2025/Grupo8/DimensionamientoFisico
Determinación de la Localización
La definición de la localización se resume a dos ubicaciones principales, General Pacheco y Zarate.
Alternativa 1 | Alternativa 2 | |||||
General Pacheco | Zarate, Partido de Tigre | |||||
(Buenos Aires, Argentina) | (Buenos Aires, Argentina) | |||||
Factor | IRFP | DRFA | IRFP x DRFA | DRFA | IRFP x DRFA | |
1 | Medios de transportes | 3 | 9 | 27 | 8 | 24 |
2 | Mano de Obra especializada | 5 | 8 | 40 | 7 | 35 |
3 | Cercania a proveedores | 4 | 8 | 32 | 6 | 24 |
4 | Cercania del Mercado | 5 | 9 | 45 | 7 | 35 |
5 | Legislación habilitante para el desarrollo de Actividades Industriales | I | SI | PA | SI | PA |
6 | Riesgo ambiental del terreno | 1 | 7 | 7 | 8 | 8 |
7 | Valor y disponibilidad de Terrenos | 3 | 6 | 18 | 9 | 27 |
8 | Topografia del Suelo | 2 | 8 | 16 | 8 | 16 |
9 | Acceso a servicios basicos | 5 | 9 | 45 | 8 | 40 |
10 | Seguridad Urbana Industrial | 4 | 7 | 28 | 8 | 32 |
11 | Comunicación y Conectividad | 4 | 9 | 36 | 7 | 28 |
Total | 360 | Total | 294 | Total | 269 | |
Total % | 81,67% | Total % | 74,72% |
A continuación se presenta el cuadro comparativo con los factores importantes para el proyecto y sus ponderaciones para cada opción. En función de la ponderación, se determina que el lugar en donde se debe ubicar la planta es General Pacheco.
Definición Técnica del Producto
Para la descripción del producto y los posteriores análisis del proceso productivo, se trabajará con un producto representativo. Puntualmente se usara como referencia un parabrisas perteneciente a la marca Renault (siendo este uno de los potenciales clientes), específicamente con el modelo H1312.
Planos del Producto
Parabrisas Serigrafiado sin Inserto
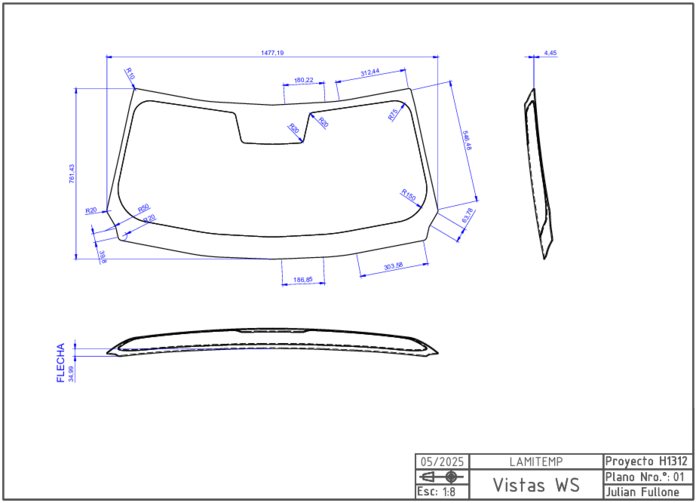
Bracket para espejo
Este producto no se fabrica internamente en la empresa, pero al formar parte del parabrisas final se dibuja y diseña para una correcta representación de este último
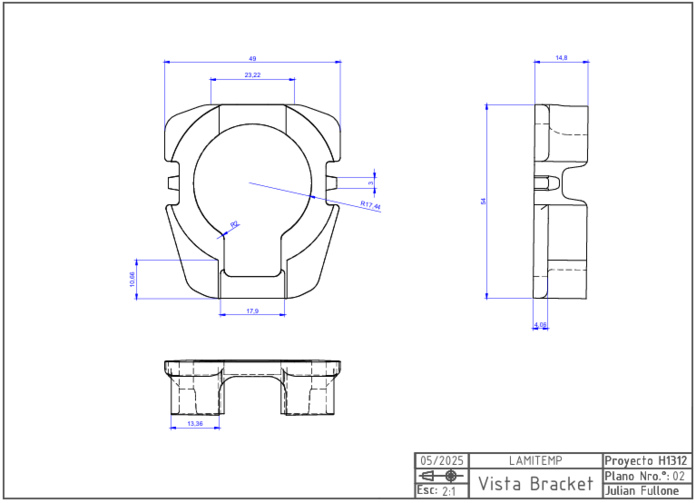
Modelado 3D
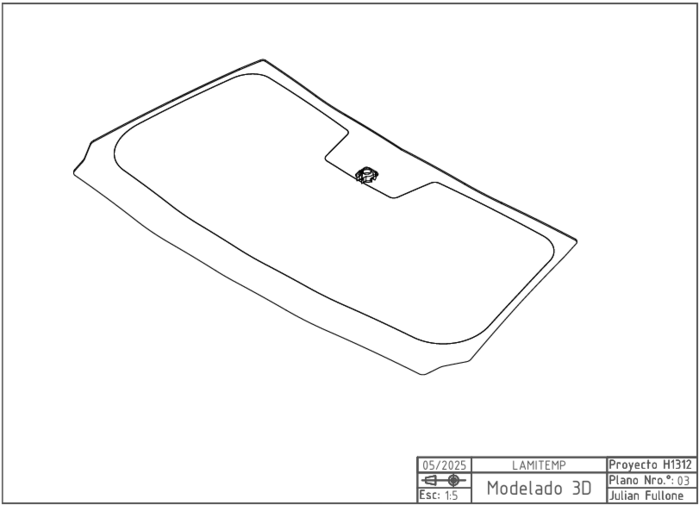
Listado de Materiales (BOM)
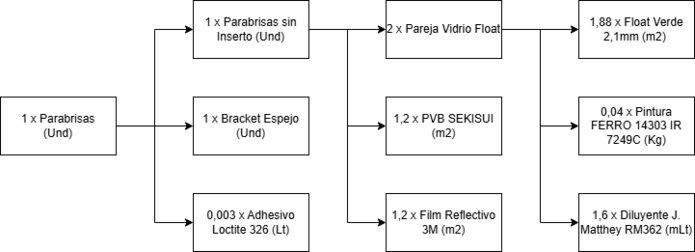
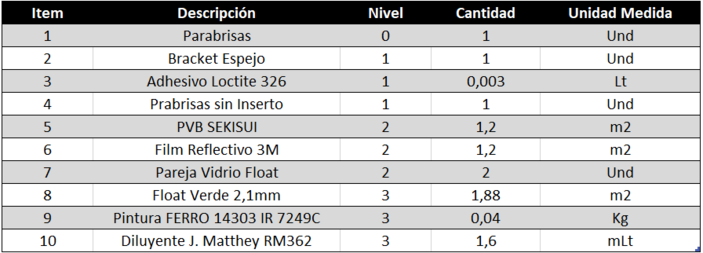
Especificaciones Técnicas y Características condición del Producto
- Peso: 9kg
- Espesor final: 4,45mm
- Tolerancia banda serigrafía: ±0,2 mm
- Curvatura/Flecha: 34mm
- Transparencia mínima: 75%
- Distorsión: El parabrisas no puede presentar distorsión de la imagen
- Respuesta al impacto: Al realizar ensayo de impacto con bola sobre el parabrisas final, la ruptura tiene que formar un círculo con arañas internas y no presentar desprendimiento de partículas de vidrio visibles
- Aspecto visual: El parabrisas no debe presentar ninguno de los siguiente defectos.
- Cachaduras
- Rayaduras
- Burbujas de aire
- Manchas de serigrafía fuera de la banda
- Banda de serigrafía incompleta/con puntos sin serigrafiar
Normas Aplicables
En lo que respecta a las normativas, solo existe una única aplicada estrictamente al producto y es el Decreto 779/95[1] que es una regulación a nivel nacional. La restricción mas importante de este Decreto es que los parabrisas deben contar con una transparencia mayor al 75%, siendo este un punto determinante para la conformidad del producto.
Cabe destacar que se pueden sumar algunas restricciones por parte de los clientes, pero las mismas son explicitadas en los planos del producto en cuanto a variaciones de tolerancias.
El resto de normas mencionadas en el Dimensionamiento Comercial corresponde a condiciones del proceso.
Plan de Ensayos
El plan de control de calidad se distribuirá en distintas etapas del proceso productivo, combinando etapas exclusivas de control y operaciones con controles visuales. Esto con el fin de identificar y segregar de forma inmediata aquellos semielaborados que no cumplan con los aspectos mencionados en las especificaciones técnicas.
