Diferencia entre revisiones de «2020/Grupo3/DimensionamientoFisico»
(No se muestran 30 ediciones intermedias de 4 usuarios) | |||
Línea 1: | Línea 1: | ||
== Determinación de la localización == | == Determinación de la localización == | ||
Para el siguiente análisis ponderamos principalmente los factores de cercanía con los clientes y los proveedores, además de que consideramos imprescindible la posibilidad de tener un terreno amplio y energía eléctrica.[[Archivo: | Para el siguiente análisis ponderamos principalmente los factores de cercanía con los clientes y los proveedores, además de que consideramos imprescindible la posibilidad de tener un terreno amplio y energía eléctrica. | ||
[[Archivo:Mdloc.png|centro|sinmarco|718x718px]] | |||
Como se puede observar en la matriz se concluye que la mejor locación para los factores que nosotros consideramos es GBA Sur(Alte Brown). | |||
== Definición técnica del producto == | == Definición técnica del producto == | ||
Línea 51: | Línea 54: | ||
|3 | |3 | ||
|mts | |mts | ||
| | |40 | ||
|- | |- | ||
|6 | |6 | ||
Línea 242: | Línea 245: | ||
* Potencia: 1,25 kW | * Potencia: 1,25 kW | ||
* Capacidad: 3.200 metros/hora | * Capacidad: 3.200 metros/hora | ||
[[Archivo:Cortadora tubos.png|no|miniaturadeimagen|Cortadora Sica TRK/SY 10-125a]] | [[Archivo:Cortadora tubos.png|no|miniaturadeimagen|Cortadora Sica TRK/SY 10-125a]]'''Selladora de bolsas''' | ||
* Marca y modelo: OM PFS400 | |||
* Potencia: 800W | |||
* Tiempo de sellado: 0,2 a 2 segundos | |||
[[Archivo:Selladora_bolsas.png|alt=|no|miniaturadeimagen|291x291px|Selladora de bolsas OM PFS400]] | |||
==== Equipos auxiliares ==== | ==== Equipos auxiliares ==== | ||
Línea 391: | Línea 398: | ||
Nuestro sistema eléctrico cuenta con un interruptor automático termomagnético y un protector de sobretensión en el tablero principal. Este tablero deriva al tablero general que contiene todos los sectores de la planta con un diferencial por sector. Luego, cada sector en sí contiene en el puesto un acceso al corte de electricidad en el puesto con un diferencial. El único tablero distinto a los demás sectores es el de extrusión que contiene un contactor para cada motos trifásico junto con un interruptor y diferencial también para cada extrusora. | Nuestro sistema eléctrico cuenta con un interruptor automático termomagnético y un protector de sobretensión en el tablero principal. Este tablero deriva al tablero general que contiene todos los sectores de la planta con un diferencial por sector. Luego, cada sector en sí contiene en el puesto un acceso al corte de electricidad en el puesto con un diferencial. El único tablero distinto a los demás sectores es el de extrusión que contiene un contactor para cada motos trifásico junto con un interruptor y diferencial también para cada extrusora. | ||
=== | === Capacidades operativas === | ||
==== | ==== BALANCE ANUAL DE MATERIAL. PRODUCCIÓN SECCIONAL ==== | ||
[[Archivo: | [[Archivo:Secciones operativas.png|sinmarco|478x478px]] | ||
Aclaración: existe merma en el cambio de calibre, pero al ser tan bajo ese peso comparado con el volumen de producción anual se lo considera despreciable. | |||
Consumo real de materia prima: | El volumen total ingresado en la primera sección operativo será de 976.922,03 kg / año. | ||
Consumo real de materia prima: 976.922 kg/año | |||
Porcentaje de desperdicio operativo: | Porcentaje de desperdicio operativo: | ||
Desperdicios totales/volumen de producción * 100 = | Desperdicios totales/volumen de producción * 100 =0 / 976.922,03 * 100 = 0% | ||
Porcentaje de desperdicio real: | Porcentaje de desperdicio real: | ||
Desperdicios no recuperables/ Volumen de producción * 100= 0 / | Desperdicios no recuperables/ Volumen de producción * 100= 0 / 976.922,03 * 100 = 0% | ||
==== | ==== RITMO DE TRABAJO ==== | ||
Horas activas por año de las maquinas operativas | Horas activas por año de las maquinas operativas | ||
[[Archivo:Punto 2 grupo 3.png|no|miniaturadeimagen]] | [[Archivo:Punto 2 grupo 3.png|no|miniaturadeimagen]] | ||
Línea 415: | Línea 423: | ||
[[Archivo:Punto 2 grupo 3 parte b.png|no|miniaturadeimagen]] | [[Archivo:Punto 2 grupo 3 parte b.png|no|miniaturadeimagen]] | ||
==== | ==== CAPACIDAD REAL ANUAL DE LA MAQUINARIA TIPO POR CADA SECCIÓN OPERATIVA ==== | ||
[[Archivo: | [[Archivo:Jkdfvndjkf.png|sinmarco|601x601px]] | ||
Aclaración: El peso unitario por bolsa es de 208gr. | |||
[[Archivo:Jkbnv.png|sinmarco|593x593px]] | |||
[[Archivo: | |||
==== | ==== DETERMINACIÓN DE LA CANTIDAD DE MÁQUINAS OPERATIVAS POR SECCIÓN. CAPACIDAD REAL ANUAL DE CADA SECCIÓN Y SU APROVECHAMIENTO EN RELACIÓN AL PROGRAMA DE PRODUCCIÓN ==== | ||
[[Archivo:Capacidad123.png|sinmarco|964x964px]] | |||
[[Archivo:Capacidad321.png|sinmarco|963x963px]] | |||
Teniendo en cuenta que debemos cambiar las boquillas para los distintos diámetros de tubo, que la extrusora es la base del proceso, es ésta la que tiene una mayor cantidad de horas de paro y por lo tanto tiene un coeficiente operativo menor. | |||
==== INDICAR EL "CUELLO DE BOTELLA" Y LA CAPACIDAD REAL ANUAL DEL EQUIPO ==== | |||
El cuello de botella será la sección de enfriamiento por ser la de mayor aprovechamiento seccional. | El cuello de botella será la sección de enfriamiento por ser la de mayor aprovechamiento seccional. | ||
{| class="wikitable" | {| class="wikitable" | ||
Línea 431: | Línea 445: | ||
|- | |- | ||
|CAPACIDAD MÁXIMA: | |CAPACIDAD MÁXIMA: | ||
| | |1.076.099 | ||
|kg/año | |kg/año | ||
|- | |- | ||
| | | | ||
|1. | |1.792.304 | ||
| | |tubos/año | ||
|- | |||
| | |||
|89.615 | |||
|bolsas/año | |||
|} | |} | ||
La capacidad real anual estará determinada por la cantidad de producción en la última sección cuando el cuello de botella funciona al 100%. Su valor será de 1. | La capacidad real anual estará determinada por la cantidad de producción en la última sección cuando el cuello de botella funciona al 100%. Su valor será de 1.792.304 tubos por año, es decir, 89.615 tubos embolsados por año. | ||
== Determinación de la evolución de las mercaderías == | == Determinación de la evolución de las mercaderías == | ||
Línea 446: | Línea 464: | ||
=== Tamaños y frecuencias de compras === | === Tamaños y frecuencias de compras === | ||
