Diferencia entre revisiones de «2020/Grupo7/DimensionamientoFisico»
Línea 996: | Línea 996: | ||
== Cronograma de ejecución == | == Cronograma de ejecución == | ||
[[Archivo:Cronogramadeejecuciónmotores.png|centro|miniaturadeimagen|1169x1169px]] |
Revisión del 21:16 1 jul 2020
Determinación de la localización
Para la determinación de la localización de nuestra planta productiva se tuvieron en cuenta:
- Distancia a proveedores.
- Distancia a distribuidores.
- Disponibilidad de servicios.
- Precio del m2.
- Disponibilidad de la mano de obra.
- Distancia a los accesos, tales como rutas nacionales o provinciales.
Estos factores se analizaron en la siguiente matriz, ponderando los mismos para seleccionar el más óptimo.
Podemos concluir entonces que la ubicación óptima de nuestra planta será en San Martín, Buenos Aires.
Definición técnica del Producto
Planos y dibujos
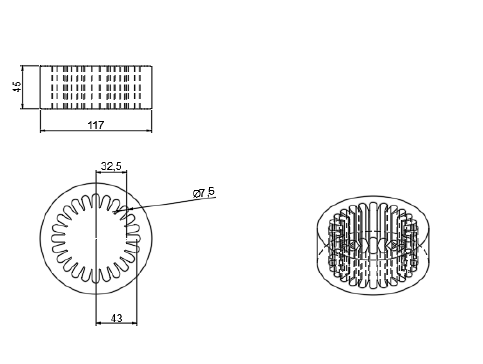
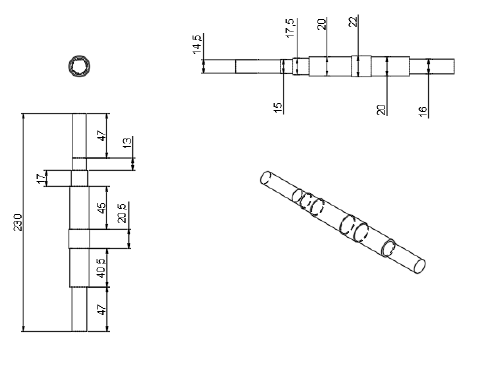
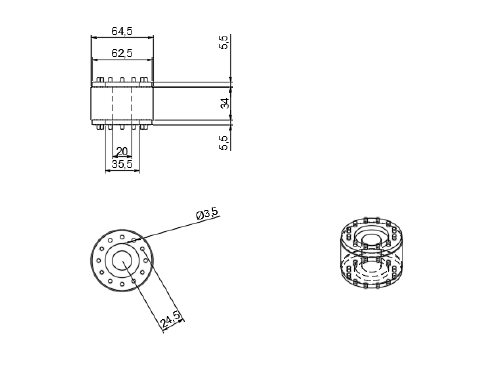
Listado de materiales
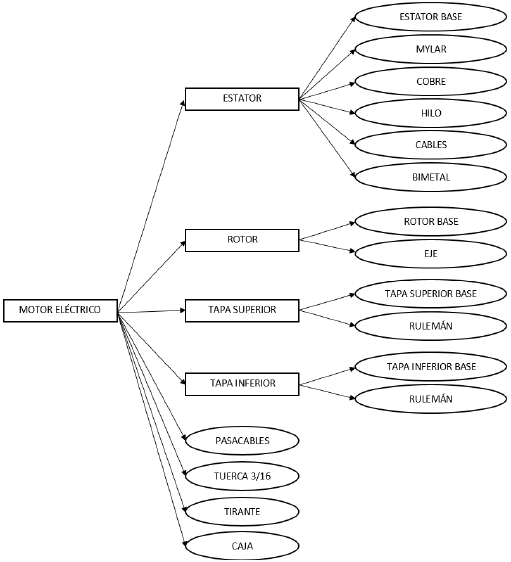
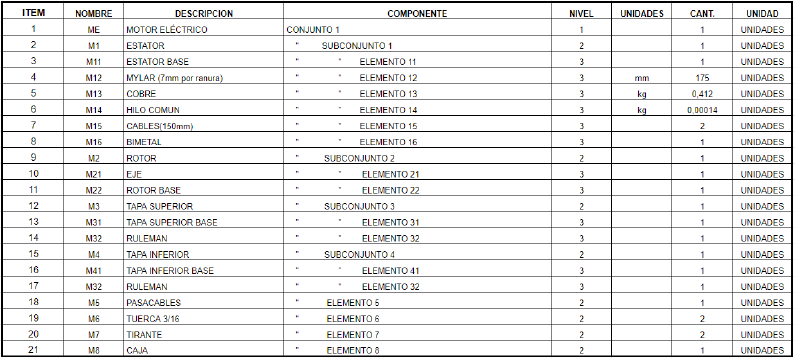
Especificaciones Técnicas
Especificaciones Técnicas Motor | |
Peso | 4,7 kg |
Corriente | Monofásica (Alterna) |
Alimentación | 220 V |
Potencia Nominal | 0,33 |
Frecuencia | 50 Hz |
R.P.M | 1200 |
Rotor | Jaula de Ardilla |
Estator | Ranurado |
Especificaciones Técnicas Componentes | |
Estator |
|
Mylar |
|
Rotor |
|
Eje |
|
Bobinas |
|
Tapas |
|
Normas Aplicables
-ISO 2372/2373: norma de límite de velocidad de vibración mecánica en máquinas rotativas la cual se basa en los HP (caballos de fuerza) de dicha máquina, aplicándose tanto para motores de corriente alterna como así también de corriente continua.
