Diferencia entre revisiones de «Dimensionamiento Técnico ó Fisico»
(→Agua) |
|||
Línea 967: | Línea 967: | ||
Otra solución en el caso de algunos procesos o líneas en los que es posible es contar con una dotación menor de empleados (o máquinas) suficientes para cubrir la necesidad del menor programa de producción, y el exceso en temporada alta contratarlo en empresas tercerizadas. | Otra solución en el caso de algunos procesos o líneas en los que es posible es contar con una dotación menor de empleados (o máquinas) suficientes para cubrir la necesidad del menor programa de producción, y el exceso en temporada alta contratarlo en empresas tercerizadas. | ||
=== | === Evolución de las Mercaderías === | ||
Ya determinadas las secciones operativas y la cantidad de máquinas ó puestos de trabajo en cada uno de estos, es necesario analizar como evolucionan las mercaderías presentes en el proyecto en sus distintos estados, tanto desde el punto de vista de los flujos como desde el punto de vista de los stocks. | |||
Para comenzar es importante diferenciar dos estados distintos desde el punto de vista de los consumos de mercaderías, el estado de régimen y el Período de Puesta en Marcha. Recordemos las definiciones de cada uno de estos: | |||
'''Período de Puesta en Marcha:''' Es el tiempo que necesario para alcanzar el diseño del producto y del proceso, tanto en calidad como costo. | |||
Durante este período ocurren 3 impactos: | |||
* El nivel de producción en menor | |||
* El nivel de desperdicios es proporcionalmente mayor | |||
* Hay un aumento en los desembolsos asociados a gastos variables por la necesidad de aprendizaje y puesta en ritmo del personal y las máquinas. | |||
'''Estado de Régimen:''' Es el período en el que se produce de acuerdo con lo pretendido en el plan de producción y con la calidad pretendida en cuanto al producto y proceso, sin pérdidas asociadas a la falta de experiencia ó falta de puesta a punto del proceso. | |||
Debido a que el estado de régimen es el estado normal al que se debería estar fabricando al final de cualquier plan ó programa, siempre se realizan los cálculos en estado de régimen y luego se estima la producción en el período de puesta en marcha. | |||
Como durante el balanceo de línea, es necesario separar el plan de producción en distintos programas para eventualmente llevar estos datos a períodos anuales sumando los distintos programas que pasan en un año. (PONER LINK). | |||
Como en el caso del balanceo de materiales, Explicaremos a continuación la evolución de las mercaderías para el caso más simple de un proceso con monoproducto y pocos insumos, con planes y programas anuales homogéneos y sin incrementos en las ventas a partir del año 2. | |||
El desarrollo de la evolución de las mercaderías de materiales para una planta multiproducto ó para el caso del uso de múltiples insumos, es explicado en un apartado diferente, (PONER LINK) así como también la evolución de las mercaderías para el caso de variaciones en la producción (PONER LINK) | |||
==== Cuadro De Evolución De Las Mercaderías ==== | |||
[[Archivo:CeMerc1.jpg|centro|miniaturadeimagen|800x800px|EVOLUCION DE LAS MERCADERIAS- Cuadro de evolución Anual de las Mercaderías]] | |||
El cuadro de evolución de las mercaderías busca mostrar la evolución en cantidades de todos los posibles estadios de las mercaderías. | |||
Si bien a simple vista parece simple, es necesario considerar dos aspectos fundamentales: | |||
* No olvidarse de identificar las unidades de cada uno de los estados de las mercaderías | |||
* Entender que mientras para los rubros que muestran flujos tales como Ventas, Producción, Desperdicios No Recuperables, Consumo y compras de Materias primas (destacados en Negrita en el cuadro) los valores indicados se tratan de los consumos anuales (ó del período si este no fuera anual) mientras que para los stocks de materias primas, mercadería en curso y producto terminado (en cursiva en el cuadro) los valores indicados se trata de la cantidad de dichos stocks al final del año ó del período si este no fuera anual. | |||
Volvamos a recordar en este punto, que si bien es posible hacer cálculos y cuadros con periodos más cortos o más largos que un año, en realidad la ventaja de generar cuadros anuales es poder eventualmente tener los datos agrupados de manera de generar flujos de cajas anuales, lo que permite obtener tasas de rentabilidad anuales, útiles para la evaluación del proyecto. | |||
En el caso de proyectos donde no se observen crecimiento en algunos períodos, es común simplificar este cuadro, agrupando los años que tienen los mismos valores. | |||
[[Archivo:CeMerc2.jpg|centro|miniaturadeimagen|800x800px|EVOLUCION DE LAS MERCADERIAS- Cuadro de evolución de las Mercaderías Agrupados por períodos]] | |||
=== Determinación del Personal === | === Determinación del Personal === |
Revisión del 21:32 14 mar 2025
Introducción y Objetivos
El dimensionamiento técnico ó físico es probablemente el núcleo de todo proyecto y por eso es el que requiere el mayor nivel de trabajo. Debido a esta cantidad y complejidad del trabajo necesario es que la mayoría de las veces el dimensionamiento técnico es subanalizado. Aquí se dan dos posibles alternativas del porque de este subanálisis:
- Demasiada Importancia al dimensionamiento Comercial y Económico: La mayoría de los cursos dados sobre evaluación de proyectos se concentran en poder calcular el potencial de ventas y los resultados esperados económicos para poder determinar un flujo de caja . Esto es generalmente llamado plan de negocios ó business plan. Esto se enseña en la infinidad de cursos de apoyo a emprendedores, en todos los masters en negocios de todas las escuelas y en las carreras de administración de empresas. Y es entendible. Es muy lindo ver cuanto se puede vender, que formidable que nos compren lo que se nos ocurrió, como nos diferenciaremos en un mercado específico y como eso nos generará gran cantidad de dinero. Luego hacen unas cuantas cuentas sobre estimación de inversiones y costos y ¡voila! ya tenemos un negocio armado. Y si ponemos el doble de dinero la ganancia se duplica! Pero lo que no ven en estos casos es que las diferenciaciones comerciales son fáciles de duplicar, fíjense sino en la etapa inicial de Internet, donde una buena idea era inmediatamente replicada múltiples veces en cuestión de días, o cuando uno pone un local exitoso, en unos meses alguien puede poner un negocio similar a solo unos metros de distancia. Lo otro que falla en ver esta perspectiva es que la cuantificación económica de un proyecto puede solo surgir de haber analizado los recursos físicos necesarios. Los costos indirectos no siempre son fijos, las inversiones en stocks no se mantienen constantes con distintos volúmenes de ventas, no se puede multiplicar alegremente las ventas si las máquinas e instalaciones no dan abasto. Por eso una elaboración económica que no se encuentra basada en un sólido análisis técnico tiene tantas posibilidades de triunfar como una estimación dada por un oráculo.
- Demasiada Confianza en la capacidad técnica del dueño del proyecto: Muchas veces quien encara un proyecto es alguien que comprende la parte técnica del proyecto, es un mecánico, un cocinero, un ingeniero, ó trabajo toda su vida en una empresa textil, un criadero de animales o sabe programar desde los 12 años. Entonces es comprensible y hasta razonable que esta persona sienta que no necesita realizar un dimensionamiento técnico. Y de hecho sus estimaciones suelen ser completamente válidas para calcular las necesidades de instalaciones, insumos y máquinas del proyecto. En verdad el trabajo en el dimensionamiento técnico puede ser duro y llevar tiempo pero la solución no es dejarlo de lado, sino eventualmente simplificarlo, sabiendo que se han tomado estimaciones, pero con una estructura adecuada que permita posteriormente mejorar y profundizar el análisis para obtener resultados más exactos, tanto para pedir préstamos a los bancos como para permitir que otras personas participen y entiendan la totalidad del proyecto. Es por esta razón que al final de la elaboración de las actividades necesarias para cumplir cada objetivo, se mostrará la manera de simplificarlas para poder realizarlas rápidamente, pero de manera adecuada.
El trabajo a realizar en el dimensionamiento técnico incluye un amplio espectro de aspectos por lo que los conocimientos y técnicas necesarias son igualmente amplias y variadas. El orden en el que se van desarrollando los distintos elementos de esta etapa, tiene una lógica de cascada donde es necesario cumplir uno para poder ir avanzando en los restantes. Dichos elementos son:
- Determinación del Tamaño y la Localización
- Determinación Técnica del producto
- Determinación de los procesos
- Determinación de las Mercaderías
- Determinación de la Organización y el Personal
- Elaboración del Anteproyecto de Planta
- Generación del Cronograma de Ejecución
Para mostrar la integración entre todas las actividades realizadas para lograr alcanzar los objetivos del dimensionamiento técnico se muestra el siguiente diagrama. Si bien es complejo, es la mejor manera de ver de manera integrada dichas actividades y entender el porque de la vinculación entre los distintos objetivos.
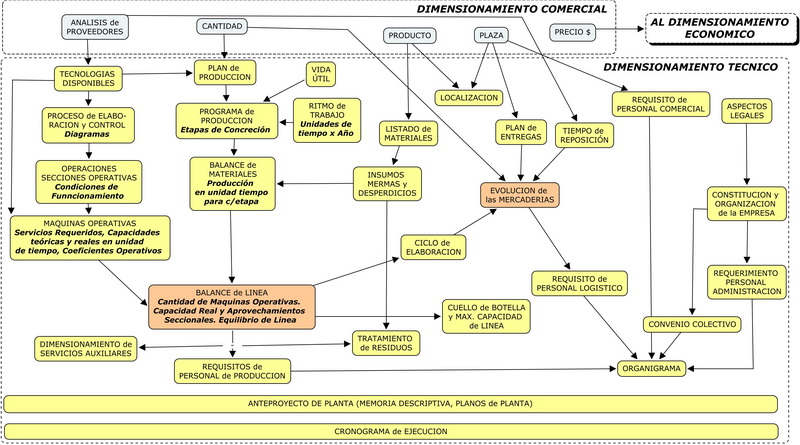
Como todos los dimensionamiento, existen luego de la etapa de Elaboración, las etapas de Formulación y Evaluación, donde presentan de manera resumida lo encontrado y se da lugar para que el inversor tome decisiones de evaluarlo.
Elaboración
Tamaño del Proyecto
Uno de los primeros temas a tratar dentro del marco del dimensionamiento técnico es la determinación del tamaño del proyecto. El tamaño de un proyecto está asociado a múltiples factores, algunos surgidos de la internalización de objetivos del inversor y otros surgidos del propio análisis en el proyecto, entre ellos del estudio de mercado que determina la demanda a satisfacer, las escalas de producción que son posibles adoptar de acuerdo a las tecnologías disponibles, las restricciones legales y sociales que pudieran haber y los recursos de financiación para el proyecto, tanto la disponibilidad de aporte de por parte del inversor como los créditos disponibles en el mercado.
La necesidad de definir el tamaño en este punto tan temprano del dimensionamiento físico está asociado a poder estimar por un lado aspectos que hacen a la optimización de la localización, y por otro lado la factibilidad de cumplir con los niveles de calidad requeridos para el producto.
Obviamente es necesario tener más información para la determinación final de las máquinas e instalaciones específicas y más adelante en el proyecto se determinarán dichas máquinas e instalaciones, así como su cantidad, necesaria para llevar a cabo los distintos programas y planes de producción, pero esta primera aproximación nos sirve como principio rector del tipo de tecnología a utilizar, así como considerar la optimización de capital y eventualmente su limitación, aspectos que son necesarios considerar como objetivos a lo largo de todo el proceso técnico. Algunos de estos conceptos son explicados a continuación, mientras que otros son abordados más adelante.
Más allá de la determinación del tamaño en este punto, la optimización de sucesivos aspectos explicitados anteriormente hará que el tamaño sea uno de los aspectos que siempre se ve actualizado al final del dimensionamiento técnico.
Pero se ha usado la palabra tamaño del proyecto sin definirla, y si bien intuitivamente todos podemos darnos una idea de lo que es el tamaño de algo, cuando nos referimos a tamaño del proyecto en este punto, este tamaño no está definido por la superficie de la planta en sí (que será determinada eventualmente teniendo en cuenta todos los aspectos productivos, logísticos y de personal necesarios), sino por los niveles de producción máximo que planean alcanzarse por etapa de concreción del proyecto y por turno.
Este tamaño deberá ser suficiente como para:
- Poder cumplimentar con los planes y programas de ventas a lo largo del período de análisis
- Considerar la estacionalidad tanto de las ventas como de las compras
- Cumplir con los requisitos de impacto ambiental y legal previsto es la normativa aplicables a distintos niveles
- Permitir la optimización del aporte de Capital
Comenzaremos por este ultimo punto, que a diferencia de los demás factores, se trata de un factor deseable aunque no necesariamente obligatorios
Criterios de Optimización de Capital
Aún si no se cuenta con una restricción del capital total a aportar, es indispensable optimizar el uso de dicho capital con el fin de mejorar tanto la tasa interna de retorno como el periodo de recupero de la inversión. Recordemos que en este punto del proyecto no hemos realizado cálculos económicos, por lo que las tecnologías a adoptar no pueden compararse en función de un criterio económico de evaluación (Valor Actual Neto, Tasa interna de retorno, etc.) por lo que la optimización del Capital es una fuerza orientadora para el proyecto más que un objetivo particular. No obstante cualquier decisión tomada en este aspecto u otros a lo largo del proyecto es susceptible de ser cambiada si se encuentran razones de peso vinculadas a criterios profesionales, o incluso de ser analizadas en el dimensionamiento de la incertidumbre y gestión del riesgo a través de herramientas como el análisis de alternativas (PONER LINK)
Todas estas son todas recomendaciones generales que se deberán adaptar a las situaciones particulares de cada proyecto, pero son criterios profesionales válidos que sirven como guía.
Determinación del Tamaño sin limitación de Capital
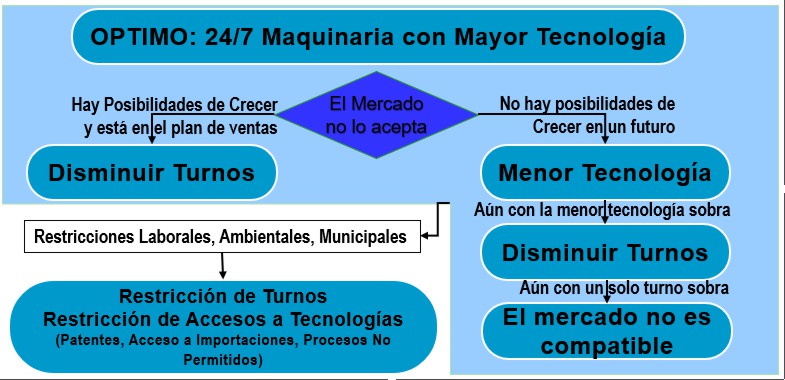
Si el monto total de la inversión no fuera una restricción, el tamaño debería estar asociado a los planes de ventas que surge del dimensionamiento comercial, empezando por considerar el mayor de ellos, generalmente el del último año, para luego tomar decisiones acerca de cómo se va a ir progresando hasta llegar a ese volumen de producción. Recordemos que existe también casos particulares donde el tamaño de la planta y de la tecnología a utilizar se realiza una sola vez para el proyecto, ya que el nivel de ventas y de producción se mantienen estables, tal es el caso de los trabajos a nivel de prefactibilidad en general o a nivel de factibilidad en el caso de que el tamaño de la planta esté limitado por cuestiones operativas o legales. Para estos casos, la determinación del tamaño se realiza en una sola etapa y no es necesario considerar el crecimiento.
La ausencia de limitación del capital, libera básicamente al elaborador del proyecto de elegir las tecnologías disponibles. Eso hace que cuando se busquen tecnologías, y de acuerdo con el algoritmo que muestra el gráfico, se debe empezar por elegir las tecnologías más avanzadas disponibles en el mercado y hacerlas trabajar todo el tiempo posible para el nivel de ventas requerido para el último año. La razón de esto es que los fabricantes de tecnología tratan de generar maquinarias y procesos cada vez más eficientes desde el punto de vista de la productividad y del costo de producción para sus clientes, y tratan de competir en función de esto.
Bien si las ventas son crecientes en el tiempo y por eso se debe considerar otras alternativas de tamaño o bien si el proyecto busca competir o se encuentran en segmentos o nichos del mercado con suficiente nivel de demanda como para requerir estas tecnologías obviamente es necesario considerar alternativas.
Para esto existen 2 alternativas
- Si se considera que es razonable pensar que las ventas tienen la posibilidad potencial de seguir creciendo (incluso más allá del período de análisis) lo ideal es seguir considerando adoptar esa misma tecnología analizada inicialmente, pero lograr la escalabilidad del proyecto agregando turnos, esto es preferible porque se optimiza el uso del capital. El usar tecnologías con menores niveles de producción e ir agregando líneas o máquinas en paralelo puede parecer mejor desde el punto de vista de la inversión inicial, pero hay que entender que la ampliación de una planta es disruptiva para una empresa en marcha, sobre todo si se realiza en el mismo predio y edificio donde ya se encuentran trabajando otras etapas. Además, por más que dicha estrategia permita diferir parte de la inversión, y eso signifique que desde el punto de vista financiero es más eficiente por el valor del dinero en el tiempo, el agregar turnos de trabajo implica solo inversiones marginales en activo de trabajo y esto de hecho es más eficiente.
- Si se considera que no existen posibilidades de crecer más allá de lo planteado en los planes de venta, se deberían considerar tecnologías más simples, pero aún considerando trabajar 3 turnos, o al menos 2 turnos. Cuando se habla de tecnologías más simples éstas abarcan un amplio espectro desde tecnologías levemente menos sofisticadas que la mejor tecnología hasta la realización de todas las tareas de manera manual siempre y cuando estas formas de realizar las tareas cumplan con los requisitos de terminación y calidad requeridos por los clientes.
Recién después de considerar trabajar tres turnos con la menor de las tecnologías (en general procesos manuales), es recomendable considerar trabajar menos de 3 turnos, hasta llegar a trabajar 1 turno.
En este punto, si trabajando un solo turno con la tecnología más simple de proceso, el aprovechamiento de la planta es inferior a los planes de ventas, es momento de pensar si el mercado atendido por el proyecto es lo suficientemente significativo como para generar un proyecto de inversión viable. Muchas veces en el afán de diferenciarse sustancialmente en nichos muy especializados para tener ventajas competitivas frente a los otros competidores, o limitar los mercados porque se considera complicado utilizar determinado canal de ventas o una plaza más amplia, es posible que quien elabora el proyecto haya cercenado demasiado el mercado potencial hasta hacer el proyecto inviable.
Las restricciones de Capital no suelen ser las única que pueden ser impuestas por el inversor. Muchas veces a lo largo del proyecto, como se explicará más adelante para el caso de la localización, los inversores pueden solicitar restricción a sus proyectos por decisiones personal, como por ejemplo que ellos se harán cargo de la empresa que surja del proyecto, y por lo tanto no quieren trabajar más de un turno, o no utilizar determinada tecnología o incluso a veces quieren evitar la contratación de mano de obra directa para evitar tener conflictos con el personal. Estas decisiones que en un principio no necesariamente son lógicas, son atendibles desde el punto de vista de que quien eventualmente pondrá en esos casos el dinero tanto para el proyecto como para el estudio que estamos elaborando es el inversor. En caso de encontrarse en esta situación, lo que se recomienda es explicar y ofrecer la mejor alternativa al inversor y que este decida si prefiere esta alternativa a aquellas alternativas que cumplen con sus criterios personales. En caso de que se elijan estas últimas, se seguirá haciendo el proyecto con dichas alternativas, pero explicitando en el mismo que no se tratan de las opciones optimas.
En reglas generales y a modo práctico si no se tiene experiencia previa en la elaboración de proyectos en general o en ese sector en particular, el elaborador del proyecto debería dimensionar una primera etapa con las maquinarias e instalaciones como para poder hacer frente al plan de ventas al cabo de un tercio del período de análisis, por ejemplo los primeros 3 años en un plan a 10 años o los primeros dos años en un plan a 5 años.
Como veremos más adelante, la primera sección operativa que se satura cuando la cantidad producida empieza a crecer es el cuello de botella. Esta será la etapa que se debe monitorear para poder determinar el momento en el cual es conveniente realizar la ampliación del tamaño.
Un poco diferente puede ser el tratamiento de los edificios y las instalaciones donde se encontrarán alojadas las maquinarias. Si la instalación de nuevas máquinas es disruptiva en una empresa ya en marcha, aún lo es más la construcción de edificios e instalaciones que demoran mucho más tiempo y que incluso pueden llevar a paradas de la línea para evitar contaminación en los productos justo en los momentos donde el cuello de botella está alcanzando su máxima capacidad. En este sentido, es recomendable considerar dimensionar el edificio y las instalaciones para poder albergar la totalidad de las máquinas y los procesos necesarios para todo el período de análisis.
Determinación del Tamaño con Limitación de Capital
Dentro de los factores internalizados el más importante en caso de existir es la disponibilidad real de aporte de capital por parte del inversor. Recordemos que uno de los objetivos propuestos a nivel económico puede ser una limitación en el aporte de dinero que está dispuesto a contribuir quien efectivamente está financiando el proyecto. En el punto que nos encontramos (si nos hallamos todavía a nivel de prefactibilidad) todavía no hemos realizados cálculos económicos asociados a la inversión total requerida, por lo que ese objetivo no hemos podido ver si se puede alcanzar o no, pero ya tenemos que estar determinando el tamaño (cantidad a fabricar, tecnologías a utilizar, edificios que necesitamos). Es otro punto en el proyecto donde podemos aplicar el concepto de planificación impulsada por descubrimientos. Lo que debemos hacer es estimar la inversión necesaria. Para esto tendremos que recurrir a información que si no hemos utilizado en la determinación del plan de ventas en el dimensionamiento comercial, la utilizaremos ahora.
Dentro de las inversiones que se generaran posteriormente, podemos estimar la inversión total a partir de calcular la inversión en activo fijo no tercerizable y calcular la inversión en activo de trabajo como el valor final del activo de trabajo. La primera es tener una idea de la maquinaria e instalaciones específicas necesarias, más los gastos necesarios para la constitución y habilitación de la empresa.
Dentro de la inversión en activo de trabajo se puede decir que si averiguo el plazo en el que me pagan la mercadería (por ejemplo 60 días) teniendo el precio de venta del estudio de mercado puedo acceder a una estimación de la inversión inicial necesaria en lo que hace a todos los posibles costos necesarios en los primeros meses de explotación. A esto habrá que sumarle las compras mínimas de materias primas si es que estas existieran.
Vamos a entonces a elaborar los conceptos para cada tipo de inversión.
Como se aclaró anteriormente, la inversión en Activo Fijo se debe calcular como la inversión en la constitución de la empresa y la inversión en bienes de uso críticos en máquinas, instalaciones asociadas a esas máquinas y Edificios.
Para el caso de la constitución y habilitación legal de una empresa, hay que tener en cuenta sobre todo las habilitaciones particulares requeridas según el tipo de industria (Salud, Alimentos, Impacto Ambiental). Esto se estima en este punto preguntando a un tecnólogo que sepa del sector. El gasto total en este rubro rondará entre los 500USD para proyectos simples en países de bajo nivel de burocracias hasta los 50.000 USD en proyectos en sectores altamente controlados en países de alto nivel de burocracia.
La inversión en bienes de uso críticos resulta aquella de la información recabada de los proveedores críticos en el Dimensionamiento Comercial. Se debe preguntar a dichos proveedores la inversión en una tecnología adecuada al nivel de inversión límite.
A través de la experiencia práctica se puede afirmar que la proporción de activo fijo y activo de trabajo es de un 50%-50% .
Por lo que si el nivel de inversión máximo esperado es de 1.000.000 USD, la mitad de esa estará dedicada al activo fijo, y de esa mitad habrá una cantidad de entre 500 y 50.000 USD de inversión en constitución de la empresa, supongamos 10.000 USD.
La inversión en máquinas e instalaciones críticas no debería superar los 490.000 USD.
El resto de las inversiones en activo fijo pueden generalmente subsanarse alquilando o tercerizándose (edificios, transporte, almacenaje) o su inversión no suele ser significativa (elementos de oficina, gasto de puesta en marcha).