Recibiremos 20.000 kg de materia prima por semana para poder abastecer nuestra producción de 80.000 kg por mes. Tendremos un stock de seguridad de 20.000 kg de materia prima para evitar cualquier atraso que pueda surgir con la entrega de los insumos de parte del proveedor. Vale aclarar que este material es apto para ser almacenado en la intemperie. | Recibiremos 20.000 kg de materia prima + 353kg de bolsas de PEAD por semana para poder abastecer nuestra producción de 80.000 kg de tubos por mes. Tendremos un stock de seguridad de 20.000 kg de materia prima + 353kg de bolsas para evitar cualquier atraso que pueda surgir con la entrega de los insumos de parte del proveedor. Vale aclarar que este material es apto para ser almacenado en la intemperie. | ||
Dentro de los 20.000 kg que nos entregarán, 16.000 kg serán de Polipropileno (PPR T3) , 3.800 kg de PPB, 0,5 kg de Masterbatch Naranja, 199,5 kg de Masterbatch Verde. | Dentro de los 20.000 kg que nos entregarán, 16.000 kg serán de Polipropileno (PPR T3) , 3.800 kg de PPB, 0,5 kg de Masterbatch Naranja, 199,5 kg de Masterbatch Verde. | ||
=== | ==== EVOLUCIÓN DE LA MERCADERÍA ==== | ||
[[Archivo:2020-09-24 at 12.24.42.jpg|sinmarco|433x433px]] | |||
[[Archivo:2020-09-24 at 12.26.38.jpg|sinmarco|447x447px]] | |||
==== | ==== STOCK PROMEDIO DE PRODUCTO ELABORADO ==== | ||
[[Archivo: | [[Archivo:2020-09-24 at 12.28.19.jpg|sinmarco|462x462px]] | ||
[[Archivo: | ==== EVOLUCIÓN DE VENTAS DURANTE LA VIDA ÚTIL DEL PROCESO ==== | ||
[[Archivo:WhatsApp Image 2020-09-24 at 12.29.58.jpg|sinmarco|613x613px]] | |||
==== | ==== CONSUMO DE MATERIA PRIMA PARA EL PROGRAMA DE PRODUCCIÓN Y FORMACIÓN DE LA MERCADERÍA EN CURSO Y SEMIELABORADO ==== | ||
[[Archivo: | [[Archivo:2020-09-24 at 12.31.58.jpg|sinmarco|565x565px]] | ||
Para el cálculo de MC y SE tomamos como datos: un stock de seguridad de 300 tubos (lo equivalente a aproximadamente 30 min de trabajo) que serían 177 kg, 40 kilos de material que se encuentran dentro de la extrusora (incluida con su tolva) y 7,08 kg en el resto de la línea de producción (aproximadamente 48 metros), donde ya se encuentra formado el tubo. | |||
==== | ==== STOCK PROMEDIO DE MATERIA PRIMA Y EL PROGRAMA DE COMPRAS ==== | ||
[[Archivo: | [[Archivo:2020-09-24 at 12.36.24.jpg|sinmarco|510x510px]] | ||
La compra de materia prima se realizará una vez por semana y será traída en camiones. Cada camión tiene capacidad de 25.000kg de carga. Una vez entrado en régimen pediremos 20.000kg por semana y se tendrá un stock de materia prima también de 20.000kg. | |||
==== | ==== CUADRO RESUMEN DEL PROGRAMA GENERAL DE EVOLUCIÓN ==== | ||
[[Archivo: | [[Archivo:2020-09-24 at 12.40.24.jpg|sinmarco|559x559px]] | ||
== Determinación del personal == | == Determinación del personal == | ||
=== Organigrama de la empresa === | === Organigrama de la empresa === | ||
[[Archivo:Organigrama | [[Archivo:Organigrama Trump.png|miniaturadeimagen|1245x1245px|Organigrama de la empresa.]] | ||
=== Descripción de los Puestos de Trabajo === | === Descripción de los Puestos de Trabajo === | ||
Línea 485: | Línea 505: | ||
* <u>Jefe de Diseño</u>: tareas de ingeniería. Adapta el diseño de los procesos a las necesidades de la organización. | * <u>Jefe de Diseño</u>: tareas de ingeniería. Adapta el diseño de los procesos a las necesidades de la organización. | ||
* <u>Jefe de Producción:</u> tareas administrativas, de ingeniería, liderazgo y mantenimiento. | * <u>Jefe de Producción:</u> tareas administrativas, de ingeniería, liderazgo y mantenimiento. | ||
* <u>Jefe de Logística:</u> tareas de staff respecto de sus subordinados. Adecuar la implementación del programa de logística tanto de traslados como de recepción y despacho a los objetivos de la organización, indicados por el gerente comercial. | * <u>Jefe de Logística:</u> tareas de staff respecto de sus subordinados. Adecuar la implementación del programa de logística tanto de traslados como de recepción y despacho a los objetivos de la organización, indicados por el gerente comercial. | ||
* <u>Administrativos:</u> Tareas administrativas. Encargados de la documentación necesaria y de brindar apoyo al sector. | * <u>Administrativos:</u> Tareas administrativas. Encargados de la documentación necesaria y de brindar apoyo al sector. | ||
* <u>Jefe de Compras:</u> Encargado de las decisiones de insumos a comprar. Realiza los pedidos enfocándose en las necesidades de la organización. | * <u>Jefe de Compras:</u> Encargado de las decisiones de insumos a comprar. Realiza los pedidos enfocándose en las necesidades de la organización. | ||
* <u>Operarios de extrusión, embalaje y armado</u>: operan las máquinas, se encargan de su puesto. Trabajan en equipo coordinados por el gerente de producción. | * <u>Operarios de extrusión, embalaje y armado</u>: operan las máquinas, se encargan de su puesto. Trabajan en equipo coordinados por el gerente de producción. | ||
* <u>Personal de mantenimiento</u>: realizan el mantenimiento y control de las máquinas, en su respectivo período y tomando todas las precauciones necesarias. | * <u>Personal de mantenimiento</u>: realizan el mantenimiento y control de las máquinas, en su respectivo período y tomando todas las precauciones necesarias. | ||
* <u>Encargados del picking, despacho y control de los almacenes</u>: tareas de control y de manejo de materiales. Realizan el chequeo y el movimiento de las materias primas y producto terminado en recepción y almacenes. Gestión de inventarios, control de stock. | * <u>Encargados del picking, despacho y control de los almacenes</u>: tareas de control y de manejo de materiales. Realizan el chequeo y el movimiento de las materias primas y producto terminado en recepción y almacenes. Gestión de inventarios, control de stock. | ||
Línea 504: | Línea 520: | ||
* <u>Jefe de Diseño</u>: deberá ser graduado de ingeniería industrial, ingeniería mecánica o tener una tecnicatura en diseño industrial. Deberá conocer profundamente los objetivos y capacidades de la empresa, para adaptar el diseño de procesos a los objetivos de negocio de la empresa. | * <u>Jefe de Diseño</u>: deberá ser graduado de ingeniería industrial, ingeniería mecánica o tener una tecnicatura en diseño industrial. Deberá conocer profundamente los objetivos y capacidades de la empresa, para adaptar el diseño de procesos a los objetivos de negocio de la empresa. | ||