-IRAM 62409: normativa de etiquetado de motores monofásicos de inducción para distinguir con facilidad cuál motor es más eficiente. La etiqueta se compone por las siguientes 4 clases de EE: IE00, IE 0, IE1 e IE 2, donde al IE 2 se le adjudica a los motores más eficientes y al IE 00 a los menos eficientes. Ambas etiquetas muestran también el rendimiento de los equipos expresado en porcentaje. Es importante destacar que para determinar la información que se incluye en las etiquetas, se llevan a cabo ensayos en laboratorios externos, que no tienen vínculo con el fabricante, y los resultados son evaluados por un organismo de certificación (acreditado por el OAA y reconocido por la Dirección de Comercio Interior), como IRAM, quien finalmente certifica los datos que el fabricante debe incluir en las etiquetas. Estas etiquetas no son obligatorias pero son fundamentales para lograr nuestra diferenciación en calidad.
Características y condición del producto
El producto será entregado en cajas individuales correctamente embaladas con fecha y número de lote y con sus etiquetas correspondientes.
Plan de ensayos
Luego del ensamble se efectúa un control para su funcionamiento de 2 minutos por motor en el cual se le coloca una mordaza conectada a corriente para probar su correcto funcionamiento, si ocurre algún error en el mismo se desarma y se lo corrige.
También Se realizarán ensayos en laboratorios externos para la certificación IRAM, además de los controles en la realización de cada proceso productivo. Se toman muestreos de equipos por lote, los cuales se retiran del depósito de producto terminado y son transportados a laboratorios externos para la realización de los ensayos.
Definición del proceso de producción
Diagrama de flujo de Fabricación y control. Cursogramas gráficos y analíticos.

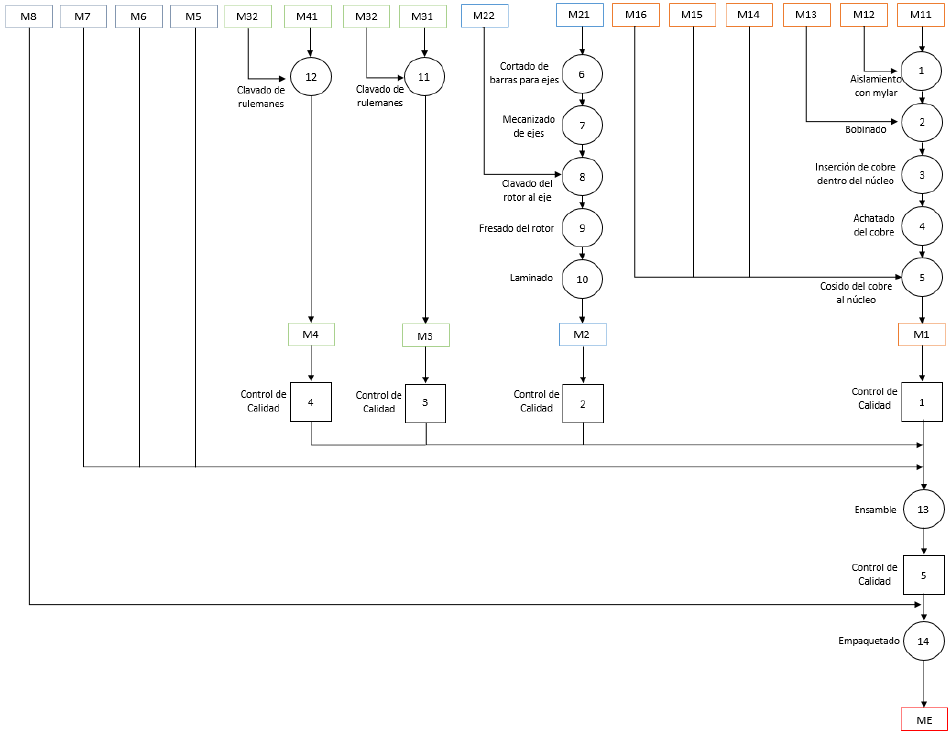
Descripción de cada etapa del proceso productivo
ESTATOR
Retiro de depósito. Se retira la base del estator del depósito.
Aislado: este proceso consiste en aislar el estator del cobre mediante un material aislante llamado mylar con fin de que no generen masa por medio del rozamiento. Primero el operario al comienzo del día coloca el rollo de mylar en la máquina. Luego sitúa el estator en la cuña de la máquina quedando fijo. A continuación, el operario configura la máquina en base a las medidas requeridas dependiendo del tamaño del estator y otros parámetros solicitados. Una vez realizados estos procedimientos, el operario acciona la aisladora. Su funcionamiento se fundamenta en un plato giratorio incorporado por agujeros, en donde por uno solo de dichos orificios se va insertando el material aislante (mylar) dentro de cada ranura del núcleo (estator). El mylar se va desenrollando y cortando a lo largo del proceso a medida que se necesite. Es importante tener en cuenta que, una vez colocado el mylar, el mismo será reemplazado cuando se haya terminado (no todos los días).
Al principio de la operación, el operario genera un desperdicio mínimo debido a que realiza un “tiro al aire” con el objetivo de calentar el equipo a utilizar. Esta merma se basa en aproximadamente 20 chavetas de 1 cm cada una.
Bobinado: esta operación se hace previamente a la inserción de cobre, como propósito de generar el campo eléctrico. Para ello, el operario, detrás de la bobinadora, inserta el carrete de cobre dentro de ella, para posteriormente, hacerlo pasar por un ojal. Por subsiguiente, el operario elige la potencia a utilizar teniendo en cuenta el núcleo a procesar, escoge el ángulo de la espira y el volumen de cobre que sea necesario. Además, el operario selecciona en el programa el sistema eléctrico (monofásico) dependiendo de la cantidad de salidas en los ochos. A mayor cantidad de cobre, mayor será la potencia del campo eléctrico. Llegado este punto, el operario acciona la bobinadora en donde la misma efectúa el bobinado generando con el cobre una forma de ochos.