Ya dado un plan de ventas crecientes, con distintas etapas de concreción, es importante entender que esta restricción de inversión es solamente una restricción de inversión inicial, por lo que esta limitación deberá aplicarse no a la inversión total necesaria para alcanzar el máximo nivel de producción, sino para aquella inversión considerada para el año 0 y el Año 1, que será la necesaria para poder cumplir con los requisitos de los primeros años de explotación del proyecto, ya que luego de esto el proyecto debería ir produciendo fondos autogenerados que permitan cubrir las inversiones en los años posteriores, y por lo tanto eximiendo al inversor de esa carga, obviamente a costa de no poder retirar fondos no aplicados en forma de dividendos.
Aquí es donde es fácil de mostrar al inversor la importancia y la ventaja de ir agregando turnos para optimizar el uso de sus aportes de capital. Es fácilmente mostrable que dada su inversión inicial, uno puede hasta cuadruplicar la producción y las ventas si se agregan turnos adicionales con un nivel de inversión similar. Obviamente esto agrega complejidad a la operación de la empresa, pero mientras que este concepto es abstracto para el inversor ya que no cuenta antes de tomar la decisión de ejecutar el proyecto con esa complejidad, si entiende la restricción de capital que tiene y como trabajar varios turnos puede hacer que produzca mucho más o la contracara que sería aportar mucho menos capital.
Dentro de los factores internalizados el más importante en caso de existir es la disponibilidad real de aporte de capital por parte del inversor. Recordemos que uno de los objetivos propuestos a nivel económico puede ser una limitación en le aporte de dinero que está dispuesto a aportar quien efectivamente está financiando este proyecto. En el punto que nos encontramos (si nos hallamos todavía a nivel de prefactibilidad) todavía no hemos realizados cálculos económicos asociados a la inversión total requerida, por lo que ese objetivo no hemos podido ver si se puede alcanzar ó no, pero ya tenemos que estar determinando el tamaño (cantidad a fabricar, tecnologías a utilizar, edificios que necesitamos). Es otro punto en el proyecto donde podemos aplicar el concepto de planificación impulsada por descubrimientos. Lo que debemos hacer es estimar la inversión necesaria. Para esto tendremos que recurrir a información que si no hemos utilizado en la determinación del plan de ventas en el dimensionamiento comercial, la utilizaremos ahora.
Dentro de las inversiones que se generaran posteriormente, podemos estimar la inversión total a partir de calcular la inversión en activo fijo no tercerizable y calcular la inversión en activo de trabajo como el valor final del activo de trabajo. La primera es tener una idea de la maquinaria e instalaciones específicas necesarias, más los gastos necesarios para la constitución y habilitación de la empresa.
Dentro de la inversión en activo de trabajo se puede decir que si averiguo el plazo en el que me pagan la mercadería (por ejemplo 60 días) teniendo el precio de venta del estudio de mercado puedo acceder a una estimación de la inversión inicial necesaria en lo que hace a todos los posibles costos necesarios en los primeros meses de explotación. A esto habrá que sumarle las compras mínimas de materias primas si es que estas existieran.
Vamos a entonces a elaborar los conceptos para cada tipo de inversión.
Como se aclaró anteriormente, la inversión en Activo Fijo se debe calcular como la inversión en la constitución de la empresa y la inversión en bienes de uso críticos en máquinas, instalaciones asociadas a esas máquinas y Edificios.
Para el caso de la constitución y habilitación legal de una empresa, hay que tener en cuenta sobre todo las habilitaciones particulares requeridas según el tipo de industria (Salud, Alimentos, Impacto Ambiental). Esto se estima en este punto preguntando a un tecnólogo que sepa del sector. El gasto total en este rubro rondará entre los 500USD para proyectos simples en países de bajo nivel de burocracias hasta los 50.000 USD en proyectos en sectores altamente controlados en países de alto nivel de burocracia.
La inversión en bienes de uso críticos resulta aquella de la información recabada de los proveedores críticos en el Dimensionamiento Comercial. Se debe preguntar a dichos proveedores la inversión en una tecnología adecuada al nivel de inversión límite.
A través de la experiencia práctica puedo afirmar que la proporción de activo fijo y activo de trabajo es de un 50%-50% .
Por lo que si el nivel de inversión máximo esperado es de 1.000.000 USD, la mitad de esa estará dedicada al activo fijo, y de esa mitad habrá una cantidad de entre 500 y 50.000 USD de inversión en constitución de la empresa, supongamos 10.000 USD.
La inversión en máquinas e instalaciones críticas no debería superar los 490.000 USD.
El resto de las inversiones en activo fijo pueden generalmente subsanarse alquilando ó tercerizándose (edificios, transporte, almacenaje) ó su inversión no suele ser significativa (elementos de oficina, gasto de puesta en marcha).
Estacionalidad en la demanda ó en la provisión de insumos
Un último aspecto para considerar en el tamaño del proyecto es la estacionalidad. La estacionalidad es la variación cíclica dentro de un período analizado tanto de la demanda como de la oferta de productos o servicios. Esta variación periódica es predecible en el tiempo y por lo tanto hay que considerarla para evitar problemas. Si bien la estacionalidad puede ser dentro de un día, una semana o un mes (por ejemplo muchos productos son comprados al inicio del mes o los fines de semana asociados a una mayor disponibilidad de dinero o tiempo por parte del cliente) esta estacionalidad suele manejarse a nivel operativo comercial con la empresa ya en marcha, y de hecho debería haber sido considerada en el dimensionamiento comercial. La estacionalidad que importa al tamaño del proyecto es aquella asociada a la disponibilidad de insumos o la producción asociada a mayor demanda en ciertos períodos del año. Los casos más comunes desde el punto de vista de los insumos es el uso de productos de origen agrícola, tales como las frutas y verduras, los cereales y legumbres e incluso la producción de productos animales como carne, leche y cueros tienen su estacionalidad. Para algunos productos existen cadenas logísticas adaptadas a proveer de los insumos todo el año aunque a diferentes costos (asociados al costo de almacenamiento) pero en otros casos no, y por lo tanto deberá procesarse dichos insumos lo antes posible. Un ejemplo claro de esto es la vinificación de las uvas, o la producción del aceite de oliva. La cosecha tiene que darse en el momento justo y dichos frutos no toleran bien el guardado en cámara ya que pierden sus características.
Entonces, por ejemplo para el caso de la producción de aceite de Oliva donde se planean vender 1200 ton de aceite de oliva por año, si uno planifica una capacidad de planta de 100 ton por mes promedio, estaría incurriendo en un error, ya que la cosecha y el mantenimiento de la fruta no dura más de 3 meses, y por lo tanto en realidad la capacidad de planta que es necesaria para poder cumplir con el plan de ventas requeridos es en realidad de 400 ton por mes, al menos para las primeras etapas del procesos, ya que el aceite una vez extraído puede almacenarse sin problema por más de un año, y entonces la etapa de envasado podrá ser de 100 ton por mes.
Algo similar sucede con los yogures pero desde el punto de vista del consumo. Si bien los yogures se consumen principalmente en verano. Siendo este un producto con una relativamente baja vida útil, estos no pueden producirse en los meses de invierno para consumirse en verano. Y por lo tanto para unas ventas de 1200 ton por año, en vez de producirse 100 ton por mes, en los meses invernales se producirán unas 70 ton y en los meses estivales unas 130 ton por mes, siendo este último el valor que se debe tomar como indicador del tamaño de la planta.

Localización
Importancia de la Localización
En esta etapa buscaremos describir distintos métodos ó herramientas para determinar la localización de un proyecto. Pero esta introducción busca aclarar algunos puntos de conflicto entre diversas líneas de pensamiento.
La distinta bibliografía disponible que se ha consultado maneja el tema de la localización de dos maneras distintas: por un lado le asigna una importancia capital, de la cual dependerán todo el resto de los factores y la elección de una mala localización podría llevar a dar un proyecto con restricciones de tecnologías y resultados económicos negativos mientras que por otro lado hay una línea que observa que todos los recursos de los que necesita un proyecto son plausibles de colocar en cualquier lugar del mundo (si uno tiene la suficiente imaginación y dinero) por lo que la localización no es esencialmente importante, más allá de la satisfacción de la mejor manera de las necesidades del cliente. La primera línea de pensamiento es generalmente sostenida por los ingenieros y otras carreras técnicas mientras que la segunda es mantenida por profesionales ligados al marketing y a las ciencias económicas.
El problema con ambas líneas de pensamiento no consideran aspectos importantes en la determinación de la localización que hacen que dependiendo del tipo de proyecto, la importancia de este factor sea mayor ó menor ó sin importancia.
Volvamos a los distintos tipos de proyectos enumerados en el capítulo de Gestión Estratégica para poder analizar la importancia de la localización.
Los proyectos de Creación ó Generativos (nuevos producto, proceso, sistema ó empresas): Para este tipo de proyectos la importancia de la determinación de la localización es mayor. El caso más general para el cual la localización tiene una gran trascendencia es la creación de nuevas empresas, ya que no existen restricciones preexistentes en el sistema que puedan llegar a limitarlo, esto permita que haya más posibilidades para elegir. Pero cada una de estas posibilidades estará asociada a un alto grado de incertidumbre por tratarse de restricciones asociadas a un entorno. Distinto es el caso de los proyectos Generativos de nuevos elementos (productos procesos ó sistemas) en una empresa existente. Para este tipo de proyecto ya existen restricciones dentro del sistema analizado (la empresa) y por lo tanto estas restricciones limitan significativamente las posibles localizaciones, por lo tanto las alternativas suelen ser menos y más fáciles de comparar.
Los proyectos de Transformación ó Reingeniería (modificación de producto, proceso, sistema ó empresas): En este punto la selección del emplazamiento es donde empieza a perder la importancia que tenía para los proyectos de Creación, excepto que una de las modificaciones que se pretende hacer durante el proyecto sea efectivamente la localización. En ese caso se debe considerar la importancia de este paso, más aún teniendo en cuenta en que las restricciones son mucho mayores ya que existen una serie de factores que probablemente se encuentren muchos más limitados porque pueden ser parte de un sistema que no se puede ni se quiere cambiar.
Los proyectos de Retirada (eliminación de producto, proceso, sistema ó empresas): Se puede afirmar que para este tipo de proyectos el peso de la determinación de la localización es virtualmente nulo, ya que el elemento del cual es objeto el proyecto ya cuenta con una localización y esta se va a perder, por lo que la localización no pasa de una simple descripción del estado actual.
Otra cosa importante acerca de la elección de la localización de un proyecto, es en muchos casos la multiplicidad de opciones, muchas veces muy poco diferenciadas unas de otras, aún en proyectos relativamente simples. Aquí puede surgir la contrapartida que es darle un exceso de importancia a esta etapa, sobre analizando decenas de factores, buscando cada vez más información para tomar una decisión fundamentada, ocasionando una perdida de tiempo importante. No olvide que uno está desarrollando un bosque (el proyecto) y no un árbol (la localización).
Otro aspecto significativo de la etapa de determinación de la localización que vale la pena aclarar en este punto es hacer hincapié en la naturaleza iterativa de la elaboración de proyectos. Es completamente falso que una mala localización pueda afectar a nivel de elaboración de un proyecto la rentabilidad ó la capacidad de cumplimiento con los clientes ó la selección de la mejor tecnología del mismo. ¡¡¡Debemos recordar que nos encontramos trabajando sobre papel!!! Si se seleccionó una localización y esto hace que no sea aceptable la atención al cliente ó no compatible con una tecnología ó me proporciona una rentabilidad negativa, a nadie se le ocurriría desechar el proyecto. Simplemente se vuelve para atrás, se elije una nueva localización y acabo con el problema. De este punto surge indirectamente otra de las aclaraciones que hemos hecho en algún momento acerca de que es importante mantener una metodología consistente y coherente, ya que si no se cuenta con esta el volver sobre los pasos puede resultar extremadamente difícil.
Macrolocalización y Microlocalización
El estudio de la localización consiste en dos etapas bien diferenciadas: la macrolocalización y la microlocalización.
La primera consiste en determinar la región geográfica en general para la ubicación del proyecto y la segunda es la determinación del espacio físico específico donde se emplazará dicho proyecto.
La diferencia sustancial entre una y otra es el determinismo a la hora de seleccionarlas. Mientras que de la macrolocalización se pueden analizar áreas extensas con características inicialmente similares para ir estrechando el campo de alternativas y restringiendo el tamaño de esas áreas, la microlocalización es exacta, ó sea se va a construir ó desarrollar el proyecto en un lote específico, con un tamaño específico y que se encuentra a la venta.
Como uno pudiera imaginarse, la condición de disponibilidad de un espacio físico para la microlocalización puede ir variando a medida que pasa el tiempo y un terreno ó planta disponible para la venta cuando se elaboró el proyecto puede no estar a la venta cuando se decide ejecutarlo. La microlocalización generalmente se sugiere justo luego de la macrolocalización y se actualiza junto con los presupuestos cuando se decide ejecutar el proyecto.
Lo que se tiende pues es a realizar un proyecto lo bastante flexible como para poder ser incorporado a un tamaño tipo de lote de acuerdo a la disponibilidad en general del área correspondiente a la macrolocalización (por ej. en la ciudad de Buenos Aires son lotes de 8,66 metros de frente por 50 metros de fondo).
Momento de la Determinación de la Macrolocalización
Una pregunta que surge frecuentemente es que momento del análisis de un proyecto se debe determinar la macrolocalización. Esto dependerá tal como se dejó entrever anteriormente del tipo de proyecto.
Para proyectos de mejora, ampliación ó retirada de una empresa, producto, proceso ó sistema existente de los cuales no se quiere ó no se puede modificar la localización, es obvio que la localización del proyecto es simplemente una nota en la descripción del mismo.
El problema comienza a suscitarse cuando la empresa ó la planta son nuevas y realmente existe un mayor grado de libertad a la hora de elegir el sitio adecuado.
Las tres alternativas posibles son:
Determinación Previa a la Factibilidad Comercial: Cuando el estudio de las variables del mercado depende de la localización para poder llevarse a cabo sin tener que estudiar para cada alternativa los clientes, proveedores y competidores. Este tipo de localización se da generalmente proyectos comerciales donde la atención se hace en forma directa al público y la diferenciación se da por la propia localización. El caso típico para esto son las estaciones de servicios, los locales de ropa ó la venta minorista de alimentos, bebidas y productos de limpieza. Lo que se trata en la factibilidad comercial es por lo tanto realizar la validación de la ubicación seleccionada. En este tipo de caso una ubicación diferente de solamente un par de metros puede ser la diferencia entre un negocio factible y uno no factible.
Una circunstancia similar se da en el caso de multinacionales con varias plantas disponibles o con representación en diversos países. La posibilidad de poner una planta en un país o en otro implica un análisis mucho más profundo que el que se puede hacer a través de una decisión subjetiva ó una matriz de localización tal como se muestra más adelante. Generalmente este tipo de organizaciones cuentan con los recursos disponibles como para realizar un análisis completo, desde los puntos de vista comercial, técnico, organizacional, legal y económico-financiero para evaluar las distintas alternativas y por lo tanto la factibilidad ó conveniencia de la localización estará determinada como uno de los objetivos del análisis.
También es el caso donde la ubicación está determinada por una restricción total de uno de los factores de la producción. Este es el caso típico de las industrias extractivas tales como las explotaciones mineras y las torres de extracción de petróleo que solamente pueden ubicarse donde se encuentran los recursos disponibles.
Determinación durante la Factibilidad Comercial: existen algunos casos en donde el mercado que se atiende se conforma con la localización como por ejemplo en el caso de las empresas distribuidoras de servicios tales como distribución de electricidad, teléfonos, agua y cloacas, gas, y empresas de televisión por cable. Excepto por este último caso, el resto de las actividades citadas se encuentran en la mayoría de los países muy reguladas por el estado por lo tanto su localización y el trazado suele estar bastante restringido, pero aún así existen casos donde es necesario hallar la mejor distribución posible.
Determinación Previa a la Factibilidad Técnica: Este es el caso aplicado para la mayoría de los proyectos industriales. Para este momento ya se cuenta con una cantidad importante de información:
- La cantidad que se va a vender lo que nos da una idea del tamaño
- Se ha investigado la demanda compuesta por los clientes y los consumidores por lo tanto se puede apreciar como van a reaccionar ante una determinada localización y donde se haya ubicada esa demanda
- Se ha analizado a los proveedores de las principales materias primas y tecnologías y se conoce su ubicación y sus políticas
- Se distinguen los canales de distribución necesarios y sus comportamientos
- Se conoce a los competidores existentes, sus ubicaciones y sus políticas de ventas y distribución
Por otro lado existen una serie de determinaciones en el la factibilidad técnica tales como la distribución en la planta, la instalación de las máquinas y equipos auxiliares y los plazos en el cronograma de ejecución y restricciones del tipo legal (todo esto se verá más adelante) que dependen de la localización.
Por eso resulta ineludible para este tipo de proyecto es seleccionar en este momento el lugar de asentamiento del proyecto.
Como las primeras alternativas (previa o durante la factibilidad comercial) no presentan mayores restricciones desarrollaremos aquí los posibles métodos para la última alternativa.
Y por último volvamos a recordar lo que se aclaró anteriormente. Si bien es necesario determinar la localización en cualquiera de estos momentos del proyecto, esto no quiere decir que dicha localización no pueda ser modificada a posteriori. En las palabras de la investigación operativa lo que se busca es una solución factible, pero no necesariamente óptima.
Métodos de Determinación
Existen 2 métodos básicos para la determinación de la localización, el primero con una tendencia más subjetiva y el segundo más racional. A pesar de lo que la mayoría de los autores sugieren, ninguno de los dos tiene mayor validez que el otro, ya que más información y técnicas más sistemáticas en realidad no dejan de lado la subjetividad a la hora del manejo y valorización de la información.
Elección Subjetiva de la Macrolocalización
Como cualquier otra toma de decisión, la localización puede estar sujeta a predisposiciones por parte de quien toma la decisión, y en el caso de los proyectos también se encuentra ligada las predisposiciones del analista, del patrocinador, de los asociados ó de los accionistas.
Estas predisposiciones pueden observarse cuando se selecciona localizaciones ligadas a aspectos afectivos ó históricos como en el caso de comprar una vieja fábrica que antes la utilizaba algún familiar o cuando se intenta poner una fábrica en un pueblo de donde uno es nativo, a razones de conveniencia tales como cercanía geográfica a la casa del dueño, a perspectivas ilusorias cuando se piensa que existirán ó se desarrollaran factores a futuro dentro de la localización seleccionada ó por simple imitación del lugar donde otras empresas ó proyectos relacionados con objetivos y funciones similares al proyecto a desarrollar.
Nadie puede discutir que muchas de las decisiones, sino la mayoría, acerca de la localización son tomadas de esta manera, sobre todo en pequeñas empresas ó proyecto. La pregunta que uno se debe hacer es si esto es adecuado ó no.
El problema con las decisiones subjetivas es su naturaleza. Uno puede argumentar con la más infalible de las lógicas, pero si quien toma la decisión decide continuar siendo subjetivo, no existe manera de ganar dicho discusión.
Para solucionar esta coyuntura lo trabajaremos con la planificación impulsada por los descubrimientos, diremos que una de las suposiciones es la localización, indicando quién fue que tomo esa decisión. Esto permitirá utilizarlo más adelante en la gestión de la incertidumbre.
Elección Racional de la Macrolocalización
Este es sin duda el método más difundido y el más aplicado en todos los cursos de ingeniería alrededor del mundo, pero como se ha visto hasta ahora solo es aplicable a unos pocos casos, ya que hay prescindir de esta técnica en todos aquellos proyectos de retirada, en los proyectos de transformación ó reingeniería, en los proyectos donde la localización es inicial en el proyecto y en aquellos donde la decisión la toma subjetivamente alguna persona.
Este procedimiento se basa en el Proceso Directivo Racional y consiste en analizar en una Matriz de Localización distintas alternativas de localización en base a diversos factores.
El secreto no pasa por la aplicación de la técnica que es relativamente sencilla sino por la correcta selección de las alternativas y de los factores, así como también por cada valoración realizada. Aquí nuevamente surge el tema de la subjetividad en la toma de decisiones, ya que cada una de los elementos antes citados y por lo tanto la necesidad del profesional de realizar el análisis más lógico y ecuánime posible.
A continuación se da un ejemplo gráfico para su mayor comprensión.
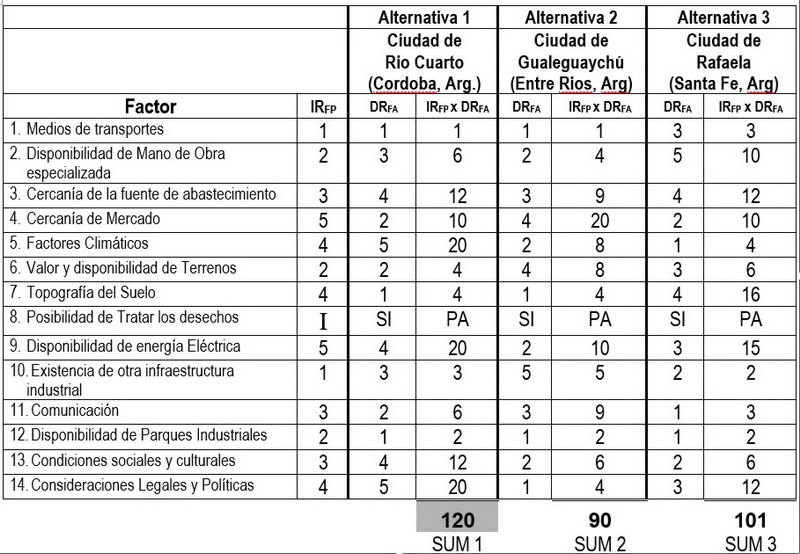
Primero hablaremos de las Alternativas. Cuando se eligen alternativas deben ser tres alternativas que contengan, por lo menos en una instancia preliminar, diferencias sustanciales desde el punto de vista de los factores que se van a analizar ya que si se analizar alternativas muy similares la tendencia de la diferencias no suelen ser significativas. Tres localizaciones separadas 20 kilómetros entre sí y las tres aptas para colocar proyecto deseado, probablemente difieran muy poco entre sí y se habrá llegado al punto de realizar una selección subjetiva que es lo que se trata de evitar con esta técnica. Tampoco tiene sentido elegir alternativas que realmente no cuenten con la infraestructura ni los factores necesarios y por lo tanto darán valorizaciones muy bajos. Esto podrá apreciarse de mejor manera en el análisis marginal explicado más adelante.
A continuación hablaremos de los Factores. En la tabla FACTORES POTENCIALES QUE AFECTAN LA LOCALIZACIÓN se enuncian una serie de factores típicos para el armado de una matriz de localización. Véase que se enumeran una serie de factores relacionados con aspectos comerciales, técnicos, legales, administrativos, y del entorno que impacten en la empresa tales como culturales, sociales y de seguridad. Cada uno de estos factores se encuentra a su vez conformados por diversos subfactores que en el armado de la matriz pueden ser puestos por separado. El caso más representativo es el de la infraestructura. En esta están incluidos subfactores tales como la disponibilidad de energía eléctrica, agua, gas ó telecomunicaciones. La importancia para cada uno de estos probablemente sea diferente en casi todos los proyectos y ponerlos todos juntos con una valoración única no es demasiado lógico. En el caso del ejemplo puede observarse en los factores 9 y 10 que se separa la Disponibilidad de energía eléctrica de la disponibilidad del resto de la infraestructura.
Mientras que algunos factores conviene disgregarlos, existen otros que no conviene ponerlos. Esto puede darse en el caso de que la existencia de un factor no tenga un impacto significativo en la localización (por ejemplo el clima) ó en el caso de que de ese factor no se pueda encontrar suficiente información como para poder realizar una valoración adecuada. Casos típicos de estas excepciones son muchas veces los factores culturales. También relacionado con esto es evitar poner factores relacionados con los costos de explotación del negocio, tales como los costos de logística, los costos de las materias primas y los costos de la mano de obra. Recordemos que nos encontramos en una etapa temprana de la formulación del proyecto y todavía no tenemos idea de los requisitos físicos para poder alcanzar la producción y las ventas estimadas y por lo tanto tampoco podemos dar fiabilidad de los costos y su estructura. Si pusiéramos este tipo de factores estaríamos realizando conjeturas poco racionales, lo que va en contra de lo esperado para este método. Solo un gasto, que luego será una inversión, puede analizarse entre los factores y este es el valor promedio de los terrenos ya que este es el único que se encuentra estrictamente relacionado con la localización.