* <u>Jefe de Producción:</u> deberá ser graduado de ingeniería industrial, ingeniería mecánica, tener una tecnicatura en producción industrial, ser licenciado en economía o tener un título secundario de algún colegio técnico industrial y no menos a 3 años de experiencia. Debe tener un conocimiento de todas las máquinas y procesos así como también de sus respectivos mantenimientos (extrusión, embalaje y armado). | * <u>Jefe de Producción:</u> deberá ser graduado de ingeniería industrial, ingeniería mecánica, tener una tecnicatura en producción industrial, ser licenciado en economía o tener un título secundario de algún colegio técnico industrial y no menos a 3 años de experiencia. Debe tener un conocimiento de todas las máquinas y procesos así como también de sus respectivos mantenimientos (extrusión, embalaje y armado). | ||
* <u>Jefe de Logística:</u> debe ser ingeniero industrial o tener una tecnicatura en logística, con no menos de 3 años de experiencia en el sector. | * <u>Jefe de Logística:</u> debe ser ingeniero industrial o tener una tecnicatura en logística, con no menos de 3 años de experiencia en el sector. | ||
* <u>Administrativos:</u> deben tener título secundario completo y experiencia en el sector. De no tener experiencia, debe pasar por el programa de capacitación. | * <u>Administrativos:</u> deben tener título secundario completo y experiencia en el sector. De no tener experiencia, debe pasar por el programa de capacitación. | ||
* <u>Jefe de Compras:</u> debe ser graduado de licenciatura en economía, licenciatura en marketing o tener título de secundaria especializado en economía. | * <u>Jefe de Compras:</u> debe ser graduado de licenciatura en economía, licenciatura en marketing o tener título de secundaria especializado en economía. | ||
* <u>Operarios de extrusión, embalaje y armado</u> deberán disponer de título secundario y tener las competencias necesarias para realizar las tareas de su puesto, el manejo de las máquinas, su respectivo mantenimiento, etcétera. Para esto, en caso de no tener experiencia previa, deberán pasar por el Programa de Capacitación. Además, es preferible que residan cerca de la fábrica. | * <u>Operarios de extrusión, embalaje y armado</u> deberán disponer de título secundario y tener las competencias necesarias para realizar las tareas de su puesto, el manejo de las máquinas, su respectivo mantenimiento, etcétera. Para esto, en caso de no tener experiencia previa, deberán pasar por el Programa de Capacitación. Además, es preferible que residan cerca de la fábrica. | ||
* <u>Personal de mantenimiento</u> deberán tener título secundario completo y tener el conocimiento de las máquinas a las cuales se les asigne su respectivo mantenimiento. | * <u>Personal de mantenimiento</u> deberán tener título secundario completo y tener el conocimiento de las máquinas a las cuales se les asigne su respectivo mantenimiento. | ||
Línea 516: | Línea 529: | ||
=== '''Programa de Capacitación''' === | === '''Programa de Capacitación''' === | ||
Los operadores requerirán de una serie de capacitaciones para poder desenvolverse sin inconvenientes en su puesto de trabajo. | Los operadores requerirán de una serie de capacitaciones para poder desenvolverse sin inconvenientes en su puesto de trabajo. Consideramos importante que los ingresantes se capaciten sobre la norma ISO 9001:15, con el objetivo de que tengan un conocimiento básico de los conceptos de calidad. Los mandos medios tomarán cursos enfocados en la planificación de los recursos, en inteligencia emocional, en la Eficiencia Global de los Equipos de Producción y en los Males de producción, además de también tener conocimientos básicos de control estadísticos de procesos; harán todos estos cursos para mejorar continuamente tanto los procesos como las competencias de cada operario. Además, todo el personal de la planta deberá tomar un curso básico de Seguridad e Higiene, para conocer el uso de extintores, manejo de manuales de cargas y el uso de los respectivos elementos de protección personal (EPP). Tanto el personal de mantenimiento como los operarios que se encarguen de una parte del mantenimiento, deberán tomar un curso para conocer el proceso y lograr mejorarlo continuamente. El objetivo principal de todos los cursos de capacitación es tanto la adquisición de los conocimientos necesarios, como también mejorar las competencias de todo el personal, generando conciencia emocional y compromiso por parte de los trabajadores para con la empresa. | ||
== '''Listado de Equipos Auxiliares, Muebles y Útiles.''' == | == '''Listado de Equipos Auxiliares, Muebles y Útiles.''' == | ||
Línea 593: | Línea 606: | ||
== Cronograma de ejecución == | == Cronograma de ejecución == | ||
[[Archivo: | [[Archivo:CalendarioInv.png|alt=|centro|sinmarco|567x567px]] |
Revisión actual - 23:11 12 oct 2020
Determinación de la localización
Para el siguiente análisis ponderamos principalmente los factores de cercanía con los clientes y los proveedores, además de que consideramos imprescindible la posibilidad de tener un terreno amplio y energía eléctrica.
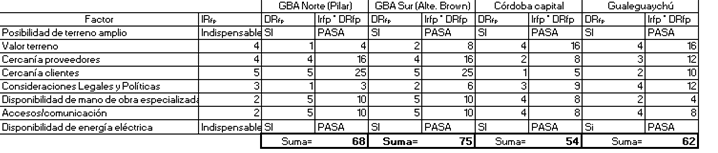
Como se puede observar en la matriz se concluye que la mejor locación para los factores que nosotros consideramos es GBA Sur(Alte Brown).
Definición técnica del producto
Plano
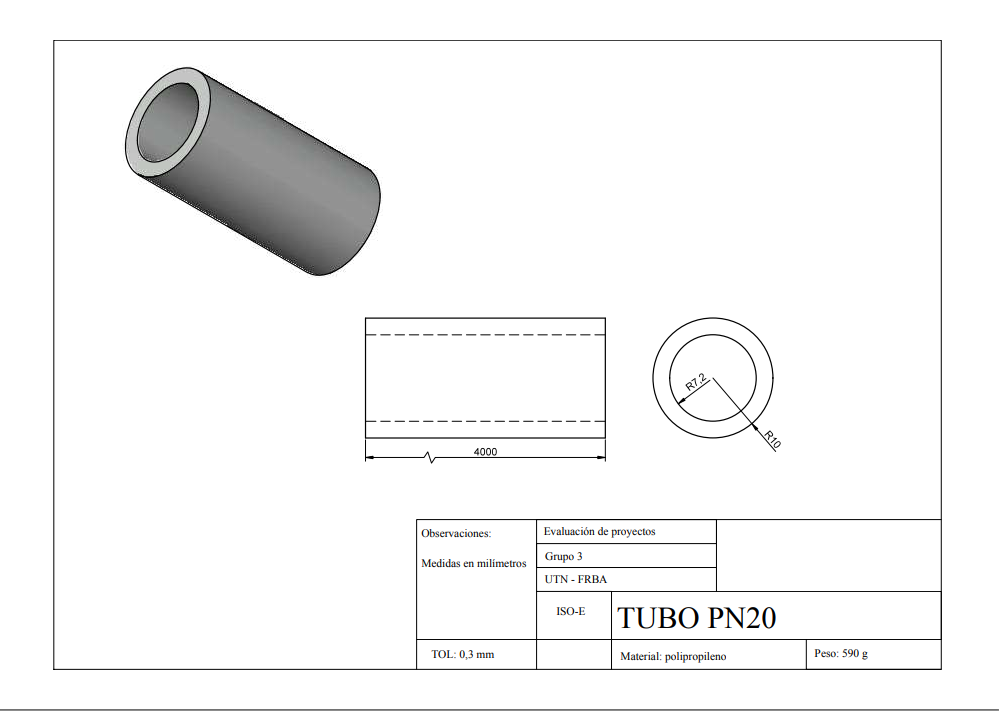
BOM
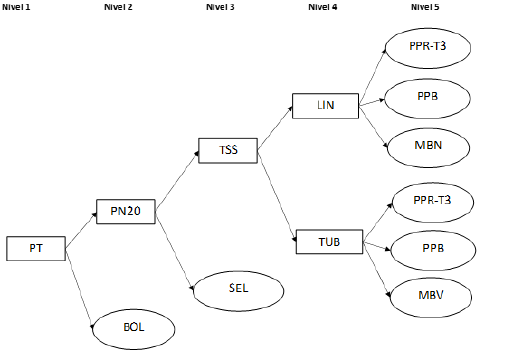
Ítem | Código | Descripción | Nivel | Unidad de medida | Cantidad |
1 | PT | 20 Tubos PN20 x 20mm embolsados | 1 | u | 1 |
2 | BOL | __Bolsa | 2 | gr | 208 |
3 | PN20 | __Tubo PN20 x 20mm | 2 | u | 20 |
4 | TSS | ____Tubo sin sellar | 3 | u | 20 |
5 | SEL | ____Sello/Cinta de marcación | 3 | mts | 40 |
6 | TUB | ______Tubo verde | 4 | u | 20 |
7 | LIN | ______Línea naranja | 4 | u | 20 |
8 | PPR-T3 | ________Polipropileno Random Tipo 3 | 5 | gr | 9.440 |
9 | PPB | ________Polipropileno Bloque | 5 | gr | 2.242 |
10 | MBv | ________Masterbatch verde | 5 | gr | 117,7 |
11 | MBn | ________Masterbatch naranja | 5 | gr | 0,3 |
Especificaciones técnicas
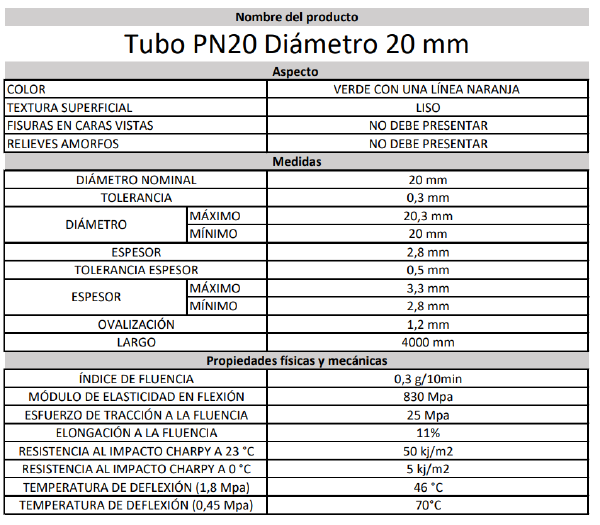
Normas aplicables
La fabricación de tubos por unión de termofusión debe ajustarse a las siguientes normas:
IRAM 13.470: "1.1. Esta norma establece las medidas y las presiones nominales de los tubos de polipropileno homopolímero (PP-H), copolímero “block” (PP-B) o “random” (PP-R), para unión por interfusión, que se destinan a la conducción de líquidos bajo presión, en general, y de agua potable, en particular."