Al igual que la aisladora, la bobinadora genera un desperdicio al principio del proceso que se debe al calentamiento de la misma. El primer bobinado se hace trabajando en vacío, causando una merma cercana al 3% de un rollo de 100m de largo.
Insertado: El operario introduce las espiras ya bobinadas en forma de ochos por dentro de las agujas de la insertadora, contando la misma tanto con agujas fijas como con móviles. Posteriormente, coloca una dispositivo similar a una manija en las agujas fijas que se encuentran en el cabezal y emplaza el núcleo en dicho cabezal de la máquina. Luego, coloca en la parte sólida del estator una tapa para su protección donde será sujetado por dos brazos de costado con el objetivo de mantenerlo en posición inmóvil. Una vez dispuesto esto, el operario acciona la máquina y, junto a un pistón a base de fuerza hidráulica, empuja las agujas móviles insertando las espiras de cobre dentro de las ranuras del estator haciendo contacto con el mylar anteriormente mencionado.
No posee ningún tipo de desperdicio.
Cosido: se realiza con la finalidad de mantener el cobre comprimido y aprisionado para no perder ningún tipo de potencia o, en caso de pérdida, la mínima posible. El operario debe coser el cobre saliente en las partes de arriba y abajo del estator mediante una única pasada de hilo común. Para este proceso simplemente será necesario una aguja e hilo. El operario enhebra el hilo en el ojo de la aguja efectuando el correspondiente nudo y mediante sus habilidades manuales cose el cobre en los bordes del estator. A considerar, esta operación puede ser realizada luego del prensado.
Además, luego de realizado el cosido, se unen los cables a las salidas de la bobinas del cobre. También, entre ellos 2, cables y las salidas de los ochos, se enlaza el bimetal.
No posee ningún tipo de desperdicio.
Aprisonamiento: al igual que el cosido, tiene como fin el compactamiento del cobre generando mayor potencia y suficiente espacio. El operario coloca horizontalmente el estator en la prensadora, sujetado por una mordaza tanto arriba como abajo apretando al mismo, y luego acciona la prensa. Este aparato se fundamenta en dos pistones, uno macho y otro hembra, donde ambos comienzan a comprimir el cobre. El pistón macho ingresa dentro del orificio del estator emprolijando su interior hasta hacer contacto con el pistón hembra quien comprime superficialmente los anillos del estator. Se debe repetir el proceso en ambos extremos del estator.
No genera ningún tipo de desperdicio.
ROTOR
Se retira la base del rotor de depósito.
Cortado (serrucho neumático): esta línea de producción arranca con el proceso de cortado. El operario carga las barras del eje y programa el serrucho neumático en las medidas correspondiente a realizar el corte. Una vez realizado estos pasos, acciona la máquina mediante un botón. El serrucho trabaja automáticamente por plc, ejecutando el corte a modo de guillotina. Una vez realizado el corte, en la parte inferior de la máquina se encuentra un microprocesador el cual al hacer contacto directo con el serrucho efectúa una señal que eleva el mismo, estando dispuesto para el próximo corte.
Desperdicio 1 kg por cada barra de 22mm de diametro y largo de 6m .
Torneado CNC: este equipo se utiliza para darle al eje distintos diámetros y medidas que servirán para la posterior colocación del estator y el rotor. El operario inserta el eje bruto dentro del cabezal principal del plato donde es sostenido por mordazas. Luego, programa las máquinas o elige la programación adecuada previamente realizada y acciona el torno. Este torno CNC, una vez encendido, ejecuta el programa donde el eje del motor gira a una velocidad determinada dentro del husillo y mediante herramientas llamadas insertos, que están enfrentadas al eje, cilindran y frentean al mismo según los requerimientos deseados. Es importante dejar un margen de error en el eje ya que luego será llevado a otros procesos de pérdidas de material.
Se genera un 20% de desperdicio en este proceso.
Clavado (prensa): el operario dispone el eje sobre el agujero de la mesa quedando el mismo inmóvil e inserta el rotor en él. Una vez colocados los materiales en la mesa se procede al accionamiento de la máquina. Esta consiste en un plato de diámetro similar al del rotor el cual empuja dicho rotor, quedando el eje en el interior del rotor sin posición definida. Por consiguiente, el operario adiciona travasil entre el rotor y el eje quedando sellados.
Fresado: este proceso sirve como medida de seguridad en caso de deterioro del sinfín por su uso. Consiste en fresar el eje quedando un orificio (más conocido como chaveta) para frenar el nuevo sinfín acoplado. El operario sube el eje en una morsa o mordaza y acciona la máquina haciendo que la misma mediante un disco dentado frese el eje dejando lugar para colocar la chaveta
Luego, el operario coloca la chaveta en el orificio hecho para luego encastrar el sinfín manualmente al eje.
El desperdicio es todo el proceso de fresado siendo aproximadamente un 1% del eje.
Laminado de roscas: en este proceso el eje adquiere el sinfín correspondiente para trabajar luego con el piñón adecuado a su requerimiento. La máquina posee dos rodillos con un dibujo dentados donde uno solo gira y el otro queda suelto. Estos rodillos deben seleccionados previamente a realizar la operación, debido a que varían dependiente el tipo de motor a hacer. El operario centra el eje en el hueco entre ambos rodillos y acciona la máquina. Los rodillos giran a una cierta velocidad con el objetivo de generar mediante presión y rozamiento el dibujo en el eje.
TAPAS
Se retiran las tapas de depósito.
Clavado de rulemanes (Prensadora Hidráulica): su fin es insertar un rodamiento (ruleman) en la tapa para facilitar el giro del eje y reduzca su fricción con la tapa. Para ello, el operario monta la tapa de aluminio sobre una superficie hembra que posee la misma forma de la tapa. Esta entra por encastre dentro de la cavidad quedando fija sin ningún tipo de sujetador. El operario coloca el rodamiento en el orificio y acciona la prensa realizando el aprisionamiento de los rulemanes dentro del orificio. Se debe repetir el procedimiento para la tapa siguiente, ya que el motor contiene dos tapas.