- Recepción de materiales: Los materiales recibidos se pueden catalogar en dos grupos.
- El primero es el Vidrio Float, siendo este el insumo más importante del producto y a la vez el más delicado. Al recibir los lotes del insumo se deberá segregar uno de ellos, desarmarlo, evaluar las condiciones visuales del mismo y aplicar ensayos de metrología sobre dos láminas de float.
- El segundo grupo integra al resto de insumos, en este caso el control debe centrarse en controlar las fechas de vencimiento y controlar que el aspecto visual de los mismos sea el adecuado.
- Control en Unidades de Trabajo: En la última sección operativa de cada Unidad de Trabajo se deberá realizar el segregado de la primera pieza. En el propio puesto se deberá hacer un control visual y por medición de dimensiones según los valores indicados en las instrucciones de control (la información sobre la documentación necesaria se explicará al final de esta sección). A su vez, metrología deberá retirar las piezas antes de finalizado el turno para hacer pruebas físicas al semielaborado.
- Control en Puestos de Trabajo: A lo largo del proceso productivo se podrán encontrar dos tipos de puestos distintos, los operativos y los de control. Las acciones de control de cada uno serán distintas.
- Los puestos operativos harán controles visuales, en donde se buscarán fundamentalmente defectos. El objetivo es que durante la actividad productiva se logren identificar piezas claramente no conformes y se segreguen rápidamente, disponiendo el producto en los correspondientes tachos de cada puesto. Es importante destacar que esto se podrá realizar al final de las unidades de trabajo y en los puestos semi-automaticos y manuales.
- Los puestos de control harán un control más exhaustivo, en donde se probarán aspectos más técnicos como puede ser la transparencia, dimensiones, curvaturas, así como tambien los defectos visuales. Estos requerirán de instrumentos puntuales, como lo son bancos con luces para probar la transparencia, reglas de flecha, entre otros.
En todos los puestos se deberá contar con documentación adicional para facilitar la identificación de fallas. Los documentos más importantes son:
- Instrucciones de Control: Cada puesto contará con una IC específica para la actividad realizada en el mismo. Las mismas definen las dimensiones, valores y características conformes para el producto. Estas se usan exclusivamente para el control de primera pieza.
- Ayudas visuales: Las mismas se encontrarán en todos los puestos y contarán con información genérica de las no conformidades. Fundamentalmente integrando referencias a los tipos de defectos para una fácil comparación e identificación.
- Instrucciones de Fabricación: Se utilizarán no como un recurso para controlar el producto, sino como una herramienta para poder repasar el proceso productivo y asi evitar errores en el mismo.
Acondicionamiento del Producto
El producto se distribuirá a los clientes a traves de un embalaje metalico especial. El mismo es adaptable a distintas dimensiones de parabrisas y permite garantizar la seguridad y optimización del espacio tanto en el almacenaje como en el transporte. Puede almacenar hasta 30 parabrisas en simultaneo. El plano del mismo es el siguiente.
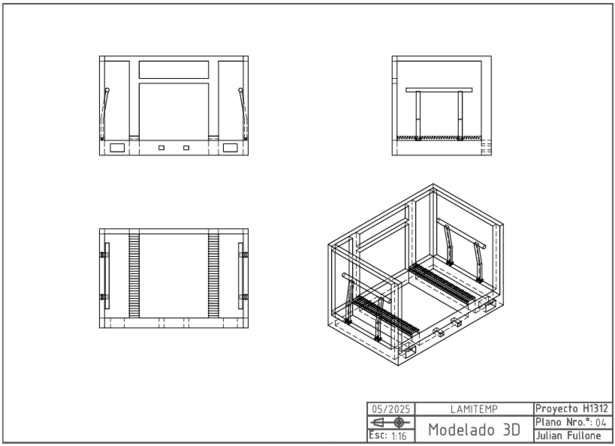
Como medida adicional, el embalado se complementa con el zunchado de los parabrisas a traves de los orificios delanteros y traseros del rack metálico.
Definición del Proceso de Producción
Diagrama de Flujo de Fabricación y Control

Diagrama de Flujo de Materias Primas-Semielaborados

Cursograma Sinóptico
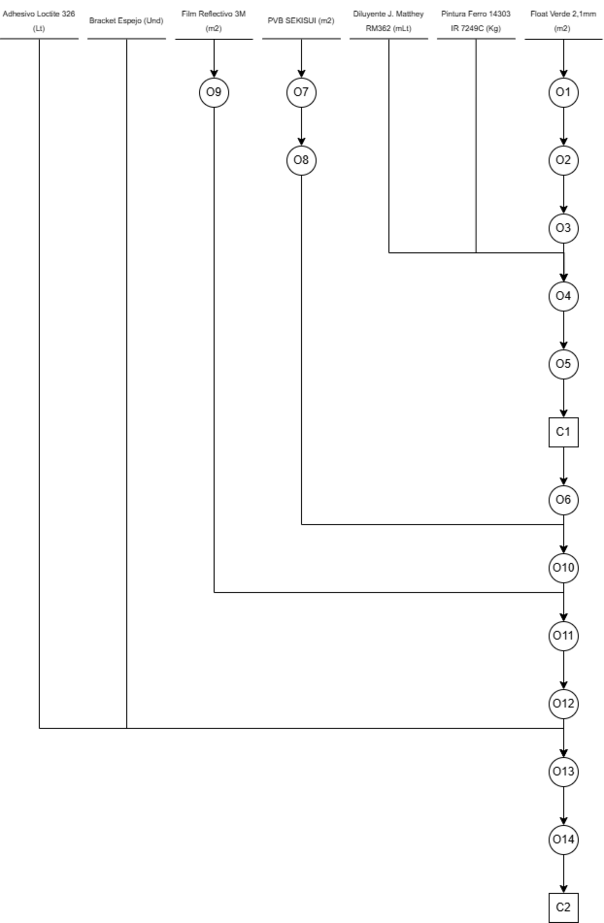
Descripción del Proceso Productivo
En esta sección se describirán cada una de las operaciones que componene al proceso productivo y las necesidades de personal para cada una de ellas.
Operación 1: Consiste en el corte de las láminas de Vidrio Float a través de una máquina CNC. La misma realiza la operación de forma automática a partir de una punta metálica que marca el vidrio, al terminar el contorneado se produce un pequeña sacudida que desprende el vidrio con la posterior segregación del excedente. Se requiere exclusivamente de un único operario que haga las actividades de preparación de la máquina, en lo que refiere a definición del modelo de Parabrisas a producir, controles de primera pieza y seguimiento del correcto funcionamiento de parámetros de la máquina. La carga de la materia prima se debe hacer con Autoelevador, acercando el lote a utilizar al puesto de trabajo y colocándolo en la alimentación de la maquinaria. A partir de esa instancia el propio equipo se encarga de tomar de a 1 pieza de vidrio y realizar la correspondiente transformación.
Operación 2: Es inmediatamente posterior a la máquina de corte, estando estas comunicadas por una cinta transportadora. El equipo fija con ventosas la lámina de vidrio cortada, para luego hacer una pasada superficial por el contorno puliendo las imperfecciones del corte. Al ser una máquina integrada con la de corte, el control y preparación se deben hacer en conjunto con esta, por ende, se requeriría al mismo operario de la Operación 1.
Operación 3: Es inmediatamente posterior a la máquina de pulido, estando estas comunicadas por una cinta transportadora. En este caso la lámina de vidrio es expuesta a chorros de agua que hacen una limpieza rápida y efectiva del semielaborado para luego hacer un proceso de secado rápido a través de aire caliente. Al ser una máquina integrada con las anteriores, el control y preparación se deben hacer en conjunto con estas, por ende se requeriría al mismo operario de la Operación 1 y 2. En todo nuevo lote de producción de una versión de parabrisas se deberá segregar la primera pieza para hacer controles de calidad y el posterior ensayo de metrología.
Operación 4: En esta operación se realiza el serigrafiado de las láminas de vidrio. El mismo se realiza con una impresora de serigrafía comunicada con las anteriores máquinas a través de una cinta transportadora. Las láminas de vidrio ingresan al equipo y son pintadas a través de dos pasadas de un espátula automática que desplaza la pintura de un extremo a otro del float. Para este proceso se requieren de pantallas, es decir, la matriz de serigrafía, siendo esta 1 por modelo. Se requiere de un único operario que se encarga de la preparación de la pintura, ya que la misma debe mezclarse con un diluyente antes de poder ser volcada en la máquina de serigrafiado. A su vez se encarga de las actividades de preparación del puesto y del cambio de pantallas de ser necesario.