IRAM 13.471: "1. Establecer los requisitos que deben cumplir los tubos fabricados con polipropileno homopolímero, copolímero “block” y copolímero “random”; para unión por interfusión, destinados al transporte de agua potable o no, bajo presión. Se incluye un anexo normativo para evaluar el material del tubo, un anexo con un método alternativo para determinar la resistencia al impacto, y otro con las condiciones de inspección y recepción."
Plan de ensayos
Resistencia al impacto
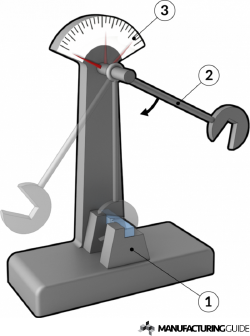
Para los tubos de hay dos ensayos de resistencia mecánica que son muy recurrentes, en primer lugar está el ensayo Charpy y en segundo lugar el ensayo Izod. Ambos miden la tenacidad o resiliencia del material pero para nuestro producto optamos solamente por realizar un ensayo Charpy.
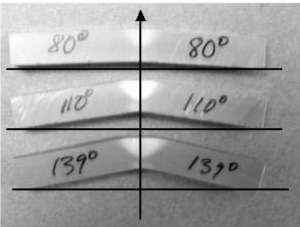
Para este ensayo contamos con el aparato estandarizado de la figura. Colocamos la probeta de prueba en unas morsas y luego se procede a destrabar la guillotina. El dinamómetro va a quedar trabado en la fuerza máxima experimentada.
La energía de rotura se puede calcular como:
Ea = MgL[cos(β) − cos(α)]
Donde M es la masa de la guillotina, g representa la fuerza de la gravedad, L la longitud del péndulo y Alpha y beta los ángulos inicial y final, después de la rotura, respectivamente.
En nuestro caso, el ensayo Charpy se produce con dos temperaturas distintas, debido que para los polímeros la temperatura influye de forma sensible en su resistencia mecánica. Las bajas temperaturas los fragilizan y altas temperaturas provocan la despolimerización del plástico.
En la medida que se aumenta la velocidad de la guillotina, la probeta empieza a ceder. El fin del ensayo es procurar con la mayor precisión cuál fue la fuerza que provocó la rotura.
Ensayo deflexión térmica
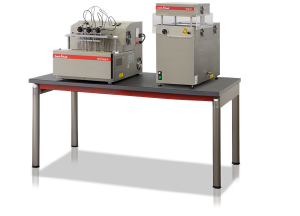
El ensayo para calcular la deflexión térmica se llama ISO HDT (Heat Deflection Temperature) y consiste en provocar una flexión a una probeta estandarizada de material con un aumento gradual de la temperatura.

Todas las condiciones del ensayo están normalizada, dentro de las cuales están las presiones posibles para el ensayo, que son de 0,45 MPa o de 1.8 MPa. Luego , la temperatura a la cual se nota una deflexión de 0.25mm es la HDT.
La velocidad de elevación de la temperatura es de aproximadamente 2 °C por minuto, es decir, la suba no es súbita.
Para nuestro caso la HDT a 0.45 MPa es 70°C y la HDT 1.8MPa es 46°C.
Ensayo de tracción
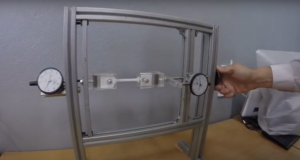
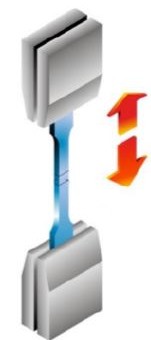
Este es el ensayo mecánico fundamental debido a todo lo que nos brinda. Para realizarlo partimos de una probeta estandarizada del material. Luego, procedemos a asegurarnos de que está bien montado al aparato, el hecho de que los ejes axiales no coincidan podría provocar el aparecimiento de fuerzas axiales.
Luego, tenemos que proceder a cargar lentamente al material de esfuerzos de tracción.
Los ensayos de tracción se utilizan para determinar el módulo de elasticidad, límite elástico, alargamiento, límite proporcional, reducción de la superficie, resistencia a la tracción, límite de elasticidad, límite elástico a la tracción y otras propiedades.
Así para nuestro caso obtenemos un índice de fluencia de 0,3g/10min. Un módulo de elasticidad en flexión de 830 MPa. Un esfuerzo de tracción a la fluencia de 25 MPa y una elongación de 11%.
Acondicionamiento del producto
El tubo será marcado según lo exigido por la Norma IRAM 13.470, la cual consta de la siguiente leyenda: " PN 20-PPR Tipo 3 SERIE S3.2 20mm x 2.8mm" SEGÚN NORMA IRAM 13470 AGUA FRIA Y CALIENTE INDUSTRIA ARGENTINA LOTE Nº = XXXXXX". El número de lote, no es exigido, pero lo hemos agregado, para realizar la trazabilidad correspondiente.
Como se mencionó, cada bolsa contendrá 20 tubos, y en esta tendrá una etiqueta la cual especificará su destino, número de lote y fecha.
Definición del proceso de producción
Diagrama de Flujo de Fabricación y Control. Cursogramas gráficos o analíticos.
