Diferencia entre revisiones de «2021/Grupo12/DimensionamientoFisico»
(No se muestran 3 ediciones intermedias de 2 usuarios) | |||
Línea 379: | Línea 379: | ||
==== Ritmo de Trabajo ==== | ==== Ritmo de Trabajo ==== | ||
Se trabajará con 1 equipo de operarios durante 5 días de la semana 1 turno diario de | Se trabajará con 1 equipo de operarios durante 5 días de la semana 1 turno diario de 4 hs. A los 365 días del año habrá que descontar los 100 dias de fin de semana de las semanas laborales, 15 días de vacaciones donde cerrará la empresa y 10 feriados obligatorios en el año. No habrá cierre por mantenimiento. | ||
<u>Hs activas/año de las máquinas operativas</u> | <u>Hs activas/año de las máquinas operativas</u> | ||
días activos/año = 365-15-10= | días activos/año = 365-100-15-10= 240 días | ||
horas activas/año = | horas activas/año = 240 días activos/año * 4hs/día = 960 hs | ||
<u>Hs/año trabajadas por cada operario</u> | <u>Hs/año trabajadas por cada operario</u> | ||
960hs / 4 operarios = 240hs | |||
==== Capacidad Real Anual de la Maquinaria Tipo de Cada Sección Operativa ==== | ==== Capacidad Real Anual de la Maquinaria Tipo de Cada Sección Operativa ==== | ||
Línea 402: | Línea 402: | ||
|- | |- | ||
|1 | |1 | ||
|170 | |170 | ||
| | |940 | ||
| | |159800 | ||
|80 | |80% | ||
| | |127840 | ||
|- | |- | ||
|2 | |2 | ||
|176 | |176 | ||
| | |940 | ||
| | |165440 | ||
|80 | |80% | ||
| | |132352 | ||
|- | |- | ||
|3 | |3 | ||
|15 | |15 | ||
| | |940 | ||
| | |14100 | ||
|75 | |75% | ||
| | |10575 | ||
|- | |- | ||
|4 | |4 | ||
|12 | |12 | ||
| | |940 | ||
| | |11280 | ||
|90 | |90% | ||
| | |10152 | ||
|- | |- | ||
|5 | |5 | ||
|36 | |36 | ||
| | |940 | ||
| | |33840 | ||
|90 | |90% | ||
| | |30456 | ||
|} | |} | ||
Línea 448: | Línea 448: | ||
|1 | |1 | ||
|4500 panes cortados | |4500 panes cortados | ||
| | |127840 | ||
|0, | |0,035 = 1 | ||
| | |127840 | ||
| | |3,52% | ||
|- | |- | ||
|2 | |2 | ||
|4500 telas cortadas | |4500 telas cortadas | ||
| | |132352 | ||
|0, | |0,034 = 1 | ||
| | |132352 | ||
| | |3,40% | ||
|- | |- | ||
|3 | |3 | ||
|4500 telas cosidas | |4500 telas cosidas | ||
| | |10575 | ||
|0, | |0,42 =1 | ||
| | |10575 | ||
| | |42,55% | ||
|- | |- | ||
|4 | |4 | ||
|4500 colchones sin embalar | |4500 colchones sin embalar | ||
| | |10152 | ||
|0, | |0,44 =1 | ||
| | |10152 | ||
| | |44,33% | ||
|- | |- | ||
|5 | |5 | ||
|4500 colchones terminados | |4500 colchones terminados | ||
| | |30456 | ||
|0, | |0,14 =1 | ||
| | |30456 | ||
| | |14,78% | ||
|} | |} | ||
==== Cuello de Botella ==== | ==== Cuello de Botella ==== | ||
El cuello de botella es la sección de mayor aprovechamiento seccional, en este caso la 4 con | El cuello de botella es la sección de mayor aprovechamiento seccional, en este caso la 4 con 44,33%. | ||
== Determinación de la evolución de mercaderías == | == Determinación de la evolución de mercaderías == | ||
Línea 620: | Línea 620: | ||
El ciclo de elaboración demanda de 1 día (desde el ingreso de la materia prima al sector operativo hasta la salida de producto terminado). | El ciclo de elaboración demanda de 1 día (desde el ingreso de la materia prima al sector operativo hasta la salida de producto terminado). | ||
Ciclos de elaboración anuales: | Ciclos de elaboración anuales: 240 días al año / 1 = '''240 ciclos de elaboración.''' | ||
<u>Consumo de materia prima</u> | <u>Consumo de materia prima</u> | ||
Línea 738: | Línea 738: | ||
|Panes 1 plaza | |Panes 1 plaza | ||
|833 panes | |833 panes | ||
| | |240 | ||
| | |3,47 p | ||
|1 | |1 | ||
| | |3,47 p | ||
|- | |- | ||
|Panes 2 plazas | |Panes 2 plazas | ||
|1418 panes | |1418 panes | ||
| | |240 | ||
| | |5,91 p | ||
|1 | |1 | ||
| | |5,91 p | ||
|- | |- | ||
|Tela 1 plaza | |Tela 1 plaza | ||
|11488,5m2 de tela | |11488,5m2 de tela | ||
| | |240 | ||
| | |47,87 m2 | ||
|1 | |1 | ||
| | |47,87 m2 | ||
|- | |- | ||
|Tela 2 plaza | |Tela 2 plaza | ||
|24777,9m2 de tela | |24777,9m2 de tela | ||
| | |240 | ||
| | |103,24 m2 | ||
|1 | |1 | ||
| | |103,24 m2 | ||
|- | |- | ||
|Vivo | |Vivo | ||
|28368 m | |28368 m | ||
| | |240 | ||
| | |118,20 m | ||
|1 | |1 | ||
| | |118,20 m | ||
|- | |- | ||
|Funda Plástica | |Funda Plástica | ||
|43503,75 m2 | |43503,75 m2 | ||
| | |240 | ||
| | |181,27 m2 | ||
|1 | |1 | ||
| | |181,27 m2 | ||
|} | |} | ||
{| class="wikitable" | {| class="wikitable" | ||
Línea 788: | Línea 788: | ||
|618,395 panes | |618,395 panes | ||
|2,45 panes | |2,45 panes | ||
|''' | |'''621,87 panes''' | ||
|- | |- | ||