Operación 5: La siguiente etapa es el secado de la serigrafía. Para ello el float pasa por un horno de secado y luego hace un breve recorrido por cinta transportadora para aclimatar el vidrio y volverlo manipulable para siguientes etapas del proceso. Esta es una actividad netamente automática en la que el operador solo debe realizar el set up de las máquinas y controles de los parámetros de las mismas. Por este grado de automatización el mismo operador que se encarga de la Operación 4 se puede encargar de esta operación.
Control de calidad 1: Esta es la primera etapa netamente de control. La misma se ubica inmediatamente después del proceso de secado. No se requiere de maquinarias específicas, sólo de un operario que controle visualmente el estado de la serigrafía y el vidrio. Así como también la realización de controles de especificaciones contra las Instrucciones de Control. También se deberá segregar la primera pieza del lote para que se puedan ejecutar los posteriores ensayos de metrología. En caso de encontrar no conformidades el producto se deberá retirar del proceso y tirar en los tachos designados en el puesto. Las piezas conformes se deberán cargar en los carros designados hasta llenarlos con un total de 30 láminas de vidrio.
Operación 6: En esta etapa se realizará el curvado de las parejas de vidrio. Los carros a la salida de CC1 se transportan manualmente hasta los Hornos. Las láminas de vidrio se cargan de una a la vez en el equipo, colocándose en la matriz correspondiente y aplicando litopone en el contorno metálico de dicha matriz para evitar el pegado del vidrio. El horno se encargará luego aplicar calor, causando la decantación y, por ende, el curvado del vidrio según el molde de la matriz. Una vez que la pieza cumple su tiempo dentro del horno debe ser retirada por el operario, utilizando los correspondientes EPPs, para luego colocarla en un molde para hacer la medición de la flecha de la pieza. En caso de que la pieza esté conforme según la medición de flecha, se coloca en un carro de descansado para que disminuya su temperatura. Si la pieza es no conforme, se segrega. Esta actividad debe ser realizada por 3 operarios:
- Uno que se encarga de las descargas y medición.
- El segundo que se encarga de las cargas y preparación de la matriz.
- Y el tercero que une las parejas de vidrio (Macho + Hembra) y las deposita en un carro para luego transportar el lote completo a la Operación 10.
Operación 7: Esta es una tarea de preparación del Polivinil Butiral (PVB). El mismo se comercializa en rollos y antes de poder ser utilizado debe ser procesado para lograr los valores adecuados de temperatura y humedad que garantizan una correcta adherencia. La máquina es plenamente automática, el operario que la maneje solo debe realizar la carga del rollo y el set up de la máquina según parámetros definidos. A su vez se debe hacer un seguimiento desde el tablero de la máquina para confirmar que el proceso sea de forma adecuada.
Operación 8: El corte de las láminas de PVB se realiza en la misma máquina que la Operación 7. Es una tarea propia del equipo que porciona en rectángulos de medida configurable el polivinil. Se requiere exclusivamente de un operario que tome las láminas cortadas y las apile una encima de la otra para su posterior uso en el armado. El operario es el mismo que prepara la Operación 7, debido al grado de automatización de la máquina.
Operación 9: En esta etapa se deberá porcionar el Film Reflectivo para su posterior colocación sobre el parabrisas. La actividad se hará de forma manual con un solo operario, este deberá desenrollar el rollo de film y con una herramienta de corte y regla porcionará las distintas láminas de Film.
Operación 10: En esta etapa se unirán las parejas de vidrio (Macho + Hembra) por medio de la lámina de PVB. Las parejas de vidrio pre armadas en la Operación 6 son tomadas entre dos operarios que las colocan sobre una cinta transportadora. Luego, por el accionar de un botón la cinta se frena y una ventosa baja verticalmente y succiona la lámina superior de la pareja. Al levantarla, los mismos dos operarios toman la lámina de PVB dispuesta en el puesto y la colocan encima de la pareja inferior de vidrio. Al accionar nuevamente el botón, la ventosa vuelve a bajar verticalmente y aplica una presión a ambas láminas de vidrio, provocando así la adherencia entre ambas con el PVB. En ese mismo momento, los operarios utilizarán herramientas de corte para rebabar el excedente de PVB con un movimiento a 45°. Por último accionarán nuevamente el botón que reinicia el avance de la cinta transportadora.
Operación 11: Entre dos operarios tomarán las láminas de Film Reflectivo y las aplicarán sobre el parabrisas. Para ello un operario deberá sostener la lámina, mientras que el segundo aplica presión con una espátula empezando desde un extremo del parabrisas para pegar el Film. Una vez colocado el Reflectivo, se deberá rebabar el excedente con una herramienta de corte y un movimiento a 45°.
Operación 12: En esta etapa se realiza una Pre-Eliminación del aire del parabrisas. Al realizar el armado del mismo, quedan espacios intermedios llenos con aire que disminuyen la adherencia entre las parejas y difcultan su manipulación en las siguientes etapas. Para ello, una maquina disminuye esos espacios a partir de la aplicación de presión en los bordes del parabrisas. Al ser un proceso completamente automático, solo se necesitaría un empleado para realizar el seteado del equipo. La alimentación del semielaborado a la maquina viene directamente desde la Operación 11 a traves de cintas transportadoras.
Operación 13: Una vez realizada la Pre-Eliminación de aire, se deberá insertar el bracket para el espejo retrovisor. Esta tarea es completamente manual y es realizada por un único operario (El mismo que realizó el seteo de la maquina de la Operación 12), el cual realiza una primera inspección visual del parabrisas, para segregar la pieza en caso de ser necesario. Luego tomará el adhesivo Loctite y aplicará una película del mismo en el contorno de la base del inserto, para después pegarlo manualmente sobre el parabrisas. El posicionamiento del inserto deberá coincidir con la marca de la serigrafía diseñada para dicho fin. El parabrisas insertado es colocado en el carro para Autoclave.
Operación 14: En esta etapa se busca eliminar completamente el aire residual entre las parejas de vidrio. Los carros de Autoclave (Cuentan con 60 Parabrisas), son cargados en el equipo con un tractor de arrastre. Una vez llenado el Autoclave, el operario deberá dar inicio al proceso de eliminación de aire desde la consola. Al finalizar el mismo, el operario descargará los carros y los trasladará a la última etapa de control.
Control de calidad 2: La etapa de carrusel consiste en una máquina rotativa, con distintas "sillas", en las cuales se depositan los parabrisas a controlar. A medida que los parabrisas giran, un operario realiza el control visual de los mismos y de características de transparencia, pudiendo frenar o dar avance al sistema de carrusel a voluntad. Además, deberá contar con un lápiz de cera para poder marcar desperfectos e indicar la conformidad del producto. Se requerirá de otros dos operarios más, uno encargado de las tareas de carga de parabrisas al sistema de carrusel y el otro encargado de la descarga y preparación del pallet metálico o de madera según el tipo de producto. El lote final de parabrisas será de 60 parabrisas que se distribuirán en 2 pallet (30 unidades por Pallet).
Los elementos de seguridad que se deberán utilizar en toda la planta sin excepción son:
- Anteojos de seguridad.
- Protectores auditivos endoaurales.
- Zapatos de seguridad.
- Pantalones que cubran la totalidad de la pierna.
Luego habrá ciertos elementos de seguridad que serán circunstanciales, en función de la tarea realizada.
- Guantes y mangas anticorte, exclusivamente para tareas en las que se manipule directamente el vidrio.
- Guantes de latex, para el uso de pegamentos o químicos.
- Casco de seguridad, para actividades en altura.
- Arnés de seguridad, para actividades en altura.
- Delantal Kevlar tricapa, para actividades en el horno.
- Guantes resistentes al calor, para actividades en el horno.
Logística Interna y Externa
En lo que respecta al transporte y movilización de de los insumos y semielaborados dentro de la empresa se contaran con los siguientes elementos.
Autoelevadores: Los mismos se utilizarán al inicio y final del proceso productivo.
- Inicialmente transportarán los pallet de vidrio float y los depositarán en la sección de alimentación de la maquina cortadora.
- Al final del proceso se encargarán de transportar los pallet de producto terminado al sector dedicado para su almacenamiento y posterior despacho.
Tractor de arrastre: Los mismos serán utilizados para movilizar los racks de semielaborado en distintas etapas intermedias.
- Traslado desde salida de serigrafía a ingreso hornos.
- Traslado desde salida de hornos a ingreso armado.
- Traslado desde salida de insertado a ingreso de autoclave.
- Traslado desde salida de autoclave a ingreso de control de calidad.
Cintas trasportadoras: Se utilizará para el avance de insumos y semielaborados en los siguientes recorridos.
