |||
|0 semanas | |||
|- | |||
|Ritmo de entregas | |||
|1 semana | |||
|- | |||
|Stock mínimo PT | |||
|0 | |||
|- | |||
|Stock máximo PT | |||
|954 unidades | |||
|- | |||
|Stock promedio PT | |||
|477 unidades | |||
|} | |||
Stock máximo PT = 44.800 unidades / 47 semanas = 954 u/semana | |||
=== Evolución de las ventas === | === Evolución de las ventas === | ||
Para determinar la evolución de las ventas, hay que considerar el volumen de producción y el stock promedio para el año 1. Para el resto de años, se trabaja en estado de régimen. | |||
Ventas año 1 = 36.655 unidades - 477 unidades = 36.178 unidaes | |||
Ventas año 2 - n = 44.800 unidades | |||
{| class="wikitable" | |||
|+ | |||
! colspan="2" |Ventas por año | |||
|- | |||
|Año 1 | |||
|36.178 unidades | |||
|- | |||
|Año 2 - n | |||
|44.800 unidades | |||
|} | |||
=== Consumo de Materia Prima para el Programa de Producción y Formación de la Mercadería en Curso y Semielaborada === | === Consumo de Materia Prima para el Programa de Producción y Formación de la Mercadería en Curso y Semielaborada === | ||
Para determinar el consumo de materia prima hay que considerar múltiples variables, una de ellas es el desperdicio que se da en producción. Se sabe que para el período de puesta en marcha se genera un 100% adicional de desperdicios no recuperables. En esta sección se trabajará con unidades equivalentes a producto terminado, no en kg. | |||
{| class="wikitable" | |||
|+ | |||
! colspan="2" |Consideraciones | |||
|- | |||
|Desperdicio no recuperable | |||
|8.404 u. eq. PT. | |||
|- | |||
|Total producción | |||
|44.800 u. | |||
|- | |||
|% desperdicio no recuperable | |||
|18,76% | |||
|- | |||
|% desperdicio adicional en PPM | |||
|100% | |||
|- | |||
|Ciclo de elaboración | |||
|5 días | |||
|} | |||
Para el año 1: | |||
{| class="wikitable" | |||
|+ | |||
! colspan="2" |Materia prima consumida para año 1 | |||
|- | |||
|Consumo MP para mercadería en curso | |||
|794 u. eq. PT. | |||
|- | |||
|Consumo MP en PPM | |||
|10.488 u. eq. PT. | |||
|- | |||
|Consumo MP resto del año | |||
|33.858 u. eq. PT. | |||
|- | |||
|Consumo MP año 1 | |||
|44.346 u. eq. PT. | |||
|- | |||
|Volumen producción año 1 | |||
|36.655 u. | |||
|- | |||
|Desperdicios no recuperables año 1 | |||
|7.691 u. eq. PT. | |||
|- | |||
|Consumo Total MP año 1 | |||
|45.140 u. eq. PT. | |||
|} | |||
Consumo mp en PPM = 8145,45 unidades * 1,2876 = 10.488 unidades | |||
Consumo mp resto del año = 4072,73 u/mes * 7 meses * 1,1876 = 33.858 unidades | |||
Con el volumen de producción del año 1 y el consumo total, se obtienen los desperdicios no recuperables del año 1: | |||
Desperdicios no recuperables año 1: 44.346 unidades - 36.655 unidades = 7.691 u. eq. PT. | |||
Por ultimo falta definir el consumo MP para mercaderia en curso, teniendo en cuenta que el ciclo de trabajo es de 5 días: | |||
(53.204 unidades / 335 días) * 5 días) = 794 u. eq. PT. | |||
Finalmente, para obtener el consumo total de MP para el año 1: | |||
Consumo total MP = Consumo MP para mercadería en curso + Consumo MP año 1 = 794 u. eq. PT. + 44.346 u. eq. PT. = 45.140 u. eq. PT. | |||
Para el año 2 - n: | |||
{| class="wikitable" | |||
|+ | |||
! colspan="2" |Materia prima consumida para año 2 - n | |||
|- | |||
|Volumen de producción | |||
|44.800 u | |||
|- | |||
|Consumo mp | |||
|53.204 u | |||
|- | |||
|Desperdicios no recuperables | |||
|8.404 u | |||
|} | |||
Consumo total mp = 44.800 unidades * 1.1876 = 53.204 unidades | |||
Desperdicios no recuperables: 53.204 unidades - 44.800 unidades = 8.404 unidades | |||
=== Stock Promedio de Materia Prima y Programa de Compras === | === Stock Promedio de Materia Prima y Programa de Compras === | ||
Para poder cumplir con el plan de ventas en el período de estado de régimen, se realizará una compra mensual de MP de 4626,43 u. eq. PT. y tendremos un consumo anual de 53.204 u. eq. PT. | |||
* En el mes de febrero se consume la mitad de lo que se habitúa consumir mensualmente. | |||
[[Archivo:Programa de compras - valvulas.png|centro|miniaturadeimagen|600x600px]] | |||
Se observa un promedio redondeado de compra mensual de MP de 4.434 u. eq. PT | |||
=== Cuadro evolución de mercaderías === | === Cuadro evolución de mercaderías === | ||
A continuación, se presenta el cuadro de evolución de mercaderías con toda la información calculada a lo largo de esta seccion. | |||
[[Archivo:Cuadro evolucion mercaderias - valvulas.png|centro|miniaturadeimagen|600x600px]] | |||
== Determinacion del Personal == | == Determinacion del Personal == | ||
Línea 766: | Línea 1548: | ||
== Anteproyecto de Planta == | == Anteproyecto de Planta == | ||
=== | === Plano de planta mostrando la distribucion de las distintas areas === | ||
[[Archivo:Plano de Planta con sus areas.jpg|miniaturadeimagen|1387x1387px|centro]] | [[Archivo:Plano de Planta con sus areas.jpg|miniaturadeimagen|1387x1387px|centro]] | ||
=== | === Plano mostrando el recorrido de los materiales === | ||
[[Archivo:Planta mostrando el recorrido de la materia prima.jpg|centro|miniaturadeimagen|1390x1390px]] | [[Archivo:Planta mostrando el recorrido de la materia prima.jpg|centro|miniaturadeimagen|1390x1390px]] | ||
== Cronograma de ejecución == | |||
[[Archivo:Cronograma ejecucion de valvex.png|centro|miniaturadeimagen|700x700px]] |
Revisión actual - 06:06 26 jun 2025
Determinación de la Localización
La matriz de localización es un elemento clave para definir la ubicación inicial de la planta y posibilitar su futura expansión. En su elaboración se consideró la opción de instalar la planta en un parque industrial, evaluando alternativas en distintas regiones del país con el objetivo de no concentrar la investigación en una sola provincia. Las opciones analizadas fueron:
- Parque Industrial Sauce Viejo (Santa Fe, Argentina): ubicado cerca de la ciudad y el puerto de Santa Fe, representa una ubicación estratégica para la recepción de materias primas e insumos importados.
- Parque Industrial Pilar y Parque Industrial San Martín (Buenos Aires, Argentina): ambos se encuentran en la provincia con mayor densidad poblacional, cercana a una gran concentración de empresas, tanto grandes como PyMEs, lo que favorece el vínculo comercial y logístico.
- Parque Industrial Ferreyra (Córdoba, Argentina): situado en una ubicación central dentro del país, ofrece ventajas logísticas para acortar distancias y tiempos de entrega hacia distintas provincias.
Los factores valorados para armar la matriz de localización son los siguientes:
- Medios de transporte: Disponibilidad y accesibilidad a redes de transporte público para que los trabajadores puedan acercarse sin inconvenientes.
- Disponibilidad de mano de obra especializada: Personal calificado para los puestos de trabajo especiales.
- Cercanía a la fuente de abastecimiento: Cercanía a puertos en donde se reciben materias primas/insumos importados.
- Cercanía de mercado: Proximidad a potenciales clientes para asegurar una entrega rápida y sin inconvenientes.
- Factores climáticos: Estabilidad climática frente a catástrofes ambientales.
- Valor y disponibilidad de terrenos: Existencia de múltiples terrenos con distintas medidas pero que tengan el acceso a los mismos servicios.
- Posibilidad de tratar los desechos: Existencia de equipos de recolección de residuos generados por las máquinas o por el personal.
- Disponibilidad de Energía Eléctrica: Energía necesaria para el funcionamiento de los equipos, máquinas y la iluminación del interior.
- Disponibilidad de Agua y Gas: Servicios necesarios para la higiene y limpieza tanto de la planta como de los empleados, mantener la red anti incendios y calefacción de las distintas áreas.
- Existencia de otra Infraestructura Industrial: Presencia de otras industrias para generar alianzas.
- Seguridad: Zona segura y vigilada para resguardar las instalaciones.
- Acceso para logística de entrada y salida: Facilidad de entrada de materias primas/insumo y salida para el producto terminado.
- Consideraciones Legales y Políticas: Cumplimiento de políticas ambientales y posibilidad de obtener beneficios fiscales.
