Diferencia entre revisiones de «2023/Grupo3/DimensionamientoFisico»
Línea 9: | Línea 9: | ||
=== Planos y Dibujos. === | === Planos y Dibujos. === | ||
[[Archivo:Barra.jpg|200x200px|sinmarco]] | |||
=== Listado de Materiales === | === Listado de Materiales === |
Revisión del 13:40 6 jul 2023
Determinación de la Localización
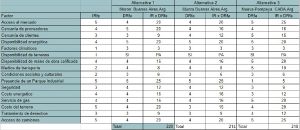
De acuerdo a los cálculos realizados en la matriz de localización, concluimos que la mejor alternativa para ubicar nuestras instalaciones es en el barrio de Morón, Provincia de Buenos Aires, ya que es la ubicación más cercana a nuestros proveedores. Además, la zona cuenta con un parque industrial cercano a la autopista de acceso oeste, lo que facilita la llegada de los camiones que cargan materias primas, semielaborados y productos terminados, así como también de medios de transporte público para los operarios. El hecho de que haya un parque industrial le permite a la empresa ahorrar en la inversión de la infraestructura base como redes de alta tensión, red de gas de alto consumo, redes pluvio-cloacales preparadas para uso industrial y redes de fibra óptica para conexiones de alta velocidad. Estos espacios también ofrecen una mayor seguridad física, industrial y sanitaria, tienen acceso a créditos con tasas preferenciales, otorgan una infraestructura compartida, fomenta la colaboración y facilita el intercambio de conocimientos y recursos entre empresas y cuentan con exenciones impositivas y de servicios, como los impuestos de Ingresos Brutos, Inmobiliarios, Sellos, Automotores y Tasas Municipales.
Definición Técnica del Producto.
Planos y Dibujos.
Listado de Materiales
Especificaciones Técnicas.
Normas Aplicables.
Características condición del Producto.
Plan de Ensayos.
Acondicionamiento del Producto
Definición del Proceso de Producción.
Diagrama de Flujo de Fabricación y Control y Cursogramas gráficos o analíticos.
Descripción de cada etapa del proceso productivo.
Determinación de las máquinas e instalaciones. Cálculos.
Especificaciones técnicas de las máquinas
El producto requerirá de diversas máquinas para desarrollarse y cada una cumplirá una función específica, tenemos:
Máquina | Parámetro | Detalle |
Tolva | Capacidad | 800 kg |
Material | Acero inoxidable | |
Dimensiones | 1200*1200*1600 mm | |
Accesorio | Balanza | |
Batidor | Capacidad | 100 L / h |
Voltaje | 220 V | |
Calefacción | a gas o eléctrico | |
Potencia | 9 KW | |
Dimensiones | 900*600*1500 mm | |
Olla industrial | Capacidad | 50 L / h |
Accesorio | Pala para agitar | |
Potencia | 0.37 KW | |
Voltaje | 220 V | |
Moleadora | Capacidad | 0,25-0,375 Toneladas / h |
Voltaje | 380 V | |
Potencia | 2.2 KW | |
Medidas | 9800*1200*1200 mm | |
Bañadora | Capacidad | 90 KG / h |
Voltaje | 380 V | |
Potencia | 1,6 KW | |
Accesorio | Sistema de refrigeración de 1100 frigorías / h | |
Envolvedora | Capacidad | 16800 Paquetes / h |
Longitud de embalaje | 70 - 360 mm | |
Altura máxima | 70 mm | |
Voltaje | 220 V | |
Potencia | 2,5 KW | |
Dimensiones | 4400*1050*1600 mm | |
Material de envoltura | CPP/PET + CPP/BOPP |
Las capacidades no son comparables debido a que las unidades que tratan no se pueden tratar en el mismo plano, con lo cual resulta indispensable convertirlas de modo que podamos efectuar la comparación:
Máquina | Capacidad en barras / h |
Batidor (1) | 15500 |
Olla industrial (2) | 69767 |
Moleadora (3) | 8721 |
Bañadora (4) | 20930 |
Envolvedora | 16800 |
Cálculos asociados:
- 1000 L de cereales = 520 KG de cereales (520 KG/M3)
Una barra posee un 78% de este componente y la barra pesa 43 g
Entonces se consiguen: 15500 barras / h
- 50 L de almíbar = 60 Kg de almíbar (1200 KG/M3)
Una barra posee un 2% de almíbar
Entonces se consiguen: 69767 barras / h
- Tomando la capacidad de 0,375 toneladas / h
Para una hora se obtiene: 8721 barras / h
- Una barra posee un 10 % de cacao
Entonces se consiguen: 20930 barras / h
La tolva no se convierte a barras por hora debido a que estará constantemente llenándose y no puede comportarse como cuello por su gran capacidad de almacenamiento. Téngase en cuenta que si bien hay más componentes que integran a la barra, muchos de ellos tales como la raíz de achicoria, las almendras, nueces, castañas y demás se agrupan dentro de los llamados cereales. Por otra parte ingredientes como los arándanos o la proteína texturizada de soja no resultan influyentes en los cálculos con lo cual pueden despreciarse
Consumos de energía, agua y otros servicios.