Se deben tener además en cuenta aquellos factores que afecten tanto la etapa de instalación de proyectos como la operación a corto, mediano y largo plazo, considerando el crecimiento que podrá tener el mismo.
Una vez enumerados todos los factores a analizar lo que se procede es a valorizar la Importancia Relativa del Factor para el Proyecto (IRFP). Este coeficiente indica cuales de los factores son más significativos para el proyecto, siempre en función de cómo se vaya a evaluar el proyecto. Esto quiere decir que si se busca la localización para un proyecto donde lo que importan son los resultados económicos se asignará un mayor valor a los factores que me reduzcan los costos y las inversiones, mientras que si lo que se desea de un proyecto es aumentar el empleo se valorizará en mayor medida los factores que generen más mano de obra por más que la productividad no sea la mejor.
La tendencia suele ser a la valorización de la Importancia Relativa del Factor para el Proyecto (IRFP) en una escala de 1 a 10 que resulta natural para la mayoría de las personas, pero en la mayoría de los casos una escala tan amplia suele traer complicaciones al tratarse de valorizaciones subjetivas, por lo que es recomendable utilizar una escala de 1 a 5 que es igual de manejable pero presenta menos inconvenientes.
Existe además un caso particular que es aquel de los factores fundamentales y obligatorios. Este suele ser el caso de algunos requisitos naturales como el clima, donde es imposible la instalación de algunos proyectos donde los materiales o las instalaciones sean susceptibles a las temperaturas altas o bajas (como es el caso de las explotaciones agropecuarias), o en los casos donde la energía eléctrica ó la disponibilidad de agua abundante es restrictiva, o en el caso donde se generan gran cantidad de residuos tóxicos y es necesario poder contar con un tratamiento adecuado de dichos desechos (este es el caso dentro del ejemplo del punto 8). Para ese tipo de factores cualquier magnitud carece de sentido y es necesario manejarlo de una manera distinta por lo que en su lugar se le asigna una letra, en este caso la I (imprescindible).
Algunos modelos buscan que la sumatoria de las importancias relativas sumen un total de 100 pero esto no aporta ni a la metodología ni a los resultados, sino que restringe el proceso de valorización y construcción de la matriz ya que en cuanto se conocen nuevos factores o más información sobre los factores existentes será necesario cambiar la importancia de uno de los factores en detrimento de los otros.
Subsiguientemente se procede a estudiar como cumple cada alternativa con cada uno de los factores y esto se valoriza a través de la Disponibilidad Relativa del Factor en la Alternativa (DRFA). Tal como en el caso del indicador anterior se recomienda hacer esta valorización en una escala de 1 a 10 o de 1 a 5, excepto para el caso de los factores imprescindibles que se procederán a apreciar como SI o NO en función que dicho factor se encuentre representado en la alternativa. En caso de que una alternativa no cuente con un factor considerado imprescindible, la misma debe descartarse como alternativa.
Fijese que en el caso de ambos factores (IRFP DRFA) y casos hablamos de cuestiones relativas debido a que estas valorizaciones dependen tanto de la información con la que se cuenta como con la subjetividad del analista. Otra cosa importante con respecto a la cuantificación de estos factores es que puede ser que realicen algunas suposiciones para fijar estas estimaciones. Si esto es así no debe uno olvidarse en que estas suposiciones así como también quien las hizo deben registrarse para poder luego utilizarse en la gestión de la incertidumbre.
También nótese que la escala comienza en ambos caso en 1 y no en 0 ya que esto implicaría ó que el factor no es importante ó que la alternativa no cuenta con ese factor, que mucho ó poco pero tiene incidencia en el proyecto.
Una vez terminado de plantear las constantes en esta matriz, se procede a ponderar los valores de IRFP y DRFA para cada alternativa (esto se aprecia en el ejemplo presentado) y finalmente se procede a realizar la sumatoria de esta ponderación y aquella que resulte mayor corresponderá a la alternativa que se debe seleccionar como localización para el proyecto, en nuestro caso la Localidad de Río Cuarto en Córdoba, Argentina.
Hasta aquí todo muy bonito y prolijo, pero lamentablemente no siempre las decisiones son tan claras. ¿Qué hubiese pasado si otra alternativa hubiera dado una sumatoria muy similar? En esos casos lo que se hace es buscar entre los factores deseables con mayor Importancia relativa y ver cual es el comportamiento de estos factores para esas alternativas y elegir aquella cuyas disponibilidades de esos factores sean las mejores. Si aún así no existe ninguna opción clara, lo único importante es... ¡Tomar una decisión! ya que se trata de alternativas prácticamente igual de convenientes para la localización de nuestro proyecto.
Por último si en vez de tomarse los valores absolutos como parámetros para la evaluación de las alternativas se busca que porcentaje estos valores representan sobre el máximo total alcanzable, se puede realizar un análisis marginal que no cambia los resultados pero sirve para entender en mayor profundidad las sumatorias resultantes.
A continuación se arma una tabla para calcular estos porcentajes.

Se puede percibir que la mejor alternativa cubre en un 62% las condiciones que se considerarían ideales para localizar el proyecto y que esta es superior con respecto a la peor alternativa en 16 puntos porcentuales. En este caso no hay problemas ya que un 62% de cobertura se encuentra dentro de lo razonable, pero se sugiere que cualquier alternativa con un porcentaje menor a un 50 % no sea considerado como alternativa válida ó que por lo menos esto quede indicado en el estudio de localización si se pretende seguir con la elección de dicha alternativa. También es importante la diferencia porcentual ya que si se tratara de locaciones con diferencias mayores al 30-35% en realidad estaríamos comparando alternativas que no son completamente comparables y habremos entrado en el campo de la subjetividad al seleccionar alternativas de menor jerarquía con el conciente ó inconciente deseo que la localización sea una ya predeterminada. Y para esto es mucho más fácil y resulta menos trabajoso realizar una decisión subjetiva, asentarlo como presunción para analizar en la incertidumbre y dedicarle el tiempo a otras cosas que se consideren más importantes.
Determinación Técnica del Producto
En este punto se busca redefinir desde un punto de vista técnico el producto que ya fue definido a nivel comercial. Como hemos visto, a nivel comercial no es necesario entrar en demasiados detalles del producto, más allá de algunas características necesarias para satisfacer necesidades específicas de los clientes, especialmente aquellas orientadas a generar alguna diferenciación con respecto a la competencia.
Debido a la gran variedad de productos y servicios que pueden generarse a partir de un proyecto, no existe un listado único y exhaustivo que invoque la totalidad de dicha variedad. Por lo tanto, si bien los aspectos explicados a continuación pueden aplicar a la mayoría de los casos, nos concentraremos en productos físicos. Es importante en este punto también empezar a formar un criterio personal (profesional ó no) y determinar cuales de estos aspectos son necesarios y cuales no.
Datos iniciales de entrada de diseño
Esto implica traer al dimensionamiento técnico los datos definidos en el dimensionamiento comercial
Nombre Genérico ó Tecnico del Producto y modelos del producto, código del producto
A partir de este momento, el nombre comercial del producto no tiene importancia, solo se trabajará con los nombres genéricos y con los modelos puntuales. Muchas veces es importante diferenciar en la etapa técnica el producto a través de códigos en lugar de referirse a ellos a partir del nombre comercial por varios motivos: por un lado permite que la documentación técnica referida a los productos esté liberada de las modificaciones comerciales de los nombres comerciales que muchas veces se mantiene a pesar de ir realizándose modificaciones técnicas, por otro lado la codificación de un nombre muchas veces permite tener información del producto sin necesidad de ver especificaciones. Por ejemplo es distinto hablar de una bomba Klein que una bomba MCC-65S1N donde cada una de las letras ó conjunto de letras tiene un significado (en este caso que tiene un motor de corriente continua, con un cabezal de 65mm para usar con tubo de silicona, con un solo sentido de giro y un accionador Neumatico).
Uso pretendido
A pesar de parecer algo obvio, el uso pretendido es algo muy importante ya que representa la primera responsabilidad legal que tiene el proyecto. Esta definición es importante porque dice al usuario que el uso del producto es ese y solo ese y que la empresa se responsabilizará si el producto es usado con ese fin solamente. Un uso demasiado amplio provocará que se tenga que definir todas las posibles implicaciones en el análisis de riesgo y un uso demasiado acotado puede limitar el público objetivo para el producto.
Productos Complementarios (enumerar los surgidos en la parte Comercial)
En este punto enumerar los productos complementarios no cumplen con una función de analizar la demanda potencial a partir de extrapolar la demanda de los complementarios, sino que lo que busca es buscar las interrelaciones y la conectividad que tendrá nuestro producto con los productos complementarios (tipo de conexiones, protocolos de comunicación, superficies de contacto, necesidades de transmisión de energía, nutrientes, información, etc.)
Especificaciones de Materiales ó Procesos
por ejemplo en caso de utilizar una fuente de energía que tipo de energía utilizará, los colores que se han de elegir para representar a la empresa ó al producto, los procesos y materiales permitidos, apropiados, recomendados y socialmente responsables necesarios.
Esquema Básico
Un esquema de producto es siempre útil para permitir seguir elaborando el producto en detalle. Nos permite dar una mirada amplia de las funciones necesarias y nos permite preguntarnos si no es necesario algún elemento adicional ó si no existen elementos superfluos.
Datos Finales de Diseño de Producto
Los datos finales de diseño son los resultados obtenidos a partir del proceso de diseño del producto. El diseño de todo producto implica un proceso creativo iterativo donde distintas alternativas son sopesadas. El proceso de diseño escapa al alcance de este libro, pero lo que se puede asegurar que no importa que tan complicado sea este proceso, los resultados finales se tienen que registrar de manera adecuada para poder garantizar la repetitibilidad de los resultados deseados y esperados cada vez que se realiza un producto o se brinda un servicio como resultado de la explotación del proyecto.
Documentos de Definición del Producto, Materisa Primas y Materiales
Nos referimos como documentos del producto al conjunto de registros y procedimientos estandarizados y disponibles para quien eventualmente elabore el producto. Algunos ejemplos de estos documentos son: Planos, Normas, Especificaciones Técnicas, hojas de seguridad, Listado de materiales, procedimientos de prestación de un servicio. Para la mayoría de los productos, existen maneras normalizadas de presentar dichos documentos, bien a través de un requisito legal, ó a través de normas del sector ó a través de usos y costumbres. Estos diversos modos pueden verse por ejemplo en el área de educación: Mientras que los contenidos de un curso de una escuela primaria debe seguir lineamientos estrictos fijados por leyes, los cursos brindados por un instituto privado de capacitación empresarial no tiene requerimientos legales pero si una estructura obligatoria fijada por normas internas del instituto, mientras que en el último caso por ejemplo los cursos de capacitación propuestos por un consultor a una empresa la estructura con los contenidos debe tener cierta información (destinatarios, contenidos mínimos, horas necesarias) pero no existe un requisito legal ó una norma unificada del sector educativo para presentarlo.
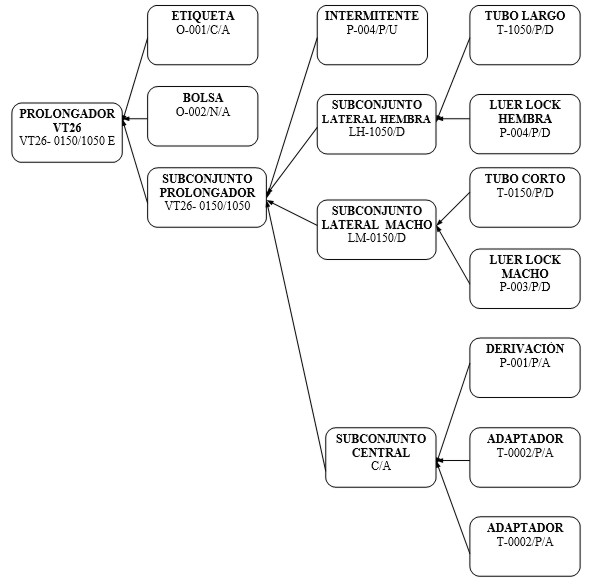
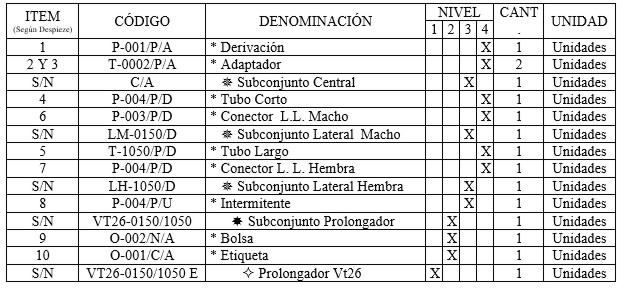
Sería imposible enumerar todos los posibles documentos de definición técnica de un producto sin embargo como anexo se presentan una serie de documentos y las recomendaciones para hacerlos.
ANEXO Documentación para la Definición técnica del producto
Características-Condición del Producto
Las características condición del productos son aquellas características que son condiciones necesarias para que el producto se considere como apto para ser usado. Si bien es discutible que todas las características de un producto hacen al mismo, la verdad es que en todos los casos existen algunas características que sin dudas son más importantes que otras. Por ejemplo en los alimentos el color de la tinta de la etiqueta puede llegar a afectar la estética del producto y hacer que se pierdan ventas, pero la seguridad microbiológica del alimento es infinitamente más importante ya que en eso puede ir la vida de las personas que consuman el alimento. No todos los casos son tan graves como el expuesto ó como es el caso de los medicamentos y productos médicos, pero es importante discriminar las características deseables de las obligatorias. Sobre estas últimas es donde se dispondrán de sistemas de control más exhaustivos ó de procesos, insumos y proveedores que garanticen la falta de problemas.
Ensayos de Validación de Concepción
Los ensayos de validación de concepción son aquellos ensayos que deberán hacerse al prototipo ó a la primera serie de productos para validar que el producto cumple con las características-condición planteadas. Ejemplos de estos ensayos son los ensayos de seguridad eléctrica en equipos eléctricos, los ensayos microbiológicos y de composición química en los alimentos, ensayos de concentración de metales del agua con la que se alimentará un proceso industrial. Estos se realizan periódicamente, generalmente anualmente pero puede ser mayor ó menor en función de requerimientos legales, y son necesarios al comienzo del proyecto para poner a punto el nivel de calidad deseado para el producto. Estos ensayos suelen ser complejos y demandar bastante tiempo y dinero, por lo cual generalmente no se realizan continuamente en todos los lotes de fabricación. Estos ensayos realizados continuamente en todos los productos ó lotes se disponen en el plan de ensayos, tal como se explica en el siguiente punto.
Plan de Ensayos
El plan de ensayos cumple la función de verificar el comportamiento de las características de un insumo, semielaborado ó producto antes de que el mismo sea liberado hacia la etapa siguiente ó para su comercialización. En cuanto al plan de ensayo hay que tratar de nivelar el costo de realizar dichos ensayos y los riesgos asociados a no realizarlos. Muchas veces al estar el riesgo disociado del costo del fabricante se dejan de hacer ensayos porque su costo ó el tiempo que tarda es demasiado sin tener en cuenta que eso puede poner en riesgo la seguridad ó la calidad de vida de los usuarios ó de otros grupos de interés.
El plan de ensayos sobre el producto se transformará a nivel de procesos en los procesos de verificación y control.
Marcado sobre el Producto
El marcado sobre el producto hace referencia a los rótulos que deben llevar los productos. La mayor parte de los productos comercializados hoy en día tienen una obligación de legal de contener cierta información: Denominación de Ventas, Pais de Origen, Fecha de Vencimiento, Cantidades Netas, Modo de Conservación, Información Nutricional, Nombre del fabricante y registro del mismo. Esta información puede variar de país en país y muchas veces de jurisdicción en jurisdicción con lo cual se debería consultar la legislación vigente. Muchas veces la legislación vigente en amplia y compleja, por lo que otro método de resolver esto se encuentra en ver que información presentan los principales competidores en sus productos y usar esto como referencia.
Pero adicionalmente existe información que uno quiere suministrar para que quien use ó mire nuestro producto ó servicio como por ejemplo la marca, ó información para que el usuario se vea tentado a usarlo. Dentro de las recomendaciones que se pueden dar en este aspecto son:
Usar Tipografías con colores que contrasten: Negro sobre blanco ó amarillo, verde sobre blanco, y dentro de esto con el mayor tamaño posible.
Usar textos “Tipo Frase” y no en “MAYUSCULAS” e interlineados grandes para entender mejor el texto
Usar referencias visuales conocidas en los envases tales como fotos, ilustraciones, iconos y gráficos y una fecha de vencimiento fácil de hallar ya que existe una reacción positiva. Es importante que este diseño refleje el contenido ya que si no se corre el riesgo de que no se genere confianza con los clientes.
Otras veces el marcado sobre el producto cumple la función de mostrar instrucciones de uso del producto (corte aquí, no someter al fuego, recargue solamente en distribuidores autorizados). En muchos casos el marcado sobre el producto debe usar no solo palabras sino también simbología, y la mayoría de las veces dicha simbología está estandarizada, este es el caso de los códigos de barras.
A continuación se muestran ejemplos de dicha simbología.

Otra parte importante comúnmente presente en los productos de consumo masivo es la incorporación de un código de Barras. Un código de Barras es un conjunto de cifras con una estructura predeterminada, cuyo objeto es lograr la identificación inequívoca de un producto. Esto facilita la circulación de las mercaderías, puede ser leído por diversos equipos de captura de datos, permite acelerar las operaciones en la caja registradora disminuyendo la posibilidad de error, extraer el precio correspondiente a cada artículo de la memoria.
La cadena de comercialización cuentan con la posibilidad de introducir un sistema de gestión de stocks para controlar, producto a producto, el movimiento de sus mercaderías.
Existen varias normas, las dos más comunes son la EAN-13, utilizada en todo el mundo excepto en EEUU donde es utilizada la norma UPC-A.
Estos implican una inversión y un costo para el proyecto, dependiendo de la cantidad de ítems que se quieran codificar. La contratación de este servicio va desde los 250USD como inversión inicial y un costo de 50 USD anual por 10 códigos de barras, hasta 10.500USD de inversión inicial y 2100USD por 100.000 códigos de barras.
También se pueden generar códigos de barra propios internos sin ningún costo, pero estos no serán aceptados en las cadenas de comercialización.
Acondicionamiento del Producto
el acondicionamiento del producto se refiere al envasado y embalado del producto. La importancia del acondicionamiento del producto es muchas veces tan importante como las características propias del producto, ya que muchas veces el cliente “compra” el envase ya que esto es lo único que se ve. También es una manera de diferenciarse en el caso del embalaje, ya que muchas veces por la facilidad de transportar ó guardar, se elige un producto sobre el otro, especialmente cuando la diferencia de precio es baja y los productos no son diferenciados.
Para más información ir al Anexo de Envases y Embalajes
Productos Complementarios (descripción Técnica)
Todo producto que se diseñe está destinado a ser usados junto con otros elementos que permiten su funcionamiento ó la consecución de su objetivo. Entre los productos complementarios debemos destacar tres grandes familias, aquellos productos que deben comercializarse con el producto, aquellos que pueden comercializarse con el producto, aquellos con los que el producto va a usarse pero se comercializan por separado.
Como ejemplo de los productos que deben comercializarse con nuestro producto se puede nombrar los manuales. Para los productos de consumo masivo eléctricos y electrónicos, para los insumos médicos, para los automóviles y para todos los productos cuya comercialización está de alguna ú otra manera regulado por el estado, los manuales son obligatorios. Estos manuales deben tener 2 características claves: deben ser fáciles de interpretar y deben cumplir con las reglamentaciones vigentes. Un ejemplo típico en donde se falla en ambas características es en el idioma en el que se redacta ya que un manual no puede estar redactado en un idioma distinto al del oficial del país donde se va a comercializar, y la simple traducción automática con un software de traducción genera muchas veces explicaciones confusas.
Otros productos que deben comercializarse con los productos son por ejemplo los certificados de garantía, los cables, servicio de mantenimiento.
Dentro de los productos que pueden comercializarse con el producto base de nuestro proyecto hay que destacar aquellos que facilitan la función y el uso de nuestro producto y aquellos que son necesarios para el uso de nuestro producto. Un buen ejemplo para ambos casos es el software para los equipos informáticos. No es obligatorio vender el software junto con los equipos, aunque es probable que si se vende sin el software las ventas sean menores, ya que los clientes tendrán que pasar por un doble proceso de compra y no estarán seguros de la compatibilidad entre los productos. Otro caso típico de estos son las recetas que se colocan en los reversos de los envases de los productos alimenticios procesados. Estas recetas deben ser adecuadas para el producto, fácil de hacer con el producto comercializado y… ¡estar seguro que funcione!
Para el caso de bienes intermedios y máquinas industriales es común también ofrecer servicios de instalación, cursos de capacitación para aprovechar mejor el uso de los productos, como diferenciación a la hora de comercializarlos. Que sean productos complementarios no implican que no se tengan que definir específicamente, ya que si se ofrece este tipo de soluciones la prestación debe realizarse con la calidad acorde al producto y con la calidad promocionada, ya que sino se podrían obtener más problemas que ventajas.
Entre los productos que son comercializados por separados, casos comunes son el combustible para los vehículos, la energía eléctrica, las baterías, los cables de audio y video, herrajes para madera. En la mayoría de los casos donde existen esta necesidad de vinculación con otros productos de otros mercados, suelen existir normas de cumplimiento obligatorios ó recomendables para evitar problema de interfaz. El no poder vincularse a productos complementarios, es muchas veces una de las causas principales de fracasos de productos ó inversiones innecesarias en rediseño.
Verificación y Liberación de Diseño
En empresas en marcha, sobre todo en aquellas que cuentan con un sistema de gestión de la calidad, es importante realizar la verificación y validación el diseño, esto incluye los ensayos necesarios para la liberación, el análisis de riesgo del producto, la aceptación de los medios de fabricación y control y el listado de documentos y datos liberados a cada área.
En proyectos de inversión, no es común que se desarrolle este punto, ya que no hacen a los presupuestos que son necesarios hacer para poder evaluar el proyecto. No obstante, cabe destacar que si es necesario realizar de manera rutinaria y continua estos procesos en la empresa que surja el proyecto, habrá que considerarlos a la hora de determinar el personal necesario.
Otras consideraciones del Diseño de Producto
Esta serie de puntos cubiertos dentro de la especificación técnicas del producto cumple con los requerimientos formales necesarios para poner en marcha el proyecto, sin embargo todos podemos comprender que el diseño de producto es algo más que la simple enumeración de los requisitos y va más allá de dicha enumeración.
A la hora de diseñar los productos se debería tener en cuenta lo que se denomina “diseño amigable”.
Un diseño, además de contar con todas los requerimientos técnicos, tiene que ser:
- Amigable con el usuario: fácil de entender de que se trata el producto, fácil de recoger o almacenar, sin un peso excesivo, generar un sentido de pertenencia y/o de diferenciación,
- Amigable con el Ambiente: Utilizar materiales reciclables tanto en el producto como en el embalaje, optimizar el uso de energía u otros consumibles
- Amigable visualmente: dar la sensación de un diseño moderno, contar con un diseño diferenciador y original, usar colores adecuados con el uso pretendido,
- Amigable con el proceso de Instalación: fácil de montar, instrucciones disponibles y fáciles e entender, contar con todos los insumos necesario para el montaje y uso final ó en su defecto aclarar donde conseguirlos.
Para ver más información acerca del proceso de Diseño de Producto, ver el anexo
Determinación y Diseño del Proceso de Elaboración y Control
Una vez determinado el producto que se quiere fabricar, es necesario empezar a determinar los procesos necesarios para poder llevarlo a cabo.
