Diferencia entre revisiones de «Dimensionamiento Técnico ó Fisico»
(No se muestran 3 ediciones intermedias del mismo usuario) | |||
Línea 1: | Línea 1: | ||
== Introducción y Objetivos == | == Introducción y Objetivos == | ||
El dimensionamiento técnico ó físico es probablemente el núcleo de todo proyecto y por eso es el que requiere el mayor nivel de trabajo. Debido a esta cantidad y complejidad del trabajo necesario es que la mayoría de las veces el dimensionamiento técnico es subanalizado. Aquí se dan dos posibles alternativas del porque de este subanálisis: | |||
* '''''Demasiada Importancia al dimensionamiento Comercial y Económico:''''' La mayoría de los cursos dados sobre evaluación de proyectos se concentran en poder calcular el potencial de ventas y los resultados esperados económicos para poder determinar un flujo de caja . Esto es generalmente llamado plan de negocios ó business plan. Esto se enseña en la infinidad de cursos de apoyo a emprendedores, en todos los masters en negocios de todas las escuelas y en las carreras de administración de empresas. Y es entendible. Es muy lindo ver cuanto se puede vender, que formidable que nos compren lo que se nos ocurrió, como nos diferenciaremos en un mercado específico y como eso nos generará gran cantidad de dinero. Luego hacen unas cuantas cuentas sobre estimación de inversiones y costos y ¡voila! ya tenemos un negocio armado. Y si ponemos el doble de dinero la ganancia se duplica! Pero lo que no ven en estos casos es que las diferenciaciones comerciales son fáciles de duplicar, fíjense sino en la etapa inicial de Internet, donde una buena idea era inmediatamente replicada múltiples veces en cuestión de días, o cuando uno pone un local exitoso, en unos meses alguien puede poner un negocio similar a solo unos metros de distancia. Lo otro que falla en ver esta perspectiva es que la cuantificación económica de un proyecto puede solo surgir de haber analizado los recursos físicos necesarios. Los costos indirectos no siempre son fijos, las inversiones en stocks no se mantienen constantes con distintos volúmenes de ventas, no se puede multiplicar alegremente las ventas si las máquinas e instalaciones no dan abasto. Por eso una elaboración económica que no se encuentra basada en un sólido análisis técnico tiene tantas posibilidades de triunfar como una estimación dada por un oráculo. | |||
* '''''Demasiada Confianza en la capacidad técnica del dueño del proyecto:''''' Muchas veces quien encara un proyecto es alguien que comprende la parte técnica del proyecto, es un mecánico, un cocinero, un ingeniero, ó trabajo toda su vida en una empresa textil, un criadero de animales o sabe programar desde los 12 años. Entonces es comprensible y hasta razonable que esta persona sienta que no necesita realizar un dimensionamiento técnico. Y de hecho sus estimaciones suelen ser completamente válidas para calcular las necesidades de instalaciones, insumos y máquinas del proyecto. En verdad el trabajo en el dimensionamiento técnico puede ser duro y llevar tiempo pero la solución no es dejarlo de lado, sino eventualmente simplificarlo, sabiendo que se han tomado estimaciones, pero con una estructura adecuada que permita posteriormente mejorar y profundizar el análisis para obtener resultados más exactos, tanto para pedir préstamos a los bancos como para permitir que otras personas participen y entiendan la totalidad del proyecto. Es por esta razón que al final de la elaboración de las actividades necesarias para cumplir cada objetivo, se mostrará la manera de simplificarlas para poder realizarlas rápidamente, pero de manera adecuada. | |||
El trabajo a realizar en el dimensionamiento técnico incluye un amplio espectro de aspectos por lo que los conocimientos y técnicas necesarias son igualmente amplias y variadas. El orden en el que se van desarrollando los distintos elementos de esta etapa, tiene una lógica de cascada donde es necesario cumplir uno para poder ir avanzando en los restantes. Dichos elementos son: | |||
* Determinación del Tamaño y la Localización | |||
* Determinación Técnica del producto | |||
* Determinación de los procesos | |||
* Determinación de las Mercaderías | |||
* Determinación de la Organización y el Personal | |||
* Elaboración del Anteproyecto de Planta | |||
* Generación del Cronograma de Ejecución | |||
Para mostrar la integración entre todas las actividades realizadas para lograr alcanzar los objetivos del dimensionamiento técnico se muestra el siguiente diagrama. Si bien es complejo, es la mejor manera de ver de manera integrada dichas actividades y entender el porque de la vinculación entre los distintos objetivos. | |||
[[Archivo:Dimfisico.jpg|centro|DIMENSIONAMIENTO FISICO- Esquema de Elaboración|alt=|marco]] | |||
Como todos los dimensionamiento, existen luego de la etapa de Elaboración, las etapas de Formulación y Evaluación, donde presentan de manera resumida lo encontrado y se da lugar para que el inversor tome decisiones de evaluarlo. | |||
== Elaboración == | == Elaboración == | ||
Línea 280: | Línea 294: | ||
Para ver más información acerca del [[proceso de Diseño de Producto]], ver el anexo | Para ver más información acerca del [[proceso de Diseño de Producto]], ver el anexo | ||
=== Determinación de los Procesos === | === Determinación y Diseño del Proceso de Elaboración y Control === | ||
Una vez determinado el producto que se quiere fabricar, es necesario empezar a determinar los procesos necesarios para poder llevarlo a cabo. | |||
Muchas veces el producto y el proceso se van desarrollando de manera paralela, ya que el diseño o materiales a usar en los productos depende de las tecnologías a utilizar. | |||
La fuente de información de las tecnologías disponibles puede provenir del análisis comercial, cuando se hizo el análisis de proveedores, o de la consulta de los expertos ó del tecnólogo. | |||
Existe una extensa diversidad de procesos que abarcan desde las industrias más conocidas como las industrias metalmecánicas, hasta las industrias electrónicas más avanzadas donde parte del proyecto implica de hecho desarrollar tecnologías nuevas y específicas. | |||
Desarrollar todos los procesos posibles escapa en este momento a los alcances de este libro, si bien en anexos se irán desarrollando el tema específico para cada tipo de industrias. | |||
==== Diagramas Iniciales del Proceso ==== | |||
Para el diseño y modelamiento del Proceso generalmente se inicia con el armado de Diagramas Iniciales de Proceso de Fabricación y Control. Para esto generalmente se utilizan diagramas de flujo. Los diagramas de flujos son representaciones gráficas que permiten esquematizar de manera simple procesos productivos y flujos de trabajo paso a paso. | |||
Si bien existen diversos tipos de simbologías para representarlos, las más comunes para procesos industriales abarcan los siguientes gráficos: | |||
[[Archivo:SimbologiaTecnica.jpg|centro|marco|DIAGRAMAS de PROCESOS- Simbología Técnica]] | |||
Otro ejemplo común de diagramas de flujos son los utilizados para procesos que incluyen el manejo de información: | |||
[[Archivo:SimbologiaSistemas.jpg|centro|marco|DIAGRAMAS DE PROCESOS- Simbología para Información]] | |||
Cualquiera que se use, se deberá usar siempre un mismo criterio, o llegado el caso indicar la simbología utilizada al pie del gráfico. | |||
==== Diseño del Proceso ==== | |||
A continuación vamos a describir conceptualmente las distintas alternativas para cada una de secciones operativas, que si bien en muchos casos es posible elegir distintos tipos de procesos para una misma sección, muchas veces esto no es conveniente ya que se producen variaciones en la calidad de los productos salidos de una misma sección operativa. | |||
Desde el punto de vista de la intervención de la mano de obra, los procesos se catalogan en: | |||
* '''Procesos Manuales''': Son aquellos donde el ritmo de trabajo depende exclusivamente de la persona que lo realiza. Puede estar acompañado del uso de herramental simple que ayuda a la persona a realizar su tarea. Ejemplos típicos de esto son los procesos ensamble, la construcción tradicional, la costura en los talleres textiles, etc. Se caracterizan por su baja necesidad de inversión y de instalaciones, por ser fácilmente escalables y por la gran variabilidad en los tiempos. También al contarse con el trabajo de personas, esto puede provocar paradas ó retrasos por cuestiones personales, falta de personal, y en algún caso riesgos vinculados a los accidentes y la salud de dicho personal. | |||
* '''Procesos Automáticos:''' son aquellos donde el ritmo de trabajo depende exclusivamente de las máquinas operativas, y no hay intervención de las personas excepto casos excepcionales (paradas, arranques o carga de materiales). Ejemplos típicos de esto son los hornos continuos, las cabinas automáticas de pintura ó los telares mecánicos. En estos casos la inversión tanto en las máquinas operativas como en las instalaciones suele ser alta, las capacidades de producción por unidad productiva también son altas, son difíciles de escalar ya que su instalación es compleja y requiere espacio. Mientras que las paradas ó retrasos son inusuales, cuando estos se producen generalmente son debido a roturas y por lo tanto muy adversos tanto desde el punto del costo como desde el punto de vista de pérdida de tiempo. | |||
* '''Procesos Semiautomáticos:''' son aquellos donde el ritmo de trabajo es compartido tanto por las personas como por las máquinas operativas. Esto provoca que tengan las ventajas y desventajas de los dos esquemas anteriores. Por lo que la inversión no es tan alta pero si es significativa, las capacidades productivas son algo intermedio entre ambas, pueden producirse paradas o falta de actividad tanto por problemas de las máquinas como por problemas ó accidentes del personal. | |||
Generalmente para un proceso dado en una industria dada, cuando se requieren bajos niveles de producción se opta por procesos manuales, luego se opta por procesos semiautomáticos y finalmente por los automáticos. | |||
Desde el punto de vista de su naturaleza, podemos catalogar los procesos en: | |||
* '''Procesos de Transformación:''' Son todos aquellos procesos donde la materia prima, mercadería en curso ó materiales que entran al mismo son distintos a los productos elaborados ó semielaborados que salen del mismo. Estas transformaciones pueden ser mecánica, procesos tales como el torneado ó fresado, puede ser transformaciones químicas como la fermentación, pueden ser un simple cambio de estado en procesos como el evaporado ó a veces el proceso de transformación son simples mezclas ó ensamblados donde la naturaleza de de las materias primas no cambia, solo su disposición es la adecuada. | |||
Los procesos de transformación son el núcleo indispensable de todo proceso productivo. | |||
Dentro de los procesos de Transformación, existen procesos especiales que son imposibles de controlar sin eliminar una característica indispensable del producto. En este caso, en lugar de controlarse dicha característica, lo que es necesario hacer es validar el proceso. Un caso típico de un proceso especial es la esterilización, ya que si uno abre el producto estéril para verificar su esterilización, el producto en sí ya deja de estar estéril. | |||
* '''Procesos de Control:''' los procesos de control son todos los procesos donde a través de la comparación del producto semielaborado ó elaborado con un standard, se decide si dicho producto está apto para pasar al siguiente proceso ó para ser liberado como producto terminado al mercado. Si bien en si los procesos de control no aportan valor intrinsecamente, ya que un producto es apto o no independientemente de haber pasado por un control, estos procesos me sirven para segregar los productos que no estén aptos y evitar potenciales problemas. | |||
Muchas veces los procesos de control surgen del último análisis del proyecto, el análisis de riesgo, ya que en este punto se identifican los posibles peligros y riesgos que puedan haber, y por lo tanto se decide implementar controles para evitarlos. | |||
En otros casos, los procesos de transformación y control se hayan combinados, este es el caso de las inspecciones visuales ó controles durante el ensamblado. | |||
* '''Procesos de Transporte:''' Los procesos de transporte cambian la ubicación ú orientación de las materias primas y productos semielaborados ó elaborados. Esto permite que dichas materias primas ó productos se encuentren disponibles para el siguiente proceso de una manera adecuada en cuanto a su disponibilidad en el lugar y momento. | |||
Los procesos de transporte pueden estar integrados a otros procesos, este es el caso de cintas trasportadoras en una línea de montaje ó los tornillos sin fin, ó pueden ser independientes como es el caso de zorras, carretillas ó apiladores. También pueden ser aprovechados para realizar tareas como son el enfriado de productos ó el secado de pegamento. | |||
* '''Procesos de Almacenaje:''' Los procesos de almacenaje surgen como necesidad para equilibrar los distintos procesos y permite garantizar el suministro continuo y oportuno de los materiales y medios de producción requeridos para asegurar la producción de forma ininterrumpida | |||
El almacenaje puede ser tanto para equilibrar los flujos con el entorno, tal es el caso de los almacenes de materias primas y productos terminados, como el flujo interno, tal es el caso de los stocks de mercadería en curso. | |||
Estos también pueden ser aprovechados para realizar tareas como son el enfriado de productos ó el secado de pegamento. | |||
Si bien son prácticamente indispensable en todos los procesos, cabe destacar que el sobredimensionamiento de estos procesos provocará en el proyecto un aumento de la inversión en activo de trabajo, por lo cual serán contraproducentes desde el punto de vista de la rentabilidad del proyecto. | |||
Desde el punto de vista de su evolución en el tiempo los procesos se clasifican en: | |||
* '''Proceso Continuo:''' Es aquel en el que la operación no se detiene. Las diversas partes de la estructura de un proceso en general siempre está recibiendo una alimentación continua y de igual manera están lanzando un producto en forma continua. Esto permite mantener un ritmo de producción constante, y suele ser económicamente más conveniente, ya que los arranques o los paros pueden ser más costosos que en una operación contínua. | |||
* '''Procesos discretos:''' también conocidos como batch o lotes son en los que si existen paradas del proceso entre lote y lote. Son más comunes en empresas pequeñas ya que suelen requerir menos inversión que los procesos continuos. Algunos procesos dada su naturaleza son necesariamente discontinuos, como la filtración, ya que después de determinados periodo de operación es necesario limpiar los filtros. | |||
Es común que cuando se combinan líneas donde hay procesos continuos y discontinuos, es común utilizar dos o más equipos de proceso discontinuo con la finalidad de poder estar alimentado un proceso continuo posterior. | |||
Para elegir cada uno de estos procesos es necesario tener en cuenta la secuencia de estos, la posibilidad de integrar procesos en una sola sección operativa, permitir un flujo equilibrado a lo largo de todo el proceso, evitar errores de mezclado e interrupciones en la producción. Si bien la mayor parte de las veces esto puede ser realizado sin problemas, muchas veces la experiencia de un tecnólogo que conozca el proceso ayuda a evitar problemas y errores comunes. | |||
Una vez identificado el proceso que se desea modelar, hay que: | |||
* Identificar y definir las etapas del proceso que se deben realizar en un orden específico. | |||
