Diferencia entre revisiones de «2018/Grupo7/DimensionamientoTecnico»
(No se muestran 67 ediciones intermedias de 4 usuarios) | |||
Línea 1: | Línea 1: | ||
== Determinación de la localización == | == Determinación de la localización == | ||
Se tuvieron en cuenta 3 alternativas para decidir la ubicación del proyecto, teniendo en cuenta los principales factores a analizar (cercanía con proveedores, clientes y accesos). | Se tuvieron en cuenta 3 alternativas para decidir la ubicación del proyecto, teniendo en cuenta los principales factores a analizar (cercanía con proveedores, clientes y accesos). | ||
Línea 9: | Línea 9: | ||
=== Matriz de localización === | === Matriz de localización === | ||
[[Archivo: | [[Archivo:Matriz_de_localizacion.jpg|568x568px]] | ||
Se opta por una ubicación en San Martín, provincia de Buenos Aires, sus grandes fortalezas son el accesos que tiene, y la cercanía con los proveedores. | Se opta por una ubicación en San Martín, provincia de Buenos Aires, sus grandes fortalezas son el accesos que tiene, y la cercanía con los proveedores. | ||
Línea 16: | Línea 16: | ||
=== Planos/ fotos === | === Planos/ fotos === | ||
A continuación, se presentan planos e imágenes del producto final. | A continuación, se presentan planos e imágenes del producto final. | ||
[[Archivo:Tender pintado1.jpg|frameless|267x267px]][[Archivo:Tender_pintado.jpg|frameless|241x241px]] | |||
[[Archivo:Tender completo.jpg|frameless|500x500px]] | |||
[[Archivo:Tender completo 2.jpg|frameless|500x500px]] | |||
[[Archivo:Tender completo 3.jpg|frameless|500x500px]] | |||
=== Especificaciones Técnicas === | === Especificaciones Técnicas === | ||
==== Alas: ==== | ==== Alas: ==== | ||
[[Archivo:Alass 11.jpg|frameless|244x244px]][[Archivo:Alas 2.jpg|frameless|384x384px]] | |||
[[Archivo:Alas perfil.jpg|frameless|404x404px]] | |||
[[Archivo:ELEMENTOS ALAS.JPG|frameless|356x356px]] | |||
==== Pata larga: ==== | ==== '''Pata larga''': ==== | ||
[[Archivo:Pata larga 1.jpg|frameless|285x285px]][[Archivo:Pata larga 2.jpg|frameless|339x339px]] | |||
[[Archivo:ELEMENTOS PATA LARGA.JPG|frameless|390x390px]] | |||
==== Pata corta ==== | ==== Pata corta ==== | ||
[[Archivo:Pata corta 1.jpg|frameless|314x314px]][[Archivo:Pata larga 2.jpg|frameless|339x339px]] | |||
[[Archivo:ELEMNTOS PATA CORTA.JPG|frameless|426x426px]] | |||
==== Manija ==== | ==== Manija ==== | ||
[[Archivo:Manija 1.jpg|frameless|567x567px]][[Archivo:Manija 2.jpg|frameless|426x426px]] | |||
[[Archivo:ELEMENTOS MANIJA.JPG|frameless|477x477px]] | |||
==== Mesa ==== | ==== Mesa ==== | ||
[[Archivo:Mesa 1.jpg|frameless|351x351px]][[Archivo:Mesa 2.jpg|frameless|479x479px]][[Archivo:Mesa 3.jpg|frameless|526x526px]] | |||
[[Archivo:ELEMENTOS MESA.JPG|frameless|432x432px]] | |||
==== Remaches ==== | ==== Remaches ==== | ||
[[Archivo:Remaches.jpg|frameless]] | |||
==== Aranlock | ==== Aranlock ==== | ||
[[Archivo:Aranlock 1.jpg|frameless|492x492px]][[Archivo:Aranlock 2.jpg|frameless|260x260px]] | |||
==== Regaton ==== | ==== Regaton ==== | ||
[[Archivo:Regaton.jpg|frameless|358x358px]][[Archivo:Regaton 2.jpg|frameless]] | |||
=== Listado de Materiales === | === Listado de Materiales === | ||
=== Diagrama Arbóreo === | === Diagrama Arbóreo === | ||
En diagrama arbóreo nos indica que hay tres niveles, cada subconjunto tendrá un código, mediante el cual veremos que elementos los componen, con sus respectivos códigos y las cantidades. | En diagrama arbóreo nos indica que hay tres niveles, cada subconjunto tendrá un código, mediante el cual veremos que elementos los componen, con sus respectivos códigos y las cantidades. | ||
[[Archivo:Arboreo.JPG|frameless|622x622px]] | |||
=== Formas de adquisición === | === Formas de adquisición === | ||
Línea 100: | Línea 75: | ||
El aprovisionamiento se activa a través de una orden de compra emitida a los proveedores. | El aprovisionamiento se activa a través de una orden de compra emitida a los proveedores. | ||
[[Archivo:FORMA DE ADQUISICION.JPG|frameless|1311x1311px]] | |||
=== Normas Aplicables === | === Normas Aplicables === | ||
No existe norma alguna que deba cumplir el producto en cuanto a la conformacion que se realiza en nuestro taller. Si hay que regular mediante controles de calidad los semielaborados provenientes del proveedor que realiza el lavado y pintado, ya que al aplicarle pintura epoxi deberá cumplir con la norma ISO 12944 (Protección contra la corrosión de estructuras de acero mediante sistemas de pintura de protección). Dicha norma trata desde ambientes de pintado, hasta forma de aplicacion segun distintos tipos de superficies en las que se encuentre el acero). | |||
A su vez, se aplicara para el control de semielaborados provenientes del proveedor, un control por lotes adecuándose a la norma IRAM 15. | |||
=== Acondicionamiento del Producto === | === Acondicionamiento del Producto === | ||
El producto será entregado en una bolsa de polietileno. | El producto será entregado en una bolsa de polietileno. | ||
[[Archivo:Acondicionamiento 1.jpg|frameless|257x257px]] | |||
A su vez, para entregas a supermercados, mayoristas, y | A su vez, para entregas a supermercados, mayoristas, y | ||
Línea 113: | Línea 91: | ||
a 6 unidades. | a 6 unidades. | ||
[[Archivo:Acondicionamiento 2.jpg|frameless|403x403px]] | |||
Las medidas de las cajas son 110 cm x 40 cm x | Las medidas de las cajas son 110 cm x 40 cm x | ||
Línea 119: | Línea 97: | ||
=== Plan de Ensayos === | === Plan de Ensayos === | ||
Una vez soldada la mesa y las alas se harán pruebas de tracción y carga (se colocara peso para simular el peso de la ropa mojada colgando) para ver la resistencia y estabilidad del conjunto. | |||
Por otro lado, para el control de los semielaborados provenientes del proveedor que realiza el pintado, se aplicaran controles del tipo anual, mensual y contra entrega de semielaborados. | |||
Con el ensamble final realizado se someterá el tendedero a esfuerzos laterales parar corroborar que mantenga el equilibrio. | |||
Para las pruebas de tracción y carga se realizara el control de todas las unidades, simulando (sobre el mismo puesto de trabajo) el peso del tender completo al 100% de ropa (7,5 KG). Las unidades que no soporten dicha prueba pasaran a formar parte del scrap. | |||
Por otro lado, al proveedor que nos entregara el semielaborado pintado, se le requerirá a nivel anual que presente los certificados del personal de inspección que realice control de los procesos en su planta, así como registros de inspección. A nivel mensual, procedimientos de inspección (llenados de reportes, calibración de equipos, etc) y posibles modificaciones que sufran para contar con los estándares que se están fijando en nuestro producto. Finalmente contra entrega del semielaborado se aplicara el método campana de vació, en el cual se tomara una muestra aleatoria del 25% del lote y se le realizaran pruebas de terminación superficial (acabado, uniformidad de la capa aplicada, igualdad entre toda la muestra tomada), que las realizara el jefe de producción. De no prestar conformidad con la muestra tomada en la primera ocasion, se separan las muestras y se advertirá al proveedor. Si se reitera 2 veces consecutivas dicha desconformidad, se procederá a licitar el servicio de pintado. | |||
Para las pruebas de esfuerzos laterales se tomara aleatoriamente cada media hora (a fin de tener muestras cercana a lo que establece la norma IRAM 15 de 20 subgrupos) 3 tendederos de dos cajas de 6 lista para la venta mayorista, se lo cargara nuevamente como se hizo para la prueba de tracción y carga, y se la aplicaran manualmente esfuerzos de la siguiente manera: | |||