Mantenimiento y medios de control
Descripción de los sistemas de seguridad
Cálculos y estimaciones
Balance anual de material y producción seccional
Para simplificar los cálculos, tomaremos los valores de producción en toneladas anuales, con lo cual en régimen:
Producción anual en régimen = [50.000.000 barras x (43 gramos/barra/1000 gramos/kg)]/1000 kg/Tn = 2.150 Tn/año
Producción anual en régimen = 2.150 Tn/año
Luego es necesario establecer el desperdicio seccional, considerando las etapas del proceso mencionadas anteriormente como las áreas por las que pasará el producto determinaremos tanto el desperdicio recuperable como no recuperable en cada una de ellas. Cabe aclarar que etapas como la recepción de materias primas o enfriamiento de las barras bañadas se descartan de este análisis por carecer de desperdicios, entonces tenemos:
Secciones | Desperdicios (t/año) | |
Recuperables | No recuperables | |
Mezclado de sólidos (1) | 20 | 10 |
Calentamiento y mezclado de líquidos (2) | 0 | 10 |
Incorporación de líquidos y sólidos (3) | 35 | 10 |
Disposición de la mezcla en cinta transportadora (4) | 0 | 5 |
Laminación y corte (5) | 0 | 100 |
Baño de chocolate (6) | 0 | 20 |
Empaquetado y embalaje (7) | 50 | 15 |
Notar que los valores son aproximados, sin embargo los mayores problemas se presentan en la laminación y corte, donde ocurre que la masa pastosa no llega a cubrir el ancho de la cinta transportadora de modo que al efectuar los cortes quedan barras imperfectas en algunos sectores. A su vez un problema recurrente es el envoltorio automático efectuado por la envolvedora, sin embargo en la mayoría de los casos se puede reingresar la barra a la máquina para repetir el proceso.
Por otro lado, los otros desperdicios suelen explicarse por el remanente de materia prima en los conductos o elementos que hacen contacto con estas, sobre todo una vez que se mezclan los líquidos con los sólidos y la probabilidad de que cierta parte se adhiera a las paredes es mayor. O por el contrario productos descartados durante el control de calidad.
Retomando ahora con los cálculos tenemos que:
Secciones | Alimentación | Desperdicios | Producciones seccionales | |
Recuperables | No recuperables | |||
1 | 2.425 | 20 | 10 | 2.395 |
2 | 2.395 | 0 | 10 | 2.385 |
3 | 2.385 | 35 | 10 | 2.340 |
4 | 2.340 | 0 | 5 | 2.335 |
5 | 2.335 | 0 | 100 | 2.235 |
6 | 2.235 | 0 | 20 | 2.215 |
7 | 2.215 | 50 | 15 | 2.150 |
Totales | 2.425 | 105 | 170 | 2.150 |
Los procesos faltantes en el cuadro no poseen desperdicios mensurables e influyentes en el proceso. De este cuadro podemos obtener la relación de cuántas toneladas de producto terminado deben ingresar y egresar para producir 2.150 toneladas al año, concretamente se requiere de 2.425 toneladas para obtener dicho número, sin embargo el consumo real de materia prima no considera aquellos desperdicios recuperables, por lo tanto el consumo será de: 2.320 toneladas.