- Corte-Pulido-Lavado-Serigrafiado-Control de calidad 1.
- Armado-Aplicación Film-Pre eliminado de aire-Insertado.
En lo que respecta a la logística externa, la misma se realizará con una flota de camiones propios, siendo la cantidad de camiones un total de 2. Esto perimitirá gestionar las entregas a los clientes de forma eficiente, segura y con la minima demora posible.
Determinación de las máquinas e instalaciones
Especificaciones Técnicas de las maquinas (capacidades, tamaño de lotes y tiempos)
Horno de Curvado
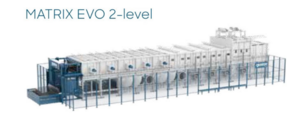
- Modelo: Matrix EVO 1220, 4 vagones[2].
- Máximo tamaño de cristal: 1200 x 1980 mm.
- Lote: 4 piezas (Un vidrio por vagón).
- Capacidad media del horno: 22 piezas/hora.
- Consumo de energía: 168 KWh/dia.
- Dimensiones: 8000 x 2300 x 1600 mm
Equipos de eliminado de aire
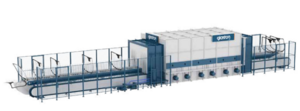
- Modelo: IKU 1423 - 600 De-airing conveyor.
- Máximo tamaño de cristal: 1400 x 2300 mm.
- Capacidad: 75 piezas/hora.
- Consumo de energia: 155 kWh/dia.
- Dimensiones: 9700 x 5000 x 3400 mm
Ventosas para la colocación de placas de PVB
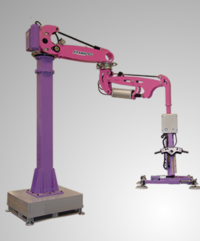
- Modelo: Famatec - Friendly Glass.
- Capacidad Máxima de carga: 500 kg.
- Capacidad: Estará determinada por la mano de obra en el puesto.
- Radio de trabajo: 3000 mm.
- Rango vertical: 1600 mm.
- Dimensiones: 1200 x 1200 mm.
Line de Corte CNC

- Modelo: Vetromac SA40-26[3].
- Peso: 1800 kg.
- Consumo de energía: 48 Kwh/dia.
- Precisión de corte: ± 0,15 mm.
- Capacidad: 30 piezas/hora.
- Dimensiones: 4000 x 2600 mm.
Pulidora Automatica
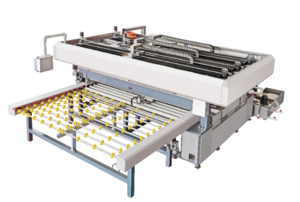
- Modelo: Lijiang[4].
- Máximo tamaño de cristal: 3000 x 2500 mm.
- Altura de trabajo: 930mm.
- Capacidad: 30 piezas/hora.
- Consumo de agua: 6,7 litros/pieza.
- Consumo de energia: 160 Kwh/dia.
- Dimensiones: 6920 x 4600 x 2200 mm.
Lavadora Automática
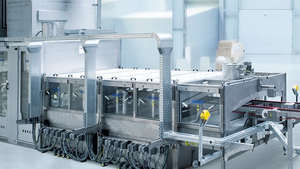
- Modelo: Benteller[5].
- Minimo tamaño de largo: 500 mm.
- Minimo tamaño de ancho: 1000 mm.
- Ancho de vidrio: 1,4 - 6 mm.
- Consumo de energía: 140 Kwh/dia.
- Consumo de agua: 8 litros/pieza.
- Capacidad: 30 piezas/hora.
- Dimensiones: 5 500 × 3 500 × 2 840 mm.
Máquina de Serigrafiado
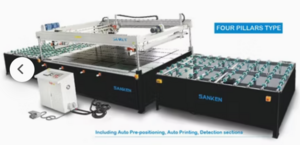
- Modelo: SKP‑1015
- Capacidad: 40 piezas/hora
- Máxima área de impresión: 1000 x 1500 mm
- Dimensiones: 6500 x 1800 x 1800 mm
- Consumo de energía: 80 Kwh/dia.
- La máquina también cuenta con un proceso de secado para el posterior control de calidad.
Autoclave
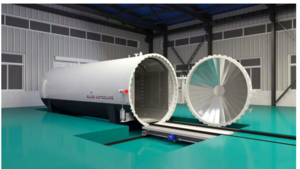
- Modelo: Lijiang[6].
- Capacidad: 60 piezas/hora.
- Consumo de energia: 198 Kwh/dia.
- Dimensiones de la maquina: 3330 x 2850 x 1180 mm.
- Tamaño de lote: 180 piezas.
Procesadora de PVB
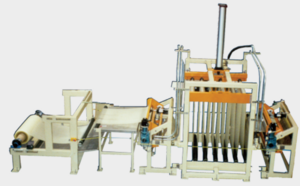
- Modelo: Glassline.
- Capacidad: 60 piezas/hora.
- Potencia: 60 Kwh/dia.
- Dimensiones: 3750 x 2000 x 2350 mm.
Consumo de Energía, Agua y Otros Servicios
Consumo de Energía
Para el consumo de electricidad confeccionamos una tabla que tiene en cuenta todas las maquinas utilizadas en el proceso que necesitan estar conectadas a la red eléctrica y además otros consumos generales utilizados diariamente.
Maquina | Cantidad | Pot consumida (kW h) | Pot total (kW h) | Horas / año | kW h por año |
Horno de Curvado | 1 | 7,00 | 7,00 | 1.920 | 13.440 |
Equipos de eliminado de aire | 1 | 6,46 | 6,46 | 1.920 | 12.400 |
Lineas de corte CNC | 1 | 2,00 | 2,00 | 1.920 | 3.840 |
Pulidora Automatica | 1 | 6,67 | 6,67 | 1.920 | 12.800 |
Lavadora Automatica | 1 | 5,83 | 5,83 | 1.920 | 11.200 |
Maquina de Serigrafeado | 1 | 3,33 | 3,33 | 1.920 | 6.400 |
Autoclave | 1 | 8,25 | 8,25 | 1.920 | 15.840 |
Procesadora de PVB | 1 | 2,50 | 2,50 | 1.920 | 4.800 |
Luminaria | 40 | 0,04 | 1,60 | 2.400 | 3.840 |
Computadora | 8 | 0,16 | 1,28 | 1.920 | 2.457,6 |
Impresoras | 1 | 0,45 | 0,45 | 360 | 162 |
Heladera | 2 | 0,115 | 0,23 | 8.760 | 2.014,8 |
Microondas | 1 | 0,065 | 0,07 | 240 | 15,6 |
Ventiladores | 8 | 0,575 | 4,60 | 100 | 460 |
Dispenser de agua | 2 | 0,575 | 1,15 | 1.920 | 2.208 |
Cafetera | 1 | 1,15 | 1,15 | 240 | 276 |
Total | 92.154 |
Nos deja un total de 92.154 Kwh/ año.
Consumo de Agua
En nuestro proceso de fabricación tendremos que tener en cuenta la lavadora y pulidora automática. Con los datos anteriores podemos estimar que el consumo de agua entre las dos máquinas será 432.000 litros/año.
Los demás consumos de agua los estimaremos en base a la cantidad de baños, lavamanos, dispensers que equivalen a unos 205.600 litros/año.
Dejándonos un total de 637.600 litros/año.
Otros Consumos
Dentro del proceso productivo destacaran el consumo de tinta para el proceso de serigrafiado y PVB para el armado del parabrisas.
- La tinta se obtendrá en bidones de 10 litros para su carga manual.
- Las láminas de PVB se obtendrán a través de rollers de 200 m.
Mantenimiento, Medios de Control y Sistemas de Seguridad
Mantenimiento
Al estar gran parte del proceso conectado entre máquinas automáticas es importante el mantenimiento del mismo para evitar fallas inesperadas, stock de pie de máquina, defectos en el producto terminado y asegurar la continuidad operativa.
- Cortadora CNC. Limpiar los rieles y guías con paño seco al final de cada turno, lubricar los ejes X e Y una vez por semana, revisar el nivel de aceite de la bomba de vacío cada 15 días, cambiar la cuchilla luego de 10.000 cortes.
- Lavadora Automática. Sacar y limpiar los filtros de agua una vez por semana, revisar las boquillas de aspersión y destaparlas si están obstruidas, verificar que los cepillos no están gastados o deformados.
- Pulidora Automática. Verificar el estado de los discos abrasivos todos los días antes de arrancar, revisar el torque de los motores mensualmente.
- Horno de curvado. Calibrar los sensores de temperatura cada mes, verificar el estado del aislante térmico interior y revisar las resistencias térmicas cada 6 meses o si se detecta un calentamiento desigual.