* Determinar en un orden específico las operaciones que conforman cada etapa. | |||
* Establecer las acciones que se deben desarrollar para completar cada operación. | |||
A continuación se muestra un ejemplo: | |||
[[Archivo:TablaProceso.jpg|centro|marco|PROCESOS- Separación en Etapas, Operaciones y Acciones]] | |||
Una vez definidos las Procesos, etapas, Operaciones y acciones, se debe definir el tipo de planta que se desea montar ó desarrollar. | |||
===== Tipos de Plantas ===== | |||
'''Plantas Monoproducto''' | |||
[[Archivo:PlantaMonoproducto.jpg|centro|marco|PLANTA MONOPRODUCTO- Esquema tipico]] | |||
Se agrupan las etapas/operaciones/acciones consecutivas que puedan realizarse de manera conjunta en una sección operativa que se numera ó nombra para poder identificarla, de cada sección operativa saldrá un semielaborado que también habrá que numerar ó nombrar para poder identificarlo unívocamente, excepto de la última sección operativa por la que saldrá el producto terminado. Para cada sección operativa, habrá que identificar por cada unidad de salida la cantidad necesaria de materias primas, materiales, desperdicios recuperables, desperdicios no recuperables. | |||
'''Plantas Multiproducto''' | |||
[[Archivo:PlantaMultiproducto.jpg|centro|marco|PLANTA MULTIPROPOSITO- Esquema]] | |||
Para el caso de las plantas multiproducto, donde todos los productos siguen la misma secuencia a través de todas las etapas de producción, el proceso de armado de la línea es similar, solo que se hace este proceso independiente para cada producto, para luego eventualmente si se desea hacer un balance de materiales total, simplemente hay que sumar los requerimientos para cada uno de los productos. Esto puede ser conveniente para mostrar el resultado total, pero más adelante con el objetivo de balancear la línea, será necesario contar con todos los flujos por separado para poder realizar los cálculos. | |||
'''Plantas Multipropósitos''' | |||
[[Archivo:PlantaMultiproposito.jpg|centro|marco|PLANTA MULTIPROPÓSITOS- Esquema]] | |||
Como puede verse, las plantas multipropósitos le agregan un grado adicional de complejidad, ya que los procesos para los mismos productos no siguen la misma secuencia. Nuevamente la técnica es la misma que para la planta multiproductos, son que en este caso, además de adicionar los requerimientos de cada producto, también es necesario adicionar los requerimientos para cada sección operativa. | |||
===== Diseño de Procesos Complejos ===== | |||
Cuando los procesos son lineales y continuos, los procesos son fáciles de diseñar, pero cuando se empiezan a incluir etapas discontinuas ó variaciones en el proceso realizado a cada producto, el diseño del proceso puede volverse desafiante. | |||
En estos casos, se recomienda seguir la siguiente técnica: | |||
# Diseñar el Proceso como si fuese Continuo | |||
# Identificación de Equipos Discontinuos: Los equipos discontinuos ó proceso batch producen cortes en las líneas continuas. Para evitar esto, suelen utilizarse dos ó más equipos discontinuos en paralelo para lograr evitar interrupciones, disminuye las necesidades de almacenamiento intermedios. | |||
# Identificación de Equipos Multitarea: Utilizar equipos multitareas permite aprovechar las capacidades ociosas, hacer un uso eficiente de recursos y generar una producción flexible y Optimizada. Sin embargo, los equipos ó secciones operativas multitareas suelen ser una pesadilla desde el punto de vista de la programación de la producción una vez puesta en marcha la empresa. Si el proceso es continuo, los requerimientos se tratan como se explicó anteriormente en lo que hace a plantas multipropósitos, si el trabajo es por lote es necesario tener en cuenta que los lotes de los diversos flujos, no necesariamente son iguales, por lo cual el equipo multitarea se deberá dimensionar para el lote de mayor tamaño. | |||
# Determinar la necesidad de Etapas Paralelas: Las etapas paralelas pueden surgir o por la necesidad de realizar distintos tratamientos a distintos productos ó por la necesidad de balancear equipos discontinuos con equipos continuos. | |||
También se usan etapas paralelas para optimizar el uso de ciertas secciones operativas de larga duración y minimizar los tiempos ociosos de los equipos. | |||
[[Archivo:Etapasolapadas.jpg|centro|marco|DISEÑO DE PROCESOS- Alternativas de configuración de Operaciones]] | |||
Como puede observarse de los gráficos anteriores, la optimización de la programación superponiendo actividades, lleva a un aumento en la capacidad de aproximadamente del 50%, y al utilizar etapas paralelas lleva a un aumento en la capacidad de más del 150% con respecto a la primera alternativa casi un 80% sobre la segunda alternativa, haciendo una inversión solamente en una de las secciones operativas. | |||
Esto también aumenta el aprovechamiento seccional en la primera y tercera sección del 21% al 43%. Y si se agregara una tercera etapa paralela en la segunda sección, los aprovechamientos seccionales subirían aún más. | |||
5. Cuantificar el Almacenamiento Intermedio: | |||
Los procesos por lotes requieren necesariamente contar con almacenamientos intermedios. | |||
Cuando se consideran almacenamientos intermedios, hay que considerar la naturaleza de los semielaborados, o sea que esto permitan ser almacenados el tiempo necesario, la inversión requerida en los equipos para almacenarlo, la disponibilidad del lugar físico para ese almacenamiento, así como también el valor de la mercadería semielaborada en sí. Si el tipo de semielaborado lo permite y la inversión en el equipo de almacenamiento y lugar físico es bajo, siempre es conveniente hacer uso de almacenamientos intermedios para optimizar el aprovechamiento de las máquinas operativas. | |||
Hay que considerar que si bien el almacenamiento intermedio permite balancear procesos por lotes, evitando la interrupción de los procesos, también puede provocar demoras por lotes fuera de especificación. | |||
==== Especificaciones de Medios de Fabricación y Control ==== | |||
Ya teniendo balanceado el proceso, es necesario determinar los equipos específicos de Fabricación y Control. | |||
Para cada sección operativa, hay que determinar ahora equipos y máquinas específicas, existe una gran cantidad de alternativas de fabricantes de máquinas y describirlos todos es imposible. | |||
Si es importante dar algunos lineamientos para selección las máquinas y equipos. | |||
Para empezar hablamos de una línea Hómogenea cuando las máquinas son del mismo fabricante. Esto generalmente facilita los procesos de balanceo de líneas, disminuyendo los stocks intermedios y facilita los procesos de mantenimiento al referenciarlos a un solo proveedor. | |||
A la hora de seleccionar los medios de fabricación y control, no hay reglas generales para la toma de decisión. | |||
En algunos casos se decide seleccionar equipos donde la capacidad del equipo exceda un poco las necesidades de producción, con lo cual se contará con un solo equipo por sección operativa. Esto se debe a que un solo equipo grande generalmente es más ventajoso desde el punto de vista del retorno de la inversión. Sin embargo, en este punto todavía no se ha desarrollado el dimensionamiento económico, por lo cual esto no se puede verificar. | |||
Cuando los equipos requieren muchas paradas de máquina para cambio de matrices o limpieza por ejemplo, es común elegir equipos con menos capacidad que permitan realizar estas paradas mientras se sigue utilizando otro de los equipos. | |||
Cuando la inversión está restringida, es común elegir procesos manuales para las secciones operativas, ya que los medios de fabricación y control en estos casos son comparativamente más baratos. La desventaja en estos casos (más allá de las explicadas anteriormente) es la variabilidad de la calidad y tiempos entre persona y personas, y para una misma persona a lo largo de la jornada laboral. | |||
No obstante todo esto, lo importante en este punto es elegir una tecnología adecuada para los procesos requeridos, y eventualmente si se tiene dudas de haber elegido la mejor alternativa, esto se suele analizar en el dimensionamiento de la incertidumbre y gestión del riesgo (AGREGAR LINK) | |||
Para cada medio de fabricación y control, será necesario contar con una hoja técnica del mismo, y de ser posible con el manual respectivo. De esa hoja técnica surgirán datos a considerarse en este momento, tal como la compatibilidad con las materias primas y materiales que se van a utilizar, las capacidades teóricas por unidad de tiempo y datos a ser utilizados más adelante en el proyecto, tales como las dimensiones, los consumos de servicios, la frecuencia de mantenimiento. | |||
Hay otras informaciones que generalmente no se encuentran en las hojas técnicas y es necesario preguntar al fabricante o proveedor para poder utilizarlos en el proyecto: | |||
* rendimiento operativo (para poder calcular la capacidad real), | |||
* requisitos especiales para la instalación (por ejemplo de un contrapiso) | |||
* Embalado (para poder organizar su armado), | |||
* Plazos de construcción y entrega (para programarlos en el cronograma de ejecución) | |||
* datos económicos (precio, formas de pagos) | |||
* Condiciones de Guardado | |||
* Frecuencia y costo de Calibrado (medios de Control) | |||
* Conexiones a los servicios (tipo y diámetro de cañerias, tipo de enchufes) | |||
Una vez que se hayan determinado las máquinas especificas, puede ser que sean necesario readecuar los procesos, además de adaptar el proceso al espacio físico disponible más adelante cuando se desarrolle el anteproyecto de Planta. | |||
Un aspecto indispensable a determinar para cada sección operativa es, dado las tecnologías y maquinas seleccionadas, los flujos de ingresos (materias primas, materiales, insumos) y de egresos (productos, subproductos, desperdicios). Esto surge también de la información suministrada ó consultada con el proveedor. Por lo que para cada sección operativa, se tendrá que conseguir esta información, que será utilizada más adelante en el balanceo de Materiales. | |||
[[Archivo:Flujo de Bienes.jpg|centro|marco|FLUJO DE BIENES- Para una sección Operativa]] | |||
==== Representación Final de los procesos ==== | |||
Una vez que se han determinado las secciones operativas y las máquinas, en necesario volver a graficar los procesos. Para esto es común utilizar cursogramas. | |||
Los cursogramas son similares a los diagramas de flujo, pero generalmente siguen normas más estrictas para su construcción, y suelen ofrecer mucha más información que los diagramas de flujo. Existen distintos tipos de Cursogramas, a continuación se muestran ejemplos de los más comunes. Para más información de las construcción de los diversos tipos de cursogramas, se desarrollará un anexo. | |||
[[Archivo:CursogramaGraf.jpg|centro|marco|CURSOGRAMA GRAFICO DE PROCESO - Ejemplo]] | |||
[[Archivo:CursogramaAnalitico.jpg|centro|marco|CURSOGRAMA ANALITICO DE PROCESO- Ejemplo]] | |||
=== Cálculo de las Maquinas y Instalaciones === | === Cálculo de las Maquinas y Instalaciones === |
Revisión actual - 00:02 16 nov 2019
Introducción y Objetivos
El dimensionamiento técnico ó físico es probablemente el núcleo de todo proyecto y por eso es el que requiere el mayor nivel de trabajo. Debido a esta cantidad y complejidad del trabajo necesario es que la mayoría de las veces el dimensionamiento técnico es subanalizado. Aquí se dan dos posibles alternativas del porque de este subanálisis:
- Demasiada Importancia al dimensionamiento Comercial y Económico: La mayoría de los cursos dados sobre evaluación de proyectos se concentran en poder calcular el potencial de ventas y los resultados esperados económicos para poder determinar un flujo de caja . Esto es generalmente llamado plan de negocios ó business plan. Esto se enseña en la infinidad de cursos de apoyo a emprendedores, en todos los masters en negocios de todas las escuelas y en las carreras de administración de empresas. Y es entendible. Es muy lindo ver cuanto se puede vender, que formidable que nos compren lo que se nos ocurrió, como nos diferenciaremos en un mercado específico y como eso nos generará gran cantidad de dinero. Luego hacen unas cuantas cuentas sobre estimación de inversiones y costos y ¡voila! ya tenemos un negocio armado. Y si ponemos el doble de dinero la ganancia se duplica! Pero lo que no ven en estos casos es que las diferenciaciones comerciales son fáciles de duplicar, fíjense sino en la etapa inicial de Internet, donde una buena idea era inmediatamente replicada múltiples veces en cuestión de días, o cuando uno pone un local exitoso, en unos meses alguien puede poner un negocio similar a solo unos metros de distancia. Lo otro que falla en ver esta perspectiva es que la cuantificación económica de un proyecto puede solo surgir de haber analizado los recursos físicos necesarios. Los costos indirectos no siempre son fijos, las inversiones en stocks no se mantienen constantes con distintos volúmenes de ventas, no se puede multiplicar alegremente las ventas si las máquinas e instalaciones no dan abasto. Por eso una elaboración económica que no se encuentra basada en un sólido análisis técnico tiene tantas posibilidades de triunfar como una estimación dada por un oráculo.
- Demasiada Confianza en la capacidad técnica del dueño del proyecto: Muchas veces quien encara un proyecto es alguien que comprende la parte técnica del proyecto, es un mecánico, un cocinero, un ingeniero, ó trabajo toda su vida en una empresa textil, un criadero de animales o sabe programar desde los 12 años. Entonces es comprensible y hasta razonable que esta persona sienta que no necesita realizar un dimensionamiento técnico. Y de hecho sus estimaciones suelen ser completamente válidas para calcular las necesidades de instalaciones, insumos y máquinas del proyecto. En verdad el trabajo en el dimensionamiento técnico puede ser duro y llevar tiempo pero la solución no es dejarlo de lado, sino eventualmente simplificarlo, sabiendo que se han tomado estimaciones, pero con una estructura adecuada que permita posteriormente mejorar y profundizar el análisis para obtener resultados más exactos, tanto para pedir préstamos a los bancos como para permitir que otras personas participen y entiendan la totalidad del proyecto. Es por esta razón que al final de la elaboración de las actividades necesarias para cumplir cada objetivo, se mostrará la manera de simplificarlas para poder realizarlas rápidamente, pero de manera adecuada.
El trabajo a realizar en el dimensionamiento técnico incluye un amplio espectro de aspectos por lo que los conocimientos y técnicas necesarias son igualmente amplias y variadas. El orden en el que se van desarrollando los distintos elementos de esta etapa, tiene una lógica de cascada donde es necesario cumplir uno para poder ir avanzando en los restantes. Dichos elementos son:
- Determinación del Tamaño y la Localización
- Determinación Técnica del producto
- Determinación de los procesos
- Determinación de las Mercaderías
- Determinación de la Organización y el Personal
- Elaboración del Anteproyecto de Planta
- Generación del Cronograma de Ejecución
Para mostrar la integración entre todas las actividades realizadas para lograr alcanzar los objetivos del dimensionamiento técnico se muestra el siguiente diagrama. Si bien es complejo, es la mejor manera de ver de manera integrada dichas actividades y entender el porque de la vinculación entre los distintos objetivos.
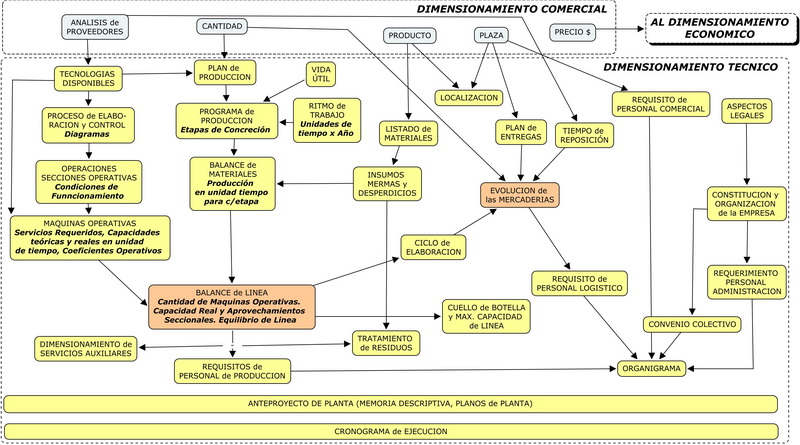
Como todos los dimensionamiento, existen luego de la etapa de Elaboración, las etapas de Formulación y Evaluación, donde presentan de manera resumida lo encontrado y se da lugar para que el inversor tome decisiones de evaluarlo.