|Panes 2 plazas | |Panes 2 plazas | ||
|1052,390 | |1052,390 | ||
|4,17 panes | |4,17 panes | ||
|''' | |'''1058,30 panes''' | ||
|- | |- | ||
|Tela 1 plaza | |Tela 1 plaza | ||
|1482,562 u = 10229,66 m2 | |1482,562 u = 10229,66 m2 | ||
|33,78 m2 | |33,78 m2 | ||
|''' | |'''10277,53 m2''' | ||
|- | |- | ||
|Tela 2 plaza | |Tela 2 plaza | ||
|2445,572 u = 21374,29 m2 | |2445,572 u = 21374,29 m2 | ||
|72,87 m2 | |72,87 m2 | ||
|''' | |'''21477,53 m2''' | ||
|- | |- | ||
|Vivo | |Vivo | ||
|21055,2 m ''(para cant año 1)'' | |21055,2 m ''(para cant año 1)'' | ||
|83,43 m | |83,43 m | ||
|''' | |'''21173,40 m''' | ||
|- | |- | ||
|Funda Plástica | |Funda Plástica | ||
|32289 m2 ''(para cant año 1)'' | |32289 m2 ''(para cant año 1)'' | ||
|127,95 m2 | |127,95 m2 | ||
|''' | |'''32470,27 m2''' | ||
|} | |} | ||
{| class="wikitable" | {| class="wikitable" | ||
Línea 989: | Línea 989: | ||
|u | |u | ||
| | | | ||
| | |621,87 | ||
|833 | |833 | ||
|- | |- | ||
Línea 995: | Línea 995: | ||
|u | |u | ||
| | | | ||
| | |1058,30 | ||
|1418 | |1418 | ||
|- | |- | ||
Línea 1001: | Línea 1001: | ||
|m2 | |m2 | ||
| | | | ||
| | |10277,53 | ||
|11488,5 | |11488,5 | ||
|- | |- | ||
Línea 1007: | Línea 1007: | ||
|m2 | |m2 | ||
| | | | ||
| | |21477,53 | ||
|24777,9 | |24777,9 | ||
|- | |- | ||
Línea 1013: | Línea 1013: | ||
|m | |m | ||
| | | | ||
| | |21173,40 | ||
|28368 | |28368 | ||
|- | |- | ||
Línea 1019: | Línea 1019: | ||
|m2 | |m2 | ||
| | | | ||
| | |32470,27 | ||
|43503,75 | |43503,75 | ||
|- | |- | ||
Línea 1064: | Línea 1064: | ||
|u | |u | ||
|75,57 | |75,57 | ||
| | |618,73 | ||
|833 | |833 | ||
|- | |- | ||
Línea 1070: | Línea 1070: | ||
|u | |u | ||
|128,567 | |128,567 | ||
| | |1053,033 | ||
|1418 | |1418 | ||
|- | |- | ||
Línea 1076: | Línea 1076: | ||
|m2 | |m2 | ||
|1335,71 | |1335,71 | ||
| | |9940,82 | ||
|11488,5 | |11488,5 | ||
|- | |- | ||
Línea 1082: | Línea 1082: | ||
|m2 | |m2 | ||
|2761,67 | |2761,67 | ||
| | |20870,46 | ||
|24777,9 | |24777,9 | ||
|- | |- | ||
Línea 1088: | Línea 1088: | ||
|m | |m | ||
|2572 | |2572 | ||
| | |21068,18 | ||
|28368 | |28368 | ||
|- | |- | ||
Línea 1094: | Línea 1094: | ||
|m2 | |m2 | ||
|3944,25 | |3944,25 | ||
| | |32308,95 | ||
|43503,75 | |43503,75 | ||
|} | |} | ||
Línea 1249: | Línea 1249: | ||
== Anteproyecto de Planta == | == Anteproyecto de Planta == | ||
[[Archivo:Croquis.png|alt=|centro|miniaturadeimagen|600x600px|Medidas en decímetros [dm]]] | |||
[[Archivo: | |||
[[Archivo:DIR dormipol.png|centro|miniaturadeimagen|450x450px]] | [[Archivo:DIR dormipol.png|centro|miniaturadeimagen|450x450px]] | ||
== Cronograma de ejecución == | == Cronograma de ejecución == | ||
[[Archivo:Cronograma de ejecución de Dormipol.png|miniaturadeimagen|1090x1090px]] | [[Archivo:Cronograma de ejecución de Dormipol.png|miniaturadeimagen|1090x1090px]] |
Revisión actual - 02:20 25 ago 2021
Determinación de la Localización
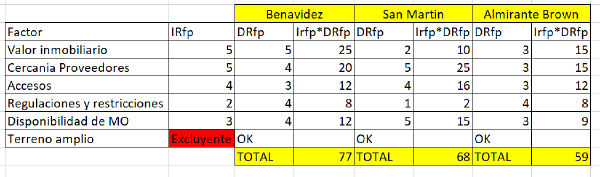
La ubicación de nuestra planta será Fray Luis Beltrán 2056. Benavidez.
Definición Técnica del Producto
Colchon de espuma de poliuretano de alta densidad 30 o 35 kg/mt3 con top pillow de 5 cm de alto en espuma viscoelastica para mayor adaptabilidad y confort. Terminado en tela de jackard o piquet, totalmente matelaseado. Muy recomendado para personas con problema cervicales y/o lumbares. Altura del colchon 27 cm. Base de sommier en madera de primera calidad, reforzada con 6 patas para sommier, parte superior en tela antideslizante (para que el colchon no se mueva) y laterales en tela igual al colchon. Altura de la base 22 cm + 12 cm de patas. 30 kg recomendado hasta 110 kg por lado. 35 kg recomendado hasta 140 kg por lado.
- Polipropilenglicol: es un plastificante cuya función principal es descomponer las cadenas de polímeros para evitar la formación de cadenas largas que convierten a la estructura en una estructura frágil. La idea del plastificante es que le dé la suavidad y maleabilidad a la espuma (Gama, Ferreria y Barros-Timmons, 2018).
- Tolueno diisocianato: tiene como función principal reaccionar con el polipropilenglicol para formar la espuma. Esta amina le da resistencia a las paredes de las células que se forman. Es importante que sean resistentes para que no colapsen con el peso del usuario del colchón, perdiendo su característica de deformarse temporalmente. La resistencia se logra agregando el insumo químico en exceso, para que se forme urea, de tal manera que se crean puentes de hidrógeno dándole mayor rigidez a la espuma (Gama et al., 2018).