Luego, la matriz de localización resulta:
Parque industrial Sauce Viejo (Sta. Fe - Arg.) | Parque industrial Pilar (Bs. As. - Arg.) | Parque industrial Ferreyra (Cba. - Arg) | Parque industrial San Martín (Bs. As. - Arg) | ||||||
---|---|---|---|---|---|---|---|---|---|
Factor | IRfp | DRfa | IRfp x DRfa | DRfa | IRfp x DRfa | DRfa | IRfp x DRfa | DRfa | IRfp x DRfa |
Medios de Transporte | 1 | 3 | 3 | 5 | 5 | 2 | 2 | 5 | 5 |
Disponibilidad de Mano de Obra Especializada | 3 | 4 | 12 | 5 | 15 | 4 | 12 | 5 | 15 |
Cercanía a la Fuente de Abastecimiento | 4 | 3 | 12 | 4 | 16 | 2 | 8 | 4 | 16 |
Cercanía de Mercado | 5 | 5 | 25 | 5 | 25 | 3 | 15 | 3 | 15 |
Factores Climáticos | 1 | 5 | 5 | 4 | 4 | 5 | 5 | 4 | 4 |
Valor y disponibilidad de Terrenos | 3 | 4 | 12 | 1 | 3 | 3 | 9 | 2 | 6 |
Posibilidad de Tratar los Desechos | 1 | 4 | 4 | 5 | 5 | 4 | 4 | 4 | 4 |
Disponibilidad de Energía Eléctrica | 4 | 5 | 20 | 5 | 20 | 5 | 20 | 5 | 20 |
Disponibilidad de Agua y Gas | 4 | 5 | 20 | 5 | 20 | 5 | 20 | 5 | 20 |
Existencia de Otra Infraestructura Industrial | 3 | 3 | 9 | 5 | 15 | 3 | 9 | 4 | 12 |
Seguridad | 3 | 5 | 15 | 5 | 15 | 5 | 15 | 3 | 9 |
Acceso para Logística de Entrada y Salida | 3 | 5 | 15 | 5 | 15 | 5 | 15 | 5 | 15 |
Consideraciones Legales y Políticas | 4 | 4 | 16 | 3 | 12 | 5 | 20 | 3 | 12 |
TOTALES | 168 | 170 | 154 | 153 |
En base a este análisis, decidimos ubicar nuestra planta en el Parque Industrial Pilar.
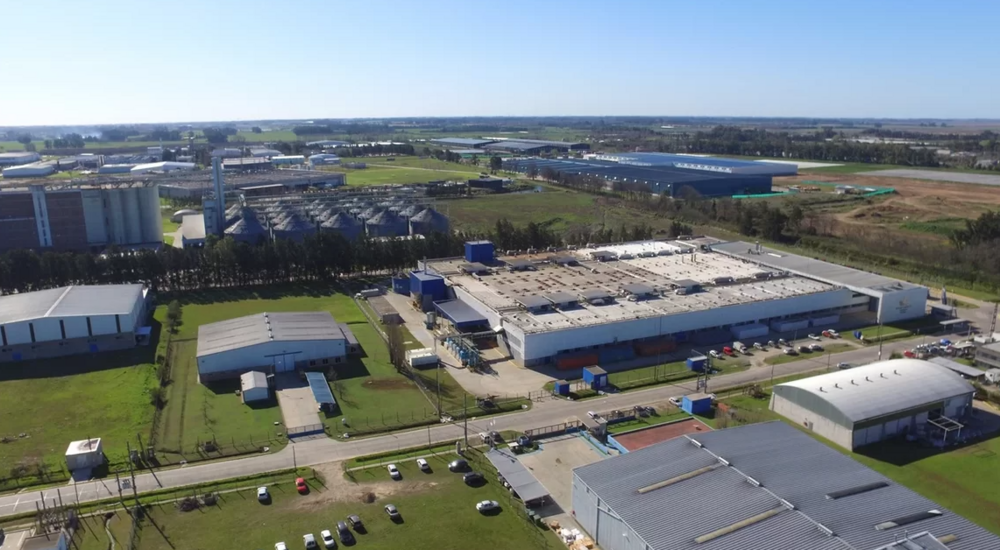
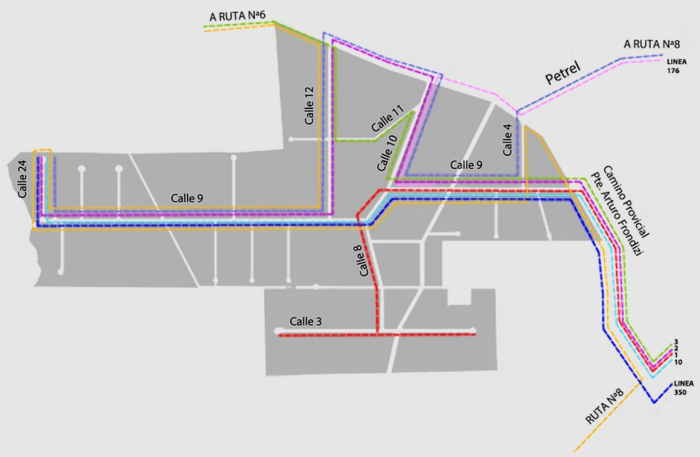
Definición Técnica del Producto
Para éste análisis trabajaremos tomando la válvula de 2 pulgadas como producto "tipo" debido a que se trata de la medida mas comercializada. Sin embargo, tal como se detalló en el dimensionamiento comercial, dentro del catálogo de Valvex se ofrecerá a la venta varias medidas de entre 1" y 6".
Planos y/o Dibujos
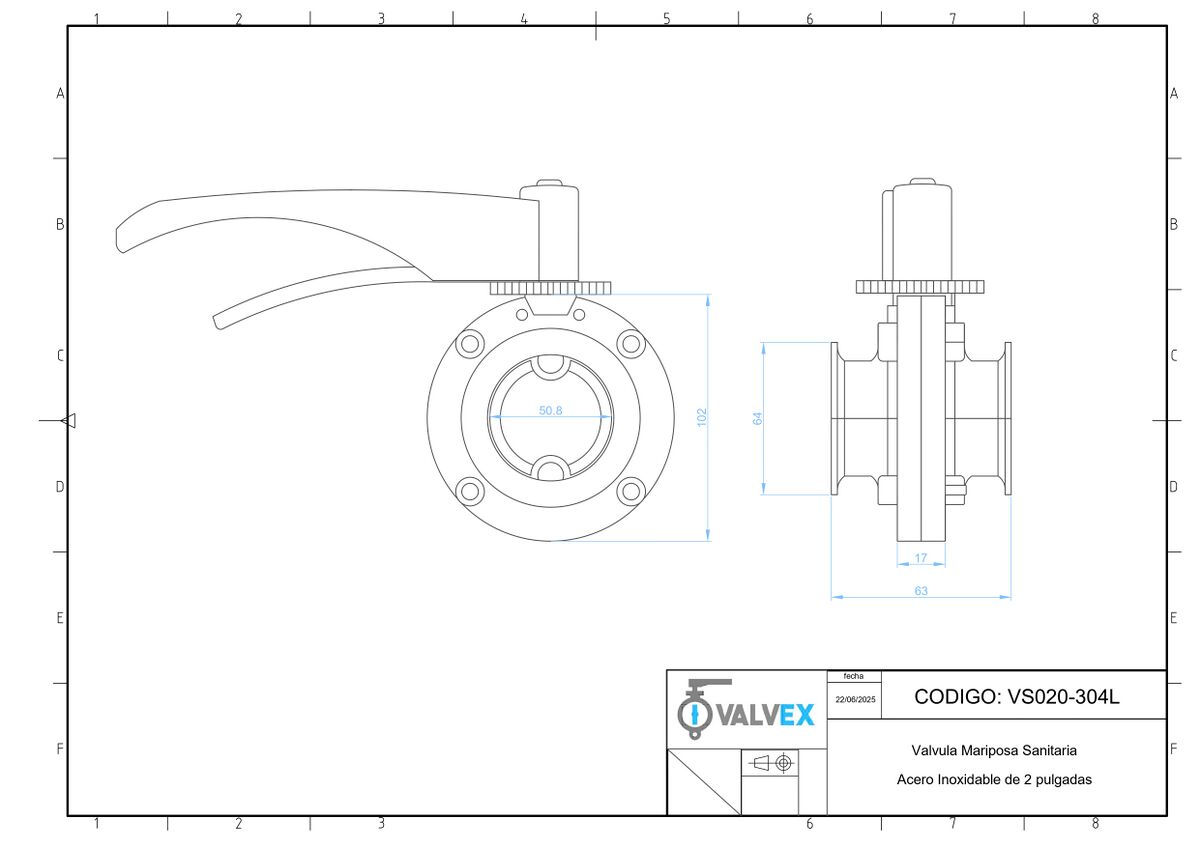
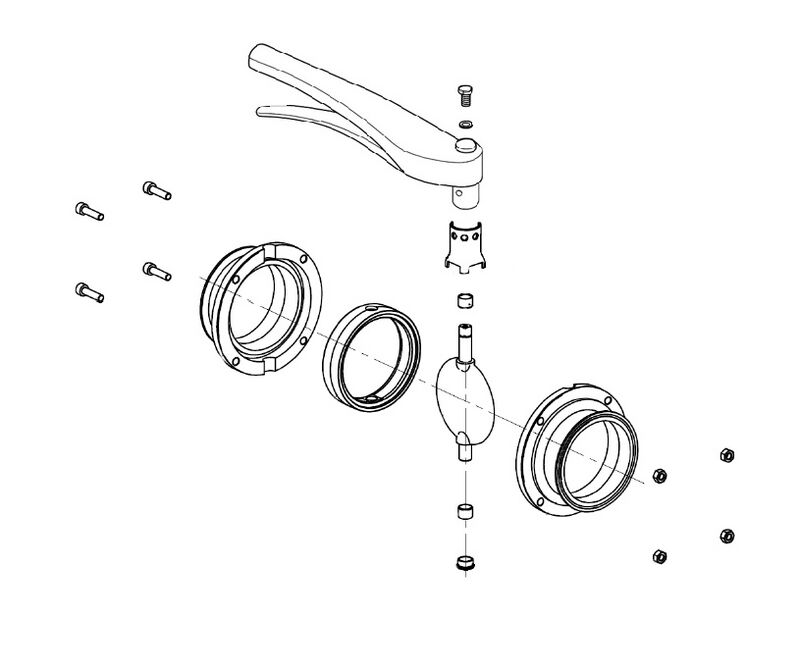
Listado de Materiales

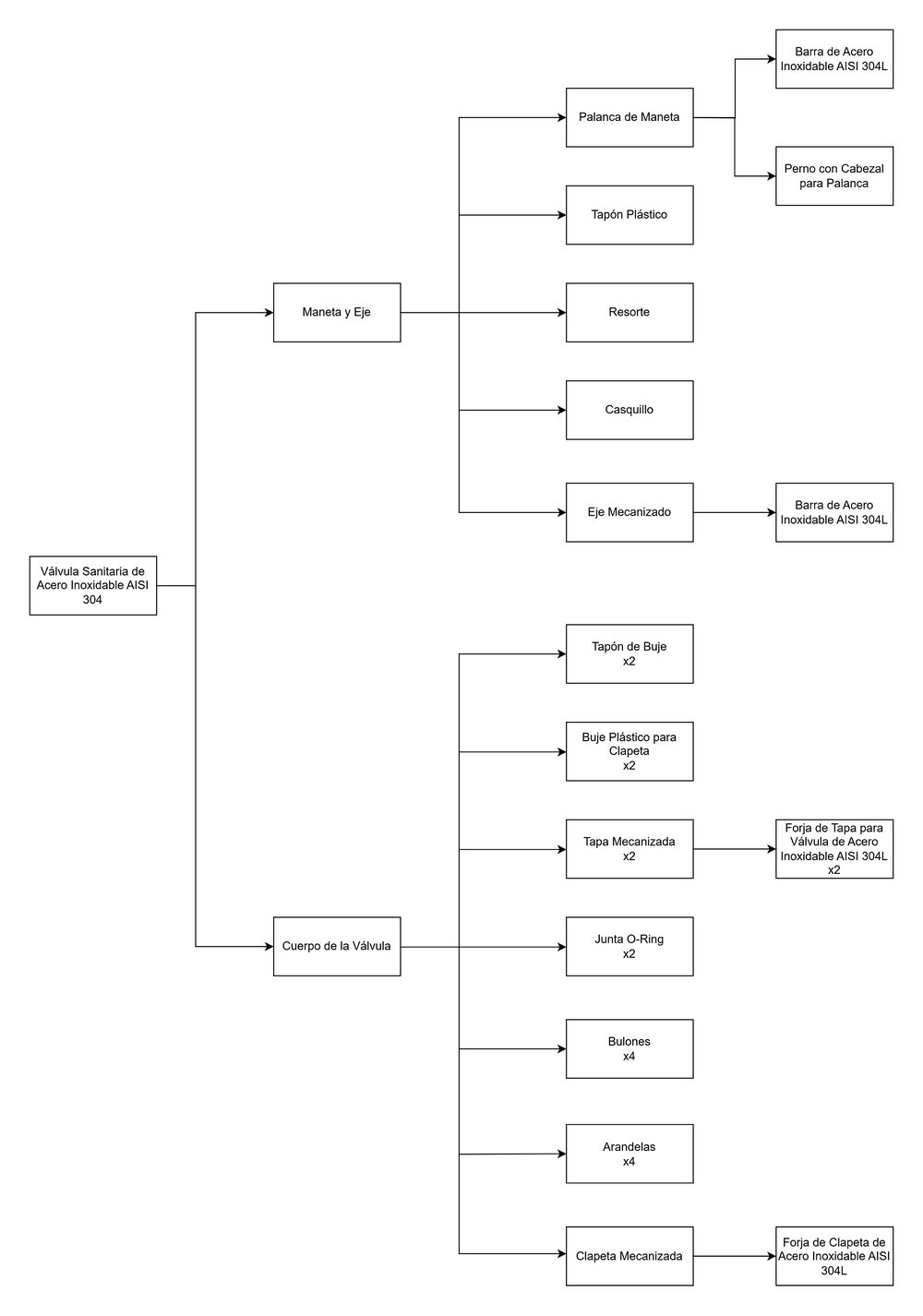
Especificaciones Técnicas del Producto
- Material: Acero inoxidable AISI 304L
- Elastómero: EPDM
- Extremos: clamp, roscados DIN 11851 y para soldadura
- Presión Máxima de Trabajo: 10 bar.
- Temperatura Máxima de Operación: 120°C
- Accionamiento: manual, con posibilidad de adaptación a actuadores automáticos.
- Acabado superficial: pulido intermedio.
- Acabado interior: pulido sanitario
Dentro del catálogo de la empresa se ofrecerán los siguientes diámetros:
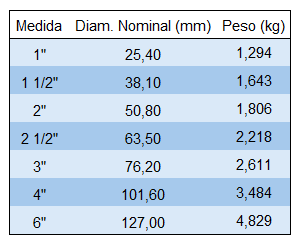
Normas Aplicables
- API 609: establece los requisitos de diseño, fabricación y pruebas para válvulas de mariposa. Estas válvulas están diseñadas para instalarse entre bridas ANSI, con diferentes tipos de conexión como lug, wafer y bridadas. La norma cubre aspectos como la resistencia a la presión y temperatura y los materiales de construcción.
- API 598: establece las normas para la inspección y prueba de válvulas, incluyendo requisitos de fuga y clasificación. Abarca una amplia gama de tipos de válvulas y se utiliza en diversos sectores industriales, especialmente en el petróleo y el gas.