- Esfuerzo normal sobre patas. | |||
- Esfuerzo normal sobre mesa. | |||
- Esfuerzo lateral y normal sobre alas. | |||
En caso de que 2 de los 3 tendederos no soporten las pruebas antes mencionadas (entiéndase por no soportar la caída del tender, la rotura de remaches o soldaduras, o la rotura de cualquier varilla que conforme la mesa) se procederá a descartar ambas cajas ya que no se consideran aptas para la venta. | |||
== Definición del Proceso de Producción == | == Definición del Proceso de Producción == | ||
Línea 124: | Línea 121: | ||
=== Diagrama de flujo de fabricación y control === | === Diagrama de flujo de fabricación y control === | ||
A continuación, se define el proceso de fabricación de un tendedero con alas: | A continuación, se define el proceso de fabricación de un tendedero con alas: | ||
[[Archivo: | [[Archivo:Diagrama_de_flujo.png|left|frameless|714x714px]] | ||
=== Descripción de cada etapa del proceso productivo === | === Descripción de cada etapa del proceso productivo === | ||
Línea 131: | Línea 128: | ||
'''Manija:''' Entra el alambre en rollo por una máquina que lo endereza, sacándole las tensiones, y lo corta a medida. Luego se le da la forma a la manija con un golpe de balancín. Finalmente se envía pintar. | '''Manija:''' Entra el alambre en rollo por una máquina que lo endereza, sacándole las tensiones, y lo corta a medida. Luego se le da la forma a la manija con un golpe de balancín. Finalmente se envía pintar. | ||
''' | '''Mesa:''' Entra el alambre en rollo por una máquina que lo endereza, sacándole las tensiones, y lo corta a medida. Después se posicionan a mano sobre el marco para darle la forma de mesa y se sueldan en una soldadora de punto. Una vez soldado se envía el subconjunto a pintar. | ||
'''Ala:''' Varillas transversales: Al igual que la mesa, se cortan las varillas a medida. | '''Ala:''' Varillas transversales: Al igual que la mesa, se cortan las varillas a medida. | ||
Línea 141: | Línea 138: | ||
'''Pintura:''' La pintura de las piezas se realiza con un tercero, quien devuelve las partes listas para continuar con la operación. | '''Pintura:''' La pintura de las piezas se realiza con un tercero, quien devuelve las partes listas para continuar con la operación. | ||
Una vez pintadas las partes, se hace el ensamble | Una vez pintadas las partes, se hace el ensamble mesa-alas, donde en una mesa de trabajo se pone la mesa junto con las alas, y con un pistón neumático se le da un golpe a los rulos de las alas para que queden ensambladas. Finalmente se fijan las alas entre sí con alambre. | ||
'''Ensamble final:''' Se colocan las patas, la manija y la | '''Ensamble final:''' Se colocan las patas, la manija y la mesa semi-ensambladas en una máquina fabricada a medida en la planta, donde se le introducen las aranlock en unas cuñas imantadas. Con el accionamiento manual por medio de un pedal, la máquina traba neumáticamente las aranlock en la mesa y la manija, haciendo que queden atrapadas las patas y ya completamente ensamblado el tendedero. | ||
'''Empaque:''' Los productos terminados se introducen manualmente en una bolsa y se la sella con una termo selladora. | '''Empaque:''' Los productos terminados se introducen manualmente en una bolsa y se la sella con una termo selladora. | ||
Línea 156: | Línea 153: | ||
Además de la amoladora de banco, se debe montar la estructura al comienzo donde se depositan los caños de 6000 mm y del otro lado la estructura donde ca el caño cortado. | Además de la amoladora de banco, se debe montar la estructura al comienzo donde se depositan los caños de 6000 mm y del otro lado la estructura donde ca el caño cortado. | ||
[[Archivo:Sierra de banco.PNG]] | |||
La misma puede ser corte caño pata larga o corte caño pata corta, para ambas se requiere un puesto de trabajo y por lo tanto un operario, siendo la duración de ambas operaciones de aproximadamente cuarenta y cinco segundos, pudiendo producirse en una jornada laboral de ocho horas 1280 unidades. | La misma puede ser corte caño pata larga o corte caño pata corta, para ambas se requiere un puesto de trabajo y por lo tanto un operario, siendo la duración de ambas operaciones de aproximadamente cuarenta y cinco segundos, pudiendo producirse en una jornada laboral de ocho horas 1280 unidades. | ||
Línea 163: | Línea 160: | ||
2. '''Dobladora hidráulica para caños y varillas (x2):''' | 2. '''Dobladora hidráulica para caños y varillas (x2):''' | ||
[[Archivo:Dobladora.PNG|right]] | |||
{| | {| | ||
|Datos técnicos: | |Datos técnicos: | ||
Línea 189: | Línea 187: | ||
<br> | <br> | ||
|} | |} | ||
Capacidad teórica/hora= 60 patas | Capacidad teórica/hora= 60 patas | ||
Línea 221: | Línea 218: | ||
A la maquina seleccionada se le agregaran topes según las medidas del caño (al igual que se hizo con la cortadora), para optimizar el proceso y establecer medidas estándar. | A la maquina seleccionada se le agregaran topes según las medidas del caño (al igual que se hizo con la cortadora), para optimizar el proceso y establecer medidas estándar. | ||
[[Archivo:Punzonado.PNG]] | |||
Capacidad teórica/hora= 90 patas | Capacidad teórica/hora= 90 patas | ||
Línea 254: | Línea 251: | ||
|} | |} | ||
[[Archivo:Cortadora de varillas.PNG]] | |||
Capacidad teórica/hora= 300 varillas | Capacidad teórica/hora= 300 varillas | ||
Línea 260: | Línea 257: | ||
5. '''Soldadora de punto:''' | 5. '''Soldadora de punto:''' | ||
La soldadura por puntos es un método de soldadura por resistencia que se basa en presión y temperatura, en el que se calienta una parte de las piezas a soldar por corriente eléctrica a temperaturas próximas a la fusión y se ejerce una presión entre las mismas. | La soldadura por puntos es un método de soldadura por resistencia que se basa en presión y temperatura, en el que se calienta una parte de las piezas a soldar por corriente eléctrica a temperaturas próximas a la fusión y se ejerce una presión entre las mismas. Se contara con 2 puestos, cada puesto cuenta con una mesada preparada para armar el esqueleto de la mesa y de las alas. | ||
Para el proceso de soldadura de | Para el proceso de soldadura de mesa (9 Varillas + contorno) se requiere 1 puesto de trabajo, el cual emplea en la operación aproximadamente 5 segundos por punto con 36 puntos más 30 segundos armado de esqueleto. | ||
Por otra parte, para el proceso de soldadura de | Por otra parte, para el proceso de soldadura de mesa (alas, 4 varillas + contorno) se requiere un puesto de trabajo, el cual también emplea aproximadamente 5 segundos por punto con 8 puntos más 20 segundos de esqueleto. | ||
[[Archivo:Soldadora de punto.PNG|right]] | |||
{| | {| | ||
|Datos técnicos: | |Datos técnicos: | ||
Línea 282: | Línea 280: | ||
|} | |} | ||
Capacidad teórica/hora= 10,9 mesas (10,9 mesas y 21,8 alas) | |||
Capacidad teórica/hora= 10,9 | |||
6. '''Martillo Neumático:''' | 6. '''Martillo Neumático:''' | ||
[[Archivo:Martillo neumatico.PNG|right]] | |||
{| | {| | ||
|Datos técnicos: | |Datos técnicos: | ||
Línea 322: | Línea 319: | ||
<nowiki>*</nowiki> Capacidad de Tanque: 50 L | <nowiki>*</nowiki> Capacidad de Tanque: 50 L | ||
|} | |} | ||