ENSAMBLE
Para este proceso solamente se requerirá de un puesto de trabajo manual. Primero, el operario centra el estator en el interior de la tapa de la parte de abajo. Seguidamente, introduce el eje con su respectivo rotor acoplado dentro del estator, haciéndolo pasar por el orificio de la tapa. Por último, cierra el motor con la tapa de la parte superior y utiliza tirante a los costados para sellar. La parte eléctrica del motor queda completamente terminada.
Luego se efectúa un control del correcto funcionamiento del motor durante 2 minutos en el cual se le coloca una mordaza conectada a corriente, y se analiza el funcionamiento, si ocurre algún error en el mismo se desarma y se lo corrige.
EMBALADO
Se coloca el motor ya terminado en cajas de cartón individuales, se le sella el numero de lote, fecha y hora, se pega las etiquetas correspondientes y por ultimo se llevan al depósito de producto terminado.
Determinación de las máquinas e instalaciones.
Especificaciones técnicas de las máquinas.
Cortadora de Metales
CARACTERISTICAS TECNICAS | |
Modelo | Modelo Z8 CN Manual |
Capacidad de corte rectangular | 250x330 mm |
Capacidad de corte redondo en | 250 mm |
Dimensión de la cinta en | 3600x27x0.9 mm |
Potencia motor principal | 0.7457 kw |
Potencia motor refrigerante | 0.089 kw |
Velocidad de la cinta | 30-60-90 m/min |
Capacidad liquido refrigerante en litros | 20 |
Diámetro de volantes en mm | 380 |
Peso aproximado en kg | 377 |
Dimensiones: largo, ancho y alto en mm | 1850 x 750 x 1200 |
Tensión de hoja | Manual |
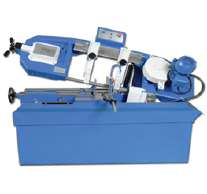
Aisladora de Mylar
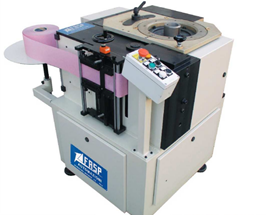
CARACTERISTICAS TECNICAS | |
Modelo | IFC7.01 FLEX |
Potencia | 2.2 Kw |
Cos fi | 0.74 |
Velocidad de giro | 1430RPM |
Peso | 600kg |
Dimensiones: largo x ancho x alto | 750 x 1100 x 1000 mm |
Alimentación | 3 x 400 V |
Frecuencia | 50hz |
Insertadora de Cobre
CARACTERISTICAS TECNICAS | |
Modelo | IMS6.04 |
Velocidad | 1450 rpm |
Presión Máxima | 100 bar |
Peso | 1000kg |
Dimensiones: largo x ancho x alto | 800 x 2500 x 3000 mm |
Alimentación | 3 x 400 V |
Frecuencia | 50 hz |
Potencia | 7.5 Kw |
Tiempo Inserción Mínimo | 15 seg |
Tiempo Inserción Máximo | 25 seg |
Velocidad de Trabajo | 2500/10000 mm/min |
Inserción máxima eje de carrera | 500mm |
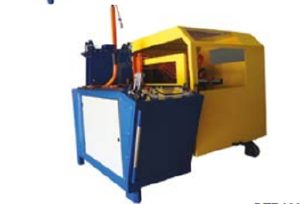
Bobinadora
CARACTERISTICAS TECNICAS | |
Modelo | DTR80 |
Alimentación | 400 V |
Frecuencia | 50hz/60hz |
Potencia | 1.1 Kw |
Dimensiones ( Largo x Ancho x Alto ) | 1700 x 1800 x 1950 |
Peso | 550kg |
Velocidad | 15-80rpm |
Diámetro bobinas | 800mm |
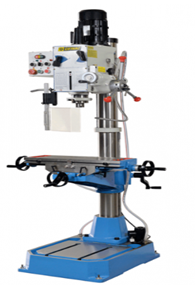
Perforadora
CARACTERISTICAS TECNICAS | |
Modelo | ZX40 |
MÁXIMA CAPACIDAD DE PERFORADO | 40mm |
MÁXIMA CAPACIDAD DE FRESADO – PLANEADO | 80 mm |
MÁXIMA CAPACIDAD DE FRESADO – RANURADO | 22 mm |
RECORRIDO DEL HUSILLO | 110 mm |
VELOCIDAD DEL HUSILLO | 6 (50-1260 rpm) |
CONO DEL HUSILLO: | MORSE 4 |
DISTANCIA HUSILLO | 272mm |
DISTANCIA HUSILLO – MESA DE TRABAJO | 745mm |
BAJADA DE HUSILLO | Automática |
DIAMETRO PINULA DE HUSILLO | 75mm |
DISTANCIA NARIZ HUSILLO A LA BASE: | 1245mm |
DIMENSIÓN DE LA MESA DE TRABAJO: | 585 x 190 mm |
RECORRIDO DE LA MESA | 370 x 140 x 515 mm |
TIPO DE CABEZAL | Caja de engranajes |
CABEZAL ROSCADOR | Hasta 16 mm |
TIPO DE COLIZAS: | 115 mm |
POTENCIA DEL MOTOR PRINCIPAL | 1.5 kW |
DIMENSIONES DE LA BASE | 690 x 520 mm |
PESO | 360kg |
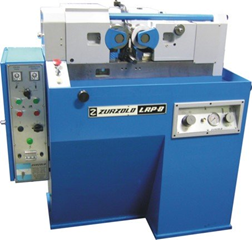
Laminadora