- Agua: importante insumo para que ocurra la reacción y se forme dióxido de carbono. Debe contar con la medida exacta de agua, ya que, a mayor cantidad, mayor CO2 se forma, obteniendo una espuma de menor densidad. De modo contrario, a menor cantidad de agua, resulta una espuma de mayor densidad. Por lo tanto, de este insumo depende la capacidad de soportar carga, puesto que está vinculado a la densidad de la espuma obtenida (Strakowska, Czlonka y Strzelec, 2019).
- Cloruro de metileno: es un agente soplante cuya función es dar suavidad a la espuma y a la vez controlar la densidad de la misma.
- Surfactante de silicona: este agente químico le da estabilidad a la espuma para que sea un producto inerte. Además, baja la tensión superficial para facilitar la reacción del tolueno diisocianato con el agua. Por último, les da resistencia a las celdas formadas durante la reacción para evitar el colapso de la espuma durante el proceso de polimerización.
Plan de Ensayos DE CALIDAD
Para el desempeño de esta labor, Dormipol cuenta con dos máquinas con sendos rodillos de 140 kg que se deslizan de un lado al otro del colchón durante 30.000 veces.
El objetivo de esta acción es simular el estado que tendría un colchón pasados 8 años, así se conoce el desgaste, la pérdida de altura, la variación de firmeza y las posibles roturas.
Todos los colchones lanzados al mercado deben superar una prueba que consiste en dejar caer una pieza metálica de 325 cm2 de superficie de contacto y 120 kg de peso 10.000 veces. Solo así garantizaremos su calidad.
Acondicionamiento del Producto. TAREA DE EMBALAJE Y PICKING
El tipo de carga de los colchones es no perecedera ya que no se dañan a corto plazo, tambien porque a La hora de transportarlo no necesitan temperatura especificas, ni medidas de seguridad tan estrictas requiriéndose condiciones ambientales moderadas.
Procesos logisticos
- Alistamiento de la materia prima
- Producción
- Apilamiento
- Almacenamiento
- Picking
- Packing
- Distribución
- Entrega
Empaque: El colchón tiene 1 empaque primario que es será plástico: que ayuda a que el colchón no se dañe o se contamine de residuos líquidos, vapores ni sólidos.
El embalaje del colchón será stretch, para agrupar colchones o bien ajustarlos para evitar movimientos en el transporte.
Almacén y almacenamiento: deberá cumplir con las siguientes condiciones:
*un lugar seguro
*libre de bacterias y humedad
*lugar amplio
*libre de objetos punzantes etc
El almacenamiento será de forma vertical u horizontal, según deposito, se utilizarán estivas para que el colchón no tenga contacto con el piso evitando contacto con el suelo y así preservar la conformidad del producto final.
Definición del Proceso de Producción
Cursograma Sinóptico de Procesos
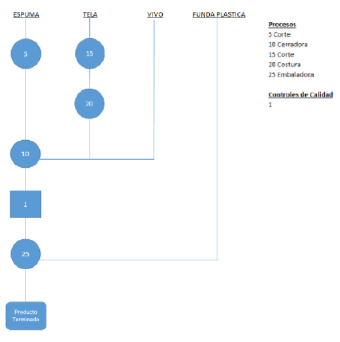
Descripción de cada etapa del proyecto productivo
Para el proceso de fabricación nos proveemos previamente de la materia prima requerida, siendo esta espuma de alta densidad (30 kg/m3), tela y el vivo.
Una vez adquiridos los insumos, tanto la espuma como el vivo son trasladados al sector de corte, mientras que la tela es previamente enviada a matelasear a otra empresa que nos provee el servicio. Una vez matelaseada, se procede a cortarla al igual que el resto de la materia prima.
En el sector de cortado, la espuma se corta a medida según se requiera un colchón de 1 plaza o de 2 plazas, con la ayuda de dos sierras, una lateral y otra horizontal. En lo que respecta a la tela, se utilizan cortadoras de tela (ya matelaseada) para obtener las medidas requeridas y trasladar el material cortado al sector de costura.
Con la tela cosida, la espuma cortada y el vivo, se procede a trasladar los 3 semielaborados al sector de ensamble, en donde participa la máquina cerradora. Es así como se localiza en la máquina la espuma cortada a medida, la tela en ambos lados encerrando el relleno, y utilizando el vivo como unificador, el equipo procede a conformar el colchón.
Al obtener los colchones ensamblados, se envían a inspeccionar para evitar devoluciones antes de ser embalados. Si el resultado del control es positivo, proceden a la máquina embaladora donde se forran con la funda plástica y quedan listos para despachar.
Determinación de Máquinas e Instalaciones
Especificaciones técnicas de las máquinas
Maquinaria por proceso:
➔ Maquina cortadora de tapas:
Se realiza cambio de cuchillas cada 1000 colchones y lubricante libre de impurezas durante el proceso de corte.
Potencia: 2 KW/W
Voltaje: 380V50Hz 220V60Hz
Velocidad: 10m/Min.
Productividad: 120 u/hora
La máquina cortadora de tapas de colchón trabaja 30 segundos por colchón.
➔ Maquina de costura recta:
Potencia: 600 W
Voltaje: Monofásico, 220V, 50Hz
Velocidad: 2500 rpm
Productividad: 30 u/hora
La máquina de costura recta trabaja 2 minutos por colchón.
➔ Máquina Cerradora:
Potencia: 3 KW
Voltaje: 220V/380V, 50/60Hz, Trifásico
Peso: 1300 kg
Tamaño: 2380 * 1830 * 1650mm
Dimensiones de la mesa: 2000 * 3950 * 900mm
Productividad: 12-18 u/hora
Durante el proceso de operación, la cinta transportadora impulsa el colchón para proceder. Cuando se termina un lado, la máquina puede girar 90 ° automáticamente para comenzar a cerrar el otro costado.
Cuando se termina de cerrar los cuatro lados de arriba, la máquina puede voltear el colchón para cerrar los otros cuatro lados de abajo.
Esta máquina requiere una sola persona para operar, lo que mejora la eficiencia del trabajo y reduce la intensidad del trabajo. Es un equipo ideal para la fabricación de colchones de alta calidad y la producción en línea de montaje.
La máquina cerradora trabaja 2.5 minutos por colchón(2 plazas). De ese tiempo, 30 segundos se usan para dar vuelta el colchón.