- Espesores mínimos de acuerdo a ASME B 16.34 o EN 12.516-1.
- ISO 5208: establece requisitos de pruebas de presion para válvulas metálicas.
- ISO 14313: especifica requerimientos y recomendaciones para el diseño, producción y prueba de válvulas para la industria del petróleo y el gas natural.
- ISO 10497: detalla los requisitos para el ensayo de fuego para válvulas.
- ISO 15510: lista las composiciones químicas del acero inoxidable basándose en los acuerdos existentes en las normas ISO, ASTM, EN, JIS, y GB.
- ISO 7005: establece especificaciones normalizadas para bridas de tuberías para aplicaciones industriales.
- ISO 5211: establece requisitos y dimensiones para la fijación de actuadores de válvulas.
Plan de Ensayos
- Control visual: El control visual de la válvula terminada consiste en inspeccionar a simple vista toda su superficie para verificar que no presente rayaduras, fisuras, poros, rebabas, manchas, ni restos de material o suciedad, asegurando así un acabado correcto y apto para su uso final.
- Control dimensional: Con ayuda de un calibre o micrómetro se controlarán las tolerancias de ensamblado, medidas de paso, longitudes totales y bocas de conexión.
- Control de rugosidad superficial: Se mide el valor en de rugosidad en zonas de contacto con los fluídos, el cual debe ser menor a 0,4 micrónes
- Ensayo de líquidos penetrantes: para detección y control de fisuras superficiales
- Ensayo funcional: se verifica que el mecanismo de cierre y apertura funcione correctamente, sin trabas y sin juego en el cierre.
- Ensayo de estanquedad: Se somete la válvula a una prueba de presión de hasta 1,5 veces superior a la de diseño, para verificar su resistencia en condiciones exigentes. Se coloca la válvula en una banco de trabajo especialmente diseñado para esto. La válvula se instala en la mesa de trabajo alrededor de un ducto que sobresale de la mesa. Luego se dispone una manguera que funciona como el otro extremo del ducto. Luego se activa el flujo de fluido de prueba (agua) y se ajusta la presión. Este ensayo se realiza tanto con la válvula abierta como cerrada.
Se dejará asentado en una planilla los resultados de cada control, con numero de lote, operario, fecha y firma.
Acondicionamiento del Producto
El producto se distribuirá a los clientes con un embalaje cuidado que lo proteja durante el traslado y evite el deterioro y el daño al mismo.
Luego de limpiar y probar el producto terminado, se le colocan protectores en las bocas. Se lo embolsa con film sellado y luego e coloca en caja individual con espuma de polietileno y se coloca la hoja técnica dentro de la caja.
Se cargan sobre pallet de madera tratada, zunchado y etiquetado y así estarán listas para enviar al cliente.
Embalaje primario:
- Protectores de goma en las bocas para evitar contaminación y golpes.
- Bolsas selladas, desecantes o film anti-humedad si se exporta o se almacena por mucho tiempo.
- Etiqueta de trazabilidad con número de lote, modelo, material y presión nominal.
Embalaje secundario:
- Caja de cartón corrugado resistente.
- Interior con espuma de polietileno para amortiguar impactos.
- Manual de instalación y hoja técnica impresa.