CARACTERISTICAS TECNICAS | |
MODELO | LRP-8 |
PRESION MAX. REGULABLE | 8 TONELADAS |
VELOCIDAD DE PENETRACION | REGULABLE |
DIAMETRO MAX. DE PIEZA | 25,4 MM |
DIAMETRO MIN. DE PIEZA | 0 MM |
ANCHO MAX. DE RODILLOS | 60 MM |
DIAMETRO MAX. DE RODILLOS | 115 MM |
DIAMETRO MIN. DE RODILLOS | 85 MM |
PASO MAXIMO | 3 MM |
INCLINACION MAX. DE CABEZALES | 0º |
DIAMETRO DE LOS EJES | 40 MM |
VELOCIDAD DE LOS EJES | 58-84 RPM |
MOTOR PRINCIPAL | 2.2kW |
MOTOR HIDRAULICO | 1.5 kW |
PESO NETO | 700 KG |
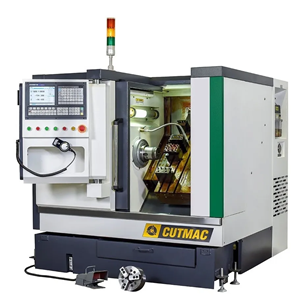
Torno CNC
CARACTERISTICAS TECNICAS | |
Modelo | HTC 1612 |
Diámetro máximo sobre la bancada | 450 mm |
Peso | 2400kg |
Dimensiones: largo x ancho x alto | 1660 x 1665 x 1540 mm |
Agujero de la nariz del husillo | 1:20 (Ø50) |
Pasaje de barra del husillo | 48 mm |
Rango de velocidades del husillo | 40 – 5000 |
Carga máxima sobre el husillo: 80 Kg | 80 kg |
Diámetro máximo admisible | 450 mm |
Largo máximo torneable | 120 mm |
Máximo diámetro torneable sobre carro | 160 mm |
Máximo torque | 64 N.m |
Dimensión de las Herramientas | 20 x 20 mm |
Avance rápido eje x/ eje z | 24 mts/min |
Carrera del eje x / eje z | 350 mm / 125 mm |
Potencia del motor | 7.5 Kw |
Motor Refrigeración | 0.2 Kw |
Motor Hidráulico | 2.2 Kw |
Servo motor eje x / eje z | 1.9Kw / 1.9Kw |
Control numérico | 65 K 9810 TDc |
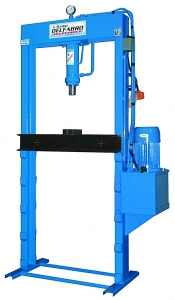
Prensa Hidráulica 15 ton
CARACTERISTICAS TECNICAS | |
Modelo | 15tn (60-005) |
Capacidad | 15tn |
Altura | 1600 mm |
Ancho | 780 mm |
Ancho columna | 120 mm |
Ancho útil | 660 mm |
Luz entre mesa | 120 mm |
Luz máxima vástago mesa | 200 mm |
Potencia motor | 1.5kW |
Peso | 120 kg |
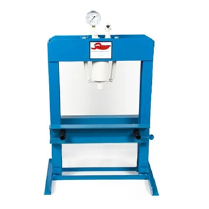
Prensa Hidráulica 10 ton
CARACTERISTICAS TECNICAS | |
Capacidad | 10tn |
Altura | 820 mm |
Ancho | 460 mm |
Carrera máxima pistón | 93 mm |
Peso | 34 kg |
Consumos de energía y servicios.
Consumo Electrico
items | Cantidad | Consumo individual (kWh) | Consumo Total (kWh) | Consumo Diario (kWh) | Consumo mensual (kWh) |
Cortadora de Metales (motor principal) | 1 | 0,7457 | 0,7457 | 5,9656 | 131,2432 |
Cortadora de Metales (motor refrigerante) | 1 | 0,089 | 0,089 | 0,712 | 15,664 |
Aisladora de Mylar | 1 | 2,2 | 2,2 | 17,6 | 387,2 |
Insertadora de Cobre | 1 | 7,5 | 7,5 | 60 | 1320 |
Bobinadora | 1 | 1,1 | 1,1 | 8,8 | 193,6 |
Perforadora | 1 | 1,5 | 1,5 | 12 | 264 |
Laminadora (motor principal) | 1 | 2,2 | 2,2 | 17,6 | 387,2 |
Laminadora (motor hidraulico) | 1 | 1,5 | 1,5 | 12 | 264 |
Torno CNC (motor principal) | 1 | 7,5 | 7,5 | 60 | 1320 |
Torno CNC (motor refrigeracionl) | 1 | 0,2 | 0,2 | 1,6 | 35,2 |
Torno CNC (motor hidraulico) | 1 | 2,2 | 2,2 | 17,6 | 387,2 |
Torno CNC (servomotor) | 1 | 1,9 | 1,9 | 15,2 | 334,4 |
Prensa Hidráulica | 1 | 1,5 | 1,5 | 12 | 264 |
Luminaria Led | 91 | 0,01 | 1,00 | 8,01 | 176,18 |
Luces de emergencia | 9 | 0,01 | 0,09 | 0,36 | 0,36 |
Ventiladores | 4 | 0,2 | 0,8 | 4,8 | 105,6 |
Aire acondicionado | 5 | 1,09 | 5,45 | 32,7 | 719,4 |
Modem | 1 | 0,006 | 0,006 | 0,144 | 4,32 |
Router | 1 | 0,006 | 0,006 | 0,144 | 4,32 |
Impresora | 2 | 0,15 | 0,3 | 0,3 | 6,6 |
Computadora | 7 | 0,4 | 2,8 | 22,4 | 492,8 |
Telefono | 7 | 0,0012 | 0,0084 | 0,0504 | 1,1088 |
Heladera | 1 | 0,08 | 0,08 | 1,92 | 57,6 |
Microondas | 1 | 1,3 | 1,3 | 1,3 | 28,6 |
Cafetera | 1 | 0,72 | 0,72 | 2,16 | 47,52 |
Total | 315,364 | 6948,112 |
Consumo de agua
Considerando los siguientes datos:
-Descarga de inodoro: 6 litros, 3 veces por día por persona.