➔ Máquina Empacadora y Compresora Automática de colchón:
Potencia: 12 KW
Voltaje: 3AC 380V, 50/60 Hz
Peso: 5000 kg
Mantenimiento y medios de control
Mantenimiento Correctivo: el cual se aplicará a los equipos con baja y mediana criticidad, mantenimiento preventivo, el cual se aplicará a los equipos con alta criticidad, acompañado del mantenimiento productivo total (TPM).
Mantenimiento de Conservación.
Lo conforman todas aquellas actividades encaminadas a que los equipos de la empresa lleguen a cumplir su tiempo de vida útil, mediante actividades básicas como: limpieza, esta
actividad se realiza con el fin de evitar daños debido al polvo, suciedad y 27 aquellos agentes externos que afecten el buen funcionamiento del equipo; ajustes, esta actividad se realiza con el fin de sujetar y asegurar los componentes mecánicos sueltos debido al movimiento relativo entre ellos, lubricación, esta actividad se realiza con el fin de disminuir el desgaste ocasionado por el constante rozamiento al que están expuestas las diferentes partes móviles, ya sean cojinetes , chumaceras, rodamientos, engranajes, etc, es decir, son una serie de trabajos que hacen posible que el equipo regrese a su estado físico inicial, evitando su degeneración o que sea atacado por agentes nocivos.
Mantenimiento de Recuperación.
Este tipo de mantenimiento lo conforman todas las actividades destinadas a la reparación o sustitución de partes, componentes o sistemas mecánicos que se encuentran en mal
funcionamiento, producto de desgaste de los equipos, mala operación, las
cuales deberán ser reemplazadas por otras y así obtener un buen desempeño del equipo; en la Figura 25, se muestra el procedimiento para ejecutar las actividades de recuperación de los equipos.
Descripción de los sistemas de seguridad (incendios, accidentes, etc.)
La Ley 19587 de Higiene y Seguridad en el Trabajo, y sus decretos Reglamentarios 351/79 y 1338/96 determinan las condiciones de seguridad que debe cumplir cualquier actividad industrial en todo el territorio de la República Argentina.
Es importante que todos los empleados tengan presente el reglamento de seguridad y salud ocupacional, que se hagan capacitaciones constantes al personal, y que se supervise que se cumplan.
A continuación, se detallan las medidas que se tomarán en consideración:
• Iluminación adecuada según área de trabajo: zona de producción y oficinas administrativas: 750 lux, almacén de materia prima 500 lux y almacén de producto
terminado 300 lux.
• Tapones para personal en planta que está expuesto a más de 85 decibeles
durante su jornada laboral de 8 horas, establecido por la Ley n.º 29783.
• Uso de fajas lumbares para la carga de materiales pesados.
• Uso de mascarillas (respiradores) de seguridad con filtros de inhalación y
válvula de exhalación para evitar la intoxicación con los gases de la reacción.
• Señalización de uso de EPP, según área, y ruta de evacuación.
• Contar con 6 extintores, 4 en la zona de producción y almacenes, debido a que el
material es altamente inflamable, y 2 en las áreas administrativas.
Todo establecimiento debe contar con provisión y reserva de agua para uso humano y eliminar toda posible fuente de contaminación y polución de las aguas que se utilicen y mantener los niveles de calidad establecidos por la legislación vigente. Por tal motivo se deben realizar análisis al agua de consumo sea obtenida dentro de su planta o traídas de otros lugares.
Análisis físico químico una vez por año.
Análisis bacteriológico dos veces por año.
Se entiende por agua para uso humano la que se utiliza para beber, higienizarse o preparar alimentos.
Capacitación El empleador está obligado a capacitar a su personal en materia de H y S, en prevención de enfermedades profesionales y de accidentes del trabajo, de acuerdo a las características y riesgos propios, generales y específicos de las tareas que desempeña. La capacitación en materia de higiene y seguridad y medicina del trabajo debe ir orientada a todos los sectores del establecimiento en sus distintos niveles:
-Nivel superior (dirección, gerencias y jefaturas).
-Nivel intermedio (supervisores y encargados)
-Nivel operativo (trabaj. de producción y adm.)
Las capacitaciones deben ser planificadas en forma anual a través de programas de capacitación para los distintos niveles.
A su vez, se procederá a estimular y desarrollar una actitud positiva respecto de la prevención de los accidentes o enfermedades que puedan derivarse de la actividad laboral.
· Instalaciones Eléctricas Protección contra riesgos de contactos directos:
Protección por alejamiento
Protección por aislamiento Protección por medio de obstáculos
Protección contra riesgos de contactos indirectos (contacto de personas con masas puestas accidentalmente bajo tensión).
Puesta a tierra de las masas (valores de resist. Tierra <10 ohm)
· Disyuntores diferenciales: deben actuar cuando la corriente de fuga a tierra toma el valor de calibración (300 mA o 30 mA según su sensibilidad) en un tiempo no mayor de 0,03 seg.
· Aislar las masas o partes conductoras con las que el hombre pueda entrar en contacto.
· Usar tensión de seguridad.
· Proteger por doble aislamiento los equipos y máquinas
eléctricas
La matriz IPER indica el nivel de riesgo de cada actividad realizada durante el
proceso y las acciones a tomar para mitigarlos.
Cálculos 1-5
Balance Anual de Material. Producción Seccional.
Sección 1: Corte Espuma
Se alimenta con panes de espuma que vienen de 1,9m x 2m x 0,3m para colchones de una plaza y 1,9m x 2,8m x 0,3m. La materia prima se comercializa en estas medidas para evitar desperdicios.
- Para colchón de 1 plaza (1,9mx1m) con un pan se producen 2 colchones.
- Para colchón de 2 plazas (1,9mx1,4m) con un pan se producen 2 colchones.
Sección 2: Corte Tela
Se alimenta con rollos de tela que vienen de ancho 1,5m para una plaza y 1,9m para dos plazas.