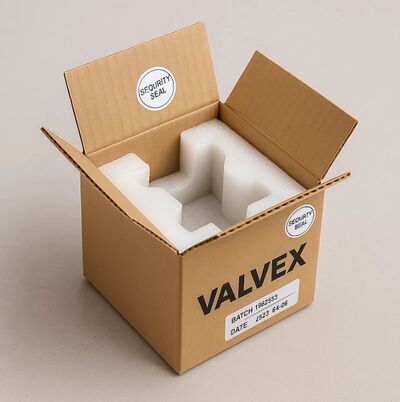
Definición del Proceso de Producción
Diagrama de Flujo de Fabricación y Control. Cursogramas gráficos o analíticos
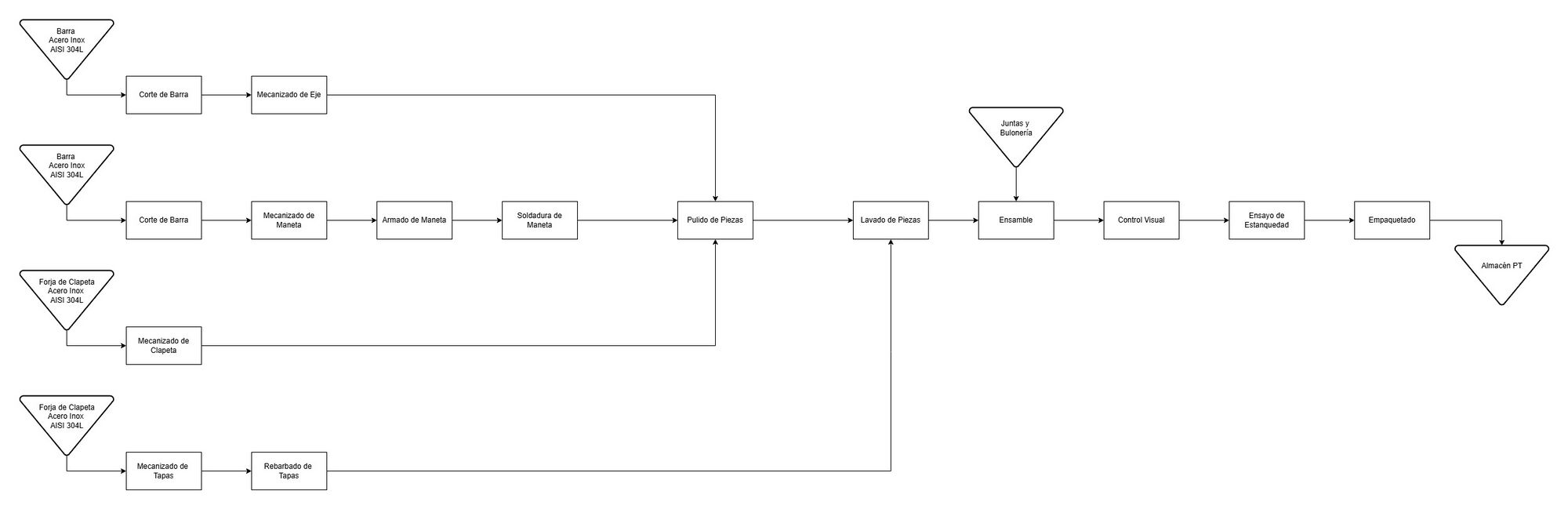
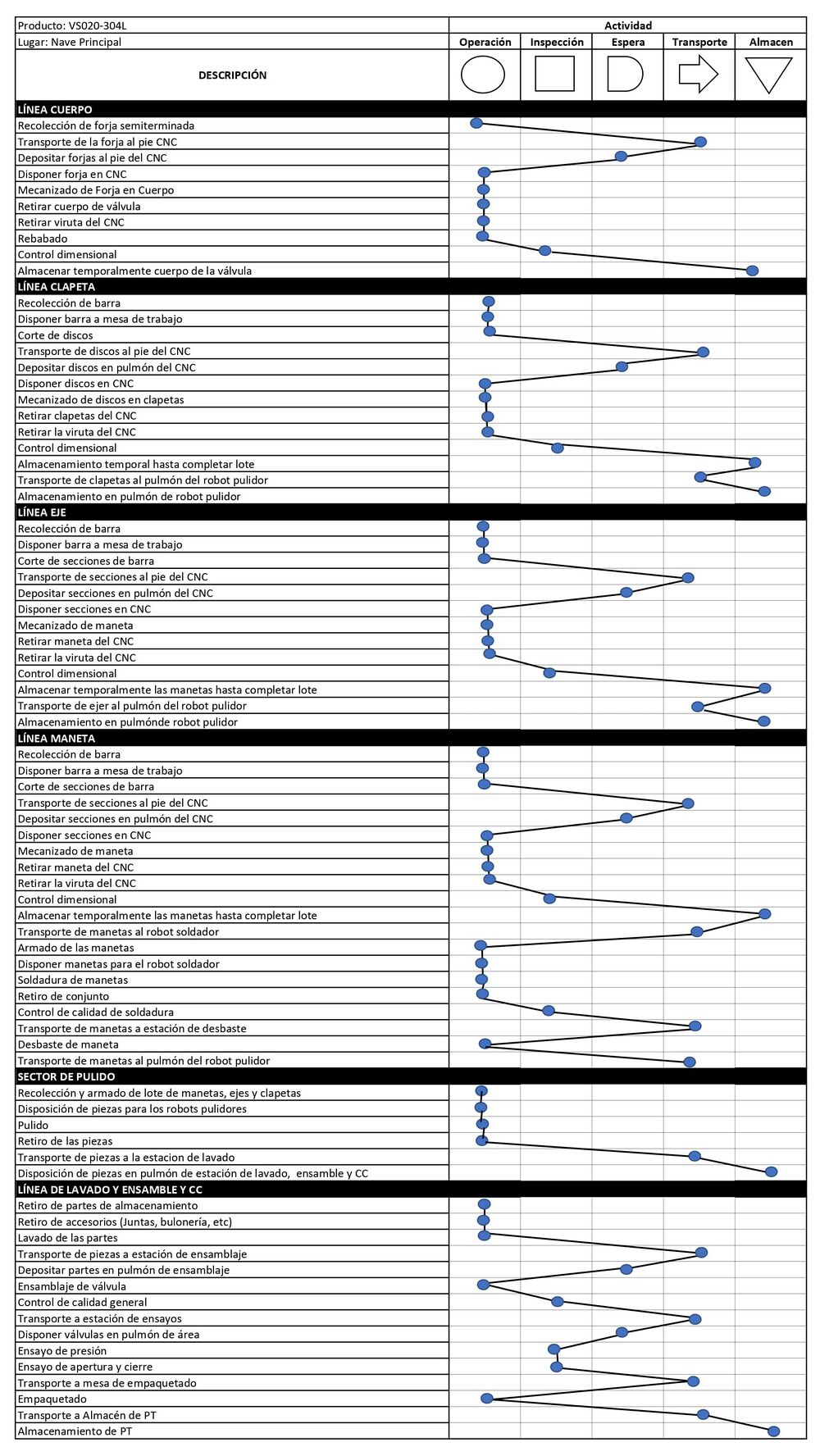
Descripción de cada etapa del proceso productivo
- Mecanizado de Tapas: a partir de una pieza pre forjada de Acero Inoxidable AISI 304L, se mecanizan las tapas que conformarán el cuerpo de la válvula en un torno CNC. Durante este proceso no solo se mecaniza el cuerpo e si mismo sino que también se realiza el avellanado de los orificios para la bulonería y para el paso del eje.
- Rebarbado de Tapas: se eliminan rebabas, aristas vivas e inperfecciones superficiales dejadas por el mecanizad, asegurando un acabado seguro y funcional.
- Mecanizado de Clapeta: a partir de un disco forjado de acero inoxidable AISI 304L, se realizan un mecanizado CNC que permite reducir su espesor al adecuado para la clapeta de la válvula.
- Mecanizado de Maneta: se realiza un mecanizado en un torno CNC de una barra maciza de acero inoxidable AISI 304L para darle forma a la maneta.
- Armado de Maneta: se ensamblan las piezas individuales que conforman la maneta, incluyendo la bulonería y los tapones de polímero y se la deja lista para ser soldada al Casquillo que la unirá al cuerpo.
- Soldadura de Maneta: se suelda la maneta en si misma al casquillo que la mantendrá fijada al cuerpo de la válvula para conformar una unidad sólida unica resistente a las condiciones de operación. La soldadura es realizada por un brazo robótico para soldadura programable.
- Mecanizado de Eje: a partir de una barra maciza de acero inoxidable AISI 304L se mecaniza en un torno CNC el eje con la medida y la tolerancia exacta requerida.
- Pulido: se pulen todas las piezas internas que conformarán la válvula. El pulido es realizado por un brazo robótico con un paño de pulir en su cabezal, y las piezas se colocan en un posicionador rotativo motorizado. El eje y la clapeta reciben un pulido sanitario cuya rugosidad debe ser menor a 0,4 micrónes, mietras que el pulido de la maneta tiene una terminación de calidad un poco inferior debido a que no entra en contacto directo con los fluídos.
- Lavado de Piezas: se lavan a mano todas las piezas antes del ensamble final para eliminar cualquier resto de polvo o viruta que pueda afectar a la calidad de terminacion de la válvula. El lavado se hace con pistolas de lavado especiales y agua destilada.
- Ensamble: se ensamblan manualmente todas las piezas de acero que conformarán la válvula. En esta etapa se agrega la bulonería, que es ajustada con torquímetros según las especificaciones del producto, así como también las juntas y O-Rings.
- Control Visual: se inspecciona el producto ensamblado para verificar la calidad del mismo, acabados superficiales, presencia de defectos y cumplimiento de especificaciones.
- Ensayo de Estanquedad: se somete la válvula a una prueba de presión de hasta 1,5 veces superior a la de diseño, para verificar su resistencia en condiciones exigentes. Se coloca la válvula en una banco de trabajo especialmente diseñado para esto. La válvula se instala en la mesa de trabajo alrededor de un ducto que sobresale de la mesa. Luego se dispone una manguera que funciona como el otro extremo del ducto. Luego se activa el flujo de fluido de prueba (agua) y se ajusta la presión. Este ensayo se realiza tanto con la válvula abierta como cerrada.
- Empaquetado: una vez ensayado el producto, se embala adecuadamente para su protección durante almacenamiento y transporte de acuerdo a el acondicionamiento del producto ya definido.
Determinación de las máquinas e instalaciones. Cálculos.
Especificaciones técnicas de las máquinas (capacidades, tamaño de lotes, tiempos).
Torno CNC
- Modelo: Hyundai WIA L300LC
- Dimensiones: 4170 x 2002 x 1997 mm
- Peso: 7600 kg
- Diámetro de giro máximo: 560 mm
- Longitud máxima de giro: 1320 mm
- Tamaño del mandril: 12"
- Velocidad del husillo: 3000 RPM
- N° de herramientas: 12
- Consumo de Energía: 24 kWh
Brazo Robótico para Soldadura
- Modelo: Yaskawa AR900
- Área de base: 927 x 927 mm
- Peso: 34 kg
- Alcance horizontal: 927 mm
- Alcance vertical: 1693 mm
- Capacidad de Carga: 7 kg
- N° de Ejes: 6
- Consumo de Energía: 1,25 kWh
Brazo Robótico para Pulido
- Modelo: Fanuc ARC Mate 100iD/8L
- Área de base: 343 x 343 mm
- Peso: 18 kg
- Alcance: 2032 mm
- Capacidad de Carga: 8 kg
- N° de Ejes: 6
- Consumo de Energía: 1 kWh
Posicionador de Piezas de Trabajo
- Modelo: ABB IRP A-250
- Área de base: 1293 x 440 x 1210 mm
- Capacidad de Carga: 250 kg
- Velocidad Máxima de Rotación: 150°/s Eje 1 - 180°/s Eje 2
- Consumo de Energía: 1 kWh
Sierra de Cinta
- Modelo: FEMI 2200 DAXL
- Área de base: 780 x 1240 x 1080 mm
- Peso: 143 kg
- Capacidad de Corte Cilindrico: 175 mm a 0°
- Velocidad de la Hoja: 35 m/min
- Consumo de Energía: 2 kWh
Banco de Pruebas para Ensayo de Estanquedad
- Modelo: YFJ-D600
- Área de base: 3100 × 1150 ×1800 mm
- Peso: 3500 kg
- Máxima Presión Nominal: 150 bar
- Consumo de Energía: 2,2 kWh
- Reposición de agua por prueba: 0,25 lt/h (circuito cerrado)
Cuadro Resumen:
Máquina | Modelo | Consumo Energético | Consumo de Agua | Dimenisones |
---|---|---|---|---|
Torno CNC | Hyundai L300LC | 24 kWh | 4170 x 2002 x 1997 mm | |
Brazo Robótico de Soldadura | Yaskawa AR900 | 1,25 kWh | 927 x 927 mm | |
Brazo Robótico de Pulido | Fanuc ARC Mate 100iD/8L | 1 kWh | 343 x 343 mm | |
Posicionador de Piezas de Trabajo | ABB IRP A-250 | 1 kWh | 1293 x 440 x 1210 mm | |
Sierra de Cinta | 2200 DAXL | 2 kWh | 780 x 1240 x 1080 mm | |
Banco de Pruebas | YFJ-D600 | 2,2 kWh | 2,5 lt/h | 3100 × 1150 ×1800 mm |
Consumos de Energía, Agua y Otros Servicios:
Mantenimiento y medios de control (máquinas, tareas, etc.)