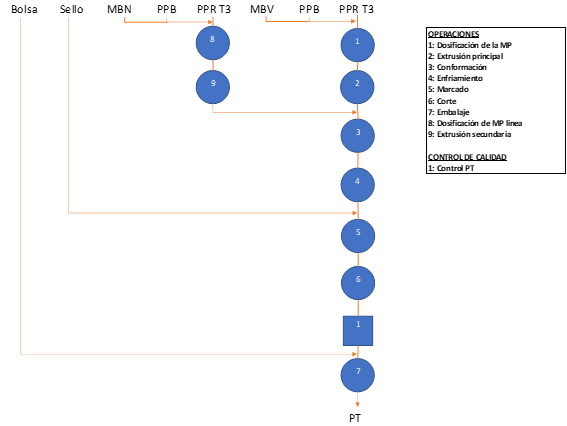
Descripción de cada etapa del proceso productivo
Dosificación de la MP
El proceso de dosificación de la materia prima consiste en preparar la carga a extruir. Esta carga consiste en polipropileno y masterbatch. Este proceso se realiza en el cargador gravimétrico cuya función consiste en corregir constantemente los desvíos que se puedan producir respecto del parámetro que queremos controlar, en este caso, la carga en la tolva. Una vez que mezclamos la materia prima en el depósito del cargador, éste la suministra en la medida que la tolva alimente a la extrusora, así siempre vamos a tener una alimentación constante de nuestra extrusora.
Extrusión principal
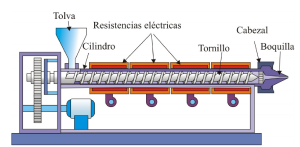
La extrusión es el proceso por el cual la materia prima sólida ingresa a un compartimiento cilíndrico en el que se haya un tornillo de arquímedes. El cilindro cuenta con un sistema de transmisión de calor y resistencias que elevan la temperatura del material sólido mientras que el tornillo genera una presurización. Esto, además de una fusión, provoca el efecto de arrastre de la materia prima sólida al inicio de la extrusora, prohibiendo así vacíos de materia prima que generen oclusiones. La zona final de la extrusora, en la que se haya el material fundido se llama zona de dosificado, a esta zona le corresponde la máxima presión.
La operación descrita anteriormente se cumple en las dos máquinas de la sección, la extrusora principal y la extrusora secundaria. Ambas forman parte de lo que se llama proceso de co-extrusión.
Dosificación de MP de línea naranja
Este proceso consiste en cargar una mezcla de masterbatch y polipropileno al cargador gravimétrico de la extrusora secundaria. Esta mezcla está destinada a conformar la línea distintiva de los tubos.
Co-extrusión/Conformación
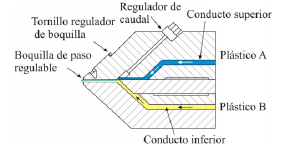
La coextrusión consiste en acoplar la línea producida en la extrusora secundaria al producto obtenido por la primaria. De esta forma queda conformado un tubo con una línea distintiva que indica sus propiedades.
Enfriamiento
Luego de salir de la extrusora el material pasa a la batea de enfriamiento que aplica una bajada de temperatura de forma tal que el plástico pueda conformar su estructura cristalina mejorando su resistencia mecánica. Un operario debe controlar la temperatura del agua adicionada, la presión dentro de la batea y el caudal de la misma. Una baja temperatura provoca el cristalizado del polímero antes de que forme su estructura. Un alto caudal en ciertas zonas provoca enfriados localizados, que pueden ser prematuros afectando la estructura, nuevamente. El operario tiene llaves de paso, termómetros y manómetros para controlar todo lo anterior. Los parámetros están prefijados. La batea mide 27 metros.
Marcado
El marcado es la escritura de los parámetros más importantes en la cara externa del tubo. Este proceso lo realiza una marcado neumática que tiene un paso para la inscripción. Se debe controlar que la cinta de marcado no presente mucha tensión y se rompa.
Corte
Una vez realizado el marcado una cuchilla debe descender cada cierto paso para obtener los tubos de manera individual. Esta cuchilla es de tipo neumática. Debe mantener tolerancias dentro de 0.3 mm que controla el operador en el puesto de control de calidad del producto terminado.
Control de calidad
Para este puesto un operario realiza primero una revisión visual del material, constituyendo esto una inspección cualitativa. Luego procede a medir algunos tubos del haz analizando que no haya desvíos, lo que constituye la inspección cuantitativa. En la inspección cualitativa se fija el color y la rugosidad. En la cuantitativa se mide el diámetro y el espesor con un calibre.
Embalaje
En este proceso un operario recibe los tubos y debe empacar el material en la misma medida de la velocidad de la línea. El embalaje se realiza mediante una máquina selladora que realiza su trabajo mediante calor, sellando el empaque actual y además sellando un lado del empaque siguiente. El operario debe acomodar el haz de tubos y descender el cabezal de la máquina para producir este proceso.
Determinación de las máquinas e instalaciones. Cálculos
Especificaciones técnicas de las máquinas (capacidades, tamaño de lotes, tiempos)
Máquinas principales
Cargador Gravimétrico
- Marca y modelo: MP Jonix
- Potencia: 2 kW
- Capacidad: 1000 kg/hora
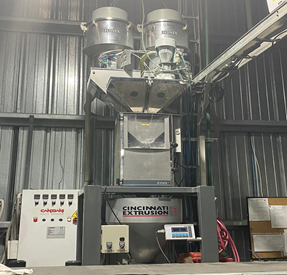
Extrusora Principal
- Marca y modelo: Cincinnati Talos 60/30G
- Potencia: 90 kW
- Dimensiones: Longitud:2.652mm Ancho:1.091mm Altura: 1.705mm
- Altura de extrusión: 1.000mm
- Peso: 2.600 kg
- Capacidad: 400 kg/h
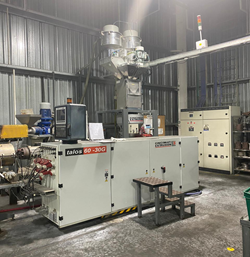
Extrusora Secundaria
- Marca y modelo: Canziani TR-25
- Potencia: 5 kW
- Capacidad: 1,5 kg/hora
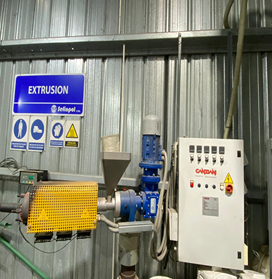
Batea de Conformación
- Marca y modelo: Cincinnati Vakon 63S/9/2-N m
- Potencia: 13,7 kW
- Dimensiones: 9 metros de largo
- Capacidad: 400 kg/hora
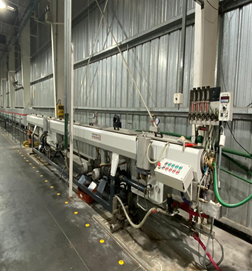
Batea de Enfriamiento
- Dimensiones: 27m de largo
- Capacidad: 270 kg/h
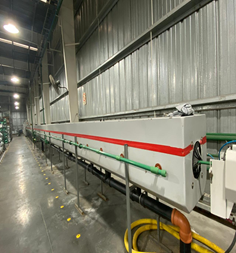
Tren de Tiro
- Marca y modelo: Sica P 125/2
- Potencia: 3,5 kW
- Capacidad: 2100 metros/hora
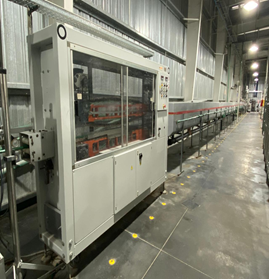
Marcadora
- Marca y modelo: Gnatta 140/SCRD/V2
- Potencia: 0,5 kW
- Capacidad: 2.000 metros/hora
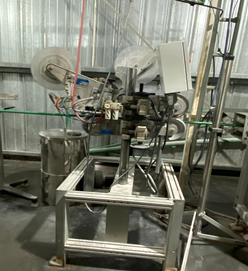
Cortadora
- Marca y modelo: Sica TRK/SY 10-125a
- Potencia: 1,25 kW
- Capacidad: 3.200 metros/hora
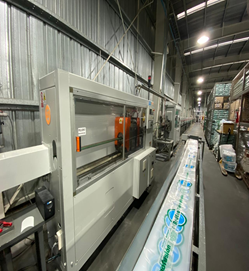
Selladora de bolsas
- Marca y modelo: OM PFS400
- Potencia: 800W
- Tiempo de sellado: 0,2 a 2 segundos
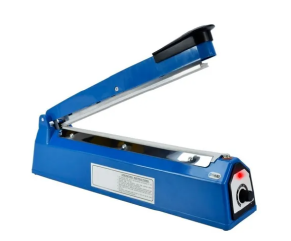
Equipos auxiliares
La batea de enfriamiento será alimentada por un circuito de enfriamiento, el cual consta de: un circuito cerrado de 40 m3, un Ablandador de agua por ósmosis inversa, una Torre de enfriamiento y 3 Bombas (1 de Impulsión, 1 de Recirculación y 1 de Back up). Mientras que los Compresores presurizan aire al Tren de tiro, la Cortadora y Cargador Gravimétrico.