Muchas veces el producto y el proceso se van desarrollando de manera paralela, ya que el diseño o materiales a usar en los productos depende de las tecnologías a utilizar.
La fuente de información de las tecnologías disponibles puede provenir del análisis comercial, cuando se hizo el análisis de proveedores, o de la consulta de los expertos ó del tecnólogo.
Existe una extensa diversidad de procesos que abarcan desde las industrias más conocidas como las industrias metalmecánicas, hasta las industrias electrónicas más avanzadas donde parte del proyecto implica de hecho desarrollar tecnologías nuevas y específicas.
Desarrollar todos los procesos posibles escapa en este momento a los alcances de este libro, si bien en anexos se irán desarrollando el tema específico para cada tipo de industrias.
Diagramas Iniciales del Proceso
Para el diseño y modelamiento del Proceso generalmente se inicia con el armado de Diagramas Iniciales de Proceso de Fabricación y Control. Para esto generalmente se utilizan diagramas de flujo. Los diagramas de flujos son representaciones gráficas que permiten esquematizar de manera simple procesos productivos y flujos de trabajo paso a paso.
Si bien existen diversos tipos de simbologías para representarlos, las más comunes para procesos industriales abarcan los siguientes gráficos:
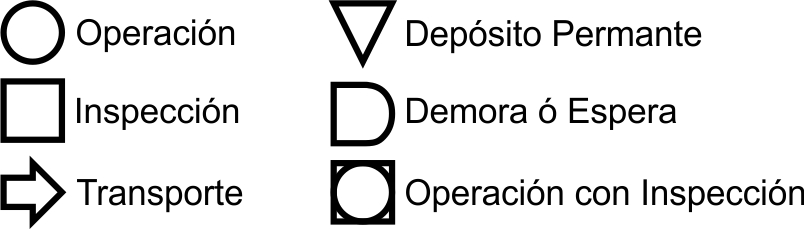
Otro ejemplo común de diagramas de flujos son los utilizados para procesos que incluyen el manejo de información:
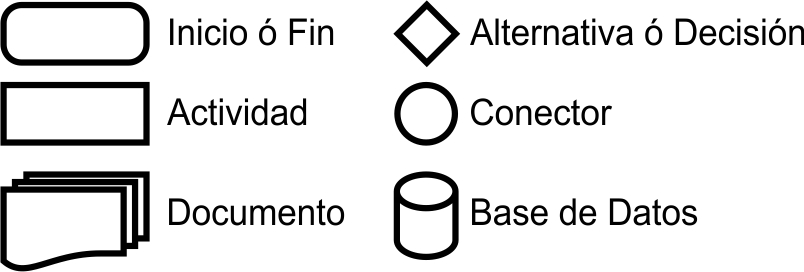
Cualquiera que se use, se deberá usar siempre un mismo criterio, o llegado el caso indicar la simbología utilizada al pie del gráfico.
Diseño del Proceso
A continuación vamos a describir conceptualmente las distintas alternativas para cada una de secciones operativas, que si bien en muchos casos es posible elegir distintos tipos de procesos para una misma sección, muchas veces esto no es conveniente ya que se producen variaciones en la calidad de los productos salidos de una misma sección operativa.
Desde el punto de vista de la intervención de la mano de obra, los procesos se catalogan en:
- Procesos Manuales: Son aquellos donde el ritmo de trabajo depende exclusivamente de la persona que lo realiza. Puede estar acompañado del uso de herramental simple que ayuda a la persona a realizar su tarea. Ejemplos típicos de esto son los procesos ensamble, la construcción tradicional, la costura en los talleres textiles, etc. Se caracterizan por su baja necesidad de inversión y de instalaciones, por ser fácilmente escalables y por la gran variabilidad en los tiempos. También al contarse con el trabajo de personas, esto puede provocar paradas ó retrasos por cuestiones personales, falta de personal, y en algún caso riesgos vinculados a los accidentes y la salud de dicho personal.
- Procesos Automáticos: son aquellos donde el ritmo de trabajo depende exclusivamente de las máquinas operativas, y no hay intervención de las personas excepto casos excepcionales (paradas, arranques o carga de materiales). Ejemplos típicos de esto son los hornos continuos, las cabinas automáticas de pintura ó los telares mecánicos. En estos casos la inversión tanto en las máquinas operativas como en las instalaciones suele ser alta, las capacidades de producción por unidad productiva también son altas, son difíciles de escalar ya que su instalación es compleja y requiere espacio. Mientras que las paradas ó retrasos son inusuales, cuando estos se producen generalmente son debido a roturas y por lo tanto muy adversos tanto desde el punto del costo como desde el punto de vista de pérdida de tiempo.
- Procesos Semiautomáticos: son aquellos donde el ritmo de trabajo es compartido tanto por las personas como por las máquinas operativas. Esto provoca que tengan las ventajas y desventajas de los dos esquemas anteriores. Por lo que la inversión no es tan alta pero si es significativa, las capacidades productivas son algo intermedio entre ambas, pueden producirse paradas o falta de actividad tanto por problemas de las máquinas como por problemas ó accidentes del personal.
Generalmente para un proceso dado en una industria dada, cuando se requieren bajos niveles de producción se opta por procesos manuales, luego se opta por procesos semiautomáticos y finalmente por los automáticos.
Desde el punto de vista de su naturaleza, podemos catalogar los procesos en:
- Procesos de Transformación: Son todos aquellos procesos donde la materia prima, mercadería en curso ó materiales que entran al mismo son distintos a los productos elaborados ó semielaborados que salen del mismo. Estas transformaciones pueden ser mecánica, procesos tales como el torneado ó fresado, puede ser transformaciones químicas como la fermentación, pueden ser un simple cambio de estado en procesos como el evaporado ó a veces el proceso de transformación son simples mezclas ó ensamblados donde la naturaleza de de las materias primas no cambia, solo su disposición es la adecuada.
Los procesos de transformación son el núcleo indispensable de todo proceso productivo.
Dentro de los procesos de Transformación, existen procesos especiales que son imposibles de controlar sin eliminar una característica indispensable del producto. En este caso, en lugar de controlarse dicha característica, lo que es necesario hacer es validar el proceso. Un caso típico de un proceso especial es la esterilización, ya que si uno abre el producto estéril para verificar su esterilización, el producto en sí ya deja de estar estéril.
- Procesos de Control: los procesos de control son todos los procesos donde a través de la comparación del producto semielaborado ó elaborado con un standard, se decide si dicho producto está apto para pasar al siguiente proceso ó para ser liberado como producto terminado al mercado. Si bien en si los procesos de control no aportan valor intrinsecamente, ya que un producto es apto o no independientemente de haber pasado por un control, estos procesos me sirven para segregar los productos que no estén aptos y evitar potenciales problemas.
Muchas veces los procesos de control surgen del último análisis del proyecto, el análisis de riesgo, ya que en este punto se identifican los posibles peligros y riesgos que puedan haber, y por lo tanto se decide implementar controles para evitarlos.
En otros casos, los procesos de transformación y control se hayan combinados, este es el caso de las inspecciones visuales ó controles durante el ensamblado.
- Procesos de Transporte: Los procesos de transporte cambian la ubicación ú orientación de las materias primas y productos semielaborados ó elaborados. Esto permite que dichas materias primas ó productos se encuentren disponibles para el siguiente proceso de una manera adecuada en cuanto a su disponibilidad en el lugar y momento.
Los procesos de transporte pueden estar integrados a otros procesos, este es el caso de cintas trasportadoras en una línea de montaje ó los tornillos sin fin, ó pueden ser independientes como es el caso de zorras, carretillas ó apiladores. También pueden ser aprovechados para realizar tareas como son el enfriado de productos ó el secado de pegamento.
- Procesos de Almacenaje: Los procesos de almacenaje surgen como necesidad para equilibrar los distintos procesos y permite garantizar el suministro continuo y oportuno de los materiales y medios de producción requeridos para asegurar la producción de forma ininterrumpida
El almacenaje puede ser tanto para equilibrar los flujos con el entorno, tal es el caso de los almacenes de materias primas y productos terminados, como el flujo interno, tal es el caso de los stocks de mercadería en curso.
Estos también pueden ser aprovechados para realizar tareas como son el enfriado de productos ó el secado de pegamento.
Si bien son prácticamente indispensable en todos los procesos, cabe destacar que el sobredimensionamiento de estos procesos provocará en el proyecto un aumento de la inversión en activo de trabajo, por lo cual serán contraproducentes desde el punto de vista de la rentabilidad del proyecto.
Desde el punto de vista de su evolución en el tiempo los procesos se clasifican en:
- Proceso Continuo: Es aquel en el que la operación no se detiene. Las diversas partes de la estructura de un proceso en general siempre está recibiendo una alimentación continua y de igual manera están lanzando un producto en forma continua. Esto permite mantener un ritmo de producción constante, y suele ser económicamente más conveniente, ya que los arranques o los paros pueden ser más costosos que en una operación contínua.
- Procesos discretos: también conocidos como batch o lotes son en los que si existen paradas del proceso entre lote y lote. Son más comunes en empresas pequeñas ya que suelen requerir menos inversión que los procesos continuos. Algunos procesos dada su naturaleza son necesariamente discontinuos, como la filtración, ya que después de determinados periodo de operación es necesario limpiar los filtros.
Es común que cuando se combinan líneas donde hay procesos continuos y discontinuos, es común utilizar dos o más equipos de proceso discontinuo con la finalidad de poder estar alimentado un proceso continuo posterior.
Para elegir cada uno de estos procesos es necesario tener en cuenta la secuencia de estos, la posibilidad de integrar procesos en una sola sección operativa, permitir un flujo equilibrado a lo largo de todo el proceso, evitar errores de mezclado e interrupciones en la producción. Si bien la mayor parte de las veces esto puede ser realizado sin problemas, muchas veces la experiencia de un tecnólogo que conozca el proceso ayuda a evitar problemas y errores comunes.
Una vez identificado el proceso que se desea modelar, hay que:
- Identificar y definir las etapas del proceso que se deben realizar en un orden específico.
- Determinar en un orden específico las operaciones que conforman cada etapa.
- Establecer las acciones que se deben desarrollar para completar cada operación.
A continuación se muestra un ejemplo:
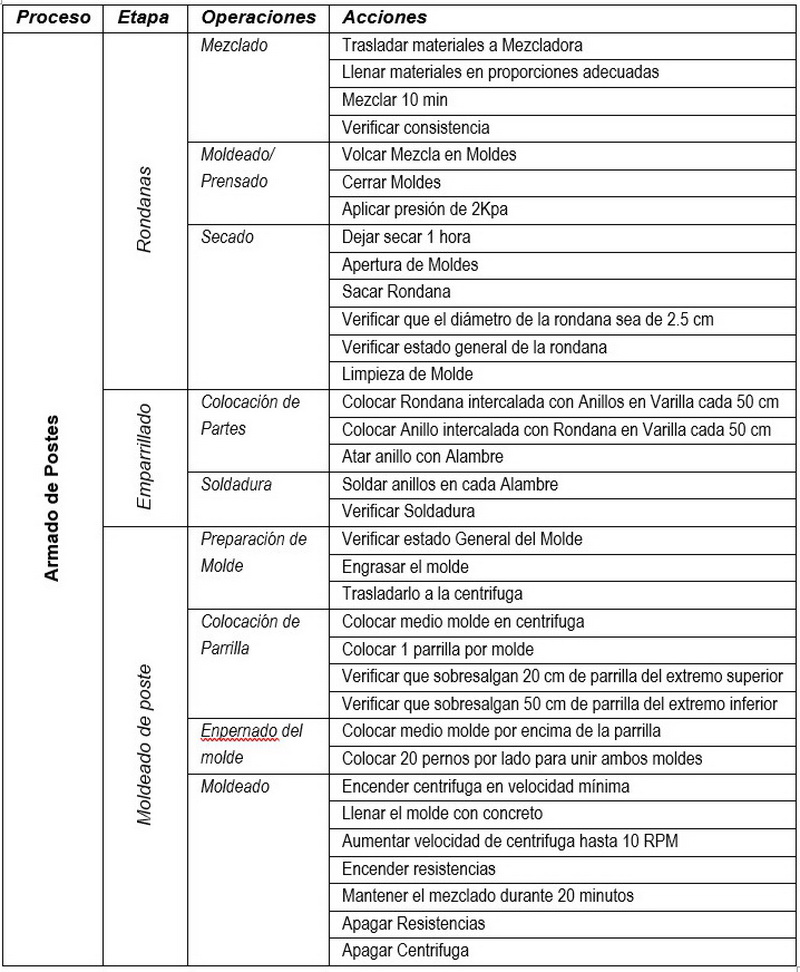
Una vez definidos las Procesos, etapas, Operaciones y acciones, se debe definir el tipo de planta que se desea montar ó desarrollar.
Tipos de Plantas
Plantas Monoproducto

Se agrupan las etapas/operaciones/acciones consecutivas que puedan realizarse de manera conjunta en una sección operativa que se numera ó nombra para poder identificarla, de cada sección operativa saldrá un semielaborado que también habrá que numerar ó nombrar para poder identificarlo unívocamente, excepto de la última sección operativa por la que saldrá el producto terminado. Para cada sección operativa, habrá que identificar por cada unidad de salida la cantidad necesaria de materias primas, materiales, desperdicios recuperables, desperdicios no recuperables.
Plantas Multiproducto

Para el caso de las plantas multiproducto, donde todos los productos siguen la misma secuencia a través de todas las etapas de producción, el proceso de armado de la línea es similar, solo que se hace este proceso independiente para cada producto, para luego eventualmente si se desea hacer un balance de materiales total, simplemente hay que sumar los requerimientos para cada uno de los productos. Esto puede ser conveniente para mostrar el resultado total, pero más adelante con el objetivo de balancear la línea, será necesario contar con todos los flujos por separado para poder realizar los cálculos.
Plantas Multipropósitos
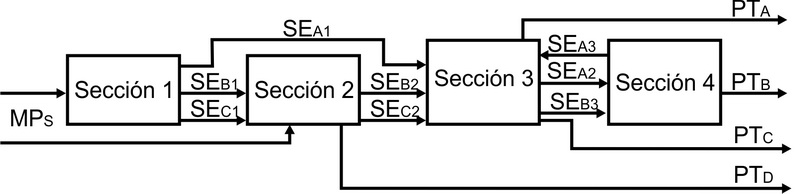
Como puede verse, las plantas multipropósitos le agregan un grado adicional de complejidad, ya que los procesos para los mismos productos no siguen la misma secuencia. Nuevamente la técnica es la misma que para la planta multiproductos, son que en este caso, además de adicionar los requerimientos de cada producto, también es necesario adicionar los requerimientos para cada sección operativa.
Diseño de Procesos Complejos
Cuando los procesos son lineales y continuos, los procesos son fáciles de diseñar, pero cuando se empiezan a incluir etapas discontinuas ó variaciones en el proceso realizado a cada producto, el diseño del proceso puede volverse desafiante.
En estos casos, se recomienda seguir la siguiente técnica:
- Diseñar el Proceso como si fuese Continuo
- Identificación de Equipos Discontinuos: Los equipos discontinuos ó proceso batch producen cortes en las líneas continuas. Para evitar esto, suelen utilizarse dos ó más equipos discontinuos en paralelo para lograr evitar interrupciones, disminuye las necesidades de almacenamiento intermedios.
- Identificación de Equipos Multitarea: Utilizar equipos multitareas permite aprovechar las capacidades ociosas, hacer un uso eficiente de recursos y generar una producción flexible y Optimizada. Sin embargo, los equipos ó secciones operativas multitareas suelen ser una pesadilla desde el punto de vista de la programación de la producción una vez puesta en marcha la empresa. Si el proceso es continuo, los requerimientos se tratan como se explicó anteriormente en lo que hace a plantas multipropósitos, si el trabajo es por lote es necesario tener en cuenta que los lotes de los diversos flujos, no necesariamente son iguales, por lo cual el equipo multitarea se deberá dimensionar para el lote de mayor tamaño.
- Determinar la necesidad de Etapas Paralelas: Las etapas paralelas pueden surgir o por la necesidad de realizar distintos tratamientos a distintos productos ó por la necesidad de balancear equipos discontinuos con equipos continuos.
También se usan etapas paralelas para optimizar el uso de ciertas secciones operativas de larga duración y minimizar los tiempos ociosos de los equipos.
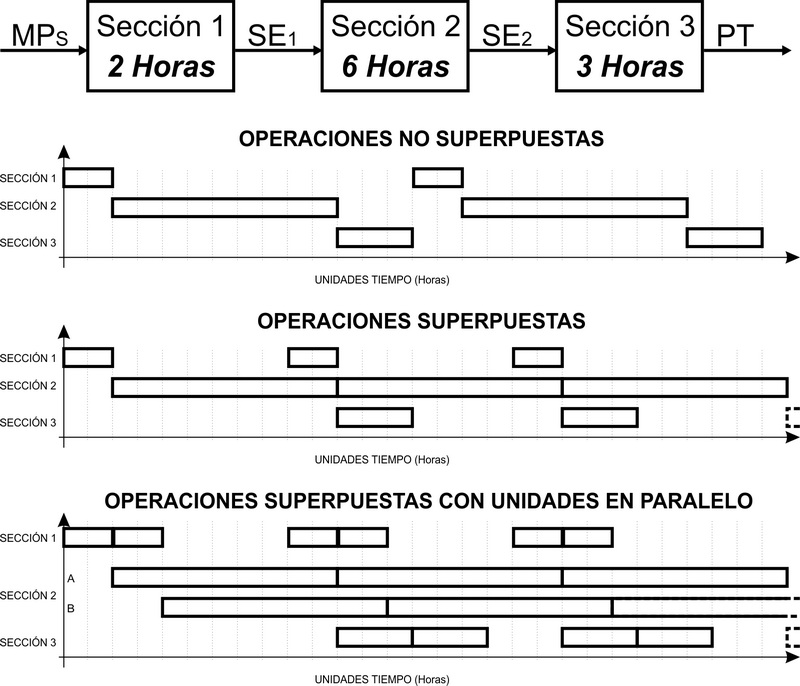
Como puede observarse de los gráficos anteriores, la optimización de la programación superponiendo actividades, lleva a un aumento en la capacidad de aproximadamente del 50%, y al utilizar etapas paralelas lleva a un aumento en la capacidad de más del 150% con respecto a la primera alternativa casi un 80% sobre la segunda alternativa, haciendo una inversión solamente en una de las secciones operativas.
Esto también aumenta el aprovechamiento seccional en la primera y tercera sección del 21% al 43%. Y si se agregara una tercera etapa paralela en la segunda sección, los aprovechamientos seccionales subirían aún más.
5. Cuantificar el Almacenamiento Intermedio:
Los procesos por lotes requieren necesariamente contar con almacenamientos intermedios.
Cuando se consideran almacenamientos intermedios, hay que considerar la naturaleza de los semielaborados, o sea que esto permitan ser almacenados el tiempo necesario, la inversión requerida en los equipos para almacenarlo, la disponibilidad del lugar físico para ese almacenamiento, así como también el valor de la mercadería semielaborada en sí. Si el tipo de semielaborado lo permite y la inversión en el equipo de almacenamiento y lugar físico es bajo, siempre es conveniente hacer uso de almacenamientos intermedios para optimizar el aprovechamiento de las máquinas operativas.
Hay que considerar que si bien el almacenamiento intermedio permite balancear procesos por lotes, evitando la interrupción de los procesos, también puede provocar demoras por lotes fuera de especificación.
Especificaciones de Medios de Fabricación y Control
Ya teniendo balanceado el proceso, es necesario determinar los equipos específicos de Fabricación y Control.
Para cada sección operativa, hay que determinar ahora equipos y máquinas específicas, existe una gran cantidad de alternativas de fabricantes de máquinas y describirlos todos es imposible.
Si es importante dar algunos lineamientos para selección las máquinas y equipos.
Para empezar hablamos de una línea Hómogenea cuando las máquinas son del mismo fabricante. Esto generalmente facilita los procesos de balanceo de líneas, disminuyendo los stocks intermedios y facilita los procesos de mantenimiento al referenciarlos a un solo proveedor.
A la hora de seleccionar los medios de fabricación y control, no hay reglas generales para la toma de decisión.
En algunos casos se decide seleccionar equipos donde la capacidad del equipo exceda un poco las necesidades de producción, con lo cual se contará con un solo equipo por sección operativa. Esto se debe a que un solo equipo grande generalmente es más ventajoso desde el punto de vista del retorno de la inversión. Sin embargo, en este punto todavía no se ha desarrollado el dimensionamiento económico, por lo cual esto no se puede verificar.
Cuando los equipos requieren muchas paradas de máquina para cambio de matrices o limpieza por ejemplo, es común elegir equipos con menos capacidad que permitan realizar estas paradas mientras se sigue utilizando otro de los equipos.
Cuando la inversión está restringida, es común elegir procesos manuales para las secciones operativas, ya que los medios de fabricación y control en estos casos son comparativamente más baratos. La desventaja en estos casos (más allá de las explicadas anteriormente) es la variabilidad de la calidad y tiempos entre persona y personas, y para una misma persona a lo largo de la jornada laboral.
No obstante todo esto, lo importante en este punto es elegir una tecnología adecuada para los procesos requeridos, y eventualmente si se tiene dudas de haber elegido la mejor alternativa, esto se suele analizar en el dimensionamiento de la incertidumbre y gestión del riesgo (AGREGAR LINK)
Para cada medio de fabricación y control, será necesario contar con una hoja técnica del mismo, y de ser posible con el manual respectivo. De esa hoja técnica surgirán datos a considerarse en este momento, tal como la compatibilidad con las materias primas y materiales que se van a utilizar, las capacidades teóricas por unidad de tiempo y datos a ser utilizados más adelante en el proyecto, tales como las dimensiones, los consumos de servicios, la frecuencia de mantenimiento.
Hay otras informaciones que generalmente no se encuentran en las hojas técnicas y es necesario preguntar al fabricante o proveedor para poder utilizarlos en el proyecto:
- rendimiento operativo (para poder calcular la capacidad real),
- requisitos especiales para la instalación (por ejemplo de un contrapiso)
- Embalado (para poder organizar su armado),
- Plazos de construcción y entrega (para programarlos en el cronograma de ejecución)
- datos económicos (precio, formas de pagos)
- Condiciones de Guardado
- Frecuencia y costo de Calibrado (medios de Control)
- Conexiones a los servicios (tipo y diámetro de cañerias, tipo de enchufes)
Una vez que se hayan determinado las máquinas especificas, puede ser que sean necesario readecuar los procesos, además de adaptar el proceso al espacio físico disponible más adelante cuando se desarrolle el anteproyecto de Planta.
Un aspecto indispensable a determinar para cada sección operativa es, dado las tecnologías y maquinas seleccionadas, los flujos de ingresos (materias primas, materiales, insumos) y de egresos (productos, subproductos, desperdicios). Esto surge también de la información suministrada ó consultada con el proveedor. Por lo que para cada sección operativa, se tendrá que conseguir esta información, que será utilizada más adelante en el balanceo de Materiales.
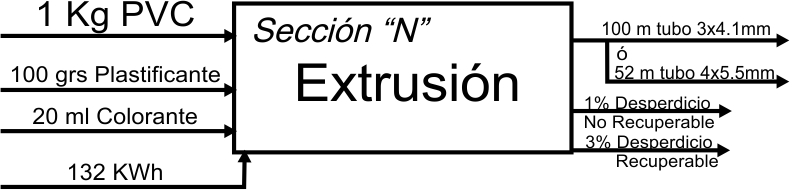
Descripción de cada Máquina y/o Puesto de Trabajo
Una vez determinadas las tecnologías a ser utilizadas en cada sección operativa, es necesario diseñar y especificar cada máquina ó Puesto de Trabajo.
En cuanto al diseño de las máquinas, además de contar con el espacio físico neto para la máquina, es necesario fijar los espacios para circulación de personal, los espacios para carga y descarga de materiales, los espacios necesarios para el mantenimiento.
La mayoría de las veces solo se piensa en el espacio superficial requerido, también hay que tener en cuenta el volumen hacia arriba (y en algunos casos hacia abajo) para la carga y descarga de materiales. Por ejemplo si se utiliza un autoelevador ó apilador para cargar los materiales, los mismos cuentan con una columna que muchas veces excede la altura de la carga.