Elaboración
Localización
Importancia de la Localización
En esta etapa buscaremos describir distintos métodos ó herramientas para determinar la localización de un proyecto. Pero esta introducción busca aclarar algunos puntos de conflicto entre diversas líneas de pensamiento.
La distinta bibliografía disponible que se ha consultado maneja el tema de la localización de dos maneras distintas: por un lado le asigna una importancia capital, de la cual dependerán todo el resto de los factores y la elección de una mala localización podría llevar a dar un proyecto con restricciones de tecnologías y resultados económicos negativos mientras que por otro lado hay una línea que observa que todos los recursos de los que necesita un proyecto son plausibles de colocar en cualquier lugar del mundo (si uno tiene la suficiente imaginación y dinero) por lo que la localización no es esencialmente importante, más allá de la satisfacción de la mejor manera de las necesidades del cliente. La primera línea de pensamiento es generalmente sostenida por los ingenieros y otras carreras técnicas mientras que la segunda es mantenida por profesionales ligados al marketing y a las ciencias económicas.
El problema con ambas líneas de pensamiento no consideran aspectos importantes en la determinación de la localización que hacen que dependiendo del tipo de proyecto, la importancia de este factor sea mayor ó menor ó sin importancia.
Volvamos a los distintos tipos de proyectos enumerados en el capítulo de Gestión Estratégica para poder analizar la importancia de la localización.
Los proyectos de Creación ó Generativos (nuevos producto, proceso, sistema ó empresas): Para este tipo de proyectos la importancia de la determinación de la localización es mayor. El caso más general para el cual la localización tiene una gran trascendencia es la creación de nuevas empresas, ya que no existen restricciones preexistentes en el sistema que puedan llegar a limitarlo, esto permita que haya más posibilidades para elegir. Pero cada una de estas posibilidades estará asociada a un alto grado de incertidumbre por tratarse de restricciones asociadas a un entorno. Distinto es el caso de los proyectos Generativos de nuevos elementos (productos procesos ó sistemas) en una empresa existente. Para este tipo de proyecto ya existen restricciones dentro del sistema analizado (la empresa) y por lo tanto estas restricciones limitan significativamente las posibles localizaciones, por lo tanto las alternativas suelen ser menos y más fáciles de comparar.
Los proyectos de Transformación ó Reingeniería (modificación de producto, proceso, sistema ó empresas): En este punto la selección del emplazamiento es donde empieza a perder la importancia que tenía para los proyectos de Creación, excepto que una de las modificaciones que se pretende hacer durante el proyecto sea efectivamente la localización. En ese caso se debe considerar la importancia de este paso, más aún teniendo en cuenta en que las restricciones son mucho mayores ya que existen una serie de factores que probablemente se encuentren muchos más limitados porque pueden ser parte de un sistema que no se puede ni se quiere cambiar.
Los proyectos de Retirada (eliminación de producto, proceso, sistema ó empresas): Se puede afirmar que para este tipo de proyectos el peso de la determinación de la localización es virtualmente nulo, ya que el elemento del cual es objeto el proyecto ya cuenta con una localización y esta se va a perder, por lo que la localización no pasa de una simple descripción del estado actual.
Otra cosa importante acerca de la elección de la localización de un proyecto, es en muchos casos la multiplicidad de opciones, muchas veces muy poco diferenciadas unas de otras, aún en proyectos relativamente simples. Aquí puede surgir la contrapartida que es darle un exceso de importancia a esta etapa, sobre analizando decenas de factores, buscando cada vez más información para tomar una decisión fundamentada, ocasionando una perdida de tiempo importante. No olvide que uno está desarrollando un bosque (el proyecto) y no un árbol (la localización).
Otro aspecto significativo de la etapa de determinación de la localización que vale la pena aclarar en este punto es hacer hincapié en la naturaleza iterativa de la elaboración de proyectos. Es completamente falso que una mala localización pueda afectar a nivel de elaboración de un proyecto la rentabilidad ó la capacidad de cumplimiento con los clientes ó la selección de la mejor tecnología del mismo. ¡¡¡Debemos recordar que nos encontramos trabajando sobre papel!!! Si se seleccionó una localización y esto hace que no sea aceptable la atención al cliente ó no compatible con una tecnología ó me proporciona una rentabilidad negativa, a nadie se le ocurriría desechar el proyecto. Simplemente se vuelve para atrás, se elije una nueva localización y acabo con el problema. De este punto surge indirectamente otra de las aclaraciones que hemos hecho en algún momento acerca de que es importante mantener una metodología consistente y coherente, ya que si no se cuenta con esta el volver sobre los pasos puede resultar extremadamente difícil.
Macrolocalización y Microlocalización
El estudio de la localización consiste en dos etapas bien diferenciadas: la macrolocalización y la microlocalización.
La primera consiste en determinar la región geográfica en general para la ubicación del proyecto y la segunda es la determinación del espacio físico específico donde se emplazará dicho proyecto.
La diferencia sustancial entre una y otra es el determinismo a la hora de seleccionarlas. Mientras que de la macrolocalización se pueden analizar áreas extensas con características inicialmente similares para ir estrechando el campo de alternativas y restringiendo el tamaño de esas áreas, la microlocalización es exacta, ó sea se va a construir ó desarrollar el proyecto en un lote específico, con un tamaño específico y que se encuentra a la venta.
Como uno pudiera imaginarse, la condición de disponibilidad de un espacio físico para la microlocalización puede ir variando a medida que pasa el tiempo y un terreno ó planta disponible para la venta cuando se elaboró el proyecto puede no estar a la venta cuando se decide ejecutarlo. La microlocalización generalmente se sugiere justo luego de la macrolocalización y se actualiza junto con los presupuestos cuando se decide ejecutar el proyecto.
Lo que se tiende pues es a realizar un proyecto lo bastante flexible como para poder ser incorporado a un tamaño tipo de lote de acuerdo a la disponibilidad en general del área correspondiente a la macrolocalización (por ej. en la ciudad de Buenos Aires son lotes de 8,66 metros de frente por 50 metros de fondo).
Momento de la Determinación de la Macrolocalización
Una pregunta que surge frecuentemente es que momento del análisis de un proyecto se debe determinar la macrolocalización. Esto dependerá tal como se dejó entrever anteriormente del tipo de proyecto.
Para proyectos de mejora, ampliación ó retirada de una empresa, producto, proceso ó sistema existente de los cuales no se quiere ó no se puede modificar la localización, es obvio que la localización del proyecto es simplemente una nota en la descripción del mismo.
El problema comienza a suscitarse cuando la empresa ó la planta son nuevas y realmente existe un mayor grado de libertad a la hora de elegir el sitio adecuado.
Las tres alternativas posibles son:
Determinación Previa a la Factibilidad Comercial: Cuando el estudio de las variables del mercado depende de la localización para poder llevarse a cabo sin tener que estudiar para cada alternativa los clientes, proveedores y competidores. Este tipo de localización se da generalmente proyectos comerciales donde la atención se hace en forma directa al público y la diferenciación se da por la propia localización. El caso típico para esto son las estaciones de servicios, los locales de ropa ó la venta minorista de alimentos, bebidas y productos de limpieza. Lo que se trata en la factibilidad comercial es por lo tanto realizar la validación de la ubicación seleccionada. En este tipo de caso una ubicación diferente de solamente un par de metros puede ser la diferencia entre un negocio factible y uno no factible.
Una circunstancia similar se da en el caso de multinacionales con varias plantas disponibles o con representación en diversos países. La posibilidad de poner una planta en un país o en otro implica un análisis mucho más profundo que el que se puede hacer a través de una decisión subjetiva ó una matriz de localización tal como se muestra más adelante. Generalmente este tipo de organizaciones cuentan con los recursos disponibles como para realizar un análisis completo, desde los puntos de vista comercial, técnico, organizacional, legal y económico-financiero para evaluar las distintas alternativas y por lo tanto la factibilidad ó conveniencia de la localización estará determinada como uno de los objetivos del análisis.
También es el caso donde la ubicación está determinada por una restricción total de uno de los factores de la producción. Este es el caso típico de las industrias extractivas tales como las explotaciones mineras y las torres de extracción de petróleo que solamente pueden ubicarse donde se encuentran los recursos disponibles.
Determinación durante la Factibilidad Comercial: existen algunos casos en donde el mercado que se atiende se conforma con la localización como por ejemplo en el caso de las empresas distribuidoras de servicios tales como distribución de electricidad, teléfonos, agua y cloacas, gas, y empresas de televisión por cable. Excepto por este último caso, el resto de las actividades citadas se encuentran en la mayoría de los países muy reguladas por el estado por lo tanto su localización y el trazado suele estar bastante restringido, pero aún así existen casos donde es necesario hallar la mejor distribución posible.
Determinación Previa a la Factibilidad Técnica: Este es el caso aplicado para la mayoría de los proyectos industriales. Para este momento ya se cuenta con una cantidad importante de información:
- La cantidad que se va a vender lo que nos da una idea del tamaño
- Se ha investigado la demanda compuesta por los clientes y los consumidores por lo tanto se puede apreciar como van a reaccionar ante una determinada localización y donde se haya ubicada esa demanda
- Se ha analizado a los proveedores de las principales materias primas y tecnologías y se conoce su ubicación y sus políticas
- Se distinguen los canales de distribución necesarios y sus comportamientos
- Se conoce a los competidores existentes, sus ubicaciones y sus políticas de ventas y distribución
Por otro lado existen una serie de determinaciones en el la factibilidad técnica tales como la distribución en la planta, la instalación de las máquinas y equipos auxiliares y los plazos en el cronograma de ejecución y restricciones del tipo legal (todo esto se verá más adelante) que dependen de la localización.
Por eso resulta ineludible para este tipo de proyecto es seleccionar en este momento el lugar de asentamiento del proyecto.
Como las primeras alternativas (previa o durante la factibilidad comercial) no presentan mayores restricciones desarrollaremos aquí los posibles métodos para la última alternativa.
Y por último volvamos a recordar lo que se aclaró anteriormente. Si bien es necesario determinar la localización en cualquiera de estos momentos del proyecto, esto no quiere decir que dicha localización no pueda ser modificada a posteriori. En las palabras de la investigación operativa lo que se busca es una solución factible, pero no necesariamente óptima.
Métodos de Determinación
Existen 2 métodos básicos para la determinación de la localización, el primero con una tendencia más subjetiva y el segundo más racional. A pesar de lo que la mayoría de los autores sugieren, ninguno de los dos tiene mayor validez que el otro, ya que más información y técnicas más sistemáticas en realidad no dejan de lado la subjetividad a la hora del manejo y valorización de la información.
Elección Subjetiva de la Macrolocalización
Como cualquier otra toma de decisión, la localización puede estar sujeta a predisposiciones por parte de quien toma la decisión, y en el caso de los proyectos también se encuentra ligada las predisposiciones del analista, del patrocinador, de los asociados ó de los accionistas.
Estas predisposiciones pueden observarse cuando se selecciona localizaciones ligadas a aspectos afectivos ó históricos como en el caso de comprar una vieja fábrica que antes la utilizaba algún familiar o cuando se intenta poner una fábrica en un pueblo de donde uno es nativo, a razones de conveniencia tales como cercanía geográfica a la casa del dueño, a perspectivas ilusorias cuando se piensa que existirán ó se desarrollaran factores a futuro dentro de la localización seleccionada ó por simple imitación del lugar donde otras empresas ó proyectos relacionados con objetivos y funciones similares al proyecto a desarrollar.
Nadie puede discutir que muchas de las decisiones, sino la mayoría, acerca de la localización son tomadas de esta manera, sobre todo en pequeñas empresas ó proyecto. La pregunta que uno se debe hacer es si esto es adecuado ó no.
El problema con las decisiones subjetivas es su naturaleza. Uno puede argumentar con la más infalible de las lógicas, pero si quien toma la decisión decide continuar siendo subjetivo, no existe manera de ganar dicho discusión.
Para solucionar esta coyuntura lo trabajaremos con la planificación impulsada por los descubrimientos, diremos que una de las suposiciones es la localización, indicando quién fue que tomo esa decisión. Esto permitirá utilizarlo más adelante en la gestión de la incertidumbre.
Elección Racional de la Macrolocalización
Este es sin duda el método más difundido y el más aplicado en todos los cursos de ingeniería alrededor del mundo, pero como se ha visto hasta ahora solo es aplicable a unos pocos casos, ya que hay prescindir de esta técnica en todos aquellos proyectos de retirada, en los proyectos de transformación ó reingeniería, en los proyectos donde la localización es inicial en el proyecto y en aquellos donde la decisión la toma subjetivamente alguna persona.
Este procedimiento se basa en el Proceso Directivo Racional y consiste en analizar en una Matriz de Localización distintas alternativas de localización en base a diversos factores.
El secreto no pasa por la aplicación de la técnica que es relativamente sencilla sino por la correcta selección de las alternativas y de los factores, así como también por cada valoración realizada. Aquí nuevamente surge el tema de la subjetividad en la toma de decisiones, ya que cada una de los elementos antes citados y por lo tanto la necesidad del profesional de realizar el análisis más lógico y ecuánime posible.
A continuación se da un ejemplo gráfico para su mayor comprensión.
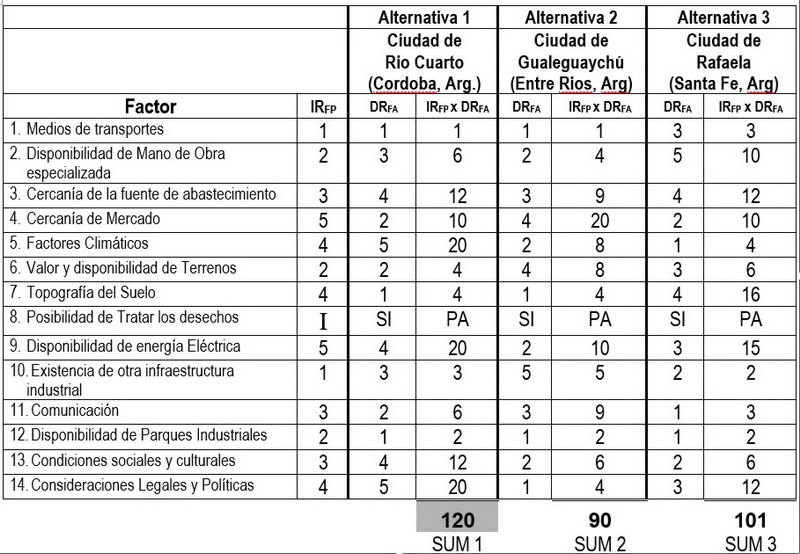
Primero hablaremos de las Alternativas. Cuando se eligen alternativas deben ser tres alternativas que contengan, por lo menos en una instancia preliminar, diferencias sustanciales desde el punto de vista de los factores que se van a analizar ya que si se analizar alternativas muy similares la tendencia de la diferencias no suelen ser significativas. Tres localizaciones separadas 20 kilómetros entre sí y las tres aptas para colocar proyecto deseado, probablemente difieran muy poco entre sí y se habrá llegado al punto de realizar una selección subjetiva que es lo que se trata de evitar con esta técnica. Tampoco tiene sentido elegir alternativas que realmente no cuenten con la infraestructura ni los factores necesarios y por lo tanto darán valorizaciones muy bajos. Esto podrá apreciarse de mejor manera en el análisis marginal explicado más adelante.