Ablandadora de Agua por Ósmosis Inversa
- Marca: Inquinat
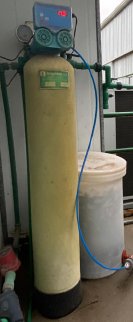
Torre de Enfriamiento
- Marca y modelo: TecnoTower 140 TR
- Potencia: 3 kW
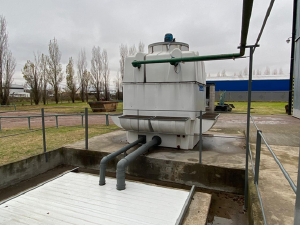
Bombas de Impulsión, Recirculación y Back Up
- Marca y modelo: Kunz 124 m3/h @ 3.6 BAR – Motor WEG
- Potencia: 20 kW
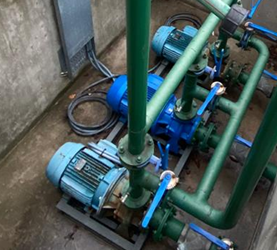
Compresor 1
- Marca y modelo: Sullair SEnergy 2200
- Potencia: 25 kW
Compresor 2
- Marca y modelo: Sullair LS-10
- Potencia: 15 kW

Consumos de energía, agua y otros servicios
Máquina | Consumo (kW) | Cant. horas por mes | Consumo mensual(kWh) |
---|---|---|---|
Cargador Gravimétrico | 2 | 320 | 640 |
Extrusora Principal | 90 | 320 | 28.800 |
Extrusora Secundaria o Coextrusora | 5 | 320 | 1.600 |
Batea de Conformación | 13,7 | 320 | 4.384 |
Tren de Tiro | 3,5 | 320 | 1.120 |
Marcadora | 0,5 | 320 | 160 |
Cortadora | 1,25 | 320 | 400 |
Torre de Enfriamiento | 3 | 320 | 960 |
Bombas de Impulsión | 20 | 320 | 6.400 |
Bombas de Recirculación | 20 | 320 | 6.400 |
Compresor 1 | 25 | 320 | 8.000 |
Compresor 2 | 15 | 320 | 4.800 |
Varios* | 40 | 320 | 12.800 |
TOTAL | 238,95 | 76.464 |
*Aclaración: "Varios" hace referencia a consumos estimados de iluminación en planta, sanitarios, cocina, comedor, oficinas. Además consideramos la aclimatización de dichos sectores.
Consumo de agua
Contaremos con un circuito cerrado de 40m3 que recirculará 3 veces por hora en la sección de enfriamiento. El agua se renovará mensualmente para evitar la formación de incrustaciones en las tuberías como también para mantener el nivel de pureza en la misma, ya que no podemos adicionarle químicos porque éstos irían a parar al tubo de polipropileno. En la cocina estimamos un consumo de 2.000 litros por mes y en los sanitarios aproximadamente 10.000 litros por mes. Estos daría un total de 52m3 de agua por mes.
Tecnología
Contaremos con un servicio de internet de una velocidad de 100Mbps para garantizar un correcto funcionamiento de las tareas administrativas y las que requieran de internet; además contrataremos un servicio de telefonía fijo para las áreas de oficina.
Mantenimiento y medio (máquinas, tareas,etc.). Descripción de los sistemas de seguridad (incendio, accidentes, etc.)
Mantenimiento y medios de control
En cuanto al mantenimiento, tenemos que mencionar que cada máquina posee un plan de mantenimiento preventivo, estructurado en un Nivel 1 (básico) que realiza regularmente el operador de la máquina y un Nivel 2 (avanzado) a cargo de la gente de Mantenimiento. El área de mantenimiento cuenta con dos oficiales de mantenimiento (un electrónico y un mecánico)
- El sistema de refrigeración es de las partes más importantes de la fábrica, por lo que el mantenimiento del mismo es de fundamental importancia. Para esto, se utilizan diariamente una válvula solenoide para comprobar el funcionamiento y un flujo de agua para corroborar si el flujo de enfriamiento es suficiente. También se dispone de un filtro de agua el cual se usa mensualmente para realizar la limpieza exterior e interior. Todas estas actividades son realizadas por los encargados de este equipo.
- El tablero eléctrico no requiere un mantenimiento diario. Se realizan actividades para verificar el funcionamiento, ajustarlo y limpiarlo con una frecuencia que ronda entre los 15 y 30 días. Se controlan tanto componentes, como la conexión, los contactos y bornes, los indicadores y su interior. De estas tareas se encarga el personal de mantenimiento.
- A los motores se le realizan controles mensualmente para verificar el consumo del mismo, limpiar la bornera y ajustar los bornes. Estas actividades son llevadas a cabo por el personal de mantenimiento.
Si hablamos del sistema de transmisión, existen variantes frecuencias dependiendo de a qué elemento le estamos realizando el mantenimiento. El aceite se controla diariamente por el responsable del equipo y se lo reemplaza semestralmente por el personal de mantenimiento, al igual que el respectivo filtro. Los comandos deben lubricarse mensualmente por el operario y el acople es realizado cada 15 días por el personal de mantenimiento para verificar el estado y sustituir la goma de ser necesario.
- Tanto el barril como los tornillos se controlan anualmente por el personal de mantenimiento.
- Al panel de comando se le verifican semanalmente los indicadores de arranque y puesta a punto, a cargo del operario.
- Al horómetro, encargado del registro de horas, se le realiza el mantenimiento semanalmente por el personal de mantenimiento.
Sistemas de Seguridad
Cuando hablamos de sistemas de seguridad, hacemos hincapié en los sistemas contra incendios. Conforme a lo exigido y al resultado del análisis de las matrices de riesgo, contamos con matafuegos distribuidos estratégicamente dentro de la planta. Si bien la carga de fuego que manejamos es importante, las probabilidades de incendio son muy bajas, debido a la reducida inflamabilidad de los productos que tratamos, sin embargo decidimos destinar parte de la inversión a este tipo de productos por dos motivos, primero para proteger a nuestro personal y maquinaria y segundo para cumplir con las normas que se exigen por ley.
Tanto para la prevención de accidentes como para el mantenimiento, los operarios tendrán que realizar la capacitación correspondiente para conocer la ubicación de los matafuegos, salidas de emergencia, equipos de mantenimiento y cómo actuar en las diferentes situaciones que puedan presentarse. También se les brindarán los elementos de protección personal (EPP) necesarios para cada operación con su correspondiente explicación de colocación y uso. Dentro de estos podemos mencionar cascos, protectores oculares y guantes.