- Procesadora de PVB. Limpiar los rodillos calientes todos los días con alcohol isopropílico, revisar la presion de los rodillos semanalmente, cambiar los filtros de aire del entorno cada dos semanas y mantener una temperatura de 15 a 20 °C.
- Serigrafeadora. Calibrar el marco para que quede alineado con la lámina de vidrio al iniciar la jornada laboral, lubricar el sistema de avance del bastidor una vez por semana, revisar el estado de la rasqueta y su filo.
- Autoclave. Revisar el nivel de aceite de la bomba cada semana, inspección y limpieza del sellado de la puerta por cada ciclo, calibrar los sensores de temperatura y presión, limpiar las válvulas de purga cada 15 días.
Medios de Control
Son primordiales para que los operarios puedan tener completo control sobre las operaciones.
- Controladores Logísticos Programables (PLCs). Contaremos con más de un control distribuidos a lo largo de la fábrica, algunos tendrán la capacidad de controlar más de una maquina como es el caso de cortado, pulido y lavado ideales para automatizar estos tipos de procesos.
- Interfaces Hombre-Maquina (HMIs). Mejorará la velocidad de interacción del operario para el control de la temperatura del horno de curvado, los sistemas eliminación de aire y ver alarmas de la autoclave. Permite monitoria ciclos completos con registros de lotes alarmas y tendencias. Aparte lleva la trazabilidad del proceso por fecha y sección.
- Variadores de Frecuencia. Controla la velocidad de los motores eléctricos de los equipos dándole protección a mi equipo y un ahorro energético.
- Sensores. Se utilizarán sensores industriales para controlar variables críticas como temperatura, presión, vacío, humedad y posición. Estos permiten asegurar la calidad del producto y la eficiencia operativa en etapas como serigrafía, laminado, curvado y autoclave. Estarán integrados a sistemas de control como PLCs y HMIs para una supervisión continua y automatizada.
Sistemas de Seguridad
- Elementos de Protección Personal (EPP). Lentes de seguridad, guantes anticorte y térmicos, protectores auditivos, ropa de trabajo ignifuga y barbijos.
- Dispositivos. botones para paradas de emergencia, encapsulado en partes móviles y poleas, detectores de puertas abiertas, alarmas visuales y sonoras ante fallos o ciclos peligrosos.
- Sistema de deteccion y extincion. Extintores, detectores de humo y de temperatura, señalización de rutas de evacuación y salidas de emergencia.
- Simulacros y Capacitación. Simulacros de evacuación, capacitación en uso de EPP, primeros auxilios y manejo de materiales peligrosos, protocolos de actuación en caso de accidentes.
Definición de cuadro de datos iniciales
Antes de realizar los cálculos correspondientes al Balanceo de Línea, se presentará a continuación un grupo de tablas con información que se referenciará y utilizará a lo largo del proceso de cálculo.
En primer instancia y tomando como punto de partida el Diagrama de Flujo de Materias Primas-Semielaborados, podemos determinar las cantidades de desperdicio para cada materia prima. Con esta información podemos armar el siguiente cuadro resumen de los insumos, en donde definiremos una ponderación para cada materia prima para así tener una equivalencia con el producto terminado. Con esta ponderación, se afectará a los porcentajes de desperdicio para tener un desperdicio referenciado al parabrisas.

Otra información adicional para el cálculo es que se trabajarán 5 días a la semana; a lo largo del año la empresa no se tomará vacaciones para cierre temporal de la planta; y durante el año se cuentan con 16 días feriados.
Como se mencionó en la Definición Técnica del Producto, se trabajará unificando todas las ramas de productos en una sola que son los parabrisas. Por ende, se unificarán las cantidades de los distintos planes de ventas identificados, llegando a una venta anual de 74.600 unidades.
Balance anual de material
En esta sección nos interesa conocer la alimentación necesaria para abastecer a nuestra producción anual en función de los desperdicios seccionales, así como también determinar los valores de desperdicio globales para futuros cálculos.
En función de la información recopilada, se elabora la siguiente tabla de balance:
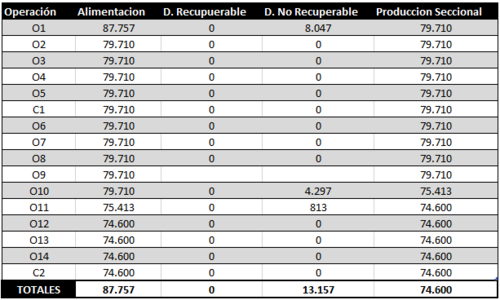
En función de los valores determinados, encontramos que la alimentación y desperdicios en función de la producción son los siguientes:
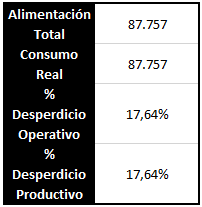
Ritmo de trabajo
Tomando la información antes definida respecto a los días laborales, encontramos que los días laborables al año son: 52 semanas/años x 5 días/semana - 16 días/año = 244 días/año.
Respecto a las horas de trabajo al día, las mismas dependerán del puesto de trabajo y las capacidades de cada uno. La información respecto a este apartado se presentará en la sección de "Capacidad real anual de la máquinaria".
Capacidad real anual de la máquinaria
En este apartado se analizarán las capacidades reales de cada una de las secciones operativas. En la siguiente tabla, se puede ver la conclusión de dicha capacidad, línea por línea, en funcion de las horas trabajadas por puesto, rendimientos operativos y demás datos de interés.
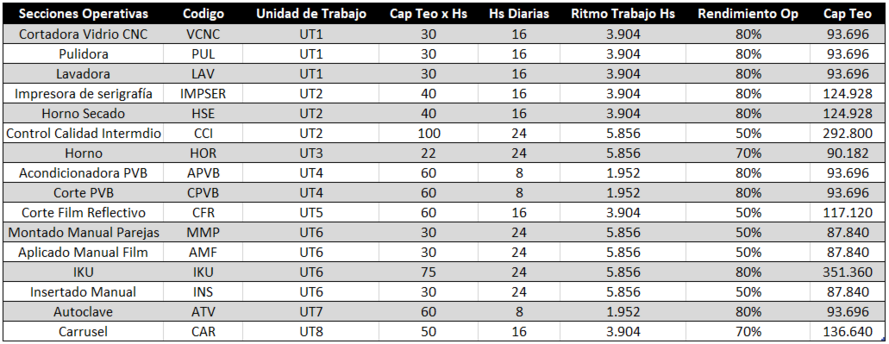
Cantidad de máquinas
En esta sección se combinará la información del "Balance anual de material" junto con la "Capacidad real anual de la máquinaria" para poder definir las necesidades de máquinarias/puestos para cada una de las secciones operativas del proceso productivo.
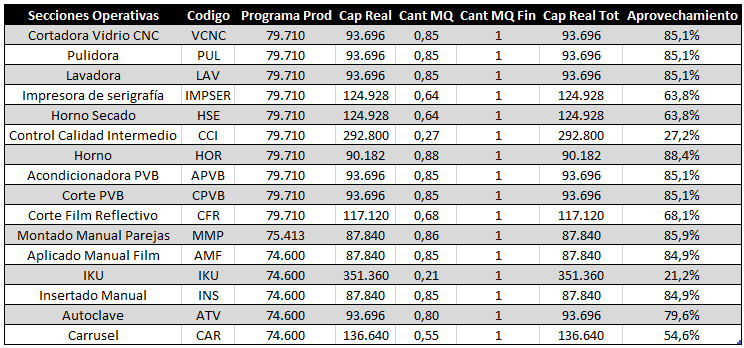
Cuello de botella y capacidad anual real del equipo
En función de lo determinado en la tabla anterior, se denota que el cuello de botella del proceso será la sección operativa de "Horno". Evaluando el trabajo de dicha sección operativa al 100% podemos determinar que la capacidad real del proceso será la siguiente.

Determinación de la evolución de las mercaderías
Evolución de la producción
Como punto de partida, nos interesa conocer los volúmenes de producción que tendremos para el año 1, contemplando el periodo de puesta en marcha, y para el resto de años trabajando a régimen.
Primero debemos contemplar que las producciones mensuales serán de 6.216,67 PT/mes.
El segundo paso es identificar cómo será la producción durante el periodo de puesta en marcha, presentándose la siguiente situación.