La determinación de todos estos espacios en este punto, ayudará a evitar problemas cuando se tengan que armar el anteproyecto de planta.
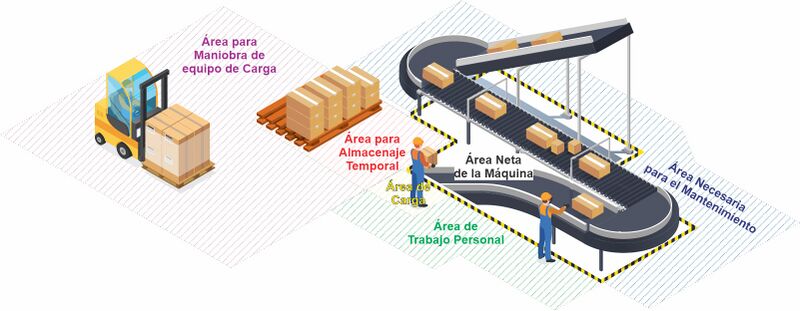
Como puede apreciarse en la imagen anterior, muchas veces la superficie requerida para todo el proceso excede significativamente la superficie de la máquina (en este caso casi el triple). Debido a que cada espacio requerido en la planta para cualquier actividad requerirá una inversión (ó un costo en caso de alquilarse el edificio), será importante eventualmente optimizar el espacio de la planta. Como todavía no se cuenta con toda la información requerida de todo el proceso ni de la cantidad de máquinas, en este punto simplemente habrá que aclarar cuales de estas superficies pueden encimarse con otro tipo de superficies, para esto se realiza una simple matriz de doble entrada indicando cuales están permitidas encimarse y cuáles no.
IMAGEN SuperpAreas
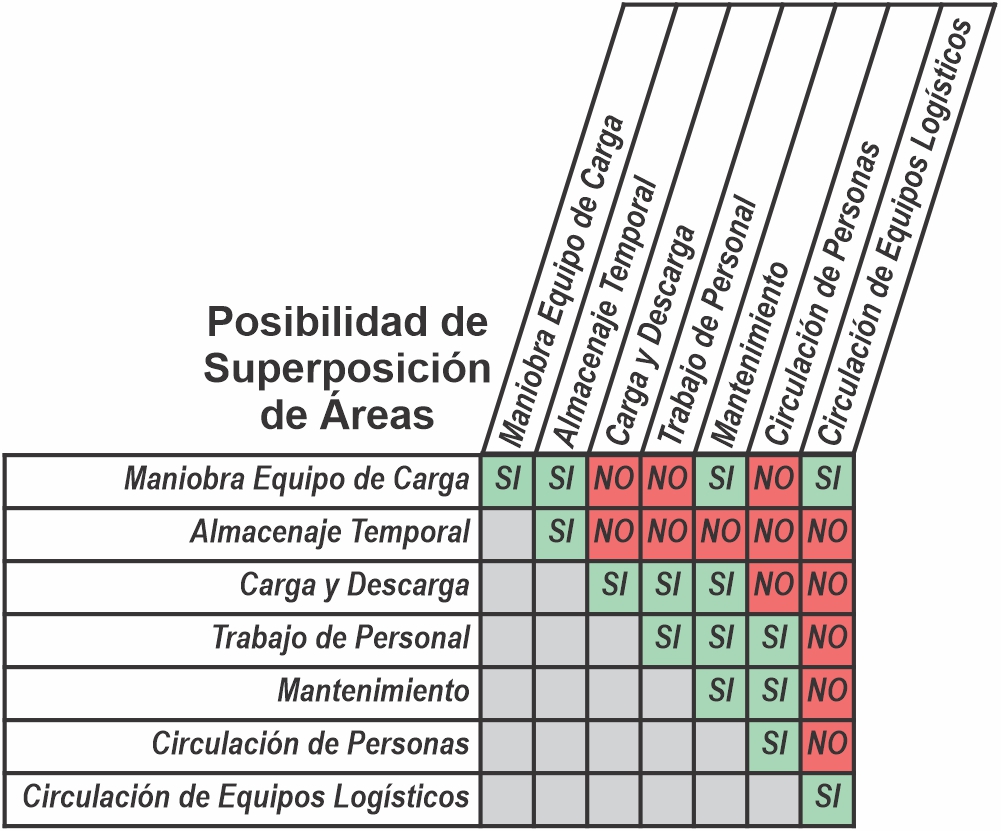
Nótese que en la diagonal de la matriz donde hace referencia a que un área puede superponerse a si misma, hace referencia por ejemplo a que las áreas de circulación de personas de un puesto de trabajo pueden superponerse a las áreas de circulación de personas de otro puesto de trabajo. Obviamente si existieran restricciones de seguridad para que esto pase, simplemente no deben superponerse. Siempre hay que recordar que cualquier calculo o determinación en cualquier parte de un proyecto aparte de usar las herramientas recomendadas, deben cruzarse con un criterio profesional por parte del analista.
En reglas generales, no se debe permitir que áreas de trabajo del personal se encimen con áreas de maniobras ó circulación de máquinas por los riesgos que pueden surgir.
Si las actividades de mantenimiento son rápidas, se realizan fuera del horario normal de trabajo ó son realizadas por el mismo trabajador a cargo de la máquina, estas superficies pueden encimarse con las áreas de trabajo ó circulación, siempre y cuando no se generen riesgos debido a esto.
Para el caso de los puestos de trabajo manuales, generalmente el diseño es más sencillo ya que las áreas de mantenimiento no suelen existir, las áreas de almacenaje temporal y carga y descarga suelen ser menores, y además el espacio ocupado por la mesa de trabajo y las personas son generalmente menores.
Sin embargo, en todas las situaciones habrá que analizar los puestos de trabajo y el espacio que ocupan las diversas actividades para evitar riesgos.
Se hablará más específicamente de este tema cuando se desarrolle el anteproyecto de planta (PONER LINK a TERCERA ITERACION ).
Es importante entender que en la mayoría de los proyectos esto está más vinculado a definir las inversiones necesarias tanto en herramental, mobiliario y espacio físico que al diseño correcto y ergonómico del puesto de trabajo, ya que un adecuado diseño ergonómico no afecta el nivel de inversión requerido, pero el espacio físico sí. Este diseño ergonómico del puesto de trabajo llevará tiempo para el analista y al fin y al cabo el tiempo con el que se cuenta para la elaboración del proyecto puede ser utilizado en realizar otras tareas mucho más significativas.
En el caso de proyectos de reingeniería ó de rediseño de puestos de trabajo, obviamente esto tiene que desarrollarse en más profundidad.
Representación Final de los procesos
Una vez que se han determinado las secciones operativas y las máquinas, en necesario volver a graficar los procesos. Para esto es común utilizar cursogramas.
Los cursogramas son similares a los diagramas de flujo, pero generalmente siguen normas más estrictas para su construcción, y suelen ofrecer mucha más información que los diagramas de flujo. Existen distintos tipos de Cursogramas, a continuación se muestran ejemplos de los más comunes. Para más información de las construcción de los diversos tipos de cursogramas, se desarrollará un anexo.
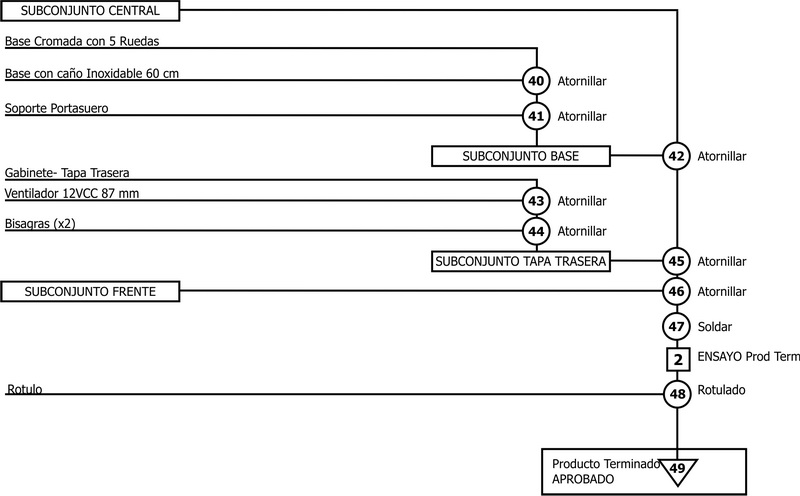
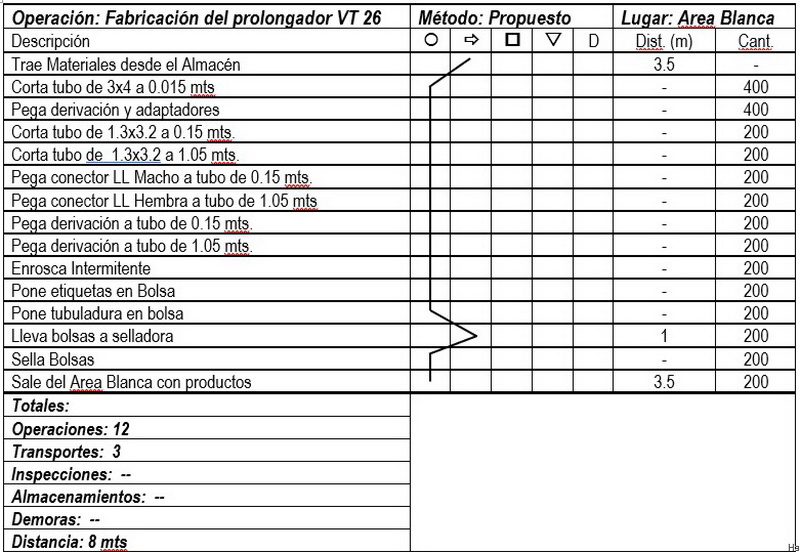
Cálculo de las Maquinas y Instalaciones
En este punto ya se han perfeccionado el proceso y sus distintas secciones operativas desde el punto de vista lógico, es importante ahora cuantificar los requerimientos de máquinas e instalaciones necesarias para cumplir el plan de ventas desarrollado a nivel comercial.
Plan de Producción y Programas de Producción
Si bien existen varios métodos para la planificación y programación de la producción para empresas en marcha, en proyectos de inversión el principal objetivo que persiguen es poder determinar la cantidad de máquinas necesarias, y en consecuencia cuantificar el flujo de materiales a lo largo de toda la planta. Por lo tanto, como en muchos otros aspectos de los proyectos de inversión, el proceso es más simple.
Para comenzar se empieza por definir el plan de Producción que en el caso de proyectos de inversión, debido a que no se cuenta como en una empresa en marcha con pedidos pendientes el plan de producción se hace coincidir con el plan de ventas en estado de régimen. Más adelante se determinará la producción y los materiales necesarios en el período de puesta en marcha (en el inicio del año 1).
Debido a que el plan de producción puede llegar a ser no homogéneo a lo largo de todo el año, es necesario separarlo en distintos programas de producción. Cada programa de producción responderá a un período donde se mantengan uniformes las condiciones de demanda y producción.
Los distintos programas de producción pueden surgir de:
- Estacionalidad en la demanda y por lo tanto en la producción
- Estacionalidad en la provisión de insumos
- Etapas de concreción cuando el proyecto tiene ventas crecientes
- Cambio en los ritmos de trabajo (pasar de 1 a 2 o 3 turnos)
Para cada uno de los programas de producción será necesario hacer un balance de materiales y de línea distinto, para finalmente llegar estos datos a períodos anuales sumando los distintos programas que pasan en un año.
El objetivo final de la programación de la producción y el balanceo de materiales y de la línea es poder realizar la Producción Demandada por el Mercado en el Tiempo Indicado. Sin embargo, existen los objetivos del proyecto, donde también se buscan maximizar los excedentes económicos, minimizar el costo de producción y eventualmente maximizar la productividad y rentabilidad del proyecto. Como en este punto del proyecto todavía no se ha desarrollado la elaboración económica, estos puntos son difíciles de verificar. Es por lo que se hace generalmente es optimizar en principio el uso en cuanto a tiempos de las máquinas e instalaciones, para luego evaluar distintas alternativas a las elegidas en el dimensionamiento de la incertidumbre y gestión del riesgo.
Para cada programa de producción, habrá que definir entonces la cantidad de cada producto a ser producido por unidad de tiempo. Si no es necesario realizar distintos programas de producción para un mismo año, generalmente la unidad de tiempo a la que se refiere es el año, si existen variaciones intraanuales, lo común es utilizar como unidad de tiempo de referencia el mes o si existieran la posibilidad de realizar varios turnos de trabajo, la unidad de tiempo de referencia es el turno. Aunque pueden realizarse, hacer un programa más específico no tiene sentido en proyectos de inversión.
A continuación, en las siguientes entradas (Balance de Materiales y energía, Ritmo de Trabajo, Balance de línea y requerimientos adicionales de procesamiento) explicaremos como llegar a cada programa de producción.
Balance de Materiales y Energía
Una vez determinado el volumen de producción necesario para cumplir con el programa de producción, es necesario realizar un balance de materiales y energía.
Explicaremos a continuación el balanceo de materiales para el caso más simple de un proceso con Monoproducto y pocos insumos. El desarrollo del balanceo de materiales para una planta multiproducto o para el caso del uso de múltiples insumos, es explicado en un apartado diferente (PONER LINK).
También se desarrollará en un apartado diferente el balance de materiales para el caso de variaciones en la producción (PONER LINK)
Conceptualmente, la lógica es muy sencilla. Para cualquier sección operativa la sumatoria de todas las entradas tiene que ser igual que la sumatoria de todas las salidas, tanto para el caso de los materiales como de la energía.
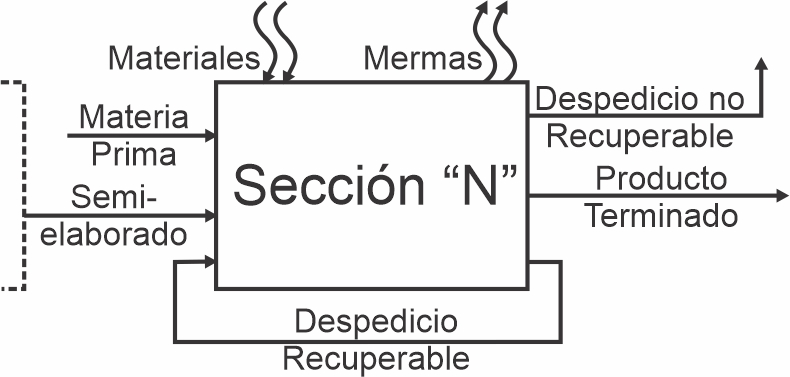
Vamos a definir en este punto cada uno de los estados en el que un recurso físico puede estar a lo largo del proceso productivo.
Materia Prima (MP): Son los recursos a partir de los cuales obtenemos, a través de un proceso de transformación, los productos terminados que se desean comercializar, y que guardan una relación proporcional con las unidades producidas.
Materiales (Mat): Conjunto de elementos que son necesarios para la fabricación o prestación de un servicio, pero no se convierten físicamente en parte del producto, generalmente no son cuantificables proporcionalmente con respecto a las unidades producidas,
Semielaborado (SE): Es un paso intermedio entre la materia prima y el producto Terminado. Generalmente son las salida de etapas intermedias del proceso.
Mercadería en Curso (MC): Es la mercadería que se encuentra dentro de un proceso productivo en un determinado momento siendo transformada. A los fines de su valuación, muchas veces se la integra a los semielaborados, y se los llama en conjunto Mercadería en Curso y Semielaborados (MCySE).
Producto Terminado: Son la salida principal del proceso productivo, las que tienen intención de comercializarse y de las cuales suelen provenir los principales ingresos del proyecto.
Subproductos: Son salidas secundarias del proceso productivo, resultan no utilizables en el proceso de producción y cuentan con un valor mensurable de recuperación económica. Categorizar a los productos comercializables en Productos terminados o subproductos muchas veces no tienen sentido, y simplemente se consideran a todos como productos terminados.
Desperdicios No Recuperables: Es el residuo de los bienes después del proceso productivo, resultan no utilizables en el proceso de producción y no cuentan con un valor mensurable de recuperación económica.
Desperdicios Recuperables: Es el residuo de los bienes después del proceso productivo al que son sometidos, pero que resultan utilizables en el proceso de producción.
Mermas: Aquello que se consume o se pierde en el proceso productivo en el volumen, peso o cantidad ocasionadas por causas inherentes a su propia naturaleza o al procesos productivo y cuya integración no se puede comprobar.
Para la mayoría de los proyectos industriales donde la demanda del producto, y por lo tanto el plan y el programa de producción, depende de las estrategias comerciales el balanceo de materiales se debe comenzar de la última sección, ya que el dato con el que se cuenta para empezar es la cantidad de producto terminado a vender.
En algunos casos específicos, como es el caso donde se procesa mercaderías de terceros o en el caso de los commodities donde la capacidad de planta está dada por la cantidad de materia prima que tengo que procesar, los cálculos pueden iniciarse con la entrada de la materia prima en la primera sección operativa
Vamos entonces a utilizar el ejemplo de un proceso sencillo.
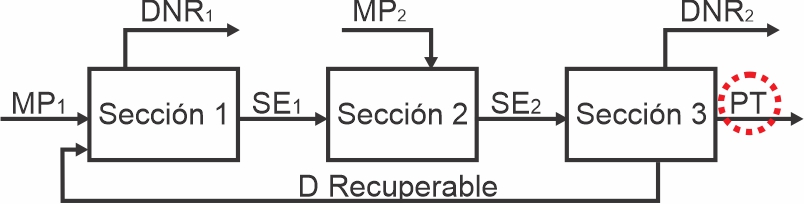
Para la última sección operativa, se tiene que comprobar que el la cantidad de Semielaborado 2 (SE2) tiene que ser igual (suficiente) para cubrir la cantidad de producto terminado a la salida de la línea, más los desperdicios no recuperables de la última sección (DNR2) y los desperdicios recuperables (D Recuperable)
Para determinar los diversos valores de cada uno de los rubros se cuenta con dos datos:
1) La cantidad de producto terminado que surgen del programa de producción
2) El flujo de bienes determinados anteriormente en el punto
Como con el flujo de bienes para una determinada sección operativa se tienen las proporciones de los semielaborados, materias primas, y desperdicios en relación con la salida de producto de dicha sección operativa se puede calcular simplemente por regla de tres el ingreso, así como también la salida de cada uno de los materiales, incluyendo cantidad de Semielaborado 2 (SE2).
Esta será la salida de la sección 2, con lo cual se puede calcular con el mismo método la cantidad del resto de los ingresos y egresos de materiales de dicha sección, incluyendo la cantidad de Semielaborado 1 (SE1) que es la salida de la primera sección.
Este proceso iterativo permite calcular la cantidad de todos los materiales (y también de energía) desde el inicio hasta el final necesarios para alcanzar el programa de producción deseado.
Como cada programa de producción implica una cantidad de producto terminado distinto, este proceso debe realizarse para cada programa.
Hay otros proyectos donde el balanceo puede comenzarse con el ingreso de las materias primas de la primera sección operativa, tal es el caso de los procesos con materias primas estacionales y perecederas, donde se requiere transformar la totalidad de la materia prima antes de que llegue su vencimiento, o en el caso donde la demanda del producto es inconmensurable con respecto a la capacidad de la planta, tal es el caso de los commodities. La lógica subyacente sigue siendo la misma, solo cambia el punto desde el cual se comienza el balanceo.
Es indispensable tener en cuenta, que durante cada proceso de transformación, las unidades de entrada y salida no son necesariamente las mismas
Una vez desarrollado todo este proceso se tendrá un esquema del siguiente tipo:
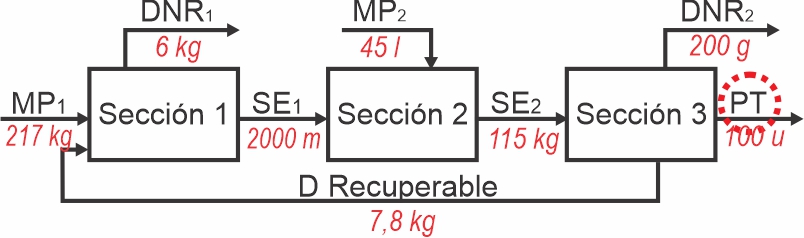
O más probablemente se tenga la misma información en una tabla, para ser utilizada a continuación en el proyecto.
El volumen de cada una de las mercaderías será utilizado para diseñar los medios de manipuleo y transporte necesarios, y en el caso de los desperdicios también los métodos para su tratamiento previo a la disposición final. Todo esto se determina en el apartado de Máquinas y equipos auxiliares (PONER LINK)
Para realizar este cálculo es importante tener en cuentas las unidades, ya que a lo largo de los procesos se van produciendo transformaciones. Todos estos valores tuvieron que ser averiguados cuando se determinaron las especificaciones de los medios de fabricación y control (PONER LINK)
En este punto pueden calcularse la proporción de desperdicio real y el proporción de desperdicio operativo.
La proporción de desperdicio real es la relación que existe entre el volumen de desperdicio no recuperable y el volumen de producción al final de la última sección operativa.
Este dato será utilizado más adelante en el cuadro de evolución de mercaderías (PONER LINK).
Si el desperdicio no recuperable y el producto terminado se expresan en las mismas unidades, la proporción de desperdicio real puede expresarse en porcentaje.
La proporción de desperdicio operativo es la relación que existe entre la suma de todos los desperdicios (tanto recuperables como no recuperables) y el volumen de producción al final de la última sección operativa.
Si los desperdicios y el producto terminado se expresan en las mismas unidades, la proporción de desperdicio real puede expresarse en porcentaje.
Estos datos de proporción de desperdicios en función de la producción tienen dos objetivos: por un lado poder calcular de manera rápida el volumen de desperdicios en caso de que la producción suba o baje, y por otro lado sirven pueden servir como indicador de gestión cuando la empresa se encuentra en marcha para verificar que los resultados obtenidos a nivel operativo siguen los supuestos del proyecto, y en caso de que esto no suceda, controlar las posibles causas de los desvíos.
Ritmo de Trabajo
El ritmo de trabajo indica la cantidad de horas, días y turnos que se trabajará. Hay que tener en cuenta que no siempre es necesario que todas las secciones operativas ni todos los procesos trabajen al mismo ritmo. Existen secciones operativas que al ser realizadas por máquinas pueden trabajar durante todo el día sin necesidad de intervención de personas, como también existen procesos de fraguado, secado, fermentado que pueden requerir varias horas o días y que sin lugar a duda durante las horas no laborables estos procesos siguen ocurriendo.
La cantidad de turnos a trabajar dependen de la localización donde se realiza el proyecto, de las limitaciones de los convenios colectivos de trabajo, de la necesidad de contar con luz diurna y muchas veces de decisiones del inversor (tal vez va a hacerse cargo de la empresa y solo quiera que se trabaje un turno).
Tal como se explicó en el tema del tamaño, desde el punto de vista de aprovechar las inversiones en máquinas y equipos de alto nivel de producción, lo recomendable es hacer un uso intensivo de los mismos y planificar trabajar las 24 hs. del día los 7 días de la semana (24/7). Para poder hacer eso, es necesario contar con 4 turnos de trabajo, generalmente en turnos rotativos.
Si una planta trabaja todos los días del año a toda hora, la cantidad total de trabajo disponible en un año es de 8760 hs.
En el otro extremo, si se decide trabajar solo 5 días de la semana 8 horas por día, la cantidad de horas trabajadas para ese turno serán de 2080hs. Esto implica que una planta en la que se trabaje en ese ritmo, solo se estará aprovechando en un 25% de la máxima capacidad posible.
Aunque desde el punto de vista del aprovechamiento el trabajar 24/7 es significativamente mayor, esto genera un sinnúmero de problemas desde el punto de vista de la organización de la producción, de la atención a los proveedores y necesidad de espacio para stock, los horarios y la atención de los trabajadores, la necesidad de contar con luz artificial y eventualmente calefacción durante las noches, etc.
Como punto de partida, es común comenzar con uno o dos turnos de trabajo, para luego ir incrementando los turnos a medida que es necesario pasar a programas de producción más grandes.