Eléctrico
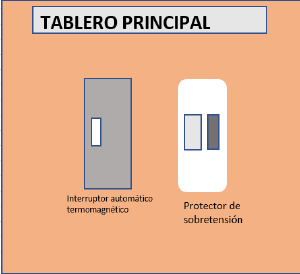
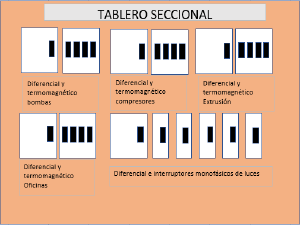
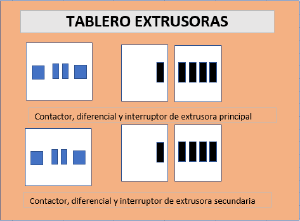
Nuestro sistema eléctrico cuenta con un interruptor automático termomagnético y un protector de sobretensión en el tablero principal. Este tablero deriva al tablero general que contiene todos los sectores de la planta con un diferencial por sector. Luego, cada sector en sí contiene en el puesto un acceso al corte de electricidad en el puesto con un diferencial. El único tablero distinto a los demás sectores es el de extrusión que contiene un contactor para cada motos trifásico junto con un interruptor y diferencial también para cada extrusora.
Capacidades operativas
BALANCE ANUAL DE MATERIAL. PRODUCCIÓN SECCIONAL
Aclaración: existe merma en el cambio de calibre, pero al ser tan bajo ese peso comparado con el volumen de producción anual se lo considera despreciable.
El volumen total ingresado en la primera sección operativo será de 976.922,03 kg / año.
Consumo real de materia prima: 976.922 kg/año
Porcentaje de desperdicio operativo:
Desperdicios totales/volumen de producción * 100 =0 / 976.922,03 * 100 = 0%
Porcentaje de desperdicio real:
Desperdicios no recuperables/ Volumen de producción * 100= 0 / 976.922,03 * 100 = 0%
RITMO DE TRABAJO
Horas activas por año de las maquinas operativas
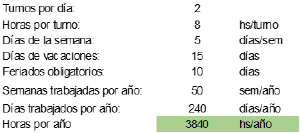
Horas por año por cada operario
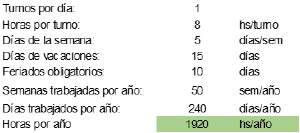
CAPACIDAD REAL ANUAL DE LA MAQUINARIA TIPO POR CADA SECCIÓN OPERATIVA
Aclaración: El peso unitario por bolsa es de 208gr.
DETERMINACIÓN DE LA CANTIDAD DE MÁQUINAS OPERATIVAS POR SECCIÓN. CAPACIDAD REAL ANUAL DE CADA SECCIÓN Y SU APROVECHAMIENTO EN RELACIÓN AL PROGRAMA DE PRODUCCIÓN
Teniendo en cuenta que debemos cambiar las boquillas para los distintos diámetros de tubo, que la extrusora es la base del proceso, es ésta la que tiene una mayor cantidad de horas de paro y por lo tanto tiene un coeficiente operativo menor.
INDICAR EL "CUELLO DE BOTELLA" Y LA CAPACIDAD REAL ANUAL DEL EQUIPO
El cuello de botella será la sección de enfriamiento por ser la de mayor aprovechamiento seccional.
CUELLO DE BOTELLA: | Enfriamiento | |
CAPACIDAD MÁXIMA: | 1.076.099 | kg/año |
1.792.304 | tubos/año | |
89.615 | bolsas/año |
La capacidad real anual estará determinada por la cantidad de producción en la última sección cuando el cuello de botella funciona al 100%. Su valor será de 1.792.304 tubos por año, es decir, 89.615 tubos embolsados por año.
Determinación de la evolución de las mercaderías
Tiempos de entrega y envío de las mercaderías
Nuestros tiempos de entrega serán de una vez por semana para no sobre-abastecernos con stock de producto terminado. Pactamos con el servicio tercerizado de logística de contar con un camión por semana que se encargará de entregar pedidos de 20.000 kg de tubos de 4 metros de longitud.
Tamaños y frecuencias de compras
Recibiremos 20.000 kg de materia prima + 353kg de bolsas de PEAD por semana para poder abastecer nuestra producción de 80.000 kg de tubos por mes. Tendremos un stock de seguridad de 20.000 kg de materia prima + 353kg de bolsas para evitar cualquier atraso que pueda surgir con la entrega de los insumos de parte del proveedor. Vale aclarar que este material es apto para ser almacenado en la intemperie.
Dentro de los 20.000 kg que nos entregarán, 16.000 kg serán de Polipropileno (PPR T3) , 3.800 kg de PPB, 0,5 kg de Masterbatch Naranja, 199,5 kg de Masterbatch Verde.
EVOLUCIÓN DE LA MERCADERÍA
STOCK PROMEDIO DE PRODUCTO ELABORADO
EVOLUCIÓN DE VENTAS DURANTE LA VIDA ÚTIL DEL PROCESO
CONSUMO DE MATERIA PRIMA PARA EL PROGRAMA DE PRODUCCIÓN Y FORMACIÓN DE LA MERCADERÍA EN CURSO Y SEMIELABORADO
Para el cálculo de MC y SE tomamos como datos: un stock de seguridad de 300 tubos (lo equivalente a aproximadamente 30 min de trabajo) que serían 177 kg, 40 kilos de material que se encuentran dentro de la extrusora (incluida con su tolva) y 7,08 kg en el resto de la línea de producción (aproximadamente 48 metros), donde ya se encuentra formado el tubo.
STOCK PROMEDIO DE MATERIA PRIMA Y EL PROGRAMA DE COMPRAS
La compra de materia prima se realizará una vez por semana y será traída en camiones. Cada camión tiene capacidad de 25.000kg de carga. Una vez entrado en régimen pediremos 20.000kg por semana y se tendrá un stock de materia prima también de 20.000kg.
CUADRO RESUMEN DEL PROGRAMA GENERAL DE EVOLUCIÓN
Determinación del personal
Organigrama de la empresa
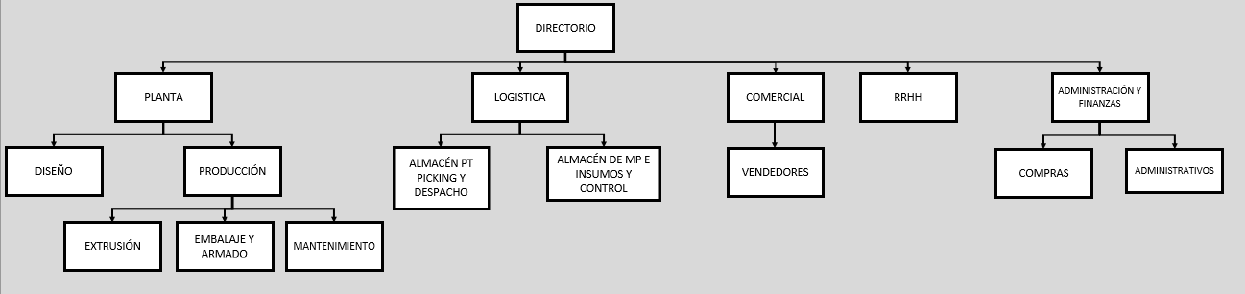
Descripción de los Puestos de Trabajo
- Directorio: encargados de las decisiones globales de la empresa.
- Gerencia de Planta: toma las decisiones más importantes del sector de planta y brinda apoyo a sus subordinados (diseño, producción).
- Gerencia Comercial: es el encargado de las decisiones más determinantes del sector comercial. Define la estrategia de ventas y procedimientos a seguir para lograr cumplir los objetivos de negocio de la empresa.
- Gerencia de Administración y Finanzas: toma de decisiones respecto a los sectores administrativo y financiero, brindando apoyo a los respectivos jefes.
- Gerencia de Recursos humanos: encargado del manejo del sector de recursos humanos. Toma las decisiones importantes (ascensos, traslados, traslados con ascenso, selección de personal).
- Jefe de Diseño: tareas de ingeniería. Adapta el diseño de los procesos a las necesidades de la organización.
- Jefe de Producción: tareas administrativas, de ingeniería, liderazgo y mantenimiento.
- Jefe de Logística: tareas de staff respecto de sus subordinados. Adecuar la implementación del programa de logística tanto de traslados como de recepción y despacho a los objetivos de la organización, indicados por el gerente comercial.
