2025/Grupo4/DimensionamientoFisico
Determinación de la localización
Para determinar la ubicación más adecuada para la planta de fabricación de cortinas roller, se analizaron tres posibles alternativas con fuerte perfil industrial, buena conectividad y acceso a recursos:
- Rosario (Santa Fe)
- La Matanza (Provincia de Buenos Aires)
- Godoy Cruz (Mendoza)
Rosario (Santa Fe) | La Matanza (Buenos Aires) | Godoy Cruz (Mendonza) | |||||
Factor | IRfp | DRfa | IRfpxDRfa | DRfa | IRfpxDRfa | DRfa | IRfpxDRfa |
Acceso al mercado | 4 | 4 | 16 | 5 | 20 | 3 | 12 |
Cercanía a proveedores | 4 | 4 | 16 | 4 | 16 | 2 | 8 |
Cercanía a clientes | 4 | 4 | 16 | 5 | 20 | 3 | 12 |
Medios de transporte | 4 | 4 | 16 | 5 | 20 | 3 | 15 |
Disponibilidad de mano de obra especializada | 4 | 4 | 16 | 4 | 16 | 3 | 12 |
Disponibilidad de terrenos | 3 | 4 | 12 | 3 | 9 | 5 | 15 |
Costo del terreno | 3 | 3 | 9 | 2 | 6 | 4 | 12 |
Disponibilidad energética | 5 | 5 | 25 | 5 | 25 | 4 | 20 |
Posibilidad de tratar los desechos | 3 | 4 | 12 | 5 | 15 | 4 | 12 |
Posible expansión | 3 | 4 | 12 | 3 | 9 | 4 | 12 |
Sumatoria | 150 | 156 | 130 |
Se construyó una matriz de localización, ponderando factores clave mediante un Índice de Relevancia (IR) y evaluando el Desempeño Relativo (DR) de cada localidad. A partir del producto IR×DR, se cuantificó la conveniencia de cada opción.
Las valoraciones de cada factor se hicieron en base a los siguientes criterios:
- Acceso al mercado: Cercanía a los principales centros de consumo del producto.
- Cercanía a proveedores: Proximidad a los proveedores de materias primas e insumos.
- Cercanía a clientes: Ubicación respecto al público objetivo o puntos de venta.
- Medios de transporte: Disponibilidad y calidad de rutas, autopistas y transporte público.
- Disponibilidad de mano de obra especializada: Presencia local de personal calificado.
- Disponibilidad de terrenos: Existencia de lotes industriales disponibles.
- Costo del terreno: Precio de compra o alquiler del terreno.
- Disponibilidad energética: Acceso a red eléctrica confiable y suficiente.
- Posibilidad de tratar los desechos: Condiciones para gestionar residuos adecuadamente.
- Posible expansión: Espacio para futuras ampliaciones de la planta
Definición técnica del producto
Planos y/o dibujos
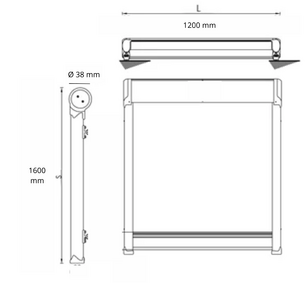
Listado de materiales BOM
Ítem | Código | Denominación | Nivel 1 | Nivel 2 | Nivel 3 | Cantidad estimada | Unidad |
---|---|---|---|---|---|---|---|
1 | C | Cortina Roller Q66 – Sistema Cadena | ✔ | 1,00 | conjunto | ||
2 | C1 | Tela técnica (Blackout / Sunscreen) | ✔ | 1,92 | m² | ||
3 | C2 | Tubo de aluminio Q66 Ø38 mm | ✔ | 1,20 | m lineal | ||
4 | C3 | Mecanismo de cadena BL | ✔ | 1,00 | unidad | ||
5 | C4 | Kit de soportes completos | ✔ | 1,00 | set | ||
5.1 | COROSOP046 | Soporte metálico 5502 | ✔ | 1,00 | unidad | ||
5.2 | COROSOP047 | Soporte metálico 7502 | ✔ | 1,00 | unidad | ||
5.3 | COROTAP050 | Tapa decorativa para soporte 5502 | ✔ | 1,00 | unidad | ||
5.4 | COROTAP052 | Tapa decorativa para soporte 7502 | ✔ | 1,00 | unidad | ||
5.5 | COROTIK009 | Tornillos fijación soporte | ✔ | 4,00 | unidades | ||
5.6 | COROFLA002 | Adaptador Q2 a sistema Bethin | ✔ | 1,00 | unidad | ||
6 | C5 | Sistema de transmisión | ✔ | 1,00 | set | ||
6.1 | COROCON007 | Cadena metálica BCH | ✔ | 3,2 | metros | ||
6.2 | COROCON002 | Conector cadena metálica | ✔ | 1,00 | unidad | ||
7 | C6 | Elementos de ajuste y alineación | ✔ | - | - | ||
7.1 | COROADA016 | Adaptador tubo Q66 | ✔ | 1,00 | unidad | ||
7.2 | COROADA067 | Adaptador tubo BL52 a Q53/Q66 | ✔ | 1,00 | unidad | ||
7.3 | COROADA058 | Adaptador resorte aligeramiento | ✔ | 1,00 | unidad | ||
7.4 | CORORES011 | Resorte aligeramiento derecho | ✔ | 1,00 | unidad | ||
7.5 | CORORES012 | Resorte aligeramiento izquierdo | ✔ | 1,00 | unidad | ||
7.6 | PEROTUB093 | Puntera regulable Q66 | ✔ | 1,00 | unidad | ||
8 | C7 | Montaje y fijación a superficie | ✔ | - | - | ||
8.1 | COROBAS002 | Base 1035.4 | ✔ | 1,00 | unidad | ||
8.2 | COROTAP019 | Tapa base 1035 | ✔ | 1,00 | unidad | ||
8.3 | COROCLI007 | Clip base 1035 | ✔ | 1,00 | unidad | ||
9 | C8 | Otros elementos funcionales y opcionales | ✔ | - | - | ||
9.1 | LAALLAM006 | Fleje Louvolite 7–8 mm | ✔ | 1,00 | unidad | ||
9.2 | CORIONS019 | Traba tela roller D3.2 | ✔ | 1,00 | unidad | ||
10 | C9 | Funda plástica protectora | ✔ | 0,78 | m² | ||
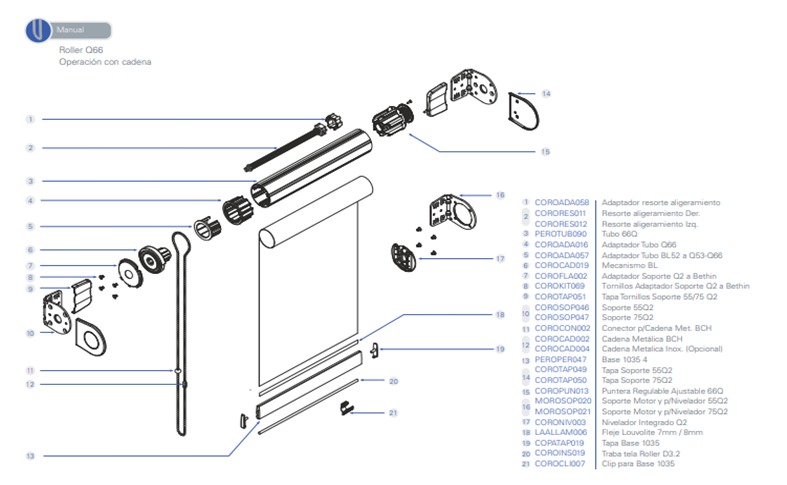
Especificaciones Técnicas
Clasificacion | Valor |
---|---|
Modelo Base | Kit estandar 120 cm ancho x 160 cm alto |
Tipo de Tela | Blackout o Screen, según elección del cliente |
Color | Blanco, gris medio, arena, beige, crema |
Dimensionales | Valor |
---|---|
Tubo de aluminio | aluminio anonizado de Ø 38 mm, espesor 1,3 mm |
Ancho de tela | 120 cm (ancho útil igual a 117 cm, se utilizan 3 centímetros dentro del mecanismo) |
Peso total de Kit | 2 kg |
Tolerancias | ± 0,5 cm en corte de tela y estructura |
Normas Aplicables
Aunque no existen normativas obligatorias específicas para cortinas roller manuales, se procurará cumplir con los siguientes estándares relevantes para asegurar calidad, seguridad y sostenibilidad del producto:
- IRAM 11605: Acondicionamiento térmico de edificios. Condiciones de habitabilidad en edificios. Aplica a productos que contribuyen al control térmico en ambientes interiores.
- IRAM 11910: Se prioriza la selección de telas con certificación de resistencia al fuego para garantizar seguridad en hogares como en espacios corporativos.
- ISO 14001: Norma internacional de gestión ambiental. Se tomará como referencia para minimizar el impacto ambiental en materiales, procesos y gestión de residuos.
Características Condición del Producto
Para garantizar el correcto funcionamiento, durabilidad y estética de las cortinas roller, se recomienda tener en cuenta las siguientes condiciones de uso y conservación:
- Instalación adecuada: Las cortinas deben instalarse en superficies niveladas y con los anclajes correctamente fijados. El uso de soportes adecuados evita deformaciones o desprendimientos.
- Evitar fuerzas excesivas: No aplicar tensión brusca sobre la cadena de accionamiento ni forzar el mecanismo de enrollado. El uso correcto asegura una mayor vida útil del sistema.
- Protección en obras: Si se realiza pintura, revoque u otro tipo de mantenimiento cerca de las cortinas, se recomienda cubrirlas completamente con film protector o plásticos para evitar manchas o daños.
- Limpieza periódica: La tela debe limpiarse con un paño seco o ligeramente húmedo, sin el uso de productos abrasivos. En zonas de alta polución o exposición al polvo, se recomienda aumentar la frecuencia de limpieza.
- Condiciones de ambiente: Evitar la exposición constante a la humedad o ambientes agresivos que puedan deteriorar los componentes metálicos. Las cortinas están diseñadas para uso interior.
- No utilizar como soporte: No colgar objetos sobre las cortinas ni utilizarlas como sostén de peso adicional.
- Almacenamiento y transporte: En caso de no instalarse inmediatamente, almacenar en un lugar seco y horizontalmente en su embalaje original para evitar deformaciones.
Plan de Ensayos
Garantizar la calidad, seguridad y sustentabilidad de las cortinas roller desde su diseño hasta su comercialización requiere la implementación de un plan de ensayos. Este plan se estructura en seis áreas técnicas, cada una con ensayos específicos, criterios de aceptación y fundamentos normativos
1. Ensayos Dimensionales y de Material
Norma aplicada: IRAM 15-100
- Verificación dimensional de la tela: Cada unidad debe cumplir con las medidas nominales (ej. 1,92 m²). Se mide una muestra del 5% del lote; se rechaza si el error excede ±0,5 cm.
- Verificación de componentes metálicos: Se controlan cortes de tubo y calidad del aluminio. Se descarta la pieza si no cumple con tolerancias operativas.
2. Ensayos Mecánicos de Funcionamiento
Norma aplicada: IRAM 15-100
- Ensayo de sistema de cadena y freno: Se realizan 10 ciclos operativos por unidad. Si hay trabas, fricción excesiva o ruido anormal, el lote completo se revisa.
- Resistencia estructural del ensamblado: Se somete a 20 ciclos de enrollado continuo en banco de prueba. Se rechaza si hay deformación o juego mecánico fuera de tolerancia.
3. Ensayos Superficiales y Visuales
Norma aplicada: IRAM 15-100
- Calidad de terminaciones: Se inspecciona el 100% de las unidades antes de embalaje, verificando ausencia de rayones, rebabas y bordes irregulares.
- Aspecto visual de telas: Se evalúa la uniformidad del color, presencia de marcas o defectos en el tramado.
4. Ensayos de Acondicionamiento Térmico
Norma aplicada: IRAM 11605
- Evaluación de telas térmicas: Se seleccionan telas blackout y screen con coeficiente de apertura ≤ 5%, conforme a estándares técnicos de confort térmico.
- Contribución a habitabilidad interior: Las telas seleccionadas permiten regular la ganancia térmica en verano y conservar calor en invierno, mejorando la eficiencia energética del ambiente.
5. Ensayos de Seguridad Ignífuga
Norma aplicada: IRAM 11910
- Ensayo de comportamiento frente al fuego: Se utilizan únicamente telas certificadas como auto extinguibles (clasificación tipo B1). Se solicita certificado al proveedor para cada lote.
6. Ensayos Ambientales y de Embalaje
Norma aplicada: ISO 14001
- Simulación de caída de embalaje: Se realizará una prueba de caída desde 1 metro sobre tres caras del empaque. El nuevo embalaje combina funda plástica interna y caja externa de cartón corrugado reciclable. Se busca garantizar que el producto llegue intacto al consumidor.
- Procedimientos ambientales: Los sobrantes de tela se derivan a un emprendimiento textil en Mendoza (fabricación de carteras a partir de materiales reciclados) y los tubos de aluminio se reciclan en Basavilbaso Metales Reciclaje (Gregorio de Laferrere).
Procedimiento en caso de no conformidad
- Las unidades fuera de norma se apartan para retrabajo o descarte.
- Se documentan en la hoja de control de calidad.
- Se notifican a Producción y Diseño.
- Se aplican acciones correctivas en línea con IRAM 15-100.
Acondicionamiento del Producto
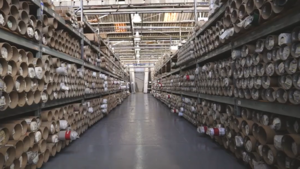
Cada cortina roller se acondiciona en una funda plástica interna, que protege la tela y los mecanismos durante el almacenamiento y manipulación. Para su distribución, se incorpora una caja externa de cartón corrugado reciclable, que brinda resistencia frente a golpes y caídas.
El empaque incluye:
- Identificación del lote.
- Fecha de fabricación.
- Modelo, dimensiones y tipo de tela.
- Código de trazabilidad QR.
- Información del lugar de producción.
- Recomendaciones básicas de instalación y conservación.
Este sistema de embalaje fue seleccionado por su capacidad para proteger componentes con bordes metálicos (ménsulas, tornillos de montaje) sin comprometer la integridad del producto.
Definición del Proceso de Producción
Diagrama de Flujo de Fabricación y Control

Cursograma
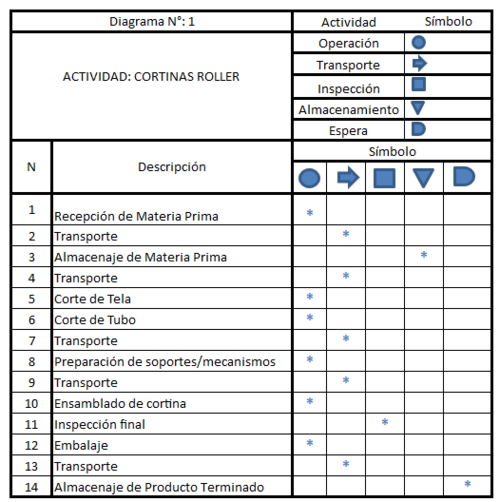
Descripción del proceso productivo
- Recepción de Materia Prima: Se reciben insumos como telas (blackout/sunscreen), tubos de aluminio, mecanismos y accesorios.
- Transporte: Traslado interno hacia el área de almacenamiento intermedio.
- Almacenaje de Materia Prima: Se clasifican y almacenan en estanterías o racks, según el tipo de insumo.
- Transporte: Se trasladan los insumos requeridos al área de corte.
- Corte de Tela: Se realiza el corte de tela según las dimensiones del producto estándar (1,2 m x 1,6 m), utilizando mesa de corte y guía.
- Corte de Tubo: Corte de tubo de aluminio a la medida requerida (1,2 m) con herramientas de precisión.
- Transporte: Se trasladan las piezas cortadas y componentes al sector de armado.
- Preparación de Soportes y Mecanismos: Se alistan kits completos (cadena, tapas, tornillos y soportes) para ensamblar cada cortina.
- Transporte: Se lleva el conjunto al área de ensamble.
- Ensamblado de Cortina: Unión de los elementos: se inserta la tela en el tubo, se colocan los mecanismos y se prueba el funcionamiento general.
- Inspección Final: Verificación visual y funcional de cada unidad antes del embalaje.
- Embalaje: Cada cortina se coloca en su funda protectora plástica y rotulada.
- Transporte: Traslado del producto terminado al depósito.
- Almacenaje de Producto Terminado: Se almacenan en el área de productos terminados, listos para despacho.
Determinación de las máquinas e instalaciones
Especificaciones técnicas de las máquinas (capacidades, tamaño de lotes, tiempos)
Para optimizar la etapa de corte y medición de tela técnica (blackout o screen), se seleccionó la máquina CTLR-3000 de la marca REXEL
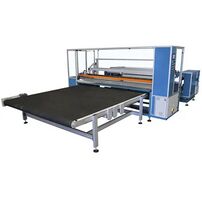
Especificaciones técnicas:
- Ancho máximo de rollo: 2500–3000 mm
- Peso máximo de rollo: hasta 40 kg
- Diámetro máximo de rollo: hasta 300 mm
- Alimentación eléctrica: 230 V
- Potencia: 0,6 kW
- Velocidad máxima: 22 m/min = 1320 m/h
- Largo de la pieza a cortar: 1,2 m
- Tipo de corte: transversal (por lo tanto, la longitud del corte es lo que determina la velocidad de avance y la cantidad de cortes por hora)
Para asegurar cortes rectos, limpios y repetitivos en los tubos de aluminio, se seleccionó la tronzadora automática SA 142/37, desarrollada por la firma alemana Elumatec, especializada en maquinaria para carpintería metálica y producción industrial
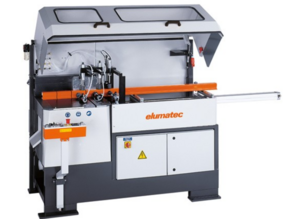
Especificaciones técnicas:
- Diámetro del disco de corte: 500 mm
- Modo de avance: Hidroneumático
- Tipos de corte: Rectos y angulares hasta 45° (grupo de sierra basculante opcional)
- Selector de ciclo: Avance simple, doble o triple
- Sistema de elevación de perfiles: evita rayones y protege la superficie durante el posicionamiento
- Sujeción multipieza: opcional para cortes simultáneos o piezas pequeñas
- Visualización digital opcional: sistema E111 para ajuste preciso de ángulos
- Alimentación eléctrica: 3×400 V – 5,5 kW
Se seleccionó la mesa de ensamblado Yewdale, diseñada específicamente para este tipo de producto. Su estructura ergonómica y modular permite aumentar la productividad, mejorar la precisión del armado y reducir el espacio ocupado en planta.
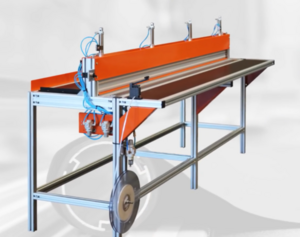
Especificaciones técnicas:
- Anchos disponibles: 2.6 m, 3 m, 3.5 m y 4.2 m
- Sistema de sujeción: pinza neumática (air clamp) de accionamiento por interruptor
- Diseño compacto: permite ubicar hasta 4 mesas en el espacio de una mesa tradicional
Se selecciono la selladora por impulso CFB-2000 N de Thermopack, diseñada especialmente para el cierre térmico
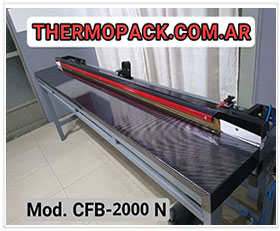
Especificaciones técnicas
- Tipo de sellado: por impulso eléctrico
- Longitud máxima de sellado: 2000 mm
- Sistema de accionamiento: neumático, con control de velocidad
- Resistencias superiores e inferiores para un sellado uniforme
- Temporizador con indicador de estado del ciclo
- Guía formadora de zócalo con regulador
- Estructura metálica con pintura epoxi y tratamiento anticorrosivo
- Laterales abiertos que facilitan el manejo de piezas largas
Para garantizar la trazabilidad y correcta identificación de cada unidad de cortina roller, se seleccionó la impresora térmica industrial ZT411 de Zebra Technologies
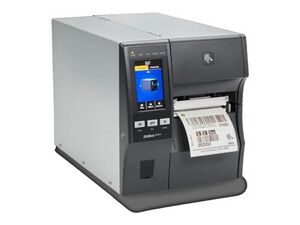
Especificaciones técnicas:
- Método de impresión: térmica directa y transferencia térmica
- Resolución: 203, 300 o 600 dpi (según modelo)
- Ancho máximo de impresión: hasta 104 mm
- Velocidad de impresión: hasta 356 mm/s
- Pantalla: táctil a color de 4.3” para configuración y monitoreo
- Conectividad: USB, Ethernet, Bluetooth 4.1, RS-232, Wi-Fi (opcional)
- Memoria: 256 MB RAM / 512 MB Flash
- Chasis: metálico con puerta lateral de acceso rápido
- Compatibilidad: etiquetas con códigos de barras, QR, texto, símbolos y datos variables
Consumos de energía, agua y otros servicios
Consumo de energía eléctrica
El consumo energético del proceso productivo se calcula en función de las potencias nominales de los equipos seleccionados y las horas de operación estimadas según el volumen proyectado de producción. Se estima una jornada de 8 horas diarias durante 240 días al año (1.920 horas anuales).
Máquina / Equipo | Potencia (kW) | Tiempo de operación anual (h) | Consumo estimado anual (kWh) |
---|---|---|---|
Medidor y cortador CTLR-3000 | 0,6 | 1.952 | 1.171 |
Tronzadora automática SA 142/37 | 5,5 | 1.952 | 10.736 |
Mesa de ensamblado Yewdale (neumática) | — | — | 0 (ver aire comprimido) |
Selladora por impulso Thermopack | 3,2 | 960 (uso parcial) | 3.072 |
Impresora térmica Zebra ZT411 | 0,1 | 960 | 96 |
Iluminación planta (LED 20 × 20W) | 0,4 | 1.952 | 781 |
Aire comprimido – Compresor 3HP | 2,2 | 960 | 2.112 |
Consumo eléctrico del proceso productivo total estimado: 17.968 kWh/año
Consumo eléctrico de equipos auxiliares y administrativos
Área | Equipo / Elemento | Potencia (kW) | Tiempo de operación anual (h) | Consumo estimado anual (kWh) |
---|---|---|---|---|
Producción | Dispenser de agua | 0,575 | 1.952 | 1.122 |
Producción | Aire acondicionado | 1,500 | 1.000 (uso estacional) | 1.500 |
Oficina de Producción | Computadora de escritorio | 0,160 | 1.952 | 624 |
Oficina de Producción | Impresora multifunción | 0,450 | 360 (uso parcial) | 162 |
Oficina de Producción | Dispenser de agua | 0,575 | 1.952 | 1.122 |
Oficina de Producción | Aire acondicionado | 1,500 | 1.000 | 1.500 |
Oficina Comercial | Computadora de escritorio | 0,160 | 1.952 | 624 |
Oficina Comercial | Impresora | 0,450 | 360 | 162 |
Oficina Comercial | Aire acondicionado | 1,500 | 1.000 | 1.500 |
Comedor | Heladera con freezer | 0,115 | 8.760 (uso continuo) | 1.007 |
Comedor | Microondas | 0,065 | 240 (uso parcial) | 15,6 |
Comedor | Cafetera eléctrica | 1,150 | 240 | 276 |
Comedor | Dispenser de agua | 0,575 | 1.952 | 1.122 |
Comedor | Aire acondicionado | 1,500 | 1.000 | 1.500 |
Consumo eléctrico total estimado de equipos auxiliares y administrativos: 12.136,6 kWh/año
Consumo eléctrico total de la planta: 30.104,6
Consumo de agua
Categoría | Estimación diaria | Días operativos/año | Consumo anual estimado |
---|---|---|---|
Limpieza de herramientas y superficies | 5 litros/día | 244 | 1.220 litros |
Uso sanitario (13 personas × 40L) | 520 litros/día | 244 | 126.880 litros |
Limpieza general de planta | 20 litros/día | 244 | 4.880 litros |
Consumo total de agua : 132.980
Otros servicios
- Internet: contratación de plan mensual de fibra óptica de 300 Mb/s para control administrativo, trazabilidad y etiquetado.
- Telefonía: línea fija + celulares corporativos para gestión de ventas y proveedores.
- Gas natural: no requerido, ya que todo el proceso productivo es eléctrico
Mantenimiento, medios de control y sistemas de seguridad
Se establecen las siguientes tareas periódicas para asegurar el funcionamiento óptimo de los equipos e instalaciones:
Equipo | Tarea de mantenimiento | Frecuencia | Observaciones técnicas |
---|---|---|---|
CTLR-3000 – REXEL | Limpieza de sensores y cuchilla | Semanal | Usar aire comprimido seco y paño antiestático |
Verificación de tensión de correas internas | Mensual | Ajustar si presenta holgura o ruido irregular | |
Actualización de firmware de pantalla táctil | Trimestral | Requiere USB o conexión externa de soporte técnico | |
SA 142/37 – Elumatec | Revisión de afilado de disco de corte | Mensual | Reemplazar si presenta rebabas o arrastre |
Inspección de sistema hidroneumático | Trimestral | Verificar estanqueidad, válvulas y cilindros | |
Calibración de ángulos de corte | Semestral | Utilizar escuadra de precisión y sistema digital E111 | |
Mesa de ensamblado – Yewdale | Verificación de presión en clamp neumático | Mensual | Presión óptima de trabajo: 5–6 bar |
Limpieza de superficie de trabajo | Diaria | Usar paño seco y alcohol isopropílico | |
Selladora Thermopack CFB-2000N | Inspección de resistencias y sensores | Mensual | Reemplazo programado cada 1.000 horas |
Calibración de tiempo de sellado | Trimestral | Revisar uniformidad y sellado sin quemado | |
Impresora Zebra ZT411 | Limpieza de cabezal y rodillo | Semanal | Limpieza del cabezal térmico |
Revisión de stock de etiquetas | Diaria | Control visual y por software de impresión | |
Compresor de aire (3 HP) | Purga de tanque y limpieza de filtro de aire | Semanal | Evita acumulación de humedad y pérdida de presión |
Control de presión de corte | Mensual | Rango operativo: 5–8 bar |
Sistemas de seguridad
Para proteger al personal y a las instalaciones, se prevén las siguientes medidas activas y pasivas:
- Extintores multipropósito (clase ABC): 1 cada 100 m², verificados semestralmente.
- Detector de humo autónomo en área de corte y armado.
- Interruptores de emergencia: en zonas críticas (CTLR-3000, SA 142/37).
- Señalización de evacuación y peligro eléctrico conforme a IRAM 10005.
- Equipos de protección personal (EPP):
- Gafas para corte y manipulación de tubos
- Guantes antiestáticos y resistentes a cortes (nivel 3 o superior)
- Zapato de seguridad con puntera metálica
- Capacitación anual en seguridad operativa y primeros auxilios.
Cálculos de máquinas e instalaciones
Balance anual de material. Producción seccional
Teniendo en cuenta el plan de ventas del año 2 proyecta una venta de 20.400 cortinas
Sección operativa | MP principal | Unidad | Entrada | Desperdicio (No recuperable) | Producción útil |
---|---|---|---|---|---|
Corte de tela | Tela técnica | m² | 40.200 | 1.000 | 39.200 |
Corte de tubo | Tubos aluminio | m | 24.800 | 320 | 24.480 |
Ensamblado | Componentes completos | unidades | 20.400 | 0 | 20.400 |
Cada cortina requiere 1,92 m2 de tela y 1,2 metros de tubo, por lo que se dimensionan los insumos totales en función directa a estas especificaciones. El desperdicio operativo considerado para tela es del 2,5% y para tubos del 1,3%, ajustado a los valores esperados por cortes defectuosos, errores dimensionales y bordes irregulares.
Ritmo de trabajo
La producción se organizará en un turno único de 8 horas diarias, operando de lunes a viernes. Para calcular la capacidad operativa anual, se parte de una estructura de días laborables y se descartan los feriados nacionales inamovibles y trasladables.
- Semanas/año: 52
- Días laborables/semana: 5: 260 días/año
- Feriados oficiales (2025): 16 días (12 inamovibles + 4 trasladables)
- Vacaciones: se alternan entre operarios para no interrumpir la producción
Días efectivos de producción: 260 – 16 = 244 días/año
Concepto | Valor |
---|---|
Jornada laboral diaria | 8 horas |
Días efectivos | 244 días/año |
Horas operativas/año | 1.952 horas/año |
Capacidad real anual de la maquinaria tipo de cada sección operativa
Sección operativa | Máquina principal | Capacidad teórica [unid/h] | Horas/año | Capacidad teórica anual [unid] | Rendimiento [%] | Capacidad real anual [unid] | Aprovechamiento [%] |
---|---|---|---|---|---|---|---|
Corte de tela | CTLR-3000 | 15 | 1.952 | 29.280 | 90 % | 26.352 | 77,45 % |
Corte de tubo | SA 142/37 | 13 | 1.952 | 25.376 | 90 % | 22.838 | 89,31 % |
Ensamble | Banco neumático Yewdale | 13 | 1.952 | 25.376 | 88 % | 22.330 | 91,36 % |
Sellado | Selladora Thermopack | 15 | 1.952 | 29.280 | 90 % | 26.352 | 77,45 % |
Etiquetado | Zebra ZT411 | 15 | 1.952 | 29.280 | 90 % | 26.352 | 77,45 % |
Determinación de la cantidad de máquinas operativas por sección, capacidad real anual de cada sección y su aprovechamiento en relación al programa de producción
Sección operativa | Producción anual proyectada [unid] | Capacidad real por máquina [unid/año] | Máquinas necesarias | Capacidad total [unid/año] | Aprovechamiento [%] |
---|---|---|---|---|---|
Corte de tela | 20.400 | 26.352 | 1 | 26.352 | 77,45 % |
Corte de tubo | 20.400 | 22.838 | 1 | 22.838 | 89,31 % |
Ensamble | 20.400 | 22.330 | 1 | 22.330 | 91,36 % |
Sellado | 20.400 | 26.352 | 1 | 26.352 | 77,45 % |
Etiquetado | 20.400 | 26.352 | 1 | 26.352 | 77,45 % |
Cuello de botella
El cuello de botella se encuentra en el Ensamble ya que es la sección con mayor grado de aprovechamiento.
Determinación de la evolución de mercaderías
Proveedores, tiempo de entregas y tipos de envío de materia prima y semi elaborados.
- Tela:
La principal materia prima que se trabajara será la tela para la cortina, en este caso de 2 tipos, blackout y screen.
Para ambas telas se elegio a Rollmat como proveedor que son importadores directos de marcas reconocidas de telas blackout y screen. Con tiempos de entrega de aproximadamente 3 días hábiles, por medio de sus propios transportistas y disponibilidad de mercadería todo el año. De esta manera contamos con un proveedor confiable, con disponibilidad continua y periodos de envió muy cortos.
- Tubos de aluminio:
Estos tubos es donde se enrolla la tela el proveedor elegido es J. L. Metales SRL , ubicada en la ciudad de Caseros en Buenos Aires zona oeste. Este mismo es un distribuidor oficial de ALUAR. Ofrecen barras y perfiles de aluminio en todos sus formatos, incluyendo tubos con un amplio stock lo cual nos brinda disponibilidad a lo largo de todo el año.
El envío promedio lleva 1 semana y teniendo en cuenta la ubicación de nuestra planta.
- Sistemas de accionamiento:
También serán comprados a Rollmat, se les comprara el conjunto entero con todos sus componentes.
Evolución de la producción
Para poder calcular esto primero deberemos definir el periodo de puesta en marcha de la fabrica.
Para este proyecto el mismo fue estimado en 3 meses, donde la producción crecerá linealmente hasta llegar al estado de régimen.
Para definir esto se realizo un estudio por un tecnólogo con experiencia en el sector y por datos obtenidos de la competencia.
Valor mensual | 57120/11,5 | 4966,95652 | |||
Mes | Ritmo de produccion al inicio % | Ritmo de produccion al final % | Produccion promedio % | Produccion mensual promedio kg | Produccion propuesta |
---|---|---|---|---|---|
1 | 0 | 25 | 12,5 | 4966,956522 | 620,869565 |
2 | 25 | 50 | 37,5 | 4966,956522 | 1862,6087 |
3 | 50 | 100 | 75 | 4966,956522 | 3725,21739 |
TOTAL | 6208,69565 | ||||
Volumen de produccion durante el resto del año | 11,5-3 = 8,5 | 8,5 x 57.120 = | 42219,13043 | ||
Volumen de produccion Año 1 | 48427,82609 | ||||
Volumen de produccion del año 2 al n | 57120 |
Stock promedio de producto elaborado
Debido a que todos nuestros proveedores tienen tiempos de entrega iguales o menores a 1 semana se tomo este periodo como el ritmo uniforme de entregas, lo cual es compatible con el tamaño de nuestros almacenes para suplir esta necesidad de materia primas.
El stock de seguridad se fijo en 0 ya que por parte de los proveedores se tiene cortos periodos de entrega y disponibilidad constante. Por lo cual almacenar un stock de seguridad generaría costos innecesarios.
Teniendo esto en cuenta y 50 semanas por año:
- Stock promedio 57.120 / 50 = 1142.4 kg
Este stock se genera inicialmente en el periodo de puesta en marcha y se va renovando manteniéndose constante.
Evolución de las ventas durante la vida útil del proyecto
En el año 1 se deberá restar la producción del stock promedio a la producción de este mismo.
48.428 - 1.142,4 = 47.285,6 kg => Año 1: 47.285,6 (16.887 cortinas).
Del año 2 al 10 se mantienen como fueron calculadas. => Año 2 al 10: 57.120 kg (20.400 cortinas).
Consumo de materia prima para el programa de producción y formación de la mercadería en curso y semielaborados
Teniendo en cuenta que durante el periodo de puesta en marcha de los primeros 3 meses, se producirá un 100% más de desperdicio no recuperable, segun estimaciones, y habiendo ya definido un desperdicio normal del 4,25%, podemos calcular:
Desperdicio Total en Puesta en Marcha = 8,5%
Desperdicio Adicional en Puesta en Marcha = 8,5%
Producción Puesta en Marcha = 6.208,7 kg
=> Desperdicio Adicional No Recuperable en Puesta en Marcha = 263.87 kg
Además, considerando que el ciclo de elaboración demanda 2 días de ritmo normal (desde ingreso de materia prima hasta producto terminado en depósito) y una operación de 240 días, la cantidad de ciclos anuales será:
Ciclos Anuales de Elaboración = 240 días / 2 días x ciclo = 120 ciclos de Elaboración al año
Calculo de Materia Prima en Proceso (Mercadería en Curso)
Componente | Valor (kg) |
---|---|
Producción diaria | 238,00 |
Días en proceso | 2 |
MP en proceso | 476,00 |
Desperdicio no recuperable (4,25%) | 20,23 |
Desperdicio recuperable (7,14%) | 33,99 |
Total MP en proceso | 530,19 |
Consumo de Materia Prima Año 1
Concepto | Valor (kg) |
---|---|
Producción puesta en marcha | 6.208,7 |
MP necesaria puesta en marcha (8,5% desperdicio) | 6.736,4 |
Producción en régimen (resto del año) | 42.219,1 |
MP necesaria en régimen (4,25% desperdicio) | 44.093,6 |
Total MP para producción año 1 | 50.830,1 |
MP en proceso y semielaborada (2 días) | 530,2 |
Consumo total de MP en año 1 | 51.360,3 |
Consumo de Materia Prima Año 2 a 10
Concepto | Valor (kg) |
---|---|
Producción en régimen | 57.120,0 |
Total MP para producción | 59.547,6 |
Cuadro de Evolucion de Mercaderias
Concepto | Año 0 | Año 1 | Año 2 – 10 |
---|---|---|---|
Ventas (kg/año) | 0 | 47.285,43 | 55.977,60 |
Stock prom (kg/año) | 0 | 1.142,40 | 1.142,40 |
Producción (kg/año) | 0 | 48.427,83 | 57.120,00 |
Mermas (kg/año) | 0 | 2.402,20 | 2.427,61 |
Consumo MP (kg/año) | 0 | 51.360,30 | 59.547,61 |
Stock MP (kg/año) | 0 | 1.142,40 | 1.142,40 |
Compra MP (kg/año) | 1.142,40 * | 51.360,30 | 59.547,61 |
*En el año 0 se hace la compra de MP para asegurar disponibilidad de Stock Inicial al año 1.
Determinación el personal
Organigrama de la empresa
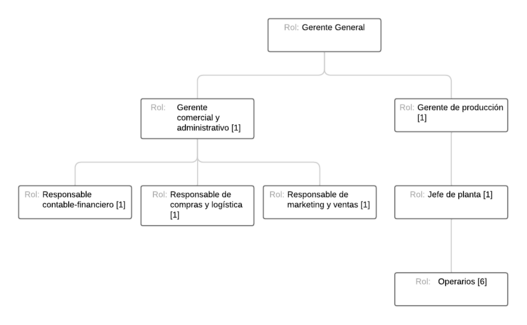
Descripción de los Puestos de Trabajo. Calificación y Formación necesaria de los Operadores
Gerente general: Responsable de la dirección estratégica y operativa de la empresa. Define la visión y misión, toma decisiones clave y coordina las distintas áreas funcionales. Se requiere formación en Ingeniería Industrial, Administración o afines. Debe contar con experiencia directiva, liderazgo sólido y visión de largo plazo.
Gerente comercial y administrativo: Supervisa la administración interna y las operaciones comerciales. Dirige al equipo de marketing, ventas y contabilidad; además de participar en análisis de mercado y estrategias de posicionamiento. Formación sugerida: Ingeniería Industrial, Administración o Marketing. Se valoran habilidades de liderazgo, comunicación y conocimientos contables.
Responsable contable-financiero: Gestiona los registros contables, flujo de caja, cumplimiento fiscal y presupuestos. Emite reportes financieros e informes para la toma de decisiones. Se recomienda formación como Contador Público o en Finanzas, con conocimientos actualizados en legislación fiscal y sistemas contables.
Responsable de compras y logística: Encargado de la adquisición de materias primas, insumos y coordinación de entregas y transporte de productos terminados. Negocia con proveedores y planifica la gestión del inventario. Formación ideal: Ingeniería Industrial, Logística o Administración. Se requieren habilidades de planificación y negociación.
Responsable de Marketing y ventas: Diseña campañas de marketing, gestiona redes sociales y coordina acciones comerciales. También interviene en el análisis de mercado y contacto con clientes. Se requiere formación en Marketing, Publicidad o Comunicación, con pensamiento creativo, habilidades interpersonales y orientación a resultados.
Gerente de producción: Planifica, organiza y supervisa todo el proceso productivo. Garantiza el cumplimiento de objetivos de calidad, tiempo y eficiencia. Coordina con mantenimiento y logística. Se busca formación en Ingeniería Industrial, con experiencia en entornos productivos y capacidad de resolución operativa.
Jefe de planta: Supervisa las actividades diarias de fabricación, aplica procedimientos de control de calidad y dirige al equipo de operarios. Resuelve imprevistos y asegura el cumplimiento de normas de seguridad. Formación técnica o en ingeniería, con fuerte capacidad de liderazgo operativo.
Operarios: Ejecutan tareas específicas del proceso productivo: corte, ensamblado, sellado, etiquetado, traslado y embalaje. Operan maquinaria, realizan controles visuales y completan registros de producción. Requieren secundario completo, buena predisposición física y formación específica interna según el puesto.
Sección operativa | Actividad principal | Operario asignado |
---|---|---|
Corte de tela | Corte inicial | 1 |
Corte de tubo | Preparación estructural | 1 |
Ensamble | Unión tela-tubo | 1 |
Sellado | Termofusión de extremos | 1 |
Etiquetado | Identificación del producto | 1 |
Y sumamos un operario más que cumple con:
- Apoyo en tareas interseccionales (traslado de herramientas/piezas, limpieza técnica)
- Control visual de calidad
- Reemplazo rotativo durante pausas o contingencias operativas
Listado de Equipos Auxiliares, Muebles y Útiles
Área | Elemento | Cantidad |
---|---|---|
Producción | Mesa de trabajo metálica | 3 |
Carros transportadores | 2 | |
Estanterías metálicas | 4 | |
Escalera tijera | 1 | |
Cesto de basura | 2 | |
Kit de herramientas manuales | 2 | |
Matafuegos tipo ABC | 2 | |
Luces de emergencia | 2 | |
Dispenser de agua | 1 | |
Aire acondicionado s | 1 | |
Balde + mopa industrial | 1 |
Área | Elemento | Cantidad |
---|---|---|
Oficina de
Producción |
Escritorio con cajonera | 2 |
Silla ergonómica | 2 | |
Computadora de escritorio | 2 | |
Impresora multifunción | 1 | |
Aire acondicionado | 1 | |
Estantería de archivos | 1 | |
Pizarra blanca | 1 | |
Matafuegos | 1 | |
Dispenser de agua | 1 | |
Teléfono fijo | 1 |
Área | Elemento | Cantidad |
---|---|---|
Oficina
Comercial |
Escritorio con cajonera | 2 |
Silla operativa | 2 | |
Computadora de escritorio | 2 | |
Impresora | 1 | |
Estantería baja | 1 | |
Teléfono fijo | 1 | |
Aire acondicionado | 1 | |
Matafuegos | 1 |
Área | Elemento | Cantidad |
---|---|---|
Comerdor | Mesa de comedor | 2 |
Sillas | 13 | |
Heladera con freezer | 1 | |
Microondas | 1 | |
Cafetera eléctrica | 1 | |
Vajilla básica (juegos) | 13 | |
Dispenser de agua | 1 | |
Aire acondicionado | 1 | |
Cesto de residuos | 2 | |
Matafuegos | 1 |
Anteproyecto de Planta
Plano de la Planta mostrando la distribución de las distintas áreas
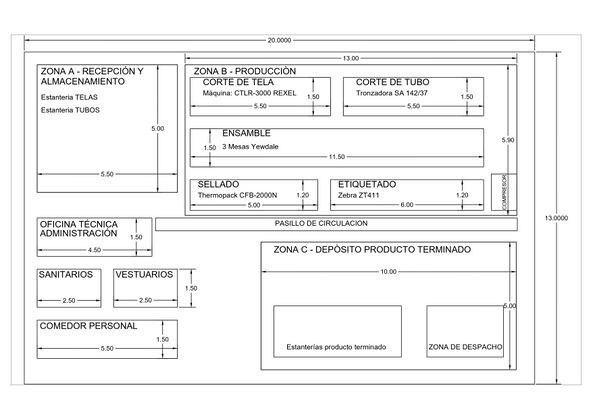
El terreno se encuentra ubicado en una esquina, con acceso de camiones en el frente para carga y distribucion de producto terminado y en el lateral izquierdo para descarga de materiales.
Plano mostrando el recorrido de los materiales
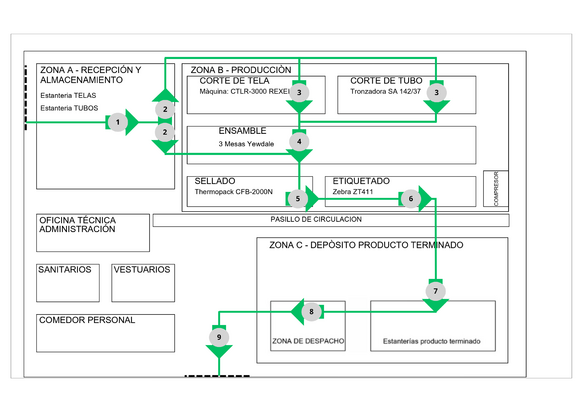
Cronograma de Ejecución
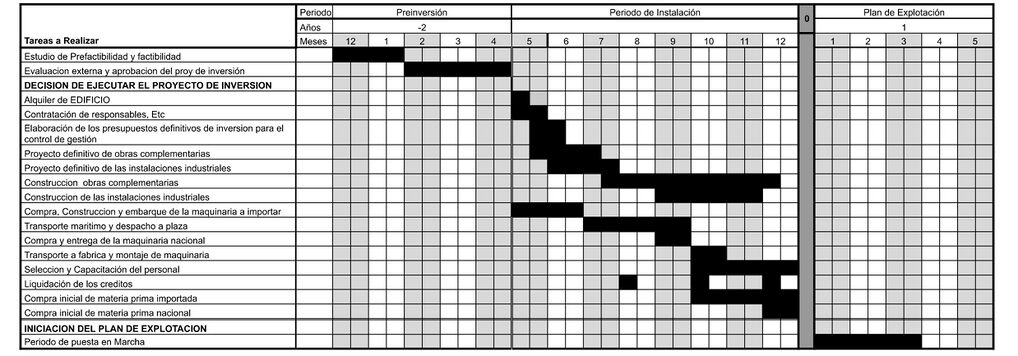