Diferencia entre revisiones de «2019/Grupo4/DimensionamientoFisico»
Línea 1: | Línea 1: | ||
== Determinación de la Localización == | == Determinación de la Localización == | ||
Para decidir la localización de la planta productiva, lo primero que hacemos es analizar si existen factores restrictivos. En nuestro proyecto, los factores más importantes a tener en cuenta son la disponibilidad de los servicios requeridos (principalmente agua y electricidad), así como la cercanía a los puntos de ventas. Con respecto a este punto, resulta muy conveniente seleccionar un lugar cercano a parques industriales o a Capital Federal, por lo que nos enfocaremos en este tipo de localizaciones. La planta junto a las oficinas administrativas, depósitos y demás requieren un gran espacio, de aproximadamente 22000m2, por lo que el precio por metro cuadrado y disponibilidad de espacios tan grandes son cruciales para decidir el lugar donde ubicar al proyecto. Aparte de estos puntos, no existen grandes restricciones que impidan ubicar el proyecto, pero si hay otros factores que influyen en la decisión, como los muestra la siguiente matriz: | Para decidir la localización de la planta productiva, lo primero que hacemos es analizar si existen factores restrictivos. En nuestro proyecto, los factores más importantes a tener en cuenta son la disponibilidad de los servicios requeridos (principalmente agua y electricidad), la disponibilidad de grandes terrenos, así como la cercanía a los puntos de ventas. Con respecto a este punto, resulta muy conveniente seleccionar un lugar cercano a parques industriales o a Capital Federal, por lo que nos enfocaremos en este tipo de localizaciones. La planta junto a las oficinas administrativas, depósitos y demás requieren un gran espacio, de aproximadamente 22000m2, por lo que el precio por metro cuadrado y disponibilidad de espacios tan grandes son cruciales para decidir el lugar donde ubicar al proyecto. Aparte de estos puntos, no existen grandes restricciones que impidan ubicar el proyecto, pero si hay otros factores que influyen en la decisión, como los muestra la siguiente matriz: | ||
=== <u>Matriz de localización:</u> === | === <u>Matriz de localización:</u> === | ||
Línea 9: | Línea 9: | ||
!Pilar | !Pilar | ||
!San Martín | !San Martín | ||
!Capital Federal | |||
|- | |- | ||
|Disponibilidad de grandes terrenos | |Disponibilidad de grandes terrenos | ||
| | |Necesario | ||
| | |si | ||
| | |si | ||
| | |si | ||
|no | |||
|- | |- | ||
|Disponibilidad de servicios (luz y agua) | |Disponibilidad de servicios (luz y agua) | ||
Línea 21: | Línea 23: | ||
|10 | |10 | ||
|9 | |9 | ||
| - | |||
|- | |- | ||
|Cercanía materia prima | |Cercanía materia prima | ||
Línea 27: | Línea 30: | ||
|5 | |5 | ||
|9 | |9 | ||
| - | |||
|- | |- | ||
|Precio m2 | |Precio m2 | ||
Línea 33: | Línea 37: | ||
|10 | |10 | ||
|3 | |3 | ||
| - | |||
|- | |- | ||
|Cercanía mercado comprador | |Cercanía mercado comprador | ||
Línea 39: | Línea 44: | ||
|8 | |8 | ||
|6 | |6 | ||
| - | |||
|- | |- | ||
|Recursos humanos especializados | |Recursos humanos especializados | ||
Línea 45: | Línea 51: | ||
|6 | |6 | ||
|8 | |8 | ||
| - | |||
|- | |- | ||
|Impuestos | |Impuestos | ||
Línea 51: | Línea 58: | ||
|9 | |9 | ||
|6 | |6 | ||
| - | |||
|- | |- | ||
|'''Total''' | |'''Total''' | ||
| | | | ||
| | |423 | ||
| | |420 | ||
| | |317 | ||
| - | |||
|} | |} | ||
La ubicación de Capital Federal la descartamos puesto que se dificulta conseguir grandes terrenos, la cual es una característica indispensable para el proyecto. Por eso no analizamos el resto de los factores para esta localización. El resto del análisis lo hacemos entonces para las 3 localidades restantes. | |||
Aclaraciones: Con respecto a la cercanía a la materia prima, la mayor parte del cartón necesario para ser reciclado se recolecta primero en Capital Federal y GBA, por lo que San Martín es el lugar más cercano, seguido por Pacheco y luego Pilar. Por otro lado, nuestros principales clientes son productores industriales, siendo que Pacheco y Pilar poseen ambos una gran cercanía con nuestros potenciales clientes, mientras que San Martín es el más alejado de los 3. | Aclaraciones: Con respecto a la cercanía a la materia prima, la mayor parte del cartón necesario para ser reciclado se recolecta primero en Capital Federal y GBA, por lo que San Martín es el lugar más cercano, seguido por Pacheco y luego Pilar. Por otro lado, nuestros principales clientes son productores industriales, siendo que Pacheco y Pilar poseen ambos una gran cercanía con nuestros potenciales clientes, mientras que San Martín es el más alejado de los 3. | ||
Línea 1134: | Línea 1145: | ||
=== Organigrama de toda la empresa === | === Organigrama de toda la empresa === | ||
[[Archivo:Organigrama cajas.jpg|miniaturadeimagen|784x784px|Organigrama|alt=|centro]] | [[Archivo:Organigrama cajas.jpg|miniaturadeimagen|784x784px|Organigrama|alt=|centro]]Aclaración: hay un gerente por cada área, mientras que para los supervisores, operarios y conductores en el organigrama están colocados las cantidades requeridas por turno (3 turnos). Los vendedores, el encargado de compras y el personal administrativo trabajan solo en un turno. Abajo se detallan la cantidad de personas que posee cada área, así como la distribución por turnos de cada puesto. | ||
=== Descripción de los Puestos de Trabajo === | === Descripción de los Puestos de Trabajo === | ||
<u>Área de calidad:</u> puestos: | <u>Área de calidad:</u> (7 personas) puestos: | ||
* Gerente de calidad, que es el encargado de determinar el tipo de ensayos que se debe realizar sobre las distintas partes del proceso, así como determinar los controles sobre los efluentes, y verificar que se cumpla con la normativa vigente. Debe revisar periódicamente que el producto se encuentre dentro de los límites de calidad determinados. El gerente de calidad trabaja 8 horas por día, 5 días a la semana. El gerente de calidad debe tener la formación en química y física suficiente (por ejemplo, ser ingeniero químico) para poder determinar los ensayos adecuados a realizar, y debe conocer profundamente el producto. | * Gerente de calidad, que es el encargado de determinar el tipo de ensayos que se debe realizar sobre las distintas partes del proceso, así como determinar los controles sobre los efluentes, y verificar que se cumpla con la normativa vigente. Debe revisar periódicamente que el producto se encuentre dentro de los límites de calidad determinados. El gerente de calidad trabaja 8 horas por día, 5 días a la semana. El gerente de calidad debe tener la formación en química y física suficiente (por ejemplo, ser ingeniero químico) para poder determinar los ensayos adecuados a realizar, y debe conocer profundamente el producto. | ||
* Operario de ensayos, los cuales son 2. Su tarea consiste en hacer los ensayos de calidad determinados por el gerente de manera regular, verificando el estado del producto, para así asegurar que se trabaje dentro de los límites establecidos. Trabajan 8 horas diarias, 5 días a la semana. Los turnos se distribuyen de manera tal que cada día al menos un operario haya estado, y que sus turnos no coincidan. Las calificaciones requeridas para este puesto son conocimientos en física y química suficiente para poder interpretar los resultados de manera correcta, y determinar las causas por las cuales pueden producirse los desvíos. Deben recibir capacitación en el uso de los aparatos de medición utilizados para los ensayos. | * Operario de ensayos, los cuales son 2. Su tarea consiste en hacer los ensayos de calidad determinados por el gerente de manera regular, verificando el estado del producto, para así asegurar que se trabaje dentro de los límites establecidos. Trabajan 8 horas diarias, 5 días a la semana. Los turnos se distribuyen de manera tal que cada día al menos un operario haya estado, y que sus turnos no coincidan. Las calificaciones requeridas para este puesto son conocimientos en física y química suficiente para poder interpretar los resultados de manera correcta, y determinar las causas por las cuales pueden producirse los desvíos. Deben recibir capacitación en el uso de los aparatos de medición utilizados para los ensayos. | ||
<u>Área de producción:</u> | En el área de calidad entonces se tiene para los 3 turnos un total de 1 gerente y 6 operarios. | ||
<u>Área de producción:</u> (52 personas) | |||
* Es dirigida por el gerente de producción, quien supervisa que se trabaje de acuerdo al plan de producción estipulado, desarrolla e implementa las mejoras necesarias, revisa que el proceso se desarrolle en forma adecuada, y sirve como nexo entre las distintas áreas de la empresa, así como en las áreas de producción, las cuales son dos: papel y cartón. Trabaja 8 horas diarias, 6 días a la semana. El gerente debe tener competencias en la planificación y control de la producción, y ser de preferencia un ingeniero industrial o haber estudiado una carrera afín. También se necesita tener experiencia en la industria del papel y el cartón. | * Es dirigida por el gerente de producción, quien supervisa que se trabaje de acuerdo al plan de producción estipulado, desarrolla e implementa las mejoras necesarias, revisa que el proceso se desarrolle en forma adecuada, y sirve como nexo entre las distintas áreas de la empresa, así como en las áreas de producción, las cuales son dos: papel y cartón. Trabaja 8 horas diarias, 6 días a la semana. El gerente debe tener competencias en la planificación y control de la producción, y ser de preferencia un ingeniero industrial o haber estudiado una carrera afín. También se necesita tener experiencia en la industria del papel y el cartón. | ||
Papel: puestos: | Papel: puestos: | ||
Línea 1151: | Línea 1164: | ||