Se desarrolla un plan de mantenimiento preventivo, el cual consiste en la revisión mensual, semanal o quincenal dependiendo de la máquinas. Se utilizarán planillas en donde se registrarán los mantenimientos realizados con fecha, observaciones y firma del responsable. Estos consisten en chequeo de temperaturas, velocidades de funcionamiento, verificación del cableado, enchufes, entre otros.
A continuación se detallan las tareas de mantenimiento sobre las maquinas:
Equipamiento | Tareas principales | Frecuencia | Medios de Control |
---|---|---|---|
Torno CNC | Lubricación, verificación de precisión, limpieza de guías, cambio de fluidos de corte, revisión de husillo, calibración de sensores. | Mensual | • Sensores de temperatura y vibración en el husillo y el motor principal.
• Sistemas de monitoreo por software. • Alarmas que indican sobrecarga, pérdida de origen o interferencias. |
Brazo Robótico de Pulido | Lubricación de ejes, chequeo de presión neumática | Quincenal | • Ciclos de calibración automática en el cabezal.
• Sensores de fin de carrera y sensores de emergencia. |
Brazo Robótico de soldadura MIG / TIG | Limpieza de boquillas, revisión de cables y gas, lubricación de ejes, chequeo de presión neumática | Quincenal | |
Banco de pruebas hidráulicas | Verificación de estanquedad, control de bomba, revisión de filtros de agua, rellenado de tanques | Mensual (el rellenado del tanque es diario) | • Manómetros calibrados y sensores de presión
• Control automático de ciclos • Sistemas de corte automático |
Además, los equipos programables con softwares integrads, como los brazos robóticos o el torno CNC, recibirán las actualizaciones correspondientes cada vez que sea necesario. El encargado de realizar esto es el responsable de programación de máquinas.
Además de estos mantenimientos, se capacitará al personal que controle y opere dichas máquinas para evitar fallas no deseadas en el funcionamiento y para realizar una limpieza adecuada y una correcta puesta en marcha de las máquinas, con el fin de asegurar los parámetros y la correcta operación de las mismas.
En caso de ocurrencia de fallas imprevistas, se contactará al proveedor de las máquinas para llevar a cabo un mantenimiento correctivo lo antes posible y continuar con la producción.
Descripción de los sistemas de seguridad (incendios, accidentes, etc.)
Para tener un funcionamiento óptimo y seguro de la planta, es esencial contar con medidas que protejan a los trabajadores, las maquinarias y la materia prima. La seguridad no solo previene accidentes, sino que garantiza el correcto funcionamiento de los procesos. Por ello se implementarán los siguientes sistemas de seguridad:
Infraestructura:
- Salidas de emergencia señalizadas y libres.
- Matafuegos tipo ABC distribuidos según carga de fuego.
- Iluminación de emergencia.
- Detectores de humo, alarma contra incendios y aspersores contra incendios, los cuales se activarán automaticamente frente a la detección de un incendio.
- Sistemas de señalización y evacuación.
- Sistemas de seguridad eléctrica como disyuntores o puesta a tierra de maquinas - en caso de detectar una pérdida, cortarán automaticamente el funcionamiento de las máquinas.
- Sistemas de seguridad eléctrica como disyuntores y puesta a tierra de maquinas que, en caso de detectar una desperfecto, cortarán automaticamente el suministro eléctrico.
Sistemas de Seguridad Activa en Máquinas:
- Botones mushroom para paradas de emergencia.
- Sensores de proximidad en prensas, herramientas de corte y robots.
- Encapsulado de partes moviles en los equipos CNC.
- Lock Out para tareas de mantenimiento.
- Tarjetas con instrucciones operativas en cada estación
Equipos de Protección Personal (EPP):
- Obligatorios: botines con puntera, anteojos, guantes, protección auditiva y ropa ignífuga (en los puestos de soldadura).
- Capacitación y cartelera con pictogramas de uso obligatorio.
Seguridad del Personal y Activos de la Empresa:
- Sistema de vigilancia CCTV.
- Alarma de seguridad antirobos.
- Sistema de control de ingresos y egresos a planta.
Balance Anual de Materiales
A continuación, presentamos el cuadro de necesidades de alimentación de MP en estado de régimen que se precisan según cada pieza, de acuerdo al volumen establecido en el plan de ventas.
Comenzamos por la salida final de la línea, donde contamos con un descarte estimado de control de calidad de 2 válvulas cada 100 fabricadas. Este descarte nos va a obligar a producir un 2% por encima de las necesidades de PT planteadas en el plan de ventas.
CONJUNTO FINAL | |||||
---|---|---|---|---|---|
Sección operativa | Alimentacion KG | Agregado | Desperdicios | Producción (KG) | |
Recuperable | No recuperable | ||||
Lavado de partes | 82285,71 | - | - | - | 82285,71 |
Ensamble de partes | 82285,71 | - | - | - | 82285,71 |
Ensayo / control de calidad | 82285,71 | - | - | Descarte de CC (2 cada 100) | 80640 |
Empaquetado | 80640 | - | - | - | 44800*1,8 = 80640 |
Trabajamos con kilogramos para poder adaptarlo a los desperdicios en función del peso. Como esta línea trabaja con válvulas completas, simplemente multiplicamos la necesidad en válvulas por el peso de una válvula de 2", nuestro producto más representativo (1,8kg).
Estimaciones de desperdicios:
Basándonos en características técnicas del mecanizado en torno CNC, estimamos un desperdicio del 15% para torneados que parten de forjas semielaboradas y un 20% para los que parten de cortes brutos de MP.
Colocamos desperdicios de entre el 0,05% y 0,5% para procesos de tratamiento de superficies como el pulido y el rebabado, donde la pérdida es mínima.
Al utilizar procesos de corte manuales con sierra, estimamos un desperdicio por corte de un 2%
Como los porcentajes de desperdicio se encuentran en función del peso, usaremos como referencia para pasar de necesidades de PT a necesidades en KG, el peso de nuestro producto más representativo, la válvula de 2", la cuál pesa 1,8kg.
Todos nuestros desperdicios son no recuperables vendibles, por lo que no afectarán a la cantidad de materia prima a adquirir.
Ahora pasamos a los procesos de fabricación del cuerpo, clapeta, eje y maneta; distinguiendo la materia prima necesaria para cada una.
FORJA PARA CUERPO | |||||
---|---|---|---|---|---|
Sección operativa | Alimentacion (KG) | Agregado | Desperdicios | Producción (KG) | |
Recuperable | No recuperable | ||||
Mecanizado de cuerpo | 67968,61 | - | - | 15% | 57773,32 |
Rebabado de cuerpo | 57773,32 | - | - | 0,30% | 44800/0,98*1.8*0.7=57600 |
Nota: el cuerpo representa un 70% del peso total de una válvula, por lo que para obtener la salida final del proceso, multiplicamos la necesidad de válvulas (tomando en cuenta el descarte de control de calidad) x 1,8kg x 0,7.
FORJA PARA CLAPETA | |||||
---|---|---|---|---|---|
Sección operativa | Alimentacion (KG) | Agregado | Desperdicios | Producción (KG) | |
Recuperable | No recuperable | ||||
Mecanizado de forja y clapeta | 4889,23 | - | - | 15% | 4155,84 |
Pulido de clapeta | 4122,53 | - | - | 0,20% | 4114,29 |
Nota: la clapeta representa aproximadamente un 5% de la totalidad de la válvula. Cálculos análogos a la forja de cuerpo.