-Lavado de manos/cara: 4 litros, 3 veces por día por persona.
-Consumo agua en cocina por persona por dia: 2 litros
-Cantidad de Empleados: 14
items | consumo diario (lt) | consumo mensual (lt) |
Baños | 420 | 9240 |
Cocina | 28 | 616 |
Total | 448 | 9856 |
Servicio de Intenet
Internet 300 megas con wifi y cableado.
Mantenimiento y medios de control.
Mantenimiento máquinas:
Se realizará un control de aceite cada 15 días en todas las prensas además de controlar que tengan un nivel de presión adecuado y en los engranajes de la fresadora.
Se rellenará el líquido refrigerante del Serrucho cada 3 días.
Se realizará diariamente el engrasado de uniones para un correcto patinaje en la insertadora.
Se realizará diariamente el pulido y la colocación de w40 en la bobinadora para que el cobre
Se realizará el cambio de aceite de forma diaria en la laminadora.
Sistemas de seguridad: se contará con los matafuegos y salidas de emergencia reglamentarias, se les brindara a los operarios la ropa adecuada para realizar sus tareas y proteger su seguridad.
Además se contaran con los tableros con sus medios de control necesarios para proteger a los empleados de fallas eléctricas y para poder controlar la producción.
Cálculos:
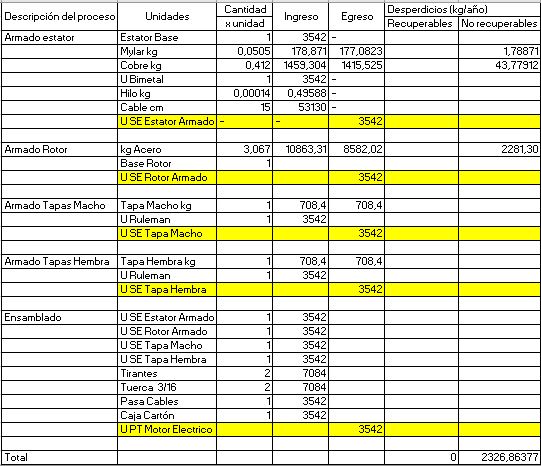
Ritmo de Trabajo
La empresa trabajará en 1 turno de 8hs, de Lunes a Viernes, cerrará 10 días al año por feriados obligatorios y no cerrará por vacaciones ya que el personal deberá tomarse las mismas de forma rotativa de modo de no cerrar la empresa por vacaciones.
Por lo tanto los días activos por año serán 260, y las horas activas anuales 2080.
Las horas por año trabajadas por cada operario serán de 2080., ya que se trabaja un solo turno.
Capacidad Real Anual de Sección Operativa.
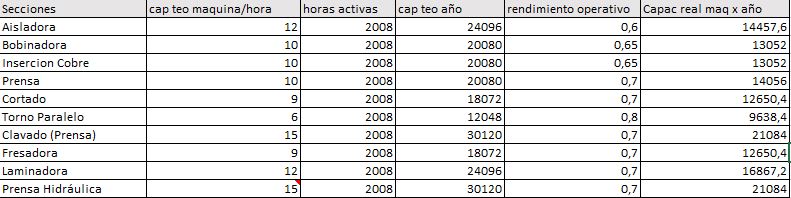
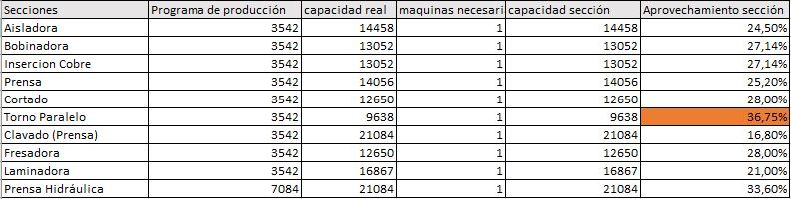
Al tener un aprovechamiento muy bajo de las secciones, principalmente en el Torno CNC, se pordía tomar como opción vender la capacidad ociosa a otras empresas.
En este gráfico notamos que nuestro cuello de botella será la prensa hidráulica, la que nos define la capacidad real anual de la fabrica en 21.840 motores por año.

Determinación de la evolución de las mercaderías
Se recibirán los pedidos y se realizarán envíos de forma semanal, con la cantidad de motores solicitados.
Cada pedido de los distribuidores varía entre 20 y 50 motores por distribuidor y dependiendo del tamaño del mismo.
Las materias primas se adquirirán de manera mensual; su tiempo de reposición no es alto.
Se fabricara semanalmente en lotes de 70 motores.
Según información brindada por el tecnólogo, el período de puesta en marcha requerirá 4 meses en los cuales se incrementara la producción de forma lineal cada mes, a 10%, 40%, 75%.
Evolución de la producción.

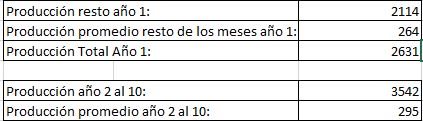
En el período de puesta en marcha se estimo que se realizarán desperdicios equivalentes al 1% de los motores fabricados por errores en el aprendizaje, por lo que el desperdicio total en este período será de 5 UE PT.
Al trabajar de forma semanal en lotes de 70 motores, el stock de producto terminado variará entre 0 y 70, por lo que el stock promedio sera de 35 Motores Terminados.
Por lo tanto al ser el primer año el momento donde genero mi stock de PT, las ventas serán:
Año 1: 2596.
Año 2: 3542.
Mercadería en curso y semielaborados.
Nuestro ciclo productivo es de 70 motores por semana, por lo que la mercadería en curso sera de 0,071 UEPT.
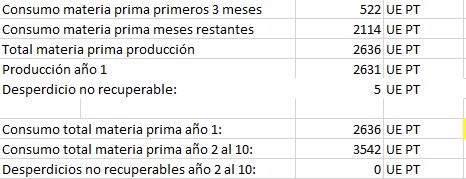
Stock promedio materia prima y programa de compras.
Se querrá tener un stock de matería prima para la fabricación de 1 mes y medio.
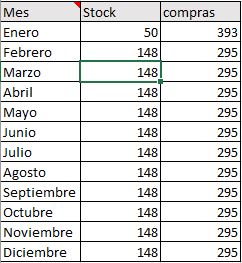
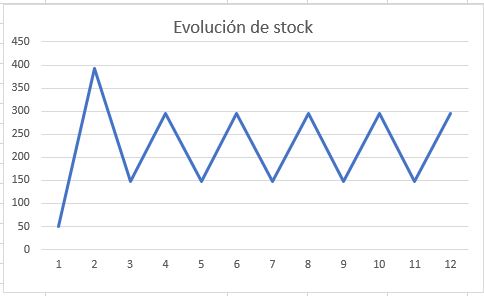
Cuadro Resumen del Programa General de Producción.
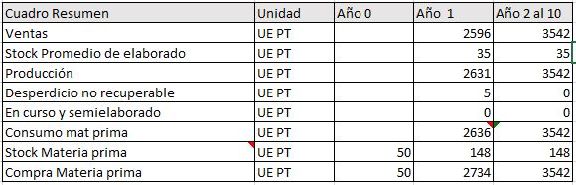
En este cuadro se encuentran detalladas en UE PT el programa general de producción, los desperdicios no recuperables de los materiales no son tenidos en cuenta en este cuadro y se detallaran en los cuadros posteriores. El desperdicio no recuperable que figura en el cuadro corresponde a la cantidad de UE PT generados en el período de puesta en marcha.
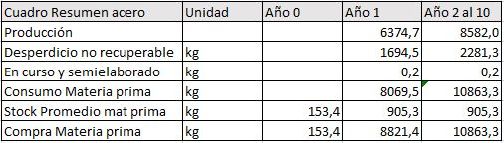
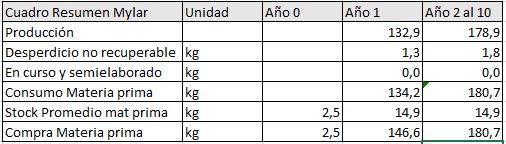
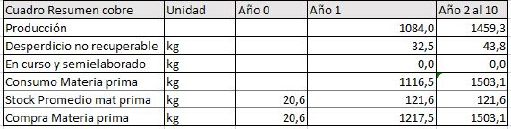
Determinación del Personal
Organigrama
Descripción de los puestos de trabajo.
Director general: Será la cabeza de la empresa, cada área le deberá rendir cuentas a él. Será la figura líder de la empresa y deberá tener el conocimiento necesario y las aptitudes para tomar las decisiones pertinentes. Será Preferentemente un Ing. industrial/Administrador de empresas con experiencia y conocimiento del rubro.
Ventas: se encargará de la relación con los distribuidores, será de suma importancia el conocimiento del producto y del proceso productivo ya que se encargará de capacitar a los vendedores de los distribuidores, realizar programas con los mismos y deberá entablar y mantener buenas relaciones que permitan la recomendación de nuestro producto.
Serán 2 empleados que deberán tener buen don de gente, experiencia y conocimiento sobre el B2B.
Administración: se encargará de la parte impositiva y contable de la empresa así como también de las cobranzas, pago a proveedores, facturas, Estará compuesto este sector por 2 personas, 2 contadores públicos con experiencia impositiva y contable..
Compras: 1 encargado se ocupará de la relación y negociación con los proveedores además de la ejecución de las compras.
Logística: Se encargará de la organización y planificación de la entrega de mercadería a distribuidores, de la llegada de materiales de los proveedores y de la entrada y salida de motores a los laboratorios IRAM.
Producción: Habrá un jefe de planta que será el encargado de la planificación y control del sistema productivo, deberá gestionar los recursos disponibles y mantendrá una estrecha relación con las áreas de compras y ventas.
Operarios: Se requerirán 6 operarios que se distribuirán de la siguiente manera: 1 en torno CNC y serrucho neumático, 1 en la prensa neumática, 1 en la fresadora y laminadora, 1 operario encargado de la aisladora, insertadora y bobinadora, 1 operario encargado de realizar el cosido y el ensamblado y 1 encargado de las prensas hidráulicas.
Estos operarios deberán tener los conocimientos básicos con respecto a las máquinas que operarán, la forma de trabajo y su mantenimiento, deberán contar con experiencia en el rubro y deberán pasar un proceso de capacitación. Serán preferentemente operarios con estudios secundarios técnicos.
Las distintas actividades que se realizarán en cada máquina fueron detalladas con anterioridad.
Listado de equipos auxiliares, muebles y útiles.
Producción:
Elementos de protección personal
Carteles de seguridad
Matafuegos
Luces
Luces de emergencia
4 Ventiladores
Sistema de ventilación
7 lockers para guardar elementos de uso personal
1 aire acondicionado frío/calor
1 Pizarra de corcho 1,20m x 0,80m
2 Mesas de trabajo
2 Sillas
Vestuarios: con 6 lockers, 4 inodoros, 1 espejo, 2 canillas, 2 lavamanos, 1 tacho de basura
Cestos de residuos
1 zorra manual
Estanterías para depósito.
2 rodados para vendedores.
Oficinas:
Modem y router
Luces de emergencia
Matafuegos
Cajoneras
Armarios
Estantería
Luces
Elementos de librería (lapiceras, tijeras, hojas, lápices, agujereadora, cuadernos, carpetas)
4 Aires Acondicionados
2 impresora
2 abrochadoras
7 sillas ergonómicas
7 escritorios
7 computadoras
7 teléfonos
8 cestos de residuos
Carpetas archivadoras (remitos, facturas, impuestos)
2Baños separados, 2 inodoros, 2 espejo, 2 canilla, 2 lavamanos, 2 tacho de basura
Cocina:
2 mesas
7 sillas
1 mesada cocina
1 heladera
1 microondas
1 cafetera
1 lavamanos
1 horno
1 cesto de residuos
Utensilios de cocina
Anteproyecto de planta
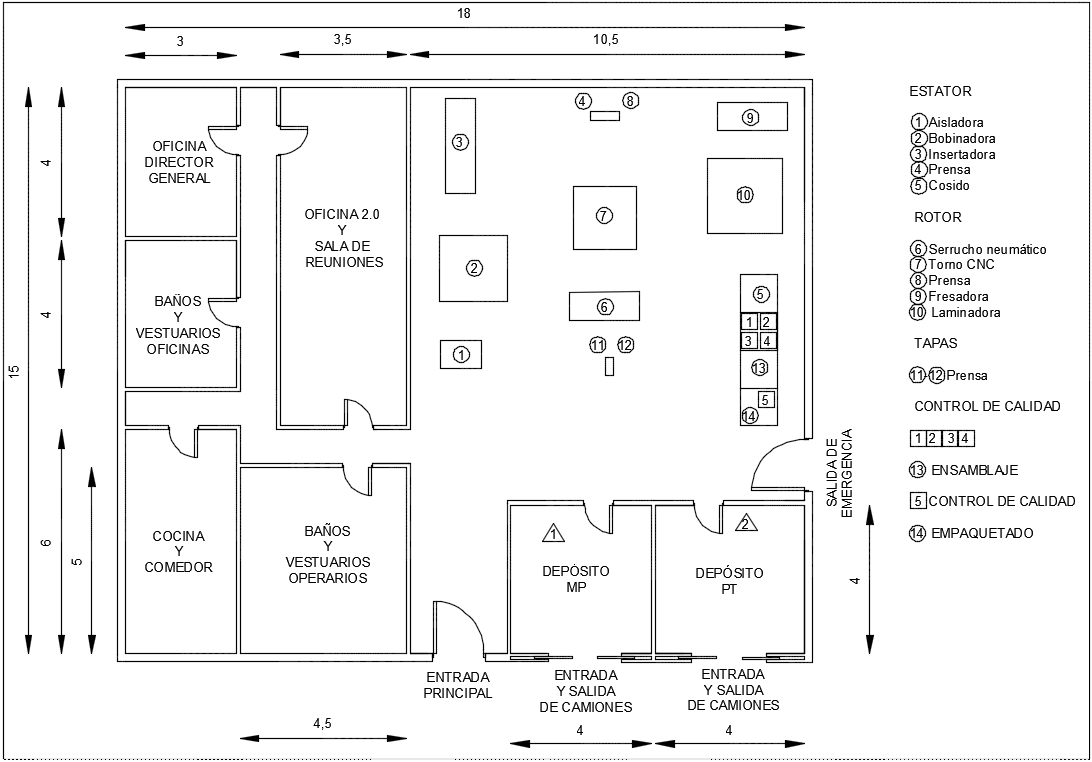

Cronograma de ejecución
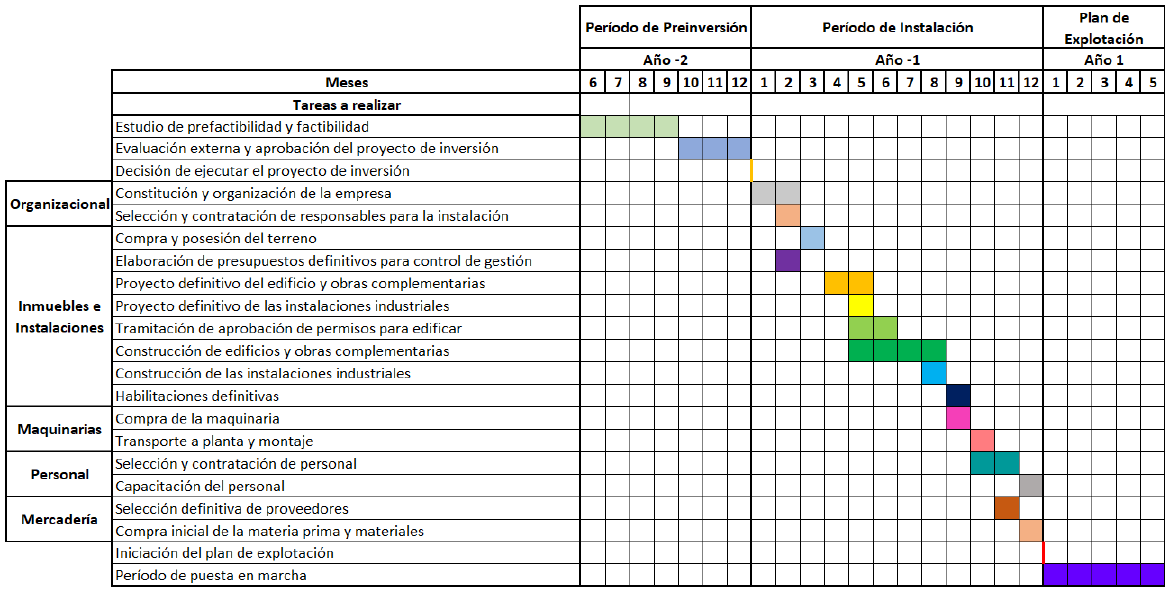