* Operario de impresión y empaquetado, tiene como tarea abastecer a las impresoras de las planchas de cartón corrugado, recibir las cajas impresas y embalarlas. También tienen que recargar las impresoras con tinta. Trabajan 3 operarios por turno en forma alternada. No se requiere tener experiencia previa ni conocimientos particulares para este puesto debido a que se brindará la capacitación necesaria. | * Operario de impresión y empaquetado, tiene como tarea abastecer a las impresoras de las planchas de cartón corrugado, recibir las cajas impresas y embalarlas. También tienen que recargar las impresoras con tinta. Trabajan 3 operarios por turno en forma alternada. No se requiere tener experiencia previa ni conocimientos particulares para este puesto debido a que se brindará la capacitación necesaria. | ||
* Conductor de clark, tiene como tarea transportar en un clark las bobinas de papel desde el área de papel hasta los depósitos, desde allí hasta el área de cartón (corrugadora), y finalmente desde las impresoras hasta el depósito de producto terminada. Trabaja un operador por turno en forma alternada. Para este puesto se requiere tener un certificado habilitante para conducir el clark. | * Conductor de clark, tiene como tarea transportar en un clark las bobinas de papel desde el área de papel hasta los depósitos, desde allí hasta el área de cartón (corrugadora), y finalmente desde las impresoras hasta el depósito de producto terminada. Trabaja un operador por turno en forma alternada. Para este puesto se requiere tener un certificado habilitante para conducir el clark. | ||
<u>Área de ventas y transporte:</u> puestos: | En el área de producción entonces se tiene para los 3 turnos un total de 1 gerente, 6 supervisores y 45 operarios (incluyendo a los operadores de clark). | ||
<u>Área de ventas y transporte:</u> (12 personas) puestos: | |||
* Gerente de ventas y transporte: tiene como tareas revisar el plan de ventas, buscar y negociar tratos con nuevos clientes, evaluar el estado de las ventas, verificar la capacidad de entrega de la empresa, coordinar con el área de producción que se pueda cumplir con las ventas realizadas, coordinar las entregas a los clientes. Trabaja 8 horas al día, 6 días a la semana. Para este puesto es preferente contar con una carrera de marketing, administración de empresas o afines. | * Gerente de ventas y transporte: tiene como tareas revisar el plan de ventas, buscar y negociar tratos con nuevos clientes, evaluar el estado de las ventas, verificar la capacidad de entrega de la empresa, coordinar con el área de producción que se pueda cumplir con las ventas realizadas, coordinar las entregas a los clientes. Trabaja 8 horas al día, 6 días a la semana. Para este puesto es preferente contar con una carrera de marketing, administración de empresas o afines. | ||
* Vendedor: sus tareas son buscar y captar nuevos clientes para la empresa, ya sea de producto terminado (cajas de cartón) como de subproducto (bobinas de papel defectuosas con valor comercial). También tienen como tarea responder ante los clientes. Hay 2 vendedores, y trabajan 8 horas al día, 5 días a la semana. No se requiere una carrera para este puesto, pero es preferente contar con experiencia en ventas | * Vendedor: sus tareas son buscar y captar nuevos clientes para la empresa, ya sea de producto terminado (cajas de cartón) como de subproducto (bobinas de papel defectuosas con valor comercial). También tienen como tarea responder ante los clientes. Hay 2 vendedores, y trabajan 8 horas al día, 5 días a la semana. No se requiere una carrera para este puesto, pero es preferente contar con experiencia en ventas | ||
* Conductor: Se encarga de manejar los camiones para transportar el producto terminado a los clientes. Hay 3 conductores, | * Conductor: Se encarga de manejar los camiones para transportar el producto terminado a los clientes. Hay 3 conductores por turno, teniendo los 3 turnos. Sin embargo los turnos de trabajo varían según el recorrido que se deba hacer hasta llegar al cliente. Se requiere una licencia de conducir profesional para este puesto. | ||
<u>Área administrativa:</u> puestos: | En el área de ventas y transporte entonces se tiene 1 gerente, 2 vendedores y 9 conductores. | ||
<u>Área administrativa:</u> (7 personas) puestos: | |||
* Gerente administrativo: se encarga de verificar que se cumplan con los lineamientos administrativos necesarios, incluyendo la gestión de pagos, cobranzas, situación contable, entre otros. Trabaja 8 horas al día, 5 días a la semana. Para este puesto es preferente contar con una carrera de administración de empresas, contabilidad o afines. | * Gerente administrativo: se encarga de verificar que se cumplan con los lineamientos administrativos necesarios, incluyendo la gestión de pagos, cobranzas, situación contable, entre otros. Trabaja 8 horas al día, 5 días a la semana. Para este puesto es preferente contar con una carrera de administración de empresas, contabilidad o afines. | ||
* Personal administrativo: Se encargan de organizar la gestión de pagos y cobranzas, atención al consumidor, pago de impuestos, entre otras tareas administrativas. Son 6 empleados, que trabajan 8 horas al día, 5 días a la semana. No se requiere una carrera para este puesto, pero es preferente tener una carrera en contabilidad o afines. | * Personal administrativo: Se encargan de organizar la gestión de pagos y cobranzas, atención al consumidor, pago de impuestos, entre otras tareas administrativas. Son 6 empleados, que trabajan 8 horas al día, 5 días a la semana. No se requiere una carrera para este puesto, pero es preferente tener una carrera en contabilidad o afines. | ||
<u>Área de compras y recepción de materia prima | En el área administrativa entonces se tiene 1 gerente y 6 empleados. | ||
* Encargado de compras: su tarea consiste en realizar las compras de materia prima e insumos a los proveedores, pedirle la información al área de producción acerca de la materia prima necesaria para cada día, pasa así asegurar que siempre haya el stock necesario, coordinar las fechas y horarios de entrega con los proveedores para distribuirlos de forma adecuada, y avisar del cronograma de entregas al encargado de la recepción de materia prima. Trabaja 8 horas al día, 5 días a la semana. No se requiere una carrera para ese puesto, pero es preferible tener experiencia en compras. | |||
<u>Área de compras y recepción de materia prima:</u> (4 personas) puestos: | |||
* Encargado de compras: su tarea consiste en realizar las compras de materia prima e insumos a los proveedores, pedirle la información al área de producción acerca de la materia prima necesaria para cada día, pasa así asegurar que siempre haya el stock necesario, coordinar las fechas y horarios de entrega con los proveedores para distribuirlos de forma adecuada, y avisar del cronograma de entregas al encargado de la recepción de materia prima (operador de clark). Trabaja 8 horas al día, 5 días a la semana. No se requiere una carrera para ese puesto, pero es preferible tener experiencia en compras. | |||
* Operador de clark: se encarga de recibir la materia prima, asegurarse de que lo que se recibe es correcto (peso y humedad), y transportar la materia prima a la playa de fardos. Su horario es variable, puesto que depende de como coordine con el encargado de compras, sin embargo trabaja un máximo de 48 horas semanales. Para este puesto se requiere tener un certificado habilitante para conducir el clark. | * Operador de clark: se encarga de recibir la materia prima, asegurarse de que lo que se recibe es correcto (peso y humedad), y transportar la materia prima a la playa de fardos. Su horario es variable, puesto que depende de como coordine con el encargado de compras, sin embargo trabaja un máximo de 48 horas semanales. Para este puesto se requiere tener un certificado habilitante para conducir el clark. | ||
En el área de compras y recepción de materia prima entonces se tiene 1 encargado de compras y 3 operadores de clark. | |||
<u>Limpieza:</u> no colocamos a la limpieza como un área dentro del organigrama puesto que la tercerizaremos. | <u>Limpieza:</u> no colocamos a la limpieza como un área dentro del organigrama puesto que la tercerizaremos. | ||
El total de personas que conforman el organigrama son entonces 82 personas. | |||
== Listado de Equipos Auxiliares, Muebles y Útiles == | == Listado de Equipos Auxiliares, Muebles y Útiles == |
Revisión del 21:24 19 ago 2019
Determinación de la Localización
Para decidir la localización de la planta productiva, lo primero que hacemos es analizar si existen factores restrictivos. En nuestro proyecto, los factores más importantes a tener en cuenta son la disponibilidad de los servicios requeridos (principalmente agua y electricidad), la disponibilidad de grandes terrenos, así como la cercanía a los puntos de ventas. Con respecto a este punto, resulta muy conveniente seleccionar un lugar cercano a parques industriales o a Capital Federal, por lo que nos enfocaremos en este tipo de localizaciones. La planta junto a las oficinas administrativas, depósitos y demás requieren un gran espacio, de aproximadamente 22000m2, por lo que el precio por metro cuadrado y disponibilidad de espacios tan grandes son cruciales para decidir el lugar donde ubicar al proyecto. Aparte de estos puntos, no existen grandes restricciones que impidan ubicar el proyecto, pero si hay otros factores que influyen en la decisión, como los muestra la siguiente matriz:
Matriz de localización:
Factor | Importancia | Pacheco | Pilar | San Martín | Capital Federal |
---|---|---|---|---|---|
Disponibilidad de grandes terrenos | Necesario | si | si | si | no |
Disponibilidad de servicios (luz y agua) | 9 | 10 | 10 | 9 | - |
Cercanía materia prima | 7 | 7 | 5 | 9 | - |
Precio m2 | 8 | 7 | 10 | 3 | - |
Cercanía mercado comprador | 7 | 10 | 8 | 6 | - |
Recursos humanos especializados | 4 | 7 | 6 | 8 | - |
Impuestos | 5 | 8 | 9 | 6 | - |
Total | 423 | 420 | 317 | - |
La ubicación de Capital Federal la descartamos puesto que se dificulta conseguir grandes terrenos, la cual es una característica indispensable para el proyecto. Por eso no analizamos el resto de los factores para esta localización. El resto del análisis lo hacemos entonces para las 3 localidades restantes.