BARRA PARA MANETA | |||||
---|---|---|---|---|---|
Sección operativa | Alimentacion (KG) | Agregado | Desperdicios | Producción (KG) | |
Recuperable | No recuperable | ||||
Corte de barra | 10569,5077 | 2% | 10358,12 | ||
Mecanizado de maneta | 10358,12 | - | - | 20% | 8286,49 |
Armado de maneta | 8286,49 | - | - | - | 8286,49 |
Soldadura de maneta | 8286,49 | - | - | - | 8286,49 |
Desbaste de maneta | 8286,49 | - | - | 0,50% | 8245,06 |
Pulido de maneta | 8245,06 | - | - | 0,20% | 8228,57 |
Nota: la maneta representa un 10% del peso de la válvula
BARRA PARA EJE | |||||
---|---|---|---|---|---|
Sección operativa | Alimentacion (KG) | Agregado | Desperdicios | Producción (KG) | |
Recuperable | No recuperable | ||||
Corte de barra | 9898,03308 | 2% | 9700,07 | ||
Mecanizado de eje | 9700,07 | - | - | 15% | 8245,06 |
Pulido de eje | 8245,06 | - | - | 0,20% | 8228,57 |
Nota: El eje representa un 10% del peso de la válvula
El resto de materias primas son componentes terminados que se ensamblan junto a las otras partes para armar las válvulas y no pasan por ningún proceso de transformación que haga que sufran desperdicios. Tomamos en cuenta que partimos de una necesidad superior a la del plan de ventas por el descarte de control de calidad:
Nivel | Componente | Material | Cantidad | Necesidad anual según plan de ventas | Necesidad anual tomando en cuenta descarte de CC | Necesidad anual redondeada |
---|---|---|---|---|---|---|
3 | Perno con Cabezal para Palanca | Acero Inoxidable 304 | 1 | 44800 | 45714,28571 | 45714 |
2 | Resorte Maneta | Acero Inoxidable 302 | 1 | 44800 | 45714,28571 | 45714 |
2 | Casquilo de Maneta | Acero Inoxidable 304 | 1 | 44800 | 45714,28571 | 45714 |
2 | Tapón Plástico Maneta | PTFE con base EPDM | 1 | 44800 | 45714,28571 | 45714 |
2 | Etiqueta Maneta | 1 | 44800 | 45714,28571 | 45714 | |
2 | Tapón de Buje | PTFE con base EPDM | 2 | 89600 | 91428,57143 | 91428 |
2 | Buje Plástico para Clapeta | PEEK (Polieter Éter Cetona) | 2 | 89600 | 91428,57143 | 91428 |
2 | Junta O-Ring | Vitón(FMK) | 2 | 89600 | 91428,57143 | 91428 |
2 | Bulones 304 | Acero Inoxidable 304 | 4 | 179200 | 182857,1429 | 182857 |
2 | Arandelas 304 | Acero Inoxidable 304 | 4 | 179200 | 182857,1429 | 182857 |
2 | Etiqueta Tapa | 1 | 44800 | 45714,28571 | 45714 |
Ritmo de Trabajo
Se decide que, en general, la planta trabajará con un turno de 8 horas, de manera tal que se obtiene el siguiente cuadro detallando el rítmo de trabajo:
Días del Año | 365 |
Feriados | 15 |
Vacaciones | 15 |
Sabados y Domingos | 100 |
Días Activos | 235 |
Turnos | 1 |
Horas por Turno | 8 |
Horas Activas | 1880 |
Sin embargo, en las secciones de mecanizado se trabajará en dos turnos de 6 horas para reducir el número de tornos necesarios en la planta.
Capacidad Real por Sección Operativa
Se analizan las capacidades reales de cada sección, teniendo en cuenta las horas activas al año, la información brindada por el tecnólogo y la capacidad teórica:
Sección Operativa | Cap. Teórica (pz/hora) | Horas Activas al Año | Cap. Teórica Anual (pz/año) | Rendimiento | Cap. Real Anual |
Mecanizado de cuerpo | 12 | 2.820 | 33.840 | 100% | 33.840 |
Rebabado de cuerpo | 60 | 1.880 | 112.800 | 95% | 107.160 |
Mecanizado de clapeta | 7,60 | 2.820 | 21.445 | 100% | 21.445 |
Pulido de clapeta | 10 | 1.880 | 18.800 | 100% | 18.800 |
Corte de barra | 60 | 1.880 | 112.800 | 95% | 107.160 |
Mecanizado de maneta | 20 | 2.820 | 56.400 | 100% | 56.400 |
Armado de maneta | 12 | 1.880 | 22.560 | 95% | 21.432 |
Soldadura de maneta | 30 | 1.880 | 56.400 | 100% | 56.400 |
Desbaste de maneta | 30 | 1.880 | 56.400 | 100% | 56.400 |
Pulido de maneta | 5 | 1.880 | 9.400 | 100% | 9.400 |
Corte de barra | 60 | 1.880 | 112.800 | 95% | 107.160 |
Mecanizado de eje | 26,32 | 2.820 | 74.211 | 100% | 74.211 |
Pulido de eje | 10 | 1.880 | 18.800 | 100% | 18.800 |
Lavado de partes | 20 | 1.880 | 37.600 | 95% | 35.720 |
Ensamble de partes | 12 | 1.880 | 22.560 | 95% | 21.432 |
Ensayo / control de calidad | 12 | 1.880 | 22.560 | 100% | 22.560 |
Empaquetado | 60 | 1.880 | 112.800 | 90% | 101.520 |
Cantidad de Máquinas y Puestos de Trabajo
En función de las capacidades reales y el programa anual de producción, se definen la cantidad de máquinas y puestos de trabajo necesarias para cumplir con el programa anual de producción:
Sección Operativa | Cap. Real Anual | Necesidad Anual | Máq. Necesarias | Máq. Necesarias Redond. | Cap. Real Anual (pz/año) | Aprovechamiento Seccional |
Mecanizado de cuerpo | 33.840 | 45.714 | 1,35 | 2 | 67.680 | 68% |
Rebabado de cuerpo | 107.160 | 45.714 | 0,43 | 1 | 107.160 | 43% |
Mecanizado de clapeta | 21.445 | 45.714 | 2,13 | 3 | 64.335 | 71% |
Pulido de clapeta | 18.800 | 45.714 | 2,43 | 3 | 56.400 | 81% |
Corte de barra | 107.160 | 45.714 | 0,43 | 1 | 107.160 | 43% |
Mecanizado de maneta | 56.400 | 45.714 | 0,81 | 1 | 56.400 | 81% |
Armado de maneta | 21.432 | 45.714 | 2,13 | 3 | 64.296 | 71% |
Soldadura de maneta | 56.400 | 45.714 | 0,81 | 1 | 56.400 | 81% |
Desbaste de maneta | 56.400 | 45.714 | 0,81 | 1 | 56.400 | 81% |
Pulido de maneta | 9.400 | 45.714 | 4,86 | 5 | 47.000 | 97% |
Corte de barra | 107.160 | 45.714 | 0,43 | 1 | 107.160 | 43% |
Mecanizado de eje | 74.211 | 45.714 | 0,62 | 1 | 74.211 | 62% |
Pulido de eje | 18.800 | 45.714 | 2,43 | 3 | 56.400 | 81% |
Lavado de partes | 35.720 | 45.714 | 1,28 | 2 | 71.440 | 64% |
Ensamble de partes | 21.432 | 45.714 | 2,13 | 3 | 64.296 | 71% |
Ensayo / control de calidad | 22.560 | 45.714 | 2,03 | 3 | 67.680 | 68% |
Empaquetado | 101.520 | 45.714 | 0,45 | 1 | 101.520 | 45% |
Cuello de botella y capacidad real
Luego de obtener las capacidades reales y el grado de aprovechamiento de las secciones, se define al proceso de "Mecanizado de cuerpo" como el cuello de botella del sistema con un aprovechamiento seccional del 71,14%.
La capacidad real del proceso será de 45.120 u/año, o bien, 24,04 u/hora.
Determinacion de la evolución de las mercaderias
Evolución de la producción y período puesta en marcha
Para obtener el volumen de producción en el año 1, hay que considerar el período de puesta en marcha que es el momento en donde se generan más desperdicios. Para los años siguientes, cómo se trabaja en estado de régimen, se estima una producción estable de acuerdo a lo establecido en el cuadro de mercaderías.
Se toma que el tiempo de trabajo neto al año es de 11 meses, por lo que se produce una cantidad de 4.072,73 u/mes.
Se define al período de puesta en marcha como los 4 primeros meses del año, quedando definido de la siguiente manera:
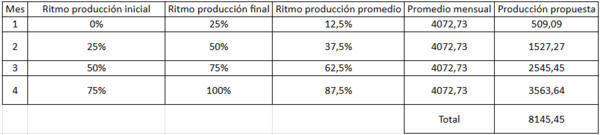
Se observa que durante el período de puesta en marcha se producen 8.146 unidades, mientras que para el resto del año (7 meses restantes) se producirán 28.509 unidades. La suma de ambas, será la producción total para el año 1, siendo 36.655 unidades,
Quedando la producción de la siguiente manera:
Producción por año | |
---|---|
Producción Año 1 | 36.655 unidades |
Producción Año 2 - n | 44.800 unidades |
Stock promedio de producto terminado
Para el stock promedio de producto terminado, hay que trabajar en el período en régimen y además, tener en cuenta el stock de seguridad y el ritmo de entregas.
- Ritmo de entregas se define en entregas cada 1 semana.
- Stock de seguridad, al ser un producto de nicho y no de consumo masivo, se estabelece en 0 semanas.
En función de dichas condiciones y las semanas activas al año (47 semanas) se establece el stock promedio de producto terminado:
Stock promedio de producto terminado | |
---|---|
Semanas activas al año | 47 semanas |
Stock de seguridad | 0 semanas |
Ritmo de entregas | 1 semana |
Stock mínimo PT | 0 |
Stock máximo PT | 954 unidades |
Stock promedio PT | 477 unidades |
Stock máximo PT = 44.800 unidades / 47 semanas = 954 u/semana
Evolución de las ventas
Para determinar la evolución de las ventas, hay que considerar el volumen de producción y el stock promedio para el año 1. Para el resto de años, se trabaja en estado de régimen.
Ventas año 1 = 36.655 unidades - 477 unidades = 36.178 unidaes
Ventas año 2 - n = 44.800 unidades
Ventas por año | |
---|---|
Año 1 | 36.178 unidades |
Año 2 - n | 44.800 unidades |
Consumo de Materia Prima para el Programa de Producción y Formación de la Mercadería en Curso y Semielaborada
Para determinar el consumo de materia prima hay que considerar múltiples variables, una de ellas es el desperdicio que se da en producción. Se sabe que para el período de puesta en marcha se genera un 100% adicional de desperdicios no recuperables. En esta sección se trabajará con unidades equivalentes a producto terminado, no en kg.
Consideraciones | |
---|---|
Desperdicio no recuperable | 8.404 u. eq. PT. |
Total producción | 44.800 u. |
% desperdicio no recuperable | 18,76% |
% desperdicio adicional en PPM | 100% |
Ciclo de elaboración | 5 días |
Para el año 1:
Materia prima consumida para año 1 | |
---|---|
Consumo MP para mercadería en curso | 794 u. eq. PT. |
Consumo MP en PPM | 10.488 u. eq. PT. |
Consumo MP resto del año | 33.858 u. eq. PT. |
Consumo MP año 1 | 44.346 u. eq. PT. |
Volumen producción año 1 | 36.655 u. |
Desperdicios no recuperables año 1 | 7.691 u. eq. PT. |
Consumo Total MP año 1 | 45.140 u. eq. PT. |
Consumo mp en PPM = 8145,45 unidades * 1,2876 = 10.488 unidades
Consumo mp resto del año = 4072,73 u/mes * 7 meses * 1,1876 = 33.858 unidades
Con el volumen de producción del año 1 y el consumo total, se obtienen los desperdicios no recuperables del año 1:
Desperdicios no recuperables año 1: 44.346 unidades - 36.655 unidades = 7.691 u. eq. PT.