En esta maquina se doblan las puntas de las alas uniéndose con la mesa. La duración de la operación del martillo neumático ronda aproximadamente cincuenta segundos y el mismo es manejado por un solo operario. | En esta maquina se doblan las puntas de las alas uniéndose con la mesa. La duración de la operación del martillo neumático ronda aproximadamente cincuenta segundos y el mismo es manejado por un solo operario. | ||
Capacidad teórica/hora= 72 | Capacidad teórica/hora= 72 mesas | ||
7. '''Remachadora:''' | 7. '''Remachadora:''' | ||
[[Archivo:Remachadora.PNG|right]] | |||
{| | {| | ||
|Datos técnicos: | |Datos técnicos: | ||
Línea 351: | Línea 348: | ||
La máquina es manejada por un operario, en la misma se emplea aproximadamente 40 segundos en la realización de su tarea. | La máquina es manejada por un operario, en la misma se emplea aproximadamente 40 segundos en la realización de su tarea. | ||
Capacidad teórica/hora= 90 patas doble. | Capacidad teórica/hora= 90 patas doble. | ||
Línea 358: | Línea 353: | ||
8. '''Puesto de ensamblado:''' | 8. '''Puesto de ensamblado:''' | ||
[[Archivo:Parrilla y patas.PNG]] | |||
Una vez pintado, se procede al armado. La operación de armado se realiza manualmente, sin embargo, se utiliza una | Una vez pintado, se procede al armado. La operación de armado se realiza manualmente, sin embargo, se utiliza una estacion fijadora sobre la cual se ubica el producto semielaborado para así evitar movimientos indeseados. | ||
La operación de ensamble cuadro mesa - alas en martillo neumático (2 por tendedero) requiere de un trabajador el cual emplea aproximadamente cuarenta segundos en la operación. | La operación de ensamble cuadro mesa - alas en martillo neumático (2 por tendedero) requiere de un trabajador el cual emplea aproximadamente cuarenta segundos en la operación. | ||
[[Archivo:Puesto ensamble.PNG]] | |||
9. ''' | 9. '''Ensamblador final:''' | ||
( | Una vez completo el ensamble cuadro mesa - alas se procede con la segunda parte del ensamble, la del ensamble final del subconjunto (con aranlock), para ello se requiere un puesto de trabajo que emplean en su actividad sesenta segundos siendo su producción en una jornada laboral de ocho horas de 240 unidades. | ||
[[Archivo:Ensamble final.PNG]] | |||
Capacidad teórica/hora= 30 tendederos. | Capacidad teórica/hora= 30 tendederos. | ||
==== Medios de fabricacion y control: ==== | |||
# Cierra circular de banco (amoladora + estructura casera para soporte de caños). | |||
# Dobladora hidraulica para caños y varillas. | |||
# Perforadora de caños para tubos redondos. | |||
# Tensadora/Cortadora. | |||
# Soldadora de punto. | |||
# Martillo Neumatico. | |||
# Remachadora. | |||
# Ensamblador final. | |||
==== Calificacion y formacion de los operadores: ==== | |||
'''Gerente General:''' Grado en Ingenieria industrial, Ingles fluido, 5 años de experiencia en funciones similares y capacidad de lidereazgo. | |||
'''Gerente Comercial:''' Licenciado en Comercializacion/Ingeniero Industrial/Licenciado en administración de empresas, ingles fluido, 5 años de experiencia en posiciones similares, experiencia en departamentos de compras y en ventas. | |||
'''Responsable Administratvo y de Finanazas:''' Grado en administracion de empresas. Experiencia de 3 años en posiciones similares. Conocimientos en logistica y experiencia en procesos de facturacion. | |||
'''Jefe de Producción:''' Ingeniero Mecánico, Industrial o de procesos. Experiencia de 5 años en posiciones similares y con personas a cargo. Liderazgo y compañerismo. Experiencia en conducción de equipos de producción. | |||
'''Operarios:''' Secundario completo (se valorara titulo técnico) y experiencia comprobable de 2 años en procesos según su función dentro de la linea. Experiencia con cierras de corte, maquinas de punzonado y soldadura de punto. | |||
Ademas, se calificara a el jefe de producción con una capacitación en compras y materiales de la extensión universitaria de la UTN. A su vez, se calificara a los operarios con una certificacion en tecnicas y oficios en aceros y superaleaciones de la extension universitaria de la UTN (para interiorizarse en el tratado del material madre del producto) y se contratara una capacitacion general (que se realizara dentro de la empresa) de la empresa Black&Decker para uso de maquinaria industrial (para operarios que utilicen cortadora, tensadora, soldadora y remachadora. | |||
Para el uso de la dobladora, perforadora y ensamblado se recurrirá a instrucciones del jefe de producción (Ingeniero) con soporte de los manuales de las respectivas maquinas. | |||
=== Consumo de energía, agua y otros servicios === | === Consumo de energía, agua y otros servicios === | ||
Por un lado, no es necesario el consumo de gas ya que no se utiliza para el proceso productivo y para los usos de cocina, vestuarios e instalaciones no productivas se dispondrá de maquinaria eléctrica. | |||
Consumo de agua: | |||
[[Archivo:Aguacons.JPG]] | |||
Consumo electrico: | |||
[[Archivo:Captura13.PNG|620x620px]] | |||
Los puestos de ensamblado no requieren de electricidad al igual que la dobladora. | |||
Por ultimo, se contratara un servicio de internet inalambrico para el cual se colocaran 3 routers, uno en la zona de planta, otro en las oficinas y el ultimo en la gerencia general. | |||
=== Mantenimiento y medios de control. Descripción de los sistemas de seguridad. === | === Mantenimiento y medios de control. Descripción de los sistemas de seguridad. === | ||
'''Sistemas de Mantenimiento:''' | |||
Se realizara un mantenimiento preventivo y un control periódico del estado de las maquinas y herramientas de trabajo. Dicho mantenimiento preventivo estara constituido por: | |||
A. Tareas de limpieza general de la planta en forma diaria, como así limpieza particular de cada puesto de trabajo al finalizar el lote de producción (para evitar desvios de eficiencia significativos por material sobrante). | |||
B. Tareas de mantenimiento de maquinaria como lubricacion (para el caso de todas las maquinas), revisión de partes móviles (para todas las maquinas, para evitar la formacion de juegos en los casos donde no son deseados) y afilado de herramientas de corte (para el caso de la cierra circular, la tensadora cortado y la punzonadora). Estas tareas se realizaran cada 2 semanas con ayuda de los operarios y dirigido por el jefe de producción. | |||
A su vez, se realizara un mantenimiento correctivo que estará constituido por tareas como el pintado de paredes, la limpieza de extractores, mantenimiento de la nave industrial, cambio o refacción de luminarias, cambio o refacción de racks, etc. | |||
Teniendo en cuenta el correcto uso de las maquinas y herramientas utilizadas, se brindara a los operarios una capacitación para evitar desgastes por mal uso. | |||
El propio operario, encargado de cada maquina, dará aviso en caso de requerimiento de un mantenimiento antes de lo programado. | |||
'''Sistemas de seguridad:''' | |||
Habrá señalización a lo largo de toda la planta sobre los elementos de protección personal requeridos en cada puesto de trabajo. Por esto mismo se brindara un kit con todos los elementos necesarios a cada operario. | |||
Se dispondrá de al menos un matafuego por cada sector de trabajo (caños, varillas, ensamble, almacenes, oficinas, etc). | |||
Capacitación al operario sobre el correcto uso de cada elemento de trabajo. | |||
Sendas de circulación peatonal para desplazarse por la planta. Así como senderos de circulación para zorras y carros de carga. | |||
Se designara un piloto de seguridad encargado de controlar que el resto de sus compañeros cumplan con todas las normas de seguridad. | |||