Aclaraciones: Con respecto a la cercanía a la materia prima, la mayor parte del cartón necesario para ser reciclado se recolecta primero en Capital Federal y GBA, por lo que San Martín es el lugar más cercano, seguido por Pacheco y luego Pilar. Por otro lado, nuestros principales clientes son productores industriales, siendo que Pacheco y Pilar poseen ambos una gran cercanía con nuestros potenciales clientes, mientras que San Martín es el más alejado de los 3.
La disponibilidad de luz y agua no es una restricción en ninguno de esos 3 lugares, por lo que los 3 tienen valores altos.
Precio m2: los valores de referencia hallados son:
San Martín | Pilar | Pacheco | |
---|---|---|---|
Compra | 225 US/m2 | 62 US/m2 | 125 US/m2 |
Alquiler mensual | 1,65 US/m2 | 0,25 US/m2 | 0,5 US/m2 |
En el ítem de impuestos, Pilar ofrece una exención del 100% del pago de ingresos brutos durante 4 años para proyectos industriales que se radiquen allí, así como una reducción al impuesto inmobiliario. En Pacheco se ofrece una reducción de entre 50 y 100% de la tasa de seguridad e higiene y la de habilitación de comercios e industrias, además de beneficios impositivos en impuestos provinciales. En San Martín se ofrece una reducción del 40% de la tasa de seguridad e higiene para industrias, y también un programa de pagos de impuestos en caso de que la empresa lo solicite. A esto hay que agregarle una exención en las tasas municipales por 1 año a aquellas industrias nuevas que se radiquen en San Martín.
Teniendo en cuenta la matriz de localización se decide ubicar al proyecto en General Pacheco.
Definición Técnica del Producto
Planos
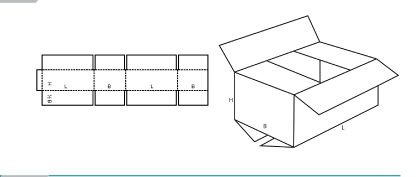
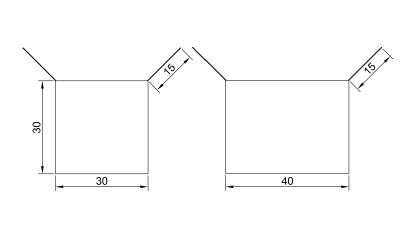
Especificaciones técnicas
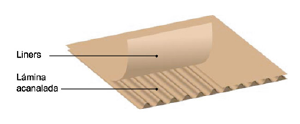
Las cajas 0201 tendrán un gramaje de 130 por cada m2 de cartón. Respecto a las dimensiones, se adaptarán a los requerimientos de los clientes.
Por otro lado, se deberá especificar el tipo de onda a usar. A continuación las más usadas en la industria.
Según su composición, trabajaremos con distintos tipos de cartón ondulado:
- Una onda. Se forma con tres láminas de papel: una onda y dos liners. La mayoría de cajas se hacen con este tipo de cartón porque es bastante resistente.
- Doble onda. Es el resultado de dos ondas separados entre si por un liner interior y dos liners exteriores. Este cartón es muy resistente y se emplea en, por ejemplo, cajas de frutas y verduras.
- Triple onda. Formado a partir de tres ondas, dos liners medios y dos externos, este cartón es ideal para proyectos que tengan que sorportar poco peso.
Normas Aplicables
En lo que a Cartón Corrugado respecta, existe un “Código Internacional para cajas de cartón ondulado” desarrollado por la Federación Europea de Fabricantes de Cartón Ondulado (FEFCO) que luego fue adoptado por la Asociación Internacional de Cajas de Cartón Ondulado (ICCA) , el cual se encuentra diseñado para ser comprendido en todo el mundo y poder utilizarlo en las transacciones comerciales.
En este se estipula las simbologías y códigos internacionales, la unidad de medición utilizada (mm), el orden de las dimensiones (L) x ancho (B) x altura (H)), la codificación para el tipo de montaje (manual, automático, ambos), tipos de cierre (encolado, con cinta adhesiva, automontaje o grapado) y los tipos de cajas:
· 01: Rollos y planchas comerciales
· 02: Cajas tipo ranurado
· 03: Cajas telescópicas
· 04: Cajas plegables y bandejas
· 05: Cajas tipo deslizante
· 06: Cajas tipo rígidas
· 07: Cajas de encolado rápido
· 09: Cajas con acondicionadores interiores
Para cada tipo de caja se estipula las características, dimensiones y planos de cada una
A su vez también existen normas IRAM vigentes para la fabricación y comercialización de cartón corrugado, entre las que se incluyen las normas específicas sobre papeles para corrugar y de cajas.
Norma | Título |
IRAM 33042 | Cartón corrugado. Determinación del espesor. |
IRAM 33044 | Método de determinación de la resistencia a la compresión |
IRAM 33045 | Método de determinación de la resistencia al reventado |
IRAM 33049 | Método de determinación de la resistencia a la compresión de la onda |
IRAM 33050 | Cartón corrugado, doble faz, para cajas tipo uso interno. |
IRAM 33052 | Cartón corrugado. Definiciones de tipos y de ondulaciones. |
IRAM 33053 | Cartón corrugado. Símbolos convencionales empleados en el dibujo de cajas. |
IRAM 33054 | Cartón corrugado. Datos que deben incluirse en el pedido de cajas. |
IRAM 33062 | Cajas de cartón corrugado. Método de determinación de las medidas internas en cajas desarmadas. |
IRAM 33066 | Cartón corrugado. Método de determinación de la resistencia a la compresión en columna. |
IRAM 33068 | Cartón corrugado. Código de cajas y accesorios de cartón corrugado. |
IRAM 33075 | Cartón corrugado y sus cajas. Defectos. |
IRAM 33089 | Cartón Corrugado. Determinación de la resistencia al agua de la adhesión entre onda y cara. Requisito y método de ensayo |
IRAM 33091 | Cartón corrugado. Clasificación del cartón corrugado, doble faz, onda tipo C, de acuerdo con su propiedad autoportante. |
IRAM 3130 | Materiales celulósicos reciclables. Clasificación y requisitos |
Así mismo si las cajas que estén destinadas a estar en contacto con alimentos son encuadrados como Riesgo Medio ya que podrían ser cedidos a los alimentos y resultar perjudiciales para la salud, por ello el ANMAT establece el procedimiento a seguir para ser autorizados a la fabricación y comercialización de los mismos.
ANMAT - Disposición 10088-E/2017: http://www.anmat.gov.ar/boletin_anmat/BO/Disposicion_10088-E-2017.pdf
Plan de Ensayos y controles
- El primer control que se hace es sobre la materia prima recibida. La materia prima (cartones para reciclar) se llevan a la planta en camiones, por lo que para verificar que el peso que traen es el que dicen se pesan los camiones en balanzas especiales, tarando su peso, de forma tal de conocer la cantidad real de materia prima que se compra. A su vez se controla la cantidad de humedad presente en el cartón, la cual no debe ser mayor al 10%.