Por ultimo falta definir el consumo MP para mercaderia en curso, teniendo en cuenta que el ciclo de trabajo es de 5 días:
(53.204 unidades / 335 días) * 5 días) = 794 u. eq. PT.
Finalmente, para obtener el consumo total de MP para el año 1:
Consumo total MP = Consumo MP para mercadería en curso + Consumo MP año 1 = 794 u. eq. PT. + 44.346 u. eq. PT. = 45.140 u. eq. PT.
Para el año 2 - n:
Materia prima consumida para año 2 - n | |
---|---|
Volumen de producción | 44.800 u |
Consumo mp | 53.204 u |
Desperdicios no recuperables | 8.404 u |
Consumo total mp = 44.800 unidades * 1.1876 = 53.204 unidades
Desperdicios no recuperables: 53.204 unidades - 44.800 unidades = 8.404 unidades
Stock Promedio de Materia Prima y Programa de Compras
Para poder cumplir con el plan de ventas en el período de estado de régimen, se realizará una compra mensual de MP de 4626,43 u. eq. PT. y tendremos un consumo anual de 53.204 u. eq. PT.
- En el mes de febrero se consume la mitad de lo que se habitúa consumir mensualmente.
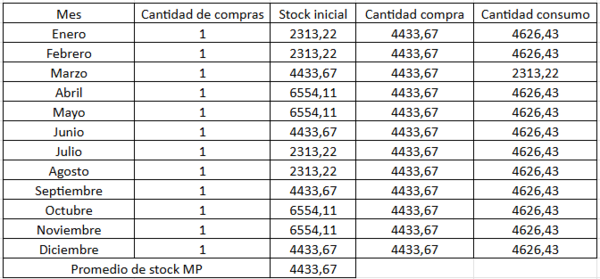
Se observa un promedio redondeado de compra mensual de MP de 4.434 u. eq. PT
Cuadro evolución de mercaderías
A continuación, se presenta el cuadro de evolución de mercaderías con toda la información calculada a lo largo de esta seccion.
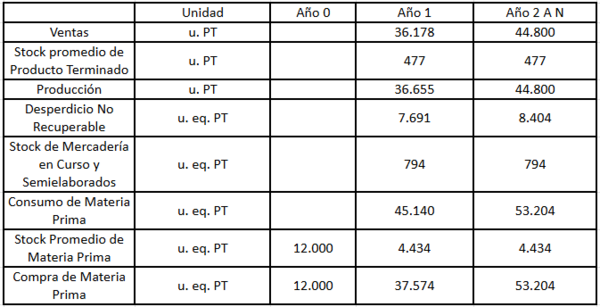
Determinacion del Personal
Organigrama de toda la empresa
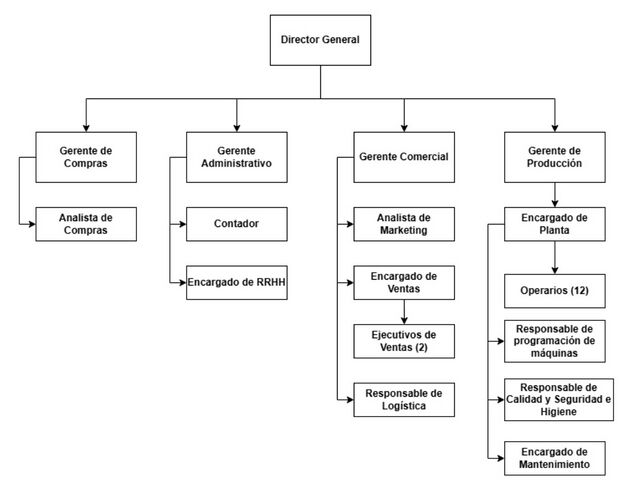
Descripción de los Puestos de Trabajo
Director general:
Es el que conduce la estrategia de la empresa, toma decisiones importantes y supervisa todas las áreas a través de los gerentes. Establece objetivos y políticas para alcanzar el éxito de la organización. Representa a la empresa antes clientes y grupos de interés.
- Ingeniero industrial, licenciado en administración de empresas con experiencia de liderazgo y conocimiento en el mercado.
Gerente de compras:
Es el que negocia con proveedores, adquiere la materia prima e insumos necesarios para llevar a cabo el proceso productivo. Se encarga de evaluar y ponderar los proveedores, para garantizar la calidad en el suministro de las materias primas.
- Ingeniero industrial, licenciado en administración de empresas, licenciado en marketing.
Analista de compras:
Asiste al gerente de compras, controla stock de las materias primas existentes para generar un requerimiento de compras en caso que sea necesario. Gestiona adquisiciones y tiempos de entrega con los proveedores.
- Puede ser un estudiante avanzado, así como licenciado en administración de empresas, licenciado en logística, ingeniero industrial.
Gerente administrativo:
Se encarga de supervisar las finanzas, contabilidad, recursos humanos, además, maneja temas legales y controla los presupuestos y balances de la empresa. Representa a la empresa frente a entidades gubernamentales como por ejemplo, para recaudación de impuestos. Planifica y coordina procedimientos, optimiza procesos.
- Ingeniero industrial, contador público, licenciado en administración de empresas.
Contador:
Lleva todos los registros contables de la empresa, realiza balances mensuales y que impuestos se deben pagar y cuales se deben cobrar. Controla presupuestos y flujos de fondos, realiza un análisis económico financiero de la empresa para evaluar la situación actual de la misma.
- Contador público, licenciado en economía, licenciado en finanzas.
Encargado de RRHH:
Planifica y administra las actividades del personal, es el encargado de reclutar y seleccionar el personal adecuado. Busca crear un ambiente de trabajo adecuado para todas las áreas.
- Licenciado en relaciones del trabajo, licenciado en recursos humanos.
Gerente comercial:
Define estrategias de ventas y marketing, lidera los equipos comerciales encargados de la programación de ventas a clientes.
- Ingeniero industrial, licenciado en marketing
Analista de Marketing:
Maneja campañas de publicidad, las redes sociales de la empresa, participa en ferias y exposiciones donde estará la empresa.
- Puede ser un estudiante avanzado, así como licenciado en marketing, licenciado en publicidad
Encargado de ventas:
Coordina a los ejecutivos de ventas. Define objetivos de ventas, realiza seguimientos de indicadores por parte de los clientes y eleva dicha información al gerente comercial.
- Ingeniero industrial, licenciado en marketing
Ejecutivo de ventas:
Tiene contacto directo con los clientes, realiza cotizaciones y presupuestos para las ventas, en caso necesario, visita a la planta/sedes de los distintos clientes.
- Puede ser un estudiante avanzado, así como licenciado en marketing, ingeniero industrial. O bien alguien con experiencia en ventas pero sin título universitario.
Responsable de logística:
Organiza tiempos y fechas de entrega, transporte y almacenamiento de producto terminado. Desarrolla planes logísticos para optimizar el flujo de la mercadería. Se encarga de ponderar y seleccionar a los proveedores de logística, realiza seguimiento de indicadores de los mismos.
- Licenciado en Transporte y logística, licenciado en administración de empresas
Gerente de producción:
Planifica, programa y controla la producción garantizando el tiempo de producción y la calidad de los procesos como de los productos. Se encarga de que se cumplan los objetivos planteados por la dirección. Identifica y realiza mejoras en los procesos productivos.
- Ingeniero industrial o mecánico
Encargado de planta:
Supervisa las operaciones en planta, coordina los turnos de trabajo, controla el flujo de trabajo, desarrolla metricas para luego ser desarrolladas y analizadas junto al gerente de producción.
- Técnico superior, ingeniero industrial, licenciado en administración de empresas
Operarios: Llevan a cabo los procesos productivos mediante manejo de máquinas u operaciones manuales. Los operarios que trabajan con las máquinas, se encargan de mantenerlas y realizarles mantenimientos diarios como limpieza, agregado de aceite (si llevan), etc.
- Título secundario completo
Responsable de calidad y seguridad e higiene:
Controla los sistemas de gestión de calidad de la planta y de la empresa, asegura el cumplimiento de normas. Garantiza la seguridad en la planta, controlando y verificando los sistemas de seguridad de la empresa, otorgando a los operarios los EPP correspondientes.
- Licenciado en seguridad e higiene, ingeniero industrial, mecánico. Técnico de normas.
Encargado de mantenimiento:
Planifica el mantenimiento preventivo de las máquinas y de las instalaciones, lleva un registro de los mantenimientos.
- Técnico de electromecánico, ingeniero industrial
Responsable de programación de máquinas:
Se encarga de cargar y verificar los programas para el torno CNC y robots de pulido. Realiza prueba y ajusta parámetros para optimizar tiempos de mecanizado y pulido.