A continuación hablaremos de los Factores. En la tabla FACTORES POTENCIALES QUE AFECTAN LA LOCALIZACIÓN se enuncian una serie de factores típicos para el armado de una matriz de localización. Véase que se enumeran una serie de factores relacionados con aspectos comerciales, técnicos, legales, administrativos, y del entorno que impacten en la empresa tales como culturales, sociales y de seguridad. Cada uno de estos factores se encuentra a su vez conformados por diversos subfactores que en el armado de la matriz pueden ser puestos por separado. El caso más representativo es el de la infraestructura. En esta están incluidos subfactores tales como la disponibilidad de energía eléctrica, agua, gas ó telecomunicaciones. La importancia para cada uno de estos probablemente sea diferente en casi todos los proyectos y ponerlos todos juntos con una valoración única no es demasiado lógico. En el caso del ejemplo puede observarse en los factores 9 y 10 que se separa la Disponibilidad de energía eléctrica de la disponibilidad del resto de la infraestructura.
Mientras que algunos factores conviene disgregarlos, existen otros que no conviene ponerlos. Esto puede darse en el caso de que la existencia de un factor no tenga un impacto significativo en la localización (por ejemplo el clima) ó en el caso de que de ese factor no se pueda encontrar suficiente información como para poder realizar una valoración adecuada. Casos típicos de estas excepciones son muchas veces los factores culturales. También relacionado con esto es evitar poner factores relacionados con los costos de explotación del negocio, tales como los costos de logística, los costos de las materias primas y los costos de la mano de obra. Recordemos que nos encontramos en una etapa temprana de la formulación del proyecto y todavía no tenemos idea de los requisitos físicos para poder alcanzar la producción y las ventas estimadas y por lo tanto tampoco podemos dar fiabilidad de los costos y su estructura. Si pusiéramos este tipo de factores estaríamos realizando conjeturas poco racionales, lo que va en contra de lo esperado para este método. Solo un gasto, que luego será una inversión, puede analizarse entre los factores y este es el valor promedio de los terrenos ya que este es el único que se encuentra estrictamente relacionado con la localización.
Se deben tener además en cuenta aquellos factores que afecten tanto la etapa de instalación de proyectos como la operación a corto, mediano y largo plazo, considerando el crecimiento que podrá tener el mismo.
Una vez enumerados todos los factores a analizar lo que se procede es a valorizar la Importancia Relativa del Factor para el Proyecto (IRFP). Este coeficiente indica cuales de los factores son más significativos para el proyecto, siempre en función de cómo se vaya a evaluar el proyecto. Esto quiere decir que si se busca la localización para un proyecto donde lo que importan son los resultados económicos se asignará un mayor valor a los factores que me reduzcan los costos y las inversiones, mientras que si lo que se desea de un proyecto es aumentar el empleo se valorizará en mayor medida los factores que generen más mano de obra por más que la productividad no sea la mejor.
La tendencia suele ser a la valorización de la Importancia Relativa del Factor para el Proyecto (IRFP) en una escala de 1 a 10 que resulta natural para la mayoría de las personas, pero en la mayoría de los casos una escala tan amplia suele traer complicaciones al tratarse de valorizaciones subjetivas, por lo que es recomendable utilizar una escala de 1 a 5 que es igual de manejable pero presenta menos inconvenientes.
Existe además un caso particular que es aquel de los factores fundamentales y obligatorios. Este suele ser el caso de algunos requisitos naturales como el clima, donde es imposible la instalación de algunos proyectos donde los materiales o las instalaciones sean susceptibles a las temperaturas altas o bajas (como es el caso de las explotaciones agropecuarias), o en los casos donde la energía eléctrica ó la disponibilidad de agua abundante es restrictiva, o en el caso donde se generan gran cantidad de residuos tóxicos y es necesario poder contar con un tratamiento adecuado de dichos desechos (este es el caso dentro del ejemplo del punto 8). Para ese tipo de factores cualquier magnitud carece de sentido y es necesario manejarlo de una manera distinta por lo que en su lugar se le asigna una letra, en este caso la I (imprescindible).
Algunos modelos buscan que la sumatoria de las importancias relativas sumen un total de 100 pero esto no aporta ni a la metodología ni a los resultados, sino que restringe el proceso de valorización y construcción de la matriz ya que en cuanto se conocen nuevos factores o más información sobre los factores existentes será necesario cambiar la importancia de uno de los factores en detrimento de los otros.
Subsiguientemente se procede a estudiar como cumple cada alternativa con cada uno de los factores y esto se valoriza a través de la Disponibilidad Relativa del Factor en la Alternativa (DRFA). Tal como en el caso del indicador anterior se recomienda hacer esta valorización en una escala de 1 a 10 o de 1 a 5, excepto para el caso de los factores imprescindibles que se procederán a apreciar como SI o NO en función que dicho factor se encuentre representado en la alternativa. En caso de que una alternativa no cuente con un factor considerado imprescindible, la misma debe descartarse como alternativa.
Fijese que en el caso de ambos factores (IRFP DRFA) y casos hablamos de cuestiones relativas debido a que estas valorizaciones dependen tanto de la información con la que se cuenta como con la subjetividad del analista. Otra cosa importante con respecto a la cuantificación de estos factores es que puede ser que realicen algunas suposiciones para fijar estas estimaciones. Si esto es así no debe uno olvidarse en que estas suposiciones así como también quien las hizo deben registrarse para poder luego utilizarse en la gestión de la incertidumbre.
También nótese que la escala comienza en ambos caso en 1 y no en 0 ya que esto implicaría ó que el factor no es importante ó que la alternativa no cuenta con ese factor, que mucho ó poco pero tiene incidencia en el proyecto.
Una vez terminado de plantear las constantes en esta matriz, se procede a ponderar los valores de IRFP y DRFA para cada alternativa (esto se aprecia en el ejemplo presentado) y finalmente se procede a realizar la sumatoria de esta ponderación y aquella que resulte mayor corresponderá a la alternativa que se debe seleccionar como localización para el proyecto, en nuestro caso la Localidad de Río Cuarto en Córdoba, Argentina.
Hasta aquí todo muy bonito y prolijo, pero lamentablemente no siempre las decisiones son tan claras. ¿Qué hubiese pasado si otra alternativa hubiera dado una sumatoria muy similar? En esos casos lo que se hace es buscar entre los factores deseables con mayor Importancia relativa y ver cual es el comportamiento de estos factores para esas alternativas y elegir aquella cuyas disponibilidades de esos factores sean las mejores. Si aún así no existe ninguna opción clara, lo único importante es... ¡Tomar una decisión! ya que se trata de alternativas prácticamente igual de convenientes para la localización de nuestro proyecto.
Por último si en vez de tomarse los valores absolutos como parámetros para la evaluación de las alternativas se busca que porcentaje estos valores representan sobre el máximo total alcanzable, se puede realizar un análisis marginal que no cambia los resultados pero sirve para entender en mayor profundidad las sumatorias resultantes.
A continuación se arma una tabla para calcular estos porcentajes.

Se puede percibir que la mejor alternativa cubre en un 62% las condiciones que se considerarían ideales para localizar el proyecto y que esta es superior con respecto a la peor alternativa en 16 puntos porcentuales. En este caso no hay problemas ya que un 62% de cobertura se encuentra dentro de lo razonable, pero se sugiere que cualquier alternativa con un porcentaje menor a un 50 % no sea considerado como alternativa válida ó que por lo menos esto quede indicado en el estudio de localización si se pretende seguir con la elección de dicha alternativa. También es importante la diferencia porcentual ya que si se tratara de locaciones con diferencias mayores al 30-35% en realidad estaríamos comparando alternativas que no son completamente comparables y habremos entrado en el campo de la subjetividad al seleccionar alternativas de menor jerarquía con el conciente ó inconciente deseo que la localización sea una ya predeterminada. Y para esto es mucho más fácil y resulta menos trabajoso realizar una decisión subjetiva, asentarlo como presunción para analizar en la incertidumbre y dedicarle el tiempo a otras cosas que se consideren más importantes.
Tamaño del Proyecto
Uno de los primeros temas a tratar dentro del marco del dimensionamiento físico es la determinación del tamaño del proyecto. El tamaño de un proyecto está asociado a múltiples factores, algunos surgidos de la internalización de objetivos del inversor y otros surgidos del propio análisis en el proyecto, entre ellos del estudio de mercado que determina la demanda a satisfacer, las escalas de producción que son posibles adoptar de acuerdo a las tecnologías disponibles, las restricciones legales y sociales que pudieran haber y los recursos de financiación para el proyecto, tanto la disponibilidad de aporte de por parte del inversor como los créditos disponibles en el mercado.
Si el monto total de la inversión no fuera una restricción, el tamaño debería estar asociado al plan de ventas que surge del dimensionamiento comercial.
Determinación del Tamaño sin limitación de Capital
Lo primero a tener en cuenta, es si las ventas son crecientes ó estables en el tiempo.
Hay casos donde el cálculo del tamaño de la planta y de la tecnología a utilizar se realiza una sola vez para el proyecto, ya que el nivel de ventas y de producción se mantienen estables, tal es el caso de los trabajos a nivel de prefactibilidad en general o a nivel de factibilidad en el caso de que el tamaño de la planta esté limitada por cuestiones operativas ó legales. Este ejemplo que es el más sencillo a la hora de dimensionar y del cual se pueden extrapolar el resto de los casos se explicará en el Cálculo de las Maquinas y Instalaciones.
En el caso donde las ventas son crecientes en el tiempo, es necesario plantear el proyecto en diversas etapas asociadas al tamaño, para evitar un gran subaprovechamiento de las las máquinas compradas.
Este caso es común en los casos donde la inversión en maquinarias es muy significativa y por lo tanto es usada 24 horas del día y los 7 días de la semana. En los casos donde la escalabilidad del proyecto puede realizarse agregando turnos, esto es preferible porque se optimiza el uso del capital, tal como se explica en el siguiente apartado.
Si bien pueden irse agregando etapas para aumentar la capacidad de la planta en cualquier momento del proyecto, hay que entender que la ampliación de una planta es disruptiva para una empresa en marcha, sobre todo si se realiza en el mismo predio y edificio donde ya se encuentran trabajando otras etapas.
En reglas generales, uno debería dimensionar una primera etapa con las maquinarias para poder hacer frente al plan de ventas al cabo de un tercio del período de análisis, por ejemplo los primeros 3 años en un plan a 10 años ó los primeros dos años en un plan a 5 años.
Como veremos más adelante, la primera sección operativa que se satura cuando la cantidad producida empieza a crecer es el cuello de botella. Esta será la etapa que se debe monitorear para poder determinar el momento en el cual es conveniente realizar la ampliación del tamaño.
Un poco diferente puede ser el tratamiento de los edificios y las instalaciones donde se encontrarán alojadas las maquinarias. Si la instalación de nuevas máquinas es disruptiva, aún lo es más la construcción de edificios e instalaciones que demoran mucho más tiempo y que incluso pueden llevar a paradas de la línea para evitar contaminación en los productos justo en los momentos donde el cuello de botella está alcanzando su máxima capacidad. En este sentido, es recomendable considerar dimensionar el edificio y las instalaciones para poder albergar la totalidad de las máquinas y los procesos necesarios para todo el período de análisis.
ANTES DE HABLAR DE ESTO TENGO QUE HABLAR DE IR ESCALANDO LA INVERSIÓN ANTE UN PLAN DE VENTAS CRECIENTES
Criterios para la Optimización del uso del Capital
No obstante que no se cuente con una restricción del capital total a aportar, es indispensable optimizar el uso de dicho capital con el fin de mejorar tanto la tasa interna de retorno como el periodo de recupero de la inversión. Recordemos que en este punto del proyecto no hemos realizado cálculos económicos, por lo que las tecnologías a adoptar no pueden compararse en función de un criterio de Valor Actual Neto.
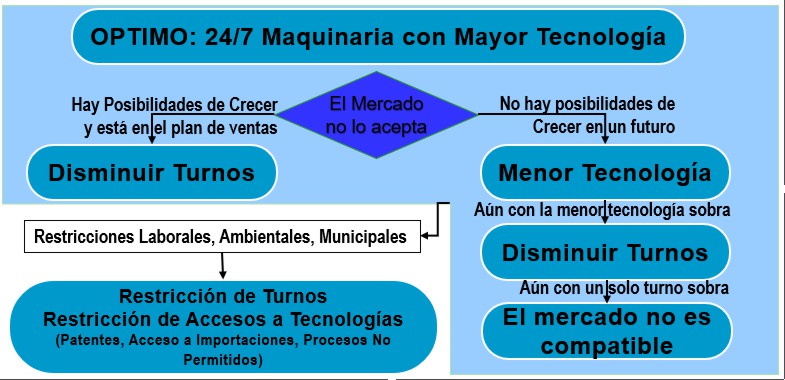
Dentro de los factores internalizados el más importante en caso de existir es la disponibilidad real de aporte de capital por parte del inversor. Recordemos que uno de los objetivos propuestos a nivel económico puede ser una limitación en le aporte de dinero que está dispuesto a aportar quien efectivamente está financiando este proyecto. En el punto que nos encontramos (si nos hallamos todavía a nivel de prefactibilidad) todavía no hemos realizados cálculos económicos asociados a la inversión total requerida, por lo que ese objetivo no hemos podido ver si se puede alcanzar ó no, pero ya tenemos que estar determinando el tamaño (cantidad a fabricar, tecnologías a utilizar, edificios que necesitamos). Es otro punto en el proyecto donde podemos aplicar el concepto de planificación impulsada por descubrimientos. Lo que debemos hacer es estimar la inversión necesaria. Para esto tendremos que recurrir a información que si no hemos utilizado en la determinación del plan de ventas en el dimensionamiento comercial, la utilizaremos ahora.
Dentro de las inversiones que se generaran posteriormente, podemos estimar la inversión total a partir de calcular la inversión en activo fijo no tercerizable y calcular la inversión en activo de trabajo como el valor final del activo de trabajo. La primera es tener una idea de la maquinaria e instalaciones específicas necesarias, más los gastos necesarios para la constitución y habilitación de la empresa.
Dentro de la inversión en activo de trabajo se puede decir que si averiguo el plazo en el que me pagan la mercadería (por ejemplo 60 días) teniendo el precio de venta del estudio de mercado puedo acceder a una estimación de la inversión inicial necesaria en lo que hace a todos los posibles costos necesarios en los primeros meses de explotación. A esto habrá que sumarle las compras mínimas de materias primas si es que estas existieran.
Vamos a entonces a elaborar los conceptos para cada tipo de inversión.
Como se aclaró anteriormente, la inversión en Activo Fijo se debe calcular como la inversión en la constitución de la empresa y la inversión en bienes de uso críticos en máquinas, instalaciones asociadas a esas máquinas y Edificios.
Para el caso de la constitución y habilitación legal de una empresa, hay que tener en cuenta sobre todo las habilitaciones particulares requeridas según el tipo de industria (Salud, Alimentos, Impacto Ambiental). Esto se estima en este punto preguntando a un tecnólogo que sepa del sector. El gasto total en este rubro rondará entre los 500USD para proyectos simples en países de bajo nivel de burocracias hasta los 50.000 USD en proyectos en sectores altamente controlados en países de alto nivel de burocracia.