- Administrativos: Tareas administrativas. Encargados de la documentación necesaria y de brindar apoyo al sector.
- Jefe de Compras: Encargado de las decisiones de insumos a comprar. Realiza los pedidos enfocándose en las necesidades de la organización.
- Operarios de extrusión, embalaje y armado: operan las máquinas, se encargan de su puesto. Trabajan en equipo coordinados por el gerente de producción.
- Personal de mantenimiento: realizan el mantenimiento y control de las máquinas, en su respectivo período y tomando todas las precauciones necesarias.
- Encargados del picking, despacho y control de los almacenes: tareas de control y de manejo de materiales. Realizan el chequeo y el movimiento de las materias primas y producto terminado en recepción y almacenes. Gestión de inventarios, control de stock.
Formación necesaria
- Directorio: sus miembros deberán ser graduados de ingeniería industrial, administración de empresas, contabilidad, licenciatura en economía o licenciatura en administración. Deberán tener un amplio conocimiento en negocios y en liderazgo, así como también un conocimiento básico de los procesos en general.
- Gerencia de planta: su ocupante debe ser graduado de ingeniería industrial, tener experiencia no menor a 4 años y conocer cada puesto de trabajo. Debe tener conocimientos de liderazgo y capacidad de trabajar en equipo.
- Gerencia comercial: su ocupante debe ser graduado en ingeniería industrial, licenciatura en marketing, licenciatura en economía, contabilidad o licenciatura en administración. Debe tener una experiencia no menor a 4 años trabajando en el rubro y conocimiento en negociación.
- Gerencia de administración y finanzas: su ocupante debe ser graduado en ingeniería industrial, licenciatura en administración, licenciatura en economía, licenciatura en finanzas o contabilidad. Debe tener no menos de 4 años de experiencia y tener un gran conocimiento en contabilidad.
- Gerencia de recursos humanos: su ocupante deberá ser graduado de ingeniería industrial o licenciatura en recursos humanos. Deberá tener experiencia no menor a 5 años en recursos humanos. Tendrá que tener conocimientos en planificación de personal, reclutamiento, selección, inducción y en psicología. Debe tener buena capacidad de negociación y de trabajo en equipo.
- Jefe de Diseño: deberá ser graduado de ingeniería industrial, ingeniería mecánica o tener una tecnicatura en diseño industrial. Deberá conocer profundamente los objetivos y capacidades de la empresa, para adaptar el diseño de procesos a los objetivos de negocio de la empresa.
- Jefe de Producción: deberá ser graduado de ingeniería industrial, ingeniería mecánica, tener una tecnicatura en producción industrial, ser licenciado en economía o tener un título secundario de algún colegio técnico industrial y no menos a 3 años de experiencia. Debe tener un conocimiento de todas las máquinas y procesos así como también de sus respectivos mantenimientos (extrusión, embalaje y armado).
- Jefe de Logística: debe ser ingeniero industrial o tener una tecnicatura en logística, con no menos de 3 años de experiencia en el sector.
- Administrativos: deben tener título secundario completo y experiencia en el sector. De no tener experiencia, debe pasar por el programa de capacitación.
- Jefe de Compras: debe ser graduado de licenciatura en economía, licenciatura en marketing o tener título de secundaria especializado en economía.
- Operarios de extrusión, embalaje y armado deberán disponer de título secundario y tener las competencias necesarias para realizar las tareas de su puesto, el manejo de las máquinas, su respectivo mantenimiento, etcétera. Para esto, en caso de no tener experiencia previa, deberán pasar por el Programa de Capacitación. Además, es preferible que residan cerca de la fábrica.
- Personal de mantenimiento deberán tener título secundario completo y tener el conocimiento de las máquinas a las cuales se les asigne su respectivo mantenimiento.
- Administrativos de logística deben tener título secundario completo y tener experiencia en el sector no menor a 2 años, de lo contrario, deberá tomar la correspondiente capacitación.
- Encargados del picking, despacho y control de los almacenes tanto de materia prima como de producto terminado deberán tener secundario completo y pasar por el programa de capacitación.
Programa de Capacitación
Los operadores requerirán de una serie de capacitaciones para poder desenvolverse sin inconvenientes en su puesto de trabajo. Consideramos importante que los ingresantes se capaciten sobre la norma ISO 9001:15, con el objetivo de que tengan un conocimiento básico de los conceptos de calidad. Los mandos medios tomarán cursos enfocados en la planificación de los recursos, en inteligencia emocional, en la Eficiencia Global de los Equipos de Producción y en los Males de producción, además de también tener conocimientos básicos de control estadísticos de procesos; harán todos estos cursos para mejorar continuamente tanto los procesos como las competencias de cada operario. Además, todo el personal de la planta deberá tomar un curso básico de Seguridad e Higiene, para conocer el uso de extintores, manejo de manuales de cargas y el uso de los respectivos elementos de protección personal (EPP). Tanto el personal de mantenimiento como los operarios que se encarguen de una parte del mantenimiento, deberán tomar un curso para conocer el proceso y lograr mejorarlo continuamente. El objetivo principal de todos los cursos de capacitación es tanto la adquisición de los conocimientos necesarios, como también mejorar las competencias de todo el personal, generando conciencia emocional y compromiso por parte de los trabajadores para con la empresa.
Listado de Equipos Auxiliares, Muebles y Útiles.
Área de Producción
- Mesa de trabajo 5mts (1)
- Estanterías (6)
- Herramientas en general
- Carteles de seguridad
- Dispénser de agua (1)
- Cestos de basura (2)
- Matafuegos (4)
- Baldes y canastos (4)
- Pizarra para colgar hojas (1)
- Elementos de limpieza
- Ventiladores (6)
- Escalera (1)
- Elementos de Protección Personal (para 7 operarios)
- Bandeja para transportar cables eléctricos y de red
- Computadoras (1)
- Tableros eléctricos con sus componentes
- Luminaria (25)
Área de Administración
- Escritorios (6)
- Sillas (25)
- Computadoras (18)
- Zapatillas (10)
- Impresora (5)
- Dispénser de agua (2)
- Armario (1)
- Estantería (2)
- Cajones y cajas (15)
- Abrochadora (6)
- Cesto de basura (5)
- Matafuego (4)
- Teléfono (4)
- Router (5)
- Aire acondicionado (4)
- Lámparas (20)
- Hojas, tinta, lapiceras, tijeras
- Televisor (1)
Baños y Vestuarios
- Inodoro (11)
- Espejo (5)
- Pileta lavamanos con canilla (4)
- Papel higiénico
- Toalla
- Jabón
- Elementos de limpieza
- Cesto de basura (3)
- Casilleros (22)
- Iluminación (10)
Cocina comedor
- Mesa grande (3)
- Sillas (30)
- Heladera (1)
- Microondas (2)
- Cafetera (1)
- Cesto de basura (2)
- Cocina con horno (1)
- Pileta (1)
- Elementos de limpieza
- Papel de cocina
- Platos, cubiertos, vasos
- Mesada para cocina
- Matafuegos (2)
- Iluminación (10)
Anteproyecto de planta
Plano de planta
Recorrido de materiales
Cronograma de ejecución
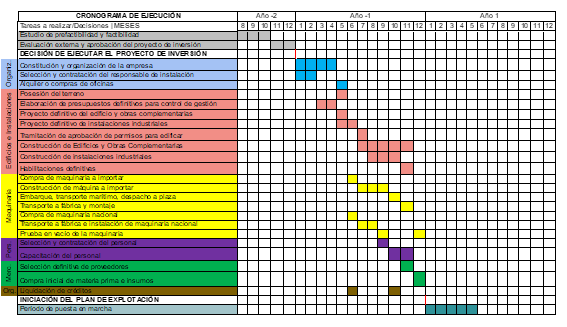