=== Ejercicios 1 a 5 de la guía de Trabajos Prácticos === | === Ejercicios 1 a 5 de la guía de Trabajos Prácticos === | ||
[[Archivo:G7 DT - Ejercicios 1-5.xlsx|none|thumb|Tablas excel ejercicios 1-5]] | |||
[[Archivo:Grupo7Archivo1.PNG|645x645px]] | |||
1) | |||
[[Archivo:MP.JPG|frameless|1355x1355px]] | |||
[[Archivo:RENDIMIENTOOO.JPG|frameless|638x638px]][[Archivo:RENDIMIENTO 2.JPG|frameless|539x539px]] | |||
[[Archivo:CANTIDAD ROLLOS.JPG|frameless|642x642px]][[Archivo:DESPERDICIO.JPG|frameless|560x560px]] | |||
2) | |||
[[Archivo:RITMO.JPG|frameless|804x804px]] | |||
3) | |||
[[Archivo:Grupo7Archivo2.PNG]] | |||
[[Archivo:G7-DT - Cuadro ej 3.JPG|none|thumb|635x635px]] | |||
4) <u>Aprovechamiento Seccional:</u> | |||
[[Archivo:Flujo ej 4.png|1000x1000px]] | |||
[[Archivo:G7-DT - Cuadro ej 4.JPG|none|thumb|636x636px]] | |||
[[Archivo:G7-DT - Cuadro ej 4 I - II (Soporte MOO).JPG|left|thumb|954x954px|En este cuadro se muestra como se distribuye el soporte de los operarios a otras secciones dentro del flujo de producción (% Hs anuales de dedicación). El operario B esta encargado del soldado de alas (para esta actividad recibirá soporte de los operarios A y E). El operario C esta encargado del doblado de manijas (para esta actividad recibirá soporte del operario A)]] | |||
[[Archivo:G7-DT - Cuadro ej 4 II.JPG|none|thumb|674x674px]] | |||
5) <u>Cuello de botella:</u> | |||
Como se puede observar en el cuadro del punto cuatro, el aprovechamiento seccional más alto se encuentra en el Operario E (que además de ser el encargado del ensamble y empaquetado final de todos los subconjuntos, dará soporte al puesto de soldadura). Por ende, el cuello de botella se encuentra en esta sección. | |||
[[Archivo:G7-DT - Cuadro ej 5.JPG|none|thumb|674x674px]] | |||
== Determinación de la evolución de las mercaderías == | == Determinación de la evolución de las mercaderías == | ||
Línea 397: | Línea 485: | ||
=== Tamaño y frecuencias de compra === | === Tamaño y frecuencias de compra === | ||
Las ventas del año 1: 14.100( | Las ventas del año 1: 14.100 | ||
Las ventas del año 2 a 5: 22.600 | |||
El aprovisionamiento de las materias primas sera de manera semanal. | |||
Entonces, se deberá contar con los siguientes insumos tos los comienzos de semana: | |||
[[Archivo:Mp semanal posta.jpeg|frameless|639x639px]] | |||
El mecanismo para solicitarles la mercadería a los proveedores es a través de ordenes de compra. | |||
=== Cálculos de los ejercicios 6 a 11 de la guía === | |||
[[Archivo:Ejs 6 11nuevo.xlsx|left|thumb|Tablas´ Excel de los Ej. 6 al 11]] | |||
Cabe destacar que todos los cálculos se efectuaran en base a cantidades de producto final, las relaciones con el BOM fueron previamente descritas. | |||
El calculo de la capacidad del sistema parte de las estimaciones de ventas del proyecto. | |||
==== 6) EVOLUCIÓN DE LA PRODUCCIÓN ==== | |||
a) Volumen de producción mensual en estado de régimen (promedio): se tienen en cuenta 285 días laborales en el año (el resto, vacaciones, fines de semana, feriados, se distribuyen a lo largo del año linealmente), resultando así un valor mensual promedio de: | |||
[[Archivo:VOLUMEN DE PRODUCCION.JPG|frameless]] | |||
b) Volumen de la producción durante el periodo de puesta en marcha: | |||
Es necesario analizar el nivel de producción durante el periodo de puesta en marcha y ver si las capacidades antes determinadas, satisfacen la demanda del primer año. | |||
[[Archivo:Ej 6.JPG|frameless|574x574px]] | |||
c) Capacidad de producción durante el resto del 1er año: 12 meses – 3 meses = 9 meses | |||
1833,33 unidades / mes * 9 meses = 16.500 | |||
d) Capacidad de producción en el año 1 = 1506,67+ 16.500 = 18006,67 | |||
Se precisan producir las unidades a vender y el stock promedio, durante los primeros 3 meses se producirán 1506,67 y el resto del año 12.811 (sale de ventas+ stock prom ('''7b''') - producción 3 meses(6b) ) | |||
e) Volumen de producción del año 2 al 5 = 22.600 | |||
==== 7) STOCK PROMEDIO DE PRODUCTO ELABORADO ==== | |||
a) Volumen de producción semanal promedio, en estado de régimen: | |||
[[Archivo:VOLUMEN DE PRODUCCION semanal2.JPG|frameless|172x172px]] | |||
b) El stock promedio de elaborado varia entre 0 y 434,61 por semana. | |||
Entonces el Stock promedio es 217,3 unidades | |||
Aunque la capacidad de producción sea 18006,67, se producirán 14.317,61 tendederos durante el primer año (ventas + stock promedio) | |||
==== 8) EVOLUCIÓN DE LAS VENTAS DURANTE LA VIDA ÚTIL DEL PROYECTO ==== | |||
Fueron previamente determinadas a partir de un estudio de mercado. | |||
(La producción es determinada en función del plan de ventas) | |||
==== 9) CONSUMO DE MATERIA PRIMA PARA EL PROGRAMA DE PRODUCCIÓN Y FORMACIÓN DE LA MERCADERÍA EN CURSO Y SEMIELABORADA. ==== | |||
En el año 1 el consumo de materia prima esta destinada a la producción realizada y a la formación de mercadería en curso. | |||
===== a) Consumo de materia prima para realizar la producción del 1er año: ===== | |||
Se multiplica la producción deseada por un factor de desperdicio propio del año 1. | |||
-En los 1eros 3 meses (puesta en marcha) '''(6b)''': 1,1 * 1506,67 = 1.657,34 unidades | |||
-En los 9 meses restantes '''(14.100 u - 7b - 6b)''': 1,05 * 12.811 = 13.451,5 unidades | |||
Se debe multiplicar el listado de componentes (BOM) por la cantidad de tendederos necesarios: 15.108,84 (1.657,34 + 13.451,5). | |||
- | -Volumen de la producción realizada en el año 1 = 14.317,3 unidades | ||
- | -Desperdicio no recuperable: 791,5 unidades | ||
'''b) Consumo de materia prima en la mercadería en proceso:''' | |||
-volumen de materia prima requerido: la alimentación de proceso durante el ciclo de elaboración. | |||
Se tiene en cuenta que son 6 turnos de 8 hs por semana,en total hay 48 hs en las que se producen 434,62 tendederos. | |||
En promedio el ciclo de elaboración del tendedero es de 0 ,11 hs. | |||
Entonces: 22.600 * 0,11 hs / (285 días * 8 hs/dia) = 1,1 unidad (se multiplica por el Bom) | |||
- | ==== '''c) Consumo total de materia prima en el año 1:''' ==== | ||
-Para los productos elaborados: 15.108,84 unidades | |||
- | -Para la mercadería en curso y semi elaborados: 1,1 unidad | ||
- | -Consumo total de materia prima año 1: 15.110 unidades | ||
[[Archivo:La paja.jpeg|frameless|636x636px]] | |||
Año 2 al 5: el consumo de materia prima es exclusivamente destinado a la producción cada año: 22.600 unidades de tendederos. | |||
==== 10) STOCK PROMEDIO DE MATERIAS PRIMA Y PROGRAMA DE COMPRAS ==== | |||
En estado de régimen sera (en unidades) | |||
a)El stock mínimo es la mitad de producción de una semana (217,3 unidades). | |||
=== | b) variación del stock de materia prima durante el año y programa de compras: | ||
[[Archivo:Stock prom.JPG|frameless|506x506px]] | |||
==== 11)CUADRO RESUMEN DEL PROGRAMA GENERAL DE EVOLUCIÓN ==== | |||
[[Archivo:Cuadro 11.JPG|frameless|635x635px]] | |||
(en el periodo de instalación se compra la MP necesario para la puesta en marcha) | |||
== Determinación del personal == | == Determinación del personal == | ||
=== Organigrama de toda la empresa === | === Organigrama de toda la empresa === | ||
[[Archivo:45.jpg|left|thumb]] | |||
=== Descripción de los puestos de trabajo === | === Descripción de los puestos de trabajo === | ||
'''Gerente General:''' Representante de la empresa para asuntos externos, determinación (en conjunto con gerentes) y aprobación de objetivos generales, control de los distintos sectores y principal allegado a los inversores. | |||