- Para un colchón de 1 plaza se necesitan 5,6m2 de tela. Cortando la tela en 2 partes de 1,5mx2,3m (6,9m2). Desperdicio por colchón=18.8%
- Total 1 plaza: 4,6m x 1665 colchones = 7659m de largo. Multiplicando por 1,5m -> 11488,5m2
- Para un colchón de 2 plazas se necesitan 7,4m2 de tela. Cortando la tela en 2 partes de 1,9mx2,3m (8,74m2). Desperdicio por colchón=15.3%
- Total 2 plazas: 4,6m x 2835 colchones = 13041m de largo. Multiplicando por 1,9m -> 24777,9m2
Sección 3: Cosido de tela
Sección 4: Cerrado de colchón
Para el colchón de 1 plaza necesitamos 5,8m de vivo y para uno de 2 plazas 6,6m de vivo
Sección 5: Embaladora
Se alimenta con rollos de funda plástica que vienen de largo 3,3m para una plaza y 4,2m para dos plazas y ambos ancho 2,5m.
- Total 1 plaza: 3,3x2,5= 8,25m2 por colchón
- Total 2 plazas: 4,2x2,5= 10,5m2 por colchón
Secciones | Alimentación | Desperdicios (u/año) | Producciones Seccionales | ||
---|---|---|---|---|---|
Recuperables | No Recuperables | ||||
1p | 1 | 833 panes | 0 | 0.5 panes | 1665 panes cortados |
2p | 1418 panes | 0 | 0.5 panes | 2835 panes cortados | |
1p | 2 | 11488,5m2 de tela | 0 | 2159,83m2 | 1665 pares de telas cortadas |
2p | 24777,9m2 de tela | 0 | 3791,01m2 | 2835 pares de telas cortadas | |
1p | 3 | 1665 pares de telas cortadas | 0 | 0 | 1665 telas cosidas |
2p | 2835 pares de telas cortadas | 0 | 0 | 2835 telas cosidas | |
1p | 4 | 1665 panes cortados | 0 | 0 | 1665 colchones sin embalar |
1665 telas cosidas | 0 | 0 | |||
9657m de vivo | 0 | 0 | |||
2p | 2835 panes cortados | 0 | 0 | 2835 colchones sin embalar | |
2835 telas cosidas | 0 | 0 | |||
18711m de vivo | 0 | 0 | |||
1p | 5 | 1665 colchones sin embalar | 0 | 0 | 1665 colchones terminados |
13736,25 m2 de funda plástica | 0 | 0 | |||
2p | 2835 colchones sin embalar | 0 | 0 | 2835 colchones terminados | |
29767,5m2 de funda plástica | 0 | 0 |
Panes 1 Plaza | 833 panes |
Panes 2 Plaza | 1418 panes |
Tela 1 Plaza | 11488,5m2 de tela |
Tela 2 Plazas | 24777,9m2 de tela |
Vivo | 28368 m |
Funda Plástica | 43503,75 m2 |
El consumo real de materia prima quedará igual que el volumen total debido a que no tenemos desperdicios recuperables.
Panes 1 Plaza | 0,06% |
Panes 2 Plaza | 0,035% |
Tela 1 Plaza | 18,8% |
Tela 2 Plazas | 15,3% |
Ritmo de Trabajo
Se trabajará con 1 equipo de operarios durante 5 días de la semana 1 turno diario de 4 hs. A los 365 días del año habrá que descontar los 100 dias de fin de semana de las semanas laborales, 15 días de vacaciones donde cerrará la empresa y 10 feriados obligatorios en el año. No habrá cierre por mantenimiento.
Hs activas/año de las máquinas operativas
días activos/año = 365-100-15-10= 240 días
horas activas/año = 240 días activos/año * 4hs/día = 960 hs
Hs/año trabajadas por cada operario
960hs / 4 operarios = 240hs
Capacidad Real Anual de la Maquinaria Tipo de Cada Sección Operativa
Secciones | Cap. Teória / máquina x hora | Horas activas /Año | Cap. Teórica/Maq x año | Rendimiento Operativo | Cap. real / maquina x año |
---|---|---|---|---|---|
1 | 170 | 940 | 159800 | 80% | 127840 |
2 | 176 | 940 | 165440 | 80% | 132352 |
3 | 15 | 940 | 14100 | 75% | 10575 |
4 | 12 | 940 | 11280 | 90% | 10152 |
5 | 36 | 940 | 33840 | 90% | 30456 |
Determinación de la cantidad de maquinas operativas por sección, capacidad real anual de cada sección y su aprovechamiento en relacion al programa de produccion.
Secciones | Prog. anual de producción | Cap. real / maquina x año | Cant. de maq necesarias | Cap. Real / sección x año | Aprovechamiento Seccional |
---|---|---|---|---|---|
1 | 4500 panes cortados | 127840 | 0,035 = 1 | 127840 | 3,52% |
2 | 4500 telas cortadas | 132352 | 0,034 = 1 | 132352 | 3,40% |
3 | 4500 telas cosidas | 10575 | 0,42 =1 | 10575 | 42,55% |
4 | 4500 colchones sin embalar | 10152 | 0,44 =1 | 10152 | 44,33% |
5 | 4500 colchones terminados | 30456 | 0,14 =1 | 30456 | 14,78% |
Cuello de Botella
El cuello de botella es la sección de mayor aprovechamiento seccional, en este caso la 4 con 44,33%.
Determinación de la evolución de mercaderías
Tiempos de entrega y envió de las mercaderías.
Para la logistica de envíos, los tiempos de entrega son variados dependiendo los kilometros a recorrer para realizar la entrega.
Para todas aquellas ciudades dentro del rango de los 400 kilometros, siendo la mas cercana las toninas y la mas lejana Villa Gesell, buscamos limitar el plazo de entrega hasta 5 dias, necesitandose en el caso de pedidos grandes de 3 dias de preparación y pronosticando cualquier tipo de inconveniente en el despacho.
A los clientes residentes de la ciudad de Necochea se les informa un plazo de 6 dias debido tanto a la mayor distancia de recorrido (540 km), como tambien por el promedio de tamaño de pedido, siendo una ciudad muy poblada y con clientes de consumo mayorista.
Por ultimo, extendemos nuestra entrega hasta la ciudad de Puerto Madryn, siendo esta nuestra principal fuente de clientes en lo que queda de las playas argentinas. Para nuestros clientes Madrynenses, ofrecemos un plazo de 7 dias de entrega, siendo esta ciudad junto con Necochea quienes demandan presentan. La distancia a recorrer es de 1330 km.
Por otro lado, un porcentaje mensual es destinado a la venta online minorista, para la cual existe la opcion de retirar el producto por la planta misma, o de pagar un adicional por envío del que se encarga Mercado Libre.
Tamaños y frecuencias de compras.