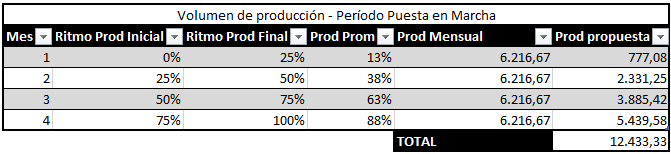
Una vez conocido el dato de producción en PPM, estamos en condiciones de conocer las producciones anuales para cada año, obteniendo asi el siguiente cuadro resumen.
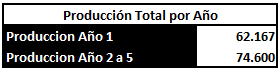
Stock promedio de producto elaborado
Para el stock promedio se trabajará sobre el periodo de régimen, contemplando la información de semanas trabajadas al año e integrando información adicional como los stock de seguridad y el ritmo de entregas semanal.
En lo que respecta a las entregas, se realizarán 2 entregas semanales. Esto es necesario para liberar espacio en la empresa y disminuir el riesgos de inmovilizar los parabrisas, debido a su fragilidad.
Los stock de seguridad se situarán en 0, ya que la demanda del producto depende de requisitos específicos de modelos por parte de los clientes, por lo que no sería razonable contar con un mínimo de mercadería.
En función de todo podemos armar la siguiente tabla resumen con el cálculo del stock promedio.
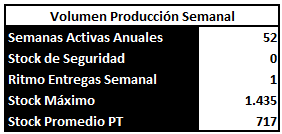
Evolución de las ventas
En esta etapa se buscarán determinar las ventas anuales en cada periodo, pero fundamentalmente en el Año 1, ya que sus ventas se limitarán a las cantidades que se puedan producir durante ese año.
En función de esto se obtiene el siguiente cuadro resumen con los valores de ventas por año.
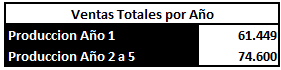
Consumos de materias primas anuales
Antes de iniciar el analisis, se debe contemplar un conjunto de datos de relevancia para el proceso. Los mismos se presentan a continuación.
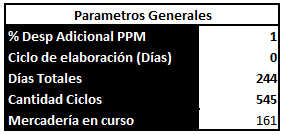
Es importante destacar que el ciclo de elaboración está calculado para un lote de 60 Parabrisas.
En lo que respecta a las materias primas consumidas, estas dependerán de la cantidad de desperdicios generados en el periodo. A raíz de esto debemos dividir este análisis en las siguientes dos partes.
- Año 1: Este periodo está afectado por el PPM, en donde los desperdicios se generan de forma distinta a la instancia de régimen. Puntualmente se da que el desperdicio es el doble del generado en el periodo normal. En función de este dato, podemos obtener la siguiente tabla resumen con los consumos de materias primas anuales.
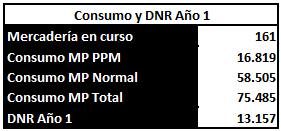
- Año 2 a 5: Estos periodos no están afectados por un PPM, por ende los valores serán los mismos para todos y se presentan en el siguiente cuadro resumen.
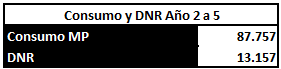
Programa de compras y stock promedio materia prima
En este apartado se presentará como será el programa de compras partiendo desde el Año 1 hasta llegar a los Años 2 a 5.
Los puntos a destacar antes de presentar el avance mes a mes son los siguientes.
- Inicialmente se hará una compra en el Año 0 para satisfacer las necesidades de todo el PPM. Esto con el fin de disponer de la totalidad de recursos y agilizar asi el periodo de pruebas.
- Las compras se realizarán cada 2 semanas.
- En la última semana del PPM se ejecturá una compra por la totalidad de insumos para las próximas dos semanas, sumando tambien una compra por todas las materias menos criticas (Todas menos el vidrio Float) para los siguientes 5 meses y 2 semanas. Esto se hace con el fin de aprovechar las largas fechas de vencimiento de los productos y que los mismos ocupan muy poco espacio, para así agilizar la disponibilidad de todos esos materiales. A la vez, permite que la compras se concentren exclusivamente en disponer del Vidrio Float, siendo este el recurso mas crítico del producto.
En función de lo mencionado, se presenta la siguiente evolución de las compras.
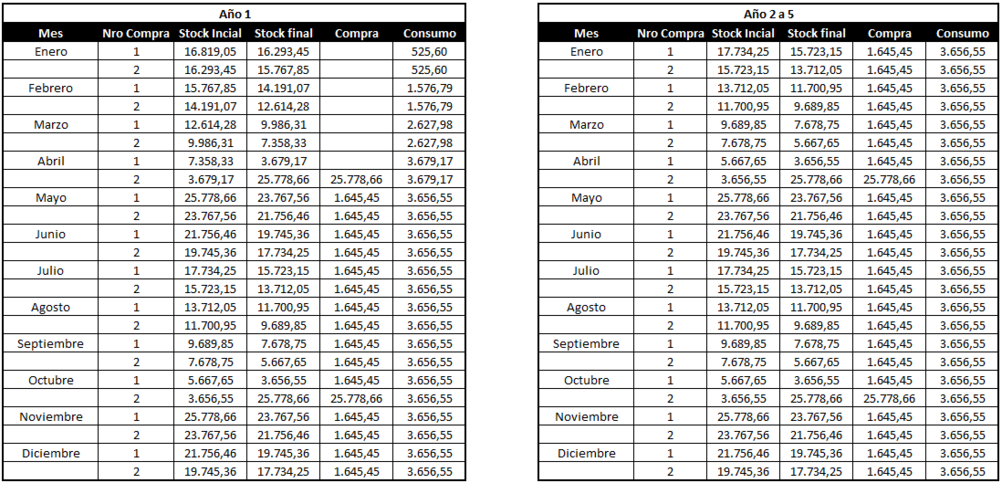
En función del avance mostrado se puede determinar que el Stock Promedio de Materias Primas es de 14.717,6 Und.
Cuadro resumen del programa general
A continuación se presentará el cuadro que condensa toda la información calculada a lo largo de las secciones anteriores.
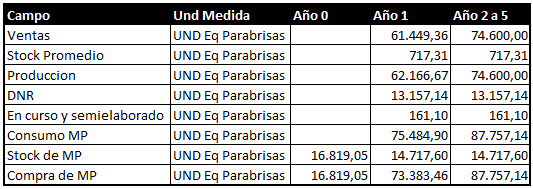
Determinación del Personal
Organigrama de la empresa
Se considerarán tres grandes áreas entre las cuales se dividirán las tareas y actividades que se llevarán a cabo.
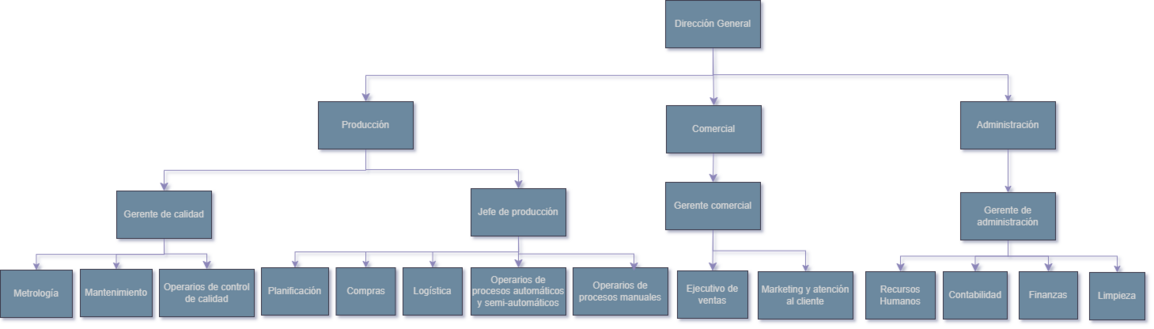
Descripción de los puestos de trabajo. Calificación y formación necesaria de los operadores.
Producción
A lo largo de la Descripción del Proceso Productivo, se detalló la necesidad de 35 operarios teniendo en cuenta los turnos que trabaja cada máquina. Se requiere que sean mayores de 18 años, con secundario completo, indiferentemente de su género.
Operarios
Todos los operarios deberán contar con título secundario completo, preferiblemente con orientación técnica.
- Operarios de procesos automáticos y semi-automáticos
- 1 operario de máquinas, con conocimientos de preparación y control de máquina CNC, pulidora y máquina de limpieza, que cuente con permiso para operar autoelevador.
- 1 operario de serigrafiado, con conocimientos de preparación y control de impresora de serigrafía, horno y chiller; y de manipuleo de sustancias químicas (pintura).
- 3 operarios encargados del proceso de curvatura del vidrio, con conocimientos de medición de curvatura, capacidad de trabajar en equipo y en ambientes de calor.
- 1 operario de preparación del PVB, con conocimientos básicos máquina, capacidad de organización para gestionar los rollos y que preste atención al detalle.