'''Gerente Comercial:''' Responsable principal de ventas y compras, contacto con proveedores, control de cumplimiento del plan de ventas y analisis de desvios, encargado de canales de venta y comunicacion del producto. Reporta al Gerente general. | |||
'''Responsables Administrativo y de Finanzas:''' Encargado de la facturación, seguimiento contable, y coordinación logística (seguimiento de pedidos e ingresos/egresos de producto terminado a nivel documental). Responsable de pagos y cobros. Reporta al Gerente general. | |||
'''Jefe de producción:''' Responsable del cumplimiento del plan de producción, disponibilidad de materias primas y mantenimiento de la maquinaria. Coordinador de equipos de trabajo y lineamientos a los 5 operarios. Reporta directamente al Gerente general. 5 operarios a cargo. | |||
'''Operarios:''' | |||
'''Operario A:''' Encargado del corte, el doblado y el punzonado de caños. Responsable de carga de materia prima al puesto de trabajo. El semielaborado se entraga a un proceso de terceros (pintado). Reporta directamente al Jefe de produccion. | |||
'''Operario B:''' Encargado del corte y tensado de varillas de alambre. Responsable de carga de materia prima al puesto de trabajo. El semielaborado es entregado a otro puesto dentro del mismo proceso productivo (soldadura). Reporta directamente al Jefe de produccion. | |||
'''Operario C:''' Encargado del doblado de varillas de alambre para la posterior formacion de la mesa. El semielaborado es entregado a otro puesto dentro del mismo proceso productivo (soldadura). Reporta directamente al Jefe de produccion. | |||
'''Operario D:''' Encargado de la soldadura de semielaborados de varillas de alambre. El semielaborado es entregado a un proceso que se realiza por terceros (pintado). Reporta directamente al Jefe de produccion. | |||
'''Operario E:''' Encargado del ensamble final y empaquetado del producto. Recibe los semielaborados desde un proceso de terceros. Control de entrada de mercaderias (calidad del pintado) con soporte del Jefe de produccion. Reporta directamente al Jefe de produccion. | |||
== Equipos auxiliares, muebles y útiles == | == Equipos auxiliares, muebles y útiles == | ||
[[Archivo:EquiposAux.PNG]] | |||
=== Plano de Planta === | |||
•Fábrica: 46.0m x 30.0m (3 lotes de 46.0m x 10.0m) | |||
•Depósito PT: 14.0m x 2.5m | |||
•Depósito SE: 14.0m x 3.5m | |||
•Depósito MP rollos: 10.0m x 3.0m | |||
•Depósito MP caños: 20.0m x 4.0m | |||
•Depósito Insumos: 7.5m x 4.0m | |||
•Depósito Patas: 7.0m x 9.0m | |||
•Depósito Mesa y Alas: 7.0m x 7.5m | |||
•Vestuario 7.0m x 10.0m (con baño de 4.0m x 4.0m) | |||
•Oficina: 9.0m x 3.0m | |||
•Sala de reunión: 5.5m x 3.0m | |||
•Cocina comedor: 3.5m x 3.0m | |||
•Baño: 3.0m x 3.5m | |||
[[Archivo:G7 DT Plano fabrica tendederos v.2.JPG|none|thumb|765x765px]] | |||
[[Archivo:G7 DT Plano fabrica tendederos (cotas) v.2.JPG|none|thumb|710x710px]] | |||
Plano del recorrido de los materiales | |||
[[Archivo:G7 DT Flujo alambre v.2.JPG|none|thumb|1233x1233px|Flujo alambre: Mesa + Alas]] | |||
[[Archivo:G7 DT Flujo caños v.2.JPG|none|thumb|1232x1232px|Flujo caños: Patas]] | |||
[[Archivo:G7 DT Flujo SE-PT v.2.JPG|none|thumb|1245x1245px|Flujo SE pintados - Ensamble PT]] | |||
== Cronograma de ejecución == | == Cronograma de ejecución == | ||
[[Archivo:G7 Cronograma ejecucion Tendederos.jpg|thumb|799x799px|none]] | |||
[[Archivo:G7 DT Cronograma Tendederos.xlsx|none|thumb|Planilla Excel con Cronograma.]] |
Revisión actual - 20:37 24 sep 2018
Determinación de la localización
Se tuvieron en cuenta 3 alternativas para decidir la ubicación del proyecto, teniendo en cuenta los principales factores a analizar (cercanía con proveedores, clientes y accesos).
Alternativa 1: Capital Federal
Alternativa 2: San Martin
Alternativa 3: Olivos
Matriz de localización
Se opta por una ubicación en San Martín, provincia de Buenos Aires, sus grandes fortalezas son el accesos que tiene, y la cercanía con los proveedores.
Definición técnica del producto
Planos/ fotos
A continuación, se presentan planos e imágenes del producto final.
Especificaciones Técnicas
Alas:
Pata larga:
Pata corta
Manija
Mesa
Remaches
Aranlock
Regaton
Listado de Materiales
Diagrama Arbóreo
En diagrama arbóreo nos indica que hay tres niveles, cada subconjunto tendrá un código, mediante el cual veremos que elementos los componen, con sus respectivos códigos y las cantidades.
Formas de adquisición
Todas las MP se adquieren por cantidades según se requiera.
El aprovisionamiento se activa a través de una orden de compra emitida a los proveedores.
Normas Aplicables
No existe norma alguna que deba cumplir el producto en cuanto a la conformacion que se realiza en nuestro taller. Si hay que regular mediante controles de calidad los semielaborados provenientes del proveedor que realiza el lavado y pintado, ya que al aplicarle pintura epoxi deberá cumplir con la norma ISO 12944 (Protección contra la corrosión de estructuras de acero mediante sistemas de pintura de protección). Dicha norma trata desde ambientes de pintado, hasta forma de aplicacion segun distintos tipos de superficies en las que se encuentre el acero).
A su vez, se aplicara para el control de semielaborados provenientes del proveedor, un control por lotes adecuándose a la norma IRAM 15.
Acondicionamiento del Producto
El producto será entregado en una bolsa de polietileno.
A su vez, para entregas a supermercados, mayoristas, y ferreterías, serán envueltos por un film de polietileno y colocados en cajas de a 6 unidades.
Las medidas de las cajas son 110 cm x 40 cm x 60 cm
Plan de Ensayos
Una vez soldada la mesa y las alas se harán pruebas de tracción y carga (se colocara peso para simular el peso de la ropa mojada colgando) para ver la resistencia y estabilidad del conjunto.
Por otro lado, para el control de los semielaborados provenientes del proveedor que realiza el pintado, se aplicaran controles del tipo anual, mensual y contra entrega de semielaborados.
Con el ensamble final realizado se someterá el tendedero a esfuerzos laterales parar corroborar que mantenga el equilibrio.
Para las pruebas de tracción y carga se realizara el control de todas las unidades, simulando (sobre el mismo puesto de trabajo) el peso del tender completo al 100% de ropa (7,5 KG). Las unidades que no soporten dicha prueba pasaran a formar parte del scrap.
Por otro lado, al proveedor que nos entregara el semielaborado pintado, se le requerirá a nivel anual que presente los certificados del personal de inspección que realice control de los procesos en su planta, así como registros de inspección. A nivel mensual, procedimientos de inspección (llenados de reportes, calibración de equipos, etc) y posibles modificaciones que sufran para contar con los estándares que se están fijando en nuestro producto. Finalmente contra entrega del semielaborado se aplicara el método campana de vació, en el cual se tomara una muestra aleatoria del 25% del lote y se le realizaran pruebas de terminación superficial (acabado, uniformidad de la capa aplicada, igualdad entre toda la muestra tomada), que las realizara el jefe de producción. De no prestar conformidad con la muestra tomada en la primera ocasion, se separan las muestras y se advertirá al proveedor. Si se reitera 2 veces consecutivas dicha desconformidad, se procederá a licitar el servicio de pintado.