La inversión en bienes de uso críticos resulta aquella de la información recabada de los proveedores críticos en el Dimensionamiento Comercial. Se debe preguntar a dichos proveedores la inversión en una tecnología adecuada al nivel de inversión límite.
A través de la experiencia práctica puedo afirmar que la proporción de activo fijo y activo de trabajo es de un 50%-50% .
Por lo que si el nivel de inversión máximo esperado es de 1.000.000 USD, la mitad de esa estará dedicada al activo fijo, y de esa mitad habrá una cantidad de entre 500 y 50.000 USD de inversión en constitución de la empresa, supongamos 10.000 USD.
La inversión en máquinas e instalaciones críticas no debería superar los 490.000 USD.
El resto de las inversiones en activo fijo pueden generalmente subsanarse alquilando ó tercerizándose (edificios, transporte, almacenaje) ó su inversión no suele ser significativa (elementos de oficina, gasto de puesta en marcha).
Estacionalidad en la demanda ó en la provisión de insumos
Determinación Técnica del Producto
En este punto se busca redefinir desde un punto de vista técnico el producto que ya fue definido a nivel comercial. Como hemos visto, a nivel comercial no es necesario entrar en demasiados detalles del producto, más allá de algunas características necesarias para satisfacer necesidades específicas de los clientes, especialmente aquellas orientadas a generar alguna diferenciación con respecto a la competencia.
Debido a la gran variedad de productos y servicios que pueden generarse a partir de un proyecto, no existe un listado único y exhaustivo que invoque la totalidad de dicha variedad. Por lo tanto, si bien los aspectos explicados a continuación pueden aplicar a la mayoría de los casos, nos concentraremos en productos físicos. Es importante en este punto también empezar a formar un criterio personal (profesional ó no) y determinar cuales de estos aspectos son necesarios y cuales no.
Datos iniciales de entrada de diseño
Esto implica traer al dimensionamiento técnico los datos definidos en el dimensionamiento comercial
Nombre Genérico ó Tecnico del Producto y modelos del producto, código del producto
A partir de este momento, el nombre comercial del producto no tiene importancia, solo se trabajará con los nombres genéricos y con los modelos puntuales. Muchas veces es importante diferenciar en la etapa técnica el producto a través de códigos en lugar de referirse a ellos a partir del nombre comercial por varios motivos: por un lado permite que la documentación técnica referida a los productos esté liberada de las modificaciones comerciales de los nombres comerciales que muchas veces se mantiene a pesar de ir realizándose modificaciones técnicas, por otro lado la codificación de un nombre muchas veces permite tener información del producto sin necesidad de ver especificaciones. Por ejemplo es distinto hablar de una bomba Klein que una bomba MCC-65S1N donde cada una de las letras ó conjunto de letras tiene un significado (en este caso que tiene un motor de corriente continua, con un cabezal de 65mm para usar con tubo de silicona, con un solo sentido de giro y un accionador Neumatico).
Uso pretendido
A pesar de parecer algo obvio, el uso pretendido es algo muy importante ya que representa la primera responsabilidad legal que tiene el proyecto. Esta definición es importante porque dice al usuario que el uso del producto es ese y solo ese y que la empresa se responsabilizará si el producto es usado con ese fin solamente. Un uso demasiado amplio provocará que se tenga que definir todas las posibles implicaciones en el análisis de riesgo y un uso demasiado acotado puede limitar el público objetivo para el producto.
Productos Complementarios (enumerar los surgidos en la parte Comercial)
En este punto enumerar los productos complementarios no cumplen con una función de analizar la demanda potencial a partir de extrapolar la demanda de los complementarios, sino que lo que busca es buscar las interrelaciones y la conectividad que tendrá nuestro producto con los productos complementarios (tipo de conexiones, protocolos de comunicación, superficies de contacto, necesidades de transmisión de energía, nutrientes, información, etc.)
Especificaciones de Materiales ó Procesos
por ejemplo en caso de utilizar una fuente de energía que tipo de energía utilizará, los colores que se han de elegir para representar a la empresa ó al producto, los procesos y materiales permitidos, apropiados, recomendados y socialmente responsables necesarios.
Esquema Básico
Un esquema de producto es siempre útil para permitir seguir elaborando el producto en detalle. Nos permite dar una mirada amplia de las funciones necesarias y nos permite preguntarnos si no es necesario algún elemento adicional ó si no existen elementos superfluos.
Datos Finales de Diseño de Producto
Los datos finales de diseño son los resultados obtenidos a partir del proceso de diseño del producto. El diseño de todo producto implica un proceso creativo iterativo donde distintas alternativas son sopesadas. El proceso de diseño escapa al alcance de este libro, pero lo que se puede asegurar que no importa que tan complicado sea este proceso, los resultados finales se tienen que registrar de manera adecuada para poder garantizar la repetitibilidad de los resultados deseados y esperados cada vez que se realiza un producto o se brinda un servicio como resultado de la explotación del proyecto.
Documentos de Definición del Producto, Materisa Primas y Materiales
Nos referimos como documentos del producto al conjunto de registros y procedimientos estandarizados y disponibles para quien eventualmente elabore el producto. Algunos ejemplos de estos documentos son: Planos, Normas, Especificaciones Técnicas, hojas de seguridad, Listado de materiales, procedimientos de prestación de un servicio. Para la mayoría de los productos, existen maneras normalizadas de presentar dichos documentos, bien a través de un requisito legal, ó a través de normas del sector ó a través de usos y costumbres. Estos diversos modos pueden verse por ejemplo en el área de educación: Mientras que los contenidos de un curso de una escuela primaria debe seguir lineamientos estrictos fijados por leyes, los cursos brindados por un instituto privado de capacitación empresarial no tiene requerimientos legales pero si una estructura obligatoria fijada por normas internas del instituto, mientras que en el último caso por ejemplo los cursos de capacitación propuestos por un consultor a una empresa la estructura con los contenidos debe tener cierta información (destinatarios, contenidos mínimos, horas necesarias) pero no existe un requisito legal ó una norma unificada del sector educativo para presentarlo.
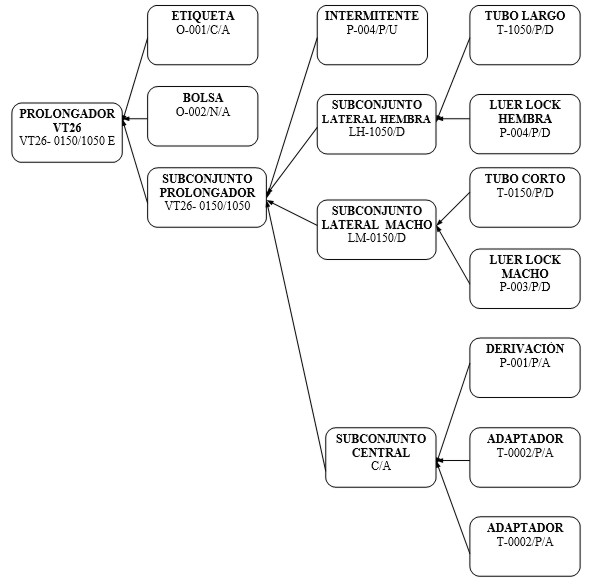
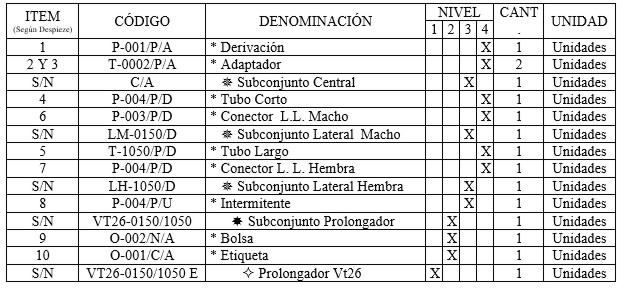
Sería imposible enumerar todos los posibles documentos de definición técnica de un producto sin embargo como anexo se presentan una serie de documentos y las recomendaciones para hacerlos.
ANEXO Documentación para la Definición técnica del producto
Características-Condición del Producto
Las características condición del productos son aquellas características que son condiciones necesarias para que el producto se considere como apto para ser usado. Si bien es discutible que todas las características de un producto hacen al mismo, la verdad es que en todos los casos existen algunas características que sin dudas son más importantes que otras. Por ejemplo en los alimentos el color de la tinta de la etiqueta puede llegar a afectar la estética del producto y hacer que se pierdan ventas, pero la seguridad microbiológica del alimento es infinitamente más importante ya que en eso puede ir la vida de las personas que consuman el alimento. No todos los casos son tan graves como el expuesto ó como es el caso de los medicamentos y productos médicos, pero es importante discriminar las características deseables de las obligatorias. Sobre estas últimas es donde se dispondrán de sistemas de control más exhaustivos ó de procesos, insumos y proveedores que garanticen la falta de problemas.
Ensayos de Validación de Concepción
Los ensayos de validación de concepción son aquellos ensayos que deberán hacerse al prototipo ó a la primera serie de productos para validar que el producto cumple con las características-condición planteadas. Ejemplos de estos ensayos son los ensayos de seguridad eléctrica en equipos eléctricos, los ensayos microbiológicos y de composición química en los alimentos, ensayos de concentración de metales del agua con la que se alimentará un proceso industrial. Estos se realizan periódicamente, generalmente anualmente pero puede ser mayor ó menor en función de requerimientos legales, y son necesarios al comienzo del proyecto para poner a punto el nivel de calidad deseado para el producto. Estos ensayos suelen ser complejos y demandar bastante tiempo y dinero, por lo cual generalmente no se realizan continuamente en todos los lotes de fabricación. Estos ensayos realizados continuamente en todos los productos ó lotes se disponen en el plan de ensayos, tal como se explica en el siguiente punto.
Plan de Ensayos
El plan de ensayos cumple la función de verificar el comportamiento de las características de un insumo, semielaborado ó producto antes de que el mismo sea liberado hacia la etapa siguiente ó para su comercialización. En cuanto al plan de ensayo hay que tratar de nivelar el costo de realizar dichos ensayos y los riesgos asociados a no realizarlos. Muchas veces al estar el riesgo disociado del costo del fabricante se dejan de hacer ensayos porque su costo ó el tiempo que tarda es demasiado sin tener en cuenta que eso puede poner en riesgo la seguridad ó la calidad de vida de los usuarios ó de otros grupos de interés.
El plan de ensayos sobre el producto se transformará a nivel de procesos en los procesos de verificación y control.
Marcado sobre el Producto
El marcado sobre el producto hace referencia a los rótulos que deben llevar los productos. La mayor parte de los productos comercializados hoy en día tienen una obligación de legal de contener cierta información: Denominación de Ventas, Pais de Origen, Fecha de Vencimiento, Cantidades Netas, Modo de Conservación, Información Nutricional, Nombre del fabricante y registro del mismo. Esta información puede variar de país en país y muchas veces de jurisdicción en jurisdicción con lo cual se debería consultar la legislación vigente. Muchas veces la legislación vigente en amplia y compleja, por lo que otro método de resolver esto se encuentra en ver que información presentan los principales competidores en sus productos y usar esto como referencia.
Pero adicionalmente existe información que uno quiere suministrar para que quien use ó mire nuestro producto ó servicio como por ejemplo la marca, ó información para que el usuario se vea tentado a usarlo. Dentro de las recomendaciones que se pueden dar en este aspecto son:
Usar Tipografías con colores que contrasten: Negro sobre blanco ó amarillo, verde sobre blanco, y dentro de esto con el mayor tamaño posible.
Usar textos “Tipo Frase” y no en “MAYUSCULAS” e interlineados grandes para entender mejor el texto
Usar referencias visuales conocidas en los envases tales como fotos, ilustraciones, iconos y gráficos y una fecha de vencimiento fácil de hallar ya que existe una reacción positiva. Es importante que este diseño refleje el contenido ya que si no se corre el riesgo de que no se genere confianza con los clientes.
Otras veces el marcado sobre el producto cumple la función de mostrar instrucciones de uso del producto (corte aquí, no someter al fuego, recargue solamente en distribuidores autorizados). En muchos casos el marcado sobre el producto debe usar no solo palabras sino también simbología, y la mayoría de las veces dicha simbología está estandarizada, este es el caso de los códigos de barras.
A continuación se muestran ejemplos de dicha simbología.

Otra parte importante comúnmente presente en los productos de consumo masivo es la incorporación de un código de Barras. Un código de Barras es un conjunto de cifras con una estructura predeterminada, cuyo objeto es lograr la identificación inequívoca de un producto. Esto facilita la circulación de las mercaderías, puede ser leído por diversos equipos de captura de datos, permite acelerar las operaciones en la caja registradora disminuyendo la posibilidad de error, extraer el precio correspondiente a cada artículo de la memoria.
La cadena de comercialización cuentan con la posibilidad de introducir un sistema de gestión de stocks para controlar, producto a producto, el movimiento de sus mercaderías.
Existen varias normas, las dos más comunes son la EAN-13, utilizada en todo el mundo excepto en EEUU donde es utilizada la norma UPC-A.
Estos implican una inversión y un costo para el proyecto, dependiendo de la cantidad de ítems que se quieran codificar. La contratación de este servicio va desde los 250USD como inversión inicial y un costo de 50 USD anual por 10 códigos de barras, hasta 10.500USD de inversión inicial y 2100USD por 100.000 códigos de barras.
También se pueden generar códigos de barra propios internos sin ningún costo, pero estos no serán aceptados en las cadenas de comercialización.
Acondicionamiento del Producto
el acondicionamiento del producto se refiere al envasado y embalado del producto. La importancia del acondicionamiento del producto es muchas veces tan importante como las características propias del producto, ya que muchas veces el cliente “compra” el envase ya que esto es lo único que se ve. También es una manera de diferenciarse en el caso del embalaje, ya que muchas veces por la facilidad de transportar ó guardar, se elige un producto sobre el otro, especialmente cuando la diferencia de precio es baja y los productos no son diferenciados.
Para más información ir al Anexo de Envases y Embalajes
Productos Complementarios (descripción Técnica)
Todo producto que se diseñe está destinado a ser usados junto con otros elementos que permiten su funcionamiento ó la consecución de su objetivo. Entre los productos complementarios debemos destacar tres grandes familias, aquellos productos que deben comercializarse con el producto, aquellos que pueden comercializarse con el producto, aquellos con los que el producto va a usarse pero se comercializan por separado.
Como ejemplo de los productos que deben comercializarse con nuestro producto se puede nombrar los manuales. Para los productos de consumo masivo eléctricos y electrónicos, para los insumos médicos, para los automóviles y para todos los productos cuya comercialización está de alguna ú otra manera regulado por el estado, los manuales son obligatorios. Estos manuales deben tener 2 características claves: deben ser fáciles de interpretar y deben cumplir con las reglamentaciones vigentes. Un ejemplo típico en donde se falla en ambas características es en el idioma en el que se redacta ya que un manual no puede estar redactado en un idioma distinto al del oficial del país donde se va a comercializar, y la simple traducción automática con un software de traducción genera muchas veces explicaciones confusas.
Otros productos que deben comercializarse con los productos son por ejemplo los certificados de garantía, los cables, servicio de mantenimiento.