Para el cálculo de la cantidad de horas trabajadas por unidad de tiempo (año o mes), es importante recordar que no todos los días son laborables.
A los días totales, hay que restar los feriados obligatorios, las vacaciones pagas en el caso de operaciones manuales o semiautomáticas donde se requieran la presencia de una persona, y las paradas de planta para realizar el mantenimiento en caso de que esto sea necesario.
Para un año típico en Argentina, considerando el trabajo de lunes a viernes 8 hs por día, considerando que la media de vacaciones pagas es de alrededor de 13 días hábiles y que existen alrededor de 20 días no laborables en cualquier actividad debido a feriados, feriados puentes, día del trabajador del sector, para una sección manual o semiautomática (dependiente del trabajador) el total de horas trabajadas anualmente es de 1800 hs, equivalente a 150 hs mensuales.
La cantidad de días y horas trabajadas, así como también la posibilidad de implementar turnos rotativos, estarán explícitos en los convenios colectivos de trabajo específicos de cada sector.
Como se dijo en el apartado del programa de producción, una alternativa donde se cambia el programa de producción es cuando se agregan turnos de trabajo. Agregar un turno de trabajo implica pasar de 150hs mensuales a 300hs mensuales.
La principal ventaja de agregar turnos de trabajo para aumentar el ritmo de producción es que se aumenta la capacidad sin aumentar las inversiones. Esto es recomendable donde las inversiones en activos fijos (máquinas, instalaciones) son muy altas o donde la inversión en la mercadería en curso también resulta demasiado alta.
Sin embargo, aumentar los turnos implicar aumentar los costos indirectos de producción (personal de supervisión, control de acceso durante más horas a la planta de trabajo).
En este punto del proyecto, no se cuenta todavía con datos de los niveles necesarios de inversión para la ampliación de la producción a través de la incorporación de nuevas máquinas, ni el costo del personal indirecto necesario para aumentar un turno. En general a partir de la experiencia del tecnólogo o del criterio del ingeniero, se selecciona una alternativa y la otra alternativa se analiza en el dimensionamiento de la incertidumbre y gestión de riesgos.
Balance de Línea
En este punto ya se cuenta con los datos fundamentales para poder determinar el balance de línea para cada programa de producción: por un lado los puestos de trabajo o máquinas operativas que van a utilizarse en cada sección operativa (poner link), por otro lado el flujo de materiales que necesitan ser procesados a lo largo de cada sección operativa (PONER LINK) y por último el ritmo de trabajo.
El primer paso es la Determinación de Cantidad de Maquinas Operativas.
Para esto se comienza con el dato de la capacidad teórica de cada máquina o puesto de trabajo determinados anteriormente (PONER LINK a 2.5 Especificaciones de Medios de Fabricación y Control), y se la multiplica por la cantidad de horas a trabajar por período dado el ritmo de trabajo.
Como las capacidades de los puestos de trabajo o de las máquinas suelen estar en unidades por hora, y el ritmo de trabajo en horas por año (o mes en el caso de programas más específicos), se contará así con la capacidad teórica de UN puesto de trabajo o máquina en un año. Esta capacidad teórica es la máxima producción en condiciones normales de funcionamiento, entre dos paros sucesivos.
A esta capacidad teórica habrá que afectarla por un rendimiento operativo.
Este rendimiento operativo es la relación que existe entre las horas reales activas de la máquina versus las horas totales disponibles y surge de analizar qué cantidad de horas inactivas por paradas esperables tales como carga y descarga de materiales, mantenimiento preventivo, limpieza para el caso de las máquinas y de factores tales como ausentismos y retrasos, descansos, fatiga, monotonía en el trabajo, por comienzo y cierre para el caso de puestos de trabajos manuales.
Como en muchos otros casos en proyectos de inversión, es necesario consultar este rendimiento operativo con un tecnólogo con experiencia en máquinas similares para dar una opinión o con una estimación surgida de cálculo hechos por un ingeniero industrial.
Valores razonables para los coeficientes operativos rondan entre el 80% y 95% para secciones automáticas, entre el 70% y 90% para secciones semiautomáticas, y entre el 50% y 80% para secciones manuales.
Una vez determinada la capacidad real de cada puesto de trabajo o máquina, es necesario la determinación de la cantidad de máquinas o puestos de trabajo. Para esto, se debe comparar el programa de producción propuesto para cada sección operativa con la capacidad real de cada máquina. Al hacer la relación entre los mismos (programa de producción / capacidad real de la máquina) se podrá determinar la cantidad de máquinas necesarias para cada sección operativa.
Como puede observarse en la tabla, la relación entre el programa de producción y la capacidad real de una máquina no siempre dará números enteros, por lo que es necesario redondear la cantidad de máquinas o puestos de trabajo al entero inmediatamente superior.
Al redondear hacia arriba la cantidad de máquinas o puestos de trabajo, en cada sección operativa queda un excedente de capacidad. Por lo tanto, la capacidad real máxima de cada sección es superior al programa de producción propuesto, lo que nos lleva a poder calcular el grado de aprovechamiento seccional.
El grado de aprovechamiento seccional es un dato muy útil que nos permite determinar varias cosas. Por un lado, al indicar como se está aprovechando cada una de las secciones, el grado de aprovechamiento nos sirve como un indicador temprano de si realmente estamos en una escala de ventas y producción rentables. Esto se debe a que las tecnologías de producción van evolucionando con la demanda de las empresas competidoras a nuestro proyecto. Si uno está utilizando una sección operativa al 10% o 15% es porque ha comprado una sola máquina y esa máquina tiene un excedente de 7 a 10 veces el plan de ventas propuesto. Si hay otros competidores que tienen esa tecnología, es probable que la estén usando con un mayor grado de aprovechamiento y por lo tanto estén comercializando hasta 10 veces la cantidad propuesta para el proyecto, eso implica que tienen 10 veces más ventas para prorratear los costos fijos de la empresa, y por lo tanto potencialmente mejor margen que nosotros, lo que redundará en una mayor tasa de rentabilidad.
Cuando se tiene una sección operativa con un bajo grado de aprovechamiento (menor al 20%) es necesario analizar la posibilidad de tercerizar dicha sección operativa.
Se debe considerar tercerizar una sección operativa solo en el caso de que dicha sección operativa no sea un proceso crítico (que se quiere mantener controlado) o diferenciador para el proyecto. Cabe recordar que en este punto todavía no se cuenta con datos económicos como analizar cuál de las dos alternativas es la mejor, por lo que en este punto se debe tomar una decisión basada en la experiencia y eventualmente en el dimensionamiento de la incertidumbre y gestión del riesgo se analizará con todos los datos la conveniencia o no de cada alternativa.
Otra alternativa a tercerizar una sección operativa es vender la capacidad ociosa con la que se cuenta al tener un bajo grado de aprovechamiento seccional. Nuevamente hay que considerar si se trata de un proceso diferenciador y se quiere proveer este servicio a competidores. También hay que tener en cuenta la logística de recepción y de entrega de la mercadería de terceros para su procesamiento.
El grado de aprovechamiento seccional por otro lado sirve para determinar si la línea está balanceada. Se habla de una línea balanceada cuando el grado de aprovechamiento seccional es similar en todas las secciones.
Si se observa una línea desbalanceada, esto puede ser indicador de que se hayan elegido tecnologías que no son compatibles en cuanto a volúmenes entre sí, puede estar indicando que hay una combinación de secciones automáticas subaprovechadas con secciones manuales.
Es muy común que cuando se decide automatizar una parte de un proceso productivo, esta sección operativa tenga un grado de aprovechamiento mucho más bajo que los procesos manuales, como puede ser el caso de una soldadora de ola en un proceso de montaje electrónico, donde el resto de los procesos suelen pueden manuales.
El tercer uso que tiene el grado de aprovechamiento seccional es la determinación del cuello de botella y la máxima capacidad de la línea.
El cuello de botella es la sección operativa con el máximo grado de aprovechamiento. Esta sección operativa es la primera que se saturará en caso de aumentar la cantidad fabricada por encima del plan de producción para responder a un aumento de las ventas.
La máxima capacidad de la planta es la producción en la última sección cuando el cuello de botella se encuentra produciendo al 100%.
Esta es la máxima cantidad por producirse sin necesidad de cambiar la tecnoestructura de la planta, por lo tanto es la cantidad óptima por producir si se quiere optimizar tanto la rentabilidad de los activos como la rentabilidad de los costos, ya que es el mayor número entre los cuales se pueden prorratear los costos fijos sin aumentarlos.
En muchos casos se hace referencia a dos capacidades máxima de una línea o de un proyecto. La primera es la definición estricta tal como se acaba de explicar, la producción en la última sección cuando el cuello de botella está trabajando al 100%.
La segunda considera el tipo de procesos que se usa en cada sección. Es común que cuando se cuenta con procesos automáticos y manuales integrados en una línea, debido a que la capacidad de las secciones automáticas es muy superior a los procesos manuales, es probable que los procesos manuales se transformen en el cuello de botella. Sin embargo, adicionar personal y herramientas para dicho personal suele ser relativamente sencillo, ya que donde trabajan 10 personas fácilmente se puedan acomodar 1, 2 o 3 puestos adicionales. Es por eso por lo que muchas veces se habla de la máximas capacidad de una línea o un proyecto como la producción en la última sección operativa cuando el proceso automático con el mayor grado de aprovechamiento se encuentra trabajando al 100%.
Consideraciones de la Cantidad de Máquinas por sección
Volviendo al cuadro de Determinación de cantidad de máquinas por sección operativa, podemos ver el caso donde para la primera sección operativa son necesarias 5.1 máquinas, y por lo tanto la lógica indicaría que es necesaria adquirir 6 máquinas para poder cumplir con el programa de producción.
Pero si se considera el proyecto desde un punto de vista sistémico, hay que entender de donde surge esta necesidad de 5.1 máquinas y los efectos de comprar una maquina adicional y analizar si existen otros cursos de acción.
Vamos a comenzar por entender en nivel de inversiones y gastos necesarios para agregar esa máquina operativa adicional. Si se tratara de una inversión baja y que no requiera gastos adicionales de personal, es razonable adquirir esa máquina o puesto de trabajo adicional sin dudarlo.
Cuando se empieza a considerar que la inversión es significativa o se genera necesidades de costos indirectos adicionales significativos, hay que considerar otras cosas.
El primer caso es si el programa de producción está sucedido por otros programas de producción donde se requieran mayor uso de esa sección operativa. En estos casos, es recomendable adquirir esa máquina o puesto de trabajo adicional ya que será utilizada más adelante en el proyecto.
El segundo caso es considerar de donde surge el cálculo. El cálculo de 5.1 máquinas surge de considerar por ejemplo un rendimiento operativo del 73%. Si el rendimiento de esas máquinas se considerara de un 75%, los cálculos indicarían que con 5 máquinas es suficiente. La diferencia es realmente poco significativa, en especial si se considera que este rendimiento fue la opinión de un experto basado en experiencia previas y no un cálculo preciso a partir de datos históricos de una máquina en marcha.
En estos casos, se puede llegar a considerar la compra de 5 máquinas, indicando este hecho como una aclaración cuando se hacen los cálculos.
También hay que considerar que el cálculo de la capacidad teórica de las máquinas se hizo en base al trabajo de 1800 hs anuales. Si se trabajaran 1826 hs en un año, se podría llegar a cumplimentar el programa de producción. Para ponerlo en perspectiva, solo se necesitaría 1 hora extra cada dos semanas para poder cumplimentar ese programa de producción sin necesidad de comprar una máquina adicional.
En estos casos, se puede considerar la compra de 5 máquinas, indicando en el trabajo y haciendo los cálculos de que será necesario trabajar esta hora extra cada 15 días.
Otro caso está vinculado a lo explicado en cuanto al aprovechamiento seccional. Si se tratara de un proceso que es fácilmente tercerizable, se puede considerar tercerizar la confección de 30 metros en el período para así no tener que adquirir en ese momento esta máquina adicional.
En estos casos, se puede considerar la compra de 5 máquinas, indicando que se tercerizará parte de la producción para poder cumplir con el programa de la producción.
Finalmente hay que considerar de donde surgió el programa de producción. Este programa surge de un plan de producción que a su vez surge de un plan de ventas. Este plan de ventas fue la mejor estimación de la demanda potencial a satisfacer con el producto, precio, promoción y plaza determinados. Esto no quita que realmente no tenemos una certeza de la necesidad de la venta de esa cantidad de producto. Es por eso que si en lugar de venderse 100 productos se vendieran 98 productos, alcanzaría con contar con 5 máquinas en la primera sección operativa.
En estos casos, se puede considerar la compra de 5 máquinas, bajando el plan de ventas de 100 unidades a 98 unidades para el período considerado, aclarando que esta situación se dio debido a la necesidad de optimizar el uso de los activos.
Hay una excepción a esta situación, que es cuando el plan de ventas surge como una condición de provisión en un contrato para un cliente. Por ejemplo, si estas 100 unidades surgieran de un contrato de exclusividad de provisión con una automotriz, constructora o un gran supermercado y esta es la base para poder asegurarse las ventas, no quedaría otra que adquirir esa máquina adicional para poder cumplir con la condición del contrato.
Es importante volver a destacar que este trabajo de balanceo de línea debe hacerse para cada programa de producción, y eventualmente, si se considera que se puede aprovechar capacidad ociosa para un determinado programa de producción para realizar trabajos de un programa de producción subsiguiente, se debe tratar de hacer.
Requerimientos Adicionales de Procesamiento
La determinación en cada sección operativa de la cantidad de cada máquinas y puestos de trabajo operativos lleva a poder determinar otros requisitos adicionales necesarios para el procesamiento, ya que prácticamente ninguna máquina o puesto de trabajo funciona sin el acceso a los recursos necesarios (insumos, transporte, energía), o extrayendo los resultados del proceso (tanto entregas de semielaborados como productos terminados como la eliminación de residuos). Antes de entrar en cada uno de estos aspectos, nuevamente es importante entender que si bien se tratará de abarcar la mayor cantidad posible de estos requisitos adicionales aplicado a la mayor cantidad posible de industrias y máquinas, cada industria, máquina y puesto de trabajo es un mundo en sí mismo si se le pregunta a un experto en ese nicho (imagínense todo lo que se puede hablar de autos y cada automotriz no tiene tener más de unas docenas de vehículos y versiones, sin embargo se publican miles de millones de páginas solo acerca de este tema). Por lo que se tratará de ir a los conceptos generales, para ir luego a algunos ejemplos particulares para algunas industrias, dejándose a futuro para cuando se vaya actualizando este libro ejemplos más particulares.
Servicios requeridos
Para empezar, es necesario el cálculo de consumos de energía, agua, gas y otros servicios necesarios. Cada máquina o puesto de trabajo requiere una cantidad de estos servicios, que se han determinado oportunamente (Poner Link). Simplemente será necesario multiplicar el consumo por máquina por la cantidad de máquinas trabajando de manera simultánea.
Al contar ya con la cantidad de máquinas requeridas en cada sección operativa, se puede comenzar a esbozar una organización de cada una de ellas, teniendo en cuenta las áreas que pueden compartirse (como por ejemplo el almacenaje temporal, el área de mantenimiento), así como también el acceso a la provisión de energía, agua, eliminación de residuos y otros servicios.
Es importante en este punto también evitar el cruce de flujo de materiales y servicios que puedan llegar a perjudicarse entre sí, por ejemplo la energía eléctrica y los líquidos, la materia prima virgen y los residuos, los insumos termosensibles o inflamables y las fuentes de calor.
La distribución final de todas las máquinas en el área productiva se llevará a cabo en el apartado de distribución de planta (PONER LINK).
Electricidad
Es tal vez el servicio más importante para la producción industrial, ya que prácticamente cualquier maquina operativa en general es eléctrica o tiene actuadores, sensores y controles que dependen de la electricidad, además de que los puestos de trabajo, más allá de no requerir máquinas eléctricas, necesitan iluminación en el puesto de trabajo. Siendo la más utilizada, es también la que más variedad y trabajo requiere a la hora de determinar sus instalaciones. Se hará una descripción general aquí de las distintas alternativas y consideraciones a la hora de determinar las instalaciones eléctricas, los cálculos específicos serán tratados en un posterior anexo (PONER LINK).
Empecemos por diferencias las diversas alternativas de provisión de electricidad a partir de una red eléctrica pública. Esta es entregada en distintos voltajes, de acuerdo con las necesidades de provisión y uso de las empresas. En general en bajas tensión puede ser monofásica (100V, 110V, 127V, 220V, 230V o 240V en 50Hz o 60Hz dependiendo del país), Trifásica o de potencia (entre 200V y 480V dependiendo del país), para luego entrar en medias tensiones entre 1KV y 36KV, en general en acuerdos específicos con las distribuidoras eléctricas, y finalmente alta tensión que es utilizada más bien para el transporte y distribución de energía eléctrica o en casos muy particulares de industrias como puede ser la Producción de Aluminio.
Dejando de lado esta última, podemos considerar que si el proyecto planteado tiene previsto el uso principalmente de herramientas eléctricas manuales o de mesa de baja intensidad de uso, puede llegar a considerarse la contratación de electricidad monofásica. En cuanto se empiezan a utilizar herramientas y máquinas con motores de potencias mayores a 1HP, o gran cantidad de máquinas de potencias medias, es conveniente considerar la contratación de electricidad trifásica. Esto tiene varias ventajas: el consumo y costo de la maquinaria trifásica es menor (en relación con aquellas similares monofásica), las instalaciones trifásicas suelen ser más robustas que las monofásicas y a partir de la electricidad trifásica puede sacarse 3 líneas de electricidad monofásica. En cuanto esto, a pesar de que se comentará en el anexo más en profundidad, es necesario balancear las cargas entre las distintas fases de la energía trifásica para optimizar el consumo.
En cuanto a las medias tensiones, estas son más eficientes desde el punto de vista de los costos que la baja tensión, pero tiene la limitación de que no todas las áreas donde se puede instalar una empresa cuentan con este tipo de provisión por parte de las distribuidoras eléctricas, por lo que es común que se utilice en general en industrias localizadas en zonas o parques industriales. Es común la contratación de media tensión en plantas petroquímicas, plantas de tratamientos de agua, sistemas ferroviarios, plantas con gran cantidad de máquinas operativas grandes eléctricas o que usan la electricidad como medio de calentamiento (por ejemplo hornos alimenticios o extrusoras de plásticos), centros comerciales con gran cantidad de instalaciones de iluminación, aeropuertos, hospitales, etc. Muchos de estos equipamientos y la iluminación en realidad usan energía eléctrica trifásica o monofásica para funcionar, pero la cantidad de consumo es tal que es necesario contar con una provisión significativa de energía.
Para dar una idea de rangos de contratación, para la empresa EPEC (proveedora de servicio eléctrico de la provincia de Córdoba en Argentina), para la baja tensión en 220V se limita hasta 5 kW de demanda máxima, para baja tensión trifásica hasta 300 kW de demanda máxima, y la media tensión entre 300 kW y 20MW de demanda máxima. En principio para un proyecto industrial podría considerarse que alrededor del 80% de la demandas está asociada al consumo de las máquinas productivas y el resto a iluminación y e instalaciones informáticas. Por lo que usando ese criterio y los rangos de contratación, podría rápidamente estimarse en este punto que tipo de servicio se necesita contratar.
Luego de saber el servicio, es importante entender la estructura de cualquier instalación eléctrica.
Primero considerar si se tendrá sistemas de generación de emergencias alternativos para la totalidad del proyecto o para una parte de él aparte de la provisión de energía eléctrica de red.
Segundo la alimentación en caso de proveerse en media tensión, deberá “bajarse” a las tensiones utilizadas por los equipamientos (generalmente 380V y 220V) esto requiere de instalaciones específicas.
Tercero contar con los sistemas de maniobra y protección adecuados para cada una de las etapas o secciones. Esto se refiere a sistemas de corte (interruptores) y a protecciones por sobrecargas, ante bajadas de tensión, ante cortocircuitos.
Cuarto es necesario realizar el transporte de dicha energía eléctrica entre la entrada del servicio hasta los centros de consumo, esto se realiza a través de conductores eléctricos acordes tanto a las cargas o consumos (a mayor consumo mayor diámetro de conductor) y a las condiciones medioambientales en las que se realiza dicho transporte (a veces en contexto de movimiento, aplastamiento, humedad, vibraciones o incluso evitar la interferencia electromagnética de la corriente eléctrica en redes de información).
Por último y como cualquier otra instalación, las instalaciones eléctricas si bien suelen ser bastante robustas, requieren de un mantenimiento tanto preventivo como correctivo.
Como se dijo antes, el cálculo y diseño de esto se realiza en un anexo especifico.
Como con cualquier otro aspecto de diseño vinculado a las máquinas y las instalaciones, a medida que se vaya avanzando en el proyecto puede llegar a haber varias iteraciones de este tipo de instalaciones, sobre todo en lo específico al transporte de la energía eléctrica. En una primera iteración lo que se busca es determinar la estructura general que en general puede lograrse a través de un diagrama unifilar, dejándose los planos o esquemas en planta para las últimas iteraciones.
ANEXO- INSTALACIONES ELÉCTRICAS
Agua
El siguiente servicio en importancia en cuanto a uso es probablemente el de agua, ya que si bien no se utiliza en todos los procesos industriales, sin duda sí son necesarios para el uso sanitario de las personas que trabajaran en la futura planta.
Como en el caso de la energía eléctrica, solo se harán algunas consideraciones generales en este punto acerca de las distintas cuestiones para tener en cuenta inicialmente, y el detalle de los cálculos se desarrollará en un anexo (PONER LINK).
Las instalaciones de agua incluyen tanto el transporte como el tratamiento vinculado a las siguientes instalaciones:
- Agua para procesos Industriales
- Agua para limpieza de instalaciones
- Agua para consumo sanitario/humano
- Agua para instalaciones de incendios
- Eliminación de aguas residuales
Como puede intuirse, cada uno de estos sistemas de aguas tienen requisitos diferentes de calidad, frecuencia y flujo. En general los requisitos asociados a los aspectos de los procesos industriales y la limpieza de instalaciones tienen que ver más con requisitos técnicos fijados por los proveedores de maquinarias y los tecnólogos. Sin embargo las instalaciones relacionadas con el consumo sanitario/humano, incendios y aguas residuales tienen en general regulaciones estatales tanto a nivel municipal, provincial y nacional, siendo el primero de estos el más común ya que las habilitaciones de las instalaciones suelen estar delegadas a ese nivel más directo y cotidiano de control. Si bien el diseño de todos estos aspectos es importante, desde el punto de vista de la cantidad a utilizarse el mayor uso es el agua para los procesos industriales, particularmente los de limpieza, por lo que suele ser este un limitante a la hora de definir localizaciones de plantas industriales.
Yendo a la provisión de esta agua, las posibilidades de provisión son diversos, y en general en orden de importancia son:
- Conexión a red de agua potable
- Pozos de agua de napas subterráneas
- Toma de aguas de cursos naturales y acequias
- Recolección de Agua Meteórica (de lluvias)
- Desalinización de Agua de mar
El orden este está generalmente vinculado a la facilidad de acceso y a la inversión y costo asociado a la consecución de agua potable a partir de estas fuentes, ya que la conexión a una red de agua potable tiene una inversión casi nula o muy baja, mientras que en el otro extremo la desalinización de agua de mar tiene tanto una inversión como un costo significativo.
Así como en las instalaciones eléctricas es necesario tener en cuenta los distintos voltajes a ser utilizados en las plantas industriales, en el caso de las aguas en general se separan en 3 líneas separadas: Agua aptas para consumo humano y usos industriales que requieren que los productos sean aptos para consumo humano, aguas residuales (tanto de residuos industriales como de residuos de la actividad humana), y aguas industriales para usos específicos pero no necesariamente aptas para consumo humano (agua para calderas, agua para productos farmacéuticos, aguas no potabilizadas, etc.).
Como en el caso de las instalaciones eléctricas, existen en las instalaciones de agua elementos de maniobra y seguridad, siendo esta última en general solo aquellas vinculadas no tanto a peligros vinculados con el riesgo del agua, sino a evitar desbordes de tanques que provoquen problemas.