Para las pruebas de esfuerzos laterales se tomara aleatoriamente cada media hora (a fin de tener muestras cercana a lo que establece la norma IRAM 15 de 20 subgrupos) 3 tendederos de dos cajas de 6 lista para la venta mayorista, se lo cargara nuevamente como se hizo para la prueba de tracción y carga, y se la aplicaran manualmente esfuerzos de la siguiente manera:
- Esfuerzo normal sobre patas.
- Esfuerzo normal sobre mesa.
- Esfuerzo lateral y normal sobre alas.
En caso de que 2 de los 3 tendederos no soporten las pruebas antes mencionadas (entiéndase por no soportar la caída del tender, la rotura de remaches o soldaduras, o la rotura de cualquier varilla que conforme la mesa) se procederá a descartar ambas cajas ya que no se consideran aptas para la venta.
Definición del Proceso de Producción
Diagrama de flujo de fabricación y control
A continuación, se define el proceso de fabricación de un tendedero con alas:
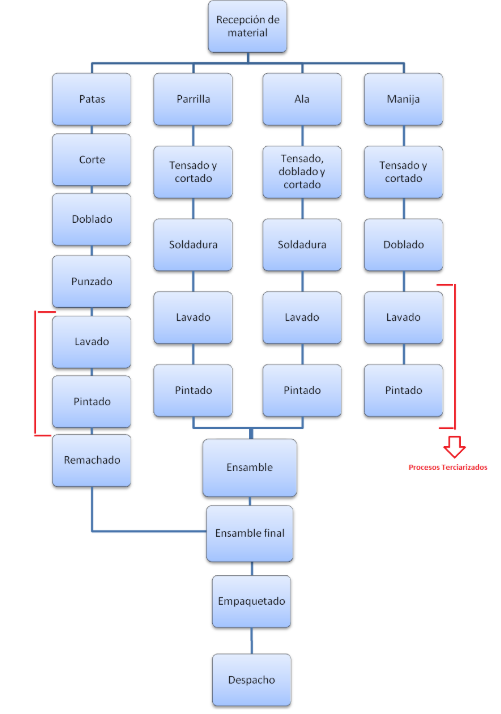
Descripción de cada etapa del proceso productivo
Patas: Se parte de la tira de caño de 5/8” x 0.7 x 6000 mm. Se corta a medida en una cortadora de caño que es una sierra con distintos topes que le dan las distintas medidas. Hay una pata más larga que la otra (ver medidas en el plano). Después se doblan en una dobladora hidráulica o una neumática. Ya dobladas las patas se perforan con una máquina neumática. Después van a pintura. Una vez que las patas están pintadas, se enderezan manualmente hasta que queden derechas, sobre un mismo plano, y no queden reviradas. Se le ponen los regatones en las puntas con un martillo manual, y por último se las remachan entre sí (pata corta con pata larga), con un balancín.
Manija: Entra el alambre en rollo por una máquina que lo endereza, sacándole las tensiones, y lo corta a medida. Luego se le da la forma a la manija con un golpe de balancín. Finalmente se envía pintar.
Mesa: Entra el alambre en rollo por una máquina que lo endereza, sacándole las tensiones, y lo corta a medida. Después se posicionan a mano sobre el marco para darle la forma de mesa y se sueldan en una soldadora de punto. Una vez soldado se envía el subconjunto a pintar.
Ala: Varillas transversales: Al igual que la mesa, se cortan las varillas a medida.
Marco: Con una máquina elaborada a medida en la planta, se endereza el alambre en rollo, se corta y se le da la forma del marco listo para soldar y ensamblar.
Conjunto Ala: Se sueldan las varillas transversales al marco por medio de la soldadora de punto y luego se envía el conjunto a pintar.
Pintura: La pintura de las piezas se realiza con un tercero, quien devuelve las partes listas para continuar con la operación.
Una vez pintadas las partes, se hace el ensamble mesa-alas, donde en una mesa de trabajo se pone la mesa junto con las alas, y con un pistón neumático se le da un golpe a los rulos de las alas para que queden ensambladas. Finalmente se fijan las alas entre sí con alambre.
Ensamble final: Se colocan las patas, la manija y la mesa semi-ensambladas en una máquina fabricada a medida en la planta, donde se le introducen las aranlock en unas cuñas imantadas. Con el accionamiento manual por medio de un pedal, la máquina traba neumáticamente las aranlock en la mesa y la manija, haciendo que queden atrapadas las patas y ya completamente ensamblado el tendedero.
Empaque: Los productos terminados se introducen manualmente en una bolsa y se la sella con una termo selladora.
Determinación de las máquinas e instalaciones. Cálculos
Especificaciones técnicas de las máquinas
A continuación, se detallan las especificaciones técnicas de las maquinas anteriormente mencionadas en los proveedores de tecnología:
- Cortadora de caños:
Cierra circular de banco de 2000 W y conexión a red de 220/240 v y 50 Hz. Hoja de cierra 250mm x 30 mm.
Además de la amoladora de banco, se debe montar la estructura al comienzo donde se depositan los caños de 6000 mm y del otro lado la estructura donde ca el caño cortado.
La misma puede ser corte caño pata larga o corte caño pata corta, para ambas se requiere un puesto de trabajo y por lo tanto un operario, siendo la duración de ambas operaciones de aproximadamente cuarenta y cinco segundos, pudiendo producirse en una jornada laboral de ocho horas 1280 unidades.
Capacidad teórica/hora= 160 patas
2. Dobladora hidráulica para caños y varillas (x2):
Datos técnicos:
*Radio máximo de tubo: 1.5mm. * Procesa estructuras de caño redondo. *Ángulo máximo: 90°. *Velocidad de curvado: 30 segundos. *Producción aproximada: 1 pata por minuto; 2 contorno de ala por minuto; 1 manija en 30 seg.
|
Dimensiones:
*Largo: 1180mm. *Ancho: 460mm. *Alto: 230mm.
|
Capacidad teórica/hora= 60 patas
Capacidad teórica/hora= 120 varillas
3. Perforadora de caños para tubos redondos:
Datos técnicos:
*Espesores has 8mm. *Diámetro de punzonado: 3 a 8 mm. *Regulador de presión. *Producción aproximada: 2 patas cada 1 min. y 20 seg. |
Dimensiones:
*Ancho: 300 mm. *Alto: 400 mm. *Peso: 200 kg. |
A la maquina seleccionada se le agregaran topes según las medidas del caño (al igual que se hizo con la cortadora), para optimizar el proceso y establecer medidas estándar.
Capacidad teórica/hora= 90 patas
4. Tensadora/Cortadora:
Datos técnicos:
*Diámetro de corte: Regulable hasta 10 mm *Material de corte: SAE1020 o dureza similar por minuto, de ser más duro el material, el tiempo varía. *Largo máximo del alambre: 1,5 mts de alambre *Operación: Rectifica la tensión del alambre y corta *Tiempo de operación: 12 segundos. *4 varillas de 5mm y 18 varillas de 3,5mm.
|
Dimensiones:
|
Capacidad teórica/hora= 300 varillas
5. Soldadora de punto:
La soldadura por puntos es un método de soldadura por resistencia que se basa en presión y temperatura, en el que se calienta una parte de las piezas a soldar por corriente eléctrica a temperaturas próximas a la fusión y se ejerce una presión entre las mismas. Se contara con 2 puestos, cada puesto cuenta con una mesada preparada para armar el esqueleto de la mesa y de las alas.
Para el proceso de soldadura de mesa (9 Varillas + contorno) se requiere 1 puesto de trabajo, el cual emplea en la operación aproximadamente 5 segundos por punto con 36 puntos más 30 segundos armado de esqueleto.
Por otra parte, para el proceso de soldadura de mesa (alas, 4 varillas + contorno) se requiere un puesto de trabajo, el cual también emplea aproximadamente 5 segundos por punto con 8 puntos más 20 segundos de esqueleto.