Dentro de los productos que pueden comercializarse con el producto base de nuestro proyecto hay que destacar aquellos que facilitan la función y el uso de nuestro producto y aquellos que son necesarios para el uso de nuestro producto. Un buen ejemplo para ambos casos es el software para los equipos informáticos. No es obligatorio vender el software junto con los equipos, aunque es probable que si se vende sin el software las ventas sean menores, ya que los clientes tendrán que pasar por un doble proceso de compra y no estarán seguros de la compatibilidad entre los productos. Otro caso típico de estos son las recetas que se colocan en los reversos de los envases de los productos alimenticios procesados. Estas recetas deben ser adecuadas para el producto, fácil de hacer con el producto comercializado y… ¡estar seguro que funcione!
Para el caso de bienes intermedios y máquinas industriales es común también ofrecer servicios de instalación, cursos de capacitación para aprovechar mejor el uso de los productos, como diferenciación a la hora de comercializarlos. Que sean productos complementarios no implican que no se tengan que definir específicamente, ya que si se ofrece este tipo de soluciones la prestación debe realizarse con la calidad acorde al producto y con la calidad promocionada, ya que sino se podrían obtener más problemas que ventajas.
Entre los productos que son comercializados por separados, casos comunes son el combustible para los vehículos, la energía eléctrica, las baterías, los cables de audio y video, herrajes para madera. En la mayoría de los casos donde existen esta necesidad de vinculación con otros productos de otros mercados, suelen existir normas de cumplimiento obligatorios ó recomendables para evitar problema de interfaz. El no poder vincularse a productos complementarios, es muchas veces una de las causas principales de fracasos de productos ó inversiones innecesarias en rediseño.
Verificación y Liberación de Diseño
En empresas en marcha, sobre todo en aquellas que cuentan con un sistema de gestión de la calidad, es importante realizar la verificación y validación el diseño, esto incluye los ensayos necesarios para la liberación, el análisis de riesgo del producto, la aceptación de los medios de fabricación y control y el listado de documentos y datos liberados a cada área.
En proyectos de inversión, no es común que se desarrolle este punto, ya que no hacen a los presupuestos que son necesarios hacer para poder evaluar el proyecto. No obstante, cabe destacar que si es necesario realizar de manera rutinaria y continua estos procesos en la empresa que surja el proyecto, habrá que considerarlos a la hora de determinar el personal necesario.
Otras consideraciones del Diseño de Producto
Esta serie de puntos cubiertos dentro de la especificación técnicas del producto cumple con los requerimientos formales necesarios para poner en marcha el proyecto, sin embargo todos podemos comprender que el diseño de producto es algo más que la simple enumeración de los requisitos y va más allá de dicha enumeración.
A la hora de diseñar los productos se debería tener en cuenta lo que se denomina “diseño amigable”.
Un diseño, además de contar con todas los requerimientos técnicos, tiene que ser:
- Amigable con el usuario: fácil de entender de que se trata el producto, fácil de recoger o almacenar, sin un peso excesivo, generar un sentido de pertenencia y/o de diferenciación,
- Amigable con el Ambiente: Utilizar materiales reciclables tanto en el producto como en el embalaje, optimizar el uso de energía u otros consumibles
- Amigable visualmente: dar la sensación de un diseño moderno, contar con un diseño diferenciador y original, usar colores adecuados con el uso pretendido,
- Amigable con el proceso de Instalación: fácil de montar, instrucciones disponibles y fáciles e entender, contar con todos los insumos necesario para el montaje y uso final ó en su defecto aclarar donde conseguirlos.
Para ver más información acerca del proceso de Diseño de Producto, ver el anexo
Determinación y Diseño del Proceso de Elaboración y Control
Una vez determinado el producto que se quiere fabricar, es necesario empezar a determinar los procesos necesarios para poder llevarlo a cabo.
Muchas veces el producto y el proceso se van desarrollando de manera paralela, ya que el diseño o materiales a usar en los productos depende de las tecnologías a utilizar.
La fuente de información de las tecnologías disponibles puede provenir del análisis comercial, cuando se hizo el análisis de proveedores, o de la consulta de los expertos ó del tecnólogo.
Existe una extensa diversidad de procesos que abarcan desde las industrias más conocidas como las industrias metalmecánicas, hasta las industrias electrónicas más avanzadas donde parte del proyecto implica de hecho desarrollar tecnologías nuevas y específicas.
Desarrollar todos los procesos posibles escapa en este momento a los alcances de este libro, si bien en anexos se irán desarrollando el tema específico para cada tipo de industrias.
Diagramas Iniciales del Proceso
Para el diseño y modelamiento del Proceso generalmente se inicia con el armado de Diagramas Iniciales de Proceso de Fabricación y Control. Para esto generalmente se utilizan diagramas de flujo. Los diagramas de flujos son representaciones gráficas que permiten esquematizar de manera simple procesos productivos y flujos de trabajo paso a paso.
Si bien existen diversos tipos de simbologías para representarlos, las más comunes para procesos industriales abarcan los siguientes gráficos:
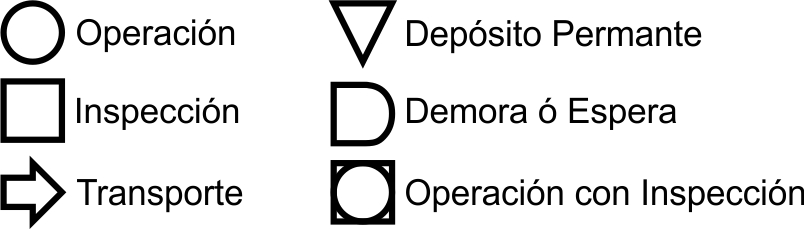
Otro ejemplo común de diagramas de flujos son los utilizados para procesos que incluyen el manejo de información:
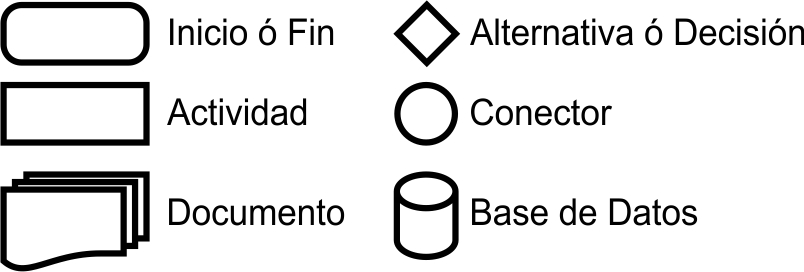
Cualquiera que se use, se deberá usar siempre un mismo criterio, o llegado el caso indicar la simbología utilizada al pie del gráfico.
Diseño del Proceso
A continuación vamos a describir conceptualmente las distintas alternativas para cada una de secciones operativas, que si bien en muchos casos es posible elegir distintos tipos de procesos para una misma sección, muchas veces esto no es conveniente ya que se producen variaciones en la calidad de los productos salidos de una misma sección operativa.
Desde el punto de vista de la intervención de la mano de obra, los procesos se catalogan en:
- Procesos Manuales: Son aquellos donde el ritmo de trabajo depende exclusivamente de la persona que lo realiza. Puede estar acompañado del uso de herramental simple que ayuda a la persona a realizar su tarea. Ejemplos típicos de esto son los procesos ensamble, la construcción tradicional, la costura en los talleres textiles, etc. Se caracterizan por su baja necesidad de inversión y de instalaciones, por ser fácilmente escalables y por la gran variabilidad en los tiempos. También al contarse con el trabajo de personas, esto puede provocar paradas ó retrasos por cuestiones personales, falta de personal, y en algún caso riesgos vinculados a los accidentes y la salud de dicho personal.
- Procesos Automáticos: son aquellos donde el ritmo de trabajo depende exclusivamente de las máquinas operativas, y no hay intervención de las personas excepto casos excepcionales (paradas, arranques o carga de materiales). Ejemplos típicos de esto son los hornos continuos, las cabinas automáticas de pintura ó los telares mecánicos. En estos casos la inversión tanto en las máquinas operativas como en las instalaciones suele ser alta, las capacidades de producción por unidad productiva también son altas, son difíciles de escalar ya que su instalación es compleja y requiere espacio. Mientras que las paradas ó retrasos son inusuales, cuando estos se producen generalmente son debido a roturas y por lo tanto muy adversos tanto desde el punto del costo como desde el punto de vista de pérdida de tiempo.
- Procesos Semiautomáticos: son aquellos donde el ritmo de trabajo es compartido tanto por las personas como por las máquinas operativas. Esto provoca que tengan las ventajas y desventajas de los dos esquemas anteriores. Por lo que la inversión no es tan alta pero si es significativa, las capacidades productivas son algo intermedio entre ambas, pueden producirse paradas o falta de actividad tanto por problemas de las máquinas como por problemas ó accidentes del personal.
Generalmente para un proceso dado en una industria dada, cuando se requieren bajos niveles de producción se opta por procesos manuales, luego se opta por procesos semiautomáticos y finalmente por los automáticos.
Desde el punto de vista de su naturaleza, podemos catalogar los procesos en:
- Procesos de Transformación: Son todos aquellos procesos donde la materia prima, mercadería en curso ó materiales que entran al mismo son distintos a los productos elaborados ó semielaborados que salen del mismo. Estas transformaciones pueden ser mecánica, procesos tales como el torneado ó fresado, puede ser transformaciones químicas como la fermentación, pueden ser un simple cambio de estado en procesos como el evaporado ó a veces el proceso de transformación son simples mezclas ó ensamblados donde la naturaleza de de las materias primas no cambia, solo su disposición es la adecuada.
Los procesos de transformación son el núcleo indispensable de todo proceso productivo.
Dentro de los procesos de Transformación, existen procesos especiales que son imposibles de controlar sin eliminar una característica indispensable del producto. En este caso, en lugar de controlarse dicha característica, lo que es necesario hacer es validar el proceso. Un caso típico de un proceso especial es la esterilización, ya que si uno abre el producto estéril para verificar su esterilización, el producto en sí ya deja de estar estéril.
- Procesos de Control: los procesos de control son todos los procesos donde a través de la comparación del producto semielaborado ó elaborado con un standard, se decide si dicho producto está apto para pasar al siguiente proceso ó para ser liberado como producto terminado al mercado. Si bien en si los procesos de control no aportan valor intrinsecamente, ya que un producto es apto o no independientemente de haber pasado por un control, estos procesos me sirven para segregar los productos que no estén aptos y evitar potenciales problemas.
Muchas veces los procesos de control surgen del último análisis del proyecto, el análisis de riesgo, ya que en este punto se identifican los posibles peligros y riesgos que puedan haber, y por lo tanto se decide implementar controles para evitarlos.
En otros casos, los procesos de transformación y control se hayan combinados, este es el caso de las inspecciones visuales ó controles durante el ensamblado.
- Procesos de Transporte: Los procesos de transporte cambian la ubicación ú orientación de las materias primas y productos semielaborados ó elaborados. Esto permite que dichas materias primas ó productos se encuentren disponibles para el siguiente proceso de una manera adecuada en cuanto a su disponibilidad en el lugar y momento.
Los procesos de transporte pueden estar integrados a otros procesos, este es el caso de cintas trasportadoras en una línea de montaje ó los tornillos sin fin, ó pueden ser independientes como es el caso de zorras, carretillas ó apiladores. También pueden ser aprovechados para realizar tareas como son el enfriado de productos ó el secado de pegamento.
- Procesos de Almacenaje: Los procesos de almacenaje surgen como necesidad para equilibrar los distintos procesos y permite garantizar el suministro continuo y oportuno de los materiales y medios de producción requeridos para asegurar la producción de forma ininterrumpida
El almacenaje puede ser tanto para equilibrar los flujos con el entorno, tal es el caso de los almacenes de materias primas y productos terminados, como el flujo interno, tal es el caso de los stocks de mercadería en curso.
Estos también pueden ser aprovechados para realizar tareas como son el enfriado de productos ó el secado de pegamento.
Si bien son prácticamente indispensable en todos los procesos, cabe destacar que el sobredimensionamiento de estos procesos provocará en el proyecto un aumento de la inversión en activo de trabajo, por lo cual serán contraproducentes desde el punto de vista de la rentabilidad del proyecto.
Desde el punto de vista de su evolución en el tiempo los procesos se clasifican en:
- Proceso Continuo: Es aquel en el que la operación no se detiene. Las diversas partes de la estructura de un proceso en general siempre está recibiendo una alimentación continua y de igual manera están lanzando un producto en forma continua. Esto permite mantener un ritmo de producción constante, y suele ser económicamente más conveniente, ya que los arranques o los paros pueden ser más costosos que en una operación contínua.
- Procesos discretos: también conocidos como batch o lotes son en los que si existen paradas del proceso entre lote y lote. Son más comunes en empresas pequeñas ya que suelen requerir menos inversión que los procesos continuos. Algunos procesos dada su naturaleza son necesariamente discontinuos, como la filtración, ya que después de determinados periodo de operación es necesario limpiar los filtros.
Es común que cuando se combinan líneas donde hay procesos continuos y discontinuos, es común utilizar dos o más equipos de proceso discontinuo con la finalidad de poder estar alimentado un proceso continuo posterior.
Para elegir cada uno de estos procesos es necesario tener en cuenta la secuencia de estos, la posibilidad de integrar procesos en una sola sección operativa, permitir un flujo equilibrado a lo largo de todo el proceso, evitar errores de mezclado e interrupciones en la producción. Si bien la mayor parte de las veces esto puede ser realizado sin problemas, muchas veces la experiencia de un tecnólogo que conozca el proceso ayuda a evitar problemas y errores comunes.
Una vez identificado el proceso que se desea modelar, hay que:
- Identificar y definir las etapas del proceso que se deben realizar en un orden específico.
- Determinar en un orden específico las operaciones que conforman cada etapa.
- Establecer las acciones que se deben desarrollar para completar cada operación.
A continuación se muestra un ejemplo:
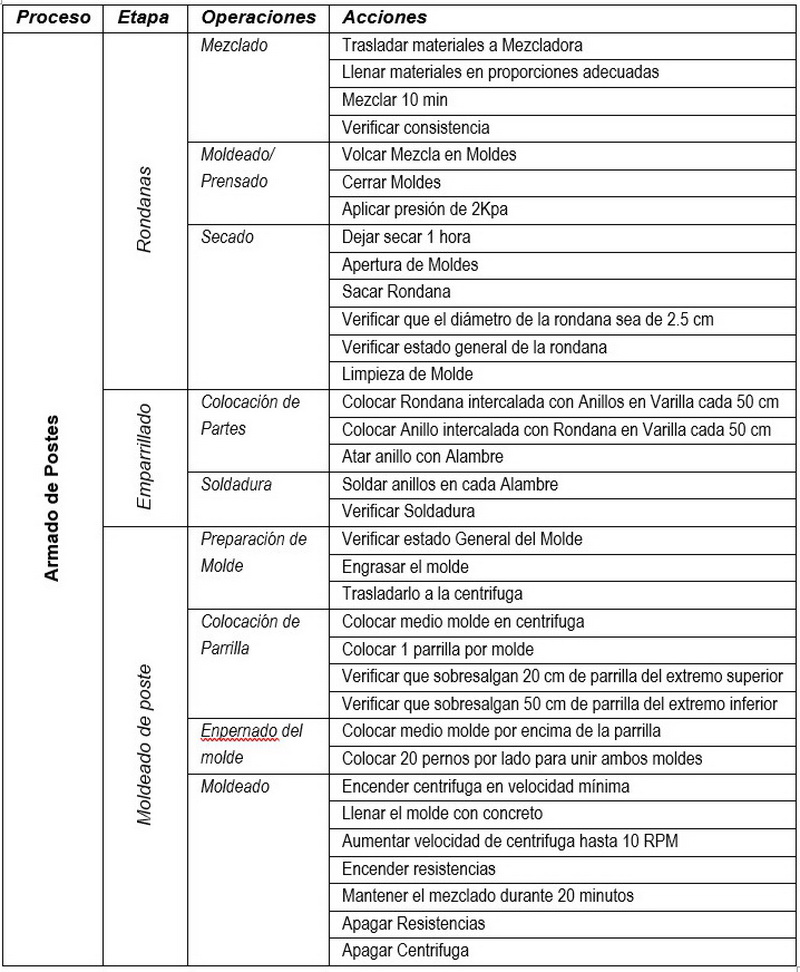
Una vez definidos las Procesos, etapas, Operaciones y acciones, se debe definir el tipo de planta que se desea montar ó desarrollar.