Los pedidos se reciben mensualmente con cierta regularidad.
El 10% de nuestra producción mensual se ve orientado hacia la venta online minorista, promediando los 40 colchones por mes.
El resto de las ventas rodean los 350 colchones, siendo posible diferenciar claramente el volumen de pedidos de las ciudades de Necochea y Puerto Madryn del resto.
Tanto para Necochea como para Madryn, programamos una entrega mensual, unificando los pedidos de todos los clientes de cada lugar.
Las entregas hacia estas ciudades llegan a cubrir el 60% de los pedidos mayoristas, en una cifra cercana a los 200 colchones, y se programan para la primera quincena del mes.
La segunda quincena apunta cubrir el resto de la demanda, con 150 colchones a repartir entre el resto de las 6 ciudades costeras restantes, junto con la producción necesaria para poder entregar en la primer semana del mes siguiente.
Cálculos 6-11
Determinar la evolución de la producción
En nuestro proyecto se alcanzará el estado en régimen en el mes 5, luego se mantendrá un nivel de producción constante durante la vida útil del proyecto.
El período de puesta en marcha será de 4 meses, en los cuales se incrementará la producción de forma lineal cada mes.
Volumen de producción en estado de régimen (promedio):
4500 unidades / 11.5 meses = 391.3 unidades/mes.
Definimos 391 Unidades por mes.
Mes | Ritmo de prod al inicio(%) | Ritmo de prod al final (%) | Prod promedio (%) | Prod mensual promedio | Prod propuesta |
---|---|---|---|---|---|
1 | 0 | 5 | 2.5 | 391 | 9 u |
2 | 5 | 15 | 10 | 391 | 39 u |
3 | 15 | 35 | 25 | 391 | 97 u |
4 | 35 | 100 | 67.5 | 391 | 263 u |
Total PeM= | 408 u |
De estos 408, 37% es de una plaza (151 unidades) y el 63% es de 2 plazas (257 unidades)
Volumen de producción el resto del año 1:
11.5 - 4 = 7.5 meses
7.5 x 391 = 2932.5 => 2932 u
De estos 2942, 37% es de una plaza (1085 unidades) y el 63% es de 2 plazas (1847 unidades)
Volumen de producción en el año 1:
408 + 2932 = 3340 u
1 plaza = 1236
2 plazas = 2104
Volumen de producción del año 2 al n:
Siguiendo con el plan de ventas es 4500 u
Determinar stock promedio de producto elaborado
Ritmo de entrega: 1 vez por semana.
Semanas al año:
52 - 2 (vacaciones) = 50 semanas/año.
4500 Unidades/año / 50 semanas = 90 Unidades/Semana.
Stock promedio de elaborado:
Stock inicial = 0 Unidades.
Stock final = 90 Unidades.
Stock promedio = 45 Unidades.
Este stock se forma en el período de puesta en marcha, y se mantendrá constante, aunque permanentemente renovado.
Determinar la evolución de las ventas durante la vida útil del proyecto
Ventas del año 1: 3340 u - 45 u = 3295 Unidades.
En el primer año se generó el stock promedio de producto terminado, por lo que en los años siguientes se vende el total de la cantidad producida.
Ventas del año 2: 4500 Unidades
Determinar el consumo de materia prima para el programa de producción y formación de la mercadería en curso y semielaborada
En el período de puesta en marcha, incluyendo la producción descartable, se produce porcentualmente un mayor desperdicio no recuperable de un 50% adicional, según lo estima el tecnólogo.
El ciclo de elaboración demanda de 1 día (desde el ingreso de la materia prima al sector operativo hasta la salida de producto terminado).
Ciclos de elaboración anuales: 240 días al año / 1 = 240 ciclos de elaboración.
Consumo de materia prima
Período | Producción | Desperdicio | Unidades consumidas |
---|---|---|---|
Puesta en Marcha (4 meses) | 151 u = 75,5 panes | 0,09% (50%+) | 75,57 panes |
7,5 meses restantes | 1085 u = 542,5 panes | 0,06% | 542,825 panes |
TOTAL MP para la producción = | 618,395 panes | ||
Vol de producción año 1 = | 1236 u = 618 panes | ||
Desperdicio no recuperable por producción realizada = | 0,395 panes de desperdicio |
Período | Producción | Desperdicio | Unidades consumidas |
---|---|---|---|
Puesta en Marcha (4 meses) | 257 u = 128,5 panes | 0,0525% (50%+) | 128,567 panes |
7,5 meses restantes | 1847 u = 923,5 panes | 0,035% | 923,823 panes |
TOTAL MP para la producción = | 1052,390 panes | ||
Vol de producción año 1 = | 2104 u = 1052 panes | ||
Desperdicio no recuperable por producción realizada = | 0,390 panes de desperdicio |
Período | Producción | Desperdicio | Unidades consumidas |
---|---|---|---|
Puesta en Marcha (4 meses) | 151 u | 28,2% (50%+) | 193,582 u |
7,5 meses restantes | 1085 u | 18,8% | 1288,98 u |
TOTAL MP para la producción = | 1482,562 u | ||
Vol de producción año 1 = | 1236 u | ||
Desperdicio no recuperable por producción realizada = | 246,562 u de desperdicio |
Período | Producción | Desperdicio | Unidades consumidas |
---|---|---|---|
Puesta en Marcha (4 meses) | 257 u | 22,95% (50%+) | 315,981 |
7,5 meses restantes | 1847 u | 15,3% | 2129,591 |
TOTAL MP para la producción = | 2445,572 | ||
Vol de producción año 1 = | 2104 | ||
Desperdicio no recuperable por producción realizada = | 341,572 u de desperdicio |
MP | Alimentación | Días x año | Alim. x día | Ciclo de elab. | Vol. de MP requerido |
---|---|---|---|---|---|
Panes 1 plaza | 833 panes | 240 | 3,47 p | 1 | 3,47 p |
Panes 2 plazas | 1418 panes | 240 | 5,91 p | 1 | 5,91 p |
Tela 1 plaza | 11488,5m2 de tela | 240 | 47,87 m2 | 1 | 47,87 m2 |
Tela 2 plaza | 24777,9m2 de tela | 240 | 103,24 m2 | 1 | 103,24 m2 |
Vivo | 28368 m | 240 | 118,20 m | 1 | 118,20 m |
Funda Plástica | 43503,75 m2 | 240 | 181,27 m2 | 1 | 181,27 m2 |
MP | Para productos elaborados | Para mercadería en curso y semielab. | TOTAL |
---|---|---|---|
Panes 1 plaza | 618,395 panes | 2,45 panes | 621,87 panes |
Panes 2 plazas | 1052,390 | 4,17 panes | 1058,30 panes |
Tela 1 plaza | 1482,562 u = 10229,66 m2 | 33,78 m2 | 10277,53 m2 |
Tela 2 plaza | 2445,572 u = 21374,29 m2 | 72,87 m2 | 21477,53 m2 |
Vivo | 21055,2 m (para cant año 1) | 83,43 m | 21173,40 m |
Funda Plástica | 32289 m2 (para cant año 1) | 127,95 m2 | 32470,27 m2 |
MP | Para productos elaborados = TOTAL |
---|---|
Panes 1 plaza | 833 panes |
Panes 2 plazas | 1418 panes |
Tela 1 plaza | 11488,5m2 de tela |
Tela 2 plaza | 24777,9m2 de tela |
Vivo | 28368 m |
Funda Plástica | 43503,75 m2 |
Determinar el stock promedio de MP y el programa de compras
MP | Consumo anual | Consumo mensual (/11,5) = compra mensual |
---|---|---|
Panes 1 plaza | 833 | 72,43 => 73 |
Panes 2 plazas | 1418 | 123,30 => 124 |
Tela 1 plaza | 11488,5 | 999 m2 |
Tela 2 plaza | 24777,9 | 2154,6 m2 |
Vivo | 28368 | 2466,78 m |
Funda Plástica | 43503,75 | 3782,93 m2 |
El stock será el consumo mensual de cada mes, por lo que se harán 12 compras iguales de ese monto.