- Técnico mecánico, electromecánica o automatización industrial
Listado de Equipos Auxiliares, Muebles y Utiles
Área | Concepto | Cantidades |
Producción | Herramientas | 12 |
Carteles de señalización | 10 | |
Ventiladores | 3 | |
Teléfonos | 2 | |
Matafuegos ABC | 4 | |
Luces de emergencia | 4 | |
Dispenser de agua | 2 | |
Cesto de basura | 4 | |
Botiquín primeros auxilios | 2 | |
Comedor | Mesas | 8 |
Sillas | 32 | |
Microondas | 4 | |
Heladera | 1 | |
Vajilla | 2 | |
Mesada | 1 | |
Cafetera | 2 | |
Dispenser de agua | 2 | |
Matafuegos ABC | 1 | |
Aire acondicionado | 1 | |
Botiquín primeros auxilios | 1 | |
Oficina producción | Escritorio | 5 |
Articulos de libreria | 20 | |
Cafetera | 1 | |
Cesto de basura | 1 | |
Cajoneras | 4 | |
Computadoras | 5 | |
Teléfonos | 5 | |
Impresora | 1 | |
Mesa | 2 | |
Sillas ergonómicas | 5 | |
SAP | 5 | |
Aire acondicionado | 1 | |
Pizarras | 1 | |
Botiquín primeros auxilios | 1 | |
Oficina Administración, comercial y compras | Escritorio | 11 |
Articulos de libreria | 44 | |
Cafetera | 2 | |
Cesto de basura | 4 | |
Cajoneras | 8 | |
Computadoras | 11 | |
Teléfonos | 10 | |
Impresora | 2 | |
Mesa | 3 | |
Sillas ergonómicas | 11 | |
SAP | 11 | |
Pizarras | 1 | |
Botiquín primeros auxilios | 2 | |
Aire acondicionado | 2 | |
Gerencia | Computadoras | 1 |
Impresora | 1 | |
Escritorio | 1 | |
Sillas ergonómicas | 2 | |
Aire acondicionado | 1 | |
Teléfonos | 1 | |
Baños | Cesto de basura | 4 |
Inodoros con mochila | 16 | |
Lavamanos | 10 | |
Lockers | 15 | |
Espejos | 10 | |
Duchas | 4 | |
Mingitorios | 3 |
Anteproyecto de Planta
Plano de planta mostrando la distribucion de las distintas areas
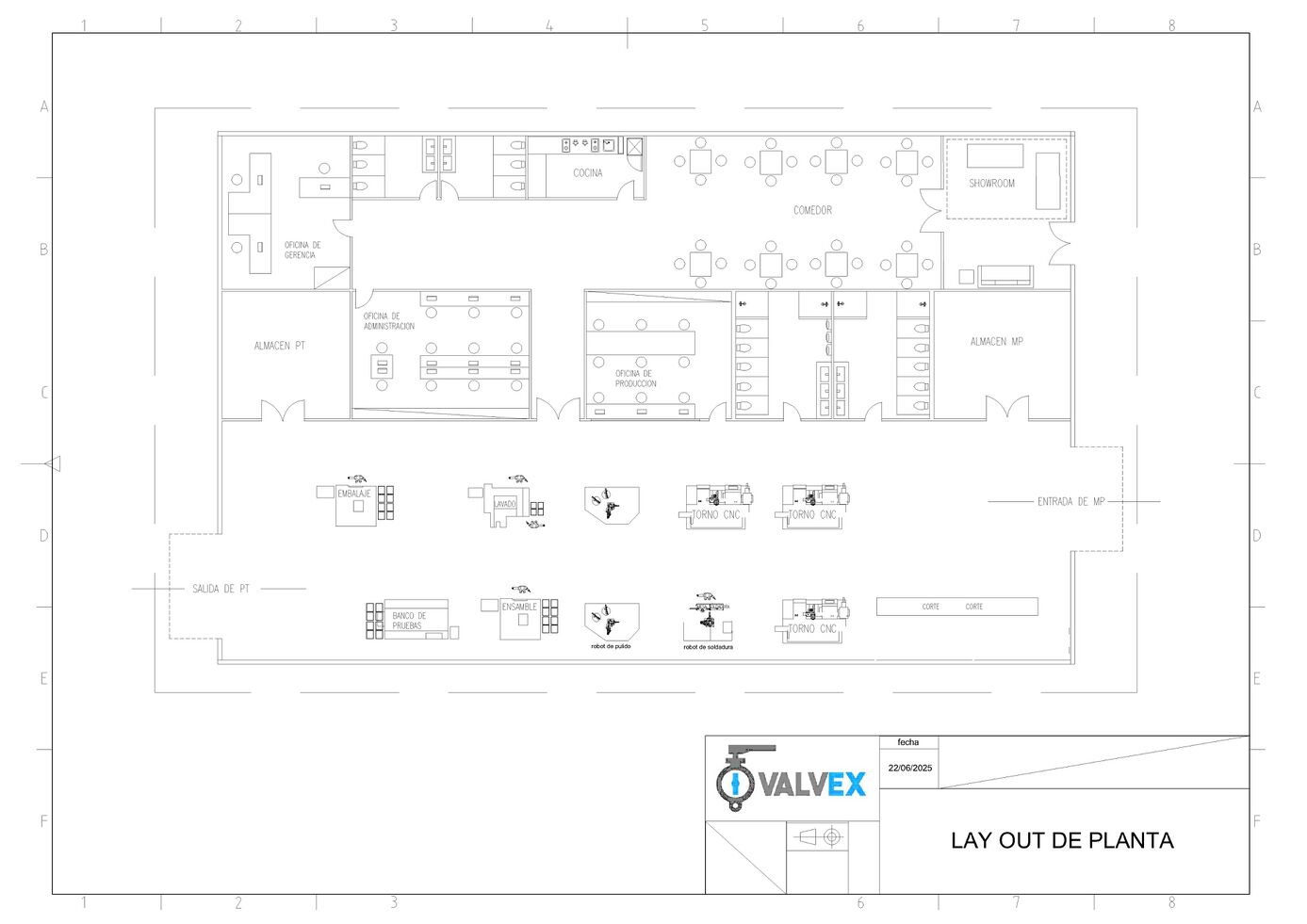
Plano mostrando el recorrido de los materiales
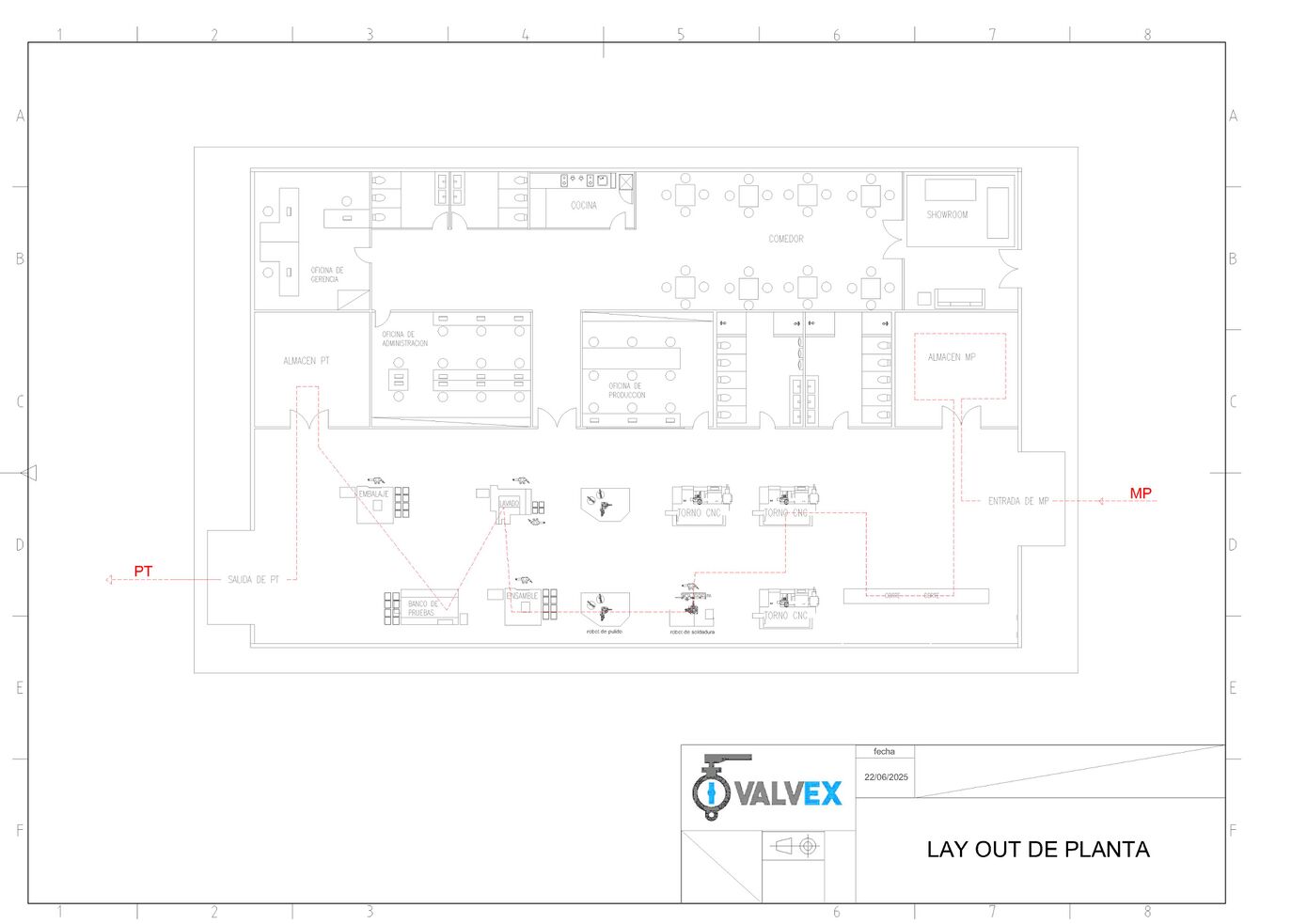
Cronograma de ejecución
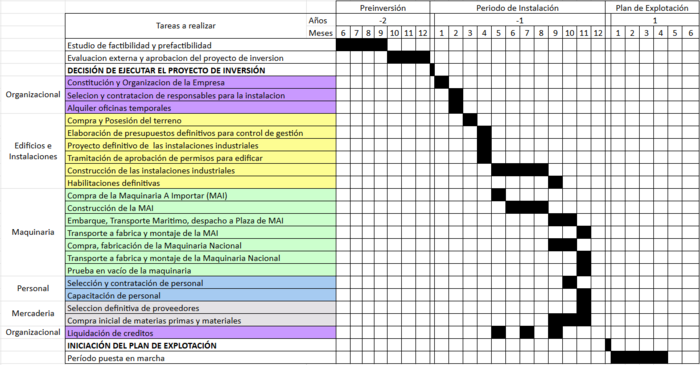