Tipos de Plantas
Plantas Monoproducto

Se agrupan las etapas/operaciones/acciones consecutivas que puedan realizarse de manera conjunta en una sección operativa que se numera ó nombra para poder identificarla, de cada sección operativa saldrá un semielaborado que también habrá que numerar ó nombrar para poder identificarlo unívocamente, excepto de la última sección operativa por la que saldrá el producto terminado. Para cada sección operativa, habrá que identificar por cada unidad de salida la cantidad necesaria de materias primas, materiales, desperdicios recuperables, desperdicios no recuperables.
Plantas Multiproducto

Para el caso de las plantas multiproducto, donde todos los productos siguen la misma secuencia a través de todas las etapas de producción, el proceso de armado de la línea es similar, solo que se hace este proceso independiente para cada producto, para luego eventualmente si se desea hacer un balance de materiales total, simplemente hay que sumar los requerimientos para cada uno de los productos. Esto puede ser conveniente para mostrar el resultado total, pero más adelante con el objetivo de balancear la línea, será necesario contar con todos los flujos por separado para poder realizar los cálculos.
Plantas Multipropósitos
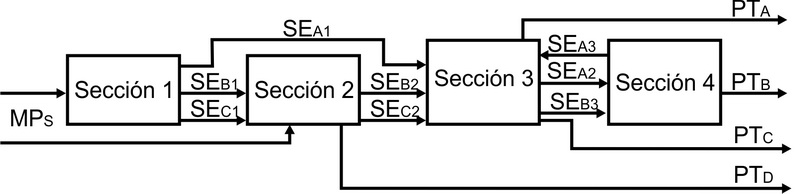
Como puede verse, las plantas multipropósitos le agregan un grado adicional de complejidad, ya que los procesos para los mismos productos no siguen la misma secuencia. Nuevamente la técnica es la misma que para la planta multiproductos, son que en este caso, además de adicionar los requerimientos de cada producto, también es necesario adicionar los requerimientos para cada sección operativa.
Diseño de Procesos Complejos
Cuando los procesos son lineales y continuos, los procesos son fáciles de diseñar, pero cuando se empiezan a incluir etapas discontinuas ó variaciones en el proceso realizado a cada producto, el diseño del proceso puede volverse desafiante.
En estos casos, se recomienda seguir la siguiente técnica:
- Diseñar el Proceso como si fuese Continuo
- Identificación de Equipos Discontinuos: Los equipos discontinuos ó proceso batch producen cortes en las líneas continuas. Para evitar esto, suelen utilizarse dos ó más equipos discontinuos en paralelo para lograr evitar interrupciones, disminuye las necesidades de almacenamiento intermedios.
- Identificación de Equipos Multitarea: Utilizar equipos multitareas permite aprovechar las capacidades ociosas, hacer un uso eficiente de recursos y generar una producción flexible y Optimizada. Sin embargo, los equipos ó secciones operativas multitareas suelen ser una pesadilla desde el punto de vista de la programación de la producción una vez puesta en marcha la empresa. Si el proceso es continuo, los requerimientos se tratan como se explicó anteriormente en lo que hace a plantas multipropósitos, si el trabajo es por lote es necesario tener en cuenta que los lotes de los diversos flujos, no necesariamente son iguales, por lo cual el equipo multitarea se deberá dimensionar para el lote de mayor tamaño.
- Determinar la necesidad de Etapas Paralelas: Las etapas paralelas pueden surgir o por la necesidad de realizar distintos tratamientos a distintos productos ó por la necesidad de balancear equipos discontinuos con equipos continuos.
También se usan etapas paralelas para optimizar el uso de ciertas secciones operativas de larga duración y minimizar los tiempos ociosos de los equipos.
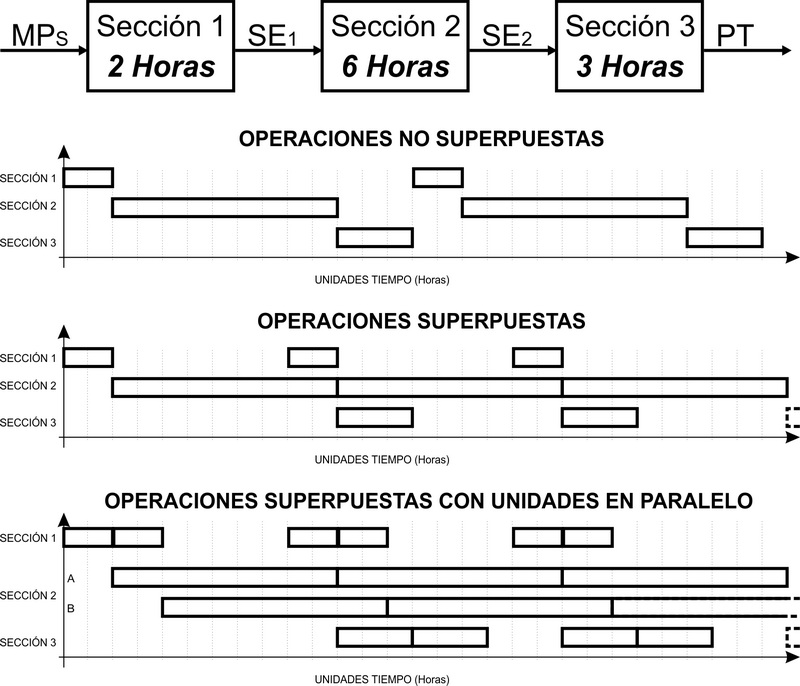
Como puede observarse de los gráficos anteriores, la optimización de la programación superponiendo actividades, lleva a un aumento en la capacidad de aproximadamente del 50%, y al utilizar etapas paralelas lleva a un aumento en la capacidad de más del 150% con respecto a la primera alternativa casi un 80% sobre la segunda alternativa, haciendo una inversión solamente en una de las secciones operativas.
Esto también aumenta el aprovechamiento seccional en la primera y tercera sección del 21% al 43%. Y si se agregara una tercera etapa paralela en la segunda sección, los aprovechamientos seccionales subirían aún más.
5. Cuantificar el Almacenamiento Intermedio:
Los procesos por lotes requieren necesariamente contar con almacenamientos intermedios.
Cuando se consideran almacenamientos intermedios, hay que considerar la naturaleza de los semielaborados, o sea que esto permitan ser almacenados el tiempo necesario, la inversión requerida en los equipos para almacenarlo, la disponibilidad del lugar físico para ese almacenamiento, así como también el valor de la mercadería semielaborada en sí. Si el tipo de semielaborado lo permite y la inversión en el equipo de almacenamiento y lugar físico es bajo, siempre es conveniente hacer uso de almacenamientos intermedios para optimizar el aprovechamiento de las máquinas operativas.
Hay que considerar que si bien el almacenamiento intermedio permite balancear procesos por lotes, evitando la interrupción de los procesos, también puede provocar demoras por lotes fuera de especificación.
Especificaciones de Medios de Fabricación y Control
Ya teniendo balanceado el proceso, es necesario determinar los equipos específicos de Fabricación y Control.
Para cada sección operativa, hay que determinar ahora equipos y máquinas específicas, existe una gran cantidad de alternativas de fabricantes de máquinas y describirlos todos es imposible.
Si es importante dar algunos lineamientos para selección las máquinas y equipos.
Para empezar hablamos de una línea Hómogenea cuando las máquinas son del mismo fabricante. Esto generalmente facilita los procesos de balanceo de líneas, disminuyendo los stocks intermedios y facilita los procesos de mantenimiento al referenciarlos a un solo proveedor.
A la hora de seleccionar los medios de fabricación y control, no hay reglas generales para la toma de decisión.
En algunos casos se decide seleccionar equipos donde la capacidad del equipo exceda un poco las necesidades de producción, con lo cual se contará con un solo equipo por sección operativa. Esto se debe a que un solo equipo grande generalmente es más ventajoso desde el punto de vista del retorno de la inversión. Sin embargo, en este punto todavía no se ha desarrollado el dimensionamiento económico, por lo cual esto no se puede verificar.
Cuando los equipos requieren muchas paradas de máquina para cambio de matrices o limpieza por ejemplo, es común elegir equipos con menos capacidad que permitan realizar estas paradas mientras se sigue utilizando otro de los equipos.
Cuando la inversión está restringida, es común elegir procesos manuales para las secciones operativas, ya que los medios de fabricación y control en estos casos son comparativamente más baratos. La desventaja en estos casos (más allá de las explicadas anteriormente) es la variabilidad de la calidad y tiempos entre persona y personas, y para una misma persona a lo largo de la jornada laboral.
No obstante todo esto, lo importante en este punto es elegir una tecnología adecuada para los procesos requeridos, y eventualmente si se tiene dudas de haber elegido la mejor alternativa, esto se suele analizar en el dimensionamiento de la incertidumbre y gestión del riesgo (AGREGAR LINK)
Para cada medio de fabricación y control, será necesario contar con una hoja técnica del mismo, y de ser posible con el manual respectivo. De esa hoja técnica surgirán datos a considerarse en este momento, tal como la compatibilidad con las materias primas y materiales que se van a utilizar, las capacidades teóricas por unidad de tiempo y datos a ser utilizados más adelante en el proyecto, tales como las dimensiones, los consumos de servicios, la frecuencia de mantenimiento.
Hay otras informaciones que generalmente no se encuentran en las hojas técnicas y es necesario preguntar al fabricante o proveedor para poder utilizarlos en el proyecto:
- rendimiento operativo (para poder calcular la capacidad real),
- requisitos especiales para la instalación (por ejemplo de un contrapiso)
- Embalado (para poder organizar su armado),
- Plazos de construcción y entrega (para programarlos en el cronograma de ejecución)
- datos económicos (precio, formas de pagos)
- Condiciones de Guardado
- Frecuencia y costo de Calibrado (medios de Control)
- Conexiones a los servicios (tipo y diámetro de cañerias, tipo de enchufes)
Una vez que se hayan determinado las máquinas especificas, puede ser que sean necesario readecuar los procesos, además de adaptar el proceso al espacio físico disponible más adelante cuando se desarrolle el anteproyecto de Planta.
Un aspecto indispensable a determinar para cada sección operativa es, dado las tecnologías y maquinas seleccionadas, los flujos de ingresos (materias primas, materiales, insumos) y de egresos (productos, subproductos, desperdicios). Esto surge también de la información suministrada ó consultada con el proveedor. Por lo que para cada sección operativa, se tendrá que conseguir esta información, que será utilizada más adelante en el balanceo de Materiales.
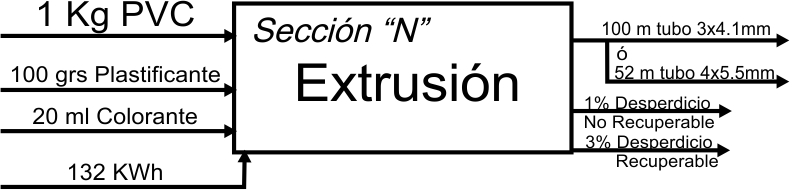
Representación Final de los procesos
Una vez que se han determinado las secciones operativas y las máquinas, en necesario volver a graficar los procesos. Para esto es común utilizar cursogramas.
Los cursogramas son similares a los diagramas de flujo, pero generalmente siguen normas más estrictas para su construcción, y suelen ofrecer mucha más información que los diagramas de flujo. Existen distintos tipos de Cursogramas, a continuación se muestran ejemplos de los más comunes. Para más información de las construcción de los diversos tipos de cursogramas, se desarrollará un anexo.
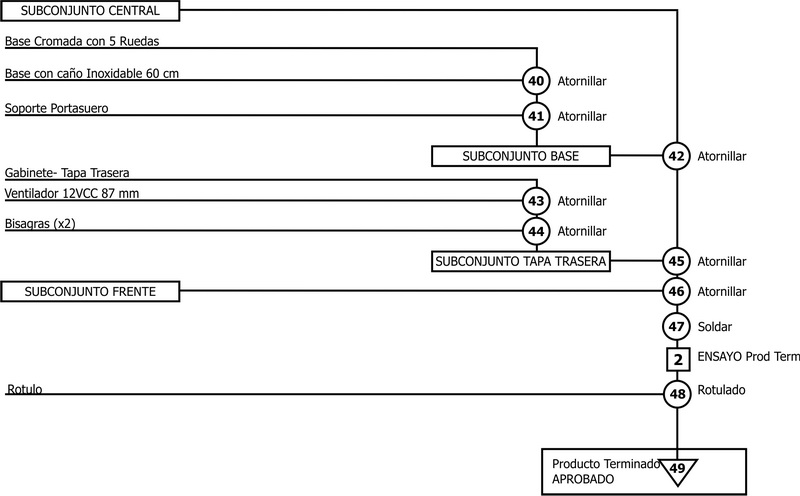
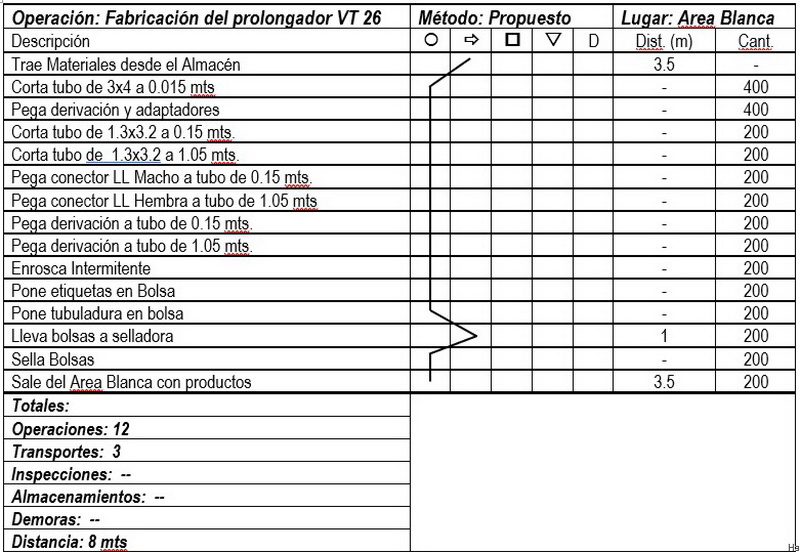
Cálculo de las Maquinas y Instalaciones
Cálculo de Evolución de las Mercaderías
Determinación del Personal
Elaboración de Anteproyecto de Planta
Generación de Cronograma de Ejecución
Una vez desarrollados todos los aspectos materiales que tienen que ver con la puesta en funcionamiento de la planta del proyecto, el último paso es tratar de poner las actividades necesarias para su realización en un marco temporal.