Datos técnicos:
* Potencia máxima 12 Kva. *Máximo soldable – Varilla alternado 12mm. Varilla continuo 9mm. |
Dimensiones:
*Longitud de brazos 400mm. *Regulaciones 5 |
Capacidad teórica/hora= 10,9 mesas (10,9 mesas y 21,8 alas)
6. Martillo Neumático:
Datos técnicos:
Diámetro del pistón: 3 17/32 pulgadas Longitud de carrera: 1 3/4 pulgadas
* Tensión: 220 V * Potencia: 1875 W - 2 5 HP * Velocidad: 2.800 RPM
|
Dimensiones:
*Largo: 1000mm. *Ancho: 0.6m. *Alto: 0.5m.
* Caudal: 203 L/min * Peso: 35 Kg * Capacidad de Tanque: 50 L |
En esta maquina se doblan las puntas de las alas uniéndose con la mesa. La duración de la operación del martillo neumático ronda aproximadamente cincuenta segundos y el mismo es manejado por un solo operario.
Capacidad teórica/hora= 72 mesas
7. Remachadora:
Datos técnicos:
*Motor: 3/4HP *Carrera: 60.2mm *Largo Máximo: 17.1mm |
Dimensiones:
*Largo: 1300mm. *Ancho: 800mm. *Alto: 1250mm. |
La máquina es manejada por un operario, en la misma se emplea aproximadamente 40 segundos en la realización de su tarea.
Capacidad teórica/hora= 90 patas doble.
8. Puesto de ensamblado:
Una vez pintado, se procede al armado. La operación de armado se realiza manualmente, sin embargo, se utiliza una estacion fijadora sobre la cual se ubica el producto semielaborado para así evitar movimientos indeseados.
La operación de ensamble cuadro mesa - alas en martillo neumático (2 por tendedero) requiere de un trabajador el cual emplea aproximadamente cuarenta segundos en la operación.
9. Ensamblador final:
Una vez completo el ensamble cuadro mesa - alas se procede con la segunda parte del ensamble, la del ensamble final del subconjunto (con aranlock), para ello se requiere un puesto de trabajo que emplean en su actividad sesenta segundos siendo su producción en una jornada laboral de ocho horas de 240 unidades.
Capacidad teórica/hora= 30 tendederos.
Medios de fabricacion y control:
- Cierra circular de banco (amoladora + estructura casera para soporte de caños).
- Dobladora hidraulica para caños y varillas.
- Perforadora de caños para tubos redondos.
- Tensadora/Cortadora.
- Soldadora de punto.
- Martillo Neumatico.
- Remachadora.
- Ensamblador final.
Calificacion y formacion de los operadores:
Gerente General: Grado en Ingenieria industrial, Ingles fluido, 5 años de experiencia en funciones similares y capacidad de lidereazgo.
Gerente Comercial: Licenciado en Comercializacion/Ingeniero Industrial/Licenciado en administración de empresas, ingles fluido, 5 años de experiencia en posiciones similares, experiencia en departamentos de compras y en ventas.
Responsable Administratvo y de Finanazas: Grado en administracion de empresas. Experiencia de 3 años en posiciones similares. Conocimientos en logistica y experiencia en procesos de facturacion.
Jefe de Producción: Ingeniero Mecánico, Industrial o de procesos. Experiencia de 5 años en posiciones similares y con personas a cargo. Liderazgo y compañerismo. Experiencia en conducción de equipos de producción.
Operarios: Secundario completo (se valorara titulo técnico) y experiencia comprobable de 2 años en procesos según su función dentro de la linea. Experiencia con cierras de corte, maquinas de punzonado y soldadura de punto.
Ademas, se calificara a el jefe de producción con una capacitación en compras y materiales de la extensión universitaria de la UTN. A su vez, se calificara a los operarios con una certificacion en tecnicas y oficios en aceros y superaleaciones de la extension universitaria de la UTN (para interiorizarse en el tratado del material madre del producto) y se contratara una capacitacion general (que se realizara dentro de la empresa) de la empresa Black&Decker para uso de maquinaria industrial (para operarios que utilicen cortadora, tensadora, soldadora y remachadora.
Para el uso de la dobladora, perforadora y ensamblado se recurrirá a instrucciones del jefe de producción (Ingeniero) con soporte de los manuales de las respectivas maquinas.
Consumo de energía, agua y otros servicios
Por un lado, no es necesario el consumo de gas ya que no se utiliza para el proceso productivo y para los usos de cocina, vestuarios e instalaciones no productivas se dispondrá de maquinaria eléctrica.
Consumo de agua:
Consumo electrico:
Los puestos de ensamblado no requieren de electricidad al igual que la dobladora.
Por ultimo, se contratara un servicio de internet inalambrico para el cual se colocaran 3 routers, uno en la zona de planta, otro en las oficinas y el ultimo en la gerencia general.
Mantenimiento y medios de control. Descripción de los sistemas de seguridad.
Sistemas de Mantenimiento:
Se realizara un mantenimiento preventivo y un control periódico del estado de las maquinas y herramientas de trabajo. Dicho mantenimiento preventivo estara constituido por:
A. Tareas de limpieza general de la planta en forma diaria, como así limpieza particular de cada puesto de trabajo al finalizar el lote de producción (para evitar desvios de eficiencia significativos por material sobrante).
B. Tareas de mantenimiento de maquinaria como lubricacion (para el caso de todas las maquinas), revisión de partes móviles (para todas las maquinas, para evitar la formacion de juegos en los casos donde no son deseados) y afilado de herramientas de corte (para el caso de la cierra circular, la tensadora cortado y la punzonadora). Estas tareas se realizaran cada 2 semanas con ayuda de los operarios y dirigido por el jefe de producción.
A su vez, se realizara un mantenimiento correctivo que estará constituido por tareas como el pintado de paredes, la limpieza de extractores, mantenimiento de la nave industrial, cambio o refacción de luminarias, cambio o refacción de racks, etc.
Teniendo en cuenta el correcto uso de las maquinas y herramientas utilizadas, se brindara a los operarios una capacitación para evitar desgastes por mal uso.
El propio operario, encargado de cada maquina, dará aviso en caso de requerimiento de un mantenimiento antes de lo programado.
Sistemas de seguridad:
Habrá señalización a lo largo de toda la planta sobre los elementos de protección personal requeridos en cada puesto de trabajo. Por esto mismo se brindara un kit con todos los elementos necesarios a cada operario.
Se dispondrá de al menos un matafuego por cada sector de trabajo (caños, varillas, ensamble, almacenes, oficinas, etc).
Capacitación al operario sobre el correcto uso de cada elemento de trabajo.
Sendas de circulación peatonal para desplazarse por la planta. Así como senderos de circulación para zorras y carros de carga.
Se designara un piloto de seguridad encargado de controlar que el resto de sus compañeros cumplan con todas las normas de seguridad.
Ejercicios 1 a 5 de la guía de Trabajos Prácticos
Archivo:G7 DT - Ejercicios 1-5.xlsx
1)
2)
3)
4) Aprovechamiento Seccional:
5) Cuello de botella:
Como se puede observar en el cuadro del punto cuatro, el aprovechamiento seccional más alto se encuentra en el Operario E (que además de ser el encargado del ensamble y empaquetado final de todos los subconjuntos, dará soporte al puesto de soldadura). Por ende, el cuello de botella se encuentra en esta sección.
Determinación de la evolución de las mercaderías
Tiempos de entrega y envío de mercadería
Los tiempos de entrega de pedidos dependen del cliente.
Se realizarán de manera quincenal para el caso de distribuidoras, supermercados, mayoristas y ferreterías.
Para enviar los pedidos hay dos posibilidades, que el cliente retire el pedido en la planta por sus propios medios, la segunda consiste en el envío a través de un operador logístico que será a cargo de la empresa si es que supera el pedido mínimo (15 cajas).
En caso de que surjan demandas espontaneas se podrá satisfacer las necesidades enviando contratando mas fletes.
Tamaño y frecuencias de compra
Las ventas del año 1: 14.100
Las ventas del año 2 a 5: 22.600
El aprovisionamiento de las materias primas sera de manera semanal.
Entonces, se deberá contar con los siguientes insumos tos los comienzos de semana:
El mecanismo para solicitarles la mercadería a los proveedores es a través de ordenes de compra.
