2018/Grupo3/DimensionamientoTecnico
3. Definición del proceso de fabricación
3.1 Recepción:
El proceso de fabricación comienza con la recepción de la materia prima, y el almacenaje de la misma en los depósitos. La distribución de los materiales que se recepcionan en el depósito se divide en 6: la zona de planchas de cartón corrugado, de artículos accesorios para la carga y descarga de los productos, de bolsas de polietileno, de tapas de cartón para los bins, de tanques de cola y por último la zona de los pallets de madera.
3.2. Encoladora:
Una vez recibido el material, y almacenado, se coloca un pallet lleno de planchas de cartón al lado del primer puesto de trabajo, que es la zona de la encoladora, junto con la cola que será utilizada en el proceso. Allí, se realiza el pegado de las 5 planchas de cartón coarrugado de forma escalonada, para generar las paredes del futuro contenedor. Cada plancha tiene una longitud de 1,60m y la mesa esta diseñada de tal manera que se genere un escalonamiento con 15cm de distancia entre cada placa, para llegar a un largo de 2,20m. Se realiza de forma escalonada ya que luego esa plancha de 5 capas, es pegada con otra plancha idéntica, formando una plancha de con un largo total de 4,40 m, con dos escalonados en cada una de las puntas, que es lo que luego nos ayudará a cerrar el cerco.
3.3 Prensa:
Una vez que disponemos de nuestra placa de 4,40 m, se desplaza al segundo puesto de trabajo que es la presa. Allì lo único que se hace es generar una presión en toda la plancha, ya que eso va a ser lo que genere el futuro cerco del contenedor. Este proceso se realiza desplazando la plancha por unos rodillos, hasta que llega a unos topes que la posicionan para que luego, solo reste presionar un botón para que los pistones bajen y generen una presión contra nuestro producto, asegurando que el pegado se realice eficientemente.
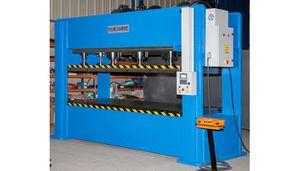
3.4. Maquina 2
Luego de que la pieza termine de ser prensada en la primera prensa, se mueven los topes, y se desplaza con la ayuda de los rodillos hacia la máquina 2. El proceso de fijación del producto es el mismo, con unos topes que aseguran que nuestro compuesto de capas este bien posicionado. Esta máquina esta compuesta por 4 "V" de metal, que lo que hacen es marcar nuestro compuesto laminado desde arriba, generándole cuatro muecas, que en un futuro van a ser las aristas de nuestro contenedor. Esas "V" metálicas están conectadas a una serie de pistones que son los realizan la fuerza necesaria para doblegar el material, y el operario lo trabajará con un botón.
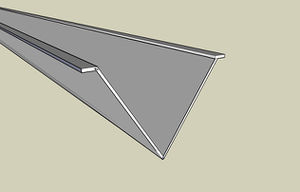
3.5 Prensa 2:
Una vez marcadas nuestras aristas, nuestro compuesto laminado pasa a la segunda prensa del proceso productivo, en donde se dobla de forma tal que el escalonado de las puntas encajen, y con un segundo encolado, se forme nuestro cerco, que luego con la ayuda de esta prensa, es presionado nuevamente con el mismo mecanismo de la prensa numero 1, asegurándonos que selle bien.
3.6 Araña
Con el cerco ya disponible, se coloca en el último puesto de trabajo llamado araña. Esta zona esta compuesta de 4 pilares que hacen de eje para poder introducir por fuera el cerco, y de esta manera poder pegarle las escuadras de ambos lados que lo que hacen, es darle rigidez y estructura al DynaCub. Se la llama araña ya que cuenta con un dispositivo móvil que baja del techo de la fabrica, y presiona hacia adentro el contenedor. De esta manera, las escuadras son selladas y bien pegadas. Este proceso se repite para poder realizarlo de ambos lados del contenedor.
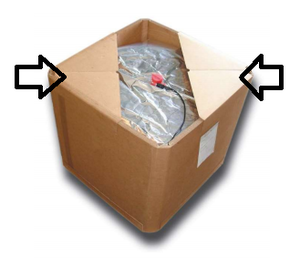