Más allá de estas observaciones generales, el cálculo y diseño de las instalaciones de agua se desarrollarán en el ANEXO- INSTALACIONES de AGUA.
Gas y/o Combustibles
Luego de las instalaciones de electricidad y agua que se encuentran presentes en todos los proyectos de inversión y las plantas que surgen de ellos, el siguiente tipo de instalaciones presente en cuanto a mayor frecuencia (aunque en mucho menor medida) son las instalaciones vinculadas al gas y los combustibles.
El gas natural y otros combustibles principalmente son utilizados en los procesos industriales con el objetivo de calefaccionar en sus distintas versiones (hervir, pasteurizar, cocción, tostado, derretir, tratamientos térmicos, secado, deshumidificación) pero también como insumo para la síntesis de productos petroquímicos, producción de plásticos, fertilizantes, generación de energía eléctrica, como combustible para vehículos y para la incineración de residuos.
Todas las instalaciones de combustibles en general, debido a que los mismos son inflamables se encuentran, más allá de las precauciones propias de las empresas, reguladas por distintos organismos estatales.
La instalaciones de combustibles líquidos en general son más acotadas en las plantas industriales, y son usados en principio como combustibles para vehículos y para la generación de energía eléctrica en grupos electrógenos.
El gas es más utilizado como combustible principalmente porque es más económico, es relativamente seguro si las instalaciones se mantienen de manera adecuada, es práctico ya al llegar vía red en general se tiene una disponibilidad inmediata y constante del mismo (aunque existen ocasiones donde hay contratos interrumpibles) y es algo más ecológico que los combustibles líquidos (aunque su combustión siempre genera CO2).
Las instalaciones de gas más allá de los sistemas de maniobra y seguridad, tiene un elemento particular que son las instalaciones de baja y aumento de presión. El gas natural tanto a partir de las redes públicas como en las instalaciones de gas natural licuado está a gran presión por lo que se debe contar con reguladores de presión. También puede llegar a pasar que por cuestiones operativas alguna maquina necesite el gas a mayor presión y por lo tanto tenga que colocarse algún sistema de represurización.
Son sistemas generalmente simples que buscan una conexión lo más recta posible entre la entrada a la planta y los consumos puntuales de las maquinas, teniendo en general como única precaución que los caños de transporte no pasen por áreas afectadas por el calor o la humedad.
Más información para el cálculo y desarrollo de estas instalaciones pueden observarse en el ANEXO- INSTALACIONES DE GAS y COMBUSTIBLES.
Aire Comprimido
Las instalaciones de aire comprimido no son tan comunes en todas las empresas. Los usos más comunes del aire comprimido es la utilización de herramientas neumáticas que tienen la ventaja de ser más livianas, rápidas, baratas y con mayor torque. Pero también es utilizados para elevadores neumáticos, sistemas de pintado, limpieza, automoción, movimiento de materiales, soplado.
Los sistemas de aire comprimido se suelen dividir en los sistemas de producción del aire a través de compresores de diversos tipos, y los sistemas de conducción, ya que la inversión en los compresores suele ser significativa y los mismos pueden ser revendidos de manera sencilla por lo que son consideradas más maquinas operativas que instalaciones industriales.
Un sistema similar al del aire comprimido son los sistemas de vacío, donde en lugar de inyectar aire, se produce una extracción de aire.
Para más información sobre este tipo de instalaciones y sus cálculos, referirse al ANEXO- INSTALACIONES DE AIRE COMPRIMIDO.
Instalaciones de Climatización / Termomecánicas
Las instalaciones de climatización comprenden a las instalaciones de calefacción y refrigeración del ambiente donde se realizan las actividades productivas así como también las administrativas y comerciales. Debido a que la generación de frío y calor en realidad surgen o de la energía eléctrica o de los combustibles, es común que los equipamientos de refrigeración y calefacción se determinen muchas veces en forma conjunta con dichas instalaciones. No obstante todo lo que hace al tendido de ductos de transmisión de aire si es que se decide ir por sistemas centralizados de climatización tiene todo un desarrollo particular. En este tipo de instalaciones también se engloban las necesidades de flujo de renovación de aire, de control de humedad y polvos en el ambiente, eliminación de sustancias nocivas gaseosas entre otras.
Comenzaremos por definir las distintas estructuras posibles. Como se planteó hace un instante, los sistemas pueden ser centralizados o descentralizados en función de que la generación de frío/calor/aspiración se halle en un solo lugar o en múltiples en función de las necesidades de cada puesto de trabajo. Las ventajas de los sistemas centralizados es que en general tienen mejor rendimiento y eficiencia energética, una mejor difusión y circulación de aire, menor emisión de ruido es relativamente sencillo de instalar en nuevas construcciones, en general son sistemas frio/calor por lo que con una sola instalación se solucionan ambos problemas. Entre las desventajas se encuentran su necesidad más elevada de inversión, el problema de que en caso de avería todo el sistema deja de funcionar y el costo de dicha reparación es más costoso, el mantenimiento y limpieza de los conductos puede ser complicados por lo que son más propensos a crear rincones donde se produce colonización de microorganismos.
En general son utilizados para grandes superficies homogéneas donde no se requieren necesidades particulares de calidad de aire en puntos determinados.
Cuando los requerimientos difieren de punto a punto, como es el caso de zonas donde se trabaja con frío y otras en máquinas que generan calor o polvos, o en ambientes limitados pequeños limitados por requerimientos del proceso es común que se utilicen sistemas descentralizados. También es común usar sistemas descentralizados cuando para la realización del proyecto se cuente con un edificio preexistente donde la instalación de ductos genere problemas de altura de circulación o requiera la rotura de losas.
Un caso particular de los sistemas de refrigeración industrial es aquel que hace referencias a las cámaras frigoríficas, utilizadas comúnmente en la industria alimenticia para mantener los alimentos frescos o congelados en un estado adecuado de conservación, y en menor medida en la industria farmacéutica donde algunos medicamentos y vacunas requieren este tipo de instalaciones.
En el caso de la industria farmacéutica, tanto en la producción de medicamentos como de productos médicos, también es común ver sistemas tanto de inyección de aire como de extracción de manera simultánea, para reutilizar gran parte del aire que se encuentra en las áreas productivas, ya que dicho aire debe ser filtrado con filtros absolutos llamados HEPA para evitar la contaminación. Estos sistemas también son utilizados en la industria electrónica donde el polvo puede provocar fallas en los circuitos.
En general las instalaciones de refrigeración se hacen a través de sistemas convectivos, aunque en algunos casos como es el caso de procesos industriales o cámaras frigoríficas se hacen a través de sistemas de conducción del tipo intercambiadores de calor. En el caso de las instalaciones de calefacción, aparte de los sistemas convectivos, que en muchas ocasiones comparten los sistemas de distribución con los sistemas de refrigeración, es común la utilización de sistema de conductivos (pisos radiantes) o sistema de calefacción por radiación (incluyendo el uso de la energía solar).
Finalmente y antes de pasar a la siguiente instalación, es importante destacar que los sistemas de refrigeración/calefacción se diseñan de manera conjunta con los edificios, o al menos se rediseñan junto con los edificios, ya que para ya que para mantener eficientes y efectivos desde el punto de vista de costos los sistemas de climatización el diseño de los edificios es importante, más específicamente sus paredes, techos y orientación. En el caso de los proyectos de inversión, más allá de que se puede llegar al nivel de detalle que se quiera, en general siempre se usan valores normales de temperaturas promedio y conductividad de paredes y techos para los cálculos, dejando el diseño específico para los profesionales responsables de la obra civil en el periodo de instalación.
Más información sobre el cálculo y diseño en proyectos de inversión de estos sistemas en el ANEXO- INSTALACIONES DE CLIMATIZACION/TERMOMECANICAS
Sistemas de transmisión y procesamiento de información
Si bien pueden llegar a existir algunas otras instalaciones específicas para algunas industrias específicas, el último tipo de instalación que suele estar presente en prácticamente todas las plantas modernas son las instalaciones destinadas a la transmisión electrónica de información, más en particular el cableado estructurado para transmisión de datos informáticos como el cableado telefónico y la transmisión de imágenes, así como sus centros de procesamientos.
Si bien estos 3 sistemas pueden ser distribuidos por cableados específicos, es común hoy en día que toda la información se digitalice y sea transmitido por el denominado cableado estructurado.
Las necesidades de transmisión de información pueden surgir de múltiples fuentes: desde el control de seguridad ante robos y siniestros, la supervisión tanto en áreas de trabajo tanto de procesos y personas, la comunicación entre las personas adentro de la organización, la utilización de sistemas integrados de gestión, el control de equipamiento en áreas remotas o ambientes poco amigables con las personas, el control de los procesos en sistemas cerrados, el registro de información que pueda ayudar a la verificación y validación de requisitos de calidad tanto de productos o procesos, hasta la transmisión de música funcional para hacer más amena la experiencia en algunos lugares de trabajo.
Al igual que otro tipo de instalaciones, en este caso se requieren aparte de los sistemas de transmisión de la información, esa información debe recogerse o transmitirse al algún hardware capaz de procesar esa información a través de software y transformarla en algo aprovechable por las personas. En ese sentido, obviamente ambos subsistemas (transmisión y procesamiento) se diseñan de manera conjunta.
Si bien sistemáticamente se ha comentado acerca del cableado para la transmisión de información, en rigor a la verdad existe la posibilidad de la transmisión inalámbrica de dicha información, que tiene la ventaja de no depender de estar físicamente en un mismo lugar todo el tiempo para recibir la información, tal es el caso de los Handies, radios móviles o teléfonos celulares, y la ventaja de no requerir la instalación de redes físicas que requieren muchas veces una inversión significativa. En general es aceptable y deseable este tipo de redes inalámbricas para la transmisión de video o voz ya que el mayor problemas con las redes inalámbricas pueden ser las interferencias y microcortes, que si bien son aceptables en los casos citados, para el manejo de datos puede ser conflictivo sobre todo si el software asociado a la recepción/emisión de datos no es los suficiente robusto para soportar cortes en la información (y en general no lo son ya que el desarrollo de software robusto en este sentido requiere mucha más inversión y tiempo de lo que las empresas en general están dispuestas a invertir dada la celeridad de la competencia en este sector).
Es por esto por lo que la transmisión de datos en general se hace a través del denominado cableado estructurado, que está muchos menos afectado por las interferencias. No obstante esto, es importante destacar que no deben usarse las mismas instalaciones (caños, bandejas, canales) para el cableado de información y el cableado eléctrico, ya que el cableado eléctrico genera campos electromagnéticos que pueden afectar la información transmitida.
Como con cualquiera de las otras instalaciones mencionadas anteriormente, el diseño de este tipo de instalaciones es toda un campo de conocimiento en sí mismo, pero en proyectos de inversión se busca determinar en principio la inversión y los costos asociados a estas instalaciones de manera razonable, por lo que esto se desarrollará en el ANEXO- SISTEMAS DE TRANSMISION Y PROCESAMIENTO DE INFORMACIÓN.
Máquinas y equipos auxiliares de transporte y manipuleo
Generalmente, para el transporte entre secciones operativas o el manipuleo de materiales, es necesario contar con equipos específicos para este tipo de tareas.
En general podemos identificar dos tipos de medios de manipuleo de materiales:
- Los medios fijos que se utilizan exclusivamente en el lugar donde están instalados de acuerdo con las necesidades productivas, tal es el caso de las cañerías, carruseles, cintas transportadoras, ascensores, malacates, etc. Estos son muy comunes en procesos continuos o de alto flujo o cadencia, que requieren soluciones específicas y eficientes.
- Los medios móviles que permiten ser trasladados entre varios lugares tales como escaleras, carretillas, carros, zorras, apiladores, autoelevadores, grúas o hasta puente grúas. Tienen la ventaja de la versatilidad ya que al ser usados en varios lugares y para varias tareas, permiten optimizar de esta manera su eficiencia. Mientras que algunos son económicos y es común que se adquieran uno para cada lugar, en otros casos como el caso de los apiladores y autoelevadores eléctricos o a combustión su inversión es significativa y por lo tanto es necesario optimizar su uso.
Mientras que las características, capacidades y tamaños de los primeros diseñan en general en forma conjunta con las máquinas del proceso operativo, en el caso de los segundos será necesario determinar la cantidad de horas necesarias para su uso en cada situación de trabajo, programar en función del tiempo su uso para cada movimiento y en este caso asignar prioridades de uso en función la criticidad de las tareas.
Como para mejorar la optimización del uso de este tipo de equipamiento es necesario no solo conocer los movimientos dentro de la planta productiva, sino también el movimiento desde y hacia los depósitos, así como también los movimientos desde los proveedores y hacia los clientes, desarrollaremos este concepto en el capítulo de logística, una vez que se ha desarrollado el Cuadro de Evolución de las mercaderías que nos muestra dichos flujos (poner LINK).
Debido a que estos medios no son todos de común conocimientos para todos los elaboradores de proyectos, se explicarán los más utilizados en el ANEXO- EQUIPOS AUXILIARES de MANIPULEO
Equipamiento para tratamiento de Residuos
Si bien el tratamiento de residuos y los equipamientos necesarios deberían ser calculados y determinados junto con el resto del proceso productivo ya que forman parte de este, debido a la naturaleza de estos procesos es común analizarlos de manera segregada.
En cuanto a la naturaleza no referimos es que la mayoría de los procesos de tratamiento de residuos suelen ser eficientes cuando se trata una gran cantidad de residuos, y tanto en los proyectos como en las empresas que surgen de ellas, los residuos es algo que se busca minimizar, por lo que no es fuera de lo común que este tipo de procesos se tercerice.
Nuevamente la gran variedad de tratamientos existentes para todos los tipos de industrias escapa al alcance de esta guía, aunque se buscará describir los más importantes y comunes en el ANEXO- METODOS y EQUIPAMIENTO PARA TRATAMIENTO DE RESIDUOS.
Sin embargo acá lo que si daremos los criterios generales para la elección de alternativas razonables.
En primer lugar, lo que se debe buscar es información a través de un tecnólogo especialista en los procesos que instalaremos o a través de información disponible en bibliografía o fuentes de confianza de la naturaleza de los residuos a ser tratados. Una manera de identificarlos es sin duda buscar empresas que fabriquen productos similares y ver qué tipo de residuos generan y como los tratan.
Podríamos categorizar según su estado a los residuos en 3 grandes grupos: Gaseosos, sólidos y líquidos (que incluye a los líquidos con sólidos en suspensión) o desde la naturaleza entre biológicos, químicos, mecánicos; pero tal vez la clasificación más importante es aquella desde el punto de vista legal, que clasifica a los residuos en regulados (también llamados peligrosos, especiales) y residuos no regulados. Esta diferencia sustancial hace que para el caso de los regulados uno tenga la obligación de tratarlos y de contar con los registros de tratamiento y trazabilidad de dichos residuos. Entre los más comúnmente regulados en todo el mundo están los residuos patológicos, los residuos radioactivos, químicos e inflamables, aunque también las normativas más modernas suelen también incluir dentro de sus criterios de residuos peligrosos a los que contienen metales pesados (Mercurio, Cadmio, Plomo, Cromo), a los que tienen una alta carga biológica o química (residuos de las industrias alimenticias, farmacéuticas), residuos corrosivos, residuos de fitosanitarios, etc. Por ejemplo para el caso de la UE existe un listado con 20 categorías de residuos y unas 800 subcategorías. En el caso de Argentina existen unas 45 categorías de residuos.
La mayoría de la normativa regula al generador del residuo, que es quien es general es responsable del residuo durante toda la vida de este, pero también regula a los transportistas y a las empresas u organizaciones encargadas del tratamiento y disposición final.
En general en los proyectos de inversión se busca plantear las siguientes estrategias, obviamente si son posibles:
- Reutilizar los potenciales residuos para transformarlos en Desperdicios Recuperables
- Elegir procesos que no generen residuos regulados
- Transformar esos residuos regulados en subproductos para otras industrias
- Minimizar la generación de residuos
- Localizar el proyecto en un parque industrial con plantas comunes para el tratamiento de ese tipo de residuos
- Eventualmente contar con plantas propias de tratamientos
- Almacenar los residuos de una manera controlada para permitir que la frecuencia de retiro de la planta sea razonable
Mientras que las primeras estrategias se explican más o menos por si solas, la última implica definir más correctamente de que se trata una frecuencia razonable de retiro, así como el almacenamiento de manera controlada.
En muchos proyectos de inversión que preceden a empresas medianas o pequeñas, la cantidad de residuos que se generan, sobre todo si son líquidos o sólidos, son relativamente bajas, en el orden de las decenas/cientos de litros o algunos kilogramos al día. Eso hace que resulte complicado que una empresa tercerizada de tratamiento vaya a realizar el viaje de manera diaria para retirar esos residuos. Además de que cada vez que se retiran residuos de una planta, estos deben ser tratados como un acto administrativo separado y por lo tanto las tramitaciones y gastos fijos asociados a cada uno de ellos deben computarse individualmente. Por eso es común que lo que se haga sea almacenar estos residuos de manera temporal en tanques, bidones, barriles o tachos adecuados para que se retiren más residuos de manera simultánea. Aquí la pregunta que surge es cual es la frecuencia deseable. En principio debería conocerse el tamaño del transporte utilizado para los residuos, que por ejemplo para el transporte de líquidos pueden estar entre los 6.000 y 36.000 litros (obviamente teniendo en cuenta que no todos los camiones pueden circular por todos los lugares), y para transportes de solidos (o líquidos en tambores) pueden ir desde los 600 kg hasta los 40.000 kg o más en el rango que va entre una furgoneta y un camión rígido o un camión con tráiler.
Obviamente que a mayor tamaño del vehículo a llevar los residuos, menor frecuencia se requerirá para el retiro de los residuos, pero como contrapeso más importante será el depósito de almacenamiento y el mayor tiempo de presencia en la planta puede provocar más riesgosos asociados al almacenamiento de dichos residuos. Si dichos residuos se trataran de recortes de chapa por ejemplo, el riesgo estaría más vinculado a cortes que a la descomposición y reacción de los residuos, mientras que si se trata de un residuo líquido, el riesgo está asociado a las perdidas en los tanques de almacenamientos o si fuera inflamable riesgos de incendios.
En general, y excepto que un tecnólogo consultado recomiende otra frecuencia, lo más común es que el retiro de residuos se planifique entre 1 vez por semana a 1 vez por mes, lo suficiente como para no complicar el trabajo operativo diario pero no tan infrecuente que el personal no recuerde por experiencia propia las normas correctas para el manipuleo de dichos materiales. Si bien es verdad que estas normas pueden reforzarse con capacitaciones, no es lo mismo hacer que escuchar cómo se hace una cosa.
Una vez más recordemos que el objetivo del proyecto es lograr para aspectos como estos, que si bien son importantes son complementarios a la operación principal, encontrar una solución razonable para lograr cuantificarlos y eventualmente valorizarlos en valores monetarios para mostrar su impacto a nivel de resultados.
Si la frecuencia de retiro de residuos es más chica que 1 o 2 veces por semana, en un equipo de transporte relativamente grande, es necesario considerar seriamente incorporar un sistema propio de tratamiento de residuos.
Un aspecto que es pocas veces considerado en cuanto al tratamiento de residuos son los residuos que surgen de los propios tratamientos, que también deberían ser considerados. Dos ejemplos clásicos de este tipo de residuos son los filtros de polvos en las cabinas de pintura o los filtros utilizados para la osmosis inversa. Estos filtros a su vez son residuos peligrosos y debe considerarse su disposición final. Obviamente su volumen es mucho menor que el aire o el agua tratada, y por eso se utilizan estos medios de filtrado, pero aun así deben ser dispuestos de acuerdo con las normas.
Hasta aquí llegan los criterios generales para considerar distintas alternativas para la consideración de los residuos, y antes de avanzar recodamos que más información sobre los métodos y residuos específicos pueden encontrarse en el ANEXO- METODOS y EQUIPAMIENTO PARA TRATAMIENTO DE RESIDUOS.
Calificación y Formación de los Operadores
Ya con la cantidad de máquinas necesarias en cada sección y dada la necesidad o no de la presencia de la cantidad de operarios por máquinas o de máquinas por supervisor, ya se empieza en este punto a definir la cantidad de mano de obra directa con la que se necesitará contar.
En este punto ya se hayan determinadas definitivamente las máquinas específicas de cada sección, por lo cual pueden comenzar a especificarse las necesidades puntuales de operarios vinculados a las máquinas y su capacitación y esta información servirá con dos propósitos: Definir la descripción del puesto de trabajo (PONER LINK) y definir el momento donde es necesario incorporar al personal a la planta (PONER LINK) si es que es necesario por ejemplo que los operarios estén presentes durante la instalación de las máquinas.
En general los puestos de trabajo responden a algunas de las siguientes categorías:
- Trabajadores Auxiliares: Son aquellos que ayudan a los trabajadores principales en tareas complementarias al trabajo principal como es la carga y descarga de materiales e insumos, tareas de limpieza y mantenimiento básico, movimientos y traslado de materiales, etc. En general son los puestos de entrada para trabajadores con poca o nula experiencia laboral, y les permite ir aprendiendo con la experiencia el trabajo y la rutina de la planta o el área de trabajo. La formación que debe darse a estos trabajadores suele ser sencillas y en general cubiertas en un par de horas del propio trabajo, además de capacitaciones reales y formales de las normas de seguridad en el lugar de trabajo, que puede ser desde 1 hora hasta cursos de 1 semana dependiendo de los riesgos que existan.
- Trabajador multipropósito: Esto en general se da en proyectos pequeños o medianos con gran variedad de trabajos necesarios para hacer relativamente simples, y donde es posible y recomendable hacer rotar a los trabajadores ya que el trabajo rutinario en un solo puesto en una sola posición puede llevar a enfermedades profesionales. También es común en máquinas multipropósito que puede ser utilizadas para diversas tareas, tal como puede ser una banda de lijado. En estos casos suelen ser más importantes los controles de verificación de que un trabajo hecho (en general visuales o con elementos de medición simples) que el trabajo en sí que suele ser sencillo por lo que la capacitación debería estar más orientada a esos controles y como realizarlos. En general son los puestos de trabajo de entrada de ascenso para los trabajadores auxiliares o desde el punto de vista de proyectos de inversión, de trabajadores que tienen como condición algún grado de experiencia en trabajos previos.
- Trabajador con actividad Única: Cuando se trata de un trabajador con una actividad única, como manejo de un torno, cocineros o vendedores, aquí la experiencia previa es casi un requisito insoslayable ya que se tratan de un conjunto de tareas específicas. En todo caso la formación y capacitación de estos trabajadores tiene más que ver con las situaciones específicas (máquina, recetas, clientes) de la empresa/proyecto y no tanto con los procesos en sí. Esta formación puede llegar a ser bastante más larga, dependiendo de la naturaleza del proyecto. Incluso puede llegar a ser necesario la contratación de este personal en el período de instalación con la puesta a punto de la maquinaria para que aprenda los requisitos de operación, limpieza y mantenimiento de dicha maquinaria.
- Trabajador con Actividad Única pero múltiples puestos de trabajo: No es fuera de lo común en algunos sectores operativos donde las maquinarias son automáticas y donde solo es necesaria la atención del operario parte del tiempo para la carga, descarga en períodos cortos de tiempo, el cambio de matrices o herramental o la inspección de algún parámetro del proceso con frecuencias relativamente bajas (atención 1 vez por hora o cada varías horas), que un operario se encuentre a cargo de varias máquinas o puestos de trabajo de manera simultánea. Ejemplos de estos son las secciones operativas de inyectoras automáticas, los centros de mecanizado automatizados, las mezcladoras o amasadoras en las industrias alimenticias, y los telares automáticos en la industria textil. Esto puede también suceder en las líneas continuas que se venden llave en mano, donde el operario realiza actividades en las distintas secciones operativas. En este caso el operario tiene una función más de supervisión de la maquinaria que de intervenir propiamente en la transformación del producto, por lo que puede consignarse en la descripción de este tipo de puestos de trabajo: o trabajadores con experiencia previa en el tipo de proceso especifico de la industria que pueda detectar por experiencia que está sucediendo, o trabajadores con experiencia previa de supervisión que tengan la habilidad de ante alguna no conformidad o desvío poder reaccionar rápidamente y solucionar el problema. Como en el caso anterior, es común que sea necesario considerar incorporarlos a este tipo de trabajadores durante la instalación y puesta a punto de las maquinarias.