- 2 operarios encargados de la unión de las parejas de vidrio, con capacidad y coordinación para el trabajo en equipo, habilidad para la manipulación del vidrio y del PVB.
- 1 operario encargado del autoclave, con conocimientos básicos de su operación y capacidad de manejar el tractor de arrastre.
- Operarios de procesos manuales
- 1 operario de corte, encargado de los films reflectivos, que cuente con habilidad manual y precisión, capacidad para trabajar con materiales frágiles.
- 2 operarios de aplicación de film, que tengan habilidad manual y precisión, coordinación para trabajar en equipo.
- 1 operario encargado de la colocación de bracket, con atención al detalle y con capacidad de identificar defectos visuales.
- 2 operarios para el control final del parabrisa, con habilidad para manipular los vidrios, capacidad física para levantar y mover los parabrisas.
- Operarios de control de calidad: requerirán habilidad, precisión y coordinación para manipular los insumos frágiles involucrados.
- 2 operarios encargados con buena visión, que presten atención al detalle para identificar no conformidades y defectos, con conocimientos sobre las normativas a cumplir. Será un requerimiento saber utilizar herramientas de medición y rapidez para actuar sobre no conformidades. Uno de ellos se encargará del control visual de serigrafía y vidrio; mientras que el otro se encargará del control de calidad del producto final
- Operarios de depósito: incluye la recepción y transporte en planta de insumos, semielaborados y la preparación y manipulación de producto terminado.
- 1 operarios encargados de recepcionar y controlar la entrega de materiales contra remito, y su posterior registro en sistema. Conocimientos previos en logística o experiencia en depósitos. Conocimiento previo en manejo de zorras.
- 1 clarkista encargado de posicionar la mercadería en los racks correspondientes y transportarla cuando sea necesario. Debe contar con carnet habilitante para el manejo de autoelevadores.
- 2 operarios encargados de la preparación y despacho de pedidos. Conocimientos previos en logística o experiencia en depósitos. Conocimiento previo en manejo de zorras.
Jefe de producción: Elabora los planes de producción según la demanda y la capacidad instalada. Coordina turnos y recursos humanos para asegurar el cumplimiento del plan. Controla el correcto funcionamiento de las líneas, y asegura el cumplimiento de los estándares de calidad. Monitorea KPIs de productividad, eficiencia, rendimiento, calidad. Elabora informes periódicos para presentar ante la dirección general, con propuestas de mejora. Actúa como nexo entre el área de procesos, producción, calidad y logística.
Deberá ser Ingeniero Industrial, con conocimientos sobre gestión de producción, normas de calidad automotriz, seguridad e higiene, y con capacidad de liderazgo y gestión de personal.
Gerente de calidad: coordina a los operarios de control de calidad. Asegura el cumplimiento y correcta ejecución del plan de control de calidad detallado anteriormente, desde la recepción de los materiales hasta el control en los puestos de trabajo. Asegura que el producto terminado cumpla con todas las especificaciones y normas establecidas, ya sea por regulación nacional como por requisito particular de los clientes. Organiza y lidera auditorías internas.
Deberá ser Ingeniero Industrial, Químico, Mecánico o afín; con conocimientos de gestión de calidad en la industria, capacidad de análisis crítico de procesos y productos, habilidades de comunicación.
Responsable de metrología: supervisa y ejecuta mediciones a lo largo del proceso productivo, para lograr que los productos cumplan con las especificaciones técnicas.
Deberá ser Técnico en Metrología o Ingeniero Mecánico o Industrial con orientación en metrología, con atención al detalle, precisión y organización para gestionar calibraciones y registros.
Responsable de mantenimiento: ejecutar rutinas de mantenimiento preventivo en los equipos, realizar chequeos periódicos. Diagnosticar y reparar fallas mecánicas, eléctricas o electrónicas en la línea. Minimizar tiempos de parada y arranque. Instalación y puesta en marcha de nuevos equipos.
Deberá ser Técnico Electromecánico, Mecánico o Electrónico, o Ingeniero Mecánico o Electromecánico, capaz de resolver rápidamente los problemas técnicos.
Responsable de logística: gestión de almacenes e inventarios de materias primas, semielaborados y producto terminado. Coordinación de entregas a clientes. Coordinación de recepción de insumos con el área de compras. Gestionar remitos y documentación aduanera en el caso que se requiera.
Deberá contar con una Licenciatura en Administración de Empresas, Ingeniería Industrial o Logística. Conocimiento y manejo de sistemas WMS, transporte, gestión de inventarios. Habilidades de organización, coordinación y orientación a la eficiencia.
Responsable de compras: gestiona la compra de materias primas, negociación con proveedores de condiciones de entrega (plazos de pago, mínimos de compra). Evaluación de proveedores, búsqueda de proveedores alternativos.
Deberá contar con una Licenciatura en Administración de Empresas, Comercio Internacional o Logística, con habilidades de negociación, organización y conocimientos sobre sistemas de gestión de compras.
Responsable de planificación: elaboración de planes de producción en función del plan de ventas, dar seguimiento al cumplimiento del plan. Dar visibilidad a comercial sobre el estado de los pedidos, capacidad de abastecimiento de las órdenes de compra.
Deberá ser Ingeniero Industrial, o contar con estudios relacionados con Logística o Administración, con conocimientos en gestión de inventarios y demanda, habilidad para la organización y coordinación de tareas, gestión de la capacidad instalada y cuellos de botella.
Comercial
Gerente comercial: reporta a la dirección general. Supervisa al equipo de ejecutivos de ventas, marketing y atención al cliente. Trabaja en conjunto con producción y logística para garantizar el cumplimiento de entregas y CSL. Define y ejecuta el plan de ventas. Desarrollo de relaciones comerciales. Realiza estudios de mercado, benchmarking de la competencia y análisis de tendencias.
Deberá contar con una Licenciatura en Administración de Empresas, Marketing o similar, con conocimientos en estrategia de ventas B2B, negociación, con capacidad de liderazgo comercial.
Ejecutivo de ventas: serán 3 colaboradores responsables de tomar contacto directo con el cliente, presentar el portfolio de productos y asesorar al cliente en base a sus requerimientos. Negociación y cierre de órdenes de compra. Atención postventa y seguimiento de consultas.
Deberán contar con una Licenciatura en Administración de Empresas, Marketing o similar, con conocimientos en estrategia de ventas B2B, negociación, capacidad de atención al cliente, resolución de conflictos.
Responsable de marketing y atención al cliente: diseño de materiales promocionales, coordinación de presencias en ferias, charlas y convenciones. Recolectar y analizar información sobre competidores, tendencias, comportamiento del cliente. Gestión de reclamos. Encuestas de satisfacción.
Deberá contar con una Licenciatura en Marketing, Comunicación, Publicidad o similares, con conocimientos de análisis de datos del mercado, creatividad, habilidades de comunicación.
Administración
Gerente de administración: reporta a la dirección general. Supervisa al equipo de finanzas, contabilidad, limpieza y recursos humanos, para asegurar una correcta gestión financiera y contable. Coordina los procesos administrativos y optimiza recursos.
Deberá contar con una Licenciatura en Administración de Empresas, Contador Público o similar, capaz de gestionar el recurso humano y gestionar tesorería y flujo de caja.
Responsable de finanzas: gestiona el flujo de fondos de la empresa, planifica tesorería, evaluar necesidad de financiamiento y relación con bancos.
Deberá contar con una Licenciatura en Administración de Empresas, Economía o Contabilidad, con conocimientos de gestión de tesorería corporativa, gestión financiera, capacidad de negociación, y atención a detalles.
Responsable de contabilidad: registro de operaciones contables, confección de balances y conciliaciones bancarias. Liquidación de impuestos.
Deberá contar con una Licenciatura en Contabilidad, capacidad de organización para cumplir plazos fiscales, precisión numérica y conocimiento de la normativa.
Responsable de recursos humanos: gestión del proceso de selección y capacitación del personal, administrar licencias, ART, coordinación de la liquidación de sueldos y beneficios con contabilidad. Asegurar cumplimiento de la ley laboral.
Deberá contar con una Licenciatura en RRHH, Relaciones Laborales o Administración, empatía, con conocimientos de liquidación de sueldos y beneficios, negociación y comunicación
Responsable de limpieza: encargados de realizar las tareas de limpieza en áreas comunes, oficinas y zonas de producción. Debido al tipo de proceso productivo, se requerirán 2 responsables para el turno mañana/tarde, mientras que se necesitará 1 responsable para el turno noche.
Deberá contar con capacidad física para realizar sus tareas de limpieza.