El stock promedio será entonces también el consumo mensual:
MP | Stock Prom |
---|---|
Panes 1 plaza | 72,43 |
Panes 2 plazas | 123,30 |
Tela 1 plaza | 999 m2 |
Tela 2 plaza | 2154,6 m2 |
Vivo | 2466,78 m |
Funda Plástica | 3782,93 m2 |
Realizar el cuadro resumen del programa general de evolución
Unidad | AÑO 0 | AÑO 1 | AÑO 2 a N | ||
---|---|---|---|---|---|
Ventas | uPT | 3295 | 4500 | ||
Stock promedio de PT | uPT | 45 | 45 | ||
Producción | uPT | 3340 | 4500 | ||
Desp. no recuperable | Panes 1 plaza | u | 0,395 | 0.5 | |
Panes 2 plazas | u | 0,390 | 0.5 | ||
Tela 1 plaza | m2 | 2034,14 | 2159,83 | ||
Tela 2 plaza | m2 | 3586,51 | 3791,01 | ||
Mercadería en Curso y Semielaborado | Panes 1 plaza | u | 2,45 | 2,45 | |
Panes 2 plazas | u | 4,17 | 4,17 | ||
Tela 1 plaza | m2 | 33,78 | 33,78 | ||
Tela 2 plaza | m2 | 72,87 | 72,87 | ||
Vivo | m | 83,43 | 83,43 | ||
Funda Plástica | m2 | 127,95 | 127,95 | ||
Consumo de MP | Panes 1 plaza | u | 621,87 | 833 | |
Panes 2 plazas | u | 1058,30 | 1418 | ||
Tela 1 plaza | m2 | 10277,53 | 11488,5 | ||
Tela 2 plaza | m2 | 21477,53 | 24777,9 | ||
Vivo | m | 21173,40 | 28368 | ||
Funda Plástica | m2 | 32470,27 | 43503,75 | ||
Stock MP | Panes 1 plaza | u | 75,57 | 72,43 | 72,43 |
Panes 2 plazas | u | 128,567 | 123,30 | 123,30 | |
Tela 1 plaza | m2 | 1335,71 | 999 | 999 | |
Tela 2 plaza | m2 | 2761,67 | 2154,6 | 2154,6 | |
Vivo | m | 2572 | 2466,78 | 2466,78 | |
Funda Plástica | m2 | 3944,25 | 3782,93 | 3782,93 | |
Compra MP
(en el año 0 se comprará lo mínimo para el período PM) |
Panes 1 plaza | u | 75,57 | 618,73 | 833 |
Panes 2 plazas | u | 128,567 | 1053,033 | 1418 | |
Tela 1 plaza | m2 | 1335,71 | 9940,82 | 11488,5 | |
Tela 2 plaza | m2 | 2761,67 | 20870,46 | 24777,9 | |
Vivo | m | 2572 | 21068,18 | 28368 | |
Funda Plástica | m2 | 3944,25 | 32308,95 | 43503,75 |
Determinación del Personal
Organigrama de la empresa
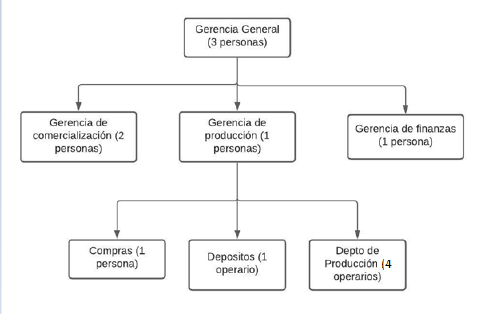
Descripción de los puestos de trabajo
Sector:
Compras (tela, espuma y vivo)
El sector de compras se encuentra en contacto con los proveedores de Materia Prima. Algunos de ellos son: Polifon S.A, Inderflex SRL, Arco Iris, Nitargen , Polimax.
Los puestos de trabajo dentro de este sector son el comprador que es el encargado de realizar un análisis de opciones de mercado y busca la mejor MP al menor costo. El otro puesto de trabajo en el área es el del transportista que es quien se encarga de la logística de entrada de la materia prima a la empresa. Este último proceso es tercerizado ya que lo realiza una empresa de transporte.
Terciarización de Matelaseado
Al recibir la tela directamente se la entregamos a Mantar SA una empresa que se encarga de la realización del Matelaseado de la tela. Este proceso consiste en brindar diferentes tensiones sobre los tejidos lo que permite disfrutar de tres versiones de confort; ya sea suave, medio o firme. Y además le da un diseño a la tela del colchón realizando un dibujo específico. Nosotros únicamente comercializamos los colchones de tela firme.