A este marco temporal se lo denomina cronograma de ejecución.
El cronograma de ejecución es un diagrama calendario (ya que en uno de sus ejes se coloca el tiempo en divisiones superiores al día), más en particular un diagrama de Gantt ya que en el Cronograma de ejecución es importante que las diversas actividades se encuentren vinculadas unas con otras.
En el cronograma de ejecución, las actividades que se ponen son orientadas específicamente a un proyecto, y primordialmente concentradas en el período de instalación ya que es importante optimizar estos tiempos para mejorar eventualmente la rentabilidad del inversor al ajustar los plazos para las inversiones que se realizan.
A continuación se muestra un cronograma de ejecución acerca del cual se irán haciendo las observaciones para su construcción:
Descripción temporal, Etapas y Momentos del Cronograma de Ejecución
Como puede apreciarse en el eje horizontal del cronograma, existen algunos aspectos constructivos específicos en el Cronograma de Ejecución.
Desde el punto de vista de las unidades de medidas, las divisiones menores suelen estar en semanas ó meses, ya que esto permitirá que el cronograma de ejecución entre fácilmente en una hoja. Si se quisieran hacer divisiones en días, esto provocaría para la mayoría de los proyectos (que tardan al menos 4-5 meses) una cantidad excesiva de divisiones, que no son fáciles de dibujar y sin una utilidad desde el punto de vista del control del proyecto.
Para el caso de algunas actividades particulares, como por ejemplo la implementación de sistemas informáticos críticos, es común que para esa actividad se despliegue un cronograma específico anexo con las divisiones en días e incluso horas.
En cuanto a las divisiones mayores, estas se colocan en las unidades que vayan a ser empleadas eventualmente para la evaluación del proyecto en su vida útil. Generalmente esto es en años, lo que me permite calcular por ejemplo una tasa interna de retorno, ó una rentabilidad ó unas utilidades anuales. En casos particulares se pueden usar trimestres, como por ejemplo en empresas que coticen en bolsa y que tengan que presentar balances trimestrales, en bimestres en empresas concursadas donde el síndico pida información cada dos meses, ó en cualquier otra que se requiera.
Existen tres etapas en todo diagrama de ejecución, la Preinversión que ocurre desde la toma de decisión de empezar a analizar metódicamente el proyecto hasta que se toma la decisión de Ejecutar el proyecto, la Instalación que va desde que se decide ejecutar el proyecto hasta que se inicia la producción con intención a la comercialización y la Explotación que va desde el fin de la instalación hasta el fin del período de análisis. De esta última etapa, generalmente solo se colocan en el diagrama los primeros meses que es donde ocurre el período de puesta en marcha y, en caso que sean necesario también se pueden describir actividades para la instalación de nueva etapa del proyecto (si es que el mismo se hace en varias etapas).
Como convención se toma como el Momento 0 el momento que separa la instalación de la explotación del proyecto. En la mayoría de los proyectos este momento es fácilmente distinguible ya que la fabricación y la comercialización inicial prácticamente al unísono, mientras que en otros proyectos tales como las explotaciones forestales ó los proyectos inmobiliarios pueden pasar años hasta que se comercialice los productos. En estos casos habrá que considerar la recomendación de acuerdo a los usos y costumbres para esa actividad.
Los años anteriores al momento 0 se considerarán como años Negativos y los años posteriores como años positivos. Cabe recordar que para todo el proyecto, los años de utilizan de manera genérica (Año -2, Año -1, Año 1, Año 2, etc.) ya que no se tiene la fecha especifica donde el inversor se decida a iniciar el proyecto, tal como se hizo en el plan de ventas y durante todo el dimensionamiento físico (y se seguirá en el resto de los dimensionamiento).
Etapa de Preinversión: Conceptos y Tareas
La etapa de preinversión comienza con el encargo por parte del patrocinador de la elaboración del proyecto y finaliza con la decisión de iniciar la ejecución del proyecto de inversión.
Estudio de prefactibilidad y factibilidad: Esta tarea incluye todos los análisis y documentos que son necesarios para elaborar y formular el proyecto.
En el caso de empresas en marcha, también incluyen una descripción de la situación actual y los planes de la empresa para poder contrastarlos con el impacto en los resultados que tendría el proyecto. El resultado de esta etapa es el documento que conocemos como “Proyecto de Inversión”.
Evaluación externa y aprobación del proyecto de inversión: Una vez confeccionado el documento citado previamente, es necesario que se envíe a todos aquellos que tengan que aprobar el proyecto: los inversores que serán quienes pondrán la parte principal de los aportes necesarios, los financistas (bancos) que necesitan la información para acordar los créditos en base a las proyecciones, y los entes gubernamentales de los cuales puede depender algún beneficio que tenga previsto el proyecto. Esta actividad puede llevar desde unas semanas hasta un tiempo indefinido que culminará con la toma de decisión del inversor de ejecutar el proyecto.
Etapa de Instalación: Conceptos y Tareas
En esta etapa es donde se realiza el mayor desarrollo de actividades y donde es indispensables optimizar el cálculo de los tiempos ya que cualquier demora por la mala programación llevaría a postergar el inicio de las actividades comerciales y por lo tanto los ingresos del proyecto.
Existen varios tipos de actividades, desde las vinculadas a la organización de la empresa, a la construcción y puesta a punto de Edificios e instalaciones, aquellas vinculadas a las máquinas, a la adquisición de materias primas y materiales y al personal. Todas estas son importantes y muchas veces se vinculan entre ellas, desde las más evidentes como la necesidad de construir el edificio y las instalaciones de manera simultánea, hasta algunas menos evidentes como contar con materias primas para hacer pruebas con las máquinas adquiridas.
Actividades de Organización de la empresa
Decisión de Ejecutar el Proyecto: Está es la actividad que dispara el proceso de instalación. En los cronogramas de ejecución se la suele indicar como una actividad instantánea, ya que es un proceso lógico y no físico.
Constitución y Organización de la empresa: Una vez tomada la decisión de ejecutar el proyecto, la primera actividades constituir la empresa de manera legal e inscribirla en el registro público correspondiente (la IGJ en Argentina) así como también inscribirla en la/s autoridad/es fiscal/es (AFIP, AGIP, ARBA, etc). Esto permitirá que todos las facturas y recibos que se hagan, ya se puedan hacer a nombre de la empresa, así como también se podrá empezar a trabajar contractualmente a nombre de la empresa.
Selección y contratación de Responsables de la Instalación: Cuando el proyecto no puede ser llevado a cabo por el inversor, es necesario que este contrate a alguien que se encargue de todas las actividades durante el período de Instalación. La persona responsable de la instalación no necesariamente será la persona responsable de la empresa que surja del proyecto, ya que ambas actividades pueden requerir habilidades diferentes. El ejemplo más claro es un Arquitecto que se encarga de la construcción de un edificio, el cual una vez listo será administrado por un administrador de consorcio. En otras ocasiones si puede ser la misma persona que se haga cargo luego de la empresa ó de una parte de la misma, por ejemplo la gerencia de producción. Esto dependerá de cada proyecto.
Esta persona será la responsable de ejecutar y controlar la instalación del proyecto, y en caso de necesitarlo tomará la decisión de contratar ó subcontratar actividades específicas o menores a lo largo del proyecto.
Alquiler o compra de Oficinas: La persona que se encarga de la instalación puede llegar a necesitar algún lugar físico para llevar a cabo sus tareas. Aunque cada vez más la mayoría de las actividades pueden hacerse de manera remota y digital, siempre será necesario contar con un domicilio donde llegue toda la información y notificaciones oficiales. Muchas veces alcanza con contar con un apartado postal para las notificaciones.
Trámites de habilitación de ante organismos Gubernamentales: Depende de la actividad que realice la empresa, es necesario contar con una habilitación previa para poder empezar a fabricar, importar, comercializar algunos productos o brindar ciertos servicios. Muchas de estas habilitaciones se han ido digitalizando y suelen ser inmediatas, pero otras suelen llevar mucho tiempo, incluso a veces años. Es importante tener en cuenta que a veces, algunas de las primeras actividades que se realizan durante la instalación están vinculadas a estos trámites, ya que sino se corre el riesgo de estar meses ó años con una planta instalada pero sin poder utilizarla.
Elaboración de presupuestos definitivos para Control de Gestión: A pesar de que en el proyecto de inversión ya se contaba con presupuestos de maquinas, equipos, edificios y construcción elaborados en el dimensionamiento económico, es necesario verificar estos presupuestos y actualizarlos para verificar que siguen estando vigentes. Esta actividad es muy común en lo que respecta a los terrenos ó edificios, ya que si bien se pudieron haber usado para el proyecto algunos que estaban disponibles en ese momento, estos pueden haber sido vendidos entre que se hizo el proyecto y se tomó la decisión.
Liquidación de Créditos: El momento de la liquidación de créditos se define en el dimensionamiento financiero (más adelante en el proyecto), por lo que cuando se confecciona inicialmente el cronograma de ejecución este dato no se haya disponible. Hay que recordar por lo tanto que, una vez que se definan los créditos y cuando se liquidan, habrá que actualizar el cronograma para incluir esta información.
Actividades vinculadas a Edificios e Instalaciones
Compra y posesión del terreno: El tiempo de esta actividad incluyen, además del hecho formal de la compra que es relativamente corto, el tiempo que se tarda en poner en condiciones dicho terreno, puede ser tanto la limpieza y el desmonte si se trata de un terreno sin mejoras, como la demolición de las edificaciones en el mismo que no sean necesarias.
Elaboración de Proyecto definitivo del Edificio y Obras complementarias y del proyecto definitivo de las instalaciones industriales: Los proyectos definitivos son necesarios desde el punto de vista práctico para poder construir los edificios e instalaciones de manera rápida, coordinada y sin contratiempos pero desde el punto de vista formal también pueden ser necesarios para la actividad siguiente es la tramitación de la aprobación para edificar.
Tramitación de Aprobación de Permisos para edificar: Lamentablemente, en muchas jurisdicciones el tiempo necesario para la aprobación de permisos para construir puede demorarse largamente, vinculados a la poca adecuación de los organismos públicos ó las empresas proveedoras de servicios para el volumen de tareas a realizar, o porque se requieren multiplicidad de pasos burocráticos y administrativos a distintos niveles. Una solución para esto muchas veces es comprar edificios previamente habilitados para la actividad que se desea realizar.
Construcción de Edificios, Obras Complementarias e Instalaciones Industriales: Suele ser la actividad que más recursos monetarios, de personal y de materiales necesita en el período de instalación, así como también un conocimiento específico de como coordinar y realizar las distintas etapas, por lo cual en general se delega esta actividad en un Arquitecto ó un Ingeniero Civil. La única precaución a tener en cuenta es que muchas veces hace falta coordinar estas actividades con la de la instalación de las máquinas y equipos, bien porque se necesita instalar las máquinas una vez ya realizado determinado trabajo (por ejemplo el piso ó contar con el techo para que no queden a la intemperie) ó porque por el tamaño de las máquinas es necesario construir el edificio después de instalar la maquinaria.
Habilitaciones definitivas: Nuevamente aquí aparece los organismos gubernamentales ó las empresas de servicios que necesitan hacer un control final de las instalaciones para habilitar la planta. Esto también puede provocar demoras adicionales, con lo cual muchas veces se solicita la inspección definitiva sin haber terminado la obra.
Actividades vinculadas a Maquinarias
Maquinaria a Importar: La maquinaria a importar implica una gran cantidad de procesos desde la compra, construcción, embarque, transporte Marítimo, despacho a Plaza, transporte a fábrica y Montaje de la dicha maquinaria. Todo este proceso es secuencial, y como en cualquier diagrama de Gantt, la planificación de dichas actividades comienza por la última en el tiempo que es el montaje de dicha maquinaria. El montaje de esa maquinaria tiene que estar listo disponible para el inicio de la prueba de las mismas. A partir de ese momento, se van hilvanando hacia atrás en el tiempo todas las actividades.
Si la maquinaria se trata de máquinas sencillas y fáciles de construir por parte del fabricante, todo este proceso puede llevar un par de meses: por ejemplo que el transporte marítimo desde China o Europa lleva alrededor de 20 o 30 días, y el despacho a plaza y transporte a fábrica puede llevar unos 10 o 15 días.
Pero para máquinas hechas a medida, que requieren gran cantidad de especificaciones por parte del cliente, máquinas grandes o con gran demanda, muchas veces los tiempos antes del embarque pueden llevar muchos meses o hasta más de un año, para luego tener que transportarse, despacharse a plaza e instalarse. Esto hace que, en algunos proyectos, la primera actividad que tenga que hacer el responsable de la instalación es colocar la orden de compra de la maquinaria para lograr que empiecen a correr todos estos tiempos lo antes posible.
Maquinaria Nacional: Si bien las observaciones realizadas para las maquinarias importadas corren también para las máquinas nacionales, los procesos de compra, transporte y montaje suelen ser más sencillos ya que se cuenta con un apoyo local con experiencia previa para estas actividades. Además que no son necesario el transporte marítimo ni el despacho a plaza.
Prueba en vacío de la Maquinaria: Una vez que se cuenta con toda la maquinaria disponible en la planta, es común realizar una prueba en vacío para verificar que todas se encuentran en un estado adecuado de funcionamiento. Una alternativa a esta actividad suele ser la realización de un primer lote de muestra para poder evaluarlo, enviarlo a analizar y poder utilizar esos datos para habilitar el producto.
Actividades vinculadas al Personal
Selección, Contratación y Capacitación de Personal: Aquí se está hablando del personal que va a estar en la empresa una vez iniciada la explotación. En muchos casos es importante contar con alguna parte del personal presente cuando se hace la instalación y prueba en vacío de la maquinaria, para que sepa su funcionamiento y puedan ser capacitados por los fabricantes de las máquinas, o se necesita del personal para poder recibir los primeros lotes de materias primas. Si no se tienen esta necesidades, muchas veces alcanza con iniciar este proceso un mes antes de la finalización de la instalación de la planta.
Actividades vinculadas a la Mercadería
Unas semanas (o meses dependiendo de la complejidad) antes de comenzar el periodo de explotación del proyecto, se realiza la Selección definitiva de Proveedores para poder realizar una Compra Inicial de Materias Primas y Materiales. Esta compra inicial debe coincidir con la confección del lote de prueba, o bien es la última actividad del período de instalación, ya que con la disponibilidad de la materia prima se puede iniciar la producción con la intención de vender, que marca el momento “0” que es el inicio del plan de explotación.
Etapa de Explotación: Conceptos y Tareas
La etapa de explotación inicia con la incorporación de la materia prima en el área de operaciones en el caso de producciones industriales, cuando se abre al público por primera vez en comercios ó cuando se empieza a contactar a los clientes en el caso de las empresas de servicios.
Como se dijo anteriormente de esta etapa, generalmente solo se colocan en el diagrama los primeros meses que es donde ocurre el período de puesta en marcha (tiempo que se tarda en alcanzar el diseño del producto y del proceso).