Transformación de los programas de producción en planes anuales
En este punto ya se cuenta con la información referente a cada Balance de Materiales y energía, Ritmo de Trabajo, Balance de línea y requerimientos adicionales de procesamiento para cada programa de producción.
Lo único que queda en este punto es combinar los distintos programas de producción para cada subperiodo para llegar a las cantidades de materiales y maquinas necesarias para cada año.
Recordemos que cada programa de producción está dado para un nivel de producción distintivo asociado por ejemplos a escalas de producción o estacionalidad, y dichos programas de producción pueden ser distintos a lo largo de un mismo año. Por eso para cada año es necesario integrar los distintos programas de producción en un plan anual, que eventualmente será aquel que será valuado para poder determinar los costos e inversiones para ese año en el dimensionamiento económico, permitiendo integrar esos costos e inversiones con aquellas surgidas de otras áreas (comercial, administración, logística, etc.) y poder configurar el flujo neto de caja anual que será utilizado para evaluar el proyecto.
Pero hay que entender que el pasar de programas a planes no significa simplemente sumar los distintos aspectos, ya que hay una diferencia entre flujos y stocks.
Para ir al caso particular de los proyectos de inversión industriales, en cuanto a las necesidades de materias primas, materiales, consumos de servicios se realiza la suma algebraica de los mismos, obteniendo el total necesario para el año.
En cuanto a las necesidades Maquinas operativas, instalaciones y equipos auxiliares, personal y stocks (esto en realidad se verá más adelante en la evolución de las mercaderías PONER LINK) no se debe hacer la suma ya que las maquinas utilizadas en un turno o subperiodo pueden ser utilizadas en los otros turnos o subperiodos, con lo cual habrá que elegir para cada uno de estos el valor más alto. Por ejemplo si en el periodo de cosecha (o en un turno) se necesitan 3 máquinas para procesar el programa de producción mientras que en el periodo sin cosecha (o en otro turno) se necesitan solamente 1 máquinas, se deberán consignar que son necesarias 3 máquinas. Es un error común no diferenciar los distintos programas e integrarlos en un plan, y proceder a hacer simplemente a hacer cálculos a nivel anual, con lo cual podría resultar que si en una temporada alta se necesitaban 3 máquinas para cubrir la demanda mientras que en una temporada baja solo se necesitaba 1 máquina, cuando uno realiza las cuentas podría verse tentado a poner que se necesitan en promedio 2 máquinas. Está definición de la cantidad de máquinas (o instalaciones) tienen como objetivo no hacer cálculos a nivel anual, que no deberían hacerse si en un año hay distintos programas, si a determinar en el dimensionamiento económico las inversiones necesarias. Y para el plan previsto, es necesario invertir en 3 máquinas porque en algún momento será necesario contar con estas 3 máquinas. Lo mismo sucede con el personal, aunque con estos el problema es distinto. Mientras que una maquinaria que no es utilizada puede ser apagada y por lo tanto no tener gastos variables, esto no sucede con el personal. Si el personal fue contratado, deberá seguir pagándose el sueldo sin importar si tiene o no trabajo para realizar. Obviamente existen soluciones a este tipo de problemáticas, por ejemplo algunos convenios colectivos de trabajo que permiten una organización estacional del trabajo o trabajadores temporales o legislaciones en algunos países que permiten la desvinculación del trabajador sin costo adicional, pero con trabajadores altamente capacitado como los descriptos en algunos casos citados en el punto anterior (PONER LINK), el perder un trabajador especializado con alto grado de capacitación específica puede ser un problema en su reposición. Es por esto por lo que en la conformación del plan anual a partir de los programas se tiene que contemplar estos aspectos. Es común entonces que a este personal se le asigne tareas adicionales en temporada baja de mantenimiento y puesta a punto de las maquinarias, o ayudar en el trabajo en otras líneas, procesos o productos o incluso llegado el caso en reconfigurar el proyecto para incluir otros productos y actividades que hagan que dichos trabajadores realicen tareas productivas.
Otra solución en el caso de algunos procesos o líneas en los que es posible es contar con una dotación menor de empleados (o máquinas) suficientes para cubrir la necesidad del menor programa de producción, y el exceso en temporada alta contratarlo en empresas tercerizadas.
Evolución de las Mercaderías
Ya determinadas las secciones operativas y la cantidad de máquinas ó puestos de trabajo en cada uno de estos, es necesario analizar como evolucionan las mercaderías presentes en el proyecto en sus distintos estados, tanto desde el punto de vista de los flujos como desde el punto de vista de los stocks.
Para comenzar es importante diferenciar dos estados distintos desde el punto de vista de los consumos de mercaderías, el estado de régimen y el Período de Puesta en Marcha. Recordemos las definiciones de cada uno de estos:
Período de Puesta en Marcha: Es el tiempo que necesario para alcanzar el diseño del producto y del proceso, tanto en calidad como costo.
Durante este período ocurren 3 impactos:
- El nivel de producción en menor
- El nivel de desperdicios es proporcionalmente mayor
- Hay un aumento en los desembolsos asociados a gastos variables por la necesidad de aprendizaje y puesta en ritmo del personal y las máquinas.
Estado de Régimen: Es el período en el que se produce de acuerdo con lo pretendido en el plan de producción y con la calidad pretendida en cuanto al producto y proceso, sin pérdidas asociadas a la falta de experiencia ó falta de puesta a punto del proceso.
Debido a que el estado de régimen es el estado normal al que se debería estar fabricando al final de cualquier plan ó programa, siempre se realizan los cálculos en estado de régimen y luego se estima la producción en el período de puesta en marcha.
Como durante el balanceo de línea, es necesario separar el plan de producción en distintos programas para eventualmente llevar estos datos a períodos anuales sumando los distintos programas que pasan en un año. (PONER LINK).
Como en el caso del balanceo de materiales, Explicaremos a continuación la evolución de las mercaderías para el caso más simple de un proceso con monoproducto y pocos insumos, con planes y programas anuales homogéneos y sin incrementos en las ventas a partir del año 2.
El desarrollo de la evolución de las mercaderías de materiales para una planta multiproducto ó para el caso del uso de múltiples insumos, es explicado en un apartado diferente, (PONER LINK) así como también la evolución de las mercaderías para el caso de variaciones en la producción (PONER LINK)
Cuadro De Evolución De Las Mercaderías
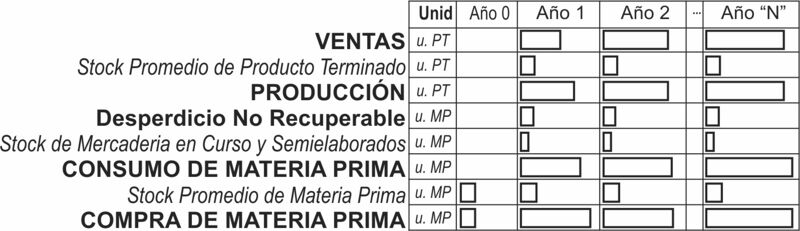
El cuadro de evolución de las mercaderías busca mostrar la evolución en cantidades de todos los posibles estadios de las mercaderías.
Si bien a simple vista parece simple, es necesario considerar dos aspectos fundamentales:
- No olvidarse de identificar las unidades de cada uno de los estados de las mercaderías
- Entender que mientras para los rubros que muestran flujos tales como Ventas, Producción, Desperdicios No Recuperables, Consumo y compras de Materias primas (destacados en Negrita en el cuadro) los valores indicados se tratan de los consumos anuales (ó del período si este no fuera anual) mientras que para los stocks de materias primas, mercadería en curso y producto terminado (en cursiva en el cuadro) los valores indicados se trata de la cantidad de dichos stocks al final del año ó del período si este no fuera anual.
Volvamos a recordar en este punto, que si bien es posible hacer cálculos y cuadros con periodos más cortos o más largos que un año, en realidad la ventaja de generar cuadros anuales es poder eventualmente tener los datos agrupados de manera de generar flujos de cajas anuales, lo que permite obtener tasas de rentabilidad anuales, útiles para la evaluación del proyecto.
En el caso de proyectos donde no se observen crecimiento en algunos períodos, es común simplificar este cuadro, agrupando los años que tienen los mismos valores.
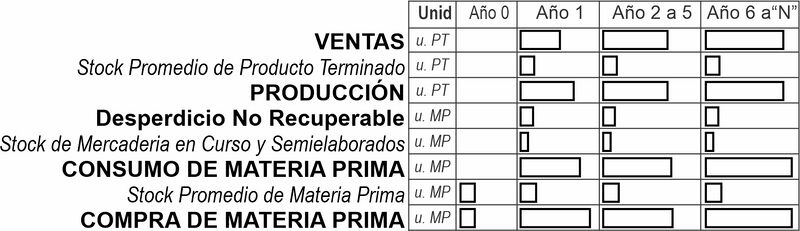
Determinación del Personal
Elaboración de Anteproyecto de Planta
Generación de Cronograma de Ejecución
Una vez desarrollados todos los aspectos materiales que tienen que ver con la puesta en funcionamiento de la planta del proyecto, el último paso es tratar de poner las actividades necesarias para su realización en un marco temporal.
A este marco temporal se lo denomina cronograma de ejecución.
El cronograma de ejecución es un diagrama calendario (ya que en uno de sus ejes se coloca el tiempo en divisiones superiores al día), más en particular un diagrama de Gantt ya que en el Cronograma de ejecución es importante que las diversas actividades se encuentren vinculadas unas con otras.
En el cronograma de ejecución, las actividades que se ponen son orientadas específicamente a un proyecto, y primordialmente concentradas en el período de instalación ya que es importante optimizar estos tiempos para mejorar eventualmente la rentabilidad del inversor al ajustar los plazos para las inversiones que se realizan.
A continuación se muestra un cronograma de ejecución acerca del cual se irán haciendo las observaciones para su construcción:
Descripción temporal, Etapas y Momentos del Cronograma de Ejecución
Como puede apreciarse en el eje horizontal del cronograma, existen algunos aspectos constructivos específicos en el Cronograma de Ejecución.
Desde el punto de vista de las unidades de medidas, las divisiones menores suelen estar en semanas ó meses, ya que esto permitirá que el cronograma de ejecución entre fácilmente en una hoja. Si se quisieran hacer divisiones en días, esto provocaría para la mayoría de los proyectos (que tardan al menos 4-5 meses) una cantidad excesiva de divisiones, que no son fáciles de dibujar y sin una utilidad desde el punto de vista del control del proyecto.
Para el caso de algunas actividades particulares, como por ejemplo la implementación de sistemas informáticos críticos, es común que para esa actividad se despliegue un cronograma específico anexo con las divisiones en días e incluso horas.
En cuanto a las divisiones mayores, estas se colocan en las unidades que vayan a ser empleadas eventualmente para la evaluación del proyecto en su vida útil. Generalmente esto es en años, lo que me permite calcular por ejemplo una tasa interna de retorno, ó una rentabilidad ó unas utilidades anuales. En casos particulares se pueden usar trimestres, como por ejemplo en empresas que coticen en bolsa y que tengan que presentar balances trimestrales, en bimestres en empresas concursadas donde el síndico pida información cada dos meses, ó en cualquier otra que se requiera.
Existen tres etapas en todo diagrama de ejecución, la Preinversión que ocurre desde la toma de decisión de empezar a analizar metódicamente el proyecto hasta que se toma la decisión de Ejecutar el proyecto, la Instalación que va desde que se decide ejecutar el proyecto hasta que se inicia la producción con intención a la comercialización y la Explotación que va desde el fin de la instalación hasta el fin del período de análisis. De esta última etapa, generalmente solo se colocan en el diagrama los primeros meses que es donde ocurre el período de puesta en marcha y, en caso que sean necesario también se pueden describir actividades para la instalación de nueva etapa del proyecto (si es que el mismo se hace en varias etapas).
Como convención se toma como el Momento 0 el momento que separa la instalación de la explotación del proyecto. En la mayoría de los proyectos este momento es fácilmente distinguible ya que la fabricación y la comercialización inicial prácticamente al unísono, mientras que en otros proyectos tales como las explotaciones forestales ó los proyectos inmobiliarios pueden pasar años hasta que se comercialice los productos. En estos casos habrá que considerar la recomendación de acuerdo a los usos y costumbres para esa actividad.
Los años anteriores al momento 0 se considerarán como años Negativos y los años posteriores como años positivos. Cabe recordar que para todo el proyecto, los años de utilizan de manera genérica (Año -2, Año -1, Año 1, Año 2, etc.) ya que no se tiene la fecha especifica donde el inversor se decida a iniciar el proyecto, tal como se hizo en el plan de ventas y durante todo el dimensionamiento físico (y se seguirá en el resto de los dimensionamiento).
Etapa de Preinversión: Conceptos y Tareas
La etapa de preinversión comienza con el encargo por parte del patrocinador de la elaboración del proyecto y finaliza con la decisión de iniciar la ejecución del proyecto de inversión.
Estudio de prefactibilidad y factibilidad: Esta tarea incluye todos los análisis y documentos que son necesarios para elaborar y formular el proyecto.
En el caso de empresas en marcha, también incluyen una descripción de la situación actual y los planes de la empresa para poder contrastarlos con el impacto en los resultados que tendría el proyecto. El resultado de esta etapa es el documento que conocemos como “Proyecto de Inversión”.
Evaluación externa y aprobación del proyecto de inversión: Una vez confeccionado el documento citado previamente, es necesario que se envíe a todos aquellos que tengan que aprobar el proyecto: los inversores que serán quienes pondrán la parte principal de los aportes necesarios, los financistas (bancos) que necesitan la información para acordar los créditos en base a las proyecciones, y los entes gubernamentales de los cuales puede depender algún beneficio que tenga previsto el proyecto. Esta actividad puede llevar desde unas semanas hasta un tiempo indefinido que culminará con la toma de decisión del inversor de ejecutar el proyecto.
Etapa de Instalación: Conceptos y Tareas
En esta etapa es donde se realiza el mayor desarrollo de actividades y donde es indispensables optimizar el cálculo de los tiempos ya que cualquier demora por la mala programación llevaría a postergar el inicio de las actividades comerciales y por lo tanto los ingresos del proyecto.
Existen varios tipos de actividades, desde las vinculadas a la organización de la empresa, a la construcción y puesta a punto de Edificios e instalaciones, aquellas vinculadas a las máquinas, a la adquisición de materias primas y materiales y al personal. Todas estas son importantes y muchas veces se vinculan entre ellas, desde las más evidentes como la necesidad de construir el edificio y las instalaciones de manera simultánea, hasta algunas menos evidentes como contar con materias primas para hacer pruebas con las máquinas adquiridas.
Actividades de Organización de la empresa
Decisión de Ejecutar el Proyecto: Está es la actividad que dispara el proceso de instalación. En los cronogramas de ejecución se la suele indicar como una actividad instantánea, ya que es un proceso lógico y no físico.
Constitución y Organización de la empresa: Una vez tomada la decisión de ejecutar el proyecto, la primera actividades constituir la empresa de manera legal e inscribirla en el registro público correspondiente (la IGJ en Argentina) así como también inscribirla en la/s autoridad/es fiscal/es (AFIP, AGIP, ARBA, etc). Esto permitirá que todos las facturas y recibos que se hagan, ya se puedan hacer a nombre de la empresa, así como también se podrá empezar a trabajar contractualmente a nombre de la empresa.
Selección y contratación de Responsables de la Instalación: Cuando el proyecto no puede ser llevado a cabo por el inversor, es necesario que este contrate a alguien que se encargue de todas las actividades durante el período de Instalación. La persona responsable de la instalación no necesariamente será la persona responsable de la empresa que surja del proyecto, ya que ambas actividades pueden requerir habilidades diferentes. El ejemplo más claro es un Arquitecto que se encarga de la construcción de un edificio, el cual una vez listo será administrado por un administrador de consorcio. En otras ocasiones si puede ser la misma persona que se haga cargo luego de la empresa ó de una parte de la misma, por ejemplo la gerencia de producción. Esto dependerá de cada proyecto.
Esta persona será la responsable de ejecutar y controlar la instalación del proyecto, y en caso de necesitarlo tomará la decisión de contratar ó subcontratar actividades específicas o menores a lo largo del proyecto.
Alquiler o compra de Oficinas: La persona que se encarga de la instalación puede llegar a necesitar algún lugar físico para llevar a cabo sus tareas. Aunque cada vez más la mayoría de las actividades pueden hacerse de manera remota y digital, siempre será necesario contar con un domicilio donde llegue toda la información y notificaciones oficiales. Muchas veces alcanza con contar con un apartado postal para las notificaciones.
Trámites de habilitación de ante organismos Gubernamentales: Depende de la actividad que realice la empresa, es necesario contar con una habilitación previa para poder empezar a fabricar, importar, comercializar algunos productos o brindar ciertos servicios. Muchas de estas habilitaciones se han ido digitalizando y suelen ser inmediatas, pero otras suelen llevar mucho tiempo, incluso a veces años. Es importante tener en cuenta que a veces, algunas de las primeras actividades que se realizan durante la instalación están vinculadas a estos trámites, ya que sino se corre el riesgo de estar meses ó años con una planta instalada pero sin poder utilizarla.
Elaboración de presupuestos definitivos para Control de Gestión: A pesar de que en el proyecto de inversión ya se contaba con presupuestos de maquinas, equipos, edificios y construcción elaborados en el dimensionamiento económico, es necesario verificar estos presupuestos y actualizarlos para verificar que siguen estando vigentes. Esta actividad es muy común en lo que respecta a los terrenos ó edificios, ya que si bien se pudieron haber usado para el proyecto algunos que estaban disponibles en ese momento, estos pueden haber sido vendidos entre que se hizo el proyecto y se tomó la decisión.
Liquidación de Créditos: El momento de la liquidación de créditos se define en el dimensionamiento financiero (más adelante en el proyecto), por lo que cuando se confecciona inicialmente el cronograma de ejecución este dato no se haya disponible. Hay que recordar por lo tanto que, una vez que se definan los créditos y cuando se liquidan, habrá que actualizar el cronograma para incluir esta información.
Actividades vinculadas a Edificios e Instalaciones
Compra y posesión del terreno: El tiempo de esta actividad incluyen, además del hecho formal de la compra que es relativamente corto, el tiempo que se tarda en poner en condiciones dicho terreno, puede ser tanto la limpieza y el desmonte si se trata de un terreno sin mejoras, como la demolición de las edificaciones en el mismo que no sean necesarias.
Elaboración de Proyecto definitivo del Edificio y Obras complementarias y del proyecto definitivo de las instalaciones industriales: Los proyectos definitivos son necesarios desde el punto de vista práctico para poder construir los edificios e instalaciones de manera rápida, coordinada y sin contratiempos pero desde el punto de vista formal también pueden ser necesarios para la actividad siguiente es la tramitación de la aprobación para edificar.
Tramitación de Aprobación de Permisos para edificar: Lamentablemente, en muchas jurisdicciones el tiempo necesario para la aprobación de permisos para construir puede demorarse largamente, vinculados a la poca adecuación de los organismos públicos ó las empresas proveedoras de servicios para el volumen de tareas a realizar, o porque se requieren multiplicidad de pasos burocráticos y administrativos a distintos niveles. Una solución para esto muchas veces es comprar edificios previamente habilitados para la actividad que se desea realizar.
Construcción de Edificios, Obras Complementarias e Instalaciones Industriales: Suele ser la actividad que más recursos monetarios, de personal y de materiales necesita en el período de instalación, así como también un conocimiento específico de como coordinar y realizar las distintas etapas, por lo cual en general se delega esta actividad en un Arquitecto ó un Ingeniero Civil. La única precaución a tener en cuenta es que muchas veces hace falta coordinar estas actividades con la de la instalación de las máquinas y equipos, bien porque se necesita instalar las máquinas una vez ya realizado determinado trabajo (por ejemplo el piso ó contar con el techo para que no queden a la intemperie) ó porque por el tamaño de las máquinas es necesario construir el edificio después de instalar la maquinaria.
Habilitaciones definitivas: Nuevamente aquí aparece los organismos gubernamentales ó las empresas de servicios que necesitan hacer un control final de las instalaciones para habilitar la planta. Esto también puede provocar demoras adicionales, con lo cual muchas veces se solicita la inspección definitiva sin haber terminado la obra.
Actividades vinculadas a Maquinarias
Maquinaria a Importar: La maquinaria a importar implica una gran cantidad de procesos desde la compra, construcción, embarque, transporte Marítimo, despacho a Plaza, transporte a fábrica y Montaje de la dicha maquinaria. Todo este proceso es secuencial, y como en cualquier diagrama de Gantt, la planificación de dichas actividades comienza por la última en el tiempo que es el montaje de dicha maquinaria. El montaje de esa maquinaria tiene que estar listo disponible para el inicio de la prueba de las mismas. A partir de ese momento, se van hilvanando hacia atrás en el tiempo todas las actividades.
Si la maquinaria se trata de máquinas sencillas y fáciles de construir por parte del fabricante, todo este proceso puede llevar un par de meses: por ejemplo que el transporte marítimo desde China o Europa lleva alrededor de 20 o 30 días, y el despacho a plaza y transporte a fábrica puede llevar unos 10 o 15 días.
Pero para máquinas hechas a medida, que requieren gran cantidad de especificaciones por parte del cliente, máquinas grandes o con gran demanda, muchas veces los tiempos antes del embarque pueden llevar muchos meses o hasta más de un año, para luego tener que transportarse, despacharse a plaza e instalarse. Esto hace que, en algunos proyectos, la primera actividad que tenga que hacer el responsable de la instalación es colocar la orden de compra de la maquinaria para lograr que empiecen a correr todos estos tiempos lo antes posible.
Maquinaria Nacional: Si bien las observaciones realizadas para las maquinarias importadas corren también para las máquinas nacionales, los procesos de compra, transporte y montaje suelen ser más sencillos ya que se cuenta con un apoyo local con experiencia previa para estas actividades. Además que no son necesario el transporte marítimo ni el despacho a plaza.
Prueba en vacío de la Maquinaria: Una vez que se cuenta con toda la maquinaria disponible en la planta, es común realizar una prueba en vacío para verificar que todas se encuentran en un estado adecuado de funcionamiento. Una alternativa a esta actividad suele ser la realización de un primer lote de muestra para poder evaluarlo, enviarlo a analizar y poder utilizar esos datos para habilitar el producto.
Actividades vinculadas al Personal
Selección, Contratación y Capacitación de Personal: Aquí se está hablando del personal que va a estar en la empresa una vez iniciada la explotación. En muchos casos es importante contar con alguna parte del personal presente cuando se hace la instalación y prueba en vacío de la maquinaria, para que sepa su funcionamiento y puedan ser capacitados por los fabricantes de las máquinas, o se necesita del personal para poder recibir los primeros lotes de materias primas. Si no se tienen esta necesidades, muchas veces alcanza con iniciar este proceso un mes antes de la finalización de la instalación de la planta.
Actividades vinculadas a la Mercadería
Unas semanas (o meses dependiendo de la complejidad) antes de comenzar el periodo de explotación del proyecto, se realiza la Selección definitiva de Proveedores para poder realizar una Compra Inicial de Materias Primas y Materiales. Esta compra inicial debe coincidir con la confección del lote de prueba, o bien es la última actividad del período de instalación, ya que con la disponibilidad de la materia prima se puede iniciar la producción con la intención de vender, que marca el momento “0” que es el inicio del plan de explotación.
Etapa de Explotación: Conceptos y Tareas
La etapa de explotación inicia con la incorporación de la materia prima en el área de operaciones en el caso de producciones industriales, cuando se abre al público por primera vez en comercios ó cuando se empieza a contactar a los clientes en el caso de las empresas de servicios.
Como se dijo anteriormente de esta etapa, generalmente solo se colocan en el diagrama los primeros meses que es donde ocurre el período de puesta en marcha (tiempo que se tarda en alcanzar el diseño del producto y del proceso).