- Antes de ingresar a la mesa de formación, que es el proceso donde comienza a sacarse el agua de la pasta del papel (ver diagramas del proceso abajo) se toman muestras para determinar la cantidad de agua presente en la pasta, puesto que se debe tener una proporción adecuada para asegurar la correcta formación del papel. Para esto se usa una balanza Schopper, la cual mide el peso hectolítrico de la pasta, y de esa forma se logra determinar su peso específico. Así se puede determinar la consistencia, que debe ser del 1% en este etapa.
- Luego del secado del papel, se debe ensayar la porosidad del papel resultante. Para esto se toman muestras en la etapa del proceso mencionada y se utiliza un medidor de lisura y porosidad o un porosímetro al aire, el cual mide la cantidad de aire que pasa en una cierta cantidad de tiempo sobre una hoja del papel. La misma debe ser cercana al 60%.
- Se mide también el gramaje con una balanza, que es el peso en gramos de un metro cuadrado de papel, el cual debe ser cercano a 130gr/m2.
- Una vez formado el cartón, se le hacen mediciones de su resistencia antes de corrugarlo, tanta a las tapas lisas de las cajas como a las láminas acanaladas. A las tapas se le mide la resistencia al estallido, es decir, a la penetración de algún objeto, mientras que a las láminas acanaladas se le mide la resistencia a la compresión vertical y horizontal. Los valores que se deben cumplir se encuentran normalizados según por las normas IRAM, y dependen de la calidad de cartón que se quiera lograr.
- Se hace una medición de los efluentes, midiendo su cantidad de bacterias y sólidos presentes. Estos parámetros deben estar de acuerdo a la legislación vigente de la localización del proyecto.
Definición del Proceso de Producción
Diagrama de Flujo de Fabricación y Control
Dividimos el proceso productivo en dos partes principales: La fabricación del papel y el armado de las cajas. En los diagramas se incluyen los controles de calidad, los cuales no se hacen sobre toda la producción, si no que se toman muestras en los puntos especificados.
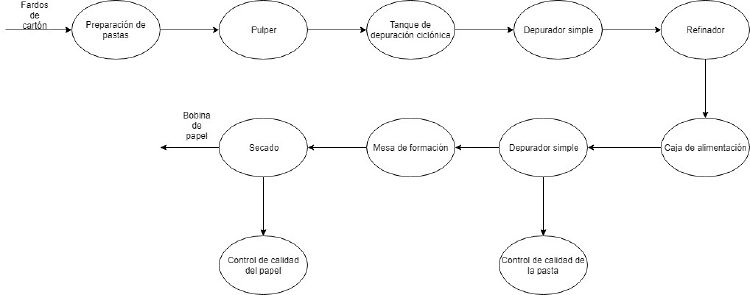
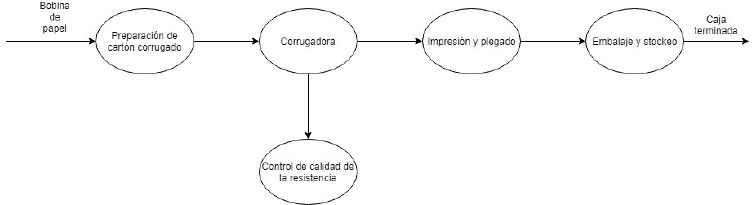
Descripción de cada etapa del proceso productivo
Preparación de pastas:
Esta etapa del proceso consiste en la transformación de la materia prima en la pasta. La materia prima utilizada proviene de orígenes variados y por ende poseen características físicas y químicas diferentes. Estas diferencias deben ser eliminadas en el mayor grado posible para producir una pasta lo más homogénea posible. Según los requerimientos de cada materia prima, las fibras son sometidas a operaciones de depuración para eliminar contaminantes, blanqueo para homogeneizar el tono, y destintado para la eliminación de tintas y cargas minerales.
Pulper
Es un depósito cilíndrico de acero inoxidable con una hélice, que, mediante la acción de un rotor y el agregado de agua, logra desfibrar la materia prima que es ingresada en forma de fardos. En el pulper se agregan distintos tipos de aditivos.
Las funciones principales del pulper son:
- Individualizar las fibras.
- Separar otras sustancias de las fibras.
- Mezcla de reactivos.
- Eliminación de contaminantes
Tanque de depuración ciclónico
El segundo paso en la fabricación de pasta, es la depuración centrífuga. Mediante este proceso se remueven, en distintas etapas, los contaminantes sólidos según su tamaño. Los equipos que intervienen en este proceso se denominan depuradores.
Durante este proceso la pasta circula a través del equipo gracias a la ayuda de las cuchillas con forma helicoidal que están enganchadas al eje. El principio de funcionamiento de esta máquina es la de tamización por tamaño. Las partículas de menor tamaño ingresan a la cámara de aceptación mientras que las partículas de mayor tamaño siguen su recorrido y quedan rechazadas.
Depurador simple
Luego de pasar por el depurador ciclónico, la pasta pasa por un depurador normal.
Su función es separar las fracciones de la alimentación en base a su densidad relativa. El fluido ingresa tangencialmente y formará una espiral descendente. Las fracciones de fibras que posean una mayor densidad chocarán contra las paredes por acción de la fuerza centrífuga, mientras que las que no posean tal densidad, permanecerán mucho más cerca del centro del ciclón. Acá la pasta va a tener un espesor de tres milímetros.
Refinador
El refinador busca aumentar los puntos de contacto entre las fibras porque cuantos más puntos de contacto haya mejor será la calidad del papel.
Caja de alimentación
A través de una bomba se hace subir la pasta hasta la caja de alimentación donde la cañería se interrumpe y se lleva a un espacio para que la altura de la columna de la pasta sea siempre igual. Para esto tenemos que asegurar un AMPA positivo y contante para la bomba que recibe esta pasta al 3,5% y la diluye para trabajarla al 1% de consistencia.
Depurador simple
El proceso que le sigue al de la caja de alimentación es otro depurador más.
La diferencia de este cleaner con respecto al anterior es que se descubrió que luego de la refinación, seguían existiendo ciertos restos de arena, la cual lograba pasar todos los anteriores filtrados y generaba problemas posteriores. Por ello se colocó este depurador el cual se encarga de volver a filtrar la pasta por diferencia de peso, eliminando estos excedentes de arena.
Luego de este limpiador se vuelve a filtrar nuevamente la pasta y se logra llegar al tamaño final de 0,20mm.
Mesa de Formación
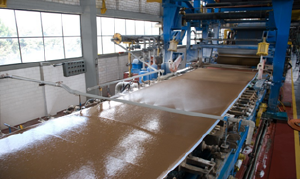
La pasta completamente refinada se vierte sobre la mesa de formación, alli a través de una tela formadora se filtra y el agua y las fibras se entrecruzan sobre la tela y forman la hoja.
Aquí los bordes de la pasta son realizados con chorros de agua a presión constante para lograr una buena terminación para luego realizar el bobinado
En este momento, la hoja deja de ser pasta para convertirse en papel con cierta cantidad de agua, ya que habrá perdido la cantidad de agua suficiente para que podamos depositarla sobre una capa de fieltro de lana o de un material sintético, lo que producirá el grano de papel.
Luego pasa a través de paños absorbentes que lo que hacen es sacarle humedad a la hoja saliendo con un 23% de sequedad
Secado
Posteriormente se pasa por unas primeras prensas con unos rollos de 600 mm de diámetro y presión neumática aplicada de 120kg/cm para llegar a una sequedad del 39%. A continuación, pasa por una segunda prensa de rollos con diámetro de 650 mm y se le aplica una fuerza de 180 kg/cm saliendo con una sequedad del 48%. Al finalizar pasa por 18 secadores de vapor con forma de rollos que aplican una presión de 6 bar para que salga con una humedad del 5%.
De aquí se lo enrolla logrando el producto semiterminado que es la bobina de papel Kraft que será enviada a la corrugadora.
Preparación Cajas de cartón corrugado
El cartón corrugado es una estructura formada por un nervio central de papel ondulado(onda), reforzado externamente por dos capas de papel (liners), las cuales son pegadas con adhesivo en la cresta de la onda. Es un material liviano, cuya resistencia se basa en el trabajo conjunto y vertical de estas tres láminas de papel
Corrugadora
Las bobinas ingresaran en la corrugadora de acuerdo al material a producir. Para ello se seleccionará la adecuada combinación de papeles y de formatos para optimizar el ancho de bobina.
El papel que luego será la onda pasa por los rodillos para tomar su formato y se encola con uno de los papeles cara, formando el llamado liner.
Luego, este se acopla con el siguiente papel formando el cartón corrugado y de acuerdo a la programación se cortan las planchas.
Impresión
Las planchas ya cortadas y plegadas ingresan en la impresora, en la cual ya fueron estipulados y programados los criterios de impresión previamente, y se imprime sobre ellas.
