2023/Grupo4/DimensionamientoFisico
Determinación de la Localización
Matriz de Localización
Luego de realizar una investigación, encontramos tres posibles lugares en donde establecer la planta y las oficinas de la empresa. Estos son el parque industrial 9 de abril (rojo), el parque industrial de Gerli (amarillo) y un lote disponible en la zona industrial del barrio de Barracas en la Capital Federal.
A continuación un mapa con las principales opciones. En base a ellas se realizará la matriz de localización.
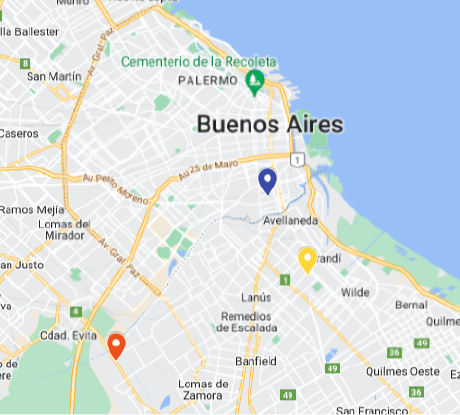
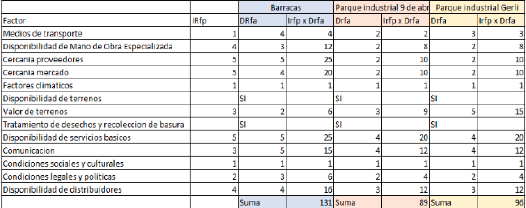
Las principales diferencias entre las opciones se dan en la cercanía de los proveedores y del mercado. Barracas al encontrarse en el sur de la capital tiene mayor cercanía con proveedores y con las ortopedias y clínicas, que la mayoría están en la capital federal. Por otra parte, una de sus ventajas es que hay mayor disponibilidad de mano de obra y que tiene una mayor posibilidad de acceso con medios de transporte público.
La empresa se va a encontrar ubicada en Santa María del Buen Ayre 347, Barracas. El terreno es de 345.95m2 total de los cuales 320m2 van a ser cubiertos por lo que nos permite poder tener espacio y contar con una zona de trabajo espaciosa, lugar de oficinas para la administración y alta dirección. Para el almacenamiento de los productos terminados y para inventarios se va a disponer de un almacén con 56.46m2.
Esta ubicación fue seleccionada ya que, para nuestro rubro, es de fácil acceso para la distribución del producto. La nave industrial cuenta con una entrada de camiones, la cual facilitara la carga y descarga de la mercadería y/o productos.
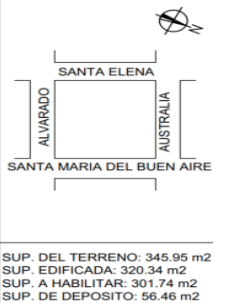
Definición Técnica del Producto.
Planos y/o Dibujos.
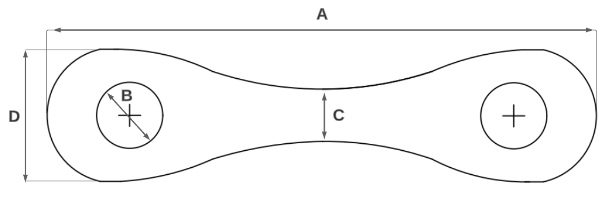
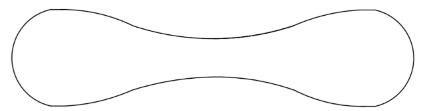
Tamaño de articulación** | COTA A | COTA B | COTA C | COTA D | UNIDAD |
Chica | 3,5 | 0,44 | 0,38 | 1 | cm |
Mediana | 4 | 0,5 | 0,5 | 1,1 | cm |
Grande | 4,5 | 0,7 | 0,6 | 1,3 | cm |
**Los dummies tienen las mismas medidas que la articulación correspondiente a su tamaño. No tienen un agujero interior.
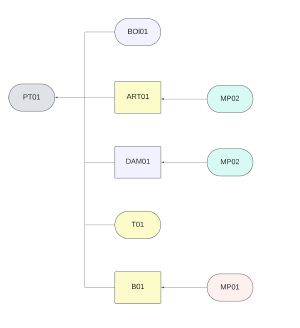
Listado de Materiales (BOM).
ITEM | DESCRIPCIÓN | NIVEL | CANTIDAD | UNIDADES |
PT01 | Producto terminado | 0 | 1 | Unidad |
BOL01 | Bolsa plástica para empacar | 1 | 1 | Unidad |
ART01 | Articulación plástica | 1 | 2 | Unidad |
DAM01 | Dummie | 1 | 2 | Unidad |
T01 | Tornillo | 1 | 4 | Unidad |
B01 | Buje | 1 | 4 | Unidad |
MP01 | Barra de acero | 2 | 4 | Unidad |
MP02 | NYLON | 2 | 17,5* | gr |
* Para cada tamaño y dureza diferente que vamos a ofrecer se utilizan diferentes cantidades de pellet, para facilitar los cálculos vamos a tomar el valor promedio.
Especificaciones Técnicas.
La articulación Tamarack es una producto que consiste en unas piezas de nylon en las que en su interior llevan unos flejes especiales que permiten su elongación. Las articulaciones se suelen utilizar como articulaciones de tobillo, aunque también se pueden utilizar como articulaciones de codo. Las articulaciones Tamarack se alinean automáticamente con los ejes articulares medial y lateral. El exclusivo núcleo de filamento interno de alta resistencia evita el alargamiento y garantiza una acción de articulación precisa.
Bolsa plástica: Material de polietileno que se obtendrá de proveedores. Su función es contener el conjunto de piezas que recibirá el cliente. Estos son 2 dummies, 2 articulaciones, 4 tornillos y 4 bujes. Además, el rótulo irá sobre esta bolsa.
Articulaciones plásticas: Pieza de plástico que se fabricará en la planta. Se ofrecerán de diferentes tamaños y durezas, para que esto sea posible se utilizan diferentes cantidades de pellet
Dummie: Pieza de plástico que el cliente utilizará para marcar la ubicación de la articulación en el moldeado de la ortesis. Esta también se fabricará en la planta y tiene las mismas características que la articulación, excepto que no tiene los agujeros interiores.
Se coloca sobre el molde de la bota. Se moldea el plástico encima del positivo, se extrae el vacío y se espera que enfríe. Cuando enfría el plástico se corta y se saca el dummie introduciendo en su lugar la articulación Tamarack
Tornillo: Pieza metálica que el cliente utilizará para unir la articulación con la ortesis. Esta se obtendrá de un proveedor.
Buje: Es una pieza de acero que se utilizará junto con el tornillo para unir la articulación con la ortesis, esta se fabricará en la planta. Este facilita el movimiento de la articulación.
Normas Aplicables.
El producto entra en la categoría de productos médicos, por lo que debe estar autorizado por la Administración Nacional de Medicamentos, Alimentos y Tecnología Médica (ANMAT). Para lograr está autorización el producto debe registrarse como producto médico bajo siguiendo la disposición 727/2013 y la Disposición 2318/2002.
Para esto es necesario que la empresa esté certificada bajo la norma de “Buenas prácticas de fabricación y productos médicos” Disposición Nº 3266/2013 ya explicada en el dimensionamiento comercial. Ambas disposiciones disponen que es obligatorio el cumplimiento de los requisitos dictados por 'REGLAMENTO TÉCNICO MERCOSUR DE REGISTRO DE PRODUCTO MEDICOS' (Resolución GMC N° 40/00).
Acondicionamiento del Producto
El producto se almacena embalado dentro de la bolsa plástica sellada. Este no necesita de ningún acondicionamiento especial para el almacenado. La única condición es evitar el almacenamiento a la intemperie porque los rayos solares pueden alterar las propiedades del plástico, al igual que las altas temperaturas. Además, no se debe almacenar sometiendo a las piezas a presiones, pesos y fuerzas, ya que el sometimiento continuo puede deformar plásticamente la pieza.
En cuanto al embalaje, este dependerá de la cantidad pedida por el cliente. Se agruparán las bolsas en cajas de cartón, no es necesario colocar papel burbuja o envoltorios especiales ya que las piezas no son frágiles. Adicionalmente, se puede agregar una etiqueta en el exterior indicando la cantidad de packs entregados y una aclaración de no exponerlo a altas temperaturas.
Plan de Ensayos
No se realizara un plan de ensayos especial para la produccion. Se controlara pieza por pieza antes del empaque y el rotulado de las mismas. El proceso de control esta explicado en la siguiente seccion.
Definición del Proceso de Producción.
Diagrama de Flujo de Fabricación y Control. Cursogramas gráficos o analíticos.
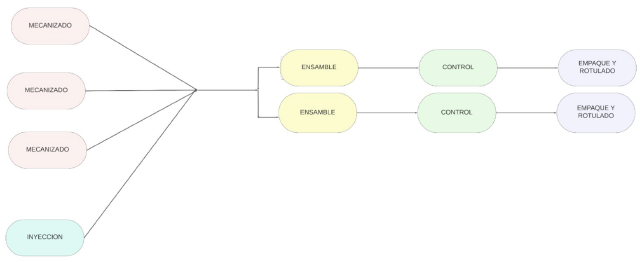
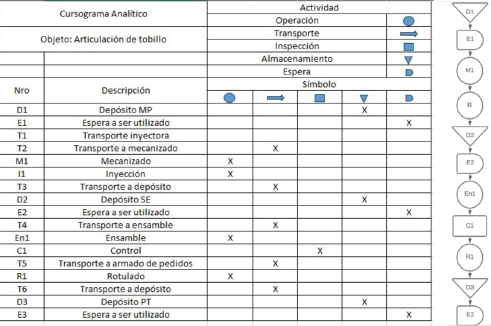
Etapas del proceso productivo
El producto terminado consiste en los siguientes proceso:
- Mecanizado: Este es el primer proceso luego de recibir la materia prima. En el se reciben las barras de acero que son necesarias para realizar los bujes. Para iniciar el proceso el operario coloca la barra en el torno cnc ,a cual sigue la siguiente secuencia:
- Agujero interno
- Roscado
- Fresados laterales
- Corte
Una vez terminado el lote de producción, los bujes son trasladados a la zona de ensamble.
Otras consideraciones del proceso:
El buje es de 1cm y las barras vienen de 3 metros.
Existen 0,5mm de despunte 3mm por corte.
Tiempo de mecanizar cada buje: 5min.
- Inyección: Junto al mecanizado también es el primer proceso de la producción ya que funcionan en paralelo. Comienza con la recepción del nylon seguido de un secado de materia prima por 24 horas con un horno Mufla. Luego se carga la inyectora al máximo (20kg de plástico) Y se procede de la siguiente manera:
- Se coloca la matriz en la inyectora para la medida que se desea fabricar (La matriz es para realizar de a 2 piezas) (1 matriz para el dummie y otra para la pieza) (1min)
- Se calibra la inyectora de acuerdo a la matriz previamente colocada, se ajustan parámetros de temperatura y cierre de la matriz. (30 min)
- Se pone en funcionamiento la inyectora
- A medida que se termina cada par de piezas, se debe retirar de la matriz (2min por par)
- Repetir el proceso hasta finalizar la capacidad de la inyectora o el cambio de matriz
- Rebabar las piezas (30s por par) con rebabador manual.
- Transportar el semielaborado al puesto de ensamble.
Consideraciones: Para cumplir tiempos de entregas se dispondrán de 4 hornos mufla.
- Ensamble :
Se toman los semielaborados provenientes de la inyectora, se le coloca el buje y luego los tornillos estándar.
- Control:
Se controlan las muestras, tanto de forma visual (revisar que todos los componentes calcen entre sí), (adicionalmente, a lo largo de todo el proceso productivo siempre se lleva un control superficial del producto)
- Empaque y rotulado :
Para el empaque se coloca dentro de la bolsa plástica el conjunto y con la selladora se sella la bolsa.
Por último, se procede a rotular el conjunto de semielaborados, conformando así el producto terminado, para su posterior distribución. Este proceso debe cumplir con el siguiente procedimiento:
- El Aseguramiento de la Calidad deberá imprimir dos tipos de rótulos para cada tipo de producto.
- El rótulo N°1 debe contener como mínimo:
- Fabricado por….
- Dirección C.A.B.A (código postal).
- Dtor.Tec.:
- Autorizado por ANMAT (PM-LLLL-XX)
3. El rótulo N°2 debe contener como mínimo:
- Código del Producto.
- Descripción del Producto.
- Código de barras.
- Número de lote.
- Número de serie.
Determinación de las máquinas e instalaciones. Cálculos.
Especificaciones técnicas de las máquinas (capacidades, tamaño de lotes, tiempos).
Horno mufla para laboratorio:
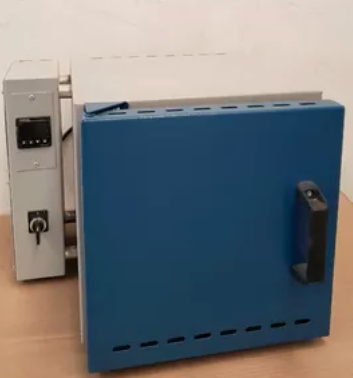
Características:
Potencia: 1800 W
Capacidad en volumen: 1.5 L
Temperatura máxima de funcionamiento: 1200 °C
Largo x Altura x Profundidad: 100 mm x 100 mm x 150 mm
Mediante el uso de este horno se seca el plástico antes de ser enviado a la inyectora. La densidad del plástico de nylon es de 1,15 kg/l. Teniendo en cuenta este dato, el horno puede procesar 1.725 kg de plástico por sesión. La temperatura de fusión del nylon es 268 °C, para secarlo debemos calentarlo a una temperatura de 120°C y durante 24 horas.
Torno Cnc- Gsk 750mm:
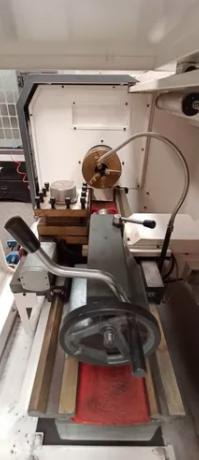
Características:
Potencia del motor principal: 7 hp = 5220 W
Control del torno: GSK
Diámetro máximo de volteo: 200 "
Distancia entre puntas: 750 mm
Este torno se utilizará para el mecanizado de bujes. El torno puede trabajar únicamente una pieza a la vez. Se calculó que cada buje toma un tiempo de 5,44 minutos para ser mecanizado.
Desbabador manual:
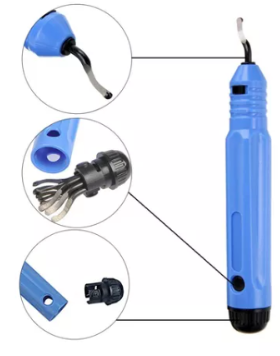
Procesa una pieza por vez, tardando un aproximado de 0,5 minutos por par.
Inyectora Babyplast 6/12 LSR:
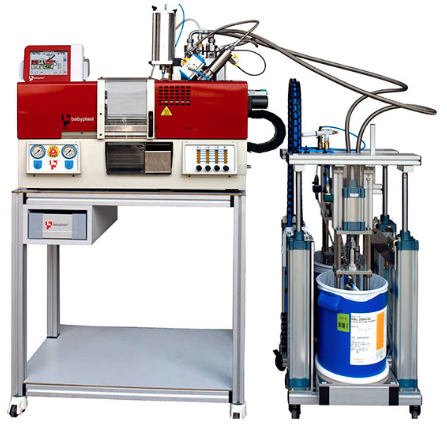
Características:
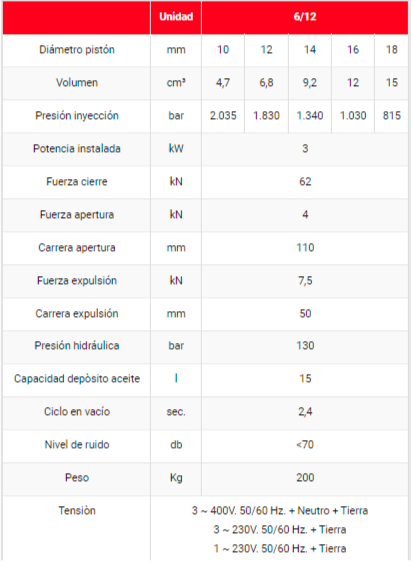
La inyectora tiene una capacidad de 20kg. Considerando que el par de piezas en promedio tiene 17gr, la inyectora por proceso de inyección puede fabricar 500 conjuntos, un conjunto contiene un par de dummies y un par de articulaciones.
La máquina puede procesar 500 conjuntos en 1312 minutos.
Selladora:
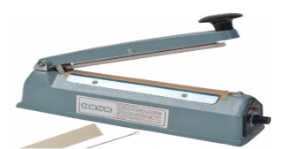
Características:
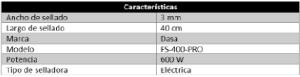
La selladora trabaja una sola bolsa a la vez, cada bolsa contiene 4 piezas que representan un conjunto. Y el tiempo de operación por bolsa se estima en 2,5 minutos (1250 minutos por lote) debido a que lo único que se debe hacer es apoyar el borde de la bolsa sobre la guillotina de la selladora. Bajar el brazo de la máquina y mantener la presión sobre la bolsa para que se selle. A ese tiempo se le suman 3 minutos de demoras técnicas de preparación en el que se establece la temperatura de operación de la selladora y se debe esperar hasta que se caliente. Esta demora técnica es única y ocurre cada vez que se enciende la máquina.
Consumos de energía, agua y otros servicios.
Para la utilización de estas máquinas se consume principalmente energía eléctrica. La selladora consume una potencia de 600W y la inyectora toma una potencia de 3 kiloWatts para su funcionamiento, en cuanto al horno su consumo energético es de 1,8 kiloWatts. Además como el proceso no requiere del uso de gas y agua el único consumo de estos servicios se atribuye a la planta o a otros productos que se fabriquen en ella. A continuación presentamos el cuadro del consumo eléctrico considerando la totalidad de horas que se utilizará cada máquina durante el desarrollo de la producción para el cumplimiento del plan de ventas establecido.
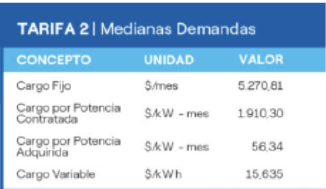
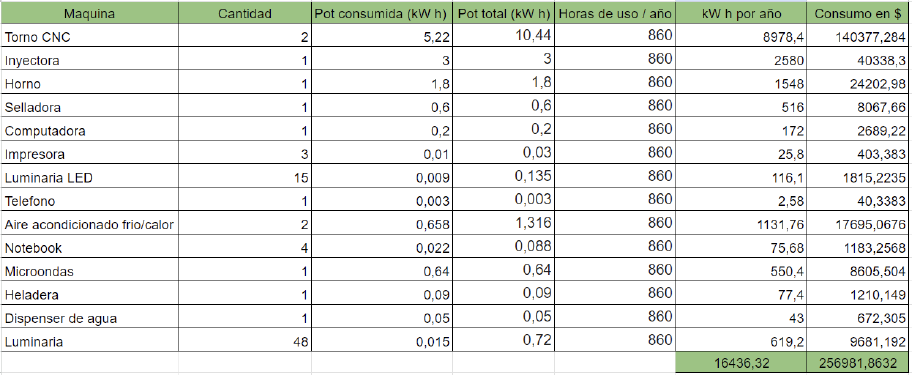
Por otra parte el consumo de energía eléctrica en luminaria y otros se va a añadir al consumo de las maquinarias.
En Argentina se calcula que una persona consume cerca de 3000kw h por año, teniendo aproximadamente 8,2 kw h diarios consumidos por persona.
Al tener 14 trabajadores se calcula que el consumo diario total será alrededor de 115 kw h, con aproximadamente 575 kw h por semana. Cabe aclarar que este cálculo se realizó en base a un consumo promedio. Posteriormente para calcular más precisamente el consumo anual se deberían considerar feriados, vacaciones, y otros factores como paros o ausencias que afectan el consumo.
El proceso productivo no requiere el consumo de agua corriente, por ende la cantidad de litros consumidos dependerá de la cantidad de empleados y el consumo para higiene y sanitarios. La empresa va a tener 14 trabajadores en un principio, contando tanto a los empleados de planta como a los administrativos.
Esto indica que en promedio se van a consumir alrededor de 660 litros de agua corriente en los días laborales, y alrededor de 3300 litros por semana.
Segun la OMS una persona consume al rededor de 50 litros de agua corriente al dia.
Mantenimiento y medios de control. Descripción de los sistemas de seguridad.
- Inyectora - Como forma de mantenimiento optamos por el mantenimiento de tipo preventivo para la inyectora, cada 20 ciclos de inyección se revisará que no hayan quedado grumos o plásticos solidificados en los conductos y en el barril o en la tolva. En caso de existir se deben quitar porque entorpecen el flujo. Además cada 10 ciclos de inyección se deberá verificar que en las matrices no se hayan quedado partículas y residuos plásticos pegados que están fuera de lugar, porque eso puede deformar al producto.
- Torno - Cada 50 piezas se realizará una revisión del torno principalmente que se encuentre alineado y que tanto el carro como el cabezal no tengan partes flojas o desajustadas.
- Horno mufla - se limpiará el exterior semanalmente con solución no abrasiva. Se deberá asegurar que exista distanciamiento entre los hornos y los equipos que lo rodean para permitir la circulación de calor. Además, se programará un mantenimiento semestral en donde se calibra el horno para corregir desfases en la temperatura de trabajo que puede modificar las propiedades del pellet. Estos cuidados permiten maximizar la vida útil.
- Selladora - para maximizar su vida útil se debe realizar el recambio de la resistencia y de la lámina de teflón. La resistencia es una fina barra metálica que transporta la electricidad y la lámina transmite el calor a la bolsa para sellarla y evitar que el plástico se queme. Ambos ítems suelen durar 2 a 3 meses, pero como depende del uso que se le de a la máquina se debe hacer un seguimiento de la misma para identificar cuando se requiere el cambio, ambos elementos son económicos y fácil de intercambiar, no debería llevar más de 20 minutos
- Mantenimiento de planta:
- Se propone aplicar una política de mantenimiento preventivo en donde se revisan todas las máquinas antes de utilizarlas con el propósito de identificar y adelantarse a anomalías en su funcionamiento.
- A su vez, se cuentan con protocolos para llevar a cabo el mantenimiento correctivo en donde se realizará la parada de máquina, se dará aviso y el encargado de mantenimiento liderará al equipo para resolver el problema. En caso de que este persista se deberá consultar con especialistas en el tema.
- Dentro del ritmo de trabajo se asignan 6 dias para el mantenimiento programado de la planta, estos se planifican para diferentes etapas del año. En estos días se evaluarán las condiciones generales de la planta, los equipos, las instalaciones eléctricas, de agua, de red, el estado de los elementos de seguridad. Se controlará el estado de los equipos informáticos que se utilizan y se coordinaran revisiones con los técnicos. Además, se analizarán las condiciones edilicias, algunas acciones que se pueden llevar a cabo son la renovación de la pintura o el arreglo de algún sector en particular que haya tenido filtraciones de humedad. En estos días también se realizarán los mantenimientos correspondientes para cada una de las máquinas, como por ejemplo la calibración de la temperatura de los hornos.
Elementos de seguridad
Según la ley 13660 una planta que no trabaje con elementos inflamables como naftas y kerosene requiere una unidad de extintor por cada 300m2 de planta cubierta. En nuestro caso tenemos 320 m2 de planta, por eso se requerirán 2 extintores.
Cada puesto de extintor tiene una alarma de incendio para notificar a toda la planta. La planta cuenta con tres puertas para salida de emergencia. Cada sector tendrá asignada una salida de emergencia y los empleados recibirán una capacitación sobre el procedimiento de evacuación y cada sector de la planta va tener un plano con el recorrido para la evacuación.
En la planta los empleados tienen prohibido comer y beber, también el uso de anillos y joyas. El uso del celular no está permitido. Como elementos de protección personal los trabajadores tendrán que usar gafas de seguridad, ropa de trabajo y guantes de poliuretano.
Cálculos de los ejercicios 1 a 5 de la Guía de Trabajos Prácticos.
Balance anual de material
Una barra de acero pesa 2,68Kg para cada buje se utilizan 0,01054KG, como cada conjunto necesita de 4 unidades, se deberan producir 20400 bujes para una produccion anual de 5100 conjuntos. Se debera tener en cuenta que se pierden 0,045 kg por cada barra utilizada, lo que equivale a 250 bujes por barra. Ya que de una barra salen 250 bujes, se necesitaran 82 barras, es decir 219,76kg de acero. El desperdicio sale de hacer 81,6x0,045kg.
Seciones operativas | Alimentacion (Kg/Año) | Desperdicio Recuperable (Kg/Año) | Desperdicio No Recuperable (Kg/Año) | Producciones seccionales (Kg/Año) |
1 - Mecanizado | 219,76 | - | 3,672 | 216,09 |
2 - Inyección | - | - | - | - |
3 - Ensamble | - | - | - | - |
4 - Control | - | - | - | - |
5 - Empaque y rotulado | - | - | - | - |
Totales (Kg) | 219,76 | 0 | 3,672 | 216,09 |
Desperdicio operativo = Desperdicio real = 1,70% El desperdicio real es igual al operativo ya que no hay desperdicio recuperable.
En el caso del nylon, el tecnólogo informa que se desperdicia un 12,4% del total. Cada conjunto requiere 35gr de nylon por lo tanto para 5100 conjuntos 178500gr más desperdicios:
Seciones operativas | Alimentacion (Tn/Año) | Desperdicio Recuperable (Kg/Año) | Desperdicio No Recuperable (Kg/Año) | Producciones seccionales (Kg/Año) |
1 - Mecanizado | - | - | - | - |
2 - Inyección | 201 | - | 22,134 | 178,50 |
3 - Ensamble | - | - | - | - |
4 - Control | - | - | - | - |
5 - Empaque y rotulado | - | - | - | - |
Totales (Kg) | 200,63 | 0 | 22,134 | 178,50 |
Desperdicio operativo = Desperdicio real = 12,4% El desperdicio real es igual al operativo ya que no hay desperdicio recuperable
Ritmo de trabajo
Se toma un año comercial de 360 días.
Días en el año | 360 |
Vacaciones | 15 días |
Mantenimiento | 6 días |
Feriados | 20 días, |
Sabados | 52 días |
Domingos | 52 días |
Teniendo en cuenta estos datos, calculamos las horas activas por día, si la empresa trabaja de lunes a viernes 4hs diarias.
Semanas activas año | 43 semanas |
Meses activos/año | 10 meses |
Horas activas | 860 hs |
Capacidad real de la maquina por sección operativa
Cada lote contiene 510 unidades de productos terminados, esto se determinó debido a la restricción del sistema el cual es el proceso de ensamble, control, empaque y rotulado. Esto se puede ver mejor explicado en la consiga de tiempos de entrega.
Secciones | Capacidad Teórica / lotes x hora | Horas activas / año | Capacidad teórica / Lotes x año | Rendimiento operativo % | Capacidad Real / lotes x año |
1 - Mecanizado | 0,012 | 860 | 10,1 | 95% | 9,61 |
2 - Inyección | 0,022 | 860 | 18,8 | 80% | 15,03 |
3 - Ensamble+control+empaque y rotulado | 0,012 | 860 | 10,0 | 100% | 10,00 |
Determinación de la Cantidad de Máquinas Operativas por Sección. Capacidad Anual de cada Sección. Aprovechamiento según el Programa de Producción
Secciones operativas | Programa anual de producción (lotes) | Capacidad Real / lotes x año | Cantidad de máquinas necesarias | Capacidad Real/ sección x año | Aprovechamiento Seccional % |
1 - Mecanizado | 10 | 9,61 | 2,00 | 19,2 | 52% |
2 - Inyección | 10 | 15,03 | 1,00 | 15,0 | 67% |
3 - Ensamble+control+empaque y rotulado | 10 | 10 | 1,00 | 10,0 | 100% |
Cuello de Botella y Capacidad Real Anual del Equipo
Con el cálculo de aprovechamiento determinamos que el cuello de botella de la línea es el sector de ensamble, control, empaque y rotulado, ya que es el que necesita hacer uso de una mayor proporción de su capacidad real. A partir de estos resultados notamos que la capacidad máxima de la línea es de 10 lotes por año, esto es porque todos trabajarán al ritmo del cuello de botella.
Determinación de la evolución de las mercaderías.
Tiempos de entrega y envió de las mercaderías.
Los tiempos de entrega se calculan teniendo en cuenta los tiempos de producción del proceso. A su vez, los lotes con los que se trabaja son de 510 unidades. En el siguiente cuadro se muestra la capacidad de cada proceso en horas por lote.
Proceso | Cantidad de puestos | Hs/lote |
Mecanizado | 2 | 42,5 |
Inyección | 1 | 45,76 |
Ensamble, control, empaque y rotulado | 1 | 86 |
Se determina que la restricción del sistema está dada por la última operación, abarcando un total de 86 horas por lote. Teniendo en cuenta que se trabajan 4 horas por día, se llega a que toma 1 mes en procesar un lote de 510 conjuntos.
A su vez, los tiempos de entrega de la mercadería no solo dependen de la producción, sino también de la ubicación de su destinatario para su distribución y logística. Para aquellos clientes que se encuentran en Capital Federal, se estiman cinco días hábiles, mientras que para el interior del país, entre siete y quince días hábiles.
Tamaños y frecuencias de compras.
Los tamaños de las compras se hacen en base a los lotes productivos, los cuales son de 510 conjuntos, teniendo en cuenta desperdicios.
En cuanto a las frecuencias de compras, para el Nylon se harán dos veces al año, mientras que para el acero se realizará una única vez.
En el caso del Nylon, para el año 0 y 1, se hará una primera compra correspondiente a lo que se consumirá durante el período de Puesta en Marcha y otra cuando ya se encuentra en régimen. Para el año 2 a 5, se hará una primera compra en el mes de enero y la segunda en el mes de julio.
Nylon:
Año | N° de compra | Cantidad [Kg] |
0 y 1 | 1° | 74,71 |
2° | 100 | |
2 a 5 | 1° | 101 |
2° | 200 |
En el caso del acero, se hara una compra tanto para el año 0 y 1 como para el año 2 al 5. Acero:
Año | Cantidad [Kg] |
0 y 1 | 191 |
2 a 5 | 220 |
Estas frecuencias y tamaños de compra se pueden ver mejor explicado en el desarrollo de los ejercicios del 6 al 11.
Cálculos de los ejercicios 6 a 11 de la Guía.
Evolución de la producción
Para este proyecto se determinó que la puesta en marcha llevará 5 meses y que se irá aumentando la producción progresivamente de la siguiente manera:
Mes 1: 28,7%
Mes 2: 40%
Mes 3: 60%
Mes 4: 85%
Mes 5: 100%
Mes | Ritmo de produccion al inicio (%) | Ritmo de produccion al final (%) | Produccion promedio (%) | Produccion mensual promedio (conjuntos) | Produccion real Conjuntos |
1 | 0,00% | 28,70% | 14,35% | 510 | 73,185 |
2 | 28,70% | 40,00% | 34,35% | 510 | 175,185 |
3 | 40,00% | 60,00% | 50,00% | 510 | 255 |
4 | 60,00% | 85,00% | 72,50% | 510 | 369,75 |
5 | 85,00% | 100,00% | 92,50% | 510 | 471,75 |
Producción mes 1 a 5 | 1345 | ||||
Producción meses restantes | 2550 | ||||
Producción años 2 a 5 | 5100 |
Stock promedio de producto elaborado
El volumen de producción mensual promedio durante el estado de régimen será de:
510 | Conjuntos/mes |
Se debe tener en cuenta que el ciclo de elaboración promedio es de un mes. Mientras que el stock promedio de semielaborados quedará en:
255 | Conjuntos |
Evolución de las ventas durante la vida útil del proyecto
Al contar con stock de seguridad, se logra cumplir con el plan de ventas:
Ventas año 1 | 3640 |
Ventas año 2 a 5 | 5096 |
Determinar el stock promedio de materia prima y el programa de compras
Según el tecnólogo durante la puesta en marcha vamos a necesitar un 40% adicional de materia prima por percances y fallas propias de este periodo (se consideran no recuperables)
MP | Nylon (KG) | Nylon (conjuntos) | Acero (KG) | Acero (Conjuntos) |
Meses 1 a 5 | 74,21 | 1882,82 | 81,13 | 1882,818 |
Meses 6 a 12 | 100,5 | 2550,00 | 109,88 | 2550 |
Sumatoria Año 1 | 174,71 | 4432,82 | 191,01 | 4432,818 |
Años 2 a 5 | 222,77 | 5652,322388 | 223,43 | 5185,2166 |
Para los años en régimen los desperdicios se mantienen iguales a como se plantearon al principio.
Acero [kg] | Nylon [kg] |
219,76 | 200,63 |
Para calcular el consumo de MP en MCySE se tiene en cuenta que el ciclo de elaboración dura un mes y que la cantidad de meses activos son 10:
Acero | Nylon | |
219,76 | 200,63 | |
Stock McySe | 21,98 | 20,06 |
En conjuntos | 510 | 510 |
Promedio | 255 | 255 |
A partir de estos datos se determina que el stock mínimo de MP será de 510 conjuntos, tanto para el acero como para el nylon.
El programa de compras del año 1 queda de la siguiente manera:
Mes | Stock inicial (KG) | Consumo (KG) | Compras (KG) | Stock Final (KG) | NYLON |
Año 0 | 0,00 | 0,00 | 74,71 | 74,71 | |
Enero | 74,71 | 4,04 | 0,00 | 70,67 | PUESTA EN MARCHA |
Febrero | 70,67 | 9,67 | 0,00 | 61,00 | |
Marzo | 61,00 | 14,07 | 0,00 | 46,93 | |
Abril | 46,93 | 20,40 | 0,00 | 26,53 | |
Mayo | 26,53 | 26,03 | 0,00 | 0,50 | |
Junio | 0,50 | 14,36 | 100,00 | 86,14 | ESTADO EN REGIMEN |
Julio | 86,14 | 14,36 | 0,00 | 71,79 | |
Agosto | 71,79 | 14,36 | 0,00 | 57,43 | |
Septiembre | 57,43 | 14,36 | 0,00 | 43,07 | |
Octubre | 43,07 | 14,36 | 0,00 | 28,71 | |
Noviembre | 28,71 | 14,36 | 0,00 | 14,36 | |
Diciembre | 14,36 | 14,36 | 0,00 | 0,00 | |
Total | 174,71 | ||||
Mes | Stock inicial (KG) | Consumo (KG) | Compras (KG) | Stock Final (KG) | ACERO |
Año 0 | 0,00 | 0,00 | 191,01 | 191,01 | |
Enero | 191,01 | 4,41 | 0,00 | 186,60 | PUESTA EN MARCHA |
Febrero | 186,60 | 10,57 | 0,00 | 176,03 | |
Marzo | 176,03 | 15,38 | 0,00 | 160,64 | |
Abril | 160,64 | 22,31 | 0,00 | 138,34 | |
Mayo | 138,34 | 28,46 | 0,00 | 109,88 | |
Junio | 109,88 | 15,70 | 0,00 | 94,18 | ESTADO EN REGIMEN |
Julio | 94,18 | 15,70 | 0,00 | 78,49 | |
Agosto | 78,49 | 15,70 | 0,00 | 62,79 | |
Septiembre | 62,79 | 15,70 | 0,00 | 47,09 | |
Octubre | 47,09 | 15,70 | 0,00 | 31,39 | |
Noviembre | 31,39 | 15,70 | 0,00 | 15,70 | |
Diciembre | 15,70 | 15,70 | 0,00 | 0,00 |
Para el año 2 a 5 quedará así:
Mes (para nylon) | Stock inicial (KG) | Consumo (KG) | Compras (KG) | Stock Final (KG) |
Enero | 0,00 | 16,72 | 101,00 | 84,28 |
Febrero | 84,28 | 16,72 | 0,00 | 67,56 |
Marzo | 67,56 | 16,72 | 0,00 | 50,84 |
Abril | 50,84 | 16,72 | 0,00 | 34,12 |
Mayo | 34,12 | 16,72 | 0,00 | 17,40 |
Junio | 17,40 | 16,72 | 0,00 | 0,68 |
Julio | 0,68 | 16,72 | 100,00 | 83,96 |
Agosto | 83,96 | 16,72 | 0,00 | 67,24 |
Septiembre | 67,24 | 16,72 | 0,00 | 50,52 |
Octubre | 50,52 | 16,72 | 0,00 | 33,81 |
Noviembre | 33,81 | 16,72 | 0,00 | 17,09 |
Diciembre | 17,09 | 16,72 | 0,00 | 0,37 |
Total | 200,63 | 201,00 | ||
Mes (para Acero) | Stock inicial (KG) | Consumo (KG) | Compras (KG) | Stock Final (KG) |
Enero | 0,00 | 18,31 | 220 | 201,45 |
Febrero | 201,45 | 18,31 | 0,00 | 183,13 |
Marzo | 183,13 | 18,31 | 0,00 | 164,82 |
Abril | 164,82 | 18,31 | 0,00 | 146,51 |
Mayo | 146,51 | 18,31 | 0,00 | 128,19 |
Junio | 128,19 | 18,31 | 0,00 | 109,88 |
Julio | 109,88 | 18,31 | 0,00 | 91,57 |
Agosto | 91,57 | 18,31 | 0,00 | 73,25 |
Septiembre | 73,25 | 18,31 | 0,00 | 54,94 |
Octubre | 54,94 | 18,31 | 0,00 | 36,63 |
Noviembre | 36,63 | 18,31 | 0,00 | 18,31 |
Diciembre | 18,31 | 18,31 | 0,00 | 0,00 |
Total | 257,28 | 220 | 220 |
Nylon | Acero | |
Stock promedio | 42,29275 | 100,7233333 |
Cuadro resumen del programa general de evolución
Todas las unidades se encuentran en conjuntos, para expresarlo de esta forma utilizamos el siguiente cuadro de pasaje de unidades:
CONVERSION DE KG A CONJUNTO | |
Para acero | |
219,76 | 5100 |
0,043 | 1 conjunto |
Para nylon | |
201 | 5100 conjuntos |
0,039 | 1 conjunto |
143,46 | 3640 conjuntos |
Conjuntos | Período de instalación | Año 1 | Año 2 al 5 |
Ventas | 0 | 3640 | 5100 |
Stock Promedio de elaborado | 0 | 255,000 | 255 |
Produccíon | 0 | 3895 | 5100 |
Desperdicio NO recuperable NYLON | 0 | 537,82 | 552,32 |
Desperdicio NO recuperable ACERO | 0 | 74,07 | 85,22 |
Mc y SE Acero por mes promedio | 0 | 255 | 255 |
Mc y SE Nylon por mes promedio | 0 | 255 | 255 |
Consumo MP ACERO | 0 | 4223,94 | 5185 |
Consumo MP NYLON | 0 | 4687,69 | 5652 |
Stock MP ACERO promedio | 4432,8 | 2337,5 | 2337,5 |
Stock MP Nylon promedio | 1895,5 | 1073,1 | 1073,1 |
Compra MP ACERO | 4432,8 | 2128,6 | 5185,2 |
Compra MP NYLON | 1895,5 | 3865,3 | 5652,3 |
Determinación del Personal.
Organigrama de toda la empresa.
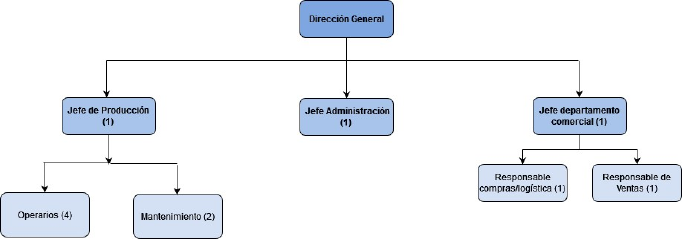
Descripción de los Puestos de Trabajo.
Director General: Tiene como responsabilidad la tarea de dirigir las actividades y tomar decisiones estratégicas para el correcto funcionamiento de la organización, asegurando el crecimiento y cumplimiento de los objetivos.
Requisitos para el puesto:
- Experiencia y profundo conocimiento en el sector industrial mínimo de cinco años
- Formación académica: Profesional graduado con título terciario de Ingeniería o carreras afines
- Habilidades de liderazgo
- Orientación al cliente y al mercado
- Visión estratégica
Producción
Jefe de producción y calidad: supervisa y coordina las actividades de producción. Planifica y organiza los recursos necesarios como la mano de obra y materiales, dirige el proceso productivo coordinando los equipos de trabajo para el cumplimiento de los objetivos de la organización. Además se encarga de garantizar que los productos cumplan con los estándares de calidad establecidos. Establece las normas de calidad, implementación de sistemas de control y supervisión de la gestión de problemas.
Requisitos para el puesto:
- Formación académica: Ingeniero Industrial con más de cinco años de experiencia en sectores productivos
- Habilidades de liderazgo
- Habilidades de comunicación y experiencia en el manejo de personal
- Habilidades analíticas
- Conocimientos técnicos y normativos (normas IRAM e ISO)
- Certificaciones específicas de calidad como Six Sigma
Operarios:
A continuación se detalla la cantidad de operarios según las tareas del proceso productivo.
Mecanizado: 2
Inyección: 1
Ensamble, empaque y rotulado: 1
Las actividades a realizar son aquellas relacionadas a la puesta en marcha de las máquinas, preparación de máquinas y puestos de trabajo, desalistamiento de las mismas, como así también cumplir con las operaciones que cada uno de sus puestos conlleva. Deberá cumplir con las reglamentaciones determinadas por el Jefe de Producción, como así también por las de la empresa. También, tendrá que cumplir con las normas de seguridad industrial y salud establecidas en cada uno de los procesos productivos, verificar sus labores de acuerdo a las especificaciones técnicas del producto y actualizar diariamente las hojas de producción.
Requisitos de los puestos:
Secundario terminado y experiencia como operadores de máquinas o ejecutores de puestos de trabajos. Deben tener un grado conocimiento del proceso. Se priorizará a aquellos que cuenten con título técnico. Deberán tener capacidad de análisis, gran grado de atención a los detalles y facilidad para el trabajo en equipo.
Mantenimiento y limpieza:
Cantidad de empleados: dos
La función del encargado de mantenimiento será establecer un plan de mantenimiento preventivo para el correcto funcionamiento de la línea productiva. Realizar tareas básicas de mantenimiento y programación de máquina.
La función del encargado de limpieza será la limpieza de las máquinas al fin de cada jornada laboral
Requisitos de los puestos:
Técnico mecánico para el área de mantenimiento. Sin formación académica determinada para el encargado de limpieza.
Administración
Jefe departamento de administración: supervisa recursos humanos, finanzas y procesos operativos. Planifica presupuestos, controla costos y reporta estados financieros. Maneja relaciones con proveedores y cumple regulaciones. Además desempeñará funciones de recursos humanos. Se encargará de supervisar y hacer seguimiento a las tareas contables las cuales serán tercerizadas.
Requisitos para el puesto:
- Formación académica: profesional graduado de Administración de empresas, Economía, Ingeniería o similares.
- Con experiencia en el mismo u otros rubros.
- Conocimiento y manejo de paquete office.
- Habilidades competitivas
Compras
Jefe departamento de compras: dirige estratégicamente las adquisiciones, selecciona proveedores y negocia contratos. Supervisa inventarios, optimiza costos y asegura la calidad.
Requisitos para el puesto:
- Formación académica: licenciado en Administración de Empresas o carreras afines con mínimo 2 años de experiencia en el área.
- Habilidades de negociación
- Liderazgo y gestión de equipos
Responsable de compras y logística: gestiona y supervisa las actividades relacionadas con la adquisición de bienes y servicios. Seleccionan y negocian con proveedores, hacen control de inventarios, planifican y coordinan la distribución y logística de los productos, entre otras.
Requisitos del puesto:
- Experiencia de 5 o más años en puestos de supply chain.
- Formación académica: profesional graduado en Ingeniería Industrial
- Conocimiento y uso de herramientas logísticas
Responsable de Ventas: lleva a cabo tareas de desarrollo de estrategias para impulsar las ventas. Realiza la búsqueda de nuevos clientes, gestión de relaciones con clientes y supervisión de la ejecución del plan de ventas.
Requisitos del puesto:
- Formación académica: título terciario en carreras afines a Administración de Empresas e Ingeniería Industrial
- Habilidades de negociación
- Habilidades interpersonales
Cuadro resumen de cantidad de personas por área:
Área | Función | Cantidad |
Dirección General | Director General | 1 |
Producción | Jefe de producción y calidad | 1 |
Operarios | Mecanizado: 2
Inyección: 1 Ensamble, control y empaque: 1 | |
Mantenimiento | 2 | |
Administración | Jefe departamento administración | 1 |
Compras | Jefe departamento comercial | 1 |
Responsable compras/logística | 1 | |
Responsable ventas | 1 |
Listado de Equipos Auxiliares, Muebles y Útiles.
Sector | Muebles | Cantidad |
Oficina Dirección Técnica | Escritorio | 1 |
Silla ergonométrica | 1 | |
Silla | 2 | |
Computadora | 1 | |
Impresora | 1 | |
Luminaria led (preferentemente indirecta) | 3 | |
Estantería | 1 | |
Teléfono | 1 | |
Aire acondicionado frío/calor | 1 | |
Cesto de basura | 1 | |
Administración y oficina técnica | Escritorio | 3 |
Silla ergonométrica | 3 | |
Luminaria led (preferentemente indirecta) | 4 | |
Notebook | 3 | |
Estantería | 2 | |
Pizarra | 1 | |
Aire acondicionado frío/calor | 1 | |
Impresora | 1 | |
Dispenser de agua | 1 | |
Cafetera | 1 | |
Cesto de basura | 1 | |
Baños | Inodoro | 3 |
Lavamanos | 2 | |
Lockers | 2 | |
Espejo | 2 | |
Luminaria led | 4 | |
Cocina | Mesa | 1 |
Silla | 6 | |
Microondas | 1 | |
Heladera | 1 | |
Dispenser de agua | 1 | |
Luminaria led | 2 | |
Atención al cliente | Escritorio | 2 |
Silla | 6 | |
Notebook | 2 | |
Luminaria led (preferentemente indirecta) | ||
Estantería | 1 | |
Pañol herramientas | Armario de herramientas | 1 |
Producción y ensamblado | Mesa de ensamble | 1 |
Rotulado | Impresora | 1 |
Notebook | ||
Empaque | Mesa | 1 |
Sector producción | Luminaria | 48 |
Depósito MP | Estanterías | 3 |
Depósito producto ensamblado | Estanterías | 3 |
Depósito producto médico | Estanterías | 3 |
Anteproyecto de Planta.
Plano de la Planta con las distribuciones de las distintas áreas
A continuacion se presenta el plano con sus medidas en metros. Para una mejor visualizacion del mismo dirigirse al link.
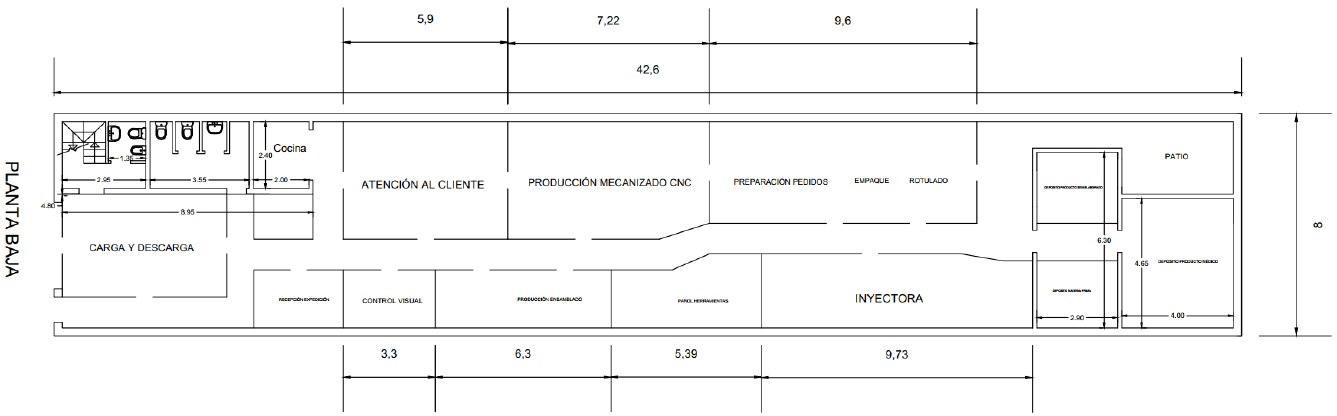
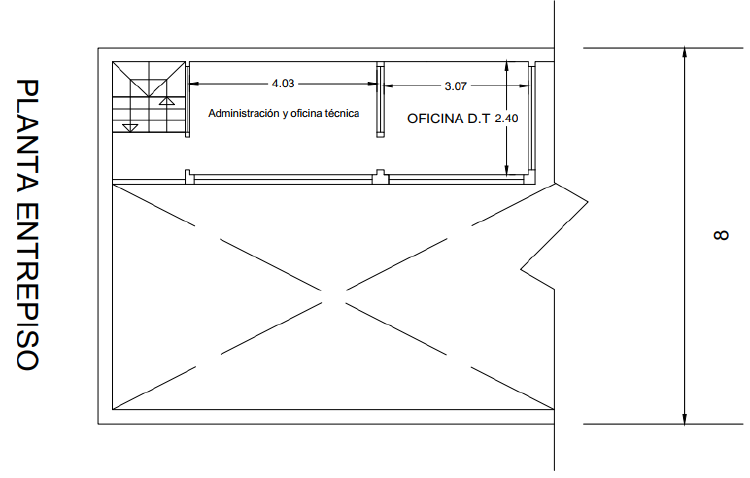
Plano mostrando el recorrido de los materiales.
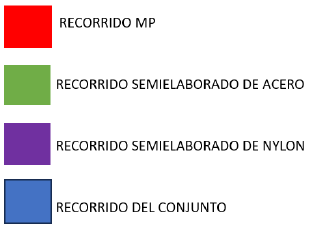
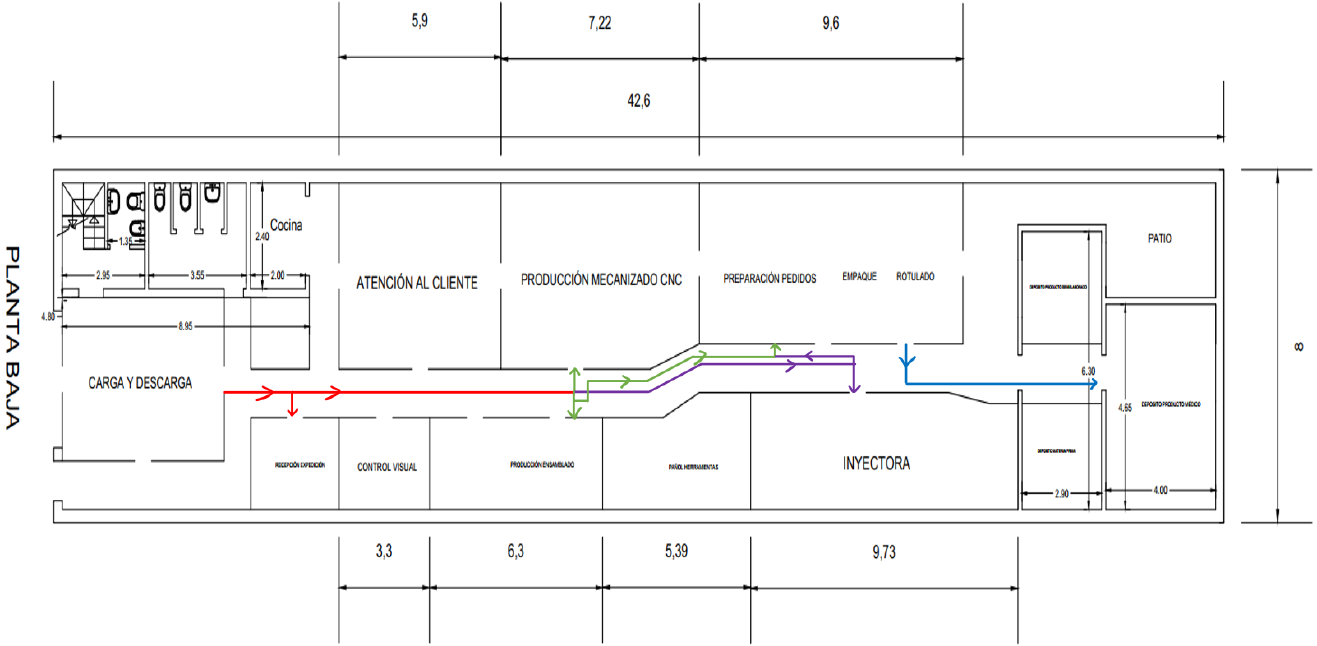
Cronograma de ejecución
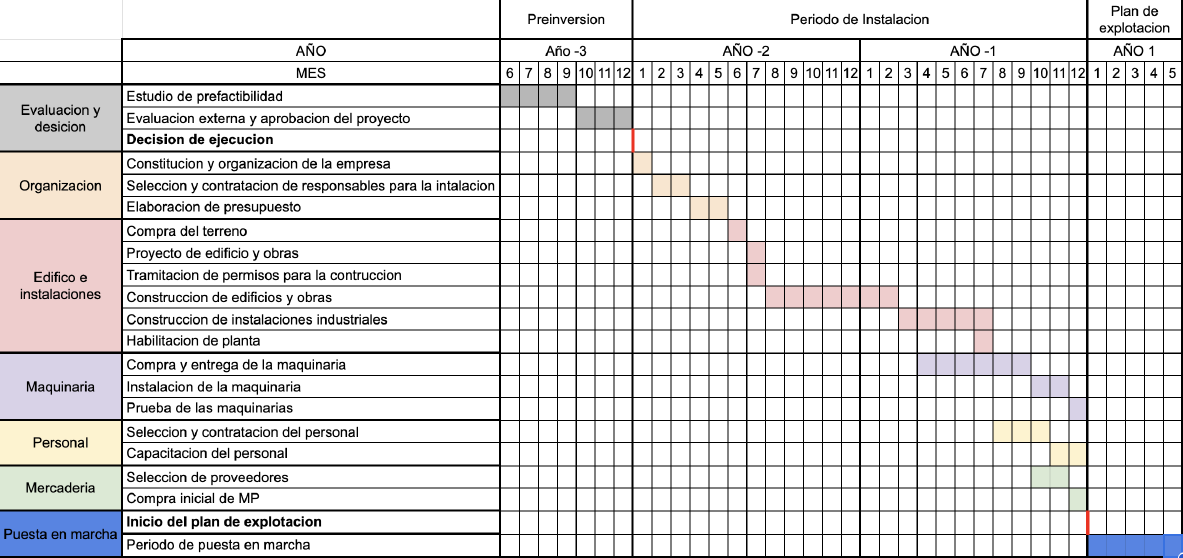
Referencias
https://docs.google.com/spreadsheets/d/1VmgEYKPQNgkQrvXY2yvvbXGag3E_QKqvcHbTF8aR1w0/edit?usp=sharing (desarrollo de los ejercicios)