Cálculos de los ejercicios 6 a 11 de la guía
Archivo:Ejs 6 11nuevo.xlsx Cabe destacar que todos los cálculos se efectuaran en base a cantidades de producto final, las relaciones con el BOM fueron previamente descritas.
El calculo de la capacidad del sistema parte de las estimaciones de ventas del proyecto.
6) EVOLUCIÓN DE LA PRODUCCIÓN
a) Volumen de producción mensual en estado de régimen (promedio): se tienen en cuenta 285 días laborales en el año (el resto, vacaciones, fines de semana, feriados, se distribuyen a lo largo del año linealmente), resultando así un valor mensual promedio de:
b) Volumen de la producción durante el periodo de puesta en marcha:
Es necesario analizar el nivel de producción durante el periodo de puesta en marcha y ver si las capacidades antes determinadas, satisfacen la demanda del primer año.
c) Capacidad de producción durante el resto del 1er año: 12 meses – 3 meses = 9 meses
1833,33 unidades / mes * 9 meses = 16.500
d) Capacidad de producción en el año 1 = 1506,67+ 16.500 = 18006,67
Se precisan producir las unidades a vender y el stock promedio, durante los primeros 3 meses se producirán 1506,67 y el resto del año 12.811 (sale de ventas+ stock prom (7b) - producción 3 meses(6b) )
e) Volumen de producción del año 2 al 5 = 22.600
7) STOCK PROMEDIO DE PRODUCTO ELABORADO
a) Volumen de producción semanal promedio, en estado de régimen:
b) El stock promedio de elaborado varia entre 0 y 434,61 por semana.
Entonces el Stock promedio es 217,3 unidades
Aunque la capacidad de producción sea 18006,67, se producirán 14.317,61 tendederos durante el primer año (ventas + stock promedio)
8) EVOLUCIÓN DE LAS VENTAS DURANTE LA VIDA ÚTIL DEL PROYECTO
Fueron previamente determinadas a partir de un estudio de mercado.
(La producción es determinada en función del plan de ventas)
9) CONSUMO DE MATERIA PRIMA PARA EL PROGRAMA DE PRODUCCIÓN Y FORMACIÓN DE LA MERCADERÍA EN CURSO Y SEMIELABORADA.
En el año 1 el consumo de materia prima esta destinada a la producción realizada y a la formación de mercadería en curso.
a) Consumo de materia prima para realizar la producción del 1er año:
Se multiplica la producción deseada por un factor de desperdicio propio del año 1.
-En los 1eros 3 meses (puesta en marcha) (6b): 1,1 * 1506,67 = 1.657,34 unidades
-En los 9 meses restantes (14.100 u - 7b - 6b): 1,05 * 12.811 = 13.451,5 unidades
Se debe multiplicar el listado de componentes (BOM) por la cantidad de tendederos necesarios: 15.108,84 (1.657,34 + 13.451,5).
-Volumen de la producción realizada en el año 1 = 14.317,3 unidades
-Desperdicio no recuperable: 791,5 unidades
b) Consumo de materia prima en la mercadería en proceso:
-volumen de materia prima requerido: la alimentación de proceso durante el ciclo de elaboración.
Se tiene en cuenta que son 6 turnos de 8 hs por semana,en total hay 48 hs en las que se producen 434,62 tendederos.
En promedio el ciclo de elaboración del tendedero es de 0 ,11 hs.
Entonces: 22.600 * 0,11 hs / (285 días * 8 hs/dia) = 1,1 unidad (se multiplica por el Bom)
c) Consumo total de materia prima en el año 1:
-Para los productos elaborados: 15.108,84 unidades
-Para la mercadería en curso y semi elaborados: 1,1 unidad
-Consumo total de materia prima año 1: 15.110 unidades
Año 2 al 5: el consumo de materia prima es exclusivamente destinado a la producción cada año: 22.600 unidades de tendederos.
10) STOCK PROMEDIO DE MATERIAS PRIMA Y PROGRAMA DE COMPRAS
En estado de régimen sera (en unidades)
a)El stock mínimo es la mitad de producción de una semana (217,3 unidades).
b) variación del stock de materia prima durante el año y programa de compras:
11)CUADRO RESUMEN DEL PROGRAMA GENERAL DE EVOLUCIÓN
(en el periodo de instalación se compra la MP necesario para la puesta en marcha)
Determinación del personal
Organigrama de toda la empresa
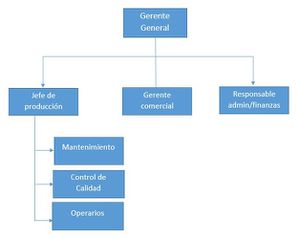
Descripción de los puestos de trabajo
Gerente General: Representante de la empresa para asuntos externos, determinación (en conjunto con gerentes) y aprobación de objetivos generales, control de los distintos sectores y principal allegado a los inversores.
Gerente Comercial: Responsable principal de ventas y compras, contacto con proveedores, control de cumplimiento del plan de ventas y analisis de desvios, encargado de canales de venta y comunicacion del producto. Reporta al Gerente general.
Responsables Administrativo y de Finanzas: Encargado de la facturación, seguimiento contable, y coordinación logística (seguimiento de pedidos e ingresos/egresos de producto terminado a nivel documental). Responsable de pagos y cobros. Reporta al Gerente general.
Jefe de producción: Responsable del cumplimiento del plan de producción, disponibilidad de materias primas y mantenimiento de la maquinaria. Coordinador de equipos de trabajo y lineamientos a los 5 operarios. Reporta directamente al Gerente general. 5 operarios a cargo.
Operarios:
Operario A: Encargado del corte, el doblado y el punzonado de caños. Responsable de carga de materia prima al puesto de trabajo. El semielaborado se entraga a un proceso de terceros (pintado). Reporta directamente al Jefe de produccion.
Operario B: Encargado del corte y tensado de varillas de alambre. Responsable de carga de materia prima al puesto de trabajo. El semielaborado es entregado a otro puesto dentro del mismo proceso productivo (soldadura). Reporta directamente al Jefe de produccion.
Operario C: Encargado del doblado de varillas de alambre para la posterior formacion de la mesa. El semielaborado es entregado a otro puesto dentro del mismo proceso productivo (soldadura). Reporta directamente al Jefe de produccion.
Operario D: Encargado de la soldadura de semielaborados de varillas de alambre. El semielaborado es entregado a un proceso que se realiza por terceros (pintado). Reporta directamente al Jefe de produccion.
Operario E: Encargado del ensamble final y empaquetado del producto. Recibe los semielaborados desde un proceso de terceros. Control de entrada de mercaderias (calidad del pintado) con soporte del Jefe de produccion. Reporta directamente al Jefe de produccion.
Equipos auxiliares, muebles y útiles
Plano de Planta
•Fábrica: 46.0m x 30.0m (3 lotes de 46.0m x 10.0m)
•Depósito PT: 14.0m x 2.5m
•Depósito SE: 14.0m x 3.5m
•Depósito MP rollos: 10.0m x 3.0m
•Depósito MP caños: 20.0m x 4.0m
•Depósito Insumos: 7.5m x 4.0m
•Depósito Patas: 7.0m x 9.0m
•Depósito Mesa y Alas: 7.0m x 7.5m
•Vestuario 7.0m x 10.0m (con baño de 4.0m x 4.0m)
•Oficina: 9.0m x 3.0m
•Sala de reunión: 5.5m x 3.0m
•Cocina comedor: 3.5m x 3.0m
•Baño: 3.0m x 3.5m
Plano del recorrido de los materiales
Cronograma de ejecución
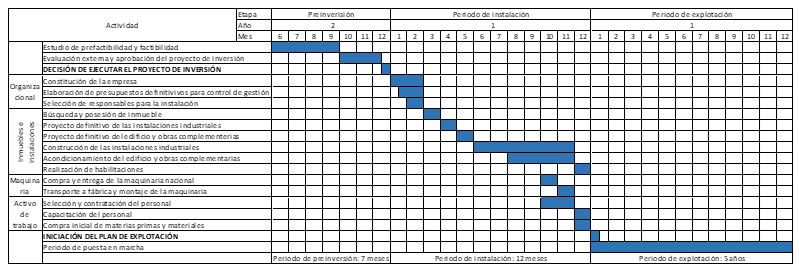