Luego como información adicional podemos indicar el porcentaje de desperdicio operativo y real, donde este último solo considera el no recuperable que efectivamente no sirve más:
- Porcentaje de desperdicio operativo:
(105 + 170) / 2.150 x 100 = 12,80 %
- Porcentaje de desperdicio real:
170 / 2.150 x 100 = 7,90 %
Notar que todos los valores están calculados en función de la producción y no de la alimentación del proceso.
Ritmo de trabajo
Posteriormente nos interesará calcular el ritmo de trabajo para el cual necesitaremos determinar la modalidad de trabajo:
- Dos equipos de trabajo
- Siete días a la semana
- Dos turnos diarios de nueve horas
Consideramos quince días de vacaciones y diez días de feriados obligatorios. Con esto en cuenta podemos determinar las horas activas al año de las máquinas:
- Horas activas/ año-maquina = (365 días - 25 días) x 18 hs/día
Horas activas/año-maquina = 6.120 horas
Así como también el ritmo de trabajo de cada operario:
- Horas activas/ año-operario = 6.120 horas / 2 equipos
Horas activas/ año-operario = 3.060 horas
Capacidad real anual de la maquinaria
Ahora nos dedicaremos a calcular la capacidad real anual de la maquinaria para cada sección operativa, para esto necesitaremos las capacidades teóricas de las máquinas calculadas anteriormente así como su rendimiento, el cual consideraremos estándar entre 75 y 90%. Armamos entonces la siguiente tabla:
Máquinas | Capacidad teórica/hora | Horas activas/año | Capacidad teórica anual | Rendimiento operativo | Capacidad real anual |
Batidor | 0,665 | 6.120 | 4.069,8 | 0,80 | 3.255,85 |
Olla industrial | 0,76 | 6.120 | 4.651,2 | 0,75 | 3.488,40 |
Moldeadora | 0,375 | 6.120 | 2.295,0 | 0,90 | 2.065,50 |
Bañadora | 0,900 | 6.120 | 5.508,0 | 0,80 | 4.406,40 |
Envolvedora | 0,7224 | 6.120 | 4.421,1 | 0,80 | 3.556,88 |
Téngase en cuenta que las capacidades están calculadas como toneladas de producto terminado por hora y no cantidad de barras por hora, eso explica la diferencia de valores con lo previamente esquematizado.
Cantidad de máquinas operativas por sección y aprovechamiento seccional
Ahora que establecimos las capacidades debemos saber cuántas máquinas necesitaremos en cada etapa para asegurar que pueda cumplirse con el plan de ventas. Cabe destacar que para hacer esto debemos relacionar los cálculos de las secciones con las capacidades de las máquinas, como estas solo se encuentran en algunas secciones filtraremos el cálculo a aquellas áreas en las que actúen las máquinas únicamente, entonces:
Sección | Programa anual de producción | Capacidad real anual | Cantidad necesaria de máquinas | Capacidad real de sección | Aprovechamiento seccional (%) |
1 | 2.395 | 3.255,85 | 1 | 3.255,85 | 73,56 |
2 | 2.385 | 3.488,40 | 1 | 3.488,40 | 68,37 |
3 | 2.340 | 3.255,85 | 1 | 3.255,85 | 71,87 |
5 | 2.235 | 2.065,50 | 2 | 4.131 | 54,10 |
6 | 2.215 | 4.406,40 | 1 | 4.406,40 | 50,26 |
7 | 2.150 | 3.556,88 | 1 | 3.556,88 | 60,44 |
Recordar que:
- Mezclado de sólidos (1) : utiliza batidor
- Calentamiento y mezclado de líquidos (2): utiliza olla industrial
- Incorporación de líquidos y sólidos (3): utiliza el mismo modelo de batidor que el proceso 1, por eso las capacidades son iguales.
- Disposición de la mezcla en cinta transportadora (4): utiliza moldeadora
- Laminación y corte (5): utiliza moldeadora
- Baño de chocolate (6): utiliza bañadora
- Empaquetado y embalaje (7): utiliza envolvedora
Tener en cuenta que los volúmenes de producción indicados en esta tabla y en el resto de los cálculos refieren al producto terminado, lo cual es lógico ya que no todas las materias primas tienen su unidad de medida básica en toneladas o alguna equivalente.
Cuello de botella del proceso productivo
Finalmente tomando como parámetro definitorio al aprovechamiento seccional, podemos decir que el cuello de botella se ubica en el proceso de mezclado de sólidos donde se emplea el batidor.