Este proceso no implica puestos de trabajo propios ya que es totalmente tercerizado. Sólo hay que encargarse de la entrega de la tela y de recibir y almacenar la tela matelaseada. La misma empresa de transporte de MP es la que se encarga de la entrada y salida de la tela pre y post proceso de matelasse.
Corte
Este sector está compuesto por dos sierras una que funciona como cortadora horizontal y la otra como cortadora vertical de espuma. Lo que se busca en este sector es conseguir que la espuma quede con la forma necesaria para funcionar como base del colchón. Además contamos con una máquina cortadora de tela (previamente matelaseada) para darle el tamaño deseado. En ambos casos de corte el pan de espuma se corta dependiendo si el colchón que vamos a realizar es de una plaza o dos y el mismo razonamiento con la tela.
Los puestos de trabajo son dos operarios para el corte del pan de espuma uno controla la sierra horizontal y el otro la vertical (ya que son procesos manuales). Y el corte de la tela lo realiza un único operario ya que otro será necesario para la costura (detallada más adelante).
Costura
En este área la tela ya tiene las dimensiones deseadas y ya fue matelaseada así que contamos con máquinas de costura recta, para unir los distintos tramos de tela que funcionará como funda de nuestro colchón.
E es un proceso que demanda de un operario capacitado y que pueda dedicar su atención al 100% para evitar accidentes de tráfico. El mismo es quien también se encarga de cortar el vivo con las dimensiones especificadas (dependiendo de si es colchón de una o dos plazas).
Cerradora
En este sector es en el cual el colchón se rellena con la espuma dentro de la tela que ya posee la forma y las dimensiones deseadas. La máquina necesaria es una cerradora que suele venir equipada con un brazo que se encarga de rotar el colchón para que el cierre sea más fácil y que el operario no tenga que realizar un gran esfuerzo.
Este es el proceso más importante porque es en el cual las 3 MP principales coinciden en un mismo punto (la tela, la espuma y el vivo). El vivo es el cordón que funciona como costura extra para que el contenido del colchón se mantenga dentro de la funda.
Necesitamos 1 operario encargado de introducir la espuma dentro de la funda de tela y otro que se encargue del control de la cerradora y del manejo del brazo.
Control de Calidad
El control de calidad es realizado por el operario más capacitado de la planta que a su vez es quien se encarga del control de la línea de embalaje automática. Este proceso se realiza mientras el colchón se encuentra en la línea de embalaje ya que el operario se encuentra desocupado.
Embaladora
El colchón en este punto ya se encuentra listo, lo único que resta es el embalado para entrega al consumidor. Este embalaje se realiza en una línea de embalaje automática en la cual ingresan los colchones y avanzan a través de rodillos giratorios que hacen llegar el colchón hasta la embaladora que le coloca la funda plástica y lo empuja fuera de la línea de producción.
Se necesitan dos operarios en este puesto. Uno más capacitado que se encargue del control de la línea de embalado y que además colabore con el hombreador para bajar los colchones de la línea.
Total de operarios: 4 operarios y un administrador de compras (comprador).
Aclaración: Todos los sectores cuentan con una zorra para la realización de la logística interna entre puesto y puesto.
Listado de Equipos Auxiliares, Muebles y Útiles.
Área | Equipo | Cantidad |
---|---|---|
Planta de producción y generales | Matafuegos | 5 |
Carteles de seguridad | 6 | |
Estanterias | 6 | |
Luminaria | 10 | |
Ventiladores | 4 | |
Set de herramientas varias | 3 | |
Computadora (con Sistema Operativo instalado) | 1 | |
Administración | Dispenser de agua | 1 |
Artículos varios de libreria | ||
Sillas de escritorio | 4 | |
Escritorios | 4 | |
Tacho de basura | 4 | |
Cajoneras | 2 | |
Aire Acondicionado | 1 | |
Baños | Inodoros | 2 |
Ducha | 1 | |
Bachas | 2 | |
Comedor | Mesa | 1 |
Sillas | 4 | |
Microondas | 1 | |
Heladera | 1 | |
Bacha | 1 | |
Vajilla completa | ||
Sistemas | Computadoras (con Sistema Operativo instalado) | 4 |
Telefonos | 2 | |
Impresora | 1 | |
Servidores | 1 | |
Licencias de Office y softwares varios |
Anteproyecto de Planta
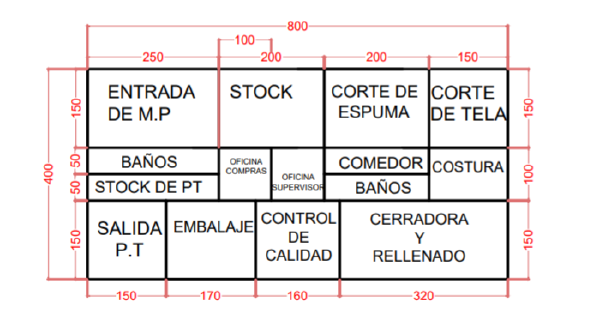
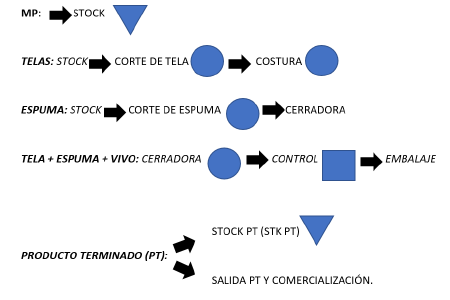
Cronograma de ejecución
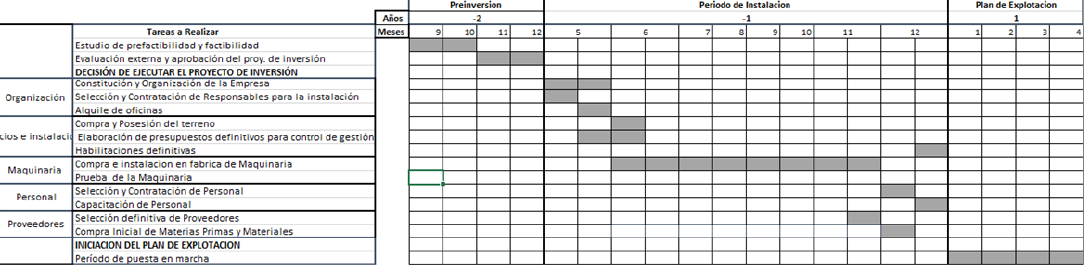