Embalaje
Este es el último paso del proceso de fabricación de cajas, donde se arman los paquetes de cajas, separando la cantidad adecuada según el pedido y se las embala. Una vez finalizado, se stockean las cajas.
Determinación de las máquinas e instalaciones
Especificaciones técnicas de las máquinas
Pulper
Se utilizará un rotor tipo Vokes con un motor de 270HP. El volumen que tiene disponible es de 27m³ con capacidad de producción a 4%. Posee una consistencia de 1000kg por batch.
Depurador de pasta densa
Trabaja por diferencia de peso, es de tipo ciclónico y utiliza la capacidad al 4%
Depurador tipo Fiberizer
Tiene un motor de 150HP. Su criba es de Ø3mm de diámetro y trabaja con capacidad al 4%.
Bombas centrífugas
Una de las bombas trabaja con 50HP mientras que la otra es de 75HP.
Refinador
Es un refinador de doble disco con ingreso duoflow y su motor es de 425HP.
Depurador selectivo
Trabaja separando por tamaño. Posee ranuras de 0.2mm de apertura y su motor es de 125HP.
Caja alimentación
Para poder distribuir el flujo de pasta al 1% de consistencia su capacidad hidráulica debe ser de 450m³/hora.
Mesa de formación
Está conformada con una tela formadora donde ese flujo se recibe en marcha para drenar el agua de la pasta y conformar una hoja que sale de la misma al 23% de sequedad.
Primera prensa
Posee dos rodillos poseen Ø600mm de diámetro y su presión neumática aplicada es de 120kg/cm con doble fieltro. La pasta sale del proceso con 39% de sequedad.
Segunda prensa
Sus rodillos tienen Ø650 mm de diámetro. La presión hidráulica aplicada es de 180kg/cm con doble fieltro. La pasta sale del proceso con 48% de sequedad.
Secadores
Son 18 secadores que poseen Ø1500mm de diámetro. Aplican 6bar presión de vapor máxima. A la salida del proceso la pasta sale con una humedad del 5%.
Consumos de energía, agua y otros servicios
Energía: basándonos en industrias similares podemos estimar que el consumo eléctrico necesario para formar una tonelada de papel es de 400kwh. A esto hay que sumarle el consumo del corrugado e impresión, que ronda los 200kwh, por lo que el consumo total de electricidad es de aproximadamente 600kwh por tonelada de producto terminado.
Agua: de forma análoga a la energía podemos estimar que el consumo de agua es de 7 metros cúbicos por tonelada de producto terminado.
Gas: el consumo de gas se estima en 200 metros cúbicos por tonelada de producto terminado.
Mantenimiento
Se ve a realizar un mantenimiento exhaustivo de todas las maquinarias en el mes de Febrero, las últimas dos semanas. Esto no significa que no se hagan mantenimientos con menor frecuencia que la anual mencionada con anterioridad.
Los depuradores van a implicar una limpieza mensual, donde se van a limpiar las paredes de la máquina para evitar que aquellas partículas de mayor tamaño queden pegadas generando que en los próximos filtrados pasen partículas de mayor tamaño al requerido.
Ya en la parte final del proceso, la corrugadora tendrá una limpieza con una periocidad de un mes y 15 días. Es importante realizar una limpieza de todos los componentes y partes de la máquina, desde los portabobinas, hasta la mesa de secado, pasando por la zona de encolado.
Respecto a las impresoras, el control y mantenimiento será por trimestre, y consiste, básicamente, en la limpieza interna de las mismas para no disminuir la calidad de impresión sobre las cajas.
Descripción de los sistemas de seguridad
Al disponer de un terreno de 110m x 150m, lo equivalente a 16.500m2 debemos y vamos a contar con los siguientes sistemas de seguridad, protegiendo la integridad de las personas:
- 1 matafuego del tipo ABC cada 400m2 lo que nos da un total de 42 matafuego distribuidos por toda la fábrica.
- Elementos de protección personal adecuados para circular y trabajar en el área productiva. Esto incluye calzado de seguridad y los tapones de tipo copa. Además, los empleados de la `planta papel contarán con máscaras respiratorias.
- Kit de primeros auxilios junto a desfibrilador. Se colocará uno en área administrativa, 3 en las áreas de producción, y uno en los ingresos a la planta. De tal modo, contabilizamos un total de % kits, que estarán identificados claramente con cartel del tipo luminoso verde.
- Salida de emergencia en el sector administrativo que cuenta con barras antipánico para ser accionadas rápidamente, como también por la parte trasera del área de producción y las zonas laterales de la misma.
Balance anual de material
Seccion Operativa | Alimentacion (kg) | Desperdicios (kg) | Producciones Seccionales (kg) | |
---|---|---|---|---|
recuperables | no recuperables | |||
Pulper | 7.176.000 | 71.000 | 4.000 | 7.101.000 |
Depuracion ciclonico | 7.101.000 | 160.000 | 7.300 | 6.933.700 |
Depuracion simple | 6.933.700 | 145.640 | 2.210 | 6.785.850 |
Refinador | 6.785.850 | 90.000 | 1.000 | 6.694.850 |
Caja de alimentación | 6.694.850 | 85.000 | 0 | 6.609.850 |
Depurador simple | 6.609.850 | 145.640 | 2.210 | 6.462.000 |
Mesa de formación | 6.462.000 | 0 | 0 | 6.462.000 |
Secado | 6.462.000 | 0 | 0 | 6.462.000 |
Corrugadora | 6.462.000 | 220.000 | 2.000 | 6.240.000 |
Impresión | 6.240.000 | 0 | 0 | 6.240.000 |
917.280 | 18.720 |
Seccion | Desperdicios (kg) | ||
---|---|---|---|
Recuperable | No recuperable | ||
1 | Pulper | 71.000 | 4.000 |
2 | Depuracion ciclonico | 160.000 | 7.300 |
3 | Depuracion simple | 145.640 | 2.210 |
4 | Refinador | 90.000 | 1.000 |
5 | Caja de alimentación | 85.000 | 0 |
6 | Depurador simple | 145.640 | 2.210 |
7 | Mesa de formación | 0 | 0 |
8 | Secado | 0 | 0 |
9 | Corrugadora | 220.000 | 2.000 |
10 | Impresión | 0 | 0 |
Volumen total ingresado | 7.176.000 | kg |
Consumo real de MP | 6.258.720 | kg |
% desperdicio operativo | 15 | % |
% desperdicio real | 0 | % |
Ritmo de trabajo
Equipos | Dias/semana | Turnos diarios | hs/turno | dias/año | vacaciones | Feriados |
---|---|---|---|---|---|---|
4 | 7 | 3 | 8 | 365 | 15 | 10 |
Dias activo/año | 340 | Días |
Horas activas/año | 8160 | Horas/año |
horas/Año por operario | 2040 | Horas/año |
Turnos | 1 | 2 | 3 | 4 | 5 | 6 | 7 | 8 | 9 | 10 | 11 | … |
6 a 14 hs | A | D | C | B | A | D | C | B | A | D | C | … |
14 a 22 hs | B | A | D | C | B | A | D | C | B | A | D | … |
22 a 6hs | C | B | A | D | C | B | A | D | C | B | A | … |
Capacidad real anual de la maquinaria tipo de cada sección operativa
Seccion | Cap teorica/maq*hora | Horas activas/año | Capacidad teorica/maq*año | Rendimiento operativo % | Capacidad real/maq*año |
---|---|---|---|---|---|
1 | 5.500 | 8.160 | 44.880.000 | 0,85 | 38.148.000 |
2 | 3.500 | 8.160 | 28.560.000 | 0,90 | 25.704.000 |
3 | 1.150 | 8.160 | 9.384.000 | 0,75 | 7.038.000 |
4 | 980 | 8.160 | 7.996.800 | 0,85 | 6.797.280 |
5 | 1.100 | 8.160 | 8.976.000 | 0,75 | 6.732.000 |
6 | 1.150 | 8.160 | 9.384.000 | 0,75 | 7.038.000 |
7 | 1.100 | 8.160 | 8.976.000 | 0,80 | 7.180.800 |
8 | 900 | 8.160 | 7.344.000 | 0,95 | 6.976.800 |
9 | 950 | 8.160 | 7.752.000 | 0,90 | 6.976.800 |
10 | 275 | 8.160 | 2.244.000 | 0,94 | 2.109.360 |
Cantidad de maquinarias operativas y capacidad anual por sección y su aprovechamiento en relación al programa de producción
Seccion | Programa Anual de Produccion | Capcidad real/maquina*año | Cantidad maquinas necesarias | Capacidad real/seccion*año | Aprovechamiento seccional % |
---|---|---|---|---|---|
1 | 7.101.000 | 38.148.000 | 1 | 38.148.000 | 18,6 |
2 | 6.933.700 | 25.704.000 | 1 | 25.704.000 | 27 |
3 | 6.785.850 | 7.038.000 | 1 | 7.038.000 | 96,4 |
4 | 6.694.850 | 6.797.280 | 1 | 6.797.280 | 98,5 |
5 | 6.609.850 | 6.732.000 | 1 | 6.732.000 | 98,2 |
6 | 6.462.000 | 7.038.000 | 1 | 7.038.000 | 91,8 |
7 | 6.462.000 | 7.180.800 | 1 | 7.180.800 | 90 |
8 | 6.462.000 | 6.976.800 | 1 | 6.976.800 | 92,6 |
9 | 6.240.000 | 6.976.800 | 1 | 6.976.800 | 89,4 |
10 | 6.240.000 | 2.109.360 | 3 | 6.328.080 | 98,6 |
Cuello de botella y capacidad real anual del equipo
El cuello de botella es la sección con mayor aprovechamiento.
En nuestro caso, el cuello de botella es la ultima sección ya que es la que mayor aprovechamiento secciónalos tiene.
Aprovechamiento | 98,60% |
---|
Por lo tanto, la capacidad real anual será la capacidad de impresión.
Capacidad (kg/año) | 6.328.080 |
---|
Determinación de la evolución de las mercaderías
Tiempos de entrega y envió de las mercaderías
El tiempo promedio entre el pedido y la entrega de la caja es de 15 días, dependiendo de la cantidad solicitada.
La empresa contara con su propia flota de transportes para encargarse completamente de la distribución del producto terminado.
Tamaños y frecuencias de compras
Los pedidos se realizan frecuentemente y las demoras están sujetas principalmente al cumplimiento de los pagos; dado que los proveedores venden lo que ya tienen en stock, no hay demoras si los pagos salen en tiempo y forma.
Los proveedores habituales son recicladores que compran cartones a los recolectores; también hay proveedores que compran los residuos de otras empresas y los separan según su uso, por ejemplo a cadenas de supermercados, automotrices, etc.
Se suele comprar entre 500 y 700tn por semana y se los paga por su peso
Cuando llegan los fardos de cartón, se pesa el camión en el que llegan para saber cuánto pesa lo que están comprando y se les hace un control de humedad, si esta es mucha se los rechazan porque estarían comprando agua en vez de fibra.
Se almacenan a la intemperie ya que se mojen no es problema, porque se los esta comprando secos, si están mojados antes de comprarlos si es un problema porque pesan mas y estarías comprando menos cantidad de m2, por eso se les hace el control de humedad una vez que llegan a la planta.
Los m2 de la MP se calculan como un 15% de mas (115%) en relación a los m2 de cajas producidas
Lo ideal seria trabajar con un stock que cubra una semana/10 días. El stock para diez días es el 10% de la producción
Evolución de la producción
Considerando un periodo de puesta en marcha de 3 meses, teniendo en cuenta los 15 dias de vacaciones y los 10 feriados obligatorios distribuidos en el año.
Se obtiene una producción anual promedio de: 48.000.000 m2 / 11,5 meses = 4.173.913,04 m2/mes
Mes | Ritmo de producción al inicio (%) | Ritmo de producción al final (%) | Producción Promedio (%) | Producción mensual promedio (m2) | Producción propuesta (m2) |
---|---|---|---|---|---|
1 | 0 | 15 | 7,5 | 4.173.913,04 | 313.043,48 |
2 | 15 | 60 | 37,5 | 4.173.913,04 | 1.565.217,39 |
3 | 60 | 100 | 80 | 4.173.913,04 | 3.339.130,43 |
TOTAL | 5.217.391 |
Los restantes 9 meses se producirán
4.173.913,04 m2/mes | 8,5 meses | 35.478.261 m2 |
El volumen de producción en el año 1 será de:
Mes 1 a 3 | Mes 4 a 11,5 | TOTAL | ||||||||||||||
---|---|---|---|---|---|---|---|---|---|---|---|---|---|---|---|---|
5.217.391,3 m2 | 35.478.260,87 m2 | 40.695.652 m2 |
En los 4 años restantes la producción ya se encontrará en régimen y se producirá cada año 48.000.000 m2 de cartón corrugado.
Stock promedio de Producto Elaborado
En el estado en régimen se considera hacer entregas semanales, de forma que al final de la semana no queda stock de producto terminado:
- 52 semanas/año - 2 semanas/año (vacaciones) = 50 semanas/año
- 48.000.000 m2/año / 50 semanas/año = 960.000 m2/semana
Entonces se considera el stock promedio de producto elaborado como 480.000 m2/semana
Evolución de las ventas durante la vida útil del proyecto
1 m2 de cartón corrugado equivale a 0,13 kg del mismo, entonces para producir 40.695.652,17 m2 en el año 1 se necesitan:
Ventas Año 1 =40.000.000 m2 - 480.000 = 39.520.000 m2 = 5.137.600 kg
Ventas Año 2-5 = 48.000.000 m2 = 6.240.000 kg (No corresponde restar el stock promedio ya que fue restado en el año 1)
Ventas Totales = 87.520.000,00 m2 = 11.377.600 kg
Consumo de materia prima para el programa de producción y formación de la mercadería en curso y semielaborada
AÑO 1
Consumo de MP
Producción | ||
---|---|---|
Mes | Año 1 | |
m2 | kg | |
1 a 3 | 5.217.391 | 678.261 |
4 a 11,5 | 35.478.261 | 4.612.174 |
Total | 40.695.652 | 5.290.435 |
MP PT Año 1 = 678.26 1* 1,04 + 4.612.174 * 1,02 = 5.409.809 kg
Desperdicios no recuperables = 5.409.809 kg - 5.290.435= 119.374 kg
Aclaración: En los 3 meses de puesta en marcha tendremos el doble de desperdicios no recuperables.
Alimentación del proceso para un ciclo de elaboración
Teniendo en cuenta que nuestro ciclo dura 1 día, tendremos 340 ciclos al año. La cantidad que MP que debemos ingresar se calcula haciendo el Volumen Total Ingresado ( calculado anteriormente) sobre la cantidad de ciclos en un año. Asi obtenemos la MP a ingresar que incluye los desperdicios, tanto recuperables como no recuperables.
7.176.000 / 340 = 21.106 kg
Consumo total de MP (CTMP)
CTMPAño 1 = 5.409.809 kg + 21.106 kg = 5.430.915 kg
AÑO 2 A 5
Consumo total de MP (CTMP)
CTMPAño 2 a 5 = 6.240.000 kg * 1,02 = 6.364.800 kg
Stock promedio de materia prima y el programa de compras
Stock mínimo de materia prima: se calcula como la materia prima que se compra durante el año dividido los meses de trabajo. En régimen queda entonces:
Stock mínimo= 6364800kg/11,5 meses = 553461 kg
Compra de materia prima:
Año 0: se compra la materia prima que se utilizará durante la puesta en marcha, es decir 678261kg más los DNR. Esto da el total de 678261kg * 1,04= 705391kg Estas compras se distribuyen en los últimos tres meses del año 0. Todos los valores del cuadro están en kilos
al fin del mes | stock | compras |
---|---|---|
octubre | 235130 | 235130 |
noviembre | 470260 | 235130 |
diciembre | 705391 | 235131 |
Año 1: El stock de seguridad es de 37440 kg, y como las compras se hacen en forma mensual queda siempre a fin de mes esa cantidad de stock, luego de la puesta en marcha.
al fin del mes | stock | compras |
---|---|---|
enero | 663068 | 0 |
febrero | 451451 | 0 |
marzo | 37440 | 37440 |
abril | 37440 | 553461 |
mayo | 37440 | 553461 |
junio | 37440 | 553461 |
julio | 37440 | 553461 |
agosto | 37440 | 553461 |
septiembre | 37440 | 553461 |
octubre | 37440 | 553461 |
noviembre | 37440 | 553461 |
diciembre | 37440 | 553461 |
Año 2 al 5: las compras en el mes de febrero son menores por las vacaciones, por lo que se produce la mitad en ese mes.
al fin del mes | stock | compras |
---|---|---|
enero | 37440 | 553461 |
febrero | 37440 | 276730,5 |
marzo | 37440 | 553461 |
abril | 37440 | 553461 |
mayo | 37440 | 553461 |
junio | 37440 | 553461 |
julio | 37440 | 553461 |
agosto | 37440 | 553461 |
septiembre | 37440 | 553461 |
octubre | 37440 | 553461 |
noviembre | 37440 | 553461 |
diciembre | 37440 | 553461 |
Stock promedio: se obtiene sumando la cantidad final e inicial de materia prima considerando el tiempo entre compra y compra. Se trabaja con aproximadamente 4 compras mensuales, por lo que el stock promedio será:
Para el año 0:
(235130+470160+705391)/12= 117557 kg = stock promedio MP año 0
Para el año 1:
[(705391+663078)/2+(663078+451451)/2+(451451+37440)/2+9(553461+37440)/2]/12= 345417 kg = stock promedio MP año 1
Para el año 2:
[11*(553461+37440)/2+(276730,5+37440)/2]/12 = stock promedio año 2 al 5 = 295450 kg
Cuadro resumen del programa general de evolución
Unidad | Periodo de Instalación | Año 1 | Año 2 | |
---|---|---|---|---|
Ventas | kg PT | 0 | 5.137.600 | 6.240.000 |
Stock promedio de elaborado | kg PT | 0 | 480.000 | 480.000 |
Producción | kg PT | 0 | 5.290.435 | 6.240.000 |
Desperdicios no recuperables | kg PT | 0 | 119.374 | 124.800 |
MP en curso | kg PT | 0 | 21.106 | 21.106 |
Consumo de MP | kg PT | 0 | 5.430.915 | 6.364.800 |
Stock de MP | kg PT | 117557 | 345.417 | 295.450 |
Compra de MP | kg PT | 705391 | 50.185.89 | 6.364.802 |
Determinación del Personal
Organigrama de toda la empresa
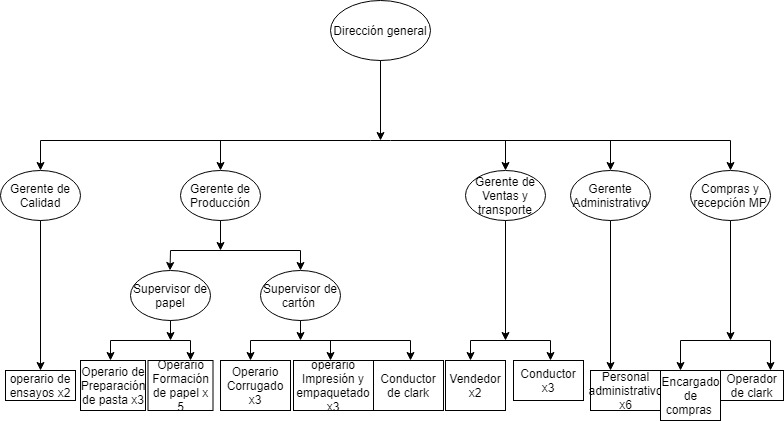
Aclaración: hay un gerente por cada área, mientras que para los supervisores, operarios y conductores en el organigrama están colocados las cantidades requeridas por turno (3 turnos). Los vendedores, el encargado de compras y el personal administrativo trabajan solo en un turno. Abajo se detallan la cantidad de personas que posee cada área, así como la distribución por turnos de cada puesto.
Descripción de los Puestos de Trabajo
Área de calidad: (7 personas) puestos:
- Gerente de calidad, que es el encargado de determinar el tipo de ensayos que se debe realizar sobre las distintas partes del proceso, así como determinar los controles sobre los efluentes, y verificar que se cumpla con la normativa vigente. Debe revisar periódicamente que el producto se encuentre dentro de los límites de calidad determinados. El gerente de calidad trabaja 8 horas por día, 5 días a la semana. El gerente de calidad debe tener la formación en química y física suficiente (por ejemplo, ser ingeniero químico) para poder determinar los ensayos adecuados a realizar, y debe conocer profundamente el producto.
- Operario de ensayos, los cuales son 2. Su tarea consiste en hacer los ensayos de calidad determinados por el gerente de manera regular, verificando el estado del producto, para así asegurar que se trabaje dentro de los límites establecidos. Trabajan 8 horas diarias, 5 días a la semana. Los turnos se distribuyen de manera tal que cada día al menos un operario haya estado, y que sus turnos no coincidan. Las calificaciones requeridas para este puesto son conocimientos en física y química suficiente para poder interpretar los resultados de manera correcta, y determinar las causas por las cuales pueden producirse los desvíos. Deben recibir capacitación en el uso de los aparatos de medición utilizados para los ensayos.
En el área de calidad entonces se tiene para los 3 turnos un total de 1 gerente y 6 operarios.
Área de producción: (52 personas)
- Es dirigida por el gerente de producción, quien supervisa que se trabaje de acuerdo al plan de producción estipulado, desarrolla e implementa las mejoras necesarias, revisa que el proceso se desarrolle en forma adecuada, y sirve como nexo entre las distintas áreas de la empresa, así como en las áreas de producción, las cuales son dos: papel y cartón. Trabaja 8 horas diarias, 6 días a la semana. El gerente debe tener competencias en la planificación y control de la producción, y ser de preferencia un ingeniero industrial o haber estudiado una carrera afín. También se necesita tener experiencia en la industria del papel y el cartón.
Papel: puestos:
- Supervisor de papel, quien está a cargo de todos los procesos de formación de papel. Sus tareas incluyen revisar que los procesos que van desde el pulper hasta el secado se desarrollen en forma correcta, que se cumpla con los volúmenes de producción requeridos y que el abastecimiento de materia prima e insumos sea el adecuado. A su vez es el encargado de corregir los problemas imprevistos que puedan aparecer en estos procesos. Trabaja un supervisor por turno, habiendo 3 supervisores que trabajan 6 días a la semana, 8 horas. El supervisor debe tener competencias en la planificación y control de la producción, y ser de preferencia un ingeniero industrial o haber estudiado una carrera afín. También se necesita tener experiencia en la industria del papel y el cartón.
- Operario de preparación de pasta, quien se encarga de todos los procesos entre el primero (preparación de la pasta), hasta el refinador. Son 3 operarios por turno, y trabajan en forma alternada; un día a la mañana, al siguiente a la tarde, el siguiente a la noche y luego un franco. Su principal tarea es mantener el flujo de fardos de cartón sobre el pulper constante, y también se encarga de verificar la cantidad de desperdicios no recuperables obtenidos en la depuración y refinado, para saber si el proceso marcha de forma adecuada. No se requiere tener experiencia previa ni conocimientos particulares para este puesto debido a que se brindará la capacitación necesaria.
- Operario de formación de papel, quien se encarga de los procesos de la caja de alimentación, depurador simple, mesa de formación y secado. Su principal tarea consiste en volver a enhebrar el papel en caso de que se corte en el proceso de secado, analizar el ancho del papel tanto en la mesa formadora como en el proceso de secado y corregir las máquinas en caso de desvíos. Deben controlar que el flujo de pasta y de agua sea la adecuada. Trabajan 5 operarios por turno, en forma alternada; un día a la mañana, al siguiente a la tarde, el siguiente a la noche y luego un franco. No se requiere tener experiencia previa ni conocimientos particulares para este puesto debido a que se brindará la capacitación necesaria.
Cartón: puestos:
- Supervisor de cartón,quien se encarga de controlar los siguientes procesos: preparación de cartón corrugado, corrugadora, impresión y plegado, embalaje y stockeo. Su trabajo consiste en asegurar que se desarrollen en forma correcta, que se cumpla con los volúmenes de producción requeridos y que el abastecimiento de materia prima e insumos sea el adecuado. A su vez es el encargado de corregir los problemas imprevistos que puedan aparecer en estos procesos. Trabaja un supervisor por turno, habiendo 3 supervisores que trabajan 6 días a la semana, 8 horas. El supervisor debe tener competencias en la planificación y control de la producción, y ser de preferencia un ingeniero industrial o haber estudiado una carrera afín. También se necesita tener experiencia en la industria del papel y el cartón.
- Operario de corrugado, quien tiene como tarea abastecer a la máquina que prepara el cartón corrugado, así como a la corrugadora. También se encarga de restablecer la continuidad de la corrugadora en caso de que una hoja de cartón se rompa. Trabajan 3 operarios por turno en forma alternada. No se requiere tener experiencia previa ni conocimientos particulares para este puesto debido a que se brindará la capacitación necesaria.
- Operario de impresión y empaquetado, tiene como tarea abastecer a las impresoras de las planchas de cartón corrugado, recibir las cajas impresas y embalarlas. También tienen que recargar las impresoras con tinta. Trabajan 3 operarios por turno en forma alternada. No se requiere tener experiencia previa ni conocimientos particulares para este puesto debido a que se brindará la capacitación necesaria.
- Conductor de clark, tiene como tarea transportar en un clark las bobinas de papel desde el área de papel hasta los depósitos, desde allí hasta el área de cartón (corrugadora), y finalmente desde las impresoras hasta el depósito de producto terminada. Trabaja un operador por turno en forma alternada. Para este puesto se requiere tener un certificado habilitante para conducir el clark.
En el área de producción entonces se tiene para los 3 turnos un total de 1 gerente, 6 supervisores y 45 operarios (incluyendo a los operadores de clark).
Área de ventas y transporte: (12 personas) puestos:
- Gerente de ventas y transporte: tiene como tareas revisar el plan de ventas, buscar y negociar tratos con nuevos clientes, evaluar el estado de las ventas, verificar la capacidad de entrega de la empresa, coordinar con el área de producción que se pueda cumplir con las ventas realizadas, coordinar las entregas a los clientes. Trabaja 8 horas al día, 6 días a la semana. Para este puesto es preferente contar con una carrera de marketing, administración de empresas o afines.
- Vendedor: sus tareas son buscar y captar nuevos clientes para la empresa, ya sea de producto terminado (cajas de cartón) como de subproducto (bobinas de papel defectuosas con valor comercial). También tienen como tarea responder ante los clientes. Hay 2 vendedores, y trabajan 8 horas al día, 5 días a la semana. No se requiere una carrera para este puesto, pero es preferente contar con experiencia en ventas
- Conductor: Se encarga de manejar los camiones para transportar el producto terminado a los clientes. Hay 3 conductores por turno, teniendo los 3 turnos. Sin embargo los turnos de trabajo varían según el recorrido que se deba hacer hasta llegar al cliente. Se requiere una licencia de conducir profesional para este puesto.
En el área de ventas y transporte entonces se tiene 1 gerente, 2 vendedores y 9 conductores.
Área administrativa: (7 personas) puestos:
- Gerente administrativo: se encarga de verificar que se cumplan con los lineamientos administrativos necesarios, incluyendo la gestión de pagos, cobranzas, situación contable, entre otros. Trabaja 8 horas al día, 5 días a la semana. Para este puesto es preferente contar con una carrera de administración de empresas, contabilidad o afines.
- Personal administrativo: Se encargan de organizar la gestión de pagos y cobranzas, atención al consumidor, pago de impuestos, entre otras tareas administrativas. Son 6 empleados, que trabajan 8 horas al día, 5 días a la semana. No se requiere una carrera para este puesto, pero es preferente tener una carrera en contabilidad o afines.
En el área administrativa entonces se tiene 1 gerente y 6 empleados.
Área de compras y recepción de materia prima: (4 personas) puestos:
- Encargado de compras: su tarea consiste en realizar las compras de materia prima e insumos a los proveedores, pedirle la información al área de producción acerca de la materia prima necesaria para cada día, pasa así asegurar que siempre haya el stock necesario, coordinar las fechas y horarios de entrega con los proveedores para distribuirlos de forma adecuada, y avisar del cronograma de entregas al encargado de la recepción de materia prima (operador de clark). Trabaja 8 horas al día, 5 días a la semana. No se requiere una carrera para ese puesto, pero es preferible tener experiencia en compras.
- Operador de clark: se encarga de recibir la materia prima, asegurarse de que lo que se recibe es correcto (peso y humedad), y transportar la materia prima a la playa de fardos. Su horario es variable, puesto que depende de como coordine con el encargado de compras, sin embargo trabaja un máximo de 48 horas semanales. Para este puesto se requiere tener un certificado habilitante para conducir el clark.
En el área de compras y recepción de materia prima entonces se tiene 1 encargado de compras y 3 operadores de clark.
Limpieza: no colocamos a la limpieza como un área dentro del organigrama puesto que la tercerizaremos.
El total de personas que conforman el organigrama son entonces 82 personas.
Listado de Equipos Auxiliares, Muebles y Útiles
Producción: los equipos auxiliares requeridos para esta área son:
- Clark
- 8 bombas, correspondientes a la preparación de pastas, pulper, tanque de depuración ciclónica, depurador simple (x2), refinador, caja de alimentación y mesa de formación
- Transformadores
- Escalera para acceder a las partes altas de las máquinas (x5)
- Tachos de basura grandes
- Cuadernos y material de escritura
- Matafuegos ABC x3
- EPP
- Equipo de ventilación industrial
Laboratorio: los equipos auxiliares requeridos para esta área son:
- Balanza Schopper
- Porosímetro
- Balanza de precisión
- Medidor de resistencia al estallido
- Medidor de aplastamiento
- Tacho de basura
- Mesa de trabajo
- Sillas x2
- Cuadernos y material de escritura
- Matafuegos ABC
Administración: los equipos auxiliares requeridos para esta área son:
- teléfonos fijos x10
- computadoras x10
- sillas x15
- escritorios x10
- Cuadernos y material de escritura
- Artículos de oficina
- Tacho de basura x10
- Cafetera
- Aire Acondicionado
- Impresora x2
- Matafuegos ABC
Transporte de PT: los equipos auxiliares requeridos para esta área son:
- Camiones x3
Recepción de materia prima: los equipos auxiliares requeridos para esta área son:
- Balanza para camiones
- Clark
- Medidor de humedad de cartones
Comedor: los equipos auxiliares requeridos para esta área son:
- Mesas x3
- Sillas x30
- Heladera
- Microondas x2
- Horno eléctrico
- Cafetera
- Aire Acondicionado
- Matafuegos ABC
- Dispenser de agua
Depósitos: los equipos auxiliares requeridos para esta área son:
- Estanterías metálicas x8
- Zorra hidraulica x3
- Matafuego ABC x4 (1 para cada deposito)
Recepción: los equipos auxiliares requeridos para esta área son:
- Escritorio
- Silla
- Sillones x3
- Mesa ratona x2
- Computadora
- Telefono fijo
- Matafuegos ABC
Vestuario: los equipos auxiliares requeridos para esta área son:
- Lockers x20
- Mingitorios x4
- Inodoros x4
- Matafuegos ABC
Seguridad: los equipos auxiliares requeridos para esta área son:
- Escritorio
- Telefono fijo
- Computadora
- Matafuego ABC
Anteproyecto de Planta
Plano de planta
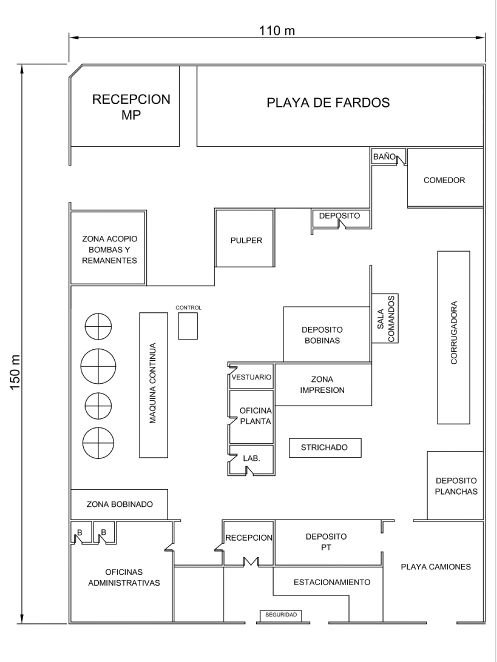
Plano de planta con recorrido de los materiales
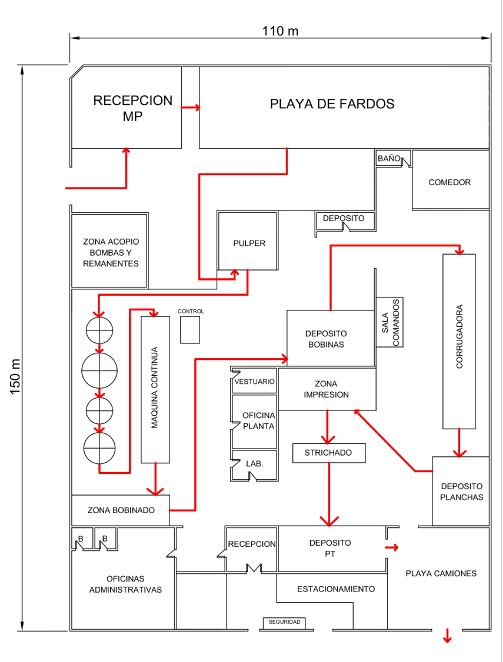
Cronograma de ejecución
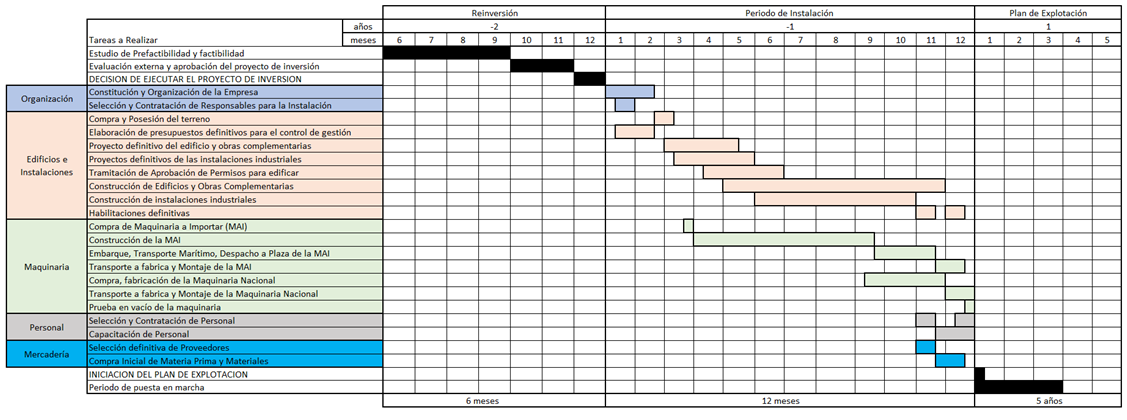