Listado de Equipos Auxiliares, Muebles y Útiles
Área | Equipos auxiliares, muebles y útiles | Cantidad |
---|---|---|
Área de producción | Mesadas de trabajo de acero inoxidable | 5 |
Racks metálicos para el almacenamiento de insumos y producto terminado | 50 | |
Armarios | 4 | |
Sillas | 17 | |
Contenedores plásticos y bandejas para la manipulación segura de vidrio y PVB | 10 | |
Tractor de arrastre | 3 | |
Clarks | 2 | |
Carros de transporte | 5 | |
Instrumental de medición | 3 | |
Instrumental para control visual (lupas, lámparas) | 3 | |
Kit de equipo de protección personal | 45 | |
Equipo ensayo bola libre (Metrología) | 1 | |
Pantalla Serigrafía | 60 | |
Matrices hornos | 240 | |
Pallet metálico | 68 | |
Flecha de curvatura | 3 | |
Calibre | 2 | |
Tachos de descarte | 3 | |
Área administrativa | Escritorios | 14 |
Sillas | 14 | |
Archiveros | 2 | |
Estanterías | 2 | |
Armarios | 2 | |
Computadoras | 14 | |
Teléfonos | 14 | |
Impresoras | 3 | |
Monitores | 14 | |
Router | 3 | |
Aire acondicionado | 2 | |
Insumos de oficina: hojas, carpetas, lapiceras. | 14 | |
Dispenser de agua | 2 | |
Kit de cafetería | 2 |
Anteproyecto de Planta
Plano de planta
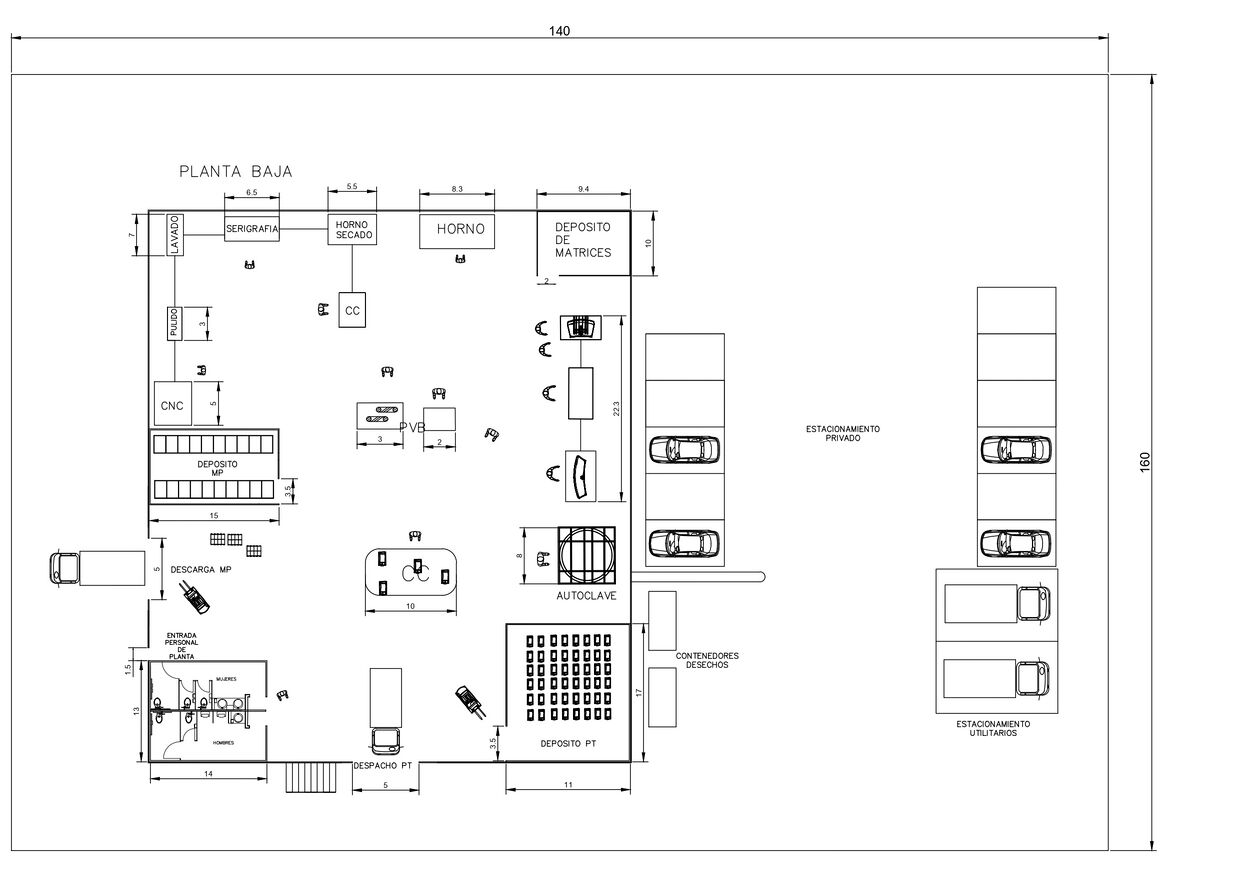
Primer piso
Aclaración: Las medidas se encuentran en metros tanto para la planta baja como el primer piso.
Recorrido de materiales
- Las flechas de color rojo indican el recorrido desde la descarga de la materia prima, su traslado al depósito correspondiente, y desde allí hasta las operaciones 1 a 5, incluyendo el primer control de calidad. Luego, continúa hasta la operación 6.
- Las flechas de color verde representan las operaciones 7, 8 y 9, las cuales se realizan en paralelo.
- Las flechas de color celeste señalan el flujo desde la operación 10 hasta la 14, pasando por el segundo control de calidad, el traslado al depósito de producto terminado, y finalmente, el despacho.
Cronograma de ejecución
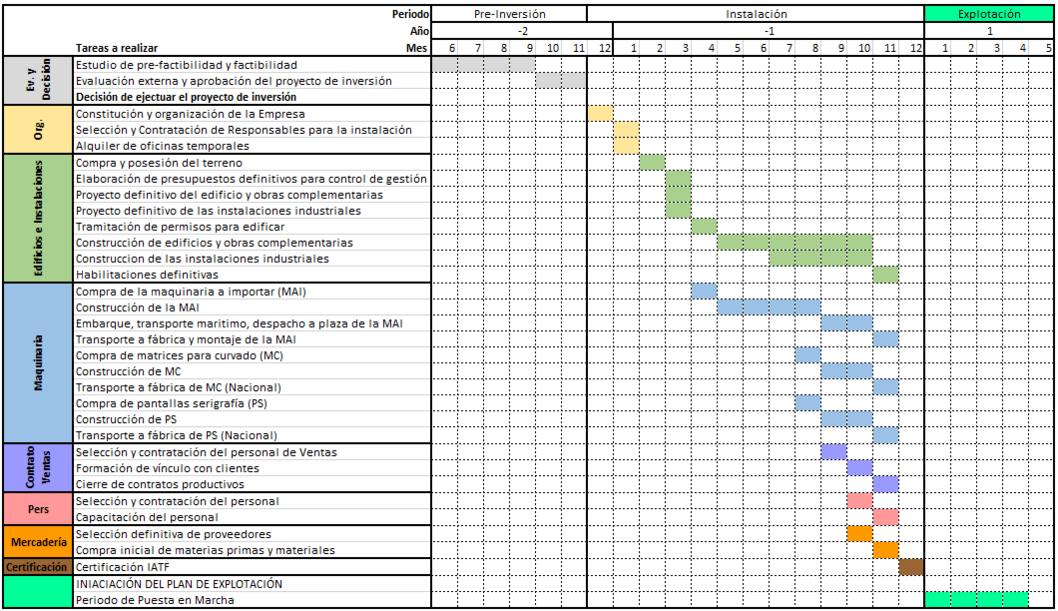
- ↑ https://servicios.infoleg.gob.ar/infolegInternet/anexos/30000-34999/30389/dto779-1995-anexoF.htm
- ↑ https://www.linkedin.com/in/moreno-magon-b0890239/recent-activity/all/
- ↑ https://evaluaciondeproyectos.com.ar/wiki/images/thumb/2/25/Pulidora_Lijiang.png/300px-Pulidora_Lijiang.png
- ↑ https://evaluaciondeproyectos.com.ar/wiki/images/thumb/6/6c/Lavadora_Benteler.png/300px-Lavadora_Benteler.png
- ↑ https://www.benteler-glass.com/en/products/washing-machines/#accordion-934-item-6
- ↑ https://www.ljglassmachinery.com/automatic-glass-processing-machine/automatic-laminated-